Conceptos que hacen más fácil la vida en la planta de inyección
Movimiento de succión o descompresión, ventajas e inconvenientes
La succión o descompresión es un movimiento disponible en las máquinas de inyección desde hace muchas décadas. Sin embargo, muchos inyectadores preguntan sobre la regulación y utilización de este parámetro o recurso disponible en el proceso de inyección.
La punta del husillo y el anillo de cierre de la misma
Para entender mejor este movimiento de succión o descompresión tenemos que revisar el proceso desde el final de la fase de compactación.
Un instante antes de que termine la fase de compactación, el husillo está empujando con cientos de bares el plástico fundido hacia el molde. El casquillo de cierre de la válvula de la punta del husillo se encuentra herméticamente presionada contra el anillo estático de ajuste trasero, de modo que el material no pueda retroceder.
Cuando la presión de compactación cesa al finalizar el tiempo de compactación, la presión acumulada en la zona delantera hace que el husillo sufra en algunos casos un pequeño rebote y la posición del anillo móvil se separe ligeramente del anillo estático trasero. Esto hace que la presión del material fundido en la zona delantera de la unidad de inyección se reduzca drásticamente.
A partir de ese momento empieza normalmente el movimiento de dosificación a través del giro del husillo. Cuando este empieza a girar, dado su diseño y funcionalidad, el polímero fundido empieza a avanzar y empuja el anillo de cierre de la punta del husillo hacia adelante dejando libre el paso interior disponible para el material fundido, esto hace que el material fundido pueda pasar a través de la punta del husillo hacia adelante.
La distancia que recorrerá el casquillo de cierre hacia adelante para permitir el paso del material fundido dependerá entre otras cosas de la viscosidad del material. En cualquier caso está limitada por la forma de la punta del husillo en su tope delantero, pero es cierto que es una distancia recorrida que el inyectador no controla directamente.
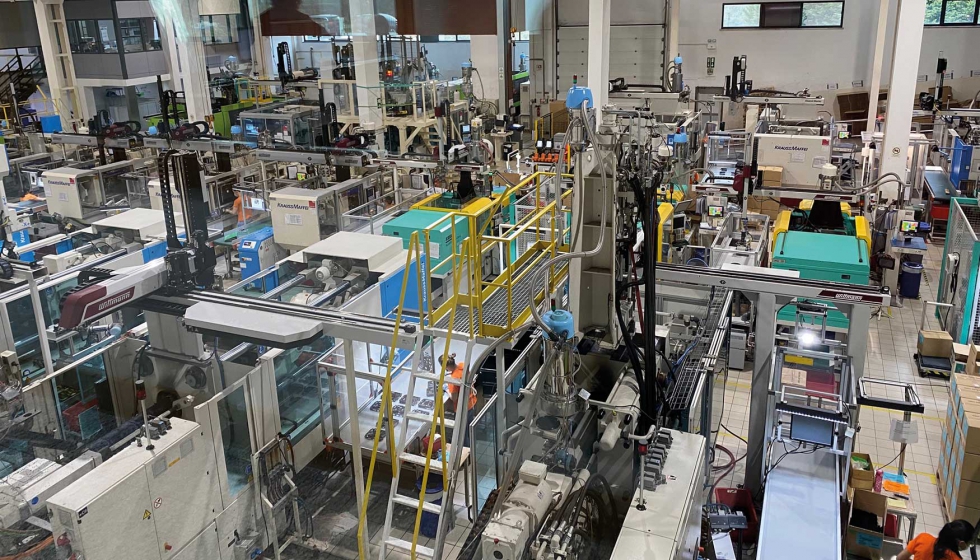
Durante el movimiento de dosificación, el material fundido avanza hacia la zona delantera de la unidad de inyección. Esto hace que la presión en esta zona delantera aumente hasta el nivel de contrapresión a la carga establecido. Ese aumento de la presión en la zona delantera del husillo hace que este vaya retrocediendo hasta alcanzar de nuevo la cota o posición de dosificación.
Durante este movimiento de giro y retroceso, el casquillo de cierre de la punta del husillo se encuentra desplazado del casquillo de cierre trasero para permitir el paso del material fundido pero no en una posición controlada, definida y repetitiva. Esta posición dependerá de la temperatura de masa, del desgaste del casquillo, del tamaño del husillo y sobre todo de la viscosidad del material.
