Los materiales plásticos para la impresión 3D protagonizan una jornada del CEP
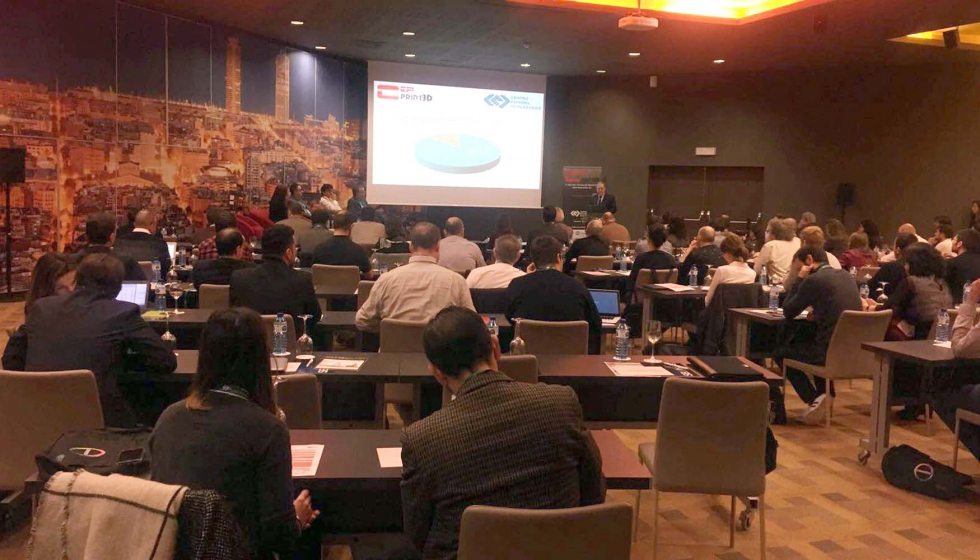
La idea de celebrar una jornada dedicada a los materiales para impresión 3D surgió tras una encuesta realizada por el CEP a sus asociados. La encuesta reflejó que el 54% de los asociados que contestaron se habían planteado el uso de esta tecnología, pero que un mayor porcentaje no conocía los materiales que ofrece el mercado, y mucho menos sus propiedades. Ante este interés, por un lado, y el desconocimiento, por el otro, el CEP decidió preparar esta jornada que acercó esta tecnología al sector del plástico. Fabricantes de maquinaria de impresión 3D, productores de materiales de impresión, centros tecnológicos, consultoras e ingenierías explicaron a través de ponencias aplicaciones, casos de éxito y ejemplos que pusieron de manifiesto que la revolución tecnológica de la impresión 3D no ha hecho más que empezar.
Gafas personalizadas
El primer ponente de la mañana fue Juan-Carlos Düsteler, Chief Innovation Officer de la compañía Horizons Optical, spin-off de Indo. Düsteler presentó el servicio Made4U, que produce gafas 100% hechas a medida a través de la impresión 3D. Después de un escaneado facial que localiza los parámetros de la cara, se imprimen las gafas por SLS (Selective Laser Sintering) con poliamida o titanio. Aunque hoy en día se fabrican solo 50.000 gafas por este procedimiento en todo el mundo, Düsteler señaló que “el crecimiento del mercado es imparable” y que este sistema permite diseños de monturas que con otras tecnologías serían imposibles. Sin embargo, el jefe de Innovación de Horizons Optical señaló que las barreras que hay para el desarrollo de gafas personalizadas es la limitación de materiales, que en estos momentos son las poliamidas y titanio o aluminio, cosa que limita los acabados y las propiedades intrínsecas de los materiales. “Cada vez más están apareciendo impresoras que permiten usar multimateriales o introducir en cada voxel el material que tú quieras y en el futuro la propiedad que tú quieras. Entre 5 y 10 años va a ser posible hacer muchas más cosas con acabados mucho mejores y apariencias también mejores”, explicó Düsteler. También, el ponente mostró ejemplos de aplicaciones de la unión del escaneo digital con la impresión 3D en el sector sanitario, con la fabricación de prótesis, lentes de múltiples tipos e incluso la reconstrucción de partes fracturadas de una forma muy rápida y totalmente a medida.
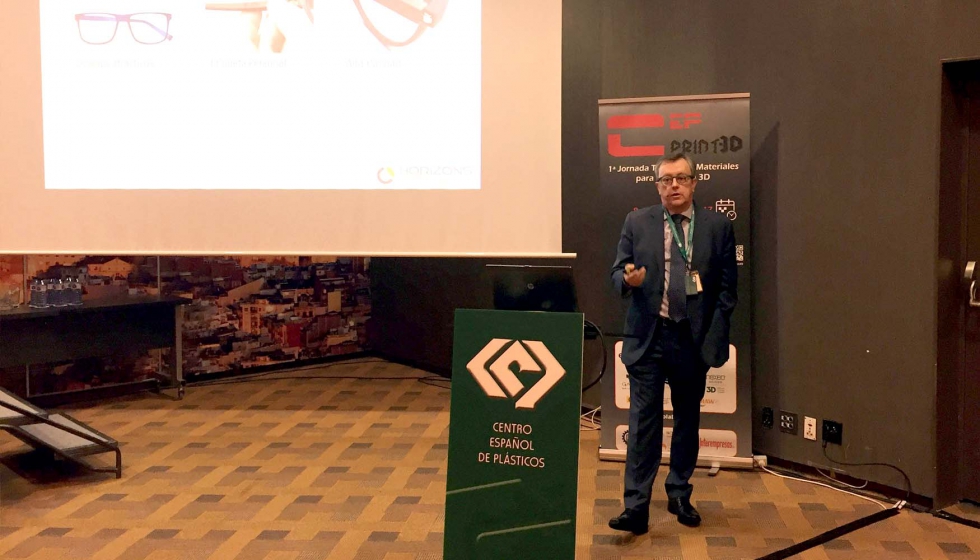
“Aunque el rapid prototiping está creciendo, el negocio real está en el consumo y en el producto final, en la fabricación de pequeñas series” señaló Juan-Carlos Düsteler. “Por ejemplo, con este sistema se podrán eliminar los stocks, que tienen como mínimo un 15% de obsolescencia y fabricar sobre la demanda. Hace posible hacer productos muy complejos que no se pueden hacer de la manera tradicional. Por lo tanto hay que pensar diferente cuando se diseña un producto para impresión 3D”, añadió.
