Automoción, moldeo técnico, sector médico, son algunas de las aplicaciones a las que se dirigen las novedades de la K de Engel
Engel sorprenderá con sus últimos desarrollos tecnológicos en la feria K 2016
En la próxima feria K, que se celebrará en Dusseldorf del 19 al 26 de octubre de 2016, Engel, representada por Helmut Roegele, se reafirmará una vez más como líder tecnológico. El fabricante de inyectoras y experto en sistemas con sede en Schwertberg (Austria) exhibirá las punteras aplicaciones que ha creado para los sectores de automoción, teletrónica, moldeado técnico, embalajes y medicina.
Gracias a sus innovadoras tecnologías de procesamiento, sus programas de fabricación diseñados a medida y sus sistemas de control inteligentes, estas sofisticadas aplicaciones reportan grandes beneficios al cliente. Así, los clientes de Engel cuentan con una ventaja decisiva en los mercados internacionales y consiguen una mayor rentabilidad, más productividad y unos niveles de calidad más estables. 'Be the first': sea el primero. Este será el lema con el que Engel estará presente en la feria K 2016 (pabellón 15, stand C58).
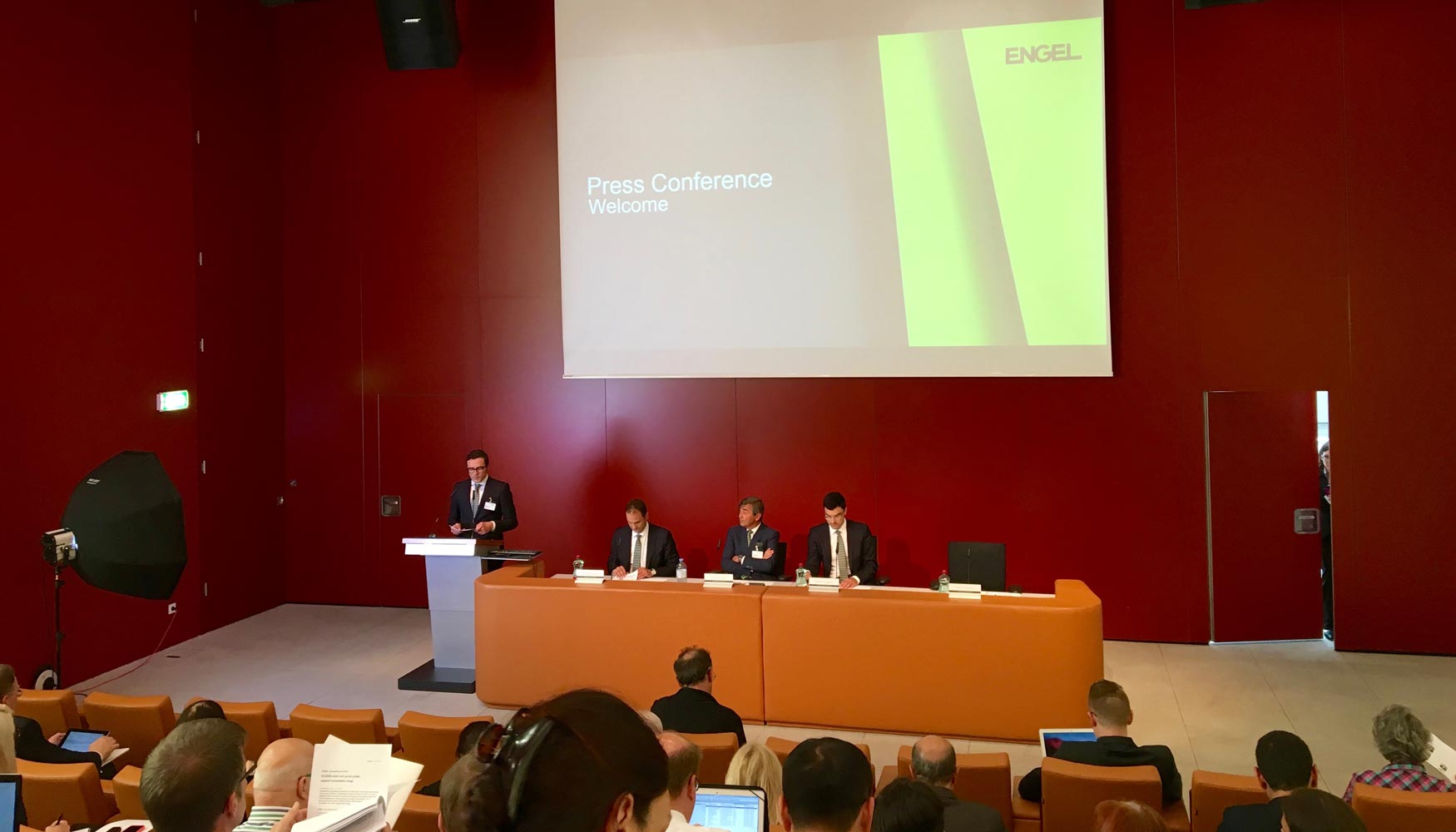
Automoción: dos estrenos que rebajarán aún más los costos unitarios
DecoJect introduce color, estructura y cualidades táctiles
Las tecnologías IMD (In-Mould Decoration o decoración en el molde) se están utilizando cada vez más para sustituir a la pintura en la producción de interiores de automóviles, ya que permiten obtener acabados de alta calidad en las superficies, procesar lotes pequeños con gran flexibilidad y lograr un bajo costo unitario. En la feria K 2016, Engel presentará junto a sus socios un nuevo avance. Se trata de DecoJect, una solución a base de film que, mediante un proceso “de rodillo a rodillo”, combina el moldeo por inyección con la tecnología IMG (In-Mould Graining o granulado en el molde). La diferencia respecto a los procesos IMD convencionales es que la pintura no se transfiere simplemente del film al componente, sino que el film se troquela y queda fijado al componente. De esta forma, además del color y el estampado, adquiere también una estructura en la superficie y unas cualidades táctiles.
DecoJect se mostrará por primera vez al público en el stand de Engel y se presentará integrada en una unidad de producción totalmente automatizada. Utilizando una inyectora Engel duo 5160/1000, se fabricarán, a modo de muestra, piezas que simularán paneles de puerta de gran tamaño. Para demostrar la amplia gama de posibilidades de esta nueva tecnología, las piezas elaboradas tendrán diferentes estructuras, entre ellas un sofisticado granulado tipo piel.
En cuanto el molde se abre y el robot retira la pieza acabada, se introduce el delgado film DecoJect, se calienta con el radiador de infrarrojos ubicado en la pinza y se preforma directamente en el molde con la ayuda de un sistema de vacío. Inmediatamente después, se inyecta el material sobre el reverso del film, y este se troquela antes de que el robot retire el componente y lo transfiera a la estación láser integrada, donde es sometido a un corte de precisión. Cada 60 segundos, sale de la unidad de producción un componente listo para montar. Si se quiere cambiar de diseño, solo hacen falta unos minutos para sustituir el rodillo. Gracias a ello, el tamaño del lote ya no repercute significativamente en el costo unitario.
El film delgado DecoJect es un producto de Benecke-Kaliko, una empresa con sede en Hanóver (Alemania) que pertenece al grupo tecnológico Continental. Puesto que es el film el que confiere al producto las características deseadas en la superficie (color, textura, solidez, sensación táctil, etc.), DecoJect permite usar como material estándar el polipropileno sin teñir, que resulta muy económico. Otro factor que mejora la eficiencia es la integración de la tecnología MuCell de la empresa Trexel (Wilmington, Massachusetts, EE UU). El moldeo por inyección de espuma reduce significativamente el peso del componente y el consumo de materias primas y energía, permitiendo no obstante fabricar piezas con dimensiones esta-bles que apenas se deforman.
Crear DecoJet ha sido posible gracias a una colaboración estrecha e interdisciplinar entre numerosas empresas asociadas. Además de Engel y Benecke-Kaliko, en el proyecto también han participado las siguientes compañías: Georg Kaufmann Formenbau (de Busslingen, Suiza), Galvanoform Gesellschaft für Galvanoplastik (de Lahr, sur de Alemania), el fabricante de canales calientes HRSflow (con sede en San Polo di Piave, Italia), Ico System International (de Lüneburg, Alemania) y Borealis (con sede en Viena, Austria), que además de suministrar la materia prima se ha encargado de analizar el flujo del moldeo. Algunos de los desafíos a la hora de desarrollar esta nueva tecnología han sido diseñar un molde IMG capaz de resistir las altas presiones que se aplican durante el proceso de moldeo por inyección y perfeccionar el modo exacto de controlar las unidades eléctricas que accionan las compuertas de la válvula.
Aportando sus conocimientos como experto en automatización, Engel ha contribuido signi-ficativamente a rentabilizar y flexibilizar el proceso. Un robot lineal Engel viper y un robot de seis ejes Engel easix se ocupan de manipular las piezas. Junto con la estación láser —que somete el film a un corte de precisión— el Engel easix está alojado en el espacio de una Engel easiCell, sumamente compacto. El diseño estandarizado pero modular de la Engel easiCell facilita la integración de robots y unidades de procesamiento tanto antes como después de la fase de moldeo por inyección. Entre otras cosas, esta unidad se puede emplear como módulo de producción para mecanizar con láser (cortar y marcar), aplicar juntas de poliuretano, tratar superficies (por ejemplo con plasma) o realizar otras tareas au-tomatizadas, como transferir bandejas o cajas.
Además de un diseño compacto, Engel easiCell ofrece al usuario otras ventajas. Por ejemplo, todos los sistemas de control que influyen en el proceso global se encuentran inte-grados en una única unidad de control CC300. En su versión independiente, Engel easi-Cell cuenta con un panel de control propio Full HD de 21 pulgadas. La unidad de producción también se puede manejar y controlar mediante el panel de una máquina de moldeo por inyección. La integración de todos los componentes del sistema de control hace que su uso resulte uniforme y fácil de aprender para los operadores de máquinas. Esta uniformidad también se manifiesta en el hecho de que cada uno de los componentes individuales cumple todos los requisitos legales aplicables. La unidad de producción completa se entrega acom-pañada de un certificado CE. La unidad de automatización Engel easiCell ha sido desarro-llada por Engel Automatisierungstechnik en Hagen (Alemania) y se presentará al público por primera vez en la feria K 2016.
