The impressesion 3D employs increasingly in the development of prototypes, tooling, components and aeroplanes no tripulados
The additive manufacture wins presence in the aerospace sectors, aeronautical sector component manufacturing sector component manufacturing and of defence
The headquarters of the National Institute of Aerospace Technician (
Stratasys Is considered, according to it indicated in the technical day his commercial director for Spain and Portugal, Inma Vázquez, like “the world-wide leader of systems of impressesion 3D”, having a long and intense experience in the world of the additive manufacture. In 1994, for example, Stratasys already sold the first thermoplastic available for a process of impressesion 3D (plastic ABS); in 2008 it launched to the market the first machine for production (Fortus 900mc); and in 2012 it contributed with his solutions to develop the first prototype of aeroplane no tripulado with wings impresas entirely in 3D (created by Aurora Flight Sciences).
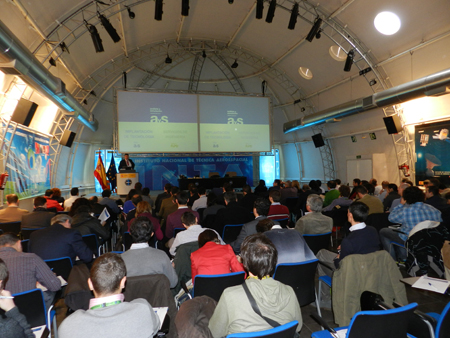
The day organised by Analysis and Simulation enjoyed of a big success of assistance.
Also in 2012, took place a decisive fact in the most recent path of Stratasys, when merging with Objet, another company of reference in the field of the impressesion 3D, been cream in 1998 and that among others historical attainments has the have manufactured the first printer 3D of desk of the world with 7 materials (Objet 30P) and the first machine of impressesion 3D with more than 100 materials.
Today, the company has more than 1.000 employees and near of 500 patents in matter of additive manufacture, offering his solutions in fields so miscellaneous like the aerospace industry, the automotive sector, the military industry, the architecture, the medicine, the sector bucodental, etc. In total, esteem that has been able to install more than 75.000 systems. “We believe passionately in the process additive”, signalled Inma Vázquez, for the one who this type of systems goes to favour a new “industrial revolution, in which the creativity no longer will have limits”.
For this technological change, Stratasys has prepared with a complete range of solutions, structured in three big series: Idea (the smallest equipment, thought for the modelación of concepts), Design (centred in the impressesion 3D of prototypes) and Production (the known equipment Fortus).
In impressesion 3D, Stratasys employs fundamentally two technologies: polyjet (fotopolímeros) in those cases in which it requires a high precision, and FDM (thermoplastic) for the applications in which it demands a high performance.
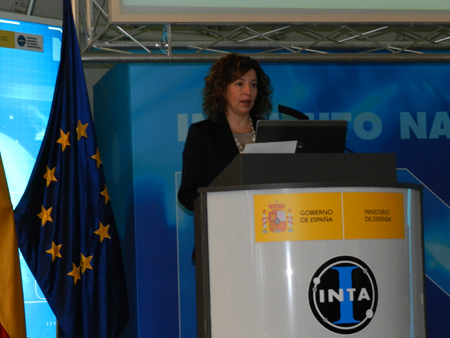
His innovative vocation in this field does not detain and the company already announces the launching of new and revolutionary printers 3D, like the Objet 500 Connex 3. All this to allow that the processes of manufacture win in rapidity and efficiency and following a tendency imparable, that went even recognised by the president himself of the EE UU, Barack Obama, in the speech of the State of the Union of the 2013 when showing his intention to incorporate the additive manufacture like a subject prioritario in all the institutes and centres of learning of the country. “We have to invest in the best ideas”, finished saying Inma Vázquez.