Plataforma abierta de HP
Aleix Oriol, 3D Printing R&D WS and Materials Manager de Hewlett Packard explicó la tecnología HP Multi Jet Fusion, en base polvo. Oriol explicó que el objetivo de HP pasa por el prototiping, “porque entendemos que es un mercado con un tamaño limitado aunque irá creciendo y llegará a procesos cada vez más eficientes”, sino a la producción de pieza final, que evolucionará desde series cortas de alto valor añadido, después series cortas de menos valor añadido y eventualmente a series más largas. HP vende un producto de acabado rápido, porque “sabemos que uno de los limitantes de la manufactura 3D es la velocidad y el nuestro es un producto diez veces más rápido que equipos del mismo rango de precios. Su coste es aún caro sobre todo en series largas pero comparado con el coste por pieza de tecnologías similares en 3D hemos rebajado un 50% el valor de cada pieza”.
Aleix Oriol expuso a plataforma que la compañía ha desarrollado con el objetivo de poder llevar a cabo piezas con diferentes tipos de materiales, y evitar así la necesidad de trabajar con un material exclusivo. “Hemos apostado por un sistema abierto porque entendemos que para que haya renovación y reducción de coste, como necesita la industria, debe haber muchos fabricantes y mucha competencia en desarrollo de materiales. No queremos introducir una máquina que tenga un set de materiales solamente de HP, pero creemos que una máquina no debe estar solamente asociada a un material. Por eso apostamos por la diversidad de productores de materiales con su creatividad para crear materiales innovadores y más baratos lo que hará que esta industria despegue. HP, como jugador global, quiere que el mercado sea lo más grande posible”, señaló Oriol.
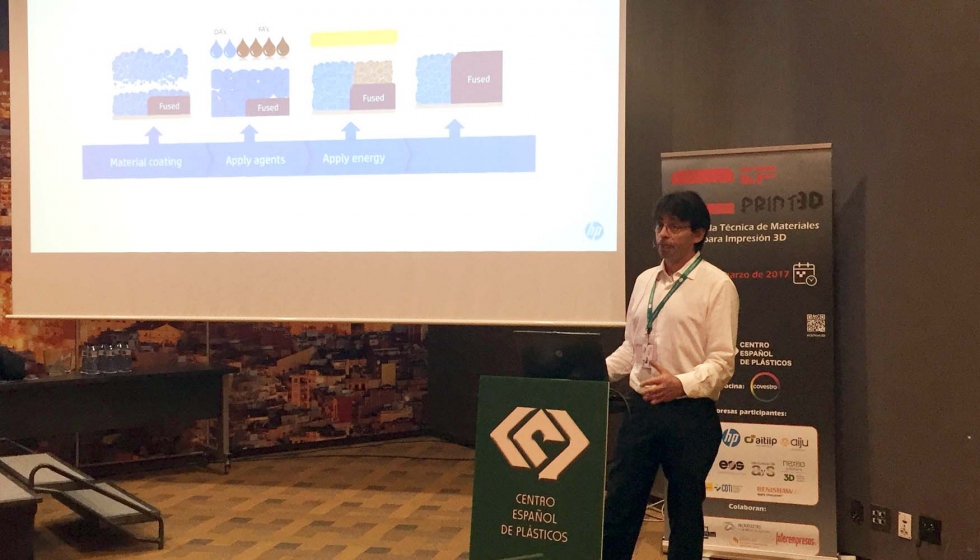
¿Y qué necesita HP de los materiales para que funcionen en su tecnología? “Necesitamos el material en polvo, que funda y consolide rápidamente, con una temperatura de fusión muy determinada, baja viscosidad de fusión y debe ser cristalinos. Los materiales amorfos tienen una manera de fundir que no es adecuada para este proceso”, explicó Aleix Oriol. A diferencia del proceso SLS, el MJF (Multi Jet Fusion) de HP no requiere materiales reactivos, por lo que no se degradan con el excesivo calor. Por ello, se puede reciclar un número infinito de veces hasta un 80% del material que no se ha fundido. Esta capacidad de reciclar material una y otra vez con un sistema automático de reciclaje que hace que la operación sea fácil y eficiente permite tener costes de material un 50% menos respeto a otras tecnologías. “A día de hoy, los materiales plásticos que se pueden utilizar con la máquina HP son los semicristalinos, aunque también dan resultado los plásticos convencionales de menor coste y también estamos desarrollando materiales de más altas propiedades. Gran parte de los materiales que se pueden utilizar con la tecnología HP, por lo creemos que hemos hecho una buena elección al elegir una tecnología que permita que los materiales funcionales más usados en la industria y más deseados desde el punto de vista de balances de propiedades mecánicas, dimensionales y cosméticas sea el adecuado”, concluyó Oriol.
Los centros tecnológicos a la vanguardia de la tecnología del 3D
La experiencia de los centros tecnológicos en la fabricación aditiva tuvo un especial protagonismo en la jornada. Gaiker-IK4, Eurecat, Aitiip y Aiju explicaron sus experiencias en el campo y cómo, desde sus respectivos centros, desarrollan nuevas tecnologías apoyando el mundo empresarial.