Además, puede suceder en determinadas condiciones que una vez que el husillo detiene su rotación y por tanto, deja de aportar material fundido y es decir, también presión en la zona delantera de la cámara de la unidad de inyección. La presión acumulada equivalente a la contrapresión a a la carga establecida haga que este casquillo flotante de cierre se desplace, por la diferencia de presión existente en la zona delantera de la unidad de inyección, hacia atrás cerrando en mayor o menor distancia. Este recorrido y posición final del casquillo es otra condición no controlada totalmente por el inyectador.
Una vez alcanzada la dosificación programada, el siguiente movimiento desde el punto de vista del husillo y del llenado del molde, es la inyección del material. Para ello el husillo se desplaza hacia adelante con la velocidad programada y utilizando la presión necesaria para cumplir con la velocidad de inyección.
Al iniciarse este movimiento lineal de avance del husillo, en los primeros milímetros de avance el casquillo de la unidad de cierre, que no olvidemos se encuentra situado en alguna parte del recorrido que le permite el diseño de la punta del husillo, se desplazará siguiendo el movimiento lineal del husillo. Por reacción, fricción con el material y presión en la zona delantera de la unidad de inyección, retrocederá hasta el casquillo estático trasero de modo que se obtenga un cierre hermético al material fundido y pueda aplicarse presión en el material fundido sin que este retroceda hacia zonas traseras de la unidad de inyección.
Este doble movimiento, el del husillo avanzando y el del casquillo retrocediendo hasta su apoyo trasero hace que durante una parte del recorrido de inyección, mientras el casquillo de cierre no esté apoyado firmemente contra el anillo estático trasero, una parte del material fundido fugará hacia la parte de atrás del husillo, de modo que parte de la dosificación obtenida en la fase de dosificación, se escapará hacia la parte trasera del husillo.
Esta fuga será de mayor o menor importancia dependiendo de factores tales como viscosidad del material, tamaño del diámetro del husillo, velocidad de inyección inicial, etc.
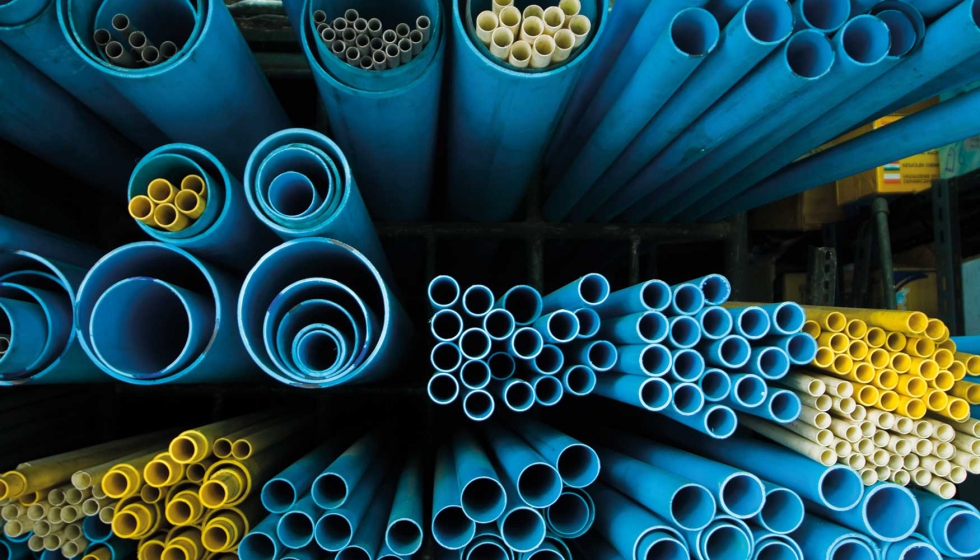
De modo que resumiendo, tenemos en un proceso de alta precisión, como el de inyección de plástico movimientos durante el llenado del molde y la dosificación, que no tenemos controlados totalmente y que no definimos totalmente con parámetros.
Estos movimientos son:
- Posición del casquillo de cierre de la punta del husillo durante la dosificación
- Posición del casquillo de cierre de la punta del husillo en el inicio del movimiento de inyección
Es decir, siendo fundamental la válvula de cierre de la punta del husillo y por lo tanto, todos sus componentes, también lo es la posición de su elemento móvil, el casquillo de cierre.
