Impulso a la fabricación aditiva de piezas y estructuras metálicas de grandes dimensiones
El centro tecnológico Tekniker ha diseñado y desarrollado con tecnología propia una máquina que permite fabricar componentes 3D de grandes dimensiones a través de la técnica de aporte directo de energía mediante tecnología láser utilizando material metálico en forma de hilo.
Las tecnologías de fabricación aditiva metálica tienen cada vez más protagonismo en el ámbito industrial en el desarrollo de nuevos productos con nuevos diseños aligerados, componentes con nuevas funcionalidades integradas o productos personalizados; en el suministro de repuestos con ‘lead-time’ reducido; así como en el reacondicionamiento y la reparación de componentes para el incremento de su vida útil.
Igualmente, existe una demanda creciente para que estas tecnologías puedan procesar o estén preparadas para abordar la fabricación de nuevos materiales de alto interés para la industria. Y, debido al alto coste de las materias primas empleadas en estos procesos productivos, cada vez cobra mayor importancia la reutilización como una característica a integrar para mejorar la sostenibilidad de los propios procesos de fabricación.
Asimismo, el aseguramiento de la calidad y de los requerimientos o especificaciones técnicas de producto es también un aspecto de vital importancia y está condicionado, por una parte, por las características de la materia prima, los parámetros seleccionados para cada uno de los procesos, el diseño del producto y la estrategia definida para abordar la fabricación y la robustez de los mismos, y por otra parte, por todas las etapas de post procesado que pueden incluirse en la cadena de valor para la optimización de las prestaciones alcanzables.
No en vano, la calidad ya no equivale únicamente a la ausencia de defectos (poros y faltas de fusión), sino que se deben asegurar unas propiedades mecánicas que solo se pueden alcanzar mediante tratamientos térmicos y de acabado optimizados para cada material.
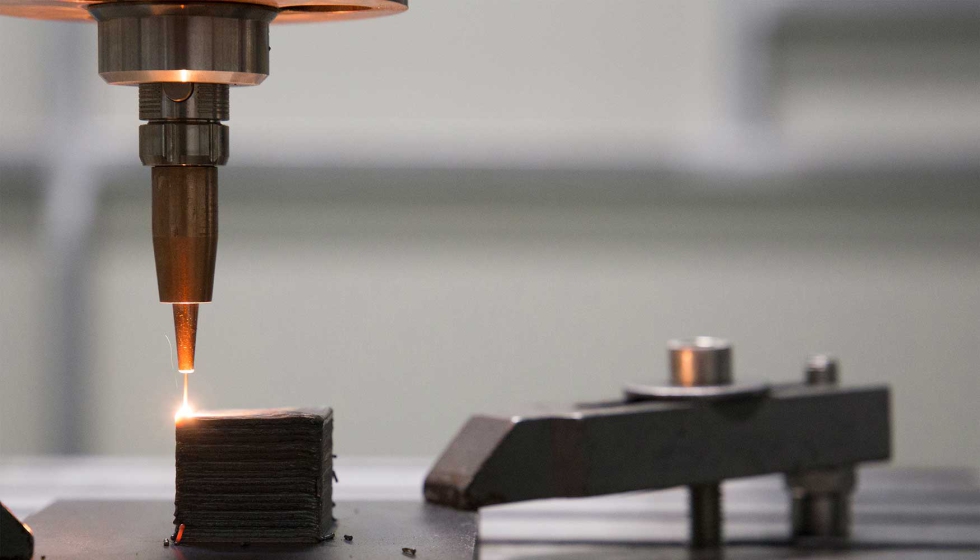
Para asegurar esta calidad, es también de vital importancia la trazabilidad del proceso de fabricación a lo largo de las diferentes etapas de la cadena de valor gracias a la integración de diferentes herramientas o habilitadores digitales.
A pesar de que las tecnologías de fabricación aditiva se engloban en el concepto de la Fabricación Digital, la digitalización en la mayoría de los casos se limita solamente a la etapa de impresión en 3D y no contempla ni las etapas previas de pre-procesado, ni las posteriores de acabado. Por este motivo, de cara a una futura industrialización de estas tecnologías, es necesario abordar la trazabilidad del proceso aplicando herramientas digitales y la digitalización de la cadena de valor.
Deposición Directa de Energía
En este escenario, una de las tecnologías de fabricación aditiva más prometedoras para atender esta demanda es la técnica DED (Direct Energy Deposition), conocida también como LMD (Laser Metal Deposition). Se trata de un proceso de aporte directo de energía en el que se emplea una fuente láser para generar un haz concentrado capaz de fundir el material, ya sea en forma de hilo o polvo metálico, permitiendo generar geometrías tridimensionales complejas y obtener recubrimientos o estructuras con propiedades idénticas o mejoradas respecto a las del material base.
