Funcionalidades de estructuras multicapa en envases soplados
28 de abril de 2011
En la actualidad y gracias a la gran versatilidad de los materiales plásticos, y los avances en las formulaciones de nuevos compuestos con propiedades de claro valor añadido se está ampliando mucho su presencia en el sector del envase soplado. Este factor, junto con la demanda sostenida en esta área, en un entorno coyuntural que ha sido adverso en otros sectores de producto explica las innovaciones que se están implantando en este proceso industrial concreto.
Así, las principales líneas de innovación dentro del sector de envase soplado están siendo:
· Mayor uso de las estructuras multicapa para conseguir el nivel de protección deseado.
· Transformación/adaptación del proceso de inyección-soplado en inyección-soplado con estirado, lo que posibilita la fabricación de envases más esbeltos, y abriendo nuevas posibilidades de diseño.
· Implantación de sistemas de vigilancia de la calidad durante la producción, mediante monitorización on-line.
· Tendencia clara hacia la adquisición de máquinas de inyección totalmente eléctricas, con las ventajas añadidas de mayor limpieza, silencio y consumos reducidos.
Las tecnologías de inyección-soplado y su evolución
El proceso de inyección-soplado combina el proceso de moldeo por inyección seguido de moldeo por soplado. Este proceso se puede dividir en dos fases claramente diferenciadas: una fase de inyección donde se produce una pieza provisional llamada preforma, y una fase de soplado donde se obtiene el producto con la forma final buscada. Posteriormente, le siguen las operaciones de post-procesado para conseguir el producto final completamente terminado, tales como operaciones de recorte, etiquetado, decoración, etc.
En el mercado se pueden encontrar diferentes variantes de este proceso, cuyas características principales, ventajas e inconvenientes se muestran en la Tabla 1.
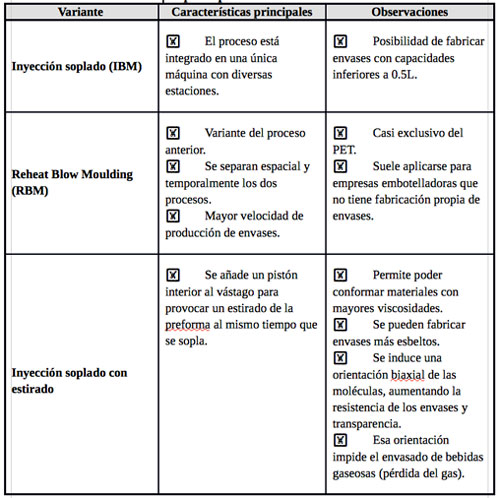
Situación actual y potencialidad del uso de estructuras multicapa en envases soplados
Una vez consolidadas estas tecnologías productivas, entre los fabricantes del sector se observa una tendencia clara en la inserción de estructuras multicapa para la fabricación de todo tipo de envases, destacando los destinados al sector alimentario: botellas, barquetas, tarrinas…
El uso de este tipo de productos se justifica desde el punto de vista de que cada vez, los envases tienen que cumplir con más requisitos y ofrecer una mayor seguridad para el contenido para tratar de alargar su vida útil.
Para cumplir este objetivo, las estructuras de los envases actuales no eran suficientes, puesto que los materiales empleados no ofrecían las propiedades protectoras adecuadas, y los que las tenían, se tenían que emplear en gran cantidad, resultando el envase demasiado caro. Por lo tanto, la salida era encontrar una solución de compromiso a través de la fabricación de envases que combinaran más de un material, de manera que se conseguía aunar las propiedades de cada uno de ellos mejorando el conjunto del envase. Con esta estrategia, se consiguen mejorar características como resistencia a la temperatura, efecto barrera ante la penetración de humedad u oxígeno, protección para evitar la evaporación o la pérdida de gases como CO2 (bebidas gaseosas), alcoholes o aromas, así como protección del contenido contra la radiación ultravioleta. También es posible mejorar el brillo superficial, la resistencia al rayado, la retención de las tintas (impresión), y abaratar los costes del envase al poder introducir material reciclado u otro tipo de rellenos.
Existen dos problemas principalmente a la hora de trabajar con este tipo de envases como son la adhesión entre los diferentes materiales y el hecho de que alguno de los materiales pueda ir perdiendo propiedades por el contacto con otras sustancias.
En el primer caso se suelen introducir capas intermedias de materiales que tengan buena adhesión con los dos, o bien se modifican químicamente para que lo sean. La necesidad de introducir esta capa implica más complejidad en el proceso por aumentar el número de materiales.
En el segundo caso, también se recurre a la introducción de capas de otros materiales que protejan al que realmente está preservando la calidad del contenido. Por ejemplo, el Evoh tiene unas excelentes propiedades barrera frente al oxígeno, pero ve mermadas sus características de manera importante con la presencia de humedad. Por ello, se aísla esta capa tanto del ambiente como del contenido mediante capas de otros materiales impermeables al agua.
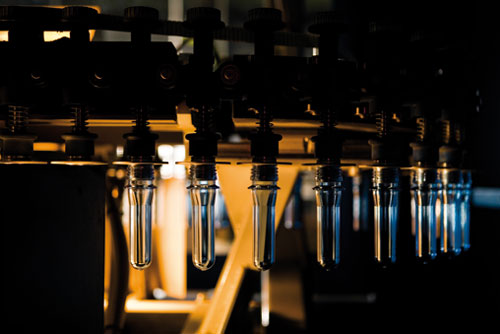
Este tipo de envases se fabrican con las mismas técnicas que se estaban usando hasta la actualidad para la fabricación de otro tipo de piezas, simplemente se tienen que adaptar los equipos que sirven para hacer la forma preliminar de los envases, es decir, se tiene que adaptar la extrusora para sacar un parison con diversas capas (coextrusión), o bien se tiene que adaptar la inyectora para poder obtener una preforma de diversas capas (coinyección); por lo que la parte de tecnología no representa demasiados problemas.
En cuanto a los principales inconvenientes que presentan estos envases es que es más difícil reintroducir el material de desecho (recortes y piezas defectuosas) por la mezcla de materiales, y el hecho de que el material reciclado todavía no está demasiado aceptado por parte de los usuarios finales, ni tampoco existe una legislación que regule el uso del mismo.
Para solventar los problemas indicados y aprovechar la potencialidad de todas las ventajas añadidas, desde Aimplas, el Instituto Tecnológico del Plástico se está trabajando en estas líneas de mejora de envases por el proceso de inyección soplado, permitiendo combinar para sus nuevos desarrollos las tecnologías de inyección y co-inyección de preformas con el proceso de estirado-soplado. Se pretende dar una respuesta adecuada al sector nacional que no lo haga dependiente de innovaciones externas y permita ampliar sus posibilidades de negocio.