Para controlar, aunque indirectamente, estas posiciones del casquillo de cierre de la punta del husillo, tenemos afortunadamente la posibilidad de programar la descompresión o succión.
Este parámetro tienes como variables programables, la carrera de descompresión, la velocidad del movimiento lineal de descompresión. También es seleccionable si la descompresión se realiza:
- Antes de la dosificación es decir entre la finalización de la fase de compactación y el inicio de la dosificación.
- Después de la dosificación, es decir, justo al acabar y alcanzar la posición de dosificación.
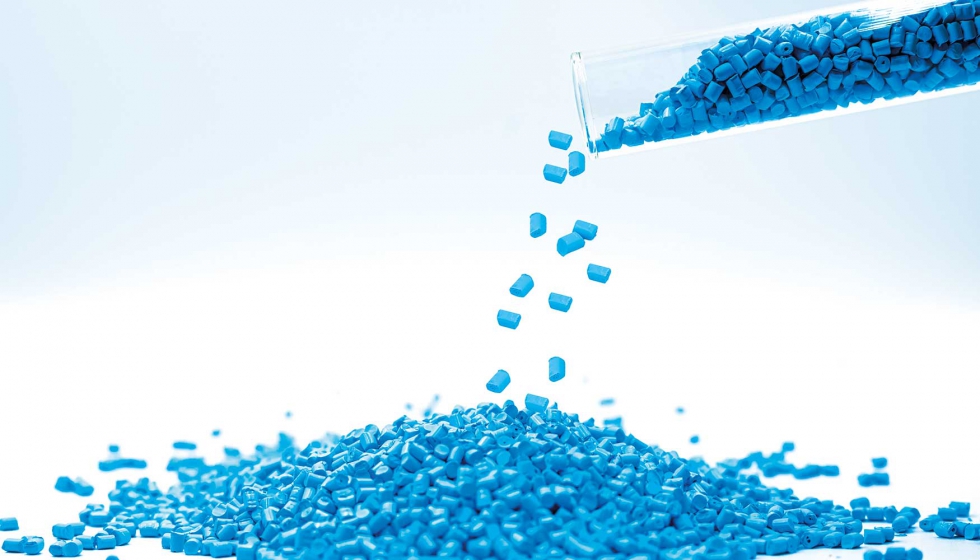
Qué nos aporta y qué es lo interesante de cada una de estas dos opciones
Descompresión antes de dosificar
La gran aportación de este movimiento es que al realizarse un movimiento lineal del husillo hacia atrás, forzamos a que el casquillo de cierre se sitúe en su posición máxima delantera, siendo una posición que, por un lado, aporta el mayor paso libre disponible para el material fundido pero, sobre todo, por otro, nos aporta que el casquillo de cierre tenga siempre una posición constante que será su posición apoyado contra el tope delantero de la punta del husillo. Con esto obtenemos un elemento clave, repetibilidad en su posición y repetibilidad en la dosificación realizada.
Descompresión después de dosificar
Este movimiento permite liberar la presión sobre el material en la zona delantera del husillo generada por la contrapresión a la carga de modo que se minimizan o eliminan los babeos o pérdidas de material fundido a través de la boquilla de la máquina o a través de los canales calientes. Otra ventaja es que aseguramos que el casquillo de cierre de la punta del husillo estará en su posición delantera, apoyado en su tope de ajuste delantero, de modo que cuando se produzca el movimiento de avance del husillo durante la inyección, el recorrido que realizará este casquillo hasta apoyarse de modo hermético en el casquillo estático será siempre el mismo y por tanto, las “fugas” durante este movimiento serán siempre las mismas asegurando un proceso mas repetitivo y constante.
Esta descompresión que se produce al desplazarse linealmente el husillo genera una caída de presión del material fundido que ha sido dosificado en la zona delantera de la unidad de inyección. Esta descompresión del material nos ayuda a evitar las fugas o babeos que se pueden producir cuando utilizamos boquillas de la unidad de inyección directas sin obturación con carro móvil de la unidad de inyección y también cuando utilizamos canal caliente sin boquillas de obturación.
