Stadler renueva el Centro Integral de Tratamiento (CTIR) de las marinas de El Campello (Alicante)
El CTIR es una instalación de grandes dimensiones, con enormes variaciones en la entrada de residuos, que da servicio a los 52 municipios de la Marina Alta, la Marina Baja y El Campello.
Tras una larga relación entre ambas compañías, Stadler, referente mundial en plantas de RSU a nivel internacional, ha sido la empresa elegida para la modificación. “El tamaño de las instalaciones, el corto plazo para hacer los trabajos y la complejidad añadida de tener que hacer la reforma con una planta en funcionamiento, fueron factores que pesaron a la hora de elegir a Stadler”, opina Javier Cerezo, director técnico de FCC Medio Ambiente.
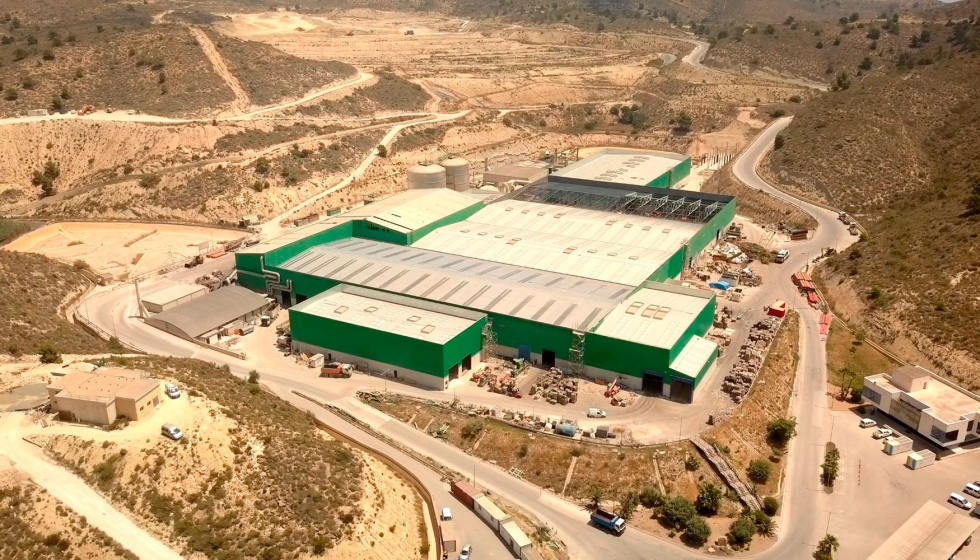
En palabras de Policarpo Caballero, director del proyecto de Stadler: “Ha sido un reto por varios motivos: se ha hecho en 5 fases diferentes y hemos tenido que ajustarnos a la infraestructura existente. En un nuevo proyecto es más fácil encajarlo todo desde el principio, y en este caso, la precisión ha sido fundamental para instalar nuestros equipos sin dañar los anteriores”.
En lo que se refiere al sector, Javier Cerezo asegura: “El sector del tratamiento de residuos en España lleva en constante cambio desde hace ya muchos años. Estos cambios van a tener que continuar ya que el reto de los objetivos europeos sigue estando presente. Por ello, el uso de nuevas tecnologías como las que aporta STADLER en sus diseños permiten extraer cada vez más materiales y de mejor calidad de los residuos tratados, para también producir compost o combustibles alternativos”.
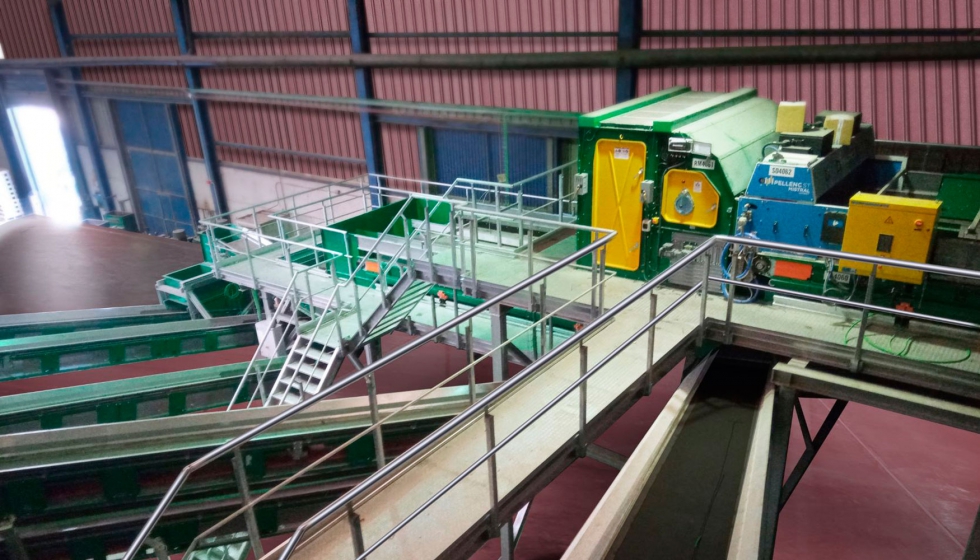
Con esta modernización, el CTIR se iguala en prestaciones a otras plantas de nueva construcción, pudiendo dar un servicio satisfactorio durante los próximos 15 años. De hecho, a lo largo de 3 meses, Stadler se ha encargado de renovar la tecnología que ya había quedado obsoleta cambiándola por equipos de última generación y marcas punteras en el sector del tratamiento de residuos.
