Fabricación de grandes piezas estructurales en composites
29 de enero de 2010
Desde su aparición, en los años 50, los composites han evolucionado de manera considerable, pero esta evolución se ha manifestado de manera muy variada, en función de los diversos ámbitos de su utilización. Inicialmente los composites fueron utilizados para fabricar piezas como cobertores, o capots, sin función estructural ni resistente. Cubrían, tapaban o protegían.
Más tarde, aunque poco, se fabricaron cascos de barcos pequeños, encontrándose que sus capacidades estructurales eran suficientes, e incluso adecuadas, con procesos productivos nada técnicos, y con alta variabilidad de condiciones, siguiéndose con esta tecnología de fabricación casi hasta nuestros días. Cuando los condicionantes típicos de los composites, como la resistencia estructural respecto de su peso y la altísima resistencia a la corrosión, fueron ampliamente demostrados, su uso fue uno de los mayores desafíos para los gabinetes de diseño.
En lugares donde el peso, con una determinada resistencia estructural, era el elemento de decisión, los composites se definieron como la solución más adecuada.
Inicialmente, el uso de los composites para resolver ciertos problemas, por ejemplo cuestiones de peso en vehículos espaciales, se ejecutaba mediante fabricaciones artesanales, poco dadas a controles. Cuando la industria aeronáutica se dio cuenta de las tremendas posibilidades de estos materiales, y quiso utilizarlos, se pusieron de manifiesto los problemas que estábamos apuntando.
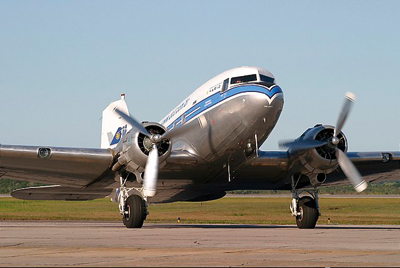
En una palabra, no era posible fabricar series con una garantía de homogeneidad. Esto era debido a que toda la tecnología existente se basaba en métodos de producción manual, con una extraordinaria dependencia de los operarios, tanto en cuanto a las fibras como en cuanto a las resinas y los métodos de impregnación y laminado.
Ya a principios de los años 80, se vio que la utilización de componentes con fibra de carbono abarataban mucho los costes de operación y mantenimiento en la industria aeronáutica, pero la necesidad de contar con elementos fiables, tanto por materia prima como por homogeneidad de proceso, eliminaba dicha utilización. Solamente prototipos fabricados por artesanos de muy alta cualificación era posible producirlos con unos costes sólo asumibles por entidades como la NASA, o cierta industria de armamento. De aquí partió toda la nueva tecnología de producción automatizada de piezas de composite.
Partiendo de que un composite es la unión de una matriz de resina con un refuerzo de fibra, en una forma y medida determinada, aceptaremos que el proceso básico de producción consiste en ‘mojar’ unas fibras, previamente patroneadas, y colocarlas en un molde para que al polimerizar la resina queden con la forma deseada.
Desde el inicio de su uso, los composites se han fabricado según varios procesos, al principio fueron absolutamente manuales y poco a poco fueron eliminando algunas de estas operaciones y se sustituyeron por otras digamos ‘de máquina’.
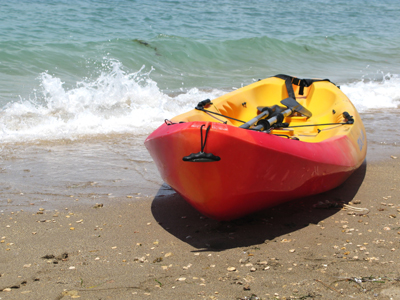
Foto: Sanja Gjenero.
Procesos automáticos actuales
Sin dejar de ser cierto todo cuanto anteriormente se ha dicho, es preciso hablar sobre varios procesos, actualmente en uso, y que realmente cumplen todas las expectativas que demandábamos en los puntos precedentes.
Estos procesos son la pultrusión, laminación en continuo, centrifugación, filament-winding, filament-laying, automated tape laying (ATL), automated fiber placement (AFP) y automated fabric laying (AFL).
Todos estos procesos tienen como punto en común una muy baja participación de la mano de obra en el proceso productivo.
Vamos a continuación a describir esquemáticamente cada proceso, así como a justificar su uso, ventajas e inconvenientes.
Pultrusión
Consiste en hacer pasar por una hilera una determinada cantidad de fibras impregnadas, que se solidifican por polimerización de la resina debido a la temperatura de que hemos dotado a la hilera. La sección de la hilera corresponde a la de la pieza, con sus contracciones correspondientes. Las fibras, en su mayor parte longitudinales, se impregnan en un baño inmediatamente antes de su entrada en la hilera, o bien lo pueden ser en una cámara presurizada donde se inyecta la resina.
