Proyecto SIGEN2H2: generar hidrógeno verde con una economía circular
Enrique Bayonne Sopo, del Clúster de Energía de la Comunidad Valenciana; María Porcel Valenzuela, del Instituto Tecnológico de la Energía; y Laura Cano Casanova, de Greene Enterprise
05/01/2023La pyme valenciana Greene, el Instituto Tecnológico de la Energía (ITE) y el Clúster de Energía de la Comunidad Valenciana (CECV) han desarrollado un proyecto innovador que combina dos aspectos de máxima actualidad en el sector energético como son la generación de energía a partir de hidrógeno verde y la economía circular. El proyecto se denomina SIGEN2H2 - Investigación base en la generación de hidrógeno por medio de técnicas de gasificación a partir de mezclas de fracciones rechazo de residuos que acaban en vertedero y modelos de simulación para su optimización.
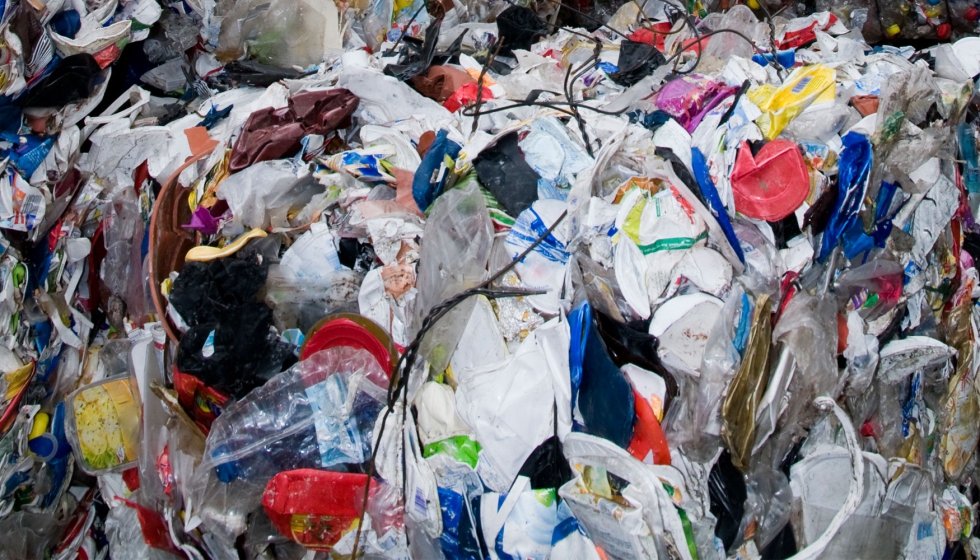
El consumo mundial de energía, las emisiones de gases de efecto invernadero y la contaminación del aire siguen aumentando; por lo tanto, es necesario desarrollar e introducir nuevas alternativas a los combustibles fósiles. El hidrógeno verde es una solución prometedora hacia un sistema energético descarbonizado, ya que se puede utilizar para el almacenamiento de energía a largo plazo a partir de fuentes de energía renovables, para la sustitución de combustibles fósiles en la movilidad y calefacción, y como materia prima limpia para la industria1,2.
La producción de H2 a partir de residuos mediante los procesos termoquímicos de gasificación con H2O, pirólisis y craqueo (proceso integral de gasificación) es una alternativa a su generación con el empleo de combustibles fósiles mediante el reformado o el producido mediante electrólisis de agua, además de ser una fuente renovable e inagotable, ya que el ser humano en su actividad diaria consume productos y materias primas de diversa índole y genera sus correspondientes residuos. La transformación de mezclas de residuos conteniendo CDRs (combustible derivado de residuos, con diversos plásticos) y biomasas mediante pirólisis térmica para la producción de hidrógeno es, por tanto, una alternativa innovadora y factible que puede ofrecer ventajas competitivas para el almacenamiento de energía.
El objetivo del proyecto ha sido la investigación base en los métodos óptimos de generación de hidrógeno a partir de mezclas de residuos, y tratados por medio de procesos de gasificación, que de otro modo acabarían en vertedero o incinerados. Como tecnologías de proceso, se ha combinado la pirólisis y gasificación con electrólisis SOEC como coadyuvante para el aporte de hidrógeno y oxígeno. La información de operación del proceso de testeo de revalorización de residuos para obtención de H2 se ha utilizado para la creación de un modelo de simulación de la parte del proceso específica de generación de hidrógeno.

