High quality of threads in process of high speed
14 March 2012
A block of big engine can easily have between 20 and 40 threads. These connections for components and groups find in crankshafts, butts, bielas and in a lot of components of mould and coined along a vehicle. In mechanical engineering, covers, threads and the centres also have numerous connections of screw. In particular in productions in series, for example in the industry of automotive sector, is vital that these threads realise of fast and reliable form, particularly when the threads are the union to a component at the end of the process of manufacture, when already they have invested a lot of hours of work in each piece and therefore the rejection arrives to be very costly.
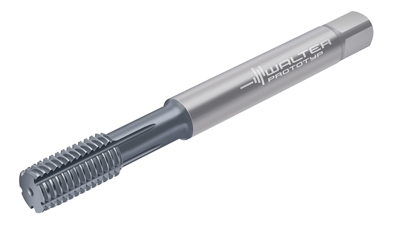
High speed of laminación with impressesive improvements in the efficiency
With these areas of application in mind. The manufacturer of tools Walter with headquarters in Tübingen present in the EMO of this year, the new male of laminación in hard metal, Protodyn HSC. This laminador has been included in the rank of tools of high speed, by means of which can reach speeds of laminación until the double that a laminador conventional HSS. The test of field in different companies have showed that the new laminador reaches a new level in quality of performance. In a threaded component by laminación, the number of threads realised using a laminador conventional step of 20.000 threads with the previous tool, to 90.000 with the new Protodyn HSC, represents an increase of 350% of useful life. The cut or better said the speed of laminación duplicate .
Besides, the 90.000 threads by laminación realised with a saving of two hours of time. For a biela, the useful life of the Protodyn HSC has expanded in 300% compared with the previous laminador. The number of threads in crankshafts increased almost four times by tool and the useful life increased in 280%. The time of schemes also reduced in 25%.
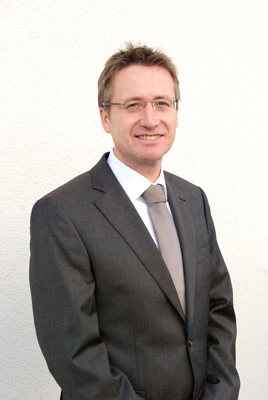
“The life of the tool until thrice more than the laminadores conventional in HSS, surpasses with grow the relative high price of purchase of the new Protodyn HSC”, declares Swindle Mager, director of Product for the manufacture of tools of threaded in Walter AG. And the reveals the recipe of the success: “A sustrato recently developed, a geometry of innovative cutting and the optimised polygon that form the singings of the laminador —these three together innovations generate the significant advantages of the Protodyn HSC—”. The sustrato of the hard metal of the laminador consists in a variety of microgramo with a high degree of hardness and tenacity, giving as resulted a high stability of laminación. The new geometry of cut means that all the corners of the polygon of the laminador participate uniformly in the process of conformed, giving as resulted a more uniform distribution of the wear that with the forms of previous cutting. This process only, allows a greater useful life until 75%. Finally the new form of the corners of the polygon minimises the generation of friction and the heat between the tool and the material, what contributes to the life of the tool.
Advantages of the thread by laminación
By the so much, the new tool HSC represents truly a high point in the area of the threads by laminación, a procedure that offers his own advantages on the threaded of cutting. In the first place the process of conformed does not generate any shaving, therefore it deletes entirely the problem of packaging of shavings, also does the process of threaded by laminación less susceptible of failures. For this reason, it is preferable to use it in deep threads. An additional advantage is the quality of the thread. During the laminación, compresses the fibres of the material in the component, in place to split them as they are in the cut. Like result, the thread has a better structure and a better surface. This has a beneficial effect on the connections of the screw, mainly in situations of dynamic loads such as the generated by the vibrations of the engine. The resistance to the traction of the threads laminadas is of 20 or 30% elder that the one of threads by cutting. This, of course, has a positive effect in the vehicles and the machinery in operation. The males of laminación also break with lower rapidity that the males of cut, since the male of cut requires of the channels for the evacuation of shaving. The transversal section of a male laminador is therefore greater that the one of the male of cutting and the global process is more stable. The director of product of Walter Swindle Mager amazes , “in some industries, the male of laminación often does not consider sufficient like alternative to the male of cut”, also is conscious of “that there is a true scepticism to the males of laminación of hard metal. Often the people prefers to use the tools of HSS”.
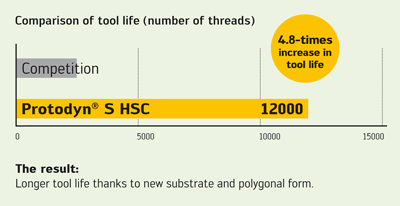
Wide range of applications
With the Protodyn HSC, however, the advantages of the threaded by laminación are entirely of self-evident, particularly in big series of production, where the essential are time and speed. In the industry of automotive sector and similar sectors with big batches, the new male of laminación can really take advantage of his potential. His procedure can be considered to use in all the moldable metallic materials, therefore for a wide spectrum of steels, stainless steels and aluminium with a content in silicon underneath of 12%. The tool reaches his best results in steps of thread of 1,5 millimetres.
The Protodyn HSC Supplies in different variants. Depending for which type of thread has developed , can use laminadores with or without internal refrigeration. With slots for grease, can be a universal use particularly in deep threads above 3xd. For applications that do not require slots of grease, can use the variant of low-price. Since there are not shavings that evacuate, the same laminador can use for blind basic threads and pasantes. In applications that requires a big number of threads to produce in series – for example in the process of bielas, special tool is the election. Then Walter configures it specifically for the thread that goes to generate, in terms of refrigeration, grease and geometry of cutting.