The Custom-Fit technology to mass customization
March 18, 2009
The new manufacturing process integrates scanning technologies, recently developed CAD (computer aided design) systems and Rapid Manufacturing technologies: the scanner get the geometric characteristics of the human body, on the basis of these data the CAD software automatically carries out the design of the product that the tools of Rapid Manufacturing print these parts without any expensive toolsunaffordable for the manufacture of exclusive products, as those who try.
This new paradigm of production has been tested on five case studies: some of them related to components custom in the medical field - implants of knee and jaw and Transfemoral prosthesis - and some consumer products individuals in which the 'tailor-made' provides a significant added valuesuch as helmets of motorcyclists and seats for motorcycles.
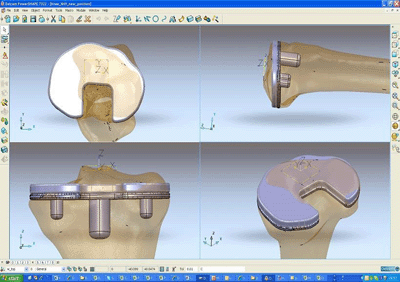
This new technology has been a success in the manufacture of custom elements. The process consists of the following: has been perfectly adjusted components of knee and jaw to the geometry of the bone that had to adapt, through the use of CAD tools that can be operated with bone implants. CT (computed Computerizada) scanning transforms them into a CAD format standard 3D (referred to as STL, standard triangulation language) - see Figure 1.
The jaw was printed with a bio-absorbable material developed with a new technology called high viscosity inkjet printer: implant is replaced within 12 months by regenerated bone - see Figure 2.
Knee implant is customized adapting not only to the form but also to the mix of material used, graduated from the bone-compatible titanium and Co-Cr high resistance with the mixture established according to particular conditions of the patient. A new design tool has been developed to maintain the optimisation of this graduate material (the MPTO or 'Optimization of topology Multi phase') and a new technology of Rapid Manufacturing, the process of printing on Metal powder, which is capable of printing titanium and parts of Co/Cr.
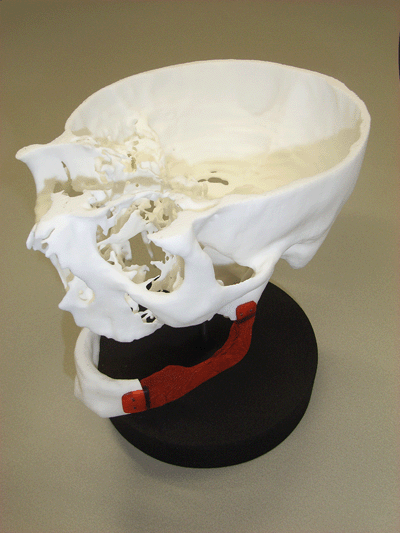
A slightly different approach was used for the hull and the seat of bike. This customization process noted external body shape, not bones with CT scans. In the case of the hull, a body scanner laser was used to obtain the geometry of the head of the motorcyclist, and designed a coating that adjust perfectly to it; It aims to integrate it into the field of security standard of the hull, which obviously cannot be changed for reasons of certification - see Figure 3.
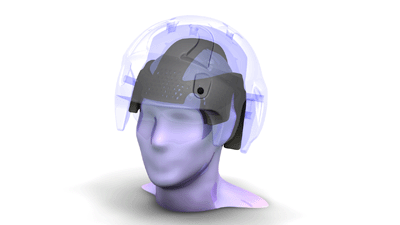
To obtain the pad with graduated compression stockings has designed a new concept of pad, with an internal structure consisting of elements in the form of Pier whose extent depends on local compression of the pad. This graduated structure was made possible by the concept of manufacturing layered and it is essentially impossible with traditional manufacturing technologies, see Figure 4.
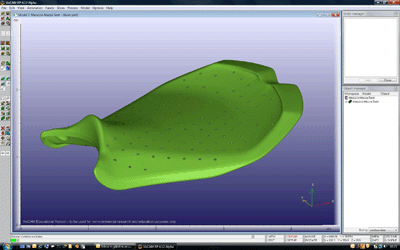