La fabricación directa a partir de datos electrónicos es ya una realidad
EOS GmbH15/10/2003
Con el fin de cubrir la amplia gama de aplicaciones para las que sirve, parece razonable utilizar un término que no se limite a un tipo concreto de aplicación, como el prototipado, ni a un motivo particular por el que se recurre a esta técnica, como puede ser su rapidez. Preferimos hablar de e-manufacturing y la definimos como: “Producción rápida, flexible y económica de piezas directamente a partir de datos electrónicos”.
Sustituir la inyección de plásticos
La producción convencional de los componentes de las cajas requería unos utillajes complejos y un montaje que llevaba demasiado tiempo. Como se indica en la figura 2, la producción mediante el moldeo por inyección obliga a un coste inicial importante (Ct1) debido al molde, seguido de un coste relativamente bajo por pieza inyectada. En el caso del sinterizado por láser, el coste por pieza sinterizada es más alto, pero también constante. El coste del molde depende mucho de la complejidad de la geometría de la pieza, mientras que con el sinterizado por láser el coste depende sobre todo del volumen y la altura de la pieza. Esto significa que para cualquier tipo de pieza, hay una cantidad de piezas a producir (nb1) por debajo de la cual el coste por unidad del sinterizado por láser es más bajo y por encima de la cual es más barato inyectar.
También hay que tener en cuenta que los costes del molde sólo se pueden estimar con antelación, mientras que los costes del sinterizado por láser se pueden predecir con mucha precisión a partir de los datos del CAD. Otra cuestión importante es que los cálculos de costes pueden cambiar si varía la cantidad que se estimaba que se iba a producir. Si hay que reducir la producción, el sinterizado por láser tiene una ventaja clara porque no se incrementa el precio unitario debido al coste fijo del molde. Si, por el contrario, hay que aumentar el número de piezas a producir, el sinterizado no ofrece el mismo potencial para la recuperación de la inversión, aunque esto es bastante más deseable, porque sólo significaría un menor beneficio, mientras que en la otra situación se producirían pérdidas. El riesgo con el sinterizado es por lo tanto menor.
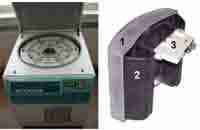
Una vez tomada esta decisión, los diseñadores de Hettich quisieron aprovechar la mayor libertad en el diseño de esta técnica y pronto se dieron cuenta de que podían obtener un mayor beneficio si integraban el elemento de fijación (figura 3). Esta integración funcional aporta varias ventajas:
•La pieza modificada sólo es un poco más cara de producir por sinterizado por láser, pero evita todos los costes del molde. Esto cambia la comparación económica de la figura 2, de forma que la inversión combinada en moldes es Ct2, que significa que las cantidades de producción de hasta nb2 son más baratas con el sinterizado por láser o que con la misma cantidad producida nb1 hay un mayor ahorro.
•Se mejora la funcionalidad del producto.
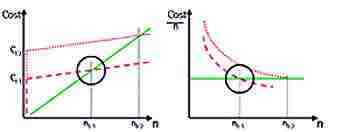
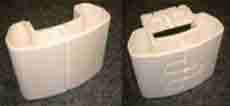
También piezas metálicas
La compañía finlandesa Rapid Product Innovations es líder en el uso del DMLS para lotes pequeños de piezas metálicas y ya ha realizado muchos proyectos de este estilo para sus clientes. Un ejemplo es el de un cliente que necesitaba un set de 300 productos, cada uno de las cuales se componía de tres piezas metálicas, para el cierre de un ordenador (figura 4). Mecanizar estas piezas en grandes cantidades es bastante costoso en términos económicos y de tiempo, como también lo es su fundición. Todas las piezas se pudieron hacer en cinco procesos de construcción en una máquina Eosint M 250 Xtended utilizando el polvo DirectMetal 20. En cada proceso se hicieron 60 sets de productos, con una duración de 32 horas. La figura 5 muestra un proyecto diferente pero con una geometría similar y muestra cómo se pueden hacer hasta 200 piezas simultáneamente en una sola plataforma de trabajo. En el proceso DMLS las piezas deben ser adjuntadas a la plataforma de trabajo. En el caso de piezas como las que se ven en la figura 4, se puede hacer utilizando estructuras de soporte diseñadas de forma que las piezas se puedan separación facilidad de la plataforma.
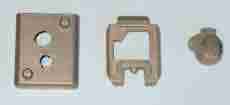
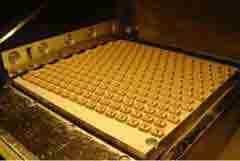
Presente y futuro de la e-manufacturing
Uno de los factores que más está impulsando esta tendencia es el coste por pieza. Una serie de tendencias en el mercado apuntan a un número creciente de variantes de productos y también a menores ciclos de vida, lo cual viene a significar una necesidad de un menor número de piezas por cada una de las variantes. En esta situación, como se muestra en la figura 2, el sinterizado por láser tiene una ventaja natural.
El coste por pieza está muy influenciado por la productividad del sistema, y esto se ha mejorado mucho en los últimos años. Por ejemplo, la Eosint P 380 logra una mejora del 100% o más en productividad si se compara con el modelo anterior Eosint P 350, gestionando la temperatura de forma óptima y controlando la exposición al láser. La productividad también se puede aumentar si se aumenta el número de piezas en cada trabajo. La empresa EOS ha lanzado un nuevo software llamado Eospace para optimizar la densidad de las piezas de una forma automatizada.
En todo esto las propiedades del material que se utiliza son muy importantes. Tanto los plásticos como los metales han sido mejorados enormemente en los últimos años de forma que, por ejemplo, las piezas realizadas en la poliamida 2200 tienen propiedades mecánicas comparables e incluso a veces mejores que la PA 12 o el ABS inyectados.
También se ha mejorado mucho la precisión y el acabado superficial de las piezas, pero es cierto que las propiedades del material continúan siendo uno de los factores que limitan el uso de esta técnica.
Si bien el uso del sinterizado por láser para el prototipado rápido está bastante extendido, los ejemplos planteados en este artículo y otros muchos que ya se están llevando a cabo a escala comercial demuestran el futuro del e-manufacturing y sus posibilidades para mejorar la calidad de las piezas y reducir sus costes.