Illig increases the number of cycles and improves the quality of the product with its new generation of moulding machines
April 22, 2009
The modular design of this concept allows combination possibilities ranging from the basic machine to high-performance machine, configured and regulated processes.
The greater the enlargement, the greater will be the production capacity and so much more convenient and faster will be the exchange of mould, reducing at the same time the cos-tes of manufacture of the product.
The characteristics of the equipment may vary according to the requirements of the customer and it is available in different combinations. With multiple variants resulting from this, the various concepts of work and the regulation of processes you can choose the most efficient technique to termoconformar almost without limitations.
Illig uses already since the 1980s the servodrive technology at thermoforming machines, being pioneer in the field.
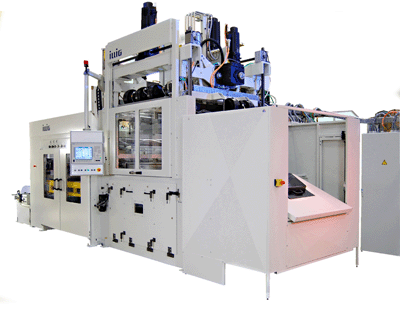
Another feature of the servo is its low power consumption compared to the pneumatic and hydraulic drive. In addition, her accuracy of reproduction of the production data is very high.
To ensure a high level of quality of the parts termoconformadas is necessary to configure all the parameters involved in the process of reproducible way. Speeds, the routes, the temperatures and empty values can be adjusted and memorize digitally. The quality of the product is tested by the quality assurance. To be carried out without problems orders later, they are stored and are archived all the data from the process. The machine works with a reproducibility nun-ca achieved so far.
For a thickness of walls more uniform of the castings is necessary to make a prior blow the heated material. This is done before blowing the plate, which comes air controlled in the House of moulding (box blowing). A photoelectric cell controls the bubble so formed, ensuring distribution of the thickness of the walls reproducible and that remains unchanged. The ultimate embedded part geometry is achieved by moulding with vacuum.
The heating of the semiproducto in the device of load reduces the time of cale-facción in the station of moulding, therefore allowing increased production. You get the work interval shorter when both stations working simultaneously. Depending on the product, this is done with the corresponding distribution of the heating time for each of the stations (station of moulding, plate loading device).
During the molding process, the immersion of the mold in preestirado material plays a prominent role. The line between the previous blown and precise synchronous movements of translation of the table influences both the uniform distribution of the material and the quality of the embedded piece, especially in the corners. The complexity of the process requires different sequences of movements to the table of moulding and the piston prior drawing, which can be obtained with digitally adjustable and memorized speed profiles for the movement of rise and fall of the molding table.
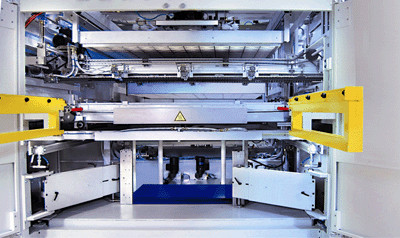
The device of load of plates automates the molding machine
In addition to obtain increased performance, the advantage of an automatic load consists of better reproducibility of the process, i.e., due to the automatic sequence and uniform of the functions, gets a better quality of the piece foil even for small amounts. In the case of manual loading, the operator influences the range of work.
The device of load includes the transportation for the semiproducto to the machine of molding device. It also allows loading plates strongly curled after warming, as well as download blank pieces molded in positive and negative, even at a depth of maximum drawing. This rises the transport so that is tilted upward. The previous setting takes place in the control panel.
An eleva-planchas powered by servo motor allows speeds of lifting of the iron. For more security, a sensor measures the default thickness of the iron in the transport and recognizes the bent.
Working from a stack of plates decentered, centered table aligns the iron in longitudinal and transversal sense in such a way that then it can be gathered from reliable transport mode. The format is adjusted automatically, being able to memorize the dimensions of the plates. Also available a car porta-planchas, which can be charged with the plates on the outside and then be pushed toward the load. You can prepare another car porta-planchas to the following order, for example.
Easy to use and computer-aided basic adjustment
Processes and applications, along with a broad knowledge of the material, technology leads to an optimal machine program which includes parameters to shape, cutting and stacking. In conjunction with the drives by servo motor, thanks to this technology processes and with the help of computer aided basic adjustment, the new mould can be calculated data adjustment and optimal process times according to the plasticthe geometry of the molded part and the construction of the mold.
All the data required for the production process are entered into the control panel and are indicated in the comparative teórico-real. Optimized data are memory-zables and are available immediately in case of repetition of the product. To control the manufacture in progress you can permanently access to all the important data of the service.
Optimal parameters of manufacturing through the regulated temperature heating
The smooth and uniform heating of the semiproducto is the key to a good result from forming. The heating are equipped with ceramic resistors for high temperatures (HTS); they are termoaisladas and have a high effective performance. The area of radiation is closed, which guarantees a good warm-up for the semiproducto to the edge for any fixation frame size.
The movement of translation of the heating is carried out by engine through a movement of sinusoidal drive. In addition to a best result of heating, this version of drive - along with the movement of translation tables--saves the most of time, therefore contributing significantly to greater production capacity.