La vista puesta en lo esencial
Las cintas termoplásticas generan grandes expectativas. Su influencia en la próxima generación de compuestos termoplásticos se prevé determinante. Sin embargo, la colocación de las cintas debe ser muy precisa o no prestarán el rendimiento esperado. Además, la tecnología para procesarlas no debe ser demasiado costosa o de lo contrario no serán rentables. Se trata de extraer el mayor provecho posible de los materiales de partida que el mercado ya ofrece actualmente. Solo así se logrará avanzar en el uso de compuestos termoplásticos basados en cintas. Engel, representada por Roegele en el mercado español, contribuye de modo importante a este avance utilizando, para colocar las cintas, un software de control muy preciso combinado con tecnología de cámara.
En la regulación convencional de procesos de colocación de cintas, el resultado depende de muchos parámetros de entrada distintos. Influye, sobre todo, la calidad del material de partida, pero también, por ejemplo, la exactitud con la que se mantiene la anchura de cinta predefinida. A la hora de colocar las cintas, el uso de sensores y software inteligente permite mejorar decisivamente la calidad del componente.
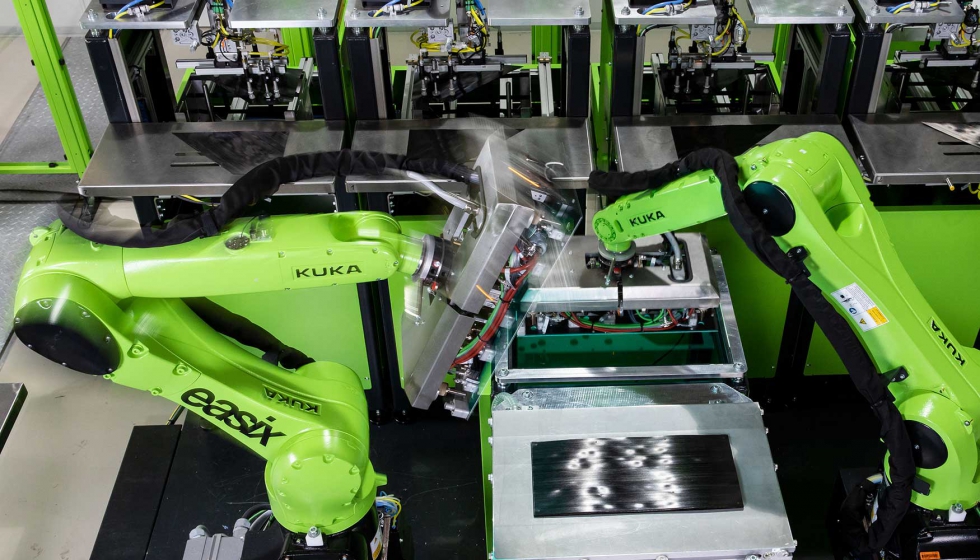
En determinados sectores, ya existen máquinas con soluciones de software avanzadas capaces de optimizar el procesamiento de forma autónoma. Para obtener aún mejores resultados en el futuro, las instalaciones de colocación de cintas deberán generar más información que pueda usarse directamente para controlar el proceso en curso. Así pues, la capacidad de detección de los sensores de las instalaciones resultará decisiva para que los compuestos termoplásticos se abran paso en el mercado.
