The exhaust air filtration with content from lubricants for machining of metals by boot of shavings
Requirements required of a modern procedure for clean air
Good cleaning of the air: systems or air purification equipment used for the cleaning of the exhaust air containing cutting fluids and are installed in or near machines and machining centers, are generally reintroducing the clean air again in the production hall. The same applies to the central facilities of aspiration that, in order to prevent loss of heat in winter, blowing the air into the production with the clean air recirculated Hall again.
To dispose of this clean air in the interior of the naves of manufacturing it is essential that the filtration system will be able to purify the air of continuously during the machining process, eliminating as much as possible of all "non-air" substancessuch as fog of emulsions and oils, carbides, metal microparticles or abrasive materials, not only in order to comply with the provisions of regulations (TRGS and MAK values), but also, first and foremost, to protect the people who are in jobs and avoid conditions to their health (eg. skin irritations allergic)(, diseases of the respiratory tract).
From the point of view of the risks that may affect human health are especially considerable importance aerosols in the polluted exhaust air, i.e. particles of liquid suspended and thinly spread in the air (fog) or solids (char)(, powders, metal particles) with dimensions< 0,5 µm. estas partículas finísimas pueden ser inhaladas por las personas con el aire que respiran, llegando hasta los pulmones. a pesar de que, tal y como se muestra en la figura 2, la parte proporcional de las mismas en la masa total de impurezas del aire es muy pequeña, es relativamente elevada la cantidad de dichas partículas. 0,5="" µm.="" estas="" partículas="" finísimas="" pueden="" ser="" inhaladas="" por="" las="" personas="" con="" el="" aire="" que="" respiran,="" llegando="" hasta="" los="" pulmones.="" a="" pesar="" de="" que,="" tal="" y="" como="" se="" muestra="" en="" la="" figura="" 2,="" la="" parte="" proporcional="" de="" las="" mismas="" en="" la="" masa="" total="" de="" impurezas="" del="" aire="" es="" muy="" pequeña,="" es="" relativamente="" elevada="" la="" cantidad="" de="" dichas=""> 0,5 µm. estas partículas finísimas pueden ser inhaladas por las personas con el aire que respiran, llegando hasta los pulmones. a pesar de que, tal y como se muestra en la figura 2, la parte proporcional de las mismas en la masa total de impurezas del aire es muy pequeña, es relativamente elevada la cantidad de dichas partículas.>
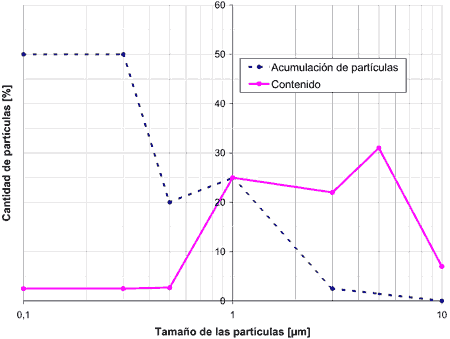
In addition to protecting the health of people must prevent was also in the surroundings of machining machines precipitation of the fog of cooling lubricants in order to avoid pockets of risks such as the high danger of slipping, adverse effects on production facilities and air conditioning, as well as elements of monitoring and control electrical and electronic or a high risk of fire due to sediments or oil deposits.
Low operating and maintenance costs: the procedures and equipment of filtration and cleaning the air that are used in practice must be made them a good cleaning of the air not only when the installation is new and after the completion of maintenance work, but the most possible continuously for long periods of use of the machine tools.
This means that cutting fluids separated in the equipment of filtration or purification of the air along with the particles of solid substances which separated, be withdrawn or filter in a way such that components or internal elements of the used filter separators should not be disabled to work properly, but who get auto - clean up greatly during the filtration process.
In case that this is not feasible, the consequences for all known will be:
- A debugging reduced air until that is cleaned equipment.
- A reduced air suction power, i.e. leave mist of fluid (cooling lubricant) Court of the domestic dwellings of the machine tools.
- High costs of maintenance and cleaning in regenerating filters.
Universal separation procedure: machine tools for machining of metals used by chip startup are not used only for machining wet or dry, but that, depending on the material to be machined isis both a machining wet with emulsion or oil, as well as a machining with minimal lubrication (MQL) or dry machining.
