Control de calidad de husillos rectificados mediante la técnica no destructiva de emisión magnética de Barkhausen
Con el fin de identificar la sensibilidad de la técnica y del sistema de medición de EMB, diseñado e implementado por los autores, se prepararon varias muestras con distintos tratamientos térmicos de temple por inducción para obtener variaciones de la capa endurecida. Adicionalmente se variaron las condiciones de rectificado con objeto de obtener muestras con distinto nivel de quema. Los parámetros derivados de las medidas de EMB se compararon con las medidas de microdureza realizadas a distintas profundidades tras el temple por inducción y el proceso de rectificado.
Los resultados obtenidos demuestran que diversos parámetros derivados de la señal EMB pueden utilizarse tanto para identificar las variaciones de dureza producidas por los distintos tratamientos de temple por inducción como para detectar las disminuciones de dureza producidas por las quemas de rectificado, permitiendo determinar unos umbrales para control de calidad que aseguren el correcto temple y rectificado de los mismos.
1. Introducción
Dentro de los programas marco europeos para el desarrollo de nuevas tecnologías y procesos que contribuyan a un transporte aéreo más eficiente y más respetuoso con el medio ambiente y así cumplir los objetivos marcados por el Consejo Asesor para la Investigación e Innovación Aeronáutica en Europa (ACARE por sus siglas en inglés de Advisory Council for Aeoronautics Research in Europe) se está apostando en las aeronaves por la sustitución de los sistemas de actuación hidráulicos por sistemas de actuación electromecánicos, siendo estos últimos mucho más ligeros, permitiendo un mayor seguimiento a su funcionamiento y en consecuencia facilitando también su mantenimiento.
Tratándose de aplicaciones críticas, los clientes requieren que todos los husillos que se van a implementar en los actuadores electromecánicos de las aeronaves estén certificados.
En este contexto, Korta se planteó como objetivo el conseguir la certificación de husillos a bolas para posicionarse en el mercado aeronáutico con un producto de alto valor añadido que cumpla con todas las especificaciones requeridas por las rigurosas normativas reguladoras de este sector. En los requerimientos técnicos del cliente se especifica que el 100% de los husillos a bolas deberán ser inspeccionados mediante un ensayo no destructivo que asegure la no pérdida de dureza debido al rectificado de los mismos y que la capa endurecida tras el temple por inducción sea correcta.
En un principio Korta optó por el proceso de etching (ataque químico de Nital) para certificar la dureza de la rosca, pero después de diversas pruebas se comprobó que el baño que se aplica durante dicho proceso puede eliminar varios micrómetros de material haciendo que el husillo no cumpliese las tolerancias geométricas exigidas, por lo que dicho proceso se consideró como destructivo y además no permitía distinguir las quemas en este material ni asegurar su capa endurecida. Se consideraron otras opciones para el análisis no destructivo de los husillos y finalmente se optó por diseñar e implementar un sistema de análisis del ruido de Barkhausen (BNA por sus siglas en inglés de Barkhausen noise analysis) que permitiera detectar las posibles pérdidas de dureza debido a quemas producidas durante el rectificado y que certificara que la profundidad de la capa exterior endurecida mediante temple estuviese dentro de un rango dado. La técnica de BNA es una técnica electromagnética que consiste en el análisis de la señal de emisión magnética de Barkhausen (EMB) que produce el movimiento de las paredes que separan los dominios magnéticos en un material ferromagnético. Este movimiento se origina cuando se aplica un campo magnético de amplitud variable en el tiempo sobre la muestra. Globalmente, el movimiento de las paredes de dominio es más fácil en un material más blando mecánicamente (con menor dureza) y esto provoca un incremento de la amplitud de la señal de EMB y que el máximo valor de la señal se obtenga a menores valores del campo aplicado [1, 2].
Para el desarrollo del sistema de BNA, Korta ha colaborado con el centro tecnológico Ceit-IK4, que cuenta con amplia experiencia en la implementación de sistemas de ensayos no destructivos.
El presente artículo se ha estructurado de la siguiente forma: primeramente se presenta el estudio de calibración necesario para identificar las características de los husillos exigidas por el cliente; a continuación se explica el sistema automático desarrollado para aplicar la técnica de BNA en planta, posteriormente se muestra un ejemplo de un defecto detectado durante la producción y finalmente se presentan las conclusiones de este trabajo.
2. Desarrollo de un sistema de certificación de los husillos a bolas
El objetivo técnico del proyecto que se presenta fue diseñar e implementar un sistema de ensayo no destructivo que a través de la técnica de BNA posibilite la detección de quemas que pueden producirse durante el rectificado de husillos a bolas y el control de la capa templada de dichos husillos y, que, por lo tanto, permita cumplir las especificaciones técnicas del cliente.
2.1 Pieza a analizar
La zona roscada del husillo que hay que analizar tiene una longitud variable.
2.2 Especificaciones
El sistema de medición no destructivo para ser válido y poder ser implementado en planta debía cumplir los siguientes requisitos:
- Asegurar una capa endurecida determinada en la rosca.
- Detectar una bajada en dureza por debajo de 58 HRC o una subida en dureza por encima de 61 HRC en la superficie de la rosca.
- Realizar medidas en continuo en toda la longitud útil de la rosca sin tener efectos de borde.
- Medir husillos de dos longitudes distintas con el mismo sistema.
2.3 Calibración del sistema de BNA
Se realizó un estudio de calibración completo del sistema de BNA mediante el análisis de las variaciones que se producen en la señal de EMB debido a los cambios en el espesor y dureza de la capa templada, y a las quemas de rectificado.
2.3.1 Metodología de estudio
Para la calibración del sistema de BNA se fabricaron varios husillos provenientes de barras de dos temples por inducción diferentes, que se rectificaron de forma correcta (OK) e incorrecta (NO OK) modificando la velocidad de avance, la profundidad de pasada y la cantidad de aceite empleado como refrigerante con el objetivo de producir quemas de distintas intensidades. En la tabla 1 se detallan los temples y el estado de los husillos analizados.