José Luis Gómez, director del Área de Plásticos de Gaiker-IK4, señaló que “los materiales determinan en gran parte el éxito de los procesos de impresión 3D”. Explicó que las tecnologías aditivas con mayor presencia en la industria son las que consumen materiales poliméricos y dentro de éstas, la más que es más familiar y accesible para los consumidores es la extrusión de filamento termoplástico. “Las compañías se pueden dotar a costes razonables de capacidad básica de fabricación digital, que se verá mejorada con la evolución de los equipos y con el desarrollo de nuevos materiales de impresión 3D con mejores prestaciones, nuevas funcionalidades y costes más reducidos”, en palabras de Gómez. A pesar de esto, las tecnologías de impresión 3D tienen limitaciones a la hora de implementarse con mayor intensidad en las empresas. “Todavía las piezas tienen cierta isotropía que generan ciertos defectos que necesitan un posprocesado para ajustar sus dimensiones finales o su calidad superficial. Todavía son procesos iterativos, que hacen que la pieza no salga bien a la primera. Faltan herramientas de simulación que permitan predecir el comportamiento de las piezas antes de fabricarlas. Son cosas que todavía están a nivel de I+D. Hay limitación respecto al tamaño de las piezas imprimidas, por la velocidad del proceso de fabricación se limitan el tamaño a pequeño o mediano. Se está intentando aumentar la velocidad de fabricación con lo cual esta limitación se irá superando. También está limitado a la fabricación de series cortas o unitarias. Por otro lado, el precio de los equipos y materiales todavía viene siendo elevado y también una gama de materiales limitada”, explicó. El planteamiento que las tecnologías aditivas no vengan a sustituir sino que complementen las otras tecnologías —substractivas o de conformado— es una forma más rápida de conseguir implementarla, porque, en el caso de los plásticos y composites, combina muy bien con los procesos de transformación. “En la medida que las tecnologías aditivas sean capaces de satisfacer las necesidades de la industria, se implementará más fácilmente. La industria necesita trabajar con materiales definitivos, por lo que es necesario que haya desarrollos en materiales. Deben estar caracterizados y homologados, para estar seguros de sus propiedades básicas de partida y que sus características sean uniformes de un lote a otro. Es necesario que sean fiables, accesibles y con un coste operativo que sea asumible por las empresas”, en palabras del director de Plásticos y Composites de Gaiker.
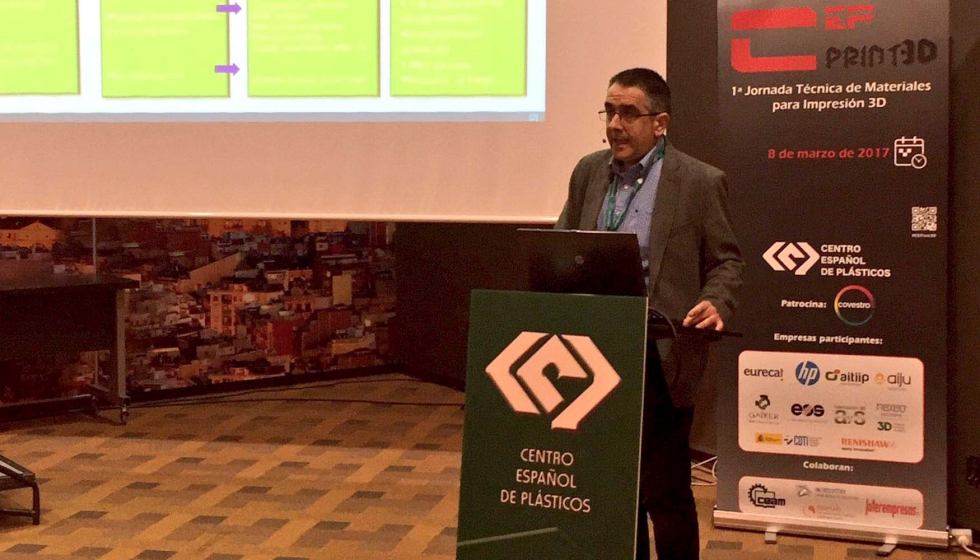
Por su parte, Xavier Plantà, director del Área de Tecnologías Industriales de Eurecat, explicó a los participantes de la jornada que el boom de la impresión 3D se inició cuando caducaron algunas patentes de esta tecnología, inventada en 1983, poniendo al alcance de la sociedad en general y de los investigadores en particular los pormenores de la fabricación aditiva. El impacto ha sido disruptivo tanto en la sociedad como en la industria, socializando y simplificando esta tecnología. “Hay muchas técnicas que funcionan de maneras distintas, con procesos distintos y materiales distintos y con piezas finales que se comportan diferente. Aquí radica uno de los principales problemas: el conocimiento exhaustivo de estas tecnologías”, explicó Plantà.
Eurecat apuesta por el desarrollo de sus propias patentes. Relacionadas con la impresión 3D tiene, de momento 3 patentes —una de metal, una de plástico y una de tecnologías combinadas— “pero también trabajamos en la mejora de los materiales y sobre todo con las empresas en aplicaciones finales”, contó Plantà. La tecnología de Eurecat dirigida al mundo de plástico es la UDM (Ultrasonic Deposition Modeling) que usa una fuente de ultrasonidos que funde un hilo de polímero. Para el metal, la fuente se basa en las microondas: Microwaves deposition modeling (MDM).
La tecnología combinada es CFIP —Continuous Fibre Injection Process—, basada en la combinación de fabricación de piezas y componentes por impresión 3D reforzándola con tecnología de infusión de resina cargada con fibras de carbono. “Esta tecnología abre mucho las posibilidades de uso porque combina las ventajas del la impresión 3D con las de los materiales compuestos reforzados con fibras estructurales. No tenemos limitación de tecnología 3D, aunque están más indicadas las tecnologías basadas en los materiales en polvo. La pieza 3D es el continente de esa función estructural, cosa que a fecha de hoy, con material compuesto es muy complicado fabricar estructuras tridimensionales con la complejidad del proceso. Se aplica el concepto de optimización topológica, reduciendo el peso y el precio del componente introduciéndole en su estructura las fibras de carbono colocadas adhoc en función del comportamiento mecánico que debe tener”, explicó Xavier Plantà. “Las tecnologías híbridas y la combinación inteligente de las tecnologías que ya existen pueden aportar valor en el desarrollo de productos a las empresas”, concluyó.
