Walter complete his range of Xtreme DM microbroaches
The last generation of broaches of hard metal of
The specialists of the taladrado are used to to use the term ‘micro taladros' to refer to small diameters of holes of until 3 millimetres. In spite of this, can achieve diameters even more small in the rank of micras, the known micro taladros that can use for diameters of hole so small like 30 micras. The typical applications of these taladros focalizan in the industry of the electronics equipment dealers equipment dealers and the micromecánica since a lot of pieces compose of materials very fine that, often, only have some hundredth or tenth of millimetre of thickness.
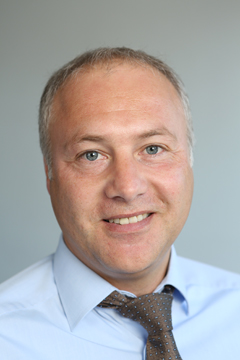
Helmut Gschrey, Manager of products for taladrado in Walter: “After a big number of experiments, have achieved characteristic of the tool with accuracy, such like hard metal, geometry, microgeometría and the design of the channels of refrigeration and slots”.
Small but deep diameter The things are different in the another extreme of the spectrum micro, where the applications head to the mechanical engineering general, the aerospace industry, the mould manufacturing and matrices or to the engineering of medical equipment. In these areas, the holes with a diameter of 2 to 3 millimetres are usually required, sometimes to depths until 20 x D or more. Some examples include holes for the refrigeration, lubrication, ventilation or filters of orifices. In these cases, the engineers of process can choose between two concepts of tools: broaches cannon and broaches helicoidal. During long, the broaches cannon dominated since, because of the requirements of high tenacity, the broaches helicoidal only could be manufactured from fast steel (HSS). When using this type of broaches, the speeds of cutting and advance were low and the holes had to be cleaned constantly, in addition to the low reliability that comported. However, the development of a special hard metal, with a high level of resistance, allowed the manufacture of broaches long and of high provision. This last generation of broaches leaves to his competitors very by behind in with regard to the times of production of pieces. The success of these tools also confirms in Walter AG, provider of one of the widest ranges of broaches of hard metal in the market of tools. “We have noticed a clear increase of the demand of micro broaches of hard metal of our range X treme ”, explains Helmut Gschrey, director of product in Walter. The manufacturer of tools of precision with headquarters in Tubingen reacted to this development by means of the enlargement, once again, of his range of products. The last update of the range entered new characteristic, as for example the new lengths of taladrado of 16 x D x 30 x D. All the upper lengths to 20 x D are now also available in a version of 2 millimetres (before 2,5). Gschrey Continues saying: " because of the demand, have increased the diameters between 0,1 and 0,5 millimetres, by what almost all the users will be able to find the broca suitable”.
The things are different in the another extreme of the spectrum micro, where the applications head to the mechanical engineering general, the aerospace industry, the mould manufacturing and matrices or to the engineering of medical equipment. In these areas, the holes with a diameter of 2 to 3 millimetres are usually required, sometimes to depths until 20 x D or more. Some examples include holes for the refrigeration, lubrication, ventilation or filters of orifices. In these cases, the engineers of process can choose between two concepts of tools: broaches cannon and broaches helicoidal. During long, the broaches cannon dominated since, because of the requirements of high tenacity, the broaches helicoidal only could be manufactured from fast steel (HSS). When using this type of broaches, the speeds of cutting and advance were low and the holes had to be cleaned constantly, in addition to the low reliability that comported this process. However, the development of a special hard metal, with a high level of resistance, allowed the manufacture of broaches long and of high provision.
This last generation of broaches leaves to his competitors very by behind in with regard to the times of production of pieces. The success of these tools also confirms in Walter AG, provider of one of the widest ranges of broaches of hard metal in the market of tools. “We have noticed a clear increase of the demand of microbroaches of hard metal of our range Xtreme”, explains Helmut Gschrey, director of product in Walter. The manufacturer of tools of precision with headquarters in Tubingen reacted to this development by means of the enlargement, once again, of his range of products. The last update of the range entered new characteristic, as for example the new lengths of taladrado of 16 x D x 30 x D. All the upper lengths to 20 x D are now also available in a version of 2 millimetres (before 2,5). Gschrey Continues saying that " because of the demand, have increased the diameters between 0,1 and 0,5 millimetres, by what almost all the users will be able to find the broca suitable”.