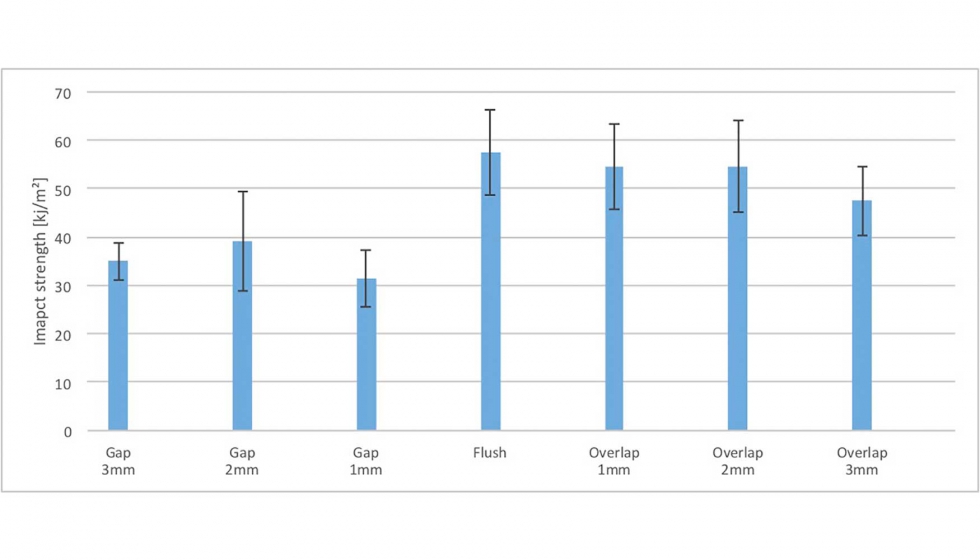
En el futuro, las instalaciones deben poder elegir, de entre una gran cantidad de datos suministrados por sensores, la información relevante para el respectivo proceso de colocación. Para ello, será esencial el uso de tecnologías de cámara. Los datos procedentes de imágenes aportan información que, mediante soluciones de software inteligentes, se puede incorporar a un proceso especialmente adaptado a cada componente individual.
Un rendimiento mecánico-estructural todavía mayor
Los compuestos termoplásticos ya están implantados en la elaboración de chapas orgánicas, donde un tejido de fibras de vidrio o de carbono se integra en una matriz termoplástica de PP, PA, PC o PEEK. Las cintas añaden otra variante de compuestos termoplásticos. Estos materiales unidireccionalmente reforzados tienen la ventaja de no presentar ondulaciones en las fibras (la subida y bajada de las mismas que es habitual en los tejidos). El componente puede tener fibras óptimamente estiradas y el resultado es un mayor rendimiento mecánico-estructural.
Además, en lo que respecta a las cintas, la fase de tejido desaparece del proceso. Mediante un proceso continuo, las mechas de fibra de vidrio o de carbono se incrustan directamente en el material de la matriz termoplástica. Además, los materiales se pueden procesar de modo que generen pocos desperdicios. Las cintas se pueden disponer de forma específica conforme a las cargas previstas y es posible trabajar con distintos grosores dentro de un componente. En resumen, hay muchos motivos para pensar que los compuestos termoplásticos basados en cintas tendrán éxito.
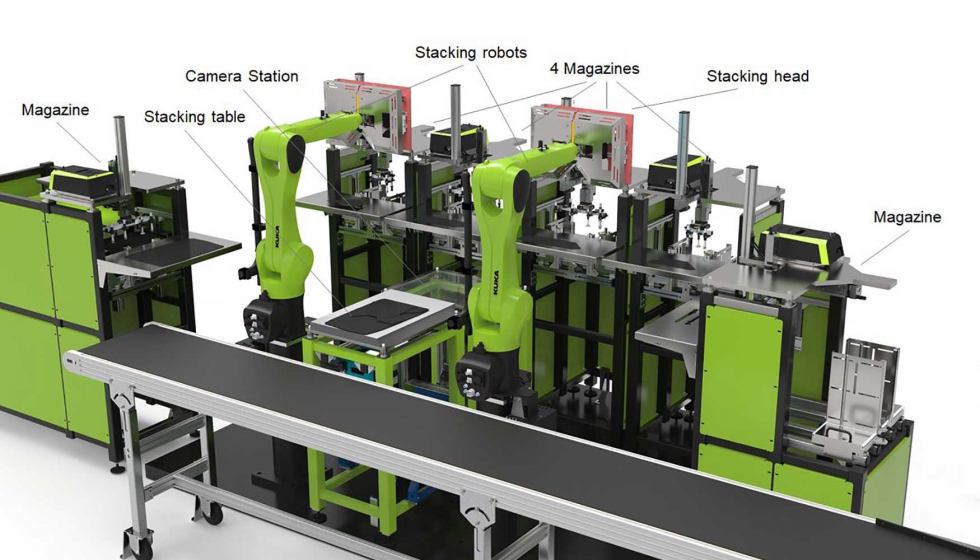
La calidad depende de la precisión de colocación
En muchas aplicaciones, una única cinta no es suficiente para lograr los parámetros mecánicos requeridos. En estos casos, es necesario unir varias cintas formando una pila y consolidarlas para crear una placa. Los grosores de cinta típicos están entre 0,14 y 0,3 mm. Para lograr un grosor de pared de por ejemplo 1,5 mm, se requieren cinco hasta diez capas de cinta. Además, a menudo hacen falta varios recortes por cada capa de cinta, bien porque la anchura que es preciso colocar no se puede abarcar con un único recorte de cinta o bien porque combinar varios recortes ayuda a minimizar los residuos.