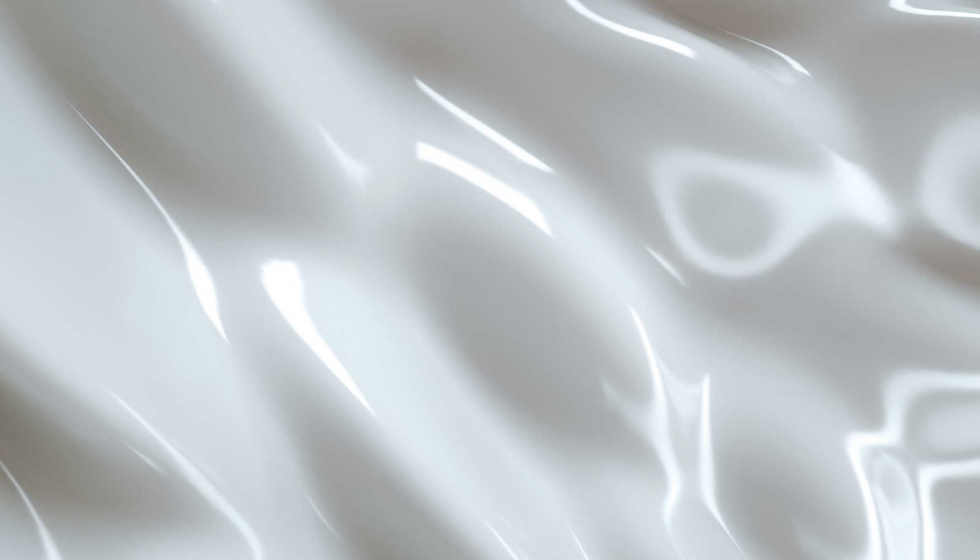
Posibles inconvenientes de la utilización de la descompresión
El principal inconveniente que podemos encontrar cuando utilizamos la descompresión es la generación de ráfagas estéticas en la superficie de las piezas inyectadas. Esto es provocado porque el conjunto boquilla de la unidad de inyección y el molde son totalmente herméticos al plástico fundido pero no son herméticos al aire. De modo que cuando se produce el movimiento lineal del husillo, este provoca una caída de presión o depresión que genera que el aire ambiental sea absorbido por el husillo entrando en la unidad de inyección.
Este aire tiene un nivel más o menos alto de humedad, dependiendo de la humedad relativa del mismo. La humedad o agua, al entrar en la unidad de inyección y debido a sus altas temperaturas, se vaporiza inmediatamente generando vapor de agua en contacto con el plástico fundido. Este vapor de agua al entrar en el molde durante la inyección del material es presurizado por la presión de inyección generando el defecto por todos conocido y denominado ráfagas de humedad.
Parámetros de programación de la descompresión o succión
Para aprovechar estas ventajas que obtenemos con este movimiento de descompresión o succión, la carrera o recorrido lineal del husillo debe ser como mínimo equivalente a la distancia que el casquillo móvil de cierre puede recorrer entre sus dos topes mecánicos con los casquillos estáticos de la punta del husillo. De esta manera aseguramos que el casquillo de cierre estará apoyado contra estos casquillos estáticos.
Respecto a la velocidad, para minimizar la problemática comentada de las ráfagas estéticas por humedad del aire, es conveniente realizar el movimiento lentamente.
Compresibilidad de los polímeros
Los polímeros en estado fundido son materiales compresibles. Es decir, cuando les aplicamos un esfuerzo o presión, tienden a absorberla antes de ponerse en movimiento.
Esto sucede cuando realizamos la inyección de plástico, el material fundido que hay en la zona delantera del husillo no se pone inmediatamente en movimiento a la vez que el husillo si no que hay una compresión previa del material fundido hasta que el movimiento del husillo se traslada efectivamente al material que entra en el molde. Este “retardo” será mayor cuanto más material o dosis vayamos a inyectar. Con una dosis pequeña tendremos poco “retardo” y con la dosis máxima de la máquina tendremos mucho más “retardo”.
Cuando realizamos la descompresión, movimiento inverso al de la inyección, sucede también lo mismo.
Si realizamos la descompresión antes de la dosificación, esta es mucho más efectiva desde el punto de vista de caída de presión que si la realizamos después de una gran dosificación. Cuanto menos material haya entre el molde o la boquilla, es decir, cuanto más cerca estemos del molde, más efectiva es la caída de presión para un mismo recorrido de descompresión del husillo.