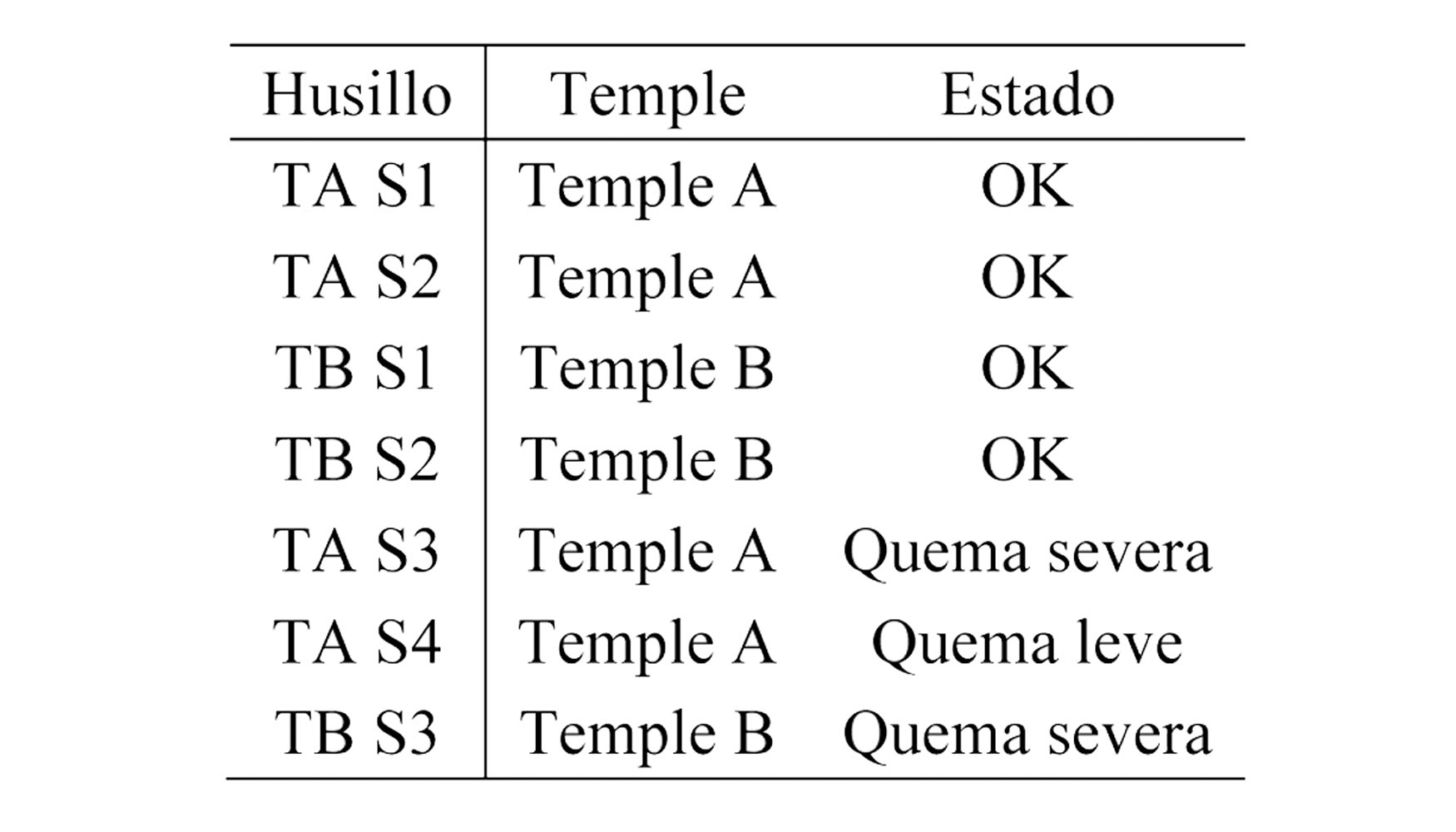
Posteriormente se procedió a realizar las medidas de EMB en estos husillos. Para la realización de las medidas se empleó un sistema de medición de BNA de laboratorio consistente en un dispositivo de medición de EMB, un cabezal excitador/sensor y un PC. El sistema de medición y el cabezal excitador/sensor se diseñaron específicamente para poder realizar medidas en estos husillos en continuo a lo largo de toda la longitud útil de su rosca en Ceit-IK4. Se usó una magnetización a baja frecuencia cuya amplitud era suficiente para saturar las muestras. Se miden el campo magnético tangencial (Ht) y la señal EMB en la superficie del husillo mediante un sensor de efecto Hall y una bobina sensora respectivamente en toda la longitud útil de la rosca realizando una medida de la señal completa de EMB cada 0,5 mm de dicha longitud. Estas dos señales se procesaron en tiempo real en el sistema de medición y se almacenaron en un PC donde se postprocesaban.
Tras las mediciones de EMB se hicieron medidas de microdureza Vickers en todos los husillos para conocer tanto las durezas superficiales como los perfiles de dureza que presentaban. Las medidas de dureza se realizaron con una carga de 1 kg en una profundidad superficial de 150 μm para la caracterización de la superficie y a mayores profundidades para caracterizar la capa endurecida. En este trabajo se muestran los valores Vickers convertidos a Rockwell C de acuerdo con la norma ASTM-E140 [3].
2.3.2 Medidas de dureza
Por motivos de claridad de la exposición, en primer lugar se mostrarán los datos de las durezas pese a que éstas se tomaron una vez realizadas las medidas de EMB sobre las piezas. Los perfiles de dureza obtenidos en los husillos más representativos se muestran en la figura 1. Los husillos mecanizados correctamente presentan unas durezas en la superficie (a una distancia de 150 μm de la superficie) en el rango de 58 HRC - 61 HRC, mientras que en los que se quemaron la dureza es dispar. El husillo TA S4 presenta una dureza superficial de 59 HRC, el husillo TB S3 muestra una dureza ligeramente inferior a 58 HRC y por último el husillo TA S3 tiene una dureza de 54 HRC.