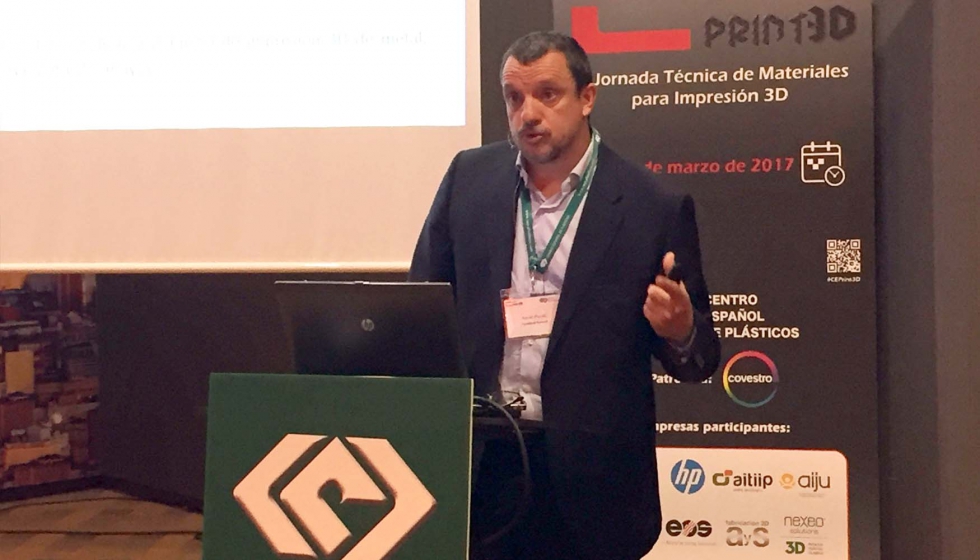
El tercer centro tecnológico invitado era Aitiip, cuyos representantes, los investigadores Berta Gonzalvo y Guillermo Vicente, explicaron cómo este centro zaragozano desarrolla tecnología propia a la vez que acompaña en la innovación a las empresas que lo solicitan. Entre los casos prácticos explicados durante la ponencia, destacó el de la moto desarrollada por el equipo EUPT Bikes de la Universidad de Zaragoza con elementos fabricados con impresión 3D y que los asistentes tuvieron la oportunidad de contemplar durante las pausas de la jornada en la zona de exposición. Con elementos estructurales —como chasis, basculante y subchasis— y elementos secundarios —estriberas, soporte de la dashboard, cárter de baterías— totalmente fabricados mediante la impresión 3D del material plástico Ultem 9085, esta moto fue merecedora del premio al mejor diseño, al segundo clasificado en pruebas dinámicas, y a la mejor moto eléctrica del certamen Motostudent 2016.
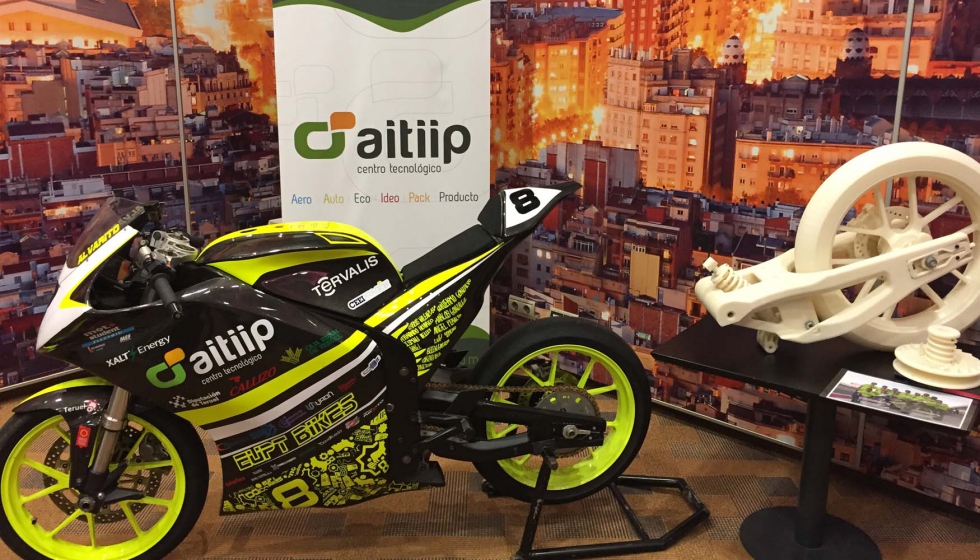
Aitiip expuso la moto con elementos impresos en 3D.
Por su parte, Aiju, Centro Tecnológico del Juguete ubicado en el ‘Valle del juguete’ en Ibi, Alicante, explicó en boca del técnico de Proyectos Francisco Varela cómo las nuevas tendencias del producto infantil y de ocio pasan por la personalización y por el desarrollo de productos que van a ser usados poco tiempo, novedades que reclaman nuevas metodologías de producción y nuevos modelos de negocio. Aiju ha entrado en el mundo de la impresión 3D con la fabricación aditiva de moldes y el desarrollo de filamentos para la impresión 3D. En este caso, Aiju ha desarrollado nuevas formulaciones de filamentos de FDM para obtener demostradores con distintas propiedades, por ejemplo físico-químicas, mecánicas (dureza, tracción), que cambian de luz y de color; filamentos conductores eléctricos; y filamentos con carácter antimicrobiano, que generan productos que son capaces de limpiar y eliminar bacterias y que están especialmente indicados para ludotecas y salas de hospital.