This flexibility of the machine tools also implies that the apparatus of separation - filtration used must obtain as something absolutely indispensable perform appropriate cleaning the air without any problem, with the separation equipment installed.
Functional and procedural security: to obtain a suction and cleaning fully operational, satisfying and safe air from machine tools with content output in cutting fluids, must be taken into account or observe the following points:
- The suction equipment installed next to or on the machine of machining be positioned as close as possible to the point from which originates the mist cutting fluids, which may keep a minimum distance of the volume of air that has to seek. This will also prevent their spread by the environment, so that the conditions to maintain framework established by the legal provisions.
- The suction power indicated by the manufacturer of the filtration apparatus should conform to the volume of air inhaled at the entrance of the device and not to the power of the fan in a State of no installation or measure in the test.
- The volume of air sucked while working the machine tool should be kept in a safe and reliable, with a constant value in order to have complete certainty that in the space of the machine tool machining or the environment are not excessively high concentrations of flammable substances.
- The refined and filtered exhaust air may contain, according to ZH 1/248, when in the case of cutting fluids and work with recirculated air, a Max. 2 mg of substances outside air per each cubic metre of air, i.e. 1/5 of the admissible MAK values.
This value must be guaranteed even when the separator apparatus has working for long periods of time.
- All suction devices, so if it's a single device as if is an installation of aspiration of groups or individual (per machine), shall not adversely affect nor on the machining processes with corresponding equipment or devices for loading and unloading, or on the environment. Suction devices must adapt accordingly to the operating processes of production and not vice versa.
Situation and technical realization
- Wet separator
- Centrifugal separator
- Electrostatic separator
- Separator mechanical filtration
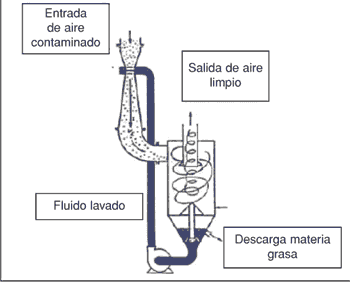
- Separators by humid way. In comparison with the other three procedures for separation or filtering only separators are used by the humid way occasionally for the cleaning of air containing cutting fluids; talk also, however, if only briefly.
In wet separators accelerates the polluted exhaust air within a Venturi nozzle at high speeds, spraying it at the same time with washing fluid cutting fluids. In this way there is a dampening of solid particles and an increase in size of the fine particles of liquid; in other words, forms a dense curtain of water of very fine droplets. Inside a tab of drops mounted below the purified air of washing water is separated under the action of the centrifugal force. The air cleansed after the separator by the humid way contains still much residual liquid very fine particles, on the other hand, to be very high relative humidity of the air. Apart from this are clearly higher acquisition and operating costs when compared with other procedures or equipment of separation.
Wet separators are used so predominantly machining dry, in those cases in them there is a risk of explosion or fire from tanks or sedimentation of powders (p. ex. in the grinding or sanding dry aluminium) or when there is a clean exhaust hot air.
- Separators centrifugal. As the name suggests they work separators centrifugal principle of centrifugal force; see Figure 5.
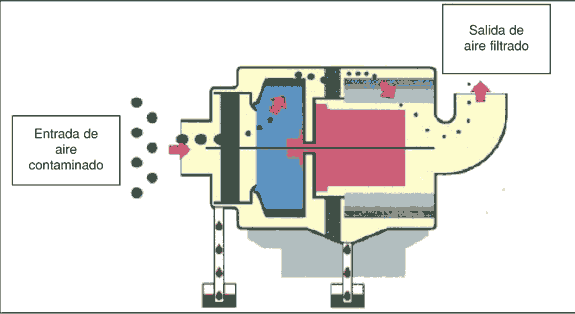
The aspirated air flow of the machine tool is accelerated outward through a rotating radial impeller with a sponge material centrifugal filter, which gives rise to the particles contained in the air will be projected outwards as in a centrifuge against the casing or fixed wrapping of the separator. The film of fluid that is formed on the wall of the shell is drained by the force of gravity, down coming out through a siphon, outside of the apparatus.The separating power of centrifugal separators is, according to the laws of physics, so greater the greater are the droplets to be separated. For the separation of fog of cutting fluids with a spectrum or range of particles of approximately 0, 1-10 µm mean that the part of larger particles may only be separated. According to the BIA assessment in the fluids of court-BIA report, the centrifugal separator is not appropriate, and can be used only with certain reservations as the previous separator for separation of aerosol and smoke. This is the reason why some manufacturers recommend additionally use another filter for clean rooms or sterile, installed after the first.
