Ejemplo de método de determinación práctica de la ventana de proceso o área de moldeo
José Ramón Lerma, dpto. técnico de Biesterfeld Ibérica
08/03/2022Ejemplo de método de determinación práctica de la ventana de proceso o área de moldeo (En este caso, para la etapa de postpresión en función de la temperatura de masa). Podemos determinar cuál es nuestra ventana de proceso, diagrama de moldeo a través de un sencillo DOE con dos factores. En este caso vamos a tratar los factores de temperatura de masa y presión de compactación.
El llenado del molde con material plástico fundido podemos dividirlo en 3 etapas claramente diferentes. La primera es la de llenado volumétrico de la cavidad. En esta fase controlamos la velocidad de entrada del material así como la temperatura del molde y de la masa. La segunda etapa es la de compactación o compensación de la contracción volumétrica que se producirá durante la etapa de enfriamiento del material dentro del molde. En esta etapa controlaremos la presión de compactación y el tiempo de aplicación de esta presión y debemos permitir la entrada de moléculas de plástico fundido en el molde hasta alcanzar el peso teórico de la pieza.
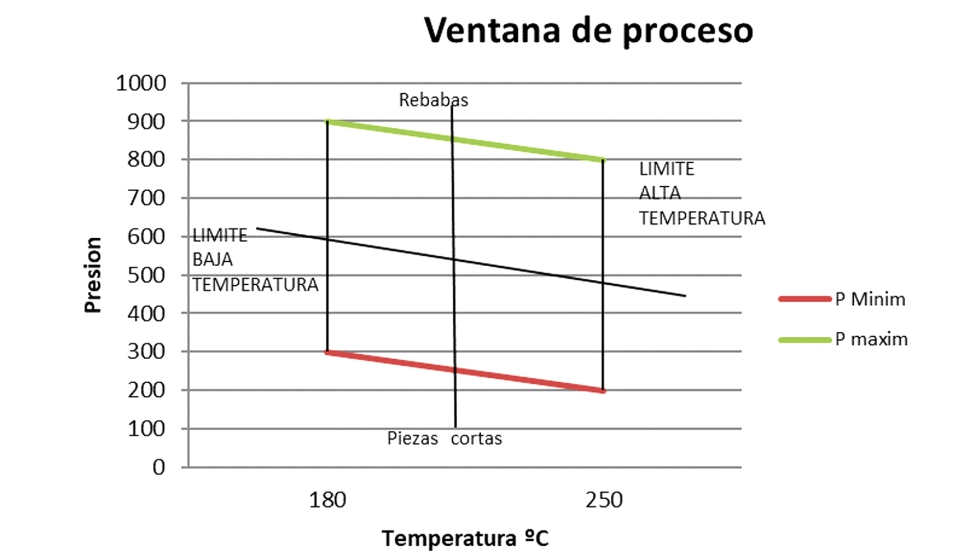
Esta segunda etapa también denominada compactación o fase de postpresión definirá en nuestra pieza inyectada, el peso, las dimensiones, la repetibilidad de la superficie del acero del molde (pulidos, texturizados, etc.), así como el nivel de estrés de moldeo, lo que puede influir en cierto tipo de 'warpage' o alabeos o en algún problema con acabados posteriores de la pieza inyectada, pintado, cromado, paso por horno, etcétera.
De aplicarse esta segunda etapa de modo insuficiente obtendremos piezas cortas, rechupadas, con vacuolas interiores o de dimensiones y peso inferiores a lo requerido o con deformaciones posteriores. Por el contrario, de aplicarse en exceso esta segunda etapa nos puede provocar piezas grandes dimensionalmente, rebabas, dificultades en la expulsión, estrés o tensiones internas etc..
Finalmente existe una tercera fase dentro de esta etapa de prostpresión denominada de mantenimiento o hold para asegurar que la entrada se cierra o se sella por efecto del enfriamiento natural del material plástico.
Para analizar y optimizar esta segunda etapa o fase de compactación se puede utilizar esta metodología denominada ventana de proceso o también diagrama de moldeo donde se determina el área en la que nuestro proceso –entiéndase como el conjunto máquina-molde-material y parámetros–, fabricará piezas aceptables dentro de especificaciones con distintas combinaciones de dos parámetros. En este caso que nos ocupa serían temperatura de masa y presión de compactación. El objetivo del inyectador es durante el análisis poder detectar causas que impiden disponer de la mayor área o ventana de proceso posible de modo que el proceso sea robusto y estable y poder determinar acciones para que esta ventana aumente en el caso de que sea insuficiente o crítica.
La alegoría aquí sería que nuestra inyectora es como un franco tirador y cada inyectada o ciclo es un disparo. Nuestra ventana de proceso sería la diana u objetivo sobre el que dispara nuestro proceso. Toda inyectada que fabrica piezas defectuosas equivale a disparos fuera de la diana.