También puede observarse que los husillos del temple TA, independientemente de tener quema o no, presentan una profundidad de la capa endurecida según la norma ANSI/AGMA 2004-B89 [4] (profundidad hasta alcanzar 48 HRC) de aproximadamente 1.200 μm, mientras que en los husillos del temple TB correctos la profundidad de la capa es de aproximadamente 600 μm y en el husillo quemado, TB S3, la profundidad de la capa es ligeramente menor, de aproximadamente 500 μm. Las profundidades de capa mostradas aquí están dentro de los rangos exigidos por el cliente.
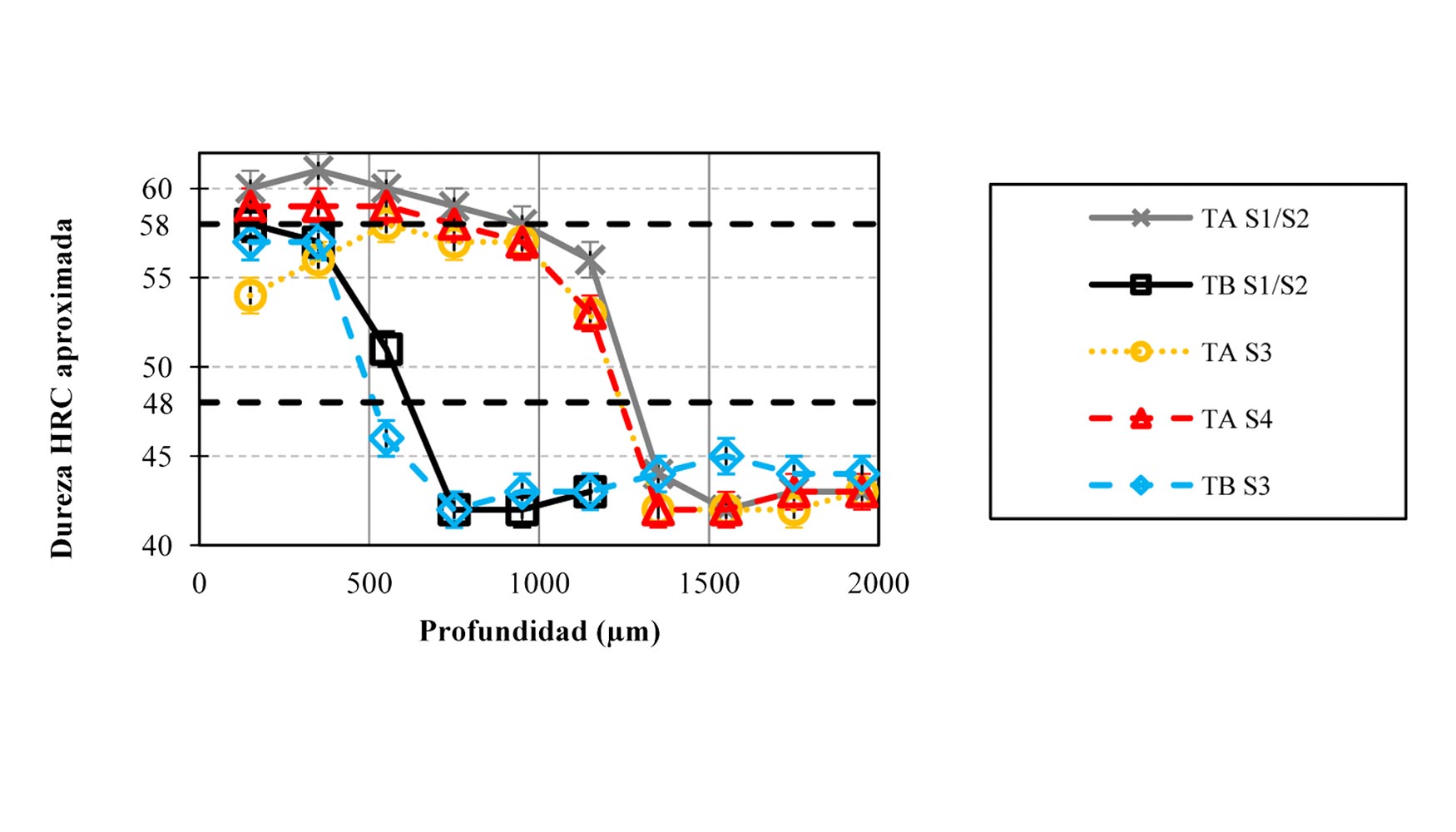
2.3.3 Caracterización de la capa de temple
En la figura 2 se muestra la envolvente representativa de la señal de EMB en función del campo magnético tangencial (Ht) medido en un punto de la superficie de la rosca para los husillos mecanizados de manera correcta. Puede verse que la envolvente de la señal EMB muestra dos picos claramente diferenciados. El primer pico proporciona información del material del núcleo, más blando, mientras que el segundo pico ofrece información del material de la superficie, más duro tras el tratamiento de temple por inducción [1, 2]. Para estudiar la profundidad de la capa en los husillos de producción es necesario medir y parametrizar las envolventes de la señal de EMB en toda la longitud útil de la rosca. Los parámetros utilizados en este caso son las amplitudes de los dos picos (P1 y P2) y el valor del campo aplicado en las posiciones en las que se producen los picos (H1 y H2). Cada punto de los valores que se muestran a continuación en función de la longitud útil de la rosca se obtiene como resultado de promediar 12 medidas de la envolvente de EMB.