Al colocar las cintas, los recortes se unen entre sí mediante soldadura por puntos. En el siguiente paso del proceso, la pila de cintas se consolida y forma una placa maciza. Para ello, toda la formación se funde con cuidado a fin de soldar entre sí las superficies enteras de todas las capas de cinta individuales, que al enfriarse se solidifican y forman una placa. Para la producción de componentes, el producto semielaborado resultante se calienta finalmente en un horno de infrarrojos, se conforma en un molde y, si es necesario, se funcionaliza mediante moldeo por inyección.
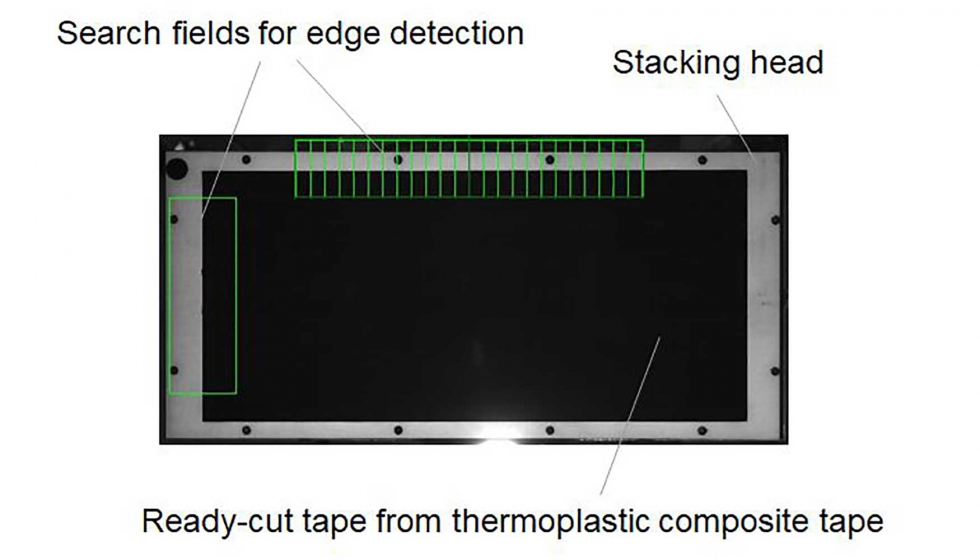
Colocar los recortes de cinta con exactitud es fundamental para la calidad del producto final. Después del proceso de colocación, ya no es posible cambiar la orientación de unas cintas respecto a otras. La fase de colocación de las cintas es, por tanto, la única y última oportunidad de efectuar correcciones. Cuando hay una separación entre dos cintas, surge lo que se conoce como un “callejón”. En él se acumula material de la matriz durante la consolidación y las fibras se pueden desplazar hacia un lado. En el peor de los casos, durante la consolidación puede incluso formarse una cavidad con forma de aguja. Otra causa de que las fibras se desvíen durante la consolidación es el solapamiento de dos cintas en un punto. En consecuencia, tanto las cavidades como los solapamientos dan lugar a puntos débiles en el componente.
La Imagen 1 muestra los resultados de un ensayo de flexión por choque. Las piezas de ensayo se fabricaron en un instalación-laboratorio (Imagen 2) utilizando cinco capas de cinta (PA6CF60). Se eligió una formación de capas de 90° y 0° (90/0/0/0/90) y en la capa del centro (de 0°) se crearon defectos con distintas anchuras de separación y solapamiento. Para ello, la capa del centro se dividió y, a continuación, se colocó de tres maneras: alineada (borde con borde), solapada y separada hasta tres milímetros. El ensayo mostró que tanto la separación como el solapamiento reducen la resiliencia, y que esta disminución de la resiliencia es más marcada en el caso de la separación que en el del solapamiento.