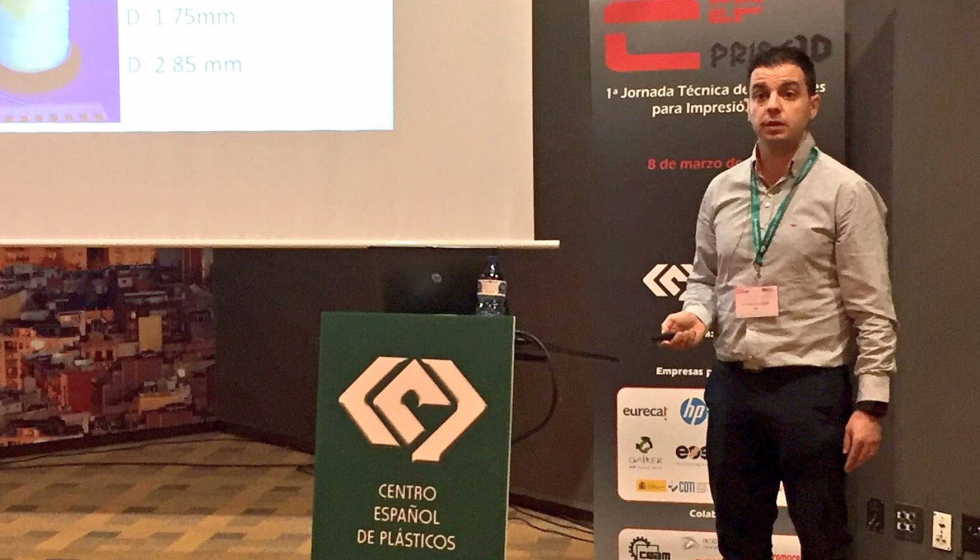
Francisco Varela también explicó la implicación del centro tecnológico en el proyecto i-BUS, “un nuevo modelo de negocio para la fabricación de productos personalizados”. Este proyecto abarca toda la cadena de valor, empezando por el niño (o familiares) que crea su propio juguete. La plataforma permite diseñar el juguete, ‘subirlo’ e indicar cuál es la mejor técnica para imprimirlo, quién puede ser el productor más cercano y con qué material. “Este proyecto producirá juguetes customizados, que se ajustan a lo que se quiere o necesita, evitando así producciones masivas”, explicó Varela.
Ninguna idea sin financiación
Durante la jornada, los asistentes también tuvieron la oportunidad de informarse sobre las herramientas de financiación del CDTI. María del Pilar de Miguel explicó cómo las empresas podían financiar sus procesos de innovación para dar forma a sus proyectos, crecer y aumentar su mercado, su competitividad e incluso internacionalizarse.
¿Tecnología abierta?
Otro caso de éxito expuesto durante la jornada fue el presentado por Josep Lladó, del departamento de Additive Manifacturing Catalunya de Análisis y Simulación Fabricación 3D. En este caso, se trataba de fabricación aditiva en el sector del molde, en concreto para la empresa Flexix que trabaja en el sector de la automoción. Josep Lladó explicó cómo el proceso consiguió agilizar el proceso de diseño de prototipos de moldes, aumentar la competitividad de la compañía, ofrecer series cortas a precios competitivos y especialmente mejorar el ROI de las inversiones. A través de la tecnología FFF con el equipo A2v2 de 3ntr, se consiguió un molde con una vida útil de 40 unidades, un 85% más económico y con un 87% más de rapidez en comparación con un molde tradicional de aluminio. “A día de hoy es factible realizar un molde con impresión 3D con series cortas y un coste muy inferior al sistema tradicional de fabricación de moldes. También es una tecnología suficientemente válida para hacer moldes prototipo. Lo importante es determinar qué tecnología y qué materiales son los indicados para desarrollar cada pieza y ponerla a su alcance”, explicó Lladó.

Héctor Mas, 3D Printing Manager de Nexeo Solutions, cerró la jornada reivindicando los sistemas abiertos en las tecnologías aditivas: “Estamos convencidos que la impresión 3D tendrá éxito en la producción real de cosas cuando sea una tecnología abierta. Los sistemas cerrados son máquinas muy buenas, que dan una gran calidad, pero la industria estará convencida de usar la impresión 3D cuando sea abierto”. Según Mas, los sistemas abiertos cambiarían la cantidad de materiales disponibles y la competencia en precios y costes, además de otorgar diferenciación respecto a la competencia. “Los sistemas cerrados donde se paga a alguien que da un servicio o un producto que funciona muy bien pero si la competencia compra la misma máquina y el mismo material y entrega el mismo producto, no hay valor añadido. La industria se moverá hacia la impresión 3D cuando sea abierto y eso será una revolución industrial muy grande”, señaló Mas.
Mas también recalcó la importancia de que en impresión 3D se usen “los plásticos de siempre” y que no todo depende del material usado: “El objetivo es que la pieza funcione y esto depende no solo del material, sino también de hardware y el software”. Además, vaticinó que “entre el próximo año y año y medio se tendrá disponibilidad comercialmente de casi todos los materiales, sin restricciones importantes”.