Challenges surpassed by the additive manufacture
Through his report, Iker Galdos, director of product for Additive Manufacture in Analysis and Simulation, wanted to stand out the reasons of the effervescence that is living in these last years all the related with the impressesion 3D. As it recognised, the possibility to print a product in any part of the world from a simple computer archive, opens all a world of possibilities. Besides, it treats of a process that, in front of other traditional alternatives of manufacture, supposes big economic savings and of time. To all this it is necessary to add that they already have caducado the patents of two leaders of the market as they are Stratasys and 3D Systems, by what is producing a 'boom' world-wide of new agents that want to go in in this sector.
According to the definition employed by Iker Galdos, the manufactura additive consists in “manipulating material to scale micrométrica and deposit it generally layer to layer, to create objects from data 3D of a model, of opposite form to the technicians of manufacture sustractiva”. And inside this general field the processes can be of the most miscellaneous: laminación or LOM (employment of layers of different materials), fotolitografía or estereolitografía (use of light UV like basic process of solidification), fusion or selective sintering by laser (use of a do of laser and electrons for the consolidation of the material), polyjet (inject layers of fotopolímero liquid in a tray and cures to the instant by means of light UV) and modelling or deposition melted - FDM (deposition of thread melted layer to layer, of thermoplastic, ABS, like basic material).
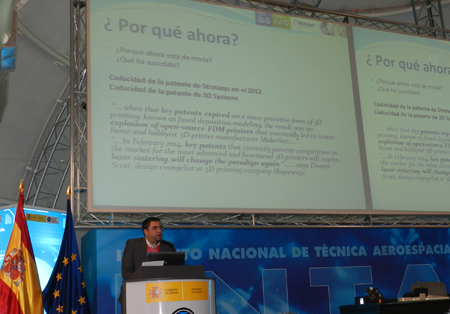
The impressesion 3D advances to a vertiginous rhythm and after beginning like a formula of fast manufacture of prototypes, has become also a profitable alternative for the manufacture of tooling and, more recently, to an option with a high potential in the digital direct manufacture (pieces of final use, in short series).
In spite of the possibilities that offer these technologies, Spain, as it recognised Iker Galdos, does not appear in the ranking of the countries that more do use of them at present (EE UU, Japan, Germany, China, United Kingdom and France lead this classification), had to especially to the traditional reticencia of our industry to advances so revolutionary and to the economic crisis that comes crossing our country in the last years.
Of course, the additive manufacture, with the last advances, has achieved to surpass challenges that seemed insalvables in the productive processes: reduction of weight, improvement of the quality, reduction of costs of development, lower time of production…, by what his future promises to be very positive.
Aerospace sector
To know the opportunities that offers specifically the additive manufacture in the aerospace sector explained in the day with the presence of Santiago Martín Churches, aerospace engineer of the INTA. A clear example of success of the penetration of the 3D in this field is the project Diana. The INTA develops, from does years, a wide program of investigation for the development of the necessary technologies that allow the design and construction of a range of aeroplanes no tripulados. One of these products is the called Diana, a system of aerial white of high provision developed to simulate real threats. By his versatility, the system can employ like system of aerial learning for big quantity of current and future arms.
In the manufacture of the mobile surfaces (structural) of this aeroplane no tripulado has substituted the elements of polymer reinforced by fibre of carbon (CFRP) by elementary integrals of polyamides. With this, as it confirmed Santiago Martín, have reduced the times in 50% for unitary production (80% in series) and the costs in 70% with regard to the laminado with core.
The main attainments of this replacement in the processes of manufacture the resumía the manager of the INTA in three: reduction of time of development (optimisation), flexibility in the production and spare parts to low cost (fast answer was cual was the version of the design).
All the structural essays that have realizar on the aeroplane no tripulado Diana have given positive results, and the proofs of flight realizar also have been successful.
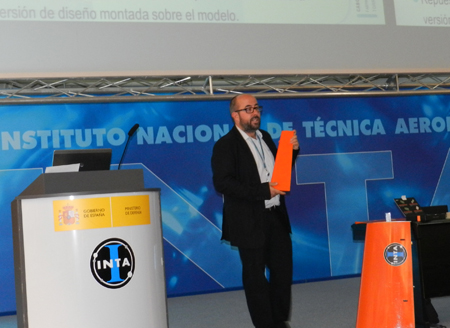
Santiago Martín Churches, aerospace engineer of the INTA.