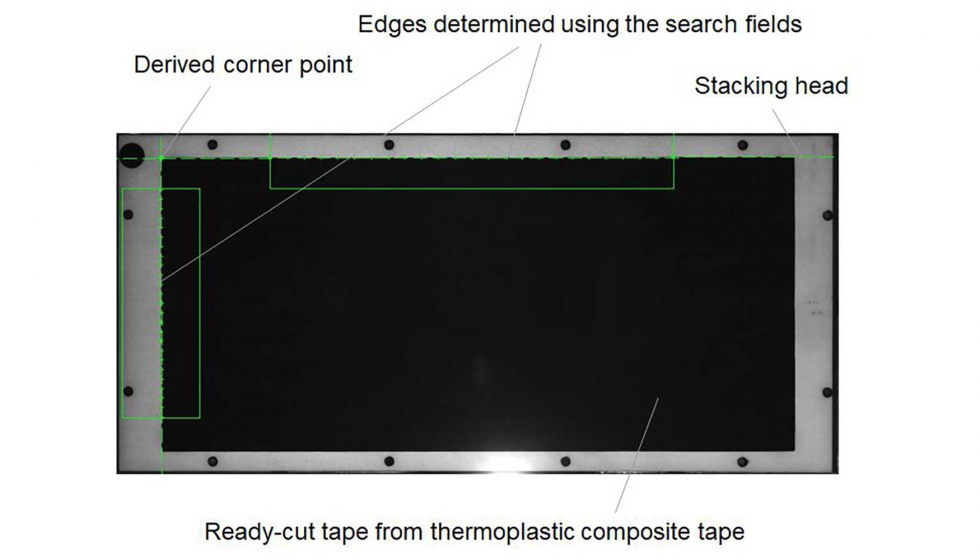
El objetivo debe ser, por tanto, colocar las cintas de manera muy precisa para acercarse mucho al ideal consistente en colocar los bordes de modo que hagan contacto. Las tolerancias típicas de separación o solapamiento rondan los ±1,0 mm. En algunas aplicaciones incluso ±0,5 mm.
En los procedimientos que emplean cintas recortadas con una anchura constante, para que la colocación sea exacta se debe mantener de modo preciso la anchura de cinta nominal. Las fluctuaciones en la anchura de la cinta repercuten automáticamente en la precisión del proceso de colocación. El desafío reside en superar esta dependencia por medio de soluciones basadas en software. Ello es posible con el procedimiento pick and place.
Tener en cuenta los valores de corrección en cada posición de colocación
Para colocar cintas según el principio pick and place, el punto de partida es utilizar recortes lo más grandes posible de tiras de cinta anchas. Los recortes con una forma simple se pueden cortar directamente del rollo. Las formas más complejas se deben troquelar. Lo prioritario es, por un lado, minimizar los residuos y, por otro, maximizar el rendimiento de la instalación.
Idealmente, ya al concebir el componente, la pila de cintas se diseña de modo que el material aproveche lo mejor posible el rollo de cinta y se puedan formar pilas con el menor número posible de operaciones de colocación.
Para un control típico del proceso según el procedimiento pick and place, se precisarían unos recortes de cinta muy exactos y unas guías precisas en los depósitos, además de unos módulos adicionales de alineación y centrado. En este contexto, la tecnología de medición óptica ofrece nuevas posibilidades. Con su ayuda se puede habilitar una instalación que funcione según el principio pick and place para que coloque las cintas unas sobre otras de modo preciso y regulado (Imagen de portada). Los recortes se toman con un cabezal de transferencia (EOAT - End-of-Arm-Tool), para lo cual no es decisiva ni la precisión del recorte ni la posición en el EOAT. En una estación de medición con cámara se averigua la posición del recorte de cinta en relación a las características de referencia del EOAT. Esta in-formación sirve para determinar la posición de destino del robot al depositar el recorte de cinta sobre la mesa de colocación.