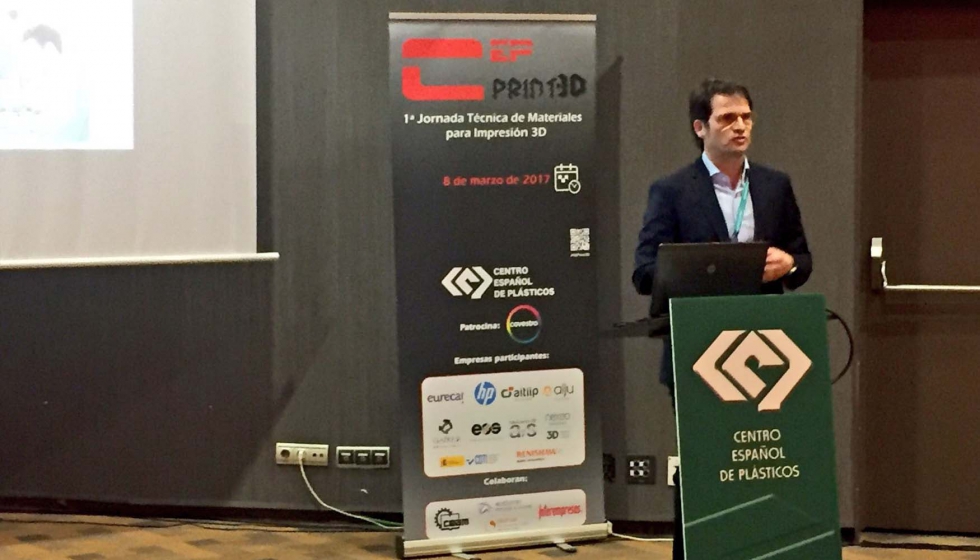
Mesa redonda de expertos
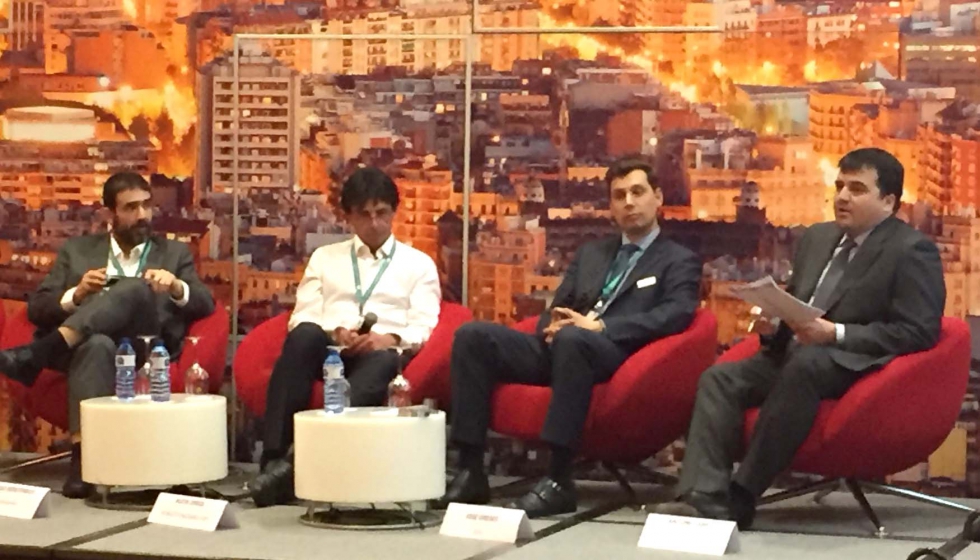
De izq. a dcha.: Íñigo Bereterbide, Aleix Oriol, José Greses y Antoni Camí, durante la mesa redonda.
He aquí algunos de los temas tratados:
Fabricación masiva con fabricación aditiva
Íñigo Bereterbide: El concepto de fabricación masiva debe ser diferente al concepto que tenemos ahora mismo. No podemos pensar hoy por hoy, con el estado actual de la tecnología, en fabricación aditiva de millones de piezas de valor añadido muy bajo de céntimos de euro. En un futuro serán miles de piezas anualmente pero debemos olvidarnos del rango de cientos de miles o de millones. A partir de ahí, cada sector deberá de definir sus rangos de masivo, pero sí que es cierto que los procesos de fabricación aditiva deberán dar un salto y cada vez ir ganando más terreno e ir aumentando su capacidad de fabricación, pero para ello la parte de diseño, de procesos, etc. tendrá que adaptarse para que la tecnología logre dar ese salto”.
Aleix Oriol: “El término ‘fabricación masiva’ es un poco truculento en el sentido que la gente se imagina 30.000 piezas exactamente iguales, muy estandarizadas y este no es el objetivo de la impresión 3D. Sus objetivos son conseguir otros beneficios, propiedades especiales, conseguir liberar peso, etc. Lo que sí es verdad es que cuando se consigan bajar costes, el punto de corte de cuánto cuesta hacerlo en aditivo y cuánto cuesta hacerlo en moldes va ir bajando. Lo fundamental a tener en cuenta es que hay aplicaciones que no se pueden hacer con 3D, y por ahí me inclino más a hablar de ‘pieza final’ en 3D. La fabricación masiva llegará, pero tomará más tiempo, cuando procesos de ignición y materiales estén optimizados para volúmenes altos pero en según qué geometrías que también se pueden hacer en 3D pero que no tienen ninguna característica especial, se seguirán haciendo con métodos tradicionales.
Sector dental como ejemplo de fabricación masiva
I.Bereterbide: “El sector dental fabrica miles de piezas al día, todas costumizadas y personalizadas. No hay dos piezas iguales. El sector médico y sobre todo el dental es el sector con mayor implantación y más extendida la tecnología de impresión 3D”.
José Greses: “Nuestros clientes en España del sector dental producen (todos juntos) unos 7.000 dientes al día todos diferentes. Es un proceso complejo, con un volumen elevado y cada pieza es diferente y es un proceso que está certificado. Es un sector clave y fundamental para la fabricación aditiva metálica. Nuestros clientes no solamente fabrican los dientes tal y como salen de máquinas sino que luego les aplican otros procesos de mecanizado, terminaciones especiales que dan un valor añadido que van mucho más allá de lo que es una simple fabricación por sinterizado”.
Implementación real de la fabricación aditiva
J. Greses: “Cuando alguien quiere implementar fabricación aditiva en sus procesos debe tener en cuenta tres pasos, y si uno de los pasos no está implementado probablemente no tendrán éxito. El primer paso es el diseño. Si no tienes un diseño optimizado para fabricación aditiva, no va a funcionar el proceso. El segundo paso es la fabricación aditiva en la máquina correcta que de las propiedades finales que el cliente requiere. Y el proceso final, tan fundamental como los dos primeros, es el posprocesado, el ‘¿cómo termino esta pieza?’. Siempre hay que tener estos tres procesos para que la implementación tenga éxito.
