Medición de oxígeno disuelto en centrales de energía
Química del agua y oxígeno disuelto
Según las recomendaciones de la VGB (Asociación de empresas Eléctricas y Generadoras térmicas en Europa) y el EPRI (Instituto de investigación de la energía eléctrica en EE UU), la evaluación de la concentración de oxígeno debe realizarse junto al análisis de pH y la pureza del agua. El alto grado de pureza del agua hace posible que la concentración de oxígeno aumente y el pH disminuya, mejorando así la protección de las tuberías de acero. Esto se debe a la oxidación de la capa protectora de magnetita a hematita. La hematita presenta una menor solubilidad y una estructura cristalina más fina, por lo que sella la porosidad de la magnetita.
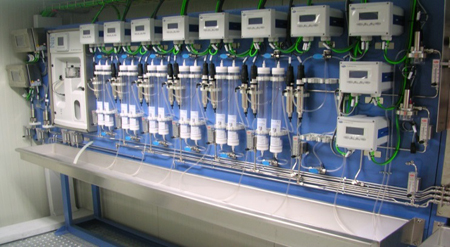
Rack Iberfluid compacto en formato accesible frontal, incluyendo analizadores de O2 LDO, Na, conductividad catiónica, etc.
Cuando no se puede conseguir una gran pureza, hay que recurrir al aumento de pH con concentraciones bajas de oxígeno como medida de protección. Pero para que la concentración de oxígeno sea muy baja hay que añadir agentes reductores muy potentes (atrapadores de oxígeno) con los que hay que ser muy cuidadoso.
En función de los componentes químicos que se apliquen al agua de la planta, el oxígeno debe mantenerse a un nivel de concentración bajo (AVT) o dentro de un rango específico (OT).
Las plantas que utilizan un tratamiento oxigenado (OT) suelen funcionar con agua de alimentación de calderas con una concentración de oxígeno de entre 50 y 200 ppb, de modo que los instrumentos para medición de oxígeno deben seleccionarse para favorecer una vida útil prolongada. En estas circunstancias, la nueva tecnología de oxígeno luminiscente (LDO) satisface esta necesidad con hasta un año de funcionamiento continuado sin necesidad de mantenimiento del sensor.
Por otro lado, las centrales de energía que optan por un tratamiento con sustancias altamente volátiles (AVT) de la química del agua con ciclos de vapor a alta presión normalmente mantienen la concentración de OD en el agua de alimentación de calderas por debajo de 5 ppb y la concentración del condensado por debajo de 20 ppb.
Por consiguiente, los instrumentos de medición de oxígeno deben tener un alto grado de sensibilidad. Con estos supuestos, los sensores de tipo LDO se pueden utilizar en la mayoría de los casos, pero los electroquímicos continúan siendo los sensores de referencia cuando la concentración de oxígeno es inferior a 1 ppb.
Estos son los distintos regímenes de tratamiento químico del agua:
- AVT: Régimen de acondicionamiento en el que solo se añaden agentes alcalinos volátiles al agua de alimentación.
- AVT(R): Condiciones reductoras (agente reductor añadido) recomendado para las unidades con aleaciones de cobre.
- AVT(O): Condiciones de oxidación (oxígeno residual presente). Solo aplicable a unidades con todos los elementos metálicos ferrosos.
- OT: Régimen de acondicionamiento donde se añaden agentes alcalinos y oxígeno al agua de alimentación. Solo aplicable con todos los elementos metálicos ferrosos y agua de alta pureza.
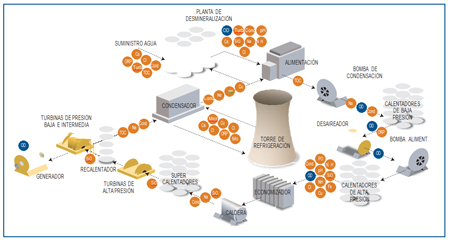
Normalmente, el análisis continuo del oxígeno disuelto se lleva a cabo en el agua de alimentación de calderas, en la salida del desaireador y en el punto de descarga del condensado.