A lo largo del borde de un recorte de cinta, se define una zona en la que, en numerosas posiciones –en el ejemplo mostrado son 25– se detecta el paso de la cinta al fondo (Imagen 3). Estos puntos se unen con una recta de ajuste óptimo que se prolonga más allá de la ventana de búsqueda. Lo mismo se hace en un segundo borde. El resultado es un vértice que resulta de prolongar ambas rectas (Imagen 4). Este vértice se puede averiguar con mucha más exactitud empleando los bordes del recorte que efectuando una medición óptica directa, ya que, al troquelar o cortar, a menudo surgen vértices inexactos y poco nítidos.
La información relativa a la posición y a la posición angular de la cinta sobre el EOAT se utiliza para posicionar la cinta al depositarla sobre la mesa de colocación. Los puntos a lo largo del borde de la cinta se pueden averiguar en un intervalo de tres píxeles. En la instalación-laboratorio se consiguió lograr, en varias series de mediciones, una exactitud de colocación por debajo de ±0,5 mm. Eso significa que la separación o el solapamiento de las cintas fue inferior a 0,5 mm. No obstante, la exactitud de colocación alcanzable también de-pende de la rectitud de los bordes cortados o troquelados. Además, el color de las cintas y el contraste con el fondo también influye en la detección de los bordes.
La exactitud en la colocación de las cintas es el valor de medición al que se dirige todo el trabajo de optimización del proceso. Sin embargo, lo principal es el concepto con el que se logra esta alta exactitud de colocación. Utilizando la tecnología de cámara, se obtiene información que permite reajustar y optimizar activamente la colocación mediante el software y así conseguir la exactitud deseada. El software trabaja ininterrumpidamente con el fin de obtener un resultado óptimo, es decir, una colocación lo más exacta posible.
Alto rendimiento en tiempo real
A medio plazo, las tecnologías de procesamiento basadas en o asistidas por software dejarán muy atrás las soluciones convencionales en muchos sectores. Aunque los métodos convencionales permitan obtener una calidad comparable mediante ensayos, ajustes y validaciones exactas, siguen dependiendo mucho de los elementos mecánicos y de la calidad del material de partida. Esta vía es de por sí limitada. Mucho más eficiente es equipar la instalación para que pueda detectar las características del material, valorarlas y operar de manera acorde.
Una manera de añadir valor consiste en utilizar los sensores, además, para observar si en las cintas hay grietas, existen alteraciones en la dirección de las fibras o faltan esquinas, lo que permite detectar diferencias mucho más pequeñas que las que llamarían la atención de un operador atento.
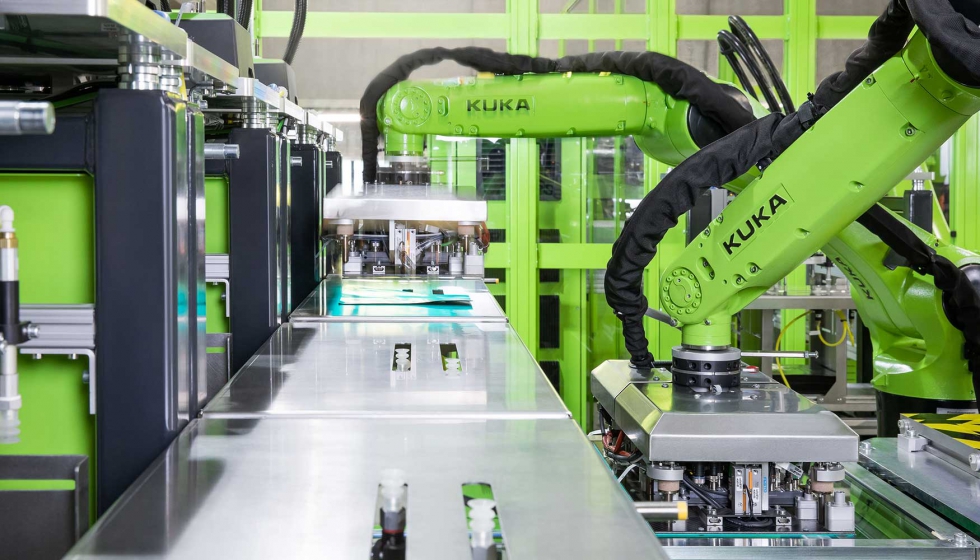
Las celdas de colocación de cintas se diseñan preferiblemente con dos robots y una estación de cámara. En la mesa de colocación, se sujeta la primera cinta mediante vacío. Cada una de las demás capas se une a las que están debajo mediante soldadura por puntos.