Figura 1. Diagrama del proceso.
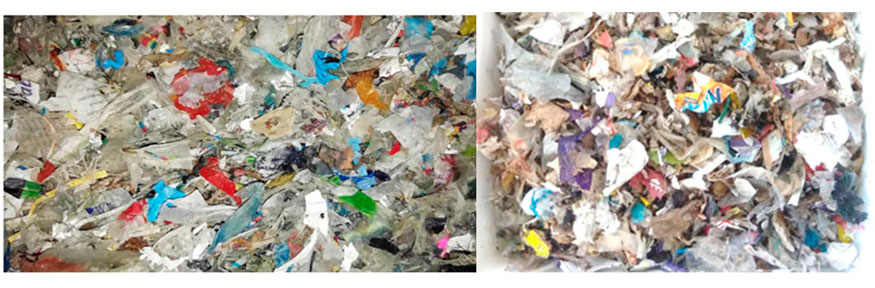
Una nueva configuración a escala de laboratorio se ha construido en donde se ha maximizado la producción de H2. El caudal de entrada de residuo ha sido de 1 Kg/h para la gasificación con vapor de agua. Con el objetivo de simplificar el proceso y poder analizar cada proceso detalladamente (pirólisis, craqueo y gasificación), en esta primera fase la configuración que se ha diseñado es en discontinuo. Una vez analizados los resultados derivados de esta configuración en la siguiente fase se estudiará el proceso en continuo. La planta se ha diseñado para estudiar el proceso en un reactor tubular horizontal, con capacidad para pirolizar hasta 10 Kg de CDR, de forma discontinua.
Para el proceso integral de gasificación para obtener H2 es importante que se produzca char para su posterior gasificación, y en este char cuanto mayor carbono fijo en el mismo, mejor. Los residuos seleccionados han sido caracterizados y se ha visto que el CDR1 es con el que mayor cantidad de char se obtenía. Sin embargo, aunque el CDR1 tiene una cantidad de carbono fijo ligeramente inferior se ha decidido utilizar para la prueba de gasificación por tener un carácter más gasificable (el CDR2 tiene más carácter coquizable).
Las condiciones de pirólisis y gasificación se han optimizado para maximizar la formación de H2/CO que luego entrará a los siguientes procesos. Se han aplicado los tratamientos térmicos sobre los residuos en los módulos diseñados a tal efecto y con los datos obtenidos se ha concluido que las condiciones de operación óptimas para la producción de hidrógeno han sido 500°C para la pirólisis y 1.200°C para la temperatura de craqueo obteniéndose una relación H2/CO de 1.35 con un 12% de H2. El proceso de gasificación con vapor de agua produce un aumento del % en H2 obtenido (~17 %) y una relación H2/CO= 1.26-1.41.
Para la reacción de water gas shift (WGS) el hecho de que la reacción sea exotérmica hace que esté favorecida termodinámicamente a bajas temperaturas y cinéticamente a altas temperaturas3. De la revisión bibliográfica realizada se ha decidido estudiar la reacción de WGS a alta temperatura ya que los catalizadores empleados presentan bajo coste y resistencia al azufre. Los catalizadores seleccionados han sido de base hierro con y sin promotores de la activad (Fe/Al2O3 y Fe (Cu, K) /Al2O3). Para la realización de las pruebas se ha diseñado un sistema experimental a escala laboratorio en las instalaciones de Greene. El sistema consta de un panel de gases para poder añadir la mezcla de gases CO y vapor de H2O y los gases de salida se han analizado con un cromatógrafo de gases acoplado. De las pruebas realizas se ha observado los mejores resultados para el catalizador Fe (Cu, K) /Al2O3 y se ha estimado una producción de hidrogeno de 0.06 kg/h.
Tal y como se ha comentado anteriormente, utilizando la información de operación del proceso de revalorización de residuos para obtención de H2 se ha desarrollado un modelo de simulación del comportamiento electroquímico-térmico del proceso específico de generación de hidrógeno en un electrolizador de óxido sólido (SOEC).