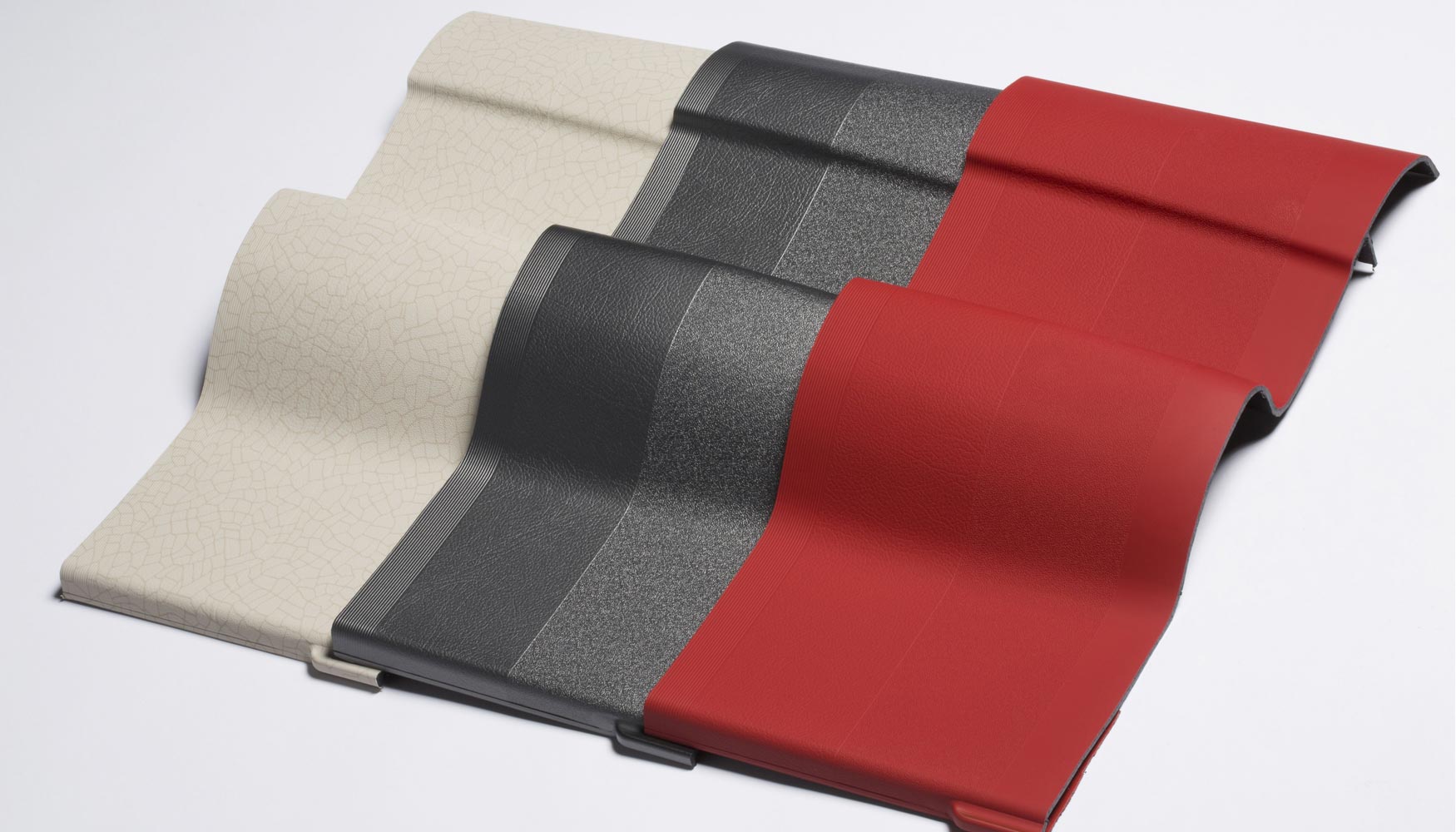
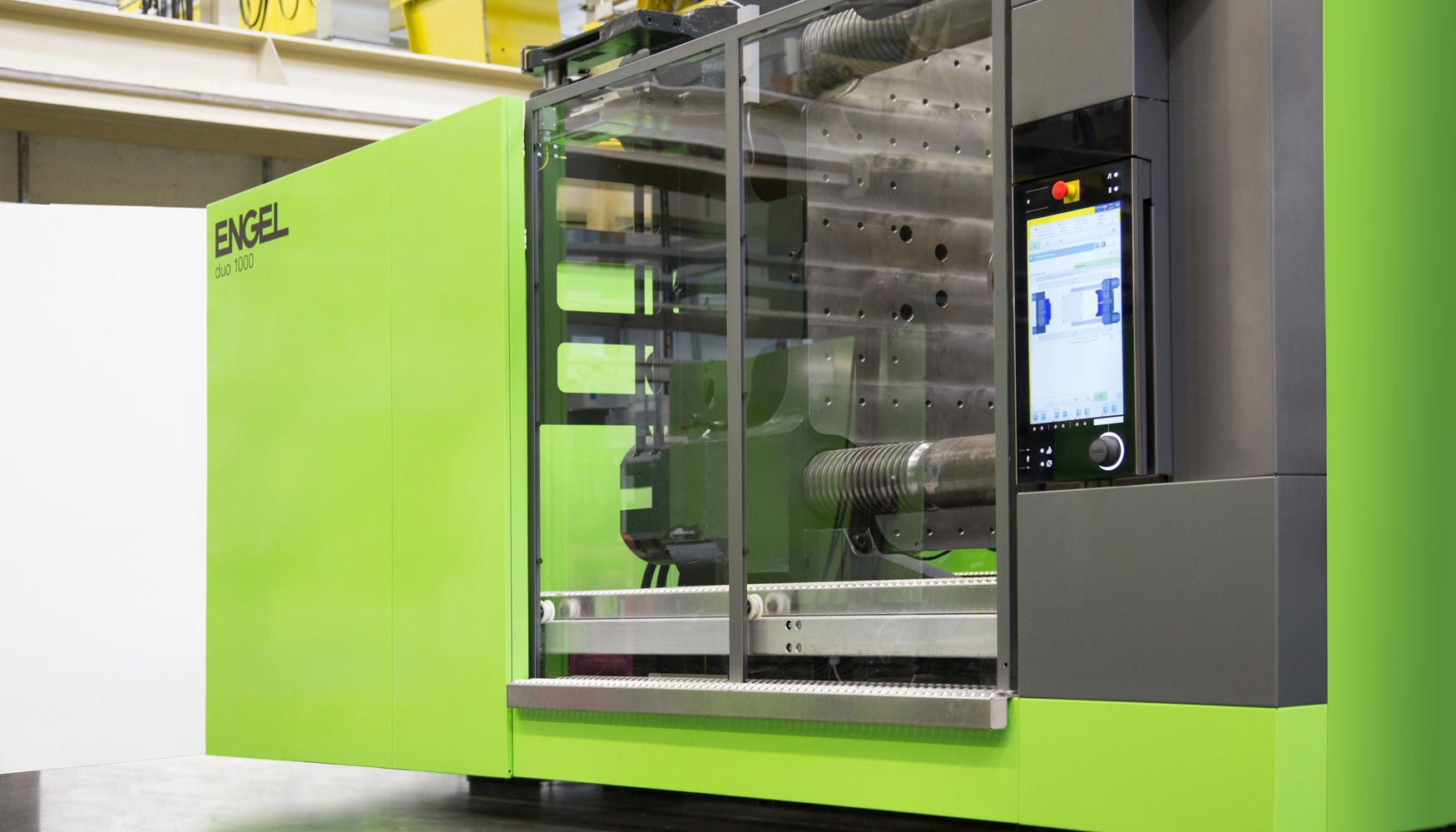
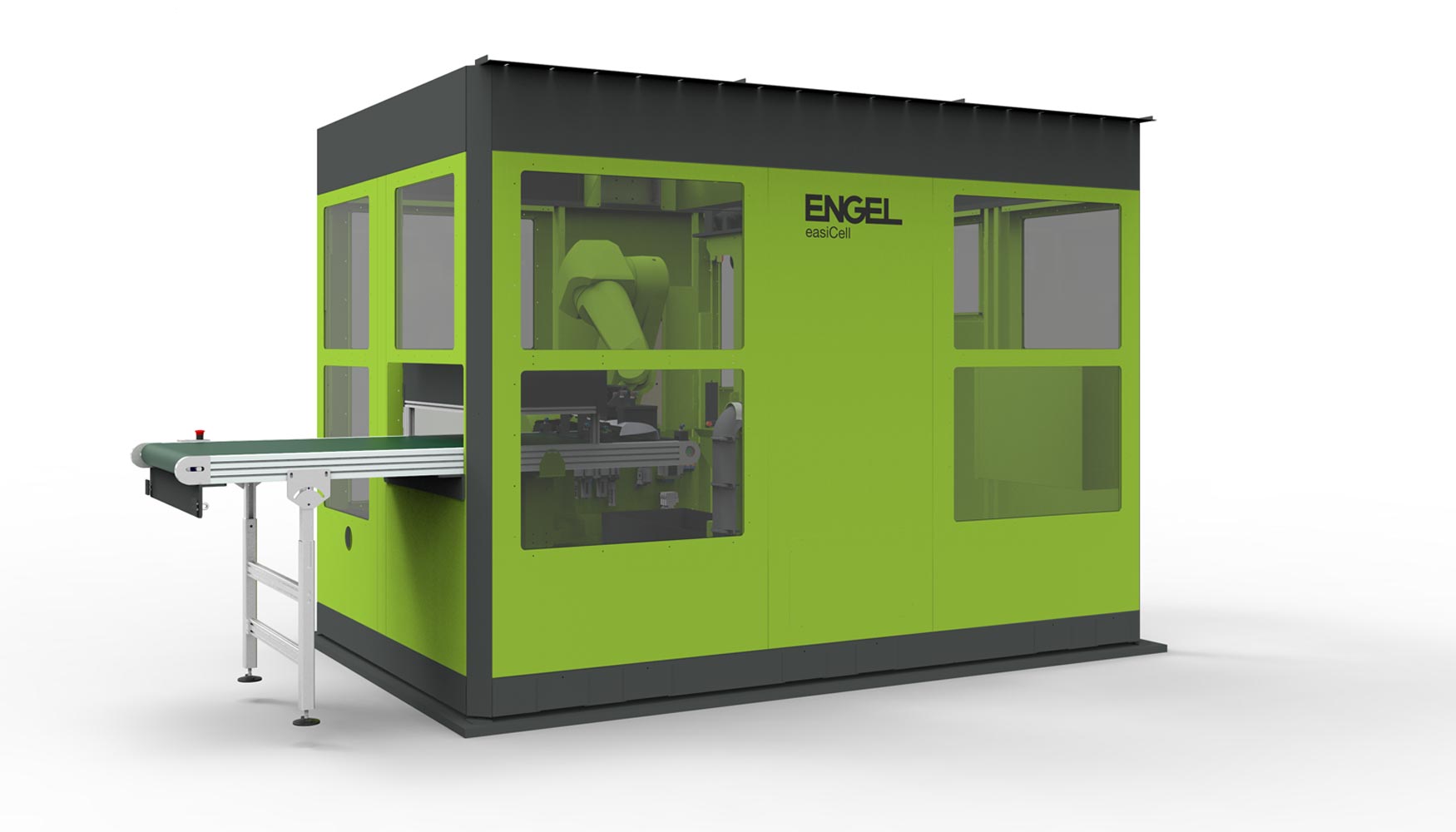
Construcción ligera: nuevos hitos no solo para el sector de la automoción
Gracias a su Centro de Tecnologías de Construcción Ligera situado en St. Valentin (Austria) Engel es uno de los socios más importantes del sector internacional de la automoción en lo que a desarrollo se refiere. Junto con otras empresas colaboradoras, Engel desarrolla procesos rentables para la producción en masa de piezas capaces de satisfacer los requisitos presentes y futuros de la construcción ligera. Hace mucho que estas piezas no se limitan al sector de la automoción, tal como demostrarán las dos aplicaciones con materiales compuestos que podrán verse en el stand de Engel durante la feria K 2016. Ambas han marcado nuevos hitos en la fabricación de productos compuestos aún más ligeros, robustos y sostenibles.
Teletrónica: procesos altamente integrados para fabricar productos de paredes ultrafinas
A la hora de producir dispositivos móviles —ya sean portátiles, tabletas o smartphones— la clave para reducir peso y aumentar la estabilidad es fabricar la carcasa con materiales com-puestos innovadores. Mejorar además de forma sustancial la eficiencia productiva es la meta de un proyecto de desarrollo colaborativo emprendido por Engel Austria y las empresas Bond-Laminates (de Brilon, Alemania, perteneciente al grupo Lanxess de Colonia, Alemania) y Leonhard Kurz (de Fürth, Alemania). En la feria K 2016, estas tres empresas presentarán el revolucionario resultado de su colaboración: el moldeo por inyección de una carcasa de paredes ultrafinas sumamente robusta, lista para montar y dotada de una sofisticada decoración en la superficie. Con paredes de tan solo 0,6 mm de grosor, esta pieza de muestra ofrecerá posibilidades totalmente nuevas.