The small details are those that matter
The range of microbroaches Xtreme offer an exceptional performance thanks to what Walter calls Xtreme DM Tecnology.: ‘D' means depth and ‘M', micro. This technology includes a series of characteristics that serian impossible without the recent advances in the design of hard metals. One of the most remarkable characteristics of this technology is the internal refrigeration by means of channels of refrigeration that visit the body of the helicoidal tool until the edges of cut, where keeps the temperature of operation more correct. The geometry of tip optimised, with a special manufacturing of the edges of cut, and the special geometry of slots ensure the perfect learning of the shaving. On the other hand, the slots pulidas support the evacuation of the shaving. A special coating to base of titanium diminishes the wear and increases the life of the tool. Besides, the Xtreme pilot 150 and the Xtreme M of 5 x D are entirely recubiertos with a layer of AML.
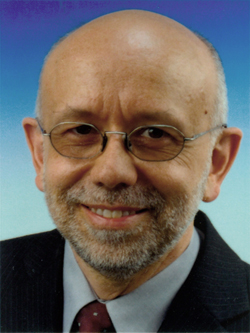
Walter instruments the deep holes with a coating of tip AMP. Like result of this, the tools are adapted for material ISO P, K, M and N and also for S and H. “It is possible taladrar material of titanium but the success depends on the proportions of alloy that contain and the type of application”, says the director of product. "What minor was the tool, more important are the details", continues.
Helmut Gschrey Explains that “after a big number of experiments, have an exact coincidence between all the characteristics of the tool, like the quality of the hard metal, the geometry, the microgeometría and the design of the channels of refrigeration and slots. The result of the perfect interaction of all the characteristics of the tool is a high performance. For example, the coating only adapts to the geometry and to the microgeometría established by Walter". The developers have not left at all at random. This attention to the detail in the tuned allows to the user achieve big increases in the productivity. The director of product affirms that these increases oscillate between the 50 and 100% and have confirmed in numerous experiments of field and of laboratory.
More difficult that in the broaches big
Taking into account the small diameter, would not be beneficial to detain the operation of taladrado deep from time to time for picotear the hole? Peter Müller, boss of development of the tool of taladrado in Walter, explains that “the reinicio of perforación means an additional load in the tool, that is just what want to avoid. Interrupt the process for picotear also comports an element of uncertainty in the sequence of the operations. The question then presents in how and when has to realizar the picoteo. The answer depends on a lot of factors that still do not know in depth. A tool that can finish his task without relief always is the best option of taladrado deep with a small diameter”.
Seen of this way, the taladrado with small diameters is not different of the taladrado with big diameters. The broaches XD of Walter, with diameters of 5 to 12 millimetres and a depth until 70 x D, also taladran until the bottom in an alone operation.

Some recommendations of Walter
The experts of taladrado of Walter Tübingen recommend some steps to the user to optimise his productivity. First, initiate the hole with the broca Xtreme pilot 150 and taladrar until roughly 1,5 x D. Next, ingresar the broca Xtreme DM in the hole to low revolutions and change to the nominal speed, put the refrigerante and taladrar until the depth required in an alone operation. After reaching the depth required, reduce the speed and retraer the tool.
In case there are doubts, the user can find the data of correct cut of the tool in the software GPS Walter. The company specifies that a pressesure of refrigeration of 20 to 70 bars ensures a good exit of the shaving. For a perfect work, the degree of filter has to be < 20 micras and the emulsions or oils of cut result adapted for the refrigeration.
The range ‘Xtreme'
Walter has completed recently his range of microbroaches Xtrem. All the lengths now can supply in a range of diameters from among 2 and 2,95 millimetres and includes the following types:
- Xtreme Pilot 150 Depth: 2 x D
- Xtreme M 5 x D
- Xtreme DM8 8 x D
- Xtreme DM12 12 x D
- Xtreme DM16 16 x D
- Xtreme DM20 20 x D
- Xtreme DM25 25 x D
- Xtreme DM30 30 x D