Cuanto mayor sea la ventana de proceso (o diana), tendremos mayor cantidad de disparos dentro de la misma y por tanto más piezas ok y mejores ratios de productividad y calidad.
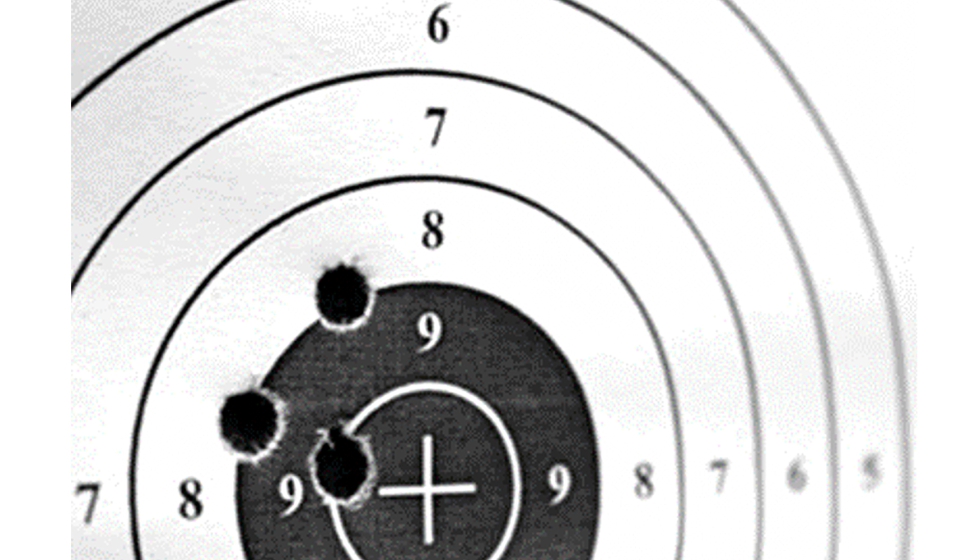
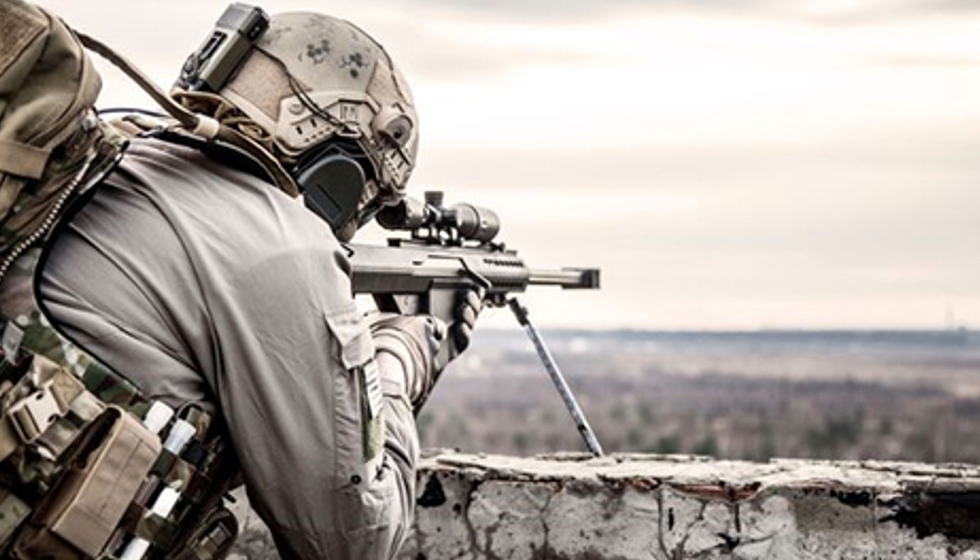
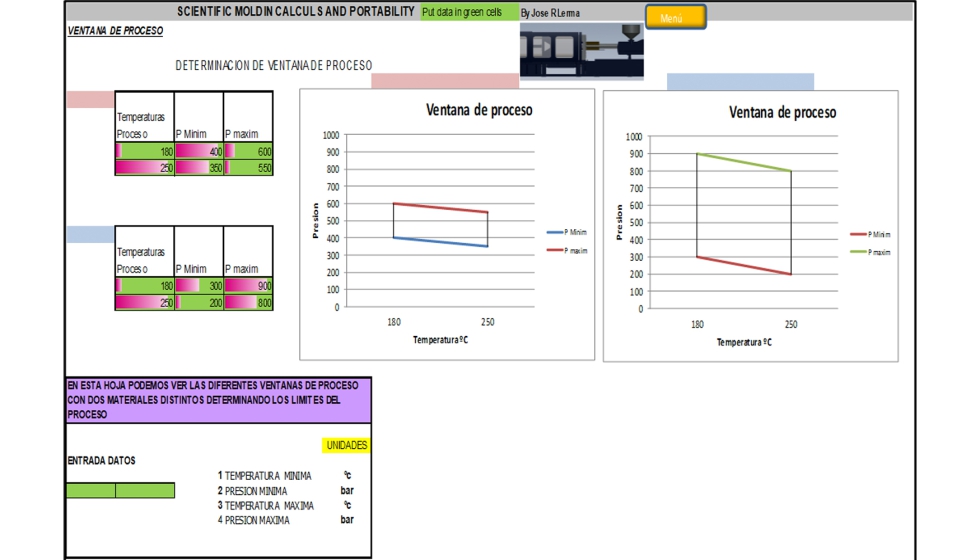
En el gráfico se puede observar que fuera de los límites del área de la ventana de proceso, se obtienen piezas con rebabas o fuera de medida en el límite superior o cortas en función de la presión de la segunda etapa de compactación. Si los límites sobrepasados respecto a los que afectan a la temperatura de masa, las piezas pueden tener ráfagas de degradación, pérdida de propiedades mecánicas, o en el otro extremo infundidos y masa no homogénea que en cualquier caso dará lugar a piezas no aceptables.