Este segundo método es mucho más técnico que el original, pues además de controlar las cantidades de resina, ésta no se encuentra al aire, y en caso de trabajar con estireno disuelto, caso de U.P. y Vinil-ester, no tendremos VOC, con lo que será más fácil cumplir las reglamentaciones de seguridad e higiene. Con este procedimiento se fabrican piezas de sección constante, de longitud variable, con secciones de hasta 1.000 milímetros en una dimensión, y con resistencia transversal.
Laminación en continuo
Sistema principalmente concebido para fabricar láminas de espesor reducido y ancho constante. Se producen láminas de hasta 3 milímetros de espesor y 2 metros de ancho.
El procedimiento consiste en depositar, de forma automática y secuencial, un gel-coat, una manta o varias, seguida de alguna otra de tejido, la cantidad de resina necesaria, y en algunos casos fibra cortada, sobre una cinta transportadora de acero que se desplaza longitudinalmente. Una vez todos los componentes depositados, una segunda cinta comprime las capas en un sistema denominado ‘Double belt press’. En esta prensa real, con desplazamiento continuo, se manifiestan tres zonas térmicas, la primera compacta el material, la segunda con alta temperatura provoca la polimerización de la resina y una final de enfriamiento. A continuación la lámina endurecida es recortada longitudinalmente, por ambos extremos, y finalmente un corte transversal nos delimita su longitud.
Tanto la cesión de gel-coat, como resina y fibra se efectúan automáticamente, así como la generación de presión, y las condiciones de polimerización, con lo que el proceso es muy estable y totalmente automático, pudiendo fabricar láminas con las dos caras acabadas.

Foto: Antonio Jiménez Alonso.
Centrifugación
Con este procedimiento es posible fabricar piezas de revolución de forma continua o discontinua. El proceso discontinuo solo es automático en el proceso de impregnación y polimerización, pero los refuerzos son colocados a mano, por lo que no lo vamos a contemplar. Diremos que se usa fundamentalmente para fabricar postes y mástiles de forma cilíndrica o cónica.
El sistema automático más utilizado es el de producción de tuberías de diámetros importantes, entre los 600 y los 3.000 milímetros.
En el interior de un mandril cilíndrico que está girando continuamente se depositan sucesivamente, resina, fibra cortada, arenas y más resina. La fuerza centrífuga hace que la masa se quede pegada a la pared interior del mandril y la temperatura va provocando el inicio de la polimerización secuencialmente.
Estas tuberías no están dedicadas a alta presión, sino que suelen ser usadas en desagües y conducciones de baja presión.
Filament winding
En español significa ‘arrollamiento filamentario’ y consiste en arrollar sobre un mandril fibras que previamente han sido impregnadas de resina. El mandril posee un movimiento de giro, y un carro con movimiento longitudinal nos va cediendo la fibra impregnada.
La conjunción del movimiento de giro con el de traslación, genera deposiciones helicoidales de fibra, con distintos ángulos. Es posible obtener ángulos entre prácticamente los 90 y los 25º, respecto al eje. Ángulos muy cerrados nos proporcionan gran resistencia a la presión interna, típico uso en depósitos a presión, de 45º resistencia combinada a cortadura, típico para ejes de transmisión, o sistemas combinados para conseguir cualquier tipo de resistencia necesaria.
El proceso es automático en cuanto a la colocación de las fibras, e incluso a la impregnación, pero la polimerización y el desmoldeo deben ser controlados aparte.
Se fabrican con este proceso las tuberías para presión de hasta 2.000 milímetros de diámetro, en longitudes de hasta 12 metros y presiones hasta los 60 bares. Para la industria química se fabrican tuberías con liner metálico, plástico o sin liner, para presiones de hasta los 200 bar y temperaturas de uso de casi los 200 °C.
Filament laying
Este es un sistema desarrollado por Eurofiber y en uso desde hace algunos años.
Como ya se ha dicho el filament winding no puede disponer las fibras paralelas al eje de bobinado, y cuando queremos obtener piezas con gran resistencia transversal, es necesario un gran aumento de la cantidad de fibras.
Esto se resuelve con el filament laying. Una máquina conceptualmente muy parecida a la de filament winding posee un sistema de cesión de fibra, con un tercer eje, que permite enhebrar la fibra en unas agujas dispuestas en los extremos del mandril. La fibra se coloca en las agujas paralelamente al eje del mandril y con un bobinado de paso muy corto se consigue una compresión de compactación, que elimina burbujas de aire ocluidas y obtiene una relación de fibra a resina muy elevada.
Con este procedimiento, es posible fabricar piezas de gran resistencia transversal con las características de fiabilidad de las piezas de filament-winding.