In the event of prolonged stops there is risk in centrifugal separators of the cutting fluids accumulated in the spongy material centrifugal filter moves down due to gravity causing, returning to put the device into service, vibrations which have an adverse effect on the supports of the rotating elements.
In the event of a machining center mounting can influence negatively such vibrations on the manufacturing tolerances. It is why what separators or centrifugal filters should not be installed on the same machines for machining, but attach to machining centres riding on a rack of independent support.
- Electrostatic separators. Electrostatic separators take advantage of the physical effect that the electrically charged particles are diverted in an electric field. As can be seen in the scheme in principle with the structure of an electrostatic separator that is shown in Figure 6, it passes through the air, previously cleaned in a previous mechanic, a so-called zone of ionization separatorthat is subject to a high voltage of 6-12 kV, in which particles drawn in the air loaded electrically into a tungsten wires through a download of effect Crown or download at the tips.
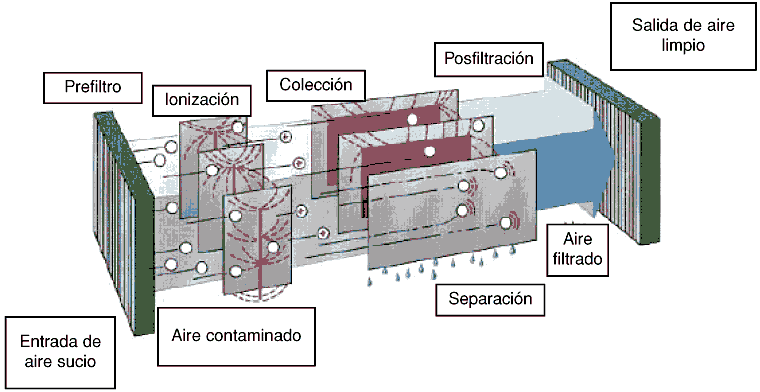
A field of high voltage that causes the diversion of the particles charged towards the metal plates is created between the metal plate charged positively and negatively. Through an ever-increasing rainfall is is forming a film of fluid is drained down inside the apparatus due to the force of gravity and can out of it through a siphon. Electrically charged particles which remain separate in the flow of air neutralize in a separator of metallic fabric mounted below, then driving through blowing.Separation of electrostatic separators performance depends on the size of the particles of foreign substances contained in the air. With plates clean sheet can bring yields of cleaning required by the BG (mutual professional accidents) < 2 µm / m3 of air when working under a system of recirculation of the air.
Especially in the separation of pure oil mist get good levels of separation, provided that the separate oil film can slip or slide well down the spacer plates and are, therefore, an effect of backflushing of the same.
If, on the other hand, is ensuciasen the spacer plates due to particles in the form of powder, high viscosity oils or emulsions viscous residues, give this place a which is progressively reduced and increasingly to a greater extent the efficiency of the separationi.e. that it can get out of dirty or polluted air apparatus. Also may occur in the plates, because metal particles or dust from grinding acceded, electrical discharges that can cause unintended disconnection of the high voltage.
Separators electrostatic established intervals of maintenance not too long, with an ultrasonic system, so as not to harm internal components must be cleaned to prevent it.
There is another problem when using electrostatic separators for the cleaning of exhaust air containing mist of emulsions. Because of the good electrical conductivity of water can produce electric shocks not desired as a result of high relative air humidity and the accumulation of water droplets on the separation plates. This results also from a reduction in the capacity of separation to the disconnection of the part of high voltage, which is not detected and can often by the user at the right time, leaving air clean.