Medición del oxígeno disuelto en el refrigerante del estator del generador
El tratamiento químico del agua del refrigerante del estator es diferente al del ciclo principal de agua porque la corrosión por sí sola no es la causa principal de los problemas que se dan en los sistemas de refrigeración del estator, sino la acumulación de depósitos en zonas críticas.
El oxígeno disuelto y el pH dan lugar a regímenes de tratamiento del agua distintos, con efectos diferentes sobre la generación y liberación de óxido de cobre.
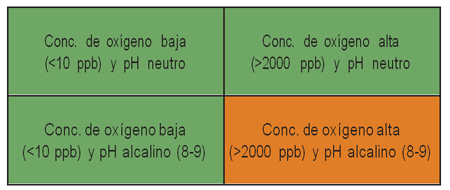
Hay cuatro opciones de tratamiento del agua del refrigerante del estator:
- Concentración de oxígeno baja y pH neutro. Esta opción de tratamiento se da en el 50 % de los sistemas de refrigerante del estator. Una fina capa de óxido cuproso pasivadora protege los tubos de cobre.
- Concentración de oxígeno baja y pH alto. Si se aumenta el pH del agua del estator a 8-9, la respuesta corrosiva durante las transiciones del oxígeno se reduce drásticamente.
- Concentración de oxígeno alta y pH neutro. El objetivo es mantener en todo momento un nivel elevado de oxígeno disuelto en el agua de refrigeración. Se calcula que el 40 % de los sistemas de refrigeración del estator basados en agua utilizan estos parámetros. Con este régimen, se forma CuO sobre el cobre que se adhiere firmemente a la superficie y crea una capa pasivadora sobre el metal. Esta capa suele ser más gruesa que la de CuO que se forma en condiciones de poco oxígeno.
- Concentración de oxígeno alta y pH alto. Esta opción no se recomienda porque aumenta la probabilidad de corrosión en el soporte de la barra.
Instalación típica
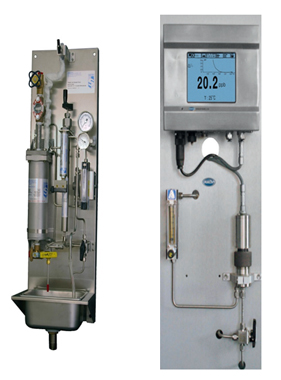
En la imagen superior (izda.) se muestra un panel Sentry de acondicionamiento de muestra según ASTM D5540, conocido como rack ‘primario’, a la salida del cual se conecta el rack de analizadores, tal como el panel de medición de O2 disuelto (dcha.). En éste, la muestra entra en el centro de la cámara de flujo a través de una válvula con tres vías. Esta válvula permite la interrupción del flujo de muestra, además del purgado de la vía de entrada. Todas las vías están unidas mediante conectores que evitan cualquier riesgo de entrada de aire. Aguas abajo de la cámara de flujo se coloca un caudalímetro con válvula reguladora. Existen varias razones para utilizar esta configuración:
- Si la muestra de agua contiene una concentración elevada de otros gases disueltos como, por ejemplo, hidrógeno (H2), en el caso del agua de refrigeración de los reactores de agua presurizada (PWR), mantiene la presión y evita la desgasificación antes de realizar la medición.
- La otra razón es que así se elimina el riesgo de contaminación de aire que puede generarse por el envejecimiento del caudalímetro, concretamente de la junta de la válvula reguladora.
El sensor debe montarse en vertical sobre la válvula de entrada y la cámara de flujo, tal como se muestra en la imagen. Con esta distribución, las burbujas de gas que entran en la cámara pasan rápidamente por el sensor hasta el puerto de salida.
Si se presta especial atención al diseño del sistema de muestreo, se pueden evitar los problemas de muestreo más frecuentes.
Uno de los problemas de muestreo más comunes son las discrepancias entre el analizador en continuo y el dispositivo portátil. Normalmente este problema se genera por una fuga en el tubo de la muestra que “suministra” una cantidad constante de oxígeno a los demás tubos. La reacción típica es una reducción de la lectura de oxígeno cuando aumenta el caudal de la muestra.