Los mandriles son algo más caros que los normales, pero las ventajas son innegables, en piezas como mástiles de todo tipo, incluidos los marinos, ejes de transmisión, tuberías a presión autosoportadas, etc.
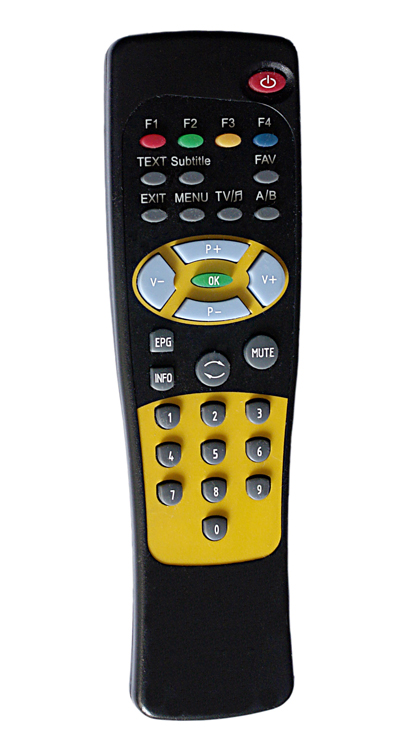
Foto: Antonio Jiménez Alonso.
Automated tape laying
Este sistema fue desarrollado para dar respuesta a las necesidades de la industria aeronáutica, con objeto de fabricar los planos aerodinámicos de las aeronaves. La absoluta necesidad de rebajar pesos en los aviones, recomendaba el uso de materiales compuestos de fibra de carbono por su relación peso-resistencia, pero no existía un sistema que cumpliera las necesidades, no solo de calidad sino de confiabilidad, ya que todos los procedimientos eran manuales.
El sistema final, actualmente fabricado por tres empresas en todo el mundo, está basado en un cabezal que alberga una bobina de material unidireccional preimpregnado. Las dimensiones de la bobina condicionan las del cabezal, de modo que actualmente se usan bobinas de 300 milímetros de ancho y un diámetro exterior de 400 como máximo. La cinta se desenrolla controladamente y se deposita sobre el molde mediante un rodillo que la aprieta sobre él. Un sistema de calefacción calienta la cinta para conseguir el tack adecuado, y ésta se adhiere al molde o a la capa ya depositada. El cabezal posee los tres movimientos en los ejes X, Y y Z, más una rotación sobre el eje vertical y una segunda sobre un eje horizontal.
La calidad obtenida es muy alta, tanto por los controles electrónicos de posición, como por los controles internos de calidad, de los que es posible dotar a la máquina. El problema de estas máquinas es la relación entre su coste y su productividad.
Automated fiber placement
Para resolver el problema del ATL, que no puede depositar curvas, se desarrolló el AFP. Si el problema se generaba por el ancho de la cinta, éste se resolvió utilizando cintas muy estrechas, entre los 3 y los 6 milímetros. En este caso sí es posible doblar la cinta sin que se generen arrugas. En lugar de utilizar una sola se usan hasta 32, cada una con su correspondiente sistema de desbobinado, transporte y compactación.
Ahora el almacén de material, 32 bobinas, ya no puede estar en el cabezal, y se sitúa en un alojamiento exterior, móvil y atemperado para el prepreg. Éste sistema también cuenta con un sistema de calefacción para generar el tack.
Automated fabric laying
El desarrollo en el uso de los composites en los últimos años hacía pensar que las necesidades de automatización llegarían a la industria general, igual que habían llegado a la aeronáutica.
El equipo de Eurofiber, que ya había desarrollado el proceso de F.L. hacía varios años, se empeñó en desarrollar un sistema equivalente para telas y fabrics. La idea era generar un sistema que tuviera una alta productividad, poca mano de obra, y nula participación de ésta en la calidad de la pieza, además de un coste de máquina asequible por la industria de composites.
Como primer paso, se fijó la deposición sobre superficies planas, aunque con grandes dimensiones y partiendo de fabrics secos para ser impregnados en línea con resina líquida. Como fruto de tres años de trabajo se ha desarrollado un procedimiento y se ha construido un primer demostrador, capaz de depositar telas de 2 metros de ancho, con una densidad de hasta 1.200 gr/m2, impregnando en línea a una velocidad de 400 mm\1s\2 lo que supone una productividad de más de 2.000 kg/h, contando paradas y cortes.
La máquina consta de un carro que se desplaza sobre las guías de un sistema Gantry, tan largo como sea necesario para la pieza. En la parte superior del carro se posiciona la bobina de material con control de tensión en el desbobinado. La tela cae sobre una pareja de rodillos que la arrastran, introduciéndola en el interior del cabezal.