That is why what reference is made also in the BIA Informa to the insufficient capacity of the separation of electrostatic separators when it comes to clean up horticultural and not pure cutting fluids.
- Separators mechanical with filters. Tabs with filters that work mechanically consist usually of a combination, see Figure 7 of separators of plates of impact or rebotamiento of different configurations for the prior cleaning of the air and filter elements mounted below (generally rooms clean or aseptic filters) for the subsequent separation of fine particles in the air output.
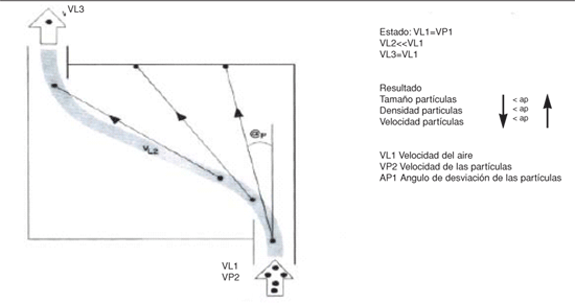
Cleaning or prior separation:
In plates of impact or rebotamiento separators installed in transversal sense to the direction of the flow of air is channelled the flow of air through special internal structures, e.g.. diverts or investment profiles concave or in the form of displaced correlatively together V or perforated plates, a sudden change of direction; see model.
Due to the centrifugal force that is generated in this way and acts on liquid or solid particles are separate these from the flow of air and are being planned against the walls of the inner structures, rushing on these walls. The film of fluid that is formed in this way is drained down, due to the force of gravity, by vertical interior structures and can flow out of separators appliances through a siphon. Thanks to this effect of self-cleaning separators of plates of impact achieved long intervals of employment without having to perform costly cleaning and maintenance work.
Good performance of separation washable impact or rebotamiento plates separators and working without wear and tear is of significant importance to the time of the filter elements mounted below and which tend to be generally wear parts. In Figure 8: we show below is intended to show which parameters influence specifically in these cases the degree of separation of the previous tabs, taking as an example a separator of perforated plates.
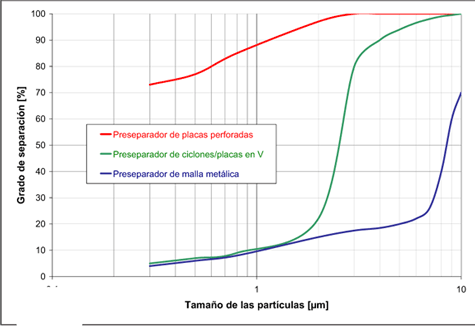
Presentation with the help of models:
- Figure 9: separator of perforated plates: positive outcome
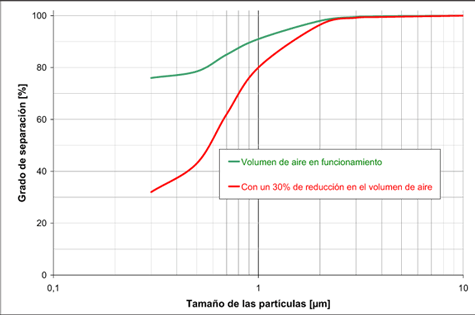
Comparatively, Figure 10:
- Separation of metallic fabric
- Investment in V separator
- Separator of perforated plates
In addition there is a peculiarity of the world of the tabs in plates of impact or rebotamiento that I have observed while preparing this Conference, Figure 11: and that I would like to present them as what might be called a cyclonic separator "to the right rather than to the left".
Further filtration:
As mentioned above often install preferably as filters later in order to achieve a really clean air, filters for substances in suspension of the US 13 type. These highly efficient filters to clean or aseptic, rooms with a capacity of separation of 99.99 percent related to dimensions of particles of 0, 3-0, 5 µm, can guarantee virtually filtering all particles of the cloud of emulsion or oil, smoke or very fine dust from grinding on an ongoing basis and with a high power of permanent filtration. Tambiény is especially true of inhalable and respirable particles of less than 0.5 µm range. This guarantee on an ongoing basis and during all the time in employment of filters values which are clearly below the tolerance value set officially to clean the air of a maximum of 2 mg of waste particles / m3 of air in circulation. There is no possibility of making a "blown" filters for particles in suspension in the air.