La unidad de producción altamente automatizada que se podrá ver funcionando en el stand de Engel ha sido diseñada expresamente para poder combinar semiproductos de termo-plástico reforzado de fibra continua (Tepex) con films IMD. Esta unidad lleva integradas tres tecnologías de procesamiento que permiten decorar dentro del molde los componentes compuestos destinados a la producción en masa. La primera es Engel organomelt, que da forma y función a semiproductos termoplásticos reforzados con fibras continuas (fibras termoplásticas) en la fase de moldeo por inyección. La segunda es Engel variomelt, que optimiza la calidad de la superficie mediante un control variotérmico de la temperatura del molde. Y la tercera es IMD (In-Mould Decoration o decoración en el molde), que otorga a la superficie un acabado óptico y funcional directamente en el molde. El corazón de la unidad de producción está formado por tres unidades: una máquina de moldeo por inyección Engel insert 500V/130 single provista de una unidad IMD de rodillo a rodillo, un robot de seis ejes Engel easix que manipula las piezas acabadas y semiacabadas y un horno de infrarrojos que precalienta las fibras termoplásticas y que también ha sido diseñado y cons-truido por Engel..
Lo especial de este nuevo método es que el semiproducto de termoplástico reforzado de fibra continua se transforma, se moldea y se decora en un solo paso. Para lograr una cohe-sión directa del material, Bond-Laminates y LEONHARD KURZ han perfeccionado tanto sus materiales como las tecnologías de moldeo y de proceso necesarias para procesarlos, lo-grando así un alto grado de integración. Tradicionalmente, para que los componentes com-puestos adquieran un acabado resistente y de alta calidad en la superficie, después del moldeo por inyección se deben someter a operaciones de tratamiento y pintura. La produc-ción integrada, en cambio, elimina varios pasos de trabajo, reduciendo no solo el tiempo y el costo de fabricación de los componentes, sino también su impacto ecológico. El proceso integrado, además de gastar menos energía, reduce significativamente el consumo de mate-rias primas y sustancias químicas de procesamiento.
Tanto el robot multieje ENGEL easix como el horno de infrarrojos están totalmente inte-grados en la unidad de control CC300 de la máquina de moldeo por inyección. Gracias a ello, desde la pantalla de la máquina de moldeo por inyección se puede controlar de manera centralizada el precalentamiento de los semiproductos. Las temperaturas y los tiempos de calentamiento se guardan con los datos del proceso de moldeo por inyección, lo cual simpli-fica las tareas de documentar, evaluar y dar seguimiento al proceso global.
En la feria K 2016, ENGEL presentará por primera vez los hornos de infrarrojos como una serie completa. Están disponibles en cinco tamaños distintos, con una superficie de calen-tamiento de hasta 1110 x 1610 mm que permitirá procesar semiproductos grandes (por ejemplo módulos de puerta completos o extremos frontales para el sector automotriz). Los hornos de infrarrojos ENGEL se caracterizan por una gran homogeneidad térmica. Los ra-diadores individuales se pueden controlar por separado, lo cual permite también calentar eficientemente semiproductos pequeños.
La máquina vertical Engel insert se presentará en Dusseldorf con un diseño optimizado que hace su uso más ergonómico. Entre otras características, el nuevo diseño facilita el acceso a la unidad de cierre, un aspecto importante cuando el proceso no es automático sino manual.
Las inyectoras Engel se pueden adquirir con una unidad de inyección vertical u horizontal. La versión vertical de la máquina de moldeo por inyección que se exhibirá en la feria impresiona por el poco espacio que requiere. En esta versión, también el armario de control eléctrico está montado en vertical, por lo que la máquina apenas requiere más espacio que el que ocupa la unidad de cierre. Durante mucho tiempo, las inyectoras Engel insert V solo se podían adquirir con fuerzas de cierre de hasta 160 toneladas. Ahora, sin embargo, la serie se ha ampliado e incluye un modelo de 200 toneladas y otro de 250.
Otro de los factores que contribuyen a que el sistema completo ocupe tan poco espacio es el robot multieje Engel easix, que también se exhibirá en la feria de Düsseldorf. Incluso en su versión estándar, los modelos Engel easix (basados en tecnología del fabricante Kuka) permiten establecer zonas prohibidas y, de ese modo, minimizar el área que es preciso blindar.
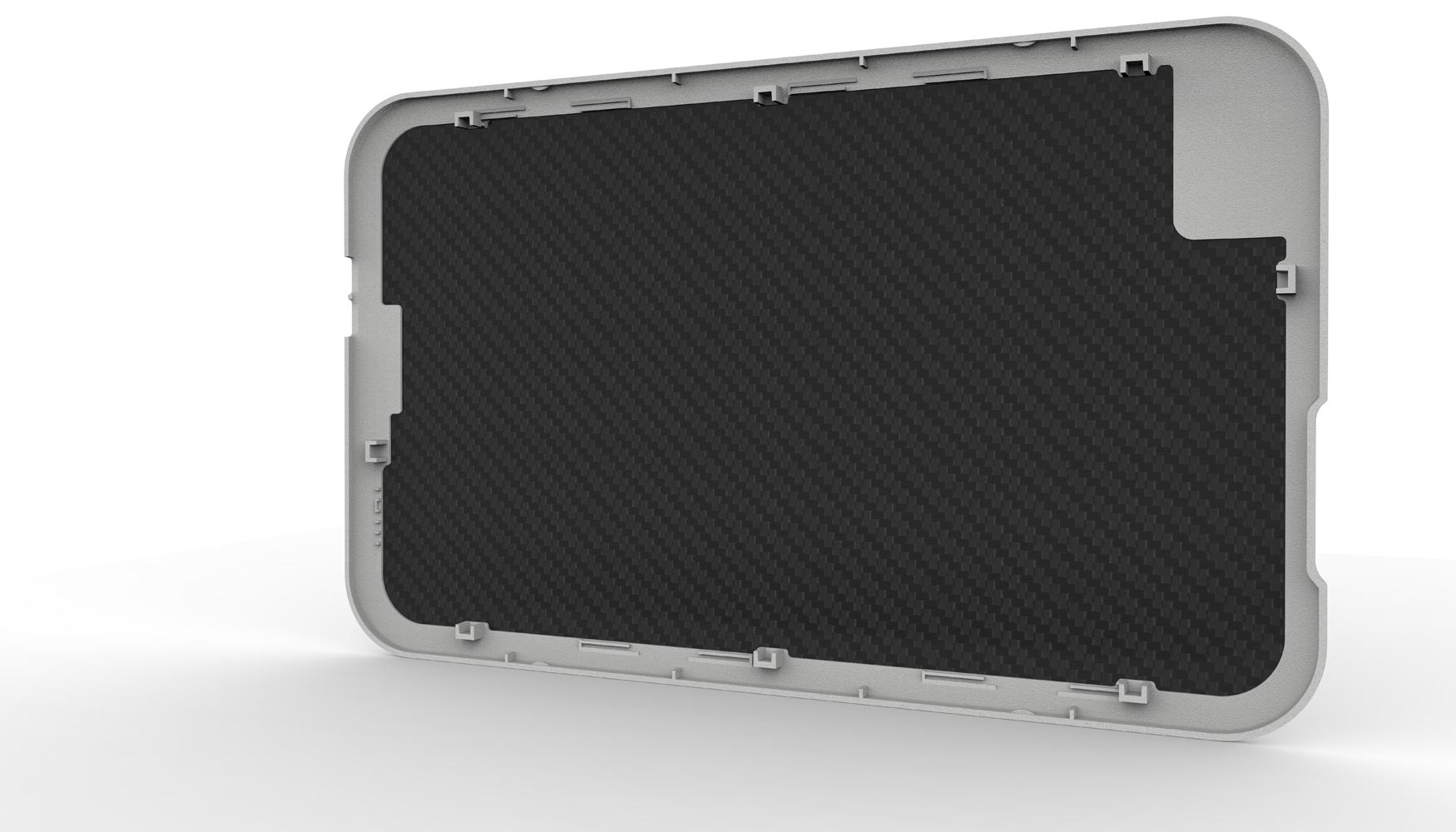
Sumamente robustas y delgadas: las carcasas tienen paredes de tan solo 0,6 mm de grosor y salen de la máquina de moldeo por inyección listas para montar. (Imagen: Engel).
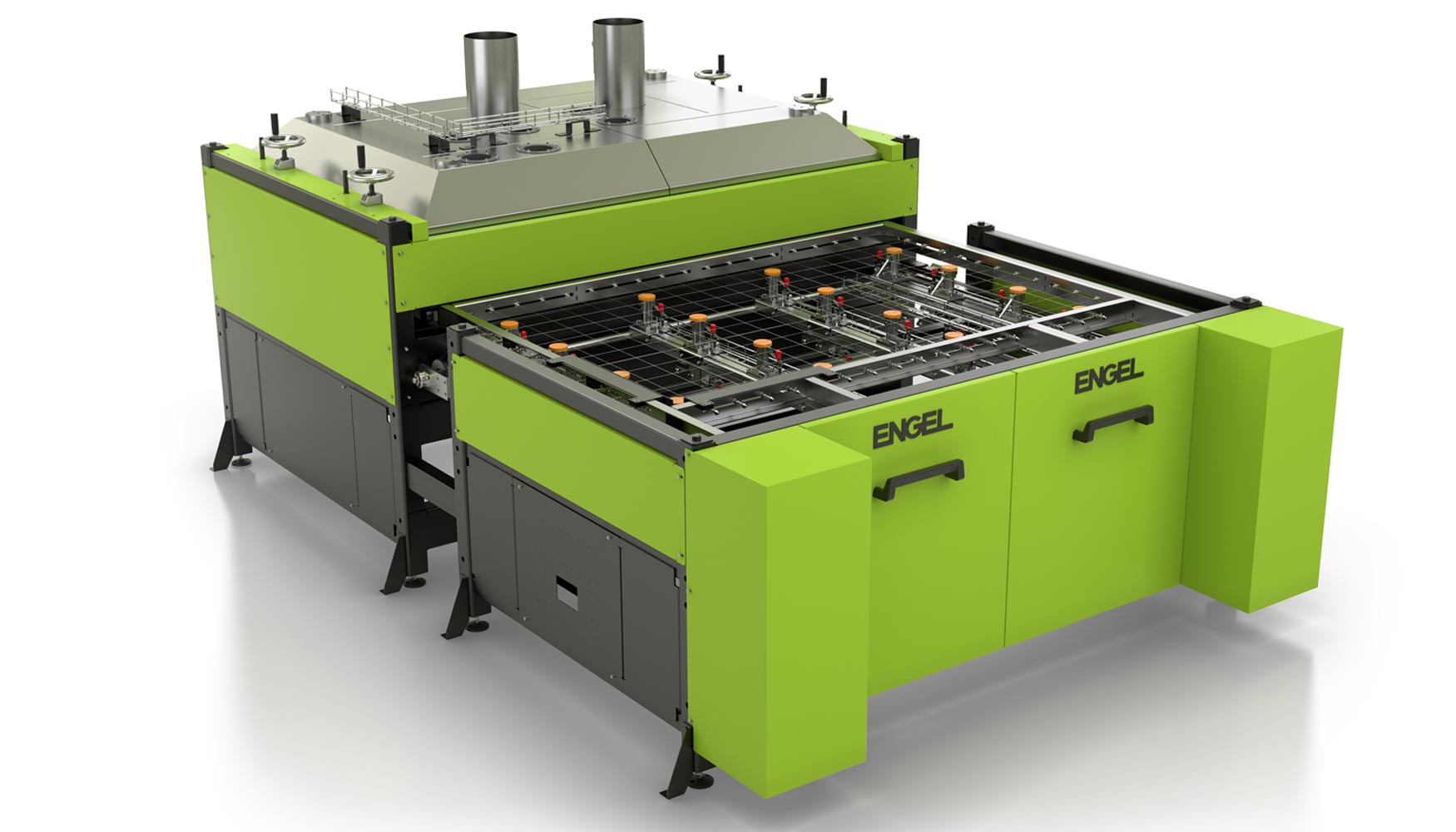
Moldeo técnico: polimerización in situ combinada con moldeo por inyección
La polimerización in situ de ε-caprolactama ofrece nuevas oportunidades para la producción, mediante matriz termoplástica, de componentes compuestos reforzados con fibra. Esta tecnología permite poner en práctica procesos muy eficientes y diseñar con flexibilidad componentes compuestos.
Partiendo de fibras secas reforzadas y preformadas (preformas), el método in situ reúne la polimerización y el moldeo en una sola máquina de moldeo por inyección. Desde que el primer prototipo de máquina se presentó hace cuatro años, Engel no ha dejado de optimizar los componentes del sistema. El resultado es una unidad reactiva que se puede combinar con distintos tipos de máquina de moldeo por inyección de Engel. Las grandes diferencias entre esta nueva unidad y el prototipo de 2012 también son tecnológicas. Engel es el único proveedor del mercado que puede fundir y procesar el monómero sólido de manera adecuada a cada necesidad. Las ventajas son una gran reducción del tiempo de permanencia del material, una menor carga térmica y, como resultado, una mayor calidad del producto. Engel ve en este método un gran potencial tanto para el sector de la automoción como para otras aplicaciones, por ejemplo en el ámbito del moldeo por inyección técnico.
En colaboración con Schöfer (Schwertberg, Austria) y otros socios de proyecto, Engel presentará en la feria K 2016 una unidad de producción que casi está lista para ser fabricada en serie y sirve para elaborar componentes compuestos de fibra termoplástica. Como muestra de su amplia gama de posibilidades, Engel exhibirá una Engel v-duo 1560/700 fabricando palas reforzadas con fibra. La unidad de cierre está equipada con una mesa deslizante provista de dos semimoldes a la que se puede acceder con suma facilidad. Las fibras de refuerzo secas preformadas se colocan en la primera cavidad y en ellas se infiltra la matriz reactiva (ε-caprolactama). Para ello, la ε-caprolactama sólida se funde y se introduce dosificadamente en la unidad reactiva. Gracias a la baja viscosidad que el monómero tiene cuando está fundido, las fibras secas se pueden humedecer especialmente bien. De ese modo, la polimerización de poliamida 6 da lugar a un compuesto muy resistente.
Durante el proceso reactivo no se supera la temperatura de fusión del polímero, por lo que el semiproducto compuesto se puede transferir a la segunda cavidad nada más ser producido, y en ella adquiere sus características funcionales mediante moldeo por inyección. Para ello se inyectan nervaduras de refuerzo y contornos de PA 6 reforzados con fibras de vidrio cortas. La polimerización y el moldeo por inyección se realizan paralelamente. Un robot doble Engel viper 40 manipula las preformas de fibra y las piezas acabadas, y transfiere los semiproductos.
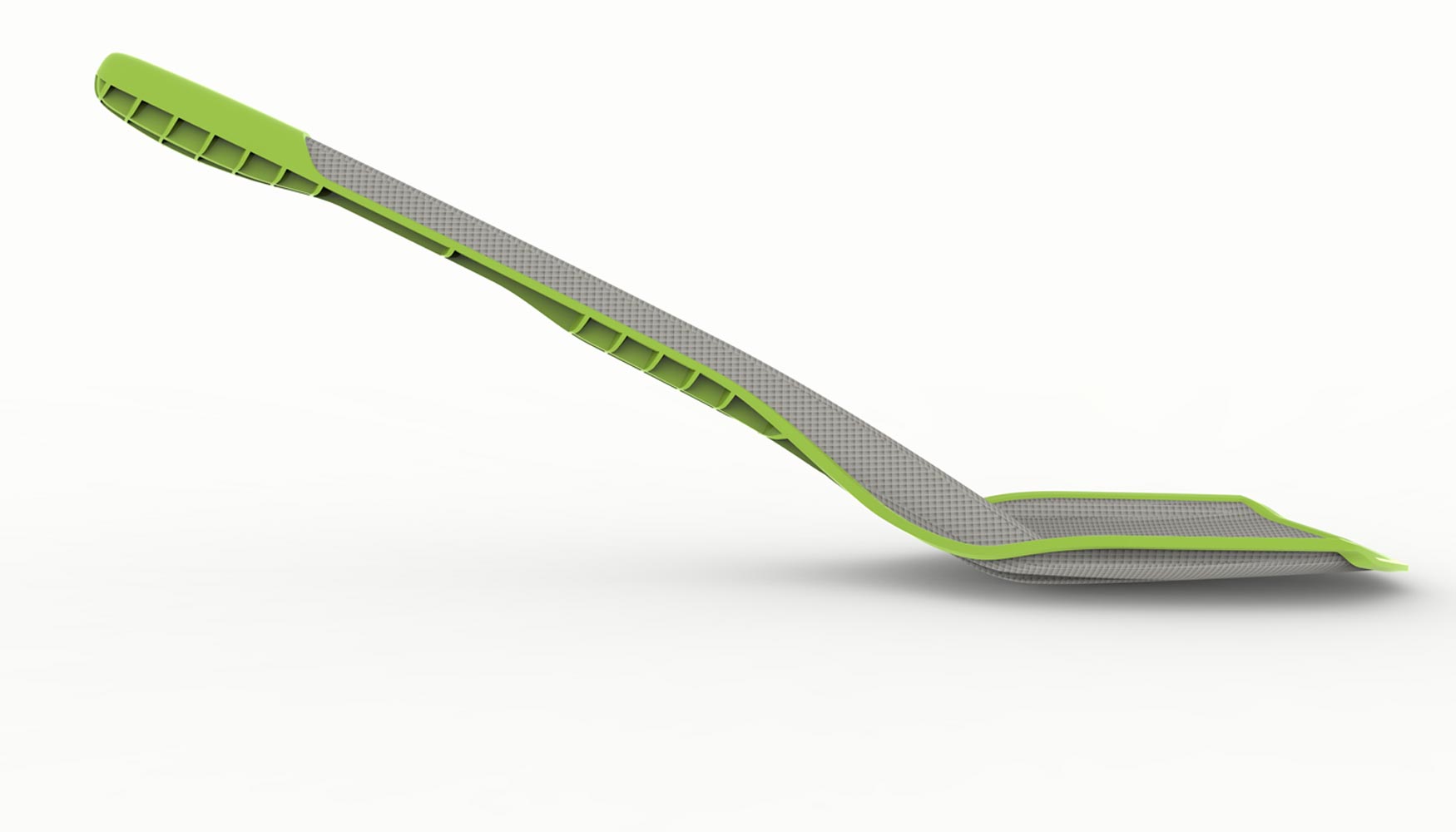
La polimerización in situ de ε-caprolactama ofrece nuevas posibilidades de producir con una matriz termoplástica componentes compuestos reforzados con fibra, no solo para el sector de la automoción. (Imágenes: Engel).
Con la serie Engel v-duo, Engel ha desarrollado una máquina de moldeo por inyección comparativamente compacta y eficiente energéticamente que se adapta específicamente a las aplicaciones con compuestos de fibras y hace la producción mucho más rentable. Su unidad de cierre vertical es accesible desde los cuatro lados, no solo desde dos. Sobre todo al procesar semiproductos de fibra con dimensiones inestables, suele resultar útil trabajar siguiendo la dirección de la gravedad.
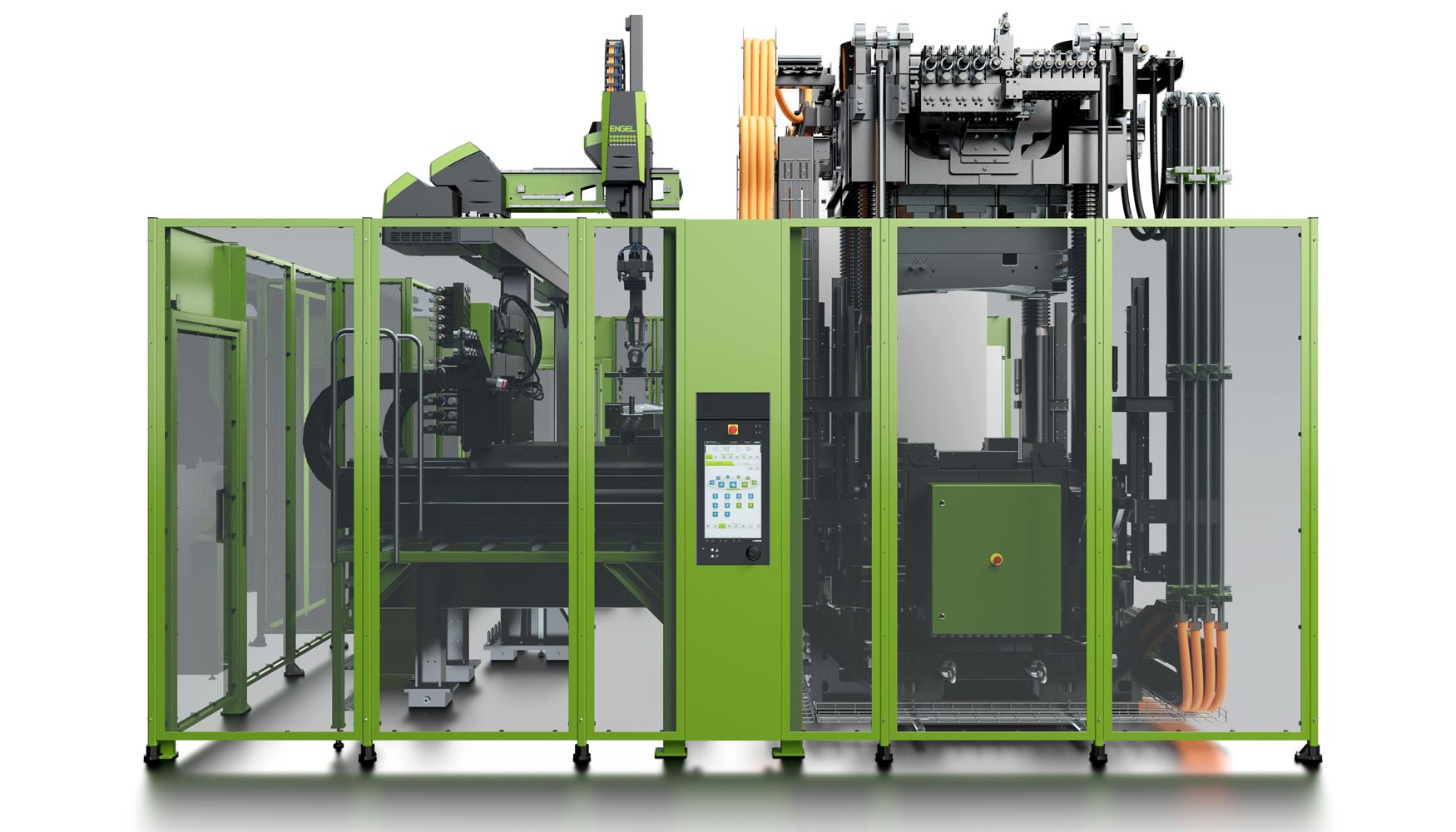
Con la serie Engel v-duo, Engel ha desarrollado una máquina de moldeo por inyección comparativamente compacta y eficiente energéticamente que se adapta específicamente a las aplicaciones con compuestos de fibras y hace la producción mucho más rentable. (Imagen: Engel).
Engel elast: la tecnología sin columnas que garantiza procesos estables y muy eficientes Uso fiable de procesos multicomponente con LSR
La tecnología multicomponente también está ganando importancia en el procesamiento de LSR (caucho de silicona líquida). En muchas aplicaciones, el moldeo por inyección es la única manera de unir los termoplásticos con la silicona en capas estables. Un ejemplo de ello son las membranas de acumulación de presión que se usan en los depósitos de compensación de presión. En la feria K 2016, Engel mostrará cómo fabricar estas piezas de dos componentes (PBT y LSR) utilizando una máquina de moldeo por inyección Engel victory 200H/200L/160 combi con un robot lineal Engel viper 40 integrado. El molde y las bombas dosificadoras de LSR son de Elmet, una empresa de Oftering (Austria) que colabora con Engel. El LSR es un producto de Wacker Silicones, empresa con sede en Burghausen (Alemania).
La fabricación de piezas de dos componentes permite aprovechar al máximo la eficiencia de la unidad de cierre sin columnas de la máquina Engel victory. El voluminoso molde llega hasta el borde mismo de la platina de montaje, y cabe por tanto en una máquina de moldeo por inyección de 160 toneladas comparativamente compacta. El segundo factor que conduce a un aumento de la eficiencia es la automatización. El robot lineal puede acceder a las cavidades directamente desde el lateral sin tener que salvar obstáculos, y puede trabajar en ellas de manera segura.
El tercer factor que contribuye decisivamente a la eficiencia global es la estabilidad del proceso, que está garantizada por la unidad de cierre sin columnas. El divisor de fuerzas patentado, el Engel force divider, permite que la platina móvil vaya perfectamente paralela al molde mientras la fuerza de cierre se está creando y garantiza que la fuerza de cierre se distribuya de manera uniforme por toda la superficie. De esta forma, tanto las cavidades externas como las internas se mantienen cerradas con la misma fuerza, lo que reduce el desgaste del molde e incrementa la calidad del producto. Un procesamiento del caucho de silicona líquida (LSR) prácticamente sin rebabas, generación de desechos, necesidad de reelaboración y completamente automatizado es el requisito previo para poder producir de forma económica productos de silicona líquida de alta tecnología.
Duradero, transparente y translúcido
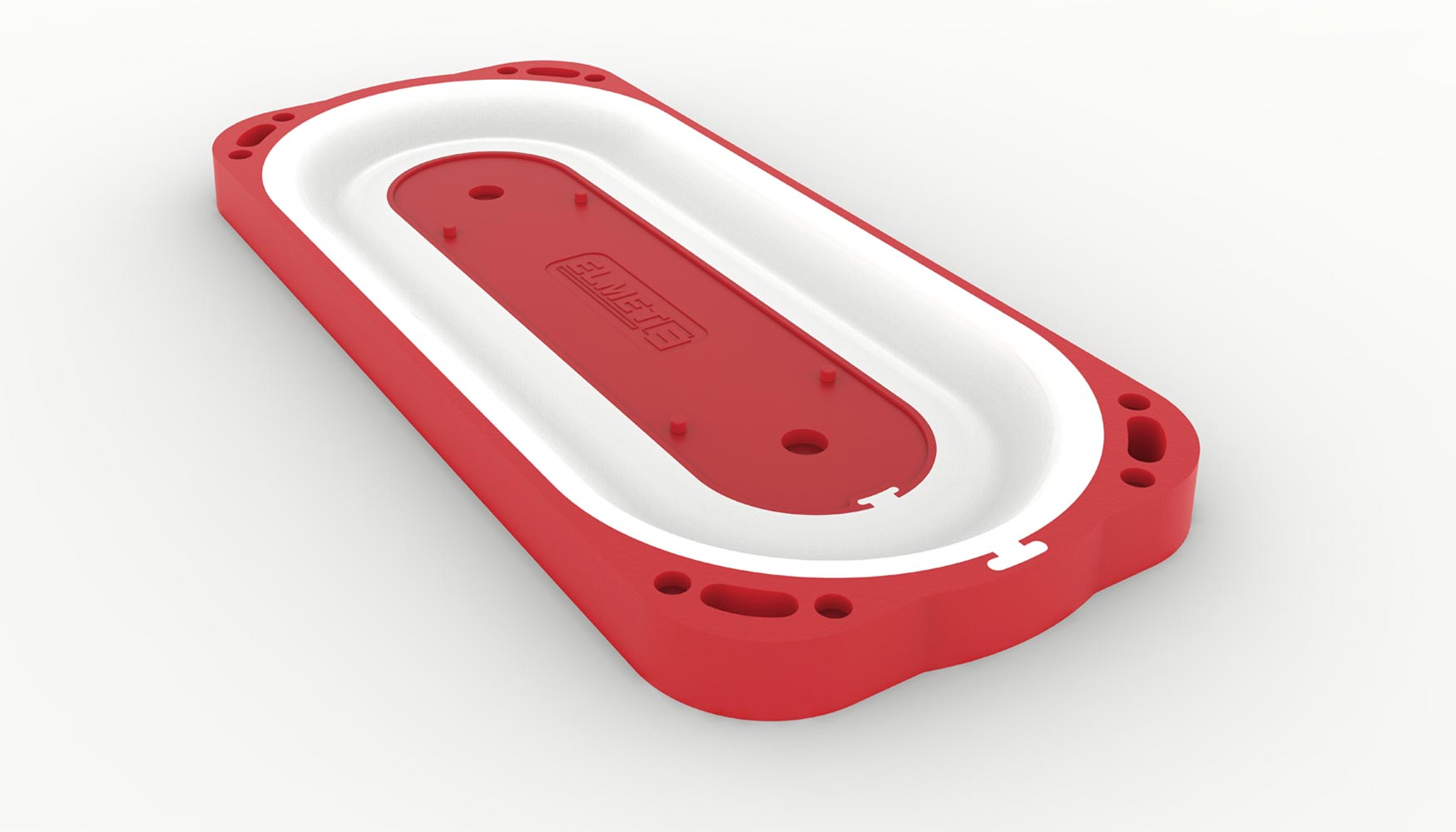
En muchas aplicaciones, el moldeo por inyección es la única manera de unir los termoplásticos con la silicona en capas estables. Un ejemplo de ello son las membranas de acumulación de presión que se usan en los depósitos de compensación de presión. (Imagen: Engel).
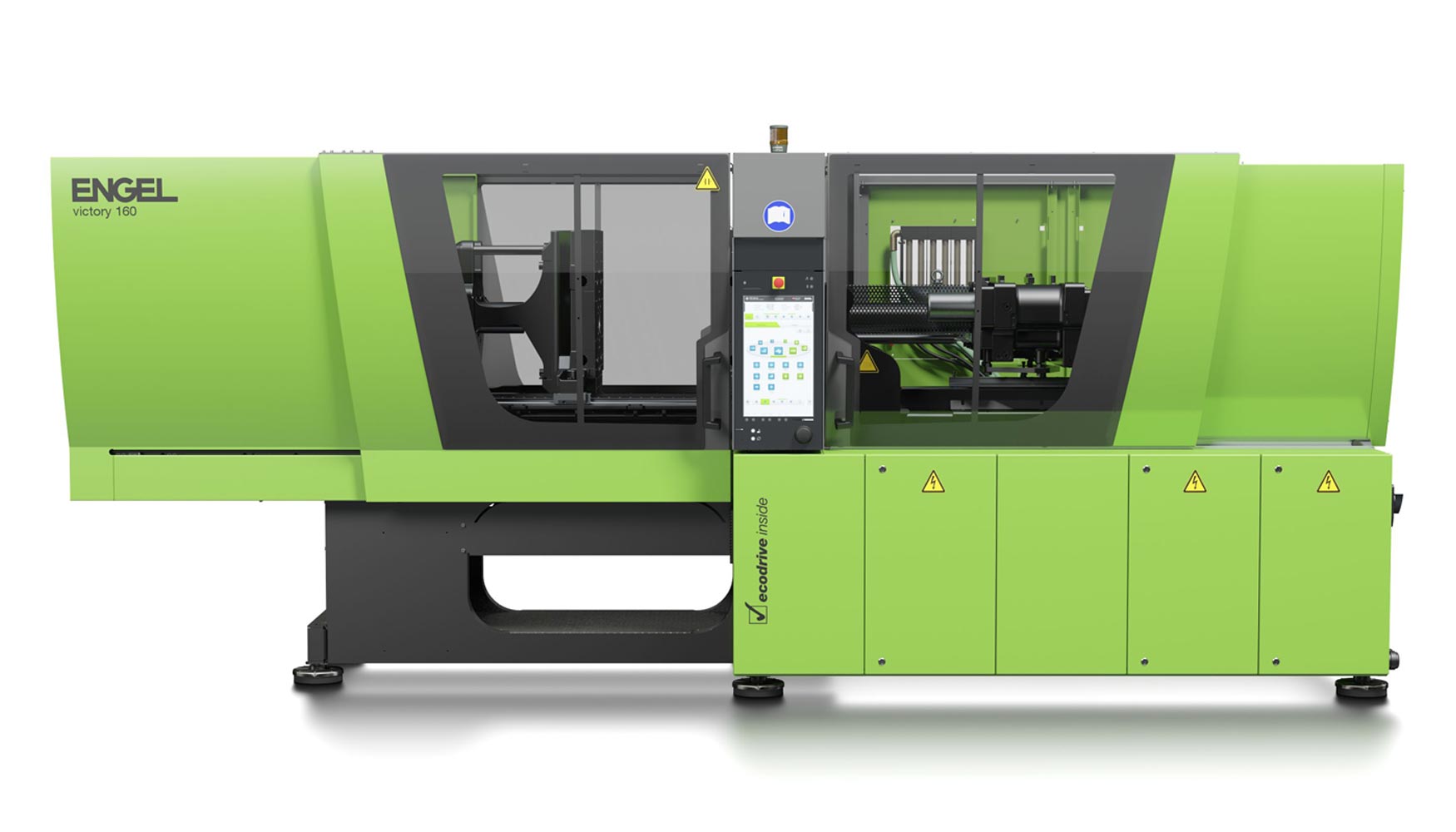
Gracias a su unidad de cierre exenta de barreras, la máquina de moldeo por inyección sin columnas Engel victory consigue una gran eficiencia en los procesos multicomponente que utilizan LSR. (Imagen: Engel).
Para el sector médico: reproducibilidad aún mayor gracias a inject 4.0
Cepillos interdentales 1-K con hasta 500 cerdas
'Scrub!' es el nombre del nuevo cepillo interdental que la empresa pheneo (de Bremen, Alemania) lanzará próximamente al mercado. Su estreno exclusivo tendrá lugar en la feria K 2016, ya que también su proceso de producción constituye una novedad mundial. Mediante moldeo por inyección de un solo componente, se pueden producir directamente hasta 500 cerdas con varilla y mango. En la feria se usará la versión para salas limpias de la máquina de moldeo por inyección totalmente eléctrica Engel e-motion 170/100 T para procesar un compuesto de tres componentes. El molde de precisión de alto rendimiento —provisto de ocho cavidades y extremadamente delicado en la zona de las cerdas— es de la empresa Hack Formenbau (Kirchheim unter Teck, Alemania), mientras que Hekuma (Eching, Alemania) ha aportado el autómata. En la presentación podrá verse una unidad de producción automatizada y altamente integrada con diseño modular HEKUflex de Hekuma. Tras el moldeo por inyección, una cámara revisa las piezas y aquellas que son buenas se embalan automáticamente en bolsas para la venta al detalle que contienen 16 piezas cada una. La unidad de producción entrega una bolsa cada cuatro segundos.
El diseño monocomponente y el altísimo grado de integración del proceso multiplican la eficiencia productiva en comparación con otros productos y métodos consolidados en el mercado. Hasta ahora, los cepillos interdentales constaban de tres componentes que normalmente se producían en procesos separados: el mango, una malla metálica y los filamentos. La nueva tecnología de Engel, Hack y Hekuma —socios en la creación de este sistema— permite por primera vez producir cepillos dotados de varillas sumamente pequeñas con gran cantidad de cerdas finas empleando el moldeo por inyección de un solo componente. A ello también ha contribuido el compuesto utilizado. La longitud de la fibra de vidrio seleccionada da estabilidad al mango y a la varilla sin penetrar en las zonas de las cerdas, que son muy delicadas.