Si el proceso definido se sitúa lo más centrado posible de la ventana de proceso, este será mucho más robusto y absorberá las variaciones naturales del proceso que se puedan producir durante las fabricaciones.
Procedimiento para determinar la ventana de proceso
Configuración de la máquina para realizar en ensayo de determinación de la ventana de proceso:
- Programar las temperaturas de proceso de masa para obtener el valor más bajo de las recomendaciones del fabricante
- Programar la velocidad de inyección obtenida del método de la viscosidad relativa o In 'mould rheology test' o la velocidad de funcionamiento normal de la pieza o molde a ensayar
- Colocar los tiempos de post presión y presión de postpresión a valores cero
- Colocar un tiempo de enfriamiento algo mayor del necesario.
Inicio del ensayo o análisis
- Arrancar a inyectar y ajustar el punto de conmutación por carrera al 95 a 98% del llenado total de la cavidad.
- Realizar varios ciclos seguidos para estabilizar el proceso.
- Colocar un valor de tiempo de compactación superior al necesario para asegurar que las entradas se congelen (solo para el ensayo)
- Incrementar la presión postpresión en intervalos de presión hasta obtener piezas aceptables.
Esta presión y temperatura son el punto de la gráfica: baja temperatura - baja presión, vértice- inferior- izquierdo.
Aumentar la presión de compactación en intervalos de presión y anotar cuando la presión es excesiva al resultar piezas con rebabas o deformaciones, agarres en molde, etc. Este punto anotarlo como baja temperatura- máxima presión vértice- superior – izquierdo
Repetir los dos pasos anteriores pero con la temperatura de masa en el extremo máximo de las recomendaciones del fabricante del material.
Esta vez los puntos encontrados serán: Alta temperatura-baja presión y alta temperatura –alta presión vértice inferior- derecho y vértice superior- derecho.
Si unimos estos cuatro puntos encontrados se crea la ventana de proceso o el diagrama de moldeo. La forma obtenida de la ventana puede ser trapezoidal dependiendo de la pieza-material- molde etc. y en ocasiones puede tener una dimensión correcta en un eje y ser muy estrecha en otro eje.
Colocar los parámetros los mas centrados con la ventana definida.
La ventana de proceso nos indica que cantidad de variabilidad puede absorber un proceso antes de empezar a fabricar piezas defectuosas es decir trabajar fuera del área de la ventana de proceso.
Es interesante cuando la ventana es estrecha y por tanto poco robusta, definir acciones para aumentar el área de la misma. Estas acciones vendrán determinadas por los defectos o problemas encontrados durante este test.
Como método de mejora del proceso, este test o estudio nos ayuda a definir los problemas que impiden que nuestra ventana de proceso sea más grande, por tanto atacando estos problemas podremos hacer crecer el área de nuestra ventana de proceso. Es por tanto también un método de mejora continua del proceso.
Abajo, la hoja de cálculo prevista para la entrada de datos y poder graficar la ventana de proceso obtenida. Disponible con el libro Manual Avanzado de Transformación de Termoplásticos.
José Ramón Lerma es autor de los libros: 'Libro Manual Avanzado de Inyección de Termoplástico', que tiene como objetivo ser, por un lado, una herramienta para la formación y, por otro, un manual de ayuda para todo el personal de una empresa de inyección de plásticos y, del recientemente editado, 'Scientific Injection Molding Tools. Productividad a través del dominio del proceso'. Ambas publicaciones, comercializadas por Plásticos Universales / Interempresas (libros@interempresas.net), consta de detallados casos prácticos, amplia información de moldeo científico y un ‘pendrive’ con 20 hojas de cálculo y herramientas de SC Molding o Scientific Injection Molding, además de optimización y definición de proceso, lo que lo hacen único en el mercado. Página web sobre Scientific Injection Molding: www.asimm.es