Calibración y validación de los dispositivos de oxígeno en continuo
Los dispositivos portátiles actuales como el analizador de oxígeno Orbisphere 3100 pueden servir de herramienta de calibración o validación en continuo. Primero hay que calibrar el dispositivo portátil conforme a un patrón trazable en el laboratorio y después se puede utilizar como referencia portátil en toda la planta. Gracias a que los analizadores en continuo tienen funciones de calibración directa, este proceso no le llevará más de unos segundos con la unidad portátil conectada a la misma ubicación en que se tomaron las muestras. En este caso, la trazabilidad y el vínculo a los patrones oficiales externos queda totalmente cubierta.
La tecnología LDO para la medición del oxígeno disuelto ofrece la ventaja de la estabilidad a largo plazo, incluso cuando el dispositivo de medición se encuentra en modo de espera. Aunque el dispositivo no se utilice durante semanas o meses, las propiedades metrológicas de la referencia de trabajo no se ven alteradas.
Por otra parte, el analizador de oxígeno portátil Orbisphere 3655, con sensor electroquímico, es el instrumento de referencia absoluta para los niveles inferiores a 5 ppb, con una señal residual del sensor mínima de 0,1 ppb.
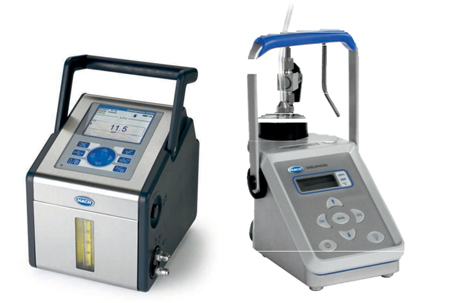
La solución de Hach Lange: el sensor Orbisphere K1100
Los sensores electroquímicos tradicionales presentan un nivel de deriva importante en solo unos meses, por lo que requieren tareas de calibración periódicas y bastante mano de obra. Debido a su tecnología luminiscente, el sensor Orbisphere K1100 está diseñado para que la deriva sea mínima, lo que lo convierte en el sensor más estable y con el mayor intervalo de calibración del sector.
Como no hay que sustituir membranas, no hay que reponer la solución electrolítica ni manipular sustancias químicas peligrosas, podemos decir que el sensor K1100 no necesita prácticamente mantenimiento, tan solo hay que dedicarle un par de minutos al año.
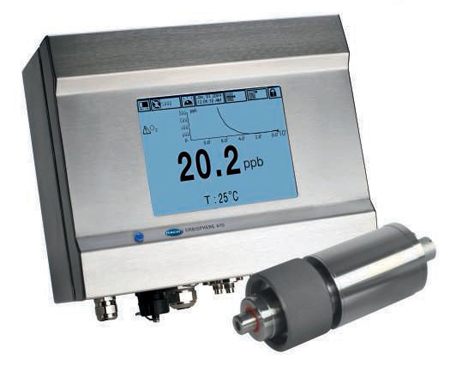
El sensor K1100 es compatible con las cámaras de flujo de 28 mm Orbisphere que se utilizaban antes con los sensores electroquímicos, de modo que no hay que recurrir a cambios de ingeniería para soldar, añadir ni comprobar nuevas conexiones. La instalación perfecta.
Con la tecnología LDO no hay que esperar a que se estabilice la unidad, una ventaja adicional para las plantas a pleno rendimiento que exigen tiempos de respuesta rápidos en todos los equipos.
La frecuencia de medición se puede configurar hasta llegar a periodos de una duración insuperable en los que no es necesario repetir la calibración.
Referencias
[1] Dooley, R. B. Power Plant Chemistry 2002, 4(6), 320.
[2] David G. Daniels, Forgotten water: Stator cooling water chemistry, M&M Engineering, Power, Dec 15, 2007.
[3] Dunand, F. et al.; LDO sensor to monitor power plant water and team cycles – PPChem 2006, 8(10).
[4] Optische Sauerstoffmessung in Kraftwerken, VGB Powertech, p119-124, 9, 2012.