Este sistema de fabricación es el resultado de un proyecto europeo coordinado por Aitiip en el que han trabajado 15 socios durante 3 años
Kraken, el sistema de fabricación por impresión 3D multimaterial más grande y preciso del mundo, ya está disponible
Kraken se presentó en el Centro Tecnológico Aitiip, ubicado en Zaragoza, en el marco de la conferencia final del proyecto, en la que participaron 120 asistentes de España, Reino Unido, Alemania, Italia, Grecia y Estados Unidos. Kraken es un resultado de investigación del programa H2020 de la UE capaz de producir piezas a través de la deposición alterna de material de fabricación aditiva con operaciones sustractivas (capa por capa) dentro de un área de trabajo máxima de 20 x 8 x 6 metros.
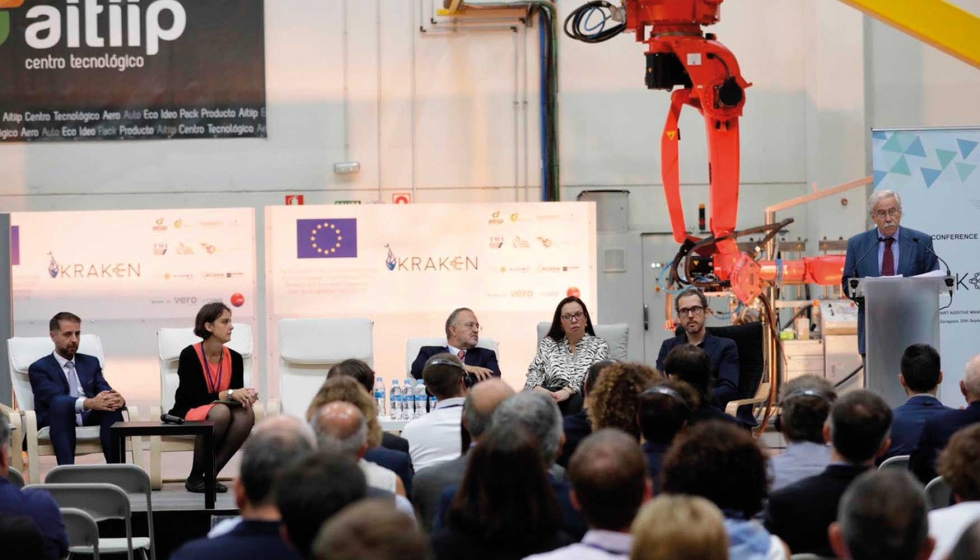
José Antonio Dieste, investigador de Aