Exoesqueletos para aliviar la tensión
El profesor Jens P. Wulfsberg es jefe del Laboratorio de Ingeniería de Producción (LaFT) de la Universidad Helmut Schmidt de Hamburgo. En LaFT se están desarrollando ayudas ergonómicas Smart Assist en un equipo interdisciplinario. Según un folleto de LaFT, se trata de “sistemas de apoyo técnico en los que la gente está realmente interesada”. Ya se han desarrollado más de 20 exoesqueletos diferentes, desde órtesis de tobillo hasta guantes de musculación.
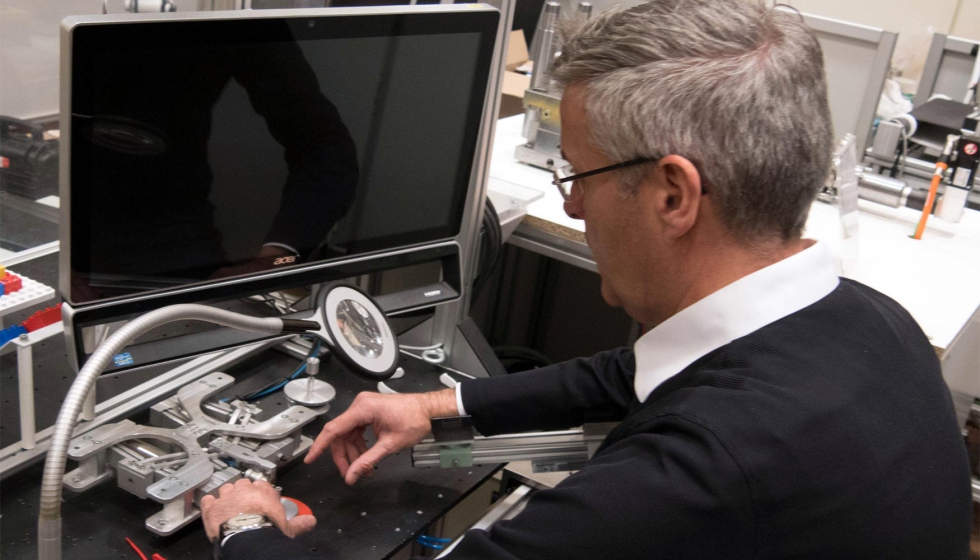
Los exoesqueletos deben ser asequibles, portátiles y ligeros.
“El objetivo de nuestros sistemas exoesqueléticos es ayudar a reducir las lesiones en el lugar de trabajo”, explica el científico deportivo Andreas Argubi-Wollesen, biomecánico senior del Instituto de Ingeniería de Construcción y Fabricación (LaFT-Institut für Konstruktions- und Fertigungstechnik). “Nuestros sistemas están diseñados para eliminar la tensión muscular de ciertas tareas y no para causar problemas adicionales por su propio peso”. El sociólogo Dr. Athanasios Karafillidis no sólo está interesado en los niveles de aceptación de los eventuales usuarios de los exoesqueletos, sino también en el desarrollo de ideas y clasificaciones relacionadas. “No era nuestra intención crear un Ironman en forma de exoesqueleto”, enfatiza el subdirector del grupo de trabajo Smart Assist. “La petición era un sistema de soporte asequible, portátil y fácil de aplicar que ofreciera la menor tecnología posible”.
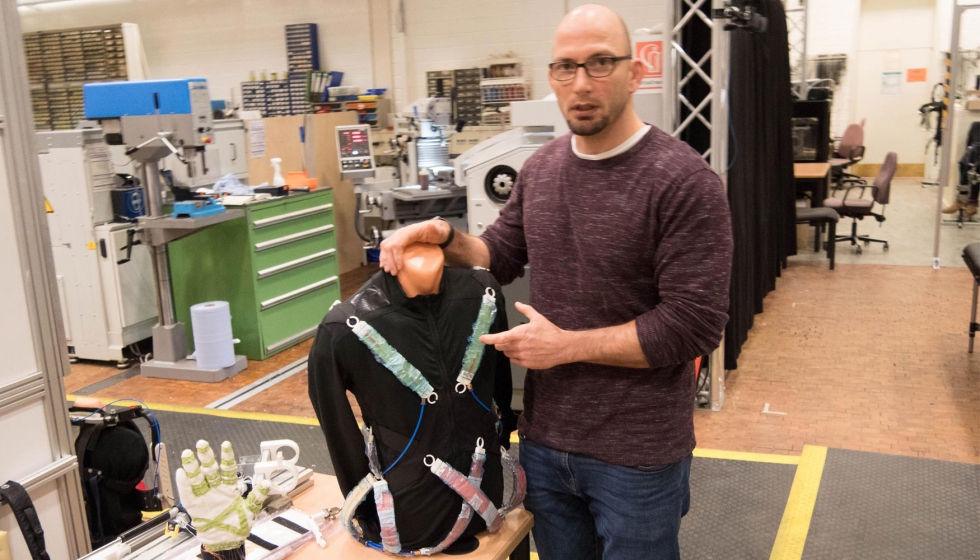
Facilitar el trabajo por encima de la cabeza
“No nos propusimos crear un exoesqueleto. Se nos encomendó la tarea de desarrollar componentes de apoyo”, dice el gerente de LaFT. “La primera solicitud provino de la planta de Airbus en Hamburgo, que quería aliviar la tensión de sus trabajadores mientras realizaban trabajos por encima de la cabeza”. Los primeros modelos funcionales se probaron allí en 2016. El objetivo principal es la prevención, es decir, la reducción del número de días perdidos por enfermedad, mediante la prevención del sobreesfuerzo. En realidad, la creación de un sistema de este tipo fue inicialmente difícil porque nadie tenía idea de las posibilidades. El equipo emprendió la tarea de manera interdisciplinaria y pragmática: desarrolló los primeros componentes, que luego probó directamente in situ. Para reducir los tiempos de desarrollo y los costes, los investigadores hanseáticos también aplican el principio Lego en su trabajo: los componentes deben ser modulares y capaces de combinarse para formar sistemas personalizados.
El ‘patio de juegos’ interdisciplinario de los investigadores se encuentra en el sótano de la universidad. Argubi-Wollesen muestra una chaqueta: “Estamos planeando el uso de ropa inteligente con elementos de soporte individuales que están reforzados neumáticamente bajo presión negativa. Las prendas liberan al usuario de la necesidad de soportar peso en ciertas posiciones”. Neumáticos, motores eléctricos o aleaciones de memoria que se deforman cuando se aplica tensión eléctrica, pueden utilizarse como accionamientos.
La aceptación juega un papel importante
La aceptación es importante en todo esto. Algunas personas dan la bienvenida a los sistemas como trucos de alta tecnología, mientras que otras los rechazan como muletas que supuestamente los hacen parecer débiles. Tales reacciones juegan un papel, especialmente en sistemas conspicuos como el de Lucy: Argubi-Wollesen muestra cómo funciona el exoesqueleto con forma de mochila. Una vez incorporado al operario, basta con silbar para que Lucy se conecte neumáticamente para soportar el peso. De repente el usuario se siente más fuerte, pudiendo sostener un objeto pesado sobre la cabeza durante más tiempo. Al bajar los brazos, la asistencia neumática se disipa. “Lucy es un sistema activo típico que sólo se utiliza para aplicaciones específicas”, explica el biomecánico. “Podemos ajustarlo individualmente para que sólo se active en ciertas posiciones con niveles de fuerza ajustables individualmente. Cuando buscas un teléfono inteligente o una herramienta, por ejemplo, se apaga sola”. Esto se debe a que la asunción completa de todo el trabajo resultaría en el debilitamiento de la musculatura y ese no es el propósito de los sistemas de apoyo.
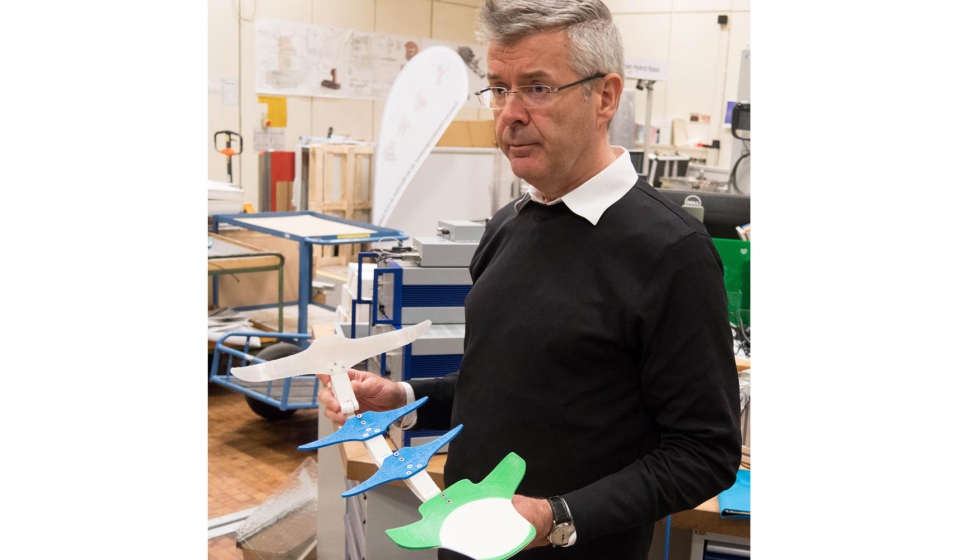
Sensores RFID para detectar herramientas
Con el fin de desarrollar sistemas practicables, los investigadores examinan los procesos de trabajo típicos con la ayuda de sensores y los llamados sistemas de subtítulos en 3D. “Esto nos permite ver cuánto esfuerzo muscular está implicado en ciertos movimientos”, afirma Argubi-Wollesen. “Luego probamos el exoesqueleto para ver cuánto apoyo le da al portador. Las pruebas de laboratorio con apoyo de energía revelan un promedio de 20 a 30% de alivio muscular. En las mediciones prácticas realizadas en fabricantes de automóviles como Ford, los niveles de alivio individual de hasta el 50% ya se han alcanzado con herramientas pesadas”.
El sistema se puede adaptar ahora para aplicaciones específicas como taladrar, rectificar o fresar. Karafillidis explica que “en el futuro, los exoesqueletos inteligentes podrán detectar el grado de tensión individual directamente a través de sensores y adaptar el nivel de soporte en consecuencia”. Sin embargo, el método también plantea interrogantes sobre el monitoreo de datos: ¿qué queremos capturar y qué se permite? “Para nosotros, como investigadores éticos, no es aceptable controlar a los empleados de esta manera, ni tampoco es legal. Al igual que con todas las tecnologías modernas, también es necesario que exista un consenso social sobre cómo abordar de manera responsable las posibilidades tecnológicas que esto abre”, continúa Karafillidis.
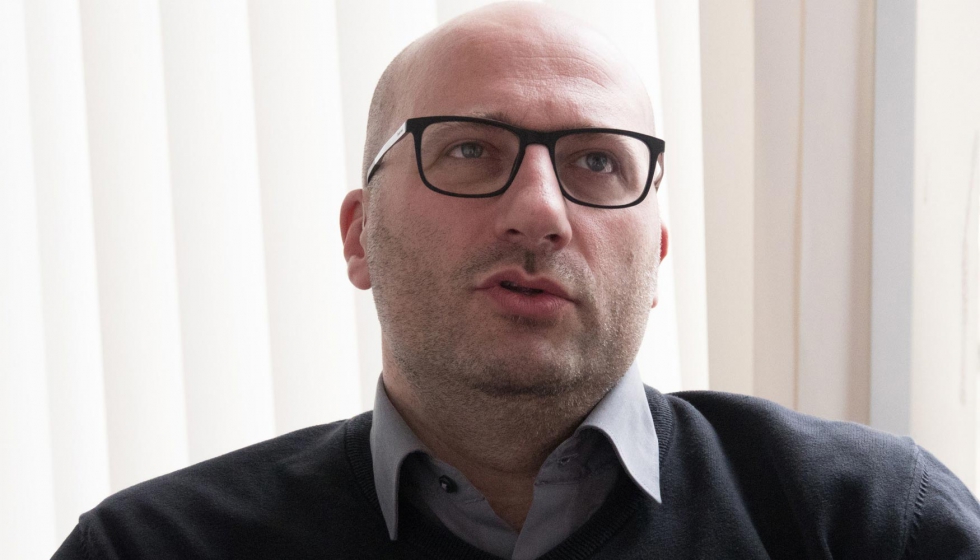
Los investigadores de Hamburgo también tienen la vista puesta en el montaje de máquinas. En un espacio del sótano están montando una pequeña unidad de avance de máquina-herramienta desarrollada internamente con dos grados de libertad accionada por dos actuadores piezoeléctricos (rango de desplazamiento: 1,6 mm x 3,5 mm, precisión: 1 µm). El elemento de accionamiento está destinado a la construcción de pequeñas máquinas-herramienta necesarias para la ‘microprodución’, la fabricación de componentes muy pequeños como los utilizados en la tecnología médica o en la industria relojera. El técnico es asistido por elementos móviles que sostienen sus brazos mientras trabaja. Se trata de planchas de agarre a medida que LaFT produce mediante la impresión en 3D. Los investigadores de Hamburgo utilizan un robot para supervisar los procesos de montaje. Con los sensores del robot se pueden registrar los recorridos y las fuerzas. Wulfsberg: “Podemos usar las secuencias grabadas para refinar el proceso de ensamblaje.” La aplicación práctica en el campo de la tecnología médica ya está prevista.
El Laboratorio de Ingeniería de Producción (LaFT) forma parte de la Facultad de Ingeniería Mecánica de la Universidad Helmut Schmidt, Universidad de las Fuerzas Armadas Federales de Hamburgo. En estrecha colaboración con socios industriales y de investigación, el WGP-Institut desarrolla productos innovadores, métodos y nuevas tecnologías en los campos de la microproducción, la robótica, la automatización y los sistemas de creación de valor. Realiza proyectos básicos de investigación y desarrollo para aplicaciones relacionadas con la industria en estas áreas.