A diferencia de otras tecnologías de fabricación aditiva, basadas en la fusión directa de hilo o polvo mediante arco eléctrico u otras fuentes de calor, esta tecnología genera mínima afectación térmica, y por tanto menor distorsión y deformación en el material, garantizando la integridad estructural de los componentes en el proceso de fabricación.
El centro tecnológico Tekniker, con una amplia experiencia en procesos de fabricación y un gran conocimiento de estas nuevas tecnologías de producción, ha dado un paso de gigante en la I+D de la técnica DED con el diseño y desarrollo de un equipamiento propio de fabricación aditiva mediante el aporte de hilo metálico a través del láser.
La máquina, denominada Titan, cuenta con unas dimensiones de 6.100 x 3.100 x 3.420 mm y es capaz de fabricar componentes de diferentes aleaciones metálicas (titanio, acero, aluminio, etc.) de gran tamaño (hasta de 1.900 x 900 x 750 mm) y de alta calidad para sectores como el aeronáutico, el automotriz, el eólico o el naval, convirtiendo al equipamiento en una gran impresora 3D para la fabricación industrial.
Aunque su principal función sea la producción de componentes de aleaciones de titanio, las características y condiciones de la máquina también permiten la fabricación de componentes de otros metales como aceros, aleaciones con base níquel o aluminio, ofreciendo una tasa de aporte de hasta 2-3 kilogramos de material por hora dependiendo del tipo de aleación.
Consiste en una máquina cartesiana de tres ejes (más dos opcionales) que tiene acoplado un cabezal láser de aporte de hilo metálico coaxial, alimentador automático con capacidad de suministrar hilo metálico con diámetro de 0,6 a 1,6 mm, una fuente láser de 4 kW de onda continua, con emisión en el espectro infrarrojo cercano, concretamente a 1.070 nm, y una placa opcional calefactora para controlar la temperatura de las piezas durante el proceso de fabricación.
Para garantizar una fabricación estable, libre de óxidos, sobre todo en aleaciones de titanio, el equipo incorpora una cabina de atmósfera controlada con un volumen total de 20.000 litros. En ella se puede trabajar en diferentes condiciones: aire (condiciones normales de presión y temperatura), baja presión (0,1 mbar), atmósfera de argón, helio, nitrógeno o CO2 (<20 ppm O2) y sobre presión en argón, helio o nitrógeno (<20 ppm O2).
Los tiempos para preparar la cabina cambian según las condiciones atmosféricas deseadas, por ejemplo, desde las 5 horas y 42 minutos que dura la adecuación a Argón (<20 ppm O2), hasta los 25 minutos que tarda en simular las condiciones de vacío (0,1 mbar) + Argón.
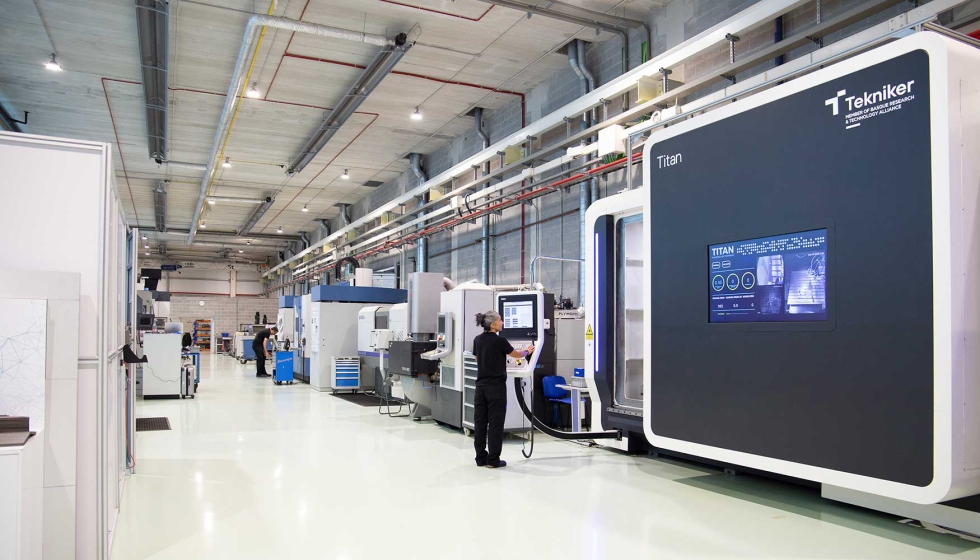
Digitalización del proceso
Los procesos DED cuentan con numerosos parámetros (temperatura, geometría, etc.) que influyen en el resultado de la pieza fabricada, lo que los convierte en procesos complejos.
