Es el primer sistema mundial que convierte escamas en pre-formas
Xtreme Renew de Erema y Sipa gana el premio World Star Packaging Award
La tecnología europea que permite producir botellas PET totalmente a partir de desechos postconsumo ha sido galardonado con el prestigioso premio WorldStar Packaging Award en una ceremonia de gala organizada por la Organización Mundial del Embalaje (WPO) en Praga, República Checa, el pasado 15 de mayo. El innovador sistema Xtreme Renew fue desarrollado conjuntamente por el especialista en tecnología de reciclaje austriaco Erema (representada en España por Protecnic 1967) y Sipa, firma especializada en sistemas de producción de preformas y botellas de PET con sede en Italia.
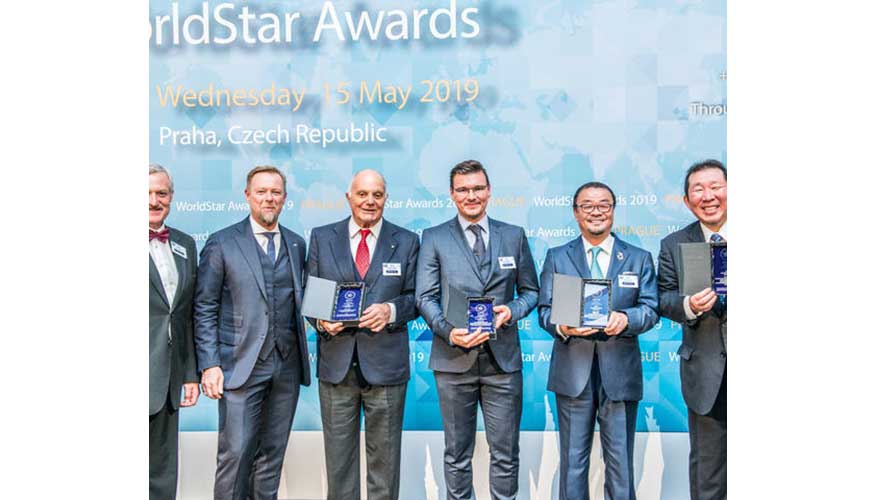
Desde la izda.: Pierre Pienaar, presidente de la organización World Packaging, Michael Heitzinger, director ejecutivo de Erema GmbH, Gianfranco Zoppas, presidente de Zoppas Industries Group/Sipa, Christoph Wöss, responsable de Desarrollo de Negocios de aplicaciones de PET, Erema, Eiichi Furusawa, presidente de Kyoei y Munehiko Takada, jefe especialista del departamento de materiales de packaging, Suntory. Créditos: World Packaging Organization.
La tecnología Xtreme Renew es única en el mundo por su capacidad para producir botellas aptas para el contacto con alimentos y con propiedades tan buenas como las de las botellas producidas a partir de PET virgen, directamente a partir de hojuelas de desechos post-consumo, en un solo ciclo de calentamiento. Permite convertir escamas en pre-formas, es decir, que produce directamente nuevas pre-formas de rPET aptas para contacto alimentario a partir de escama de PET reciclado en un proceso de un solo paso.
Comercialmente entró en funcionamiento por primera vez a fines del año pasado: Erema y Sipa colaboraron con dos socios japoneses también citados para el premio, Kyoei Industry (una importante empresa de reciclaje) y Suntory (uno de los mayores fabricantes de bebidas del mundo), en una instalación en Kasama, Japón. El sistema puede producir más de 300 millones de envases al año.
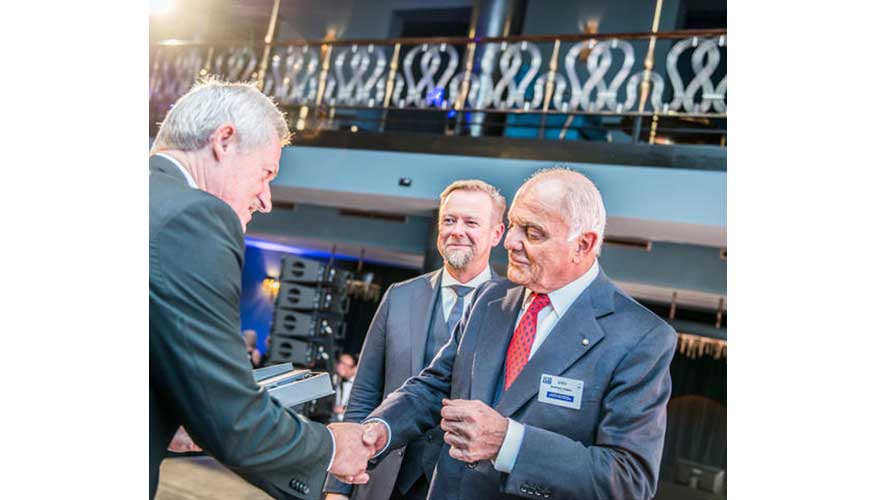
Gianfranco Zoppas (SIPA) (derecha) y Michael Heitzinger (Erema) recibieron el premio WorldStar Packaging Award del Prof. Pierre Pienaar, Presidente de la WPO (izquierda). Foto: Sipa.