Certificaciones de piezas
Antoni Camí: “Las tecnologías de fabricación aditiva están cogiendo una madurez que no tenían, gracias a la publicidad y a que ahora hay más interés desde los diferentes sectores. Pero ¿cómo certificamos que una pieza producida está bien fabricada? No sólo directamente desde la empresa que te la vende sino con sistemas parecidos a la automoción, desde los proveedores de estas piezas”.
I.Bereterbide: “El proceso de certificación es básico para que las empresas cojan confianza que esta tecnología es una tecnología válida para producir pieza final. Con un prototipo cualquiera se atreve pensando ‘esto no va a salir de mi casa’ y si pasa algo se asumen las consecuencias. Cuando vendes algo producido con esta tecnología te responsabilizas de su calidad, con lo cual hay muchos fabricantes que quieren tener la seguridad que va a estar certificado de alguna manera. Es verdad que las certificaciones actuales no están muy adaptadas al 3D y muchas de ellas son específicas para otro tipo de procesos y sería necesario desarrollar otras. Pero algunas sí que son posibles adaptarlas de manera relativamente fácil, y cuanto antes se haga este proceso, mejor. Esta confianza y esta garantía de la certificación permite a los usuarios finales tener la seguridad que aunque se ha hecho con 3D, se pueden fiar de sus prestaciones”.
J.Greses: “Las certificaciones dependerán de las aplicaciones. Por ejemplo, las aplicaciones del sector aeronáutico, en Europa, Airbus debe demostrar a EASA (European Aviation Safety Agency) que esa pieza funciona. Eso no es diferente a la certificación que tiene que pasar una pieza que se ha hecho por fundición o mecanizado. Simplemente hay más desconocimiento del proceso de fundición, pero no significa que sea un proceso de especificación diferente. Es el mismo pero llevará más tiempo porque se tendrá que hacer más pruebas. Al mismo tiempo, abre nuevas perspectivas porque cuando se hace una pieza por colada no se tiene ni idea de lo que hay dentro, a no ser que se hagan rayos X o tomografías. Sin embargo, con esta tecnología aditiva se puede monitorizar punto a punto, capa a capa, las propiedades y qué ha pasado durante el proceso y con eso se abren nuevos retos respecto al manejo del volumen de datos”.
Impresión 3D de polímeros
A.Oriol: “En pieza final, la impresión 3D en polímeros ha empezado más tarde pero ha acabado llegando. Las especificaciones son diferentes porque el material es diferente pero va a llegar a todas las industrias”.
J.Greses: “Las aplicaciones en plástico fueron las primeras que se utilizaron en aeroespacial hace 20 años. Boeing en su F18 tiene 32 ó 34 piezas implementadas y desde EOS estamos participando en la ejecución de piezas que están dentro del avión, y la parte metálica ha sido posterior. En aeronáutica esta tecnología encaja muy bien porque son series relativamente cortas”.
Antoni Camí: “No se trata de preguntar ¿qué máquina debo comprarme? La pregunta correcta es ¿qué quieres hacer? ¿Cuál es la aplicación?, y entonces buscar la herramienta para conseguir este fin. Hay que conocer esta tecnología, conocer cuáles son las diferentes siglas, nomenclaturas de aplicaciones que puedes tener y a partir de ahí ver cómo lo puedes aplicar a tu proceso.
¿Comprar o subcontratar? El bureau de impresión
J.Greses: “No hace falta comprarse una máquina. Hay muchas empresas que ofrecen servicios de calidad. Lo mejor es empezar subcontratando estos servicios y fijar el modelo de negocio, aprender a cómo rediseñar un producto. Hay que interiorizar estos procesos y pensar de manera diferente dentro de la empresa y poco a poco, cuando sea más rentable comprar una máquina, ese es el punto de comenzar a implementarlo. Es un proceso lógico y que funciona muy bien”.
I.Bereterbide: “El proceso lógico es primero determinar las aplicaciones que la tecnología tradicional no funciona. Se empieza subcontratando, mirando las diferentes tecnologías, comparando los materiales accesibles, y después hay que hacer la inversión en la maquinaria. Hay que tener persistencia pero no impaciencia. La vía de la subcontratación es muy válida y nosotros la recomendamos a determinados clientes, o bien por su volumen de negocio o bien por otros motivos no van a ser un cliente potencial y nada justifica la adquisición de una máquina. En Renishaw hemos ido un paso más allá y con clientes en que sí pueden tener un potencial más grande de desarrollo a futuro hemos creado una red que se llama ‘Solutions Center’. Por la vía de la subcontratación adquieres ciertos conocimientos pero no se aprende los entresijos de toda la fabricación. Con ‘Solutions Center’ damos un servicio que incluye otras cosas como por ejemplo, si se hace una inversión para adquirir una máquina, que sea capaz de utilizarla con el apoyo de técnicos de materiales, de técnicos de diseño que orientan a los diseñadores de la empresa, etc.”.
A. Camí: “En impresión 3D se están repitiendo patrones que ya han sucedido en el mercado en otros sectores como la impresión convencional. En este mercado, desde el inicio de las grandes empresas, aparecieron otras que ofrecían sus servicios como bureau de impresión, en algunos casos cercanas a la ingeniería, que se articulan como una especie de bisagra entre la adquisición de la máquina y tener acceso a estas tecnologías que requieren una inversión más elevada”.
A. Oriol: “Hay algunas empresas que no quieren sacar sus diseños fuera porque son muy celosos de que sus piezas sean hechas por otros. Los proveedores de impresión, tienen la ventaja que, por un lado, son más expertos en las diferentes tecnologías y podrán asesorar; y por otro, tienen la capacidad de hacerlo en menos tiempo y esfuerzo que lo haría su cliente”.
Competencia dentro del sector
I. Bereterbide: “El hecho que unos monstruos industriales como HP o General Electric hayan dado el salto para ‘colarse’ en el mundo de la fabricación aditiva demuestra que es una tecnología con un recorrido muy grande y un potencial bestial”.