Se han realizado simulaciones para evaluar el proceso de obtención de hidrógeno bajo distintas condiciones de funcionamiento: temperatura, caudal de entrada de agua, densidad de corriente aplicada, presión, etc. Como resultado de las simulaciones realizadas se han obtenido las curvas de consumo específico de energía eléctrica (Figura 3) donde se observa que para un caudal de 0.16kg/h de agua el consumo es mayor de 150kWh/kg de H2 y para un caudal de entrada de H2O de 1.6kg/h está en torno a 30kWh/kg de H2 producido en el electrolizador tipo SOEC.
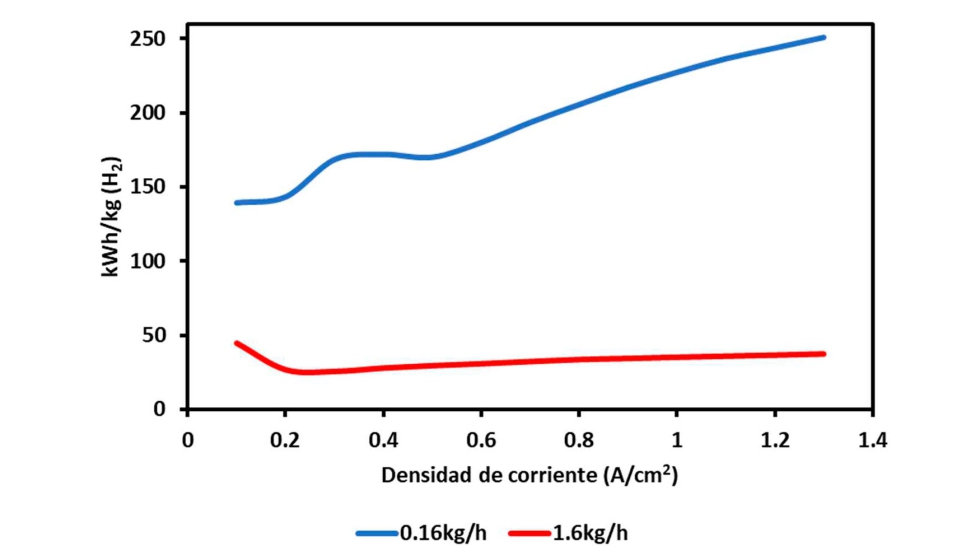
Además del consumo específico también se ha obtenido el rendimiento farádico del electrolizador SOEC (Figura 4) a 800°C para un caudal de 0.16gk/h de H2O (curva azul) estando este en torno al 18.5%. Para un caudal de 1.6kg/h de H2O (curva roja) el rendimiento mayor del 90%.
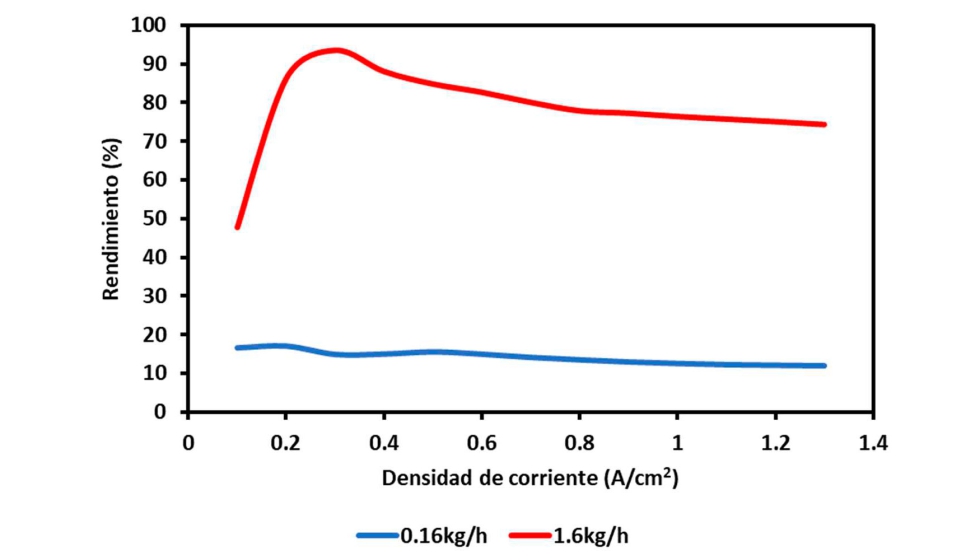
Figura 4. Rendimiento farádico del electrolizador SOEC a 800°C para un caudal de 0.16gk/h de H2O (curva azul) y 1.6kg/h de H2O (curva roja).