Los recortes de cinta se separan en los depósitos de pilas, se disponen sobre mesas de recogida y se mantienen en posición para que los robots puedan aproximarse a dichas mesas a gran velocidad (Imagen 5). En el EOAT hay ventosas que levantan los recortes. Esta configuración permite, en cada paso de la secuencia, un proceso de colocación muy dinámico. En varias series de ensayos y con los robots funcionando de forma alterna, se logró con la instalación de ensayo un tiempo de colocación de 3,4 segundos por cada recorte de cinta.
Para poder detectar bien la cinta en el EOAT al efectuar la medición óptica, toda la superficie de recepción se ilumina con una película electroluminiscente y el EOAT se presiona junto con la cinta contra una placa de vidrio. Se detectan los bordes y se averiguan los vértices del recorte de cinta, y los resultados se ponen en relación con el centro del EOAT. La información derivada de ello se transmite al control del robot para corregir la posición y la posición angular de la cinta. De este modo, la cinta se puede depositar con total exactitud y alineada con un borde de colocación ya existente. Los algoritmos para averiguar la posición de colocación exacta se aplican a las imágenes digitales mientras la cinta ya se está moviendo hacia la mesa de colocación. Por consiguiente, este procedimiento exige de la instalación una gran capacidad de rendimiento en tiempo real.
Pick and place también para pilas híbridas
Con una celda de colocación de cintas pick and place se pueden formar pilas de cintas en el mínimo tiempo y con la máxima precisión. A fin de alcanzar una alta velocidad de colocación y facilitar puntualmente los datos de corrección necesarios, para la medición óptica solo se detectan bordes y vértices seleccionados. No obstante, las grabaciones de imágenes se pueden guardar para evaluar la calidad de la pila y para analizarla posteriormente. Dependiendo de la calidad de producto requerida, se decide qué archivos se guardan automática-mente junto con los datos de proceso. De las piezas que influyen decisivamente en la seguridad se guardan todos los datos de imagen. De las demás piezas solo es necesario guardar aquellas imágenes que se pueden relacionar con fallos en la secuencia o desechos.
Una ventaja importante del concepto pick and place es la posibilidad de formar pilas híbridas. En los depósitos de pilas no solo se pueden colocar cintas, sino también chapas orgánicas con varias capas de tejido, placas de cintas ya consolidadas con grosor de pared constante u otros productos semielaborados termoplásticos. Por eso, como material de partida se pueden emplear semiproductos económicos de varias capas que solo es preciso reforzar in situ. En muchos casos, el reforzamiento de componentes in situ conforme a la ruta de carga permite reducir el grosor de pared inicial. Por consiguiente, con formaciones de material híbridas puede reducirse claramente no solo el peso, sino a menudo también los costes. Y a su vez, como disminuye el grosor de pared inicial del componente, cabe considerar la posibilidad de usar fibras de carbono caras para la producción de series grandes. Las zonas del componente que soportan cargas pequeñas se pueden reforzar con fibras de vidrio económicas, reservando las de carbono para aquellas zonas que deban aguantar esfuerzos mayores. Para una construcción ligera rentable, la colocación de cintas es una tecnología clave.
Fabricación ligera eficiente
La fusión y la solidificación son los procesos físicos centrales que caracterizan la transformación de termoplásticos. Estos cambios de estado se pueden producir en un tiempo relatiamente corto. Por eso, el procesamiento de termoplásticos tiene una productividad superior a la media. En compuestos es habitual usar fibras largas, idealmente fibras sin fin. El resultado son componentes ligeros con valores de rigidez y solidez realmente altos. Los compuestos termoplásticos combinan dos características: procesos muy eficientes y fabricación ligera con unas características excelentes. Precisamente por eso son tan interesantes para la construcción ligera en series grandes.