Llenar completamente ocho cavidades con un máximo de 500 cerdas cada una y un peso total de inyección de tan solo 1,93 gramos supone un difícil reto no solo para el molde, sino también para la inyectora. La tecnología de accionamiento, totalmente eléctrica, garantiza la máxima precisión en los movimientos de la máquina, y los productos iQ de la gama inject 4.0 de Engel compensan posibles fluctuaciones en las condiciones ambientales o la materia prima. En cada inyección, iQ weight control analiza la evolución de la presión en las distintas posiciones del husillo, ajustando el punto de conmutación y el perfil de inyección a las condiciones actuales. Al mismo tiempo, iQ clamp control monitoriza la respiración del molde para cada inyección por separado y ajusta automáticamente la fuerza de cierre. Como tercer sistema de asistencia, Engel e-flomo mantiene constante la temperatura del molde. En esta aplicación, el control descentralizado y ejercido directamente en la máquina garantiza la máxima estabilidad del proceso, evita piezas desechadas y garantiza un costo unitario competitivo.
Esta nueva tecnología ofrece grandes posibilidades en diversos sectores, desde la medicina hasta la cosmética. Los cepillos aplicadores de rímel, por ejemplo, también deben producir-se, como los cepillos interdentales, en grandes lotes y a un bajo costo unitario.
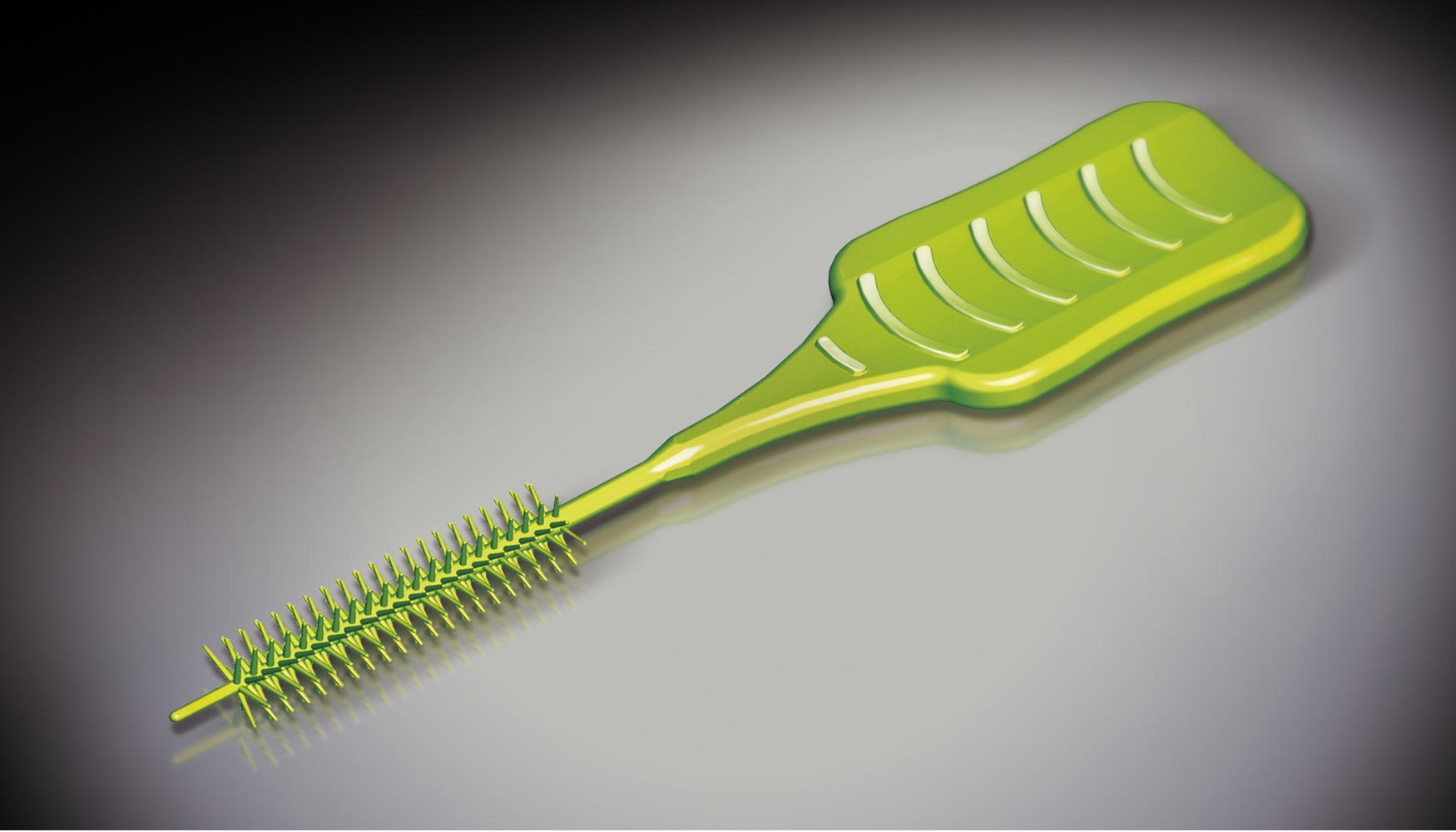
Hasta 500 cerdas se pueden moldear mediante el proceso de inyección de un solo componente. (Imagen: Engel).
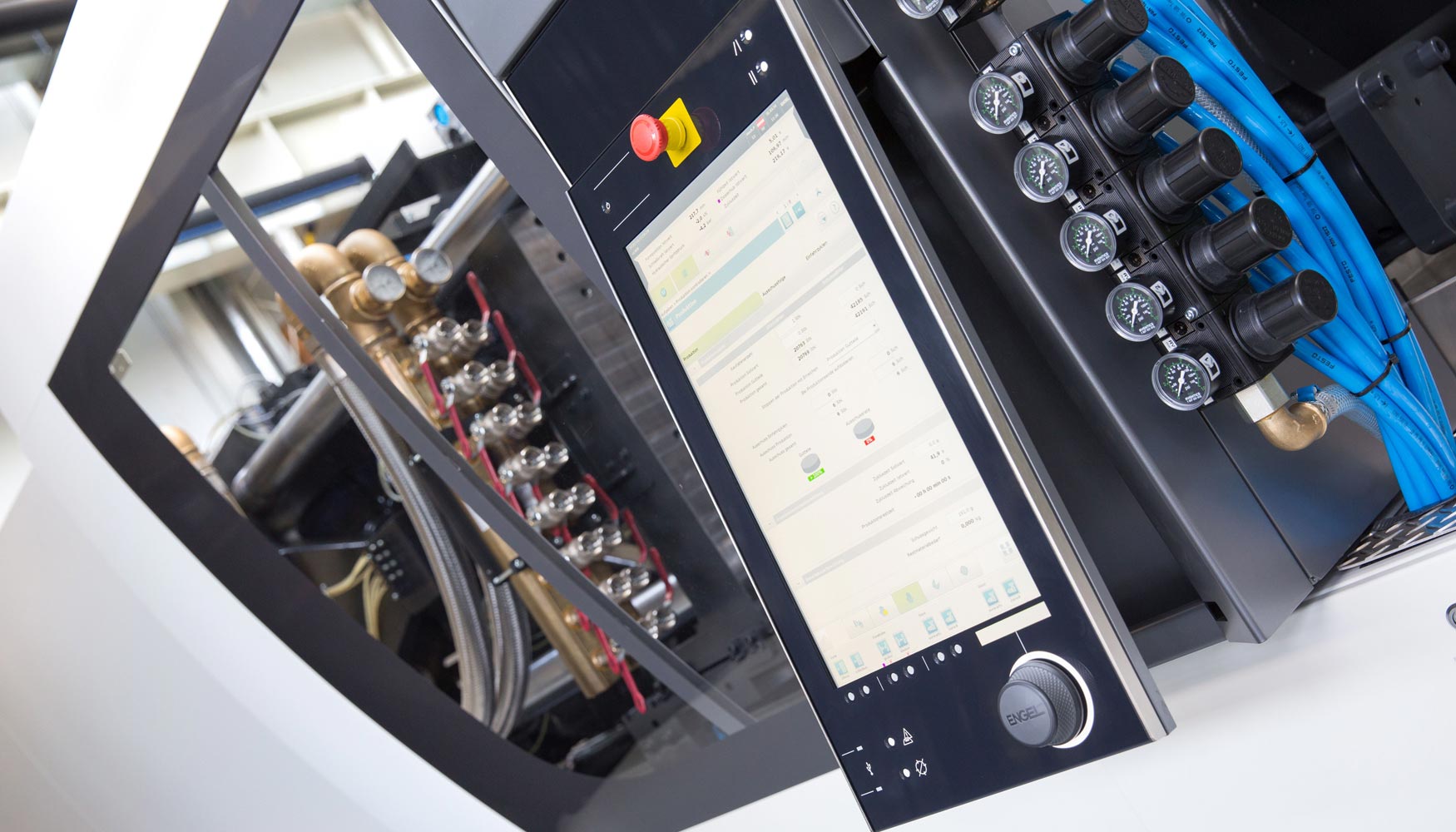
Los sistemas de asistencia integrados en la unidad de control CC300 de la máquina de moldeo por inyección Engel e-motion (perteneciente a la gama 4.0 de Engel) compensan las posibles fluctua-ciones del proceso antes incluso de que se produzcan piezas inservibles. (Imagen: Engel).
Envases: la integración del proceso reduce el costo unitario
Moldeo por inyección y soplado integrado hasta en 96 cavidades
El moldeo por inyección y soplado permite producir, de manera rentable y en un solo paso, recipientes pequeños listos para usar. Hasta ahora, sin embargo, el número de cavidades posibles era limitado. Engel se ha asociado con Foboha (Haslach, Alemania) y Alpla Werke Alwin Lehner (Hard, Austria) para mejorar la integración del proceso y permitir el uso de moldes multicavidad que acortan significativamente los ciclos. La tecnología de cubo permite usar hasta 96 cavidades sin prolongar la duración del ciclo ni perder precisión, reduciendo así el costo unitario para grandes volúmenes de producción. En la feria K 2016, Engel demostrará las posibilidades del nuevo proceso de moldeo por inyección y soplado usando como ejemplo la producción de envases.
En una máquina de moldeo por inyección totalmente eléctrica Engel e-motion 740/220 T WP, y empleando un molde cúbico de 8 cavidades, fabricará prototipos de recipientes de polipropileno que demostrarán la eficacia de esta tecnología. Los recipientes han sido diseñados por Alpla para un cliente asiático que hasta ahora vendía sus productos en envases de cristal. Cambiando el material, se han reducido los costos de producción y el peso de los envases, y se ha aumentado la seguridad del consumidor.
Para lograr ciclos cortos, mientras se moldean preformas por inyección, en la posición opuesta del molde se soplan las preformas ya elaboradas. Al mismo tiempo, el robot de seis ejes Engel easix integrado en la unidad de producción retira de la cuarta posición los recipientes terminados y los coloca en la cinta transportadora con la abertura hacia arriba. De este modo, toda la manipulación se sincroniza con la operación de inyección y soplado y no se alarga la duración del ciclo. Una cubierta aislante situada en la posición 2 evita que las preformas se enfríen. El peso de inyección es de 8 gramos por recipiente.
La tecnología de moldeo por inyección y soplado es de Bauer Compressors, una empresa colaboradora con sede en Aix-Les-Bains (Francia). Como parte integral del proceso, la pre-sión del gas se puede controlar mediante la unidad de control CC300 de la máquina de moldeo por inyección Engel.