Like potential applications of the additive manufacture inside the aeronautical sector component manufacturing sector component manufacturing sector, Santiago Martín aims, between others, the topological optimisation of the structures, systems optimised of refrigeration, elements of radiofrecuencia, maquetas and the special primary structures (integrated refrigeration, for example).
Did not want to finish the manager of the INTA his report without before mention some needs that have the designers and engineers of this type of products and in whose solution still could deepen the solutions of impressesion 3D, especially in the aerospace field where a minimum error can be fatal: improve the binomial machine-material, optimisation of productive strategies, development of new materials, new strategies of design, specific superficial treatments, positioning of insertos during the process, insertion of steeringal continuous fibres, greater rapidity, precision and trazabilidad of the quality… In summary, and as it concluded the manager of the INTA, “it is necessary to risk, it is necessary to support this type of developments, without losing win them and the illusion”.
Before the pause of the coffee, David of the Ash, of Analysis and Simulation, did a brief summary of the three models Fortus that there is at present in the market, 360 mc, 400 mc and 900 mc, which differentiate between yes, fundamentally, by the size and by the materials that can employ. “The machines Fortus are the most reliable that have seen in this market, amortise in very little time, allow to manufacture of a very agile form and his installation is really simple”, affirmed.
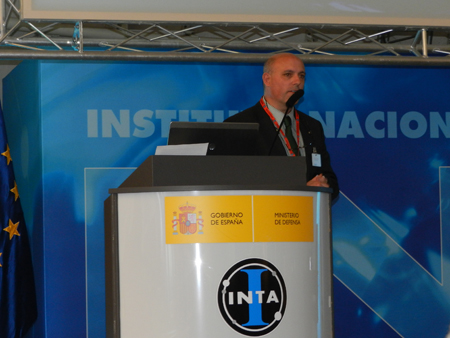
David of the Ash, of Analysis and Simulation.
Current materials in FDM
In 1988 Scott Crump invented the modelling by deposition melted (FDM) in the kitchen of his familiar house by means of the mix of the formulas of wax and plastic. Since, the varieties that can employ with this technology have grown exponencialmente. FDM Uses thermoplastic of industrial quality and the suitable material is in function of the application that go him to give and of the temperature that go to reach.
Some of the most employed materials at present are: ABS-M30, ABS-ESD7, PC (polycarbonate), PC-ABS, PPSF/PPSU, FDM Nylon 12 and Ultem 9085 (an increasingly used material by his very high performance).
These materials use , for example, in the design and prototyping functional, of the that David of the Ash put, in another of his reports, some examples of success that have comported important savings of money and time with regard to the processes of manufacture previously used. A very remarkable case is the one of a motopropulsor of more than 200 pieces that with the employment of a Fortus 900mc allowed a saving of 875.000 dollars (the manufacture of the prototype so only cost 25.000 dollars in front of the 900.000 dollars that had cost if it had mechanised ), as well as a reduction of 7,5 months in the time of production (with the Fortus could do the prototype in 1,5 months in front of the 9 months that had taken if it had mechanised ).
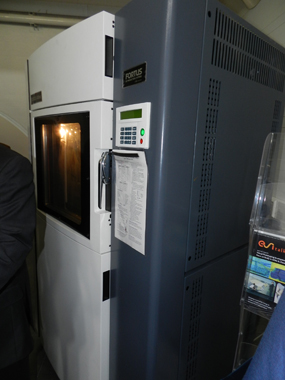
Also have attained important savings of money and time in the manufacture of another type of prototypes, like the pipes of hydraulics driving of a hybrid aeroplane-helicopter, in the train of landing of an aeroplane… In the aerospace field, David of the Ash detained in two very striking cases in whose prototypes has employed additive manufacture. To work in the International Space Station has developed the robot Robonaut 2, whose prototype has realizar with machines Fortus and with the polycarbonate like material. To realizar this prototype has taken two weeks with a cost of 36.000 euros, whereas with the traditional formulas had taken 36 weeks with a cost of 180.000 euros.