Además, mediante la simulación también se obtienen resultados acerca de las fracciones molares de cada reactivo (H2O) y producto (H2, O2) en el interior de los canales del electrolizador.
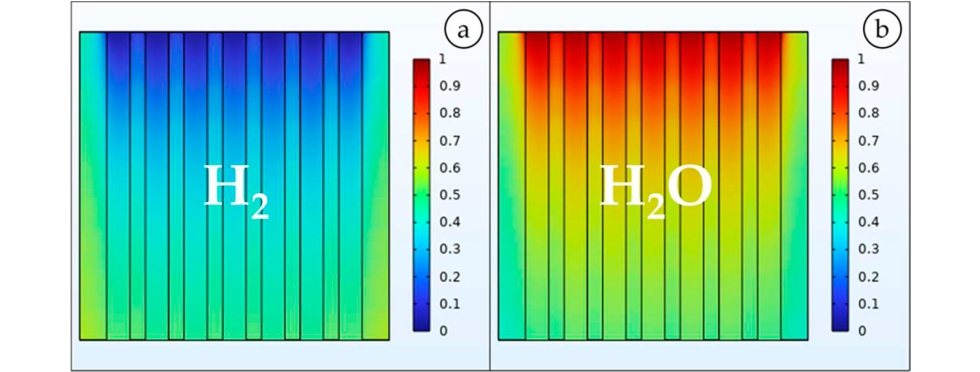
Figura 5. Distribución de fracción molar en los canales internos del electrolizador SOEC para 1.3A/cm2 y 800°C. a) H2 en el cátodo. b) H2O en el ánodo.
Como resultado de la simulación también se ha evaluado el comportamiento térmico de la corriente de gas en el cátodo y en la capa difusora de gases, obteniéndose un comportamiento térmico similar en estos componentes del electrolizador tipo SOEC. Además, también se ha observado que el enfriamiento es menor para valores menores de densidad de corriente y de flujo de entrada de H2O. En cambio, cuando el flujo de H2O es mayor, se observa un mayor enfriamiento.
Conclusiones
• Al aplicar los tratamientos térmicos (pirólisis-gasificación) sobre los residuos en la planta diseñada para tal efecto, se ha concluido que las condiciones de operación óptimas para la producción de hidrógeno han sido 500°C para la pirólisis y 1200°C para la temperatura de craqueo. En la gasificación con vapor de agua se ha conseguido un aumento del % en H2 hasta el (~17 %) y una relación H2/CO= 1.26-1.41.
• Se ha estudiado la reacción de WGS a alta temperatura ya que los catalizadores empleados presentan bajo coste y resistencia al azufre. Los catalizadores seleccionados han sido de base hierro (Fe/Al2O3 y Fe (Cu, K) /Al2O3). De las pruebas realizas se ha observado los mejores resultados para el catalizador Fe (Cu, K) /Al2O3 y se ha estimado una producción de hidrogeno de 60 g.
• Mediante estudios de simulación de comportamiento electroquímico-térmico de electrolizador SOEC se han obtenido resultados del consumo específico de energía eléctrica y rendimiento farádico para distintos valores de flujo de entrada de H2O y temperatura de funcionamiento de 800°C. Es conveniente optimizar el flujo ya que un valor de flujo insuficiente se traduce en un consumo rápido del reactivo (H2O) y como consecuencia, la reacción se ralentiza al agotarse el reactivo, o cuando la concentración de los productos (H2 y O2) es elevada.
Referencias
- D. Jure-Jovan, G. Dolanc, Energies, 13 (2020) 6599.
- Dincer, Int. J. Hydrogen Energy, 37 (2012) 1954–1971.
- T. Shido, Y. Iwasaea, 141 (1979) 109–105.