A la hora de desarrollar esta tecnología, se ha prestado especial atención a la estabilidad y la precisión del proceso. Tanto en la zona de la rosca como en el cuerpo del recipiente se han respetado tolerancias sumamente ajustadas. El proceso global solo puede ofrecer y mantener una alta calidad si las preformas ya tienen un grosor de pared muy constante. La tecnología de accionamiento totalmente eléctrica de la inyectora Engel e-motion contribuye significativamente a eliminar por completo los defectos de pro-ducción. Especialmente importantes en esta aplicación son los sistemas de asistencia inteligentes iQ weight control e iQ clamp control. El análisis constante de los parámetros esenciales del proceso permite detectar hasta el más mínimo cambio en las condiciones ambientales y en la materia prima, y compensarlo automáticamente en la misma inyección.
También el control de la temperatura repercute en la calidad. Seis baterías mezcladoras de agua Engel e-flomo, cada una equipada con cuatro circuitos de regulación de temperatu-ra, monitorizan continuamente y controlan activamente los caudales.
La presentación que tendrá lugar durante la feria demostrará de manera impresionante cómo se puede combinar la productividad con la máxima fiabilidad mediante una máquina totalmente eléctrica de alto rendimiento que logra un alto grado de integración de los procesos y emplea sistemas de asistencia inteligentes. Con ello se abre una amplia gama de posibilidades para aplicaciones avanzadas de moldeo por inyección y soplado. Además de para fabricar recipientes, el proceso se puede emplear para producir biberones o tarros de cosméticos. Para poder ser usado en el sector farmacéutico, todo el sistema ha sido construido conforme a las normas cGMP.
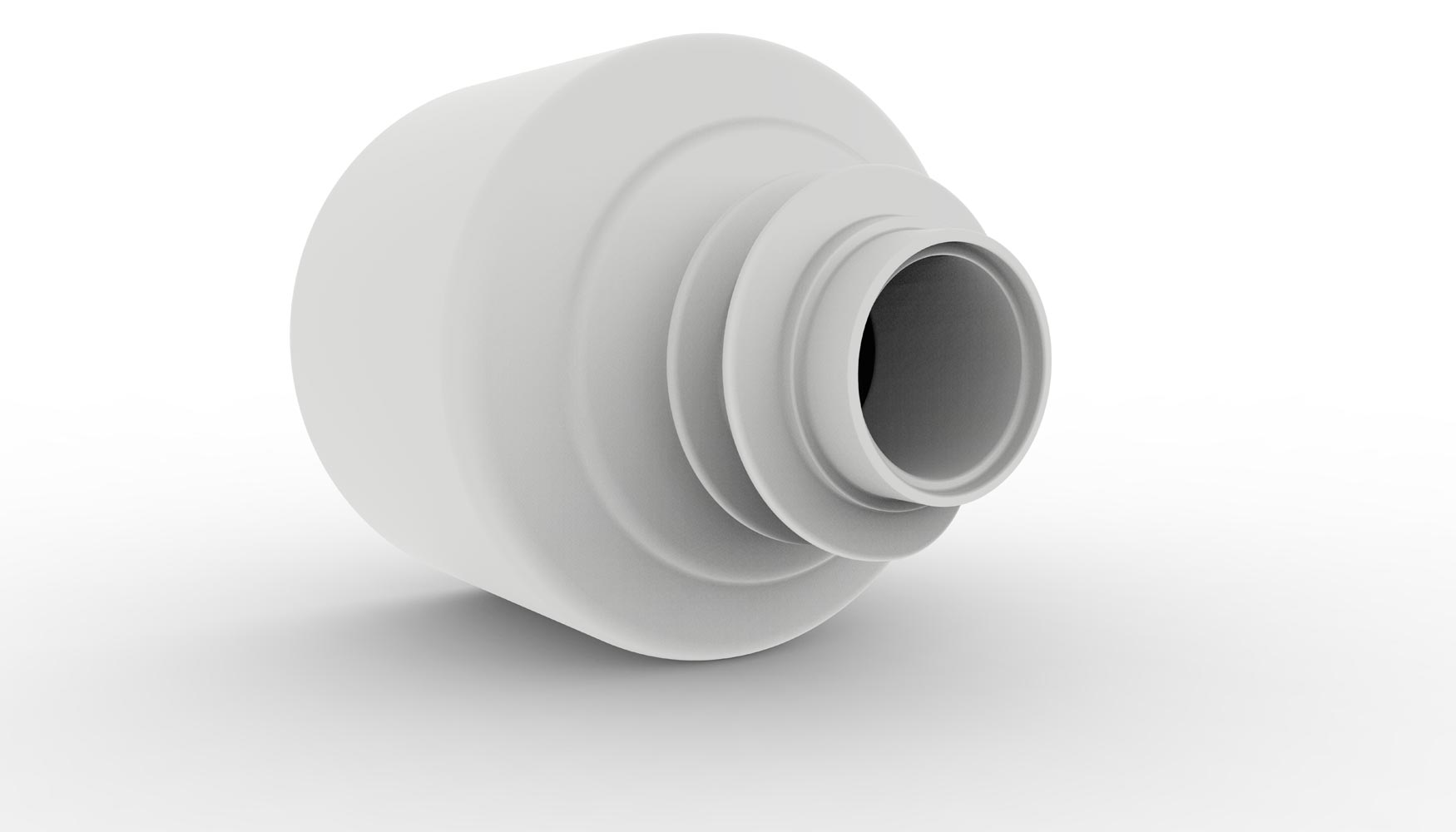
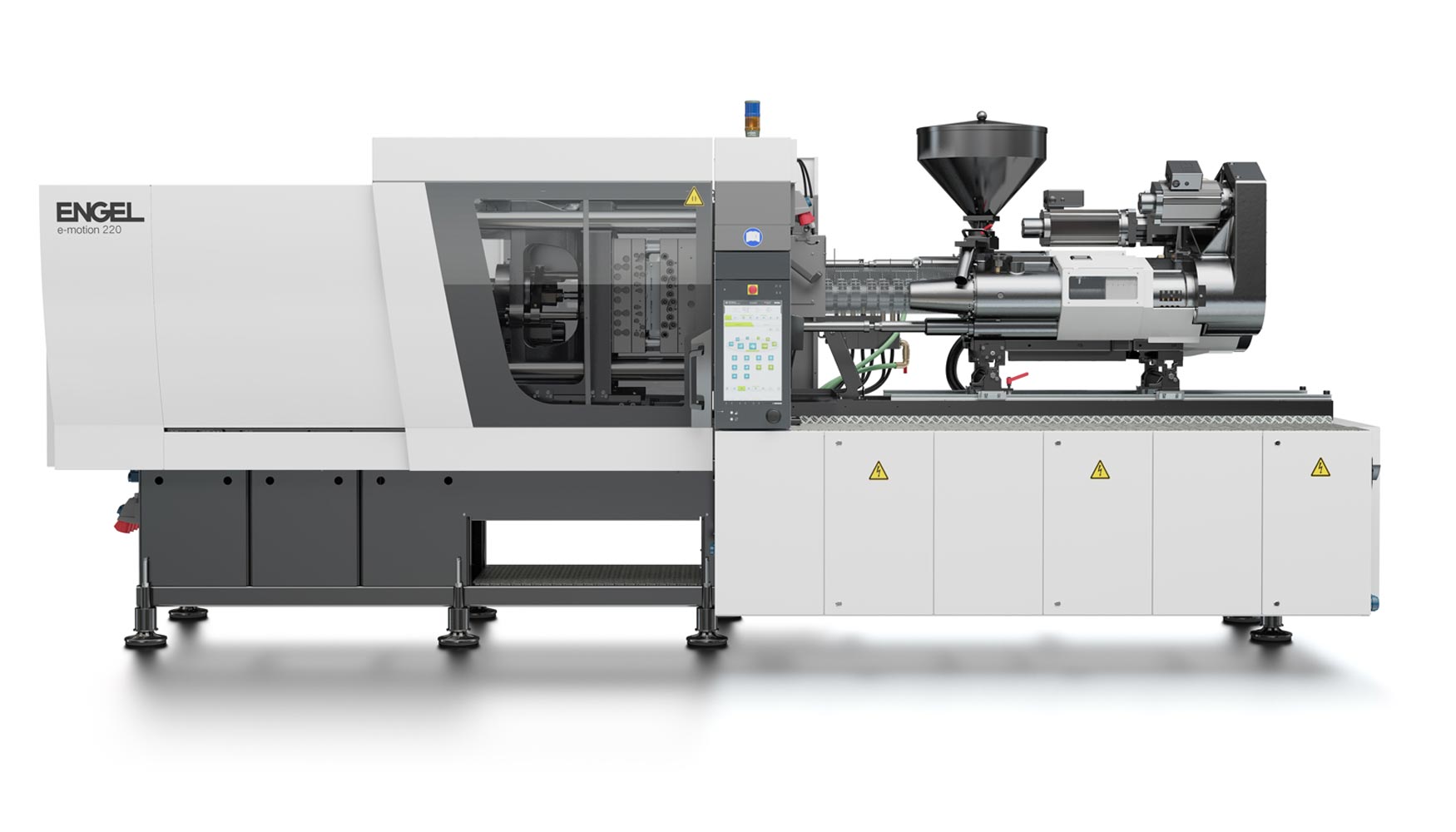
Alto rendimiento en una nueva dimensión
Gracias a su innovador concepto de accionamiento, las máquinas de moldeo por inyección de la serie Engel e-speed garantizan una gran eficiencia y una velocidad de funcionamiento continuamente alta aunque los pesos de inyección y las fuerzas de cierre sean elevados. Sin embargo, en la feria K 2016 Engel irá un paso más allá. Allí demostrará cómo ahora, gracias a la integración de IML, se pueden fabricar mediante moldeo por inyección envases largos de paredes delgadas listos para llenar. Engel presentará en Düsseldorf este avance produciendo cartuchos para los sectores de la construcción y el bricolaje. Para ello, combinará una máquina de moldeo por inyección Engel e-speed 500/90 con un autómata IML de la empresa Beck Automation (Oberengstringen, Suiza). El molde de 16 cavidades lo proporcionará Otto Hofstetter (Uznach, Suiza) y las etiquetas serán de Verstraete in mould labels, empresa colaboradora ubicada en Maldegem (Bélgica). Por primera vez será posible decorar cartuchos utilizando la tecnología IML. Y es que la complicada relación entre longitud y diámetro de los cartuchos requiere el uso de soluciones específicas IML.
Con la producción de cartuchos se aprovechan al máximo las ventajas de esta máquina híbrida, que tiene una unidad de cierre eléctrica y una unidad de inyección servohidráulica. Para moldear los cuerpos largos y huecos con un grosor de pared de solo 1,2 mm se precisa un gran dinamismo y una gran capacidad de inyección. Los ciclos conseguidos son muy cortos a pesar que el peso de inyección total (800 gramos) es relativamente alto. Un requisito básico para que el proceso IML sea muy eficiente es que los movimientos de la platina de montaje del molde sean muy precisos, algo que la Engel e-speed garantiza gracias a su unidad de cierre totalmente eléctrica.
En la feria K 2016, la máquina Engel e-speed de 5.000 kN con husillo de 90 mm se presentará por primera vez con su nuevo diseño. Como en la versión más grande (fuerza de cierre de 6.500 kN y husillo de 120 mm de diámetro), las toberas son de fácil acceso. El sistema hidráulico de la máquina también se ha optimizado. El resultado es un mayor dinamismo y, gracias a ello, una inyección más rápida y precisa. A partir de la K 2016, toda la gama Engel e-speed incluirá de serie la unidad servohidráulica ecodrive de Engel.
La excepcional eficiencia energética de la Engel e-speed ha contribuido en gran medida a su gran éxito en el mercado internacional de productos para envasado. Para evitar picos de carga cuando se trabaja a grandes velocidades y con fuerzas de cierre altas, un sistema que funciona según el principio de un volante almacena la energía de frenado de los movimientos de la platina y la transfiere de vuelta al motor cuando es necesario (por ejemplo cuando hace falta volver a acelerar la platina). Gracias a este sistema de almacenamiento de energía integrado, la Engel e-speed puede funcionar con una potencia conectada relativamente baja y, sobre todo, constante.