The problem with these filters for substances in suspension consists of substances alien to the air are separated from the same (especially oily products) are deposited in such a way the filter fabric cannot be removed by washing, thus reducing the time or length of life of the filters. Because of this it is necessary to replace filters for particles in suspension used by new ones in order to proceed to their elimination.
Alternatives to the subsequent filtration:
As an alternative to the subsequent filtration through filters for particles in suspension can be used particularly in machining processes emulsion with little formation of mist, a subsequent tab that works without any wear and consisting of a separator of metallic fabric or fabric combined made of metallic fabric with integrated polyester fabric. These subsequent tabs makes a further additional cleaning through adhesion and condensation of liquid particles.
In the following figure 12 (AFS apparatus): the completion of a combined system of impact plates and filters in a device used in practice.
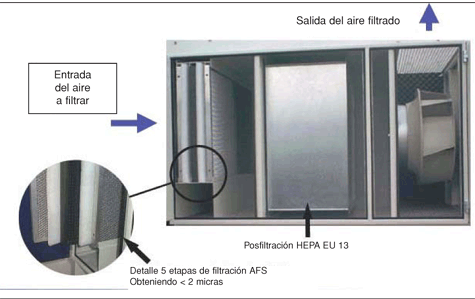
Employment in the practice of clean air systems
Individual equipment:
The aspiration of one or two adjacent machining machines can be done with the individual tabs. The debugging output air is projected once again in the production hall. Must be met, therefore, the legal provisions relating to the recirculation of air (max. 2 mg/m3).
The following figures (13-16) show the attached mounting or mounting tabs machining centres:
- Figure 13: AFS 600 Stama
- Figure 14: AFS 1100 DMG
- Figure 15: AFS 1100 Pfauter
- Figure 16: AFS 4000 B & W
Facilities of aspiration of groups of machines:
If it had to seek the exhaust air of several machines for machining are not too far away each other, it may be with an installation of aspiration for groups. You can see the structure or configuration of an installation of aspiration of groups of this type.
Also in the case of large central facilities of aspiration is similar the structure submitted to an installation of aspiration of groups; Figure. 19:
Air recirculation system (in the winter months):
To prevent loss of heat during the winter months through the hot air expelled abroad when working with systems of direct expulsion of air into the atmosphere, air purified from the AFS devices can be projected back to the production halli.e. the air stays within the premises. Thanks to this recirculation of the air we do without warming, necessary in other cases, of cold air from the outside to replace the air expelled abroad, be required for this 1.0 l of fuel-oil approximately per every 1,000 cubic metre of outdoor cold air. The limit values maximum allowable established for the operation with recirculated air are kept fully and even clearly lower values are achieved.
Operation with expulsion of air to the outside (in the summer months):
In the summer months we can work with the mode of operation with expulsion of air to the outside through a channel of air which leads directly to the outside (and that it can be also used at a later time). The hot air, purified, is expelled outside, at the same time allowing the entry of fresh air from the outside through doors, doors or Windows open in order to maintain a natural air conditioning of the craft of production without the need of additional fans. In correlation with the savings of energy during the winter are may expel comparatively abroad an amount of heat of approximately 1.0 (l) of fuel oil every 1,000 m3 of air.
You can also replace or change the subsequent filter for clean rooms installed when working with the system of recirculation of the air (filter for particles in suspension of type US 13) by a subsequent tab of metallic fabric that works without any wear, and its possible cleaning a washing machine with an alkaline agent.
Summary
As we have shown in the previous exhibition, there is no "the" optimal separator for numerous specific individual cases that arise in practice with the most various lubricants.
The mechanical separator combined with filter developed by AFS approaches however quite it. Thanks to the combination with complementary effects of impact plates separators or rebotamiento with filter fleece additional integrated and filters to clean or aseptic rooms mounted below can be guaranteed, even when it has to work for long periods of time with individual cases of application, both high constant cleaning performance and long periods of service life of the filter media: this is also the reason why the AFS Air Filter Systeme GmbH company is engaged in the manufacture of such devices of clean airdistributing them for years, with success in the market along with the Bantleon House among others.