For the exploration of the planet Mars also has been decisive the participation of the machines Fortus since near of 70% of the pieces employed in the manufacture of the robot Rover are done in polycarbonate with this type of machines.
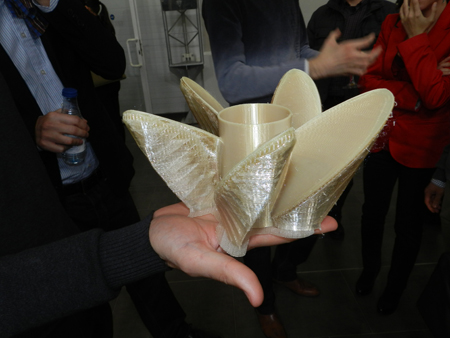
Direct manufacture
The day organised by Analysis and Simulation in the INTA finished with the exhibition of different real cases of direct manufacture of aeronautical sector component manufacturing sector component manufacturing tooling, aeroplanes no tripulados and aeronautical sector component manufacturing sector component manufacturing components. The own David of the Ash exposed different examples of how the additive manufacture has achieved to reduce the economic costs and the time employed for the development of different products. There are cases in which the manufacturers have obtained savings in the costs of until 95% and of the times of 88%, like the mentioned in the day of a manufacturer that happened to manufacture with ABS in place of by smelting by process to stray wax.
In processes like the manufacture of helmets for military use, composites for the repair of helicopters, destined components to the interior of aircraft of luxury, pieces of gimbals of surveillance, carcasas fireproof for instrumentation of aeroplanes, fuselages and streamlinings for aeroplanes no tripulados, etc. employ already successfully systems of manufactura additive.
Boing, for example, manufactures aeroplanes no tripulados light for military use (UAV RM-1) by means of machines Fortus 400mc and employing like material ABS. In hardly three days can manufacture one of these aeroplanes. And even there is a company, UAV Solutions, that already develops aeroplanes no tripulados entirely in Ultem 9085.
The most immediate future in the field of the aeroplanes no tripulados, as it concluded David of the Ash, raisin also by the direct impressesion of the circuits, a field in which already there are companies working acutely (phase of development).
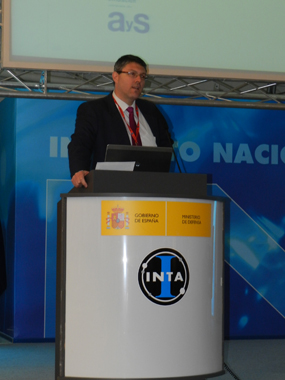
Solutions adapted to the needs of the customers
Analysis and Simulation is, as it indicates his director manager José Julián Martínez, “a skilled engineering in the integration and implantation of technology advanced, for the development and innovation of product, optimisation and improvement of the processes of manufacture, management and infrastructure”.
Inside the structure of this group also finds the company P&PD, an engineering of services specialised in the design, simulation and development of product, taking into account the process fabril.
With the New ‘lemma forms to do' from the company works to create habits with the new technologies, collaborate and execute new projects and qualify to the people for the exert of his functions. “We want to contribute value to the companies”, resumía José Julián Martínez.
Analysis and Simulation, founded in 1997, account to day of today with 74 workers, which conform “a stable team, motivated, qualified, multidisciplinary and oriented to the people”, indicated the responsible maximum of the company. Has headquarters in Álava, Barcelona, Guadalajara, United Kingdom and China, and offers a wide variety of services pre-ordering/quality consultancy (rediseño of pieces, calculation, simulation, additive manufacture, essays…) and services postventa (installation of machines and systems, learning, technical assistance, maintenance…). Besides, for those customers that require it the company also puts to his disposal complete packages of work with human resources and technicians of Analysis and Simulation (except the works of laboratory, that externalizan).