“El Centro Integral de Tratamiento (CITR) de Las Marinas en El Campello lleva funcionando desde abril de 2009 y le tocaba una renovación y modernización de sus instalaciones. Así, este proyecto surge por la necesidad de adaptar la planta a las nuevas normativas en las que se requiere una mayor recuperación de materiales, un tratamiento de residuo orgánico de recogida selectiva y un tratamiento más cuidadoso con el medioambiente desde el punto de vista de emisión de olores. Además, una instalación como el CITR Campello es una herramienta que juega un papel clave en la economía circular”, puntualiza Javier Cerezo.
Un proyecto en tiempo récord
Además, la planta ha seguido funcionando con normalidad, permitiendo así que el cliente siguiera procesando material. “Sólo hemos tenido que parar la planta 2 días. Estamos realmente satisfechos, tanto por la excelente colaboración de FCC Medio Ambiente, como por no tener que interrumpir la actividad de la planta. Esto fue posible gracias a un By-pass diseñado con cintas que ya estaban, conectando el trómel existente a la cabina existente”, explica Policarpo Caballero.
Por su parte, Ana López, responsable del desarrollo del concepto de la planta de Stadler, asegura: “Es importante que no se haya parado la actividad porque, al estar situada en una de las zonas más turísticas de la Península, su funcionamiento es prácticamente ininterrumpido, trabajando 7 días a la semana, 24 horas al día. Asimismo, ha supuesto un gran reto por ser una instalación de gran capacidad de tratamiento de residuos, con altos niveles de exigencia en cuanto a ingeniería, tecnología y trabajo de obra. Pero se ha podido lograr gracias al profesional equipo de montaje de Stadler y a un diseño de fábrica preparado para un rápido ensamblaje en obra. La buena ejecución de estos factores unidos a la coordinación con el cliente y el esfuerzo conjunto ha llevado a un resultado exitoso”.
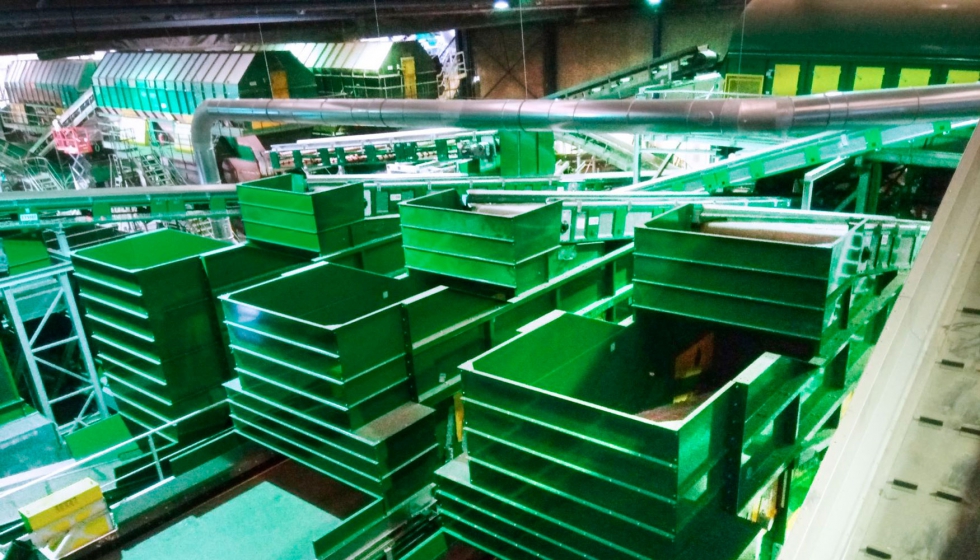
Javier Cerezo lo confirma: “Esta reforma de la planta ha tenido que hacerse con la planta en funcionamiento y teniendo en cuenta la estacionalidad en la generación de los residuos que se producen en los más de 50 municipios a los que da servicio. Estos municipios situados en las comarcas de la Marina Alta y Baja cubren una gran parte de la costa alicantina con poblaciones tan conocidas como por ejemplo Benidorm, Denia, Calpe o Jávea”.