J. Greses: “Toda la gente que se está incorporando en el camino lo que está haciendo es sumar. Además, que se incorporen con poliamida 12 es señal que esto está funcionando y que el potencial y el recorrido es mucho mayor. Y todos los que se incorporan nos empujan a hacerlo mejor”.
A. Oriol: “Durante los primeros años de una tecnología, las empresas no competimos tanto entre nosotros sino con métodos de fabricación diferentes. A todos nos interesa que ésta sea percibida como una tecnología válida. Entre los fabricantes no competiremos exactamente por los mismos clientes ni las mismas aplicaciones porque cada tecnología tiene su foco y sus puntos ideales de funcionamiento. Lo que queremos es que la gente se dé cuenta que hay muchas posibilidades, que las explore y vaya identificando cuál de los fabricantes de máquinas se adapta mejor a sus necesidades. Mientras el mercado siga creciendo a ritmos altos no nos vamos a ‘pelear’ entre nosotros porque todos tendremos mejores resultados el año que viene que este año. El mercado no está maduro, no es el caso ni lo será en los próximos 10 ó 20 años”.
Proveedores de materiales
J. Greses: “En las máquinas EOS siempre se ha podido implementar el material que hemos querido, tanto en metal como en plástico, sin problema. El problema es conseguir un material que funcione, por ejemplo, una poliamida con una granulometría específica, con control de calidad, etc. Esto lleva un proceso y es una inversión importante”.
A. Oriol: “Como fabricantes, lo que tenemos que comprobar cuando entran nuevos materiales es que la seguridad del usuario está asegurada y que la fiabilidad del equipo está garantizada. A partir de ahí, las propiedades, obviamente, deben cumplir un mínimo porque está en juego la imagen del fabricante. Si el fabricante nos garantiza unas propiedades y aplicaciones, entendemos que el ingenio y la capacidad de los fabricantes para encontrar un material que abra aplicaciones nuevas son bastantes grandes, por tanto debería permitirse esta entrada. Obviamente, con los parámetros de control que permitan asegurar que la fiabilidad de la máquina y su robustez sea suficiente como para admitir ese material”.
I. Bereterbide: “Los materiales deben cumplir ciertas características pero cuando hablamos de un proceso repetitivo de una pieza, otro tema importante es que los proveedores de los materiales, a pesar de ser un único proveedor, sean fiables en la repetitibilidad de los lotes, porque se puede dar el caso que de un lote a otro varía algunas propiedades y las fabricaciones no sean exactamente iguales. No es tan sencilla la intercambiabilidad de proveedores de polvo ni la libertad de decisión de compra de materiales. Sí que se puede hacer, pero en este caso el proveedor y el usuario de la tecnología que quiere comprar a distintos proveedores se tendrán que asegurar previamente a lanzar los trabajos, a parte de una investigación previa de cada lote que recibe cumple esas expectativas”.
Nuevos materiales poliméricos y metálicos
J. Greses: “En los últimos 3-4 años ha habido un gran avance y expansión de materiales y vamos a ver un ritmo mayor en los próximos años. Pero a día de hoy, lo que funciona es la poliamida 12 y los clientes se tienen que adaptar a usar este material.
A. Oriol: “La poliamida 12, dentro de sus limitaciones, da un abanico suficientemente grande de aplicaciones. Si no ha habido más innovación con materiales diferentes es porque muchas aplicaciones se pueden cubrir bien con esta familia de materiales y da propiedades de acabados suficientes. A medida que se vayan incorporando aplicaciones y se vayan viendo maneras diferentes de hacer las cosas la evolución de los materiales seguirá ese ritmo”.
I. Bereterbide: “Las limitaciones de materiales con parámetros establecidos son quizás mayores en el plástico porque todos los fabricantes tenemos un rango de metales parametrizados que podemos garantizar que funcionan correctamente. Hay muchos clientes que están desarrollando sus propios parámetros, o bien a través de centros tecnológicos y universidades, o bien directamente ellos. Es un reto para el mundo de los fabricantes de materiales la preparación de aleaciones específicamente para esta tecnología.
Inputs para el futuro
Durante la jornada, varias voces hicieron sus predicciones sobre el prometedor futuro de esta tecnología y la evolución de sus materiales. Veamos algunas:
- Juan-Carlos Düsteler, Horizons Optical: “Según un estudio de Siemens, en los próximos 5 años imprimir en 3D será un 50% más barato y se multiplicará por 4 la velocidad”.
- Aleix Oriol, HP: “En cuanto al mercado, en 2014 era relativamente reducido pero para 2020 se espera una tasa de crecimiento compuesto del 30% anual. Un mejor rendimiento y calidad de las impresoras 3D; más materiales disponibles y mejor adecuación a los diferentes verticales; y menor coste de los materiales mejorando relación de coste con los métodos de producción tradicional impulsarán este crecimiento”.
- Aleix Oriol, HP: “Pensad en el 3D como mercado de futuro. Es verdad que tomará su tiempo y que el 3D no va a sustituir totalmente a los moldes, sino que simplemente los va a complementar; pero pensad en todas las posibilidades que da y que esto solo irá a más en el futuro. Por tanto, id pensando cómo crear nuevos materiales, cuáles serán más necesarios, cómo hacerlos más baratos y más innovadores, y sobre todo cómo se van a diseñar las piezas del futuro para que vuestros materiales se adapten a estas aplicaciones”.
- José Luis Gómez, Gaiker-IK4: “En los próximos 5 años, el 38% de las empresas contemplan la utilización de las tecnologías de impresión 3D en sus instalaciones complementando a sus tecnologías de fabricación”.
- Xavier Plantà, Eurecat: “La impresión 3D abre un mundo de expectativas y de oportunidades sólo limitada por nuestra imaginación”.
- Héctor Mas, Nexeo Solutions: “Cada vez hay más materiales y cada vez se desarrollarán más. El gran cambio está sucediendo ahora y es el mejor momento para meterse en este mundo”.