En la figura 3 a) se presenta la amplitud del primer pico (P1) obtenida en toda la longitud útil de la rosca. Se observa que se obtienen mayores valores de P1 para los husillos provenientes del temple TB, que puede explicarse considerando que en estos husillos el núcleo se encuentra más cerca (figura 1) y por tanto la atenuación que sufre la señal de EMB emitida desde el núcleo es menor al atravesar un menor espesor de material [2, 5].
La posición del primer pico (H1) se presenta en la figura 3 b). Puede observarse que los husillos provenientes del temple TA necesitan unos valores mayores del campo aplicado, H1, lo que puede explicarse por la mayor profundidad de capa de este temple (figura 1). El campo magnético aplicado se atenúa al penetrar en el material [6] y por tanto si el núcleo se encuentra a mayor distancia para tener el mismo campo aplicado en el núcleo es necesario tener mayores valores del campo aplicado en la superficie.
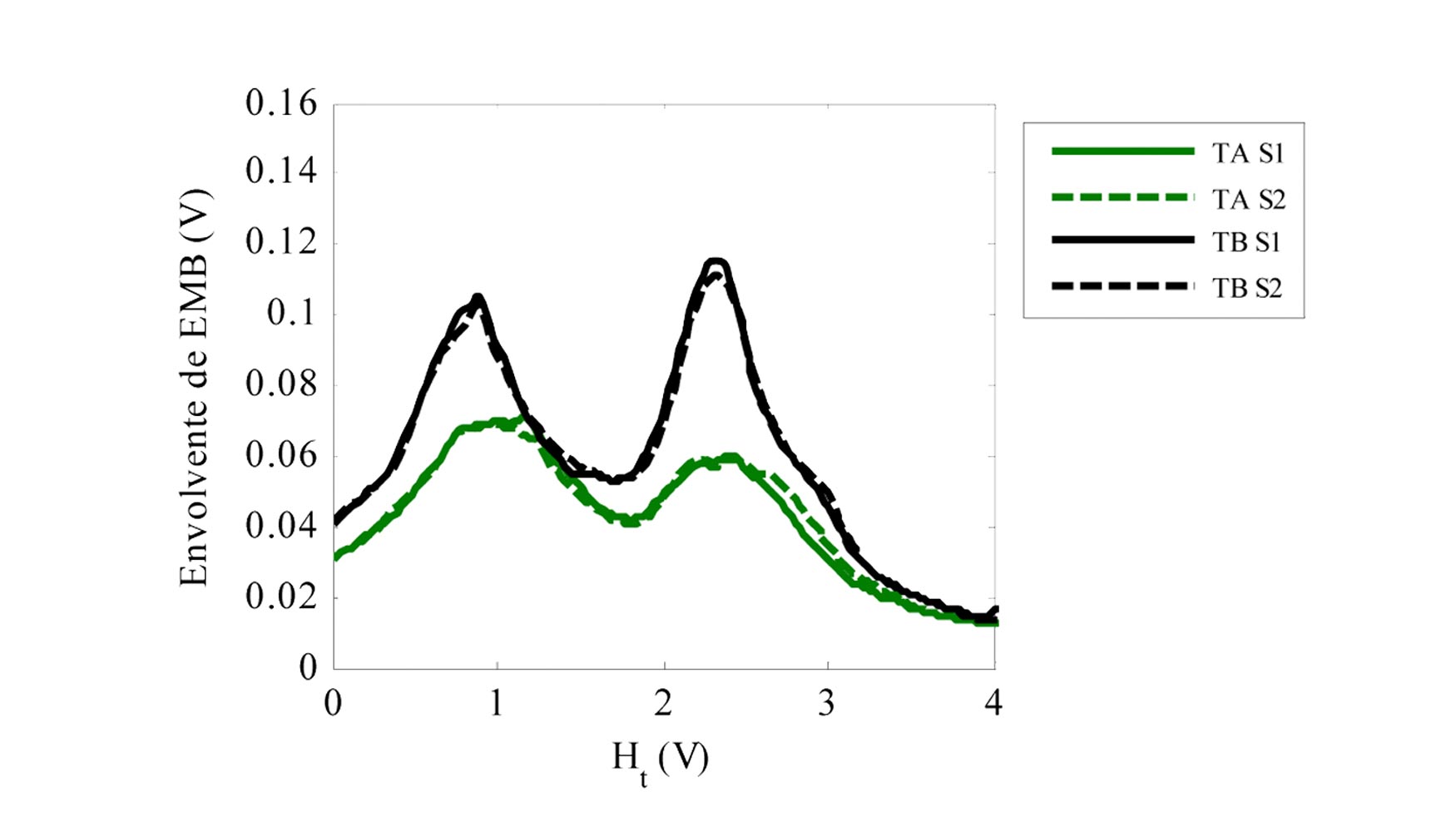
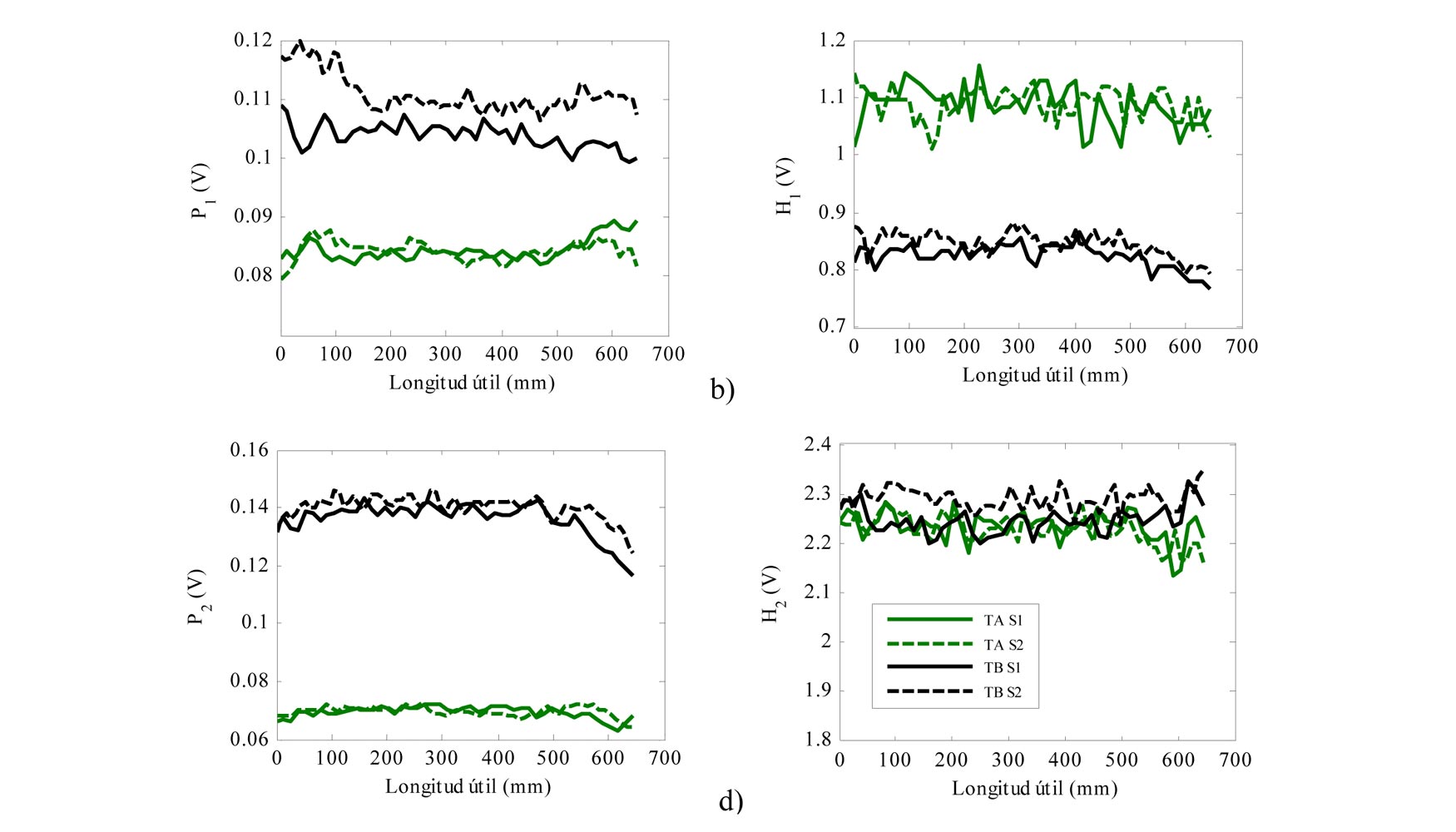
En la figura 3 c) se muestra la amplitud del segundo pico (P2). Se aprecia que se obtienen mayores valores de P2 para los husillos provenientes del temple TB. El mayor valor de P2 que se obtiene en el temple TB puede explicarse porque este temple es más blando globalmente (menor dureza superficial y menor profundidad de capa endurecida) y en los casos en los que la dureza se reduce la amplitud del pico de EMB se incrementa [7]. La posición del segundo pico (H2) se presenta en la figura 3 d), obteniéndose valores similares de este parámetro independientemente del temple analizado. Por tanto, se puede concluir que el análisis combinado de estos parámetros ofrece información de la profundidad y las características de la capa endurecida, lo que permite poder certificar la calidad del temple mediante la técnica de BNA.
2.3.4 Caracterización de las quemas
En la figura 4 a) y figura 4 b) se muestra la envolvente representativa de la señal de EMB en función del campo magnético tangencial (Ht) medido en un punto de la superficie de la rosca para los husillos correctos y quemados del temple TA, y del temple TB, respectivamente. Se aprecia que independientemente del temple analizado la posición del segundo pico (H2) de los husillos quemados se desplaza hacia menores valores de campo aplicado e incluso en los que han sufrido una quema más severa se tiene un único pico claro. Sin embargo, no existe una relación directa entre la quema y la amplitud de los distintos picos, obteniéndose amplitudes similares, mayores o menores en los distintos casos analizados. Se ha utilizado el parámetro H2 para separar los husillos quemados de los mecanizados correctamente. En el caso de que se tenga un único pico se considera la posición de este pico como la del segundo pico puesto que es el segundo pico el que se modifica en las quemas al ser el que aporta la información de la superficie.