En ocasiones, se necesita un gran número de ensayos experimentales. Sin embargo, la gran sensibilidad de las condiciones de fabricación ante pequeñas variaciones puede provocar que estos ensayos se alarguen en exceso, o incluso que las condiciones supuestas como adecuadas no sean extrapolables a la pieza definitiva. Por esta razón, la monitorización y el control del proceso es un aspecto necesario para garantizar la fabricabilidad y calidad de las piezas generadas por fabricación aditiva.
En este sentido, Titan integra diferentes herramientas digitales como un software propio (Tekam) desarrollado por Tekniker que simula y genera las trayectorias para procesos de fabricación por DED, un pirómetro coaxial para monitorizar la temperatura durante el proceso y un sistema de visión capaz de monitorizar la geometría del baño fundido en tiempo real.
La máquina también genera mapas tridimensionales con la evolución de los datos de la ruta de deposición del material para su posterior análisis y correlación a través de la monitorización y registro durante el proceso de fabricación de la posición, los parámetros del proceso, la vibración del propio hilo metálico, la temperatura o la geometría de la pieza. Estas variables se procesan, sincronizan, fusionan y visualizan durante todo el proceso de fabricación.
La medición y el control geométrico se realiza in situ para medir la geometría de la pieza fabricada a través de un escáner 3D basado en la proyección de luz estructurada integrado en la máquina. El mismo dispositivo se emplea para medir la altura de la pieza durante el proceso de fabricación con el fin de asegurar una fabricación capa a capa estable. Para ello, la máquina dispone de un control capaz de actuar sobre diferentes parámetros del proceso, como la velocidad de avance del cabezal para asegurar la estabilidad geométrica durante el proceso de fabricación, en función de la medida del escáner.
Reparación y producción en 3D
Entre las principales aplicaciones de Titan en fabricación industrial se encuentra por un lado la reparación de utillajes, moldes, matrices o engranajes, ya sea por errores producidos en procesos de fresado, por cambios en el diseño, por desgaste o por impactos durante la vida útil de estos componentes.
En este sentido, la técnica DED puede ser una solución para otorgar a los equipos de un recubrimiento protector contra la corrosión por desgaste e incluso como barrera térmica.
Por otro lado, la principal aplicación de la máquina de Tekniker es la fabricación de piezas en tres dimensiones, en especial en sectores cuya actividad se desarrolla en condiciones extremas.
Ejemplo de ello es la tobera que el centro tecnológico está fabricando en la Titan con la técnica láser DED por aporte de hilo metálico en el marco del proyecto Hiperion II, financiado por el programa Elkartek del Gobierno Vasco. Se trata de una pieza crítica en motores de combustión de aeronaves espaciales y que debe ser capaz de soportar condiciones atmosféricas de Marte (formada principalmente por un 95% de CO2 y presión atmosférica media de 6 mbar).
Para ello, la tobera, de 650 mm de altura y 450 mm de diámetro máximo, se está fabricando simulando las condiciones de la atmósfera marciana y con aporte de una superaleación de níquel, para cumplir el requisito de funcionamiento de temperaturas superiores a los 2.000 °C, así como soportar las fuerzas de expansión que se producen en este tipo de piezas para cohetes espaciales.
El proyecto de investigación tiene el objetivo de facilitar, mediante el aumento de conocimiento sobre la tecnología láser DED la fabricación in situ, futuras misiones de exploración en Marte, a través de la fabricación o recuperación de componentes metálicos que puedan sufrir desperfectos durante la misión.
Un fallo de un componente en el espacio puede resultar crítico para una misión espacial, por lo que el sobredimensionamiento de los componentes, la predicción y estrategia de actuación ante todos los posibles fallos, así como la redundancia funcional de los sistemas son las estrategias típicas de diseño para asegurar el éxito de la misión.
En el caso de una misión a Marte, enviar una pieza a reparar a la Tierra o enviar una pieza de reemplazo desde aquí no sería una opción viable por el coste y tiempo que supondría.
Tekniker presentará en su stand en la próxima edición de la Bienal de Máquina Herramienta la máquina Titan junto a la tobera en desarrollo y otra serie de piezas como demostrador de las capacidades de la tecnología de fabricación aditiva DED mediante hilo metálico en procesos de fabricación avanzada. Pabellón 1, stand E15.