El sistema utiliza la tecnología Erema para convertir las hojuelas de botellas convencionales lavadas, en PET fundido filtrado descontaminado grado alimenticio con una viscosidad (IV) mayor, que luego se utiliza para alimentar directamente al sistema de moldeado de preforma por inyección-compresión Sipa Xtreme (a diferencia de otros sistemas de moldeado presentes en el mercado, donde hay que partir del material peletizado denominado RPET). Los envases producidos a partir de estas preformas son estéticamente excelentes, gracias a la eliminación del proceso completo de fusión, que por otra parte podría producir un amarilleo en la resina.

"Esta es una solución que representa la respuesta perfecta a los requisitos de la nueva economía circular", indica Gianfranco Zoppas, Presidente de la empresa matriz Sipa de Zoppas Industries. “El reprocesamiento de los desechos se ha convertido en sostenible y económico fabricando nuevos productos de la más alta calidad. Esta tecnología innovadora utiliza un 30% menos de electricidad que los procesos de reciclaje tradicionales, gracias en gran parte a la integración de los sistemas, mientras que las emisiones de CO2 disminuyen en un 25%, un masivo 60% cuando se compara con la producción de botella a partir de resina virgen.
"Me siento particularmente honrado de que esta tecnología verde austro-italiana haya recibido un importante reconocimiento internacional. Ya ha tenido tanto éxito en Japón que nuestros socios están pensando en dos instalaciones adicionales que triplicarán la capacidad de producción hasta casi mil millones de botellas RPET al año".
Más información: https://www.sipasolutions.es/es/
Cuatro pioneros que han unido su conocimiento con éxito
El desarrollo conjunto del proceso fue iniciado en 2014 por Kyoei Industry y Suntory. El proceso galardonado se basa en la combinación de la tecnología probada botella a botella Vacurema, la cual ha sido mejorada para esta aplicación con el sistema XTREM. Esta nueva planta produce nuevas pre-formas de PET aptas para contacto alimentario directamente de escama de PET. Después de haber estado en funcionamiento durante casi un año en Kyoei Industry en Kasama (Japón), este sistema de escama a pre-forma no sólo produce pre-formas con valores de calidad impresionantes, sino que también proporciona un rendimiento ecológico y económico únicos. La capacidad anual de producción de esta planta es de 300 millones de containers. El cliente para este volumen de producción es el fabricante internacional de bebidas japonés Suntory.
La parte Vacurema de la planta descontamina las escamas e incrementa la viscosidad del material de entrada, que es fundido y filtrado. La masa apta para contacto alimentario se alimenta entonces directamente en la máquina de inyección de moldes XTREMA proveída por SIPA. Con este sistema, ya no se requiere un proceso de fusión adicional (i.e. para fundir la granza de rPET, que es necesario en los procesos convencionales). De esta forma se elimina el riesgo de amarilleo y de formación de compuestos orgánicos volátiles. Por tanto, las botellas hechas de estas pre-formas distan mucho en apariencia del resto de productos provenientes al 100% de rPET. “Si la calidad de las escamas lavadas es correcta, las pre-formas en línea no están muy lejos de ser comparadas con productos vírgenes de moldeo por inyección”, indicó Christoph Woess, responsable de Desarrollo de Negocios de aplicaciones de PET en Erema.
La combinación de las cuatro fases - descontaminación, estabilización de la IV, filtración y estampado por inyección- en un único sistema, reduce el consumo de energía en un 30% en comparación con los sistemas convencionales. Asimismo se reducen las emisiones de CO2 en un 25% y en consecuencia, son significativamente inferiores a las que se emiten en la producción de botellas de PET convencionales provenientes de rPET. Ya que no se produce granza de rPET, tampoco se necesitan secadores ni zonas de almacenaje, lo cual resulta en un menor coste