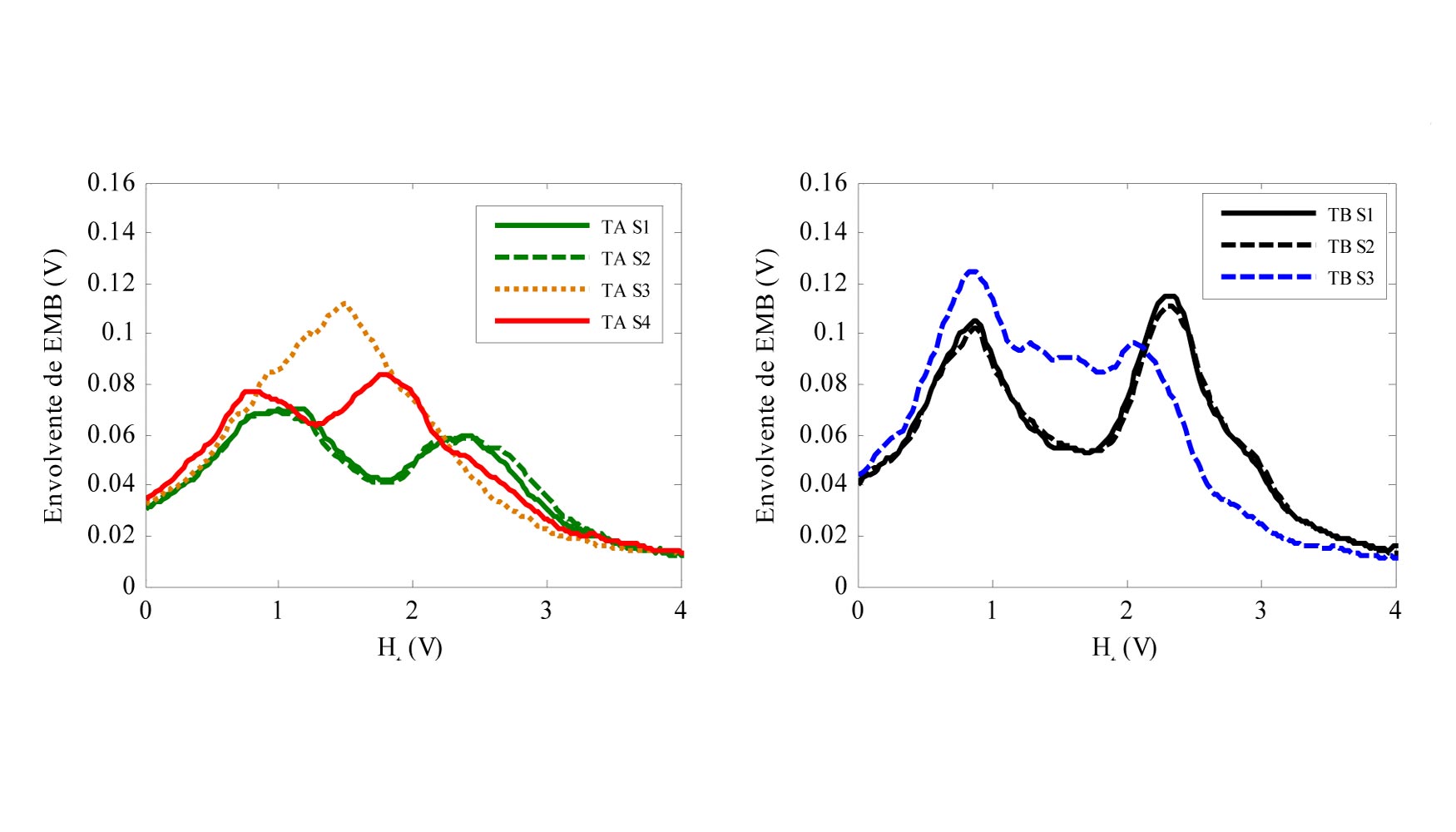
En la figura 5 se muestra el parámetro H2 obtenido a lo largo de la longitud útil de la rosca en todos los husillos y se puede observar que éste no está influenciado por los distintos temples y que se desplaza a menores valores del campo aplicado en los husillos que han sufrido una quema de rectificado. Por tanto, con la selección de unos umbrales de control para este parámetro se podrían distinguir todos los husillos mecanizados correctamente de los que no lo están.
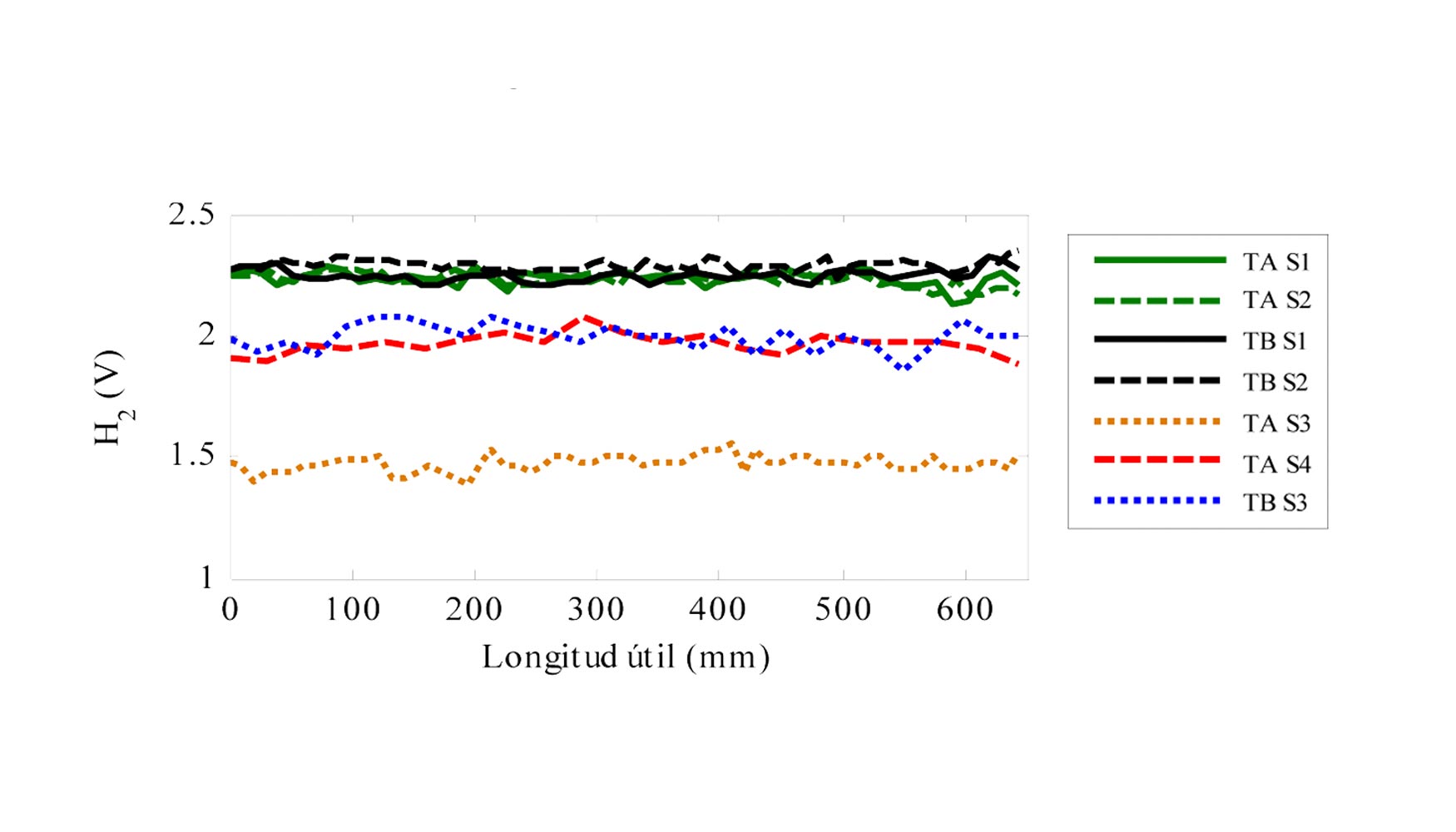
2.4 Desarrollo y automatización del sistema BNA robusto para medidas en planta
Una vez realizada la calibración del sistema no destructivo se desarrolló un sistema de BNA robusto que permitía integrar el dispositivo de medición de EMB y el cabezal excitador/sensor en un entorno industrial para realizar las medidas de forma automática, reproducible y repetitiva. Este sistema consta de tres elementos principales:
- Una bancada de medición
- Un dispositivo de medición de EMB
- Un ordenador
Tal y como se muestra en la figura 6 la bancada de medición está compuesta por una base (A); dos columnas móviles, una de las cuales (B) está compuesta por una pinza (C) unida solidariamente a un motor (D) que aplica el giro a los husillos y la otra (E) está compuesta por una punta retráctil (F) que permite el cambio de un husillo por otro de manera rápida y sencilla; un sistema de guiado (G) donde va acoplado el cabezal excitador/sensor (H); y dos sensores de proximidad (I). Esta bancada mediante el giro del husillo, controlado desde el ordenador, hace desplazarse al cabezal excitador/sensor a lo largo de la rosca de los husillos. Se aplica una velocidad de giro tal que se adquiere una medición a lo largo del perímetro de cada rosca cada 0,5 mm. Mediante los dos sensores de proximidad se le indica al ordenador cuándo el cabezal