Cinco fases para adaptar la planta a las nuevas necesidades
Las cinco fases han consistido en instalar nuevos equipos en diferentes zonas de la planta:
Compost, Afino, Biometanización, RSU y FORS. Para conseguir una óptima recuperación en la separación óptica se han tenido que suministrar e implantar, 2 trómeles para cribado de bolsas cerradas y botellería con diferentes calibres, 3 separadores balísticos para cada una de las fracciones del trómel y una tercera proveniente de voluminosos, previo paso por un triturador.
“En la planta de Biometanización, nuestras cintas se han colocado entre muchas cintas y maquinaria ya existente. En la planta de RSU, hemos reutilizado trómeles, cabinas, alimentadores y hemos tenido que ajustar cintas ya existentes del cliente alargando y/o acortando según las necesidades del diseño de la nueva planta”, afirma Policarpo Caballero.
Además, Stadler ha instalado una nueva línea de pretratamiento FORS (orgánica de recogida selectiva), para tratar este flujo de forma diferenciada, dando así cumplimiento a la normativa vigente en materia de gestión de residuos y una nueva línea de afino de compost y selección de vidrio.
Un aspecto especialmente novedoso de la planta ha sido la incorporación de una línea de producción de CSR (Combustible Sólido Recuperado) para cementera. Javier Cerezo explica: “Esta línea incorpora, entre otros procesos, una etapa de secado a baja temperatura para garantizar el grado de humedad requerido. La planta se ha provisto con los equipos necesarios para poder producir un CSR prácticamente a la carta, pudiendo controlar parámetros como la composición, granulometría y humedad del mismo”.
Objetivos cumplidos
Con este proceso, los objetivos principales se han alcanzado a través de un proyecto de ingeniería de gran envergadura desarrollado por Stadler. Estos han sido: el incremento de capacidad de tratamiento de la planta y de los ratios de recuperación, instalación de una nueva línea diferenciada para el tratamiento de FORS, instalación de la nueva línea de CSR, mejora en el proceso de afino de compost y reducción del rechazo (residuo enviado a vertedero).
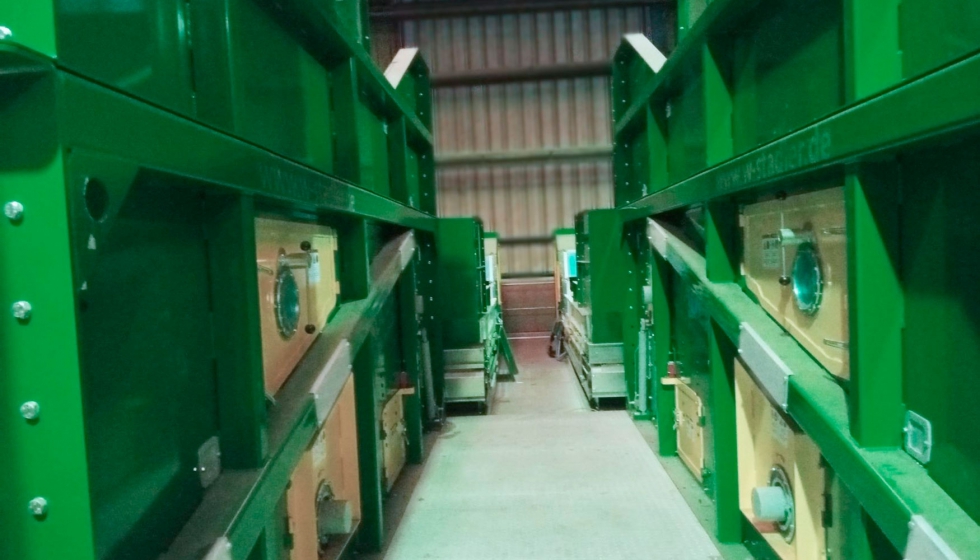
“En definitiva, conseguir reciclar más y mejor, reduciendo el impacto ambiental”, añade Ana López. “Era una planta automática con separadores ópticos, pero con modelos antiguos que no funcionaban correctamente. La tecnología de la planta había quedado obsoleta, habiendo cumplido su vida útil. Para conseguir los objetivos de tratamiento y recuperación de subproductos deseada, había que introducir nuevos equipos con la última tecnología”, matiza.
“La verdad es que todo ha salido muy bien, el trabajo fue desarrollado en tiempo. Todo ello gracias a nuestros magníficos montadores y a la buena coordinación con FCC Medio Ambiente”, concluye Policarpo Caballero. Javier Cerezo coincide: “Los equipos de ambas empresas han sabido coordinarse perfectamente y adaptarse a los cambios”.
Asimismo, expresa su satisfacción hacia el trabajo de Stadler: “Su experiencia en el diseño de líneas de tratamiento de residuos ha sido de enorme ayuda para la modernización del CITR. Recomiendo Stadler por su seriedad, profesionalidad, la calidad de sus equipos y la maquinaria instalada, entre otras razones. Sin duda, Stadler nos ha demostrado ser un proveedor fiable para plantas de tratamiento de residuos”.