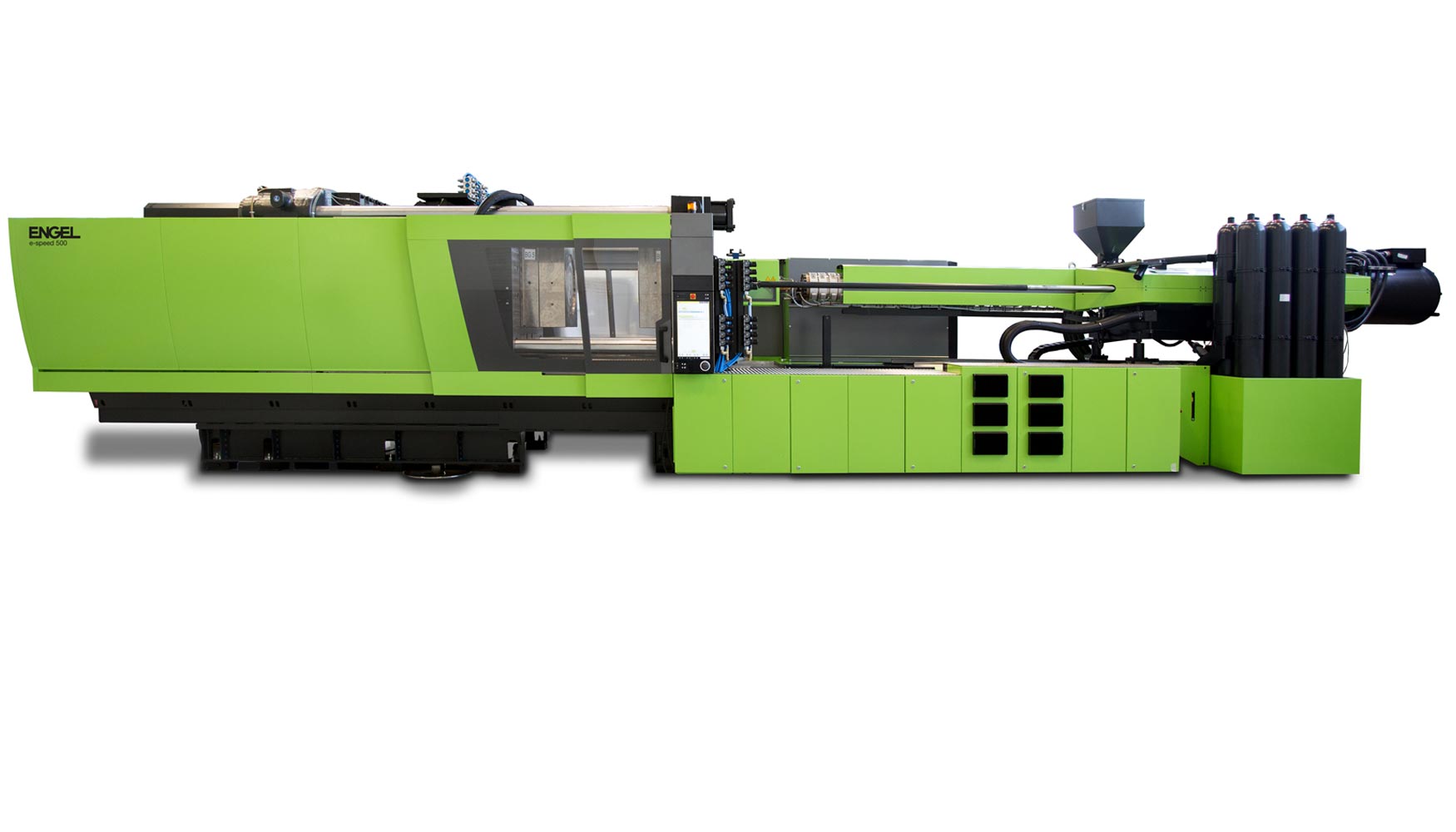
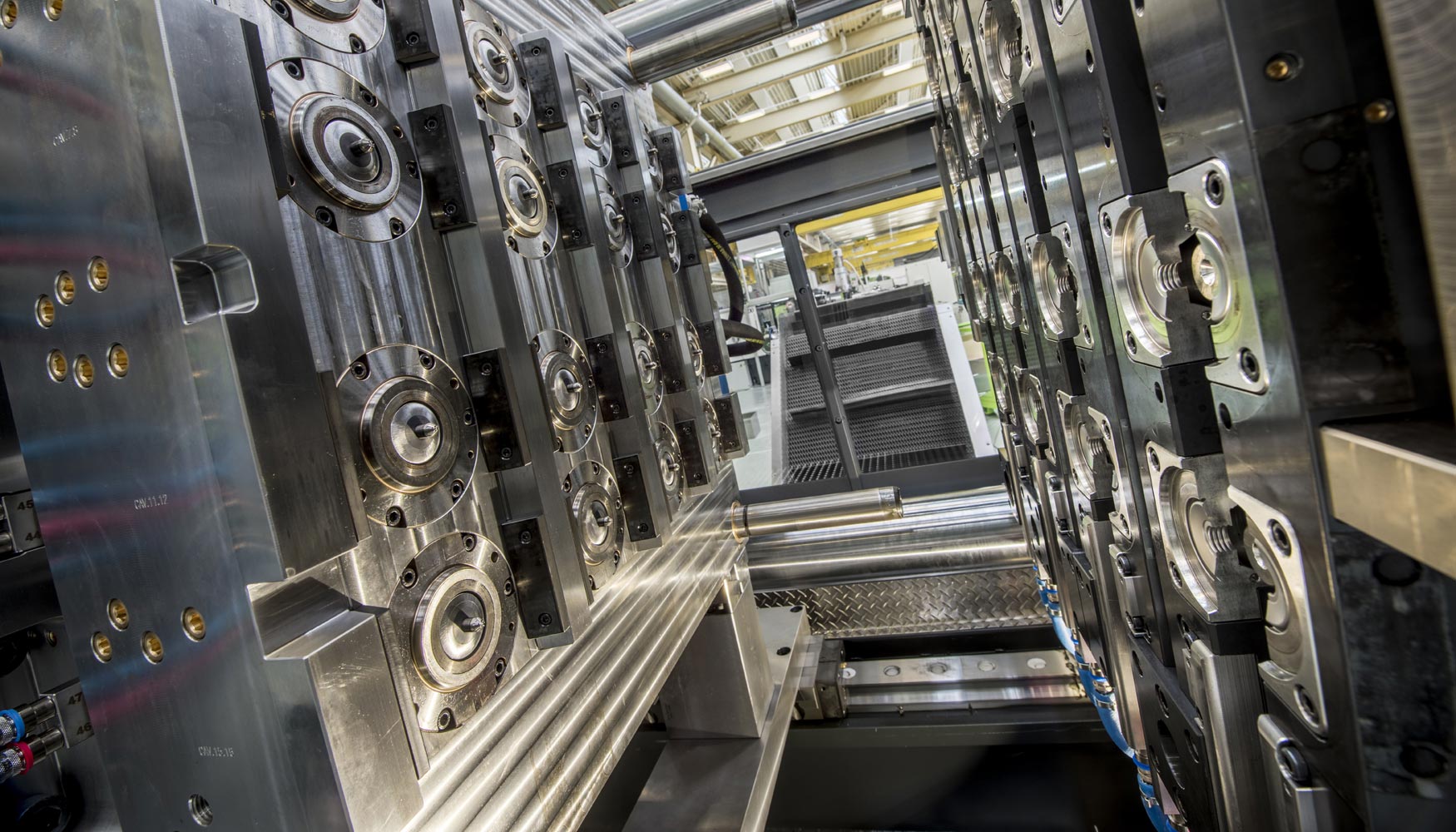
Engel en la K 2016: pabellón 15, stand C58
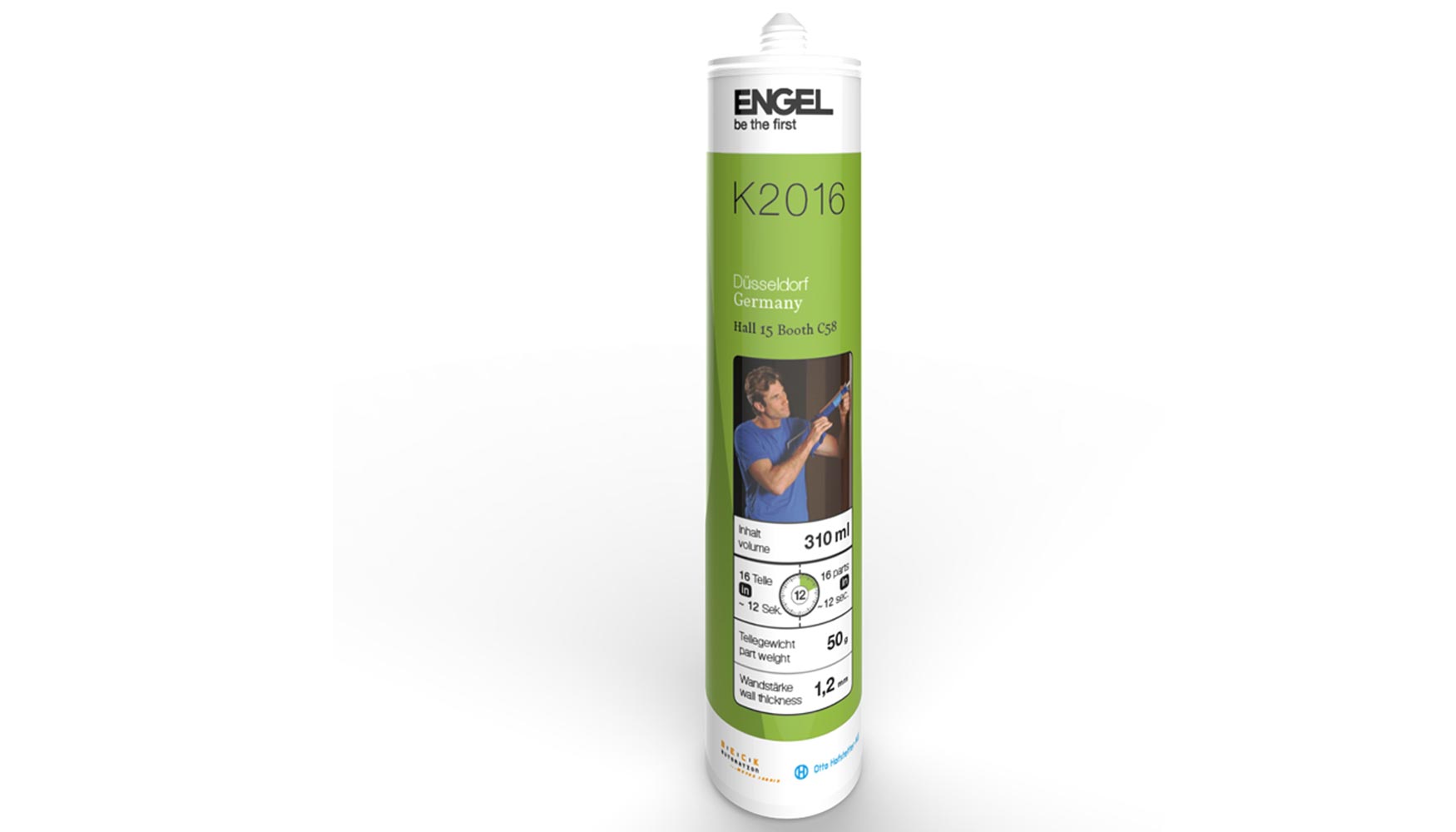