se encuentra en el punto donde debe iniciarse o finalizarse la medición y de este modo medir toda la longitud útil de la rosca de los husillos. El dispositivo de medición de EMB descrito en el apartado 2.3.1 se encarga de acondicionar las señales de excitación y de enviarlas al cabezal excitador/sensor y de adquirir y procesar las señales adquiridas en dicho cabezal en tiempo real y de enviarlas al ordenador. El ordenador realiza el control del movimiento del cabezal excitador/sensor a lo largo de la rosca iniciando y finalizando la medida cuando el cabezal se encuentra al inicio y al final de la longitud útil de los husillos. Además, tras la medida realiza el procesamiento necesario de las señales adquiridas y determina si los husillos son aptos o no aptos.
Se realizó un estudio de repetitividad y reproducibilidad y se comprobó que este sistema era válido para poder realizar las medidas en la planta de producción de forma que los datos recogidos dependiesen únicamente de las propiedades de los husillos, sin influencias de ruidos o condiciones externas.
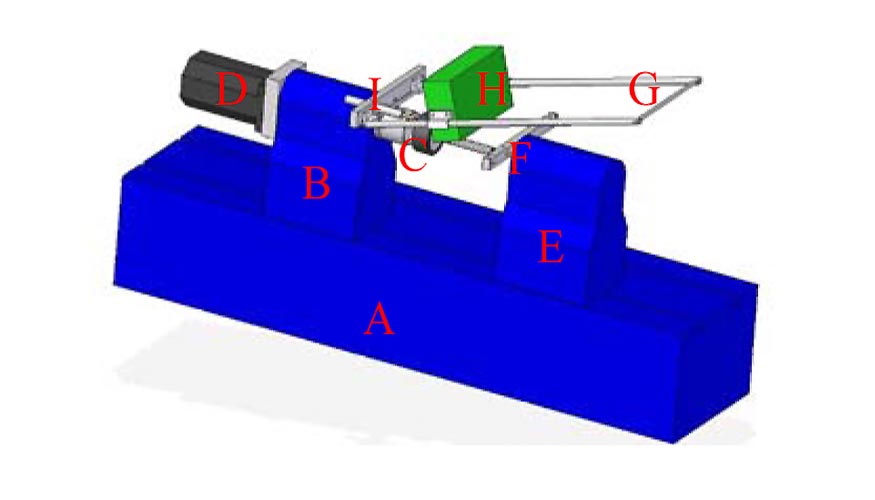
3. Medidas en planta: detección de defectos en producción
Una vez que se realizó la calibración y automatización del sistema se procedió a realizar las medidas y certificar todos los husillos fabricados por Korta. A continuación se muestra un ejemplo de un husillo con defecto de rectificado detectado durante la producción. En la figura 7 se presentan los valores de H2 de las medidas de lotes de producción de 50 husillos de dos temples distintos. Se puede ver cómo uno de los husillos de producción (‘TB quemado’) muestra valores significativamente menores a los umbrales establecidos. Para asegurar que dicho husillo había sufrido una quema se procedió a medirlo mediante microdurezas y se constató que efectivamente su dureza superficial estaba por debajo de 58 HRC.
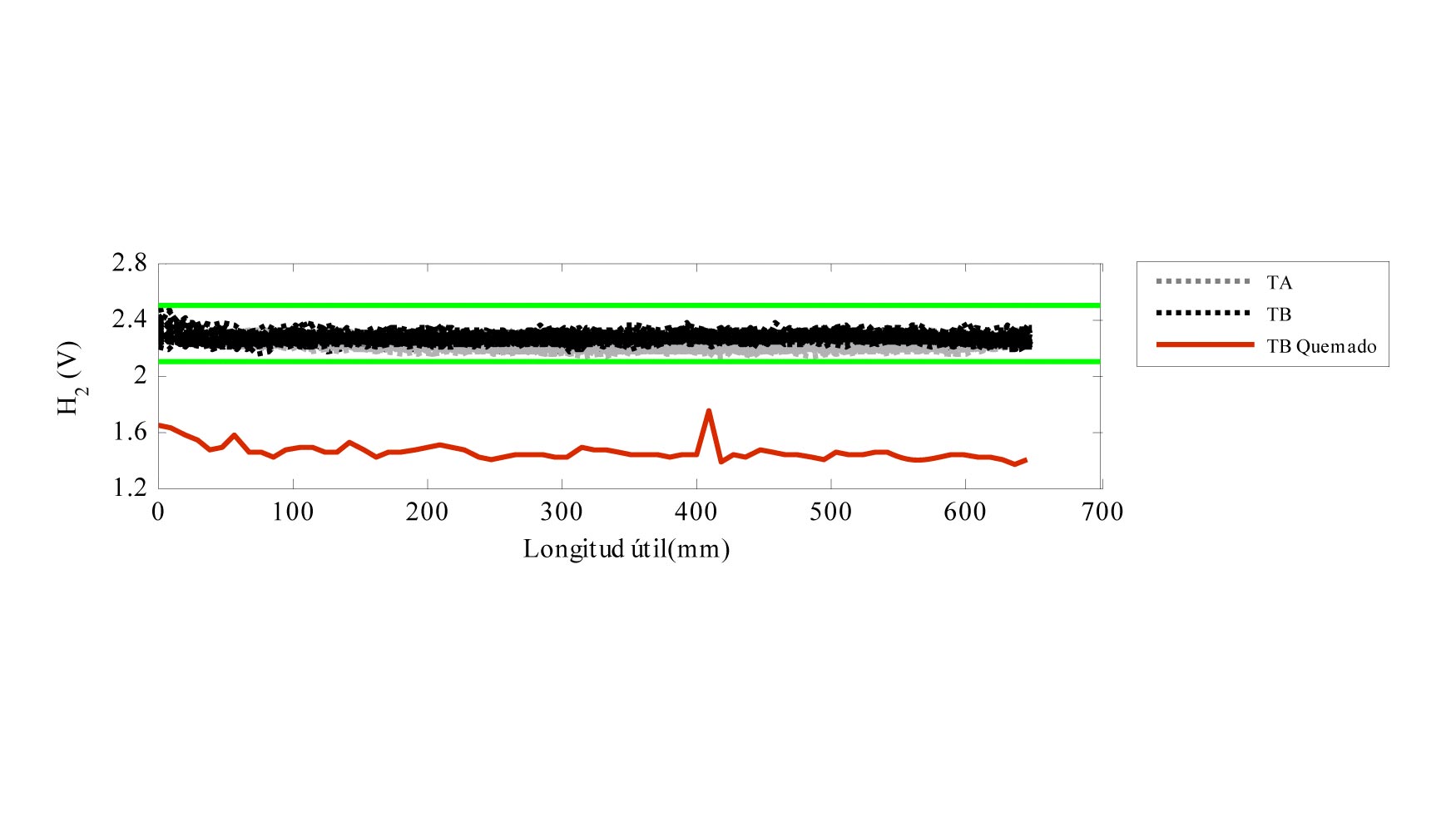
4. Conclusiones
El sistema de BNA desarrollado permite analizar y estimar la profundidad de la capa endurecida mediante tratamiento térmico de temple por inducción y poder controlar que la pieza no haya sufrido quemas de rectificado en husillos a bolas. Se ha comprobado que realizando un estudio multiparamétrico de la envolvente de la señal de EMB se puede obtener información sobre el espesor de la capa endurecida y detectar que este espesor es insuficiente. Además, se ha concluido que la posición del segundo pico de la envolvente, H2, puede emplearse para detectar que un husillo ha sufrido una quema de rectificado independientemente de la profundidad de capa superficial que tenga. Con la realización de este trabajo la empresa KORTA S.A. ha obtenido un sistema de control de calidad no destructivo y automatizado que le permite detectar las quemas de rectificado y controlar la capa endurecida en la rosca del 100% de los husillos de producción. De esta forma es capaz de cumplir los requisitos exigidos por su cliente, certificando la integridad superficial y la capa endurecida de los husillos.
Referencias
[1] V. Moorthy, B. A. Shaw, ‘Magnetic Barkhausen Emission Measurements for Evaluation of Material Properties in Gears’, Nondestructive Testing and Evaluation, v 23, n 4, p 317-347, 2008.
[2] V. Moorthy, B. A. Shaw, J. T. Evans, ‘Evaluation of Tempering Induced Changes in the Hardness Profile of Case-Carburised EN36 Steel using Magnetic Barkhausen Noise Analysis’, NDT and E International, v 36, n 1, p 43-49, 2003.
[3] ASTM E 140, ‘Standard Hardness Conversion Tables for Metals Relationship among Brinell Hardness, Vickers Hardness, Rockwell Hardness, Superficial Hardness, Knoop Hardness, Scleroscope Hardness, and Leeb Hardness’, 2007.
[4] ANSI/AGMA 2004-B89, ‘Gear Materials and Heat Treatment Manual’, 1995.
[5] O. Kypris, I. C. Nlebedim, D. C. Jiles, ‘A New Method for Obtaining Stress-Depth Calibration Profiles for Non-Destructive Evaluation using a Frequency-Dependent Model of Barkhausen Emissions’, IEEE Transactions On Magnetics, v 49, n 7, p 3893-3896, 2013.
[6] D. C. Jiles, ‘Introduction to magnetism and magnetic materials’, ed Chapman & Hall, Boca Raton, 1998.
[7] F. A. Franco, M. F. R. Gonzalez, M. F. De Campos, L. R. Padovese, ‘Relation between Magnetic Barkhausen Noise and Hardness for Jominy Quench Tests in SAE 4140 and 6150 Steels’, Journal of Nondestructive Evaluation, v 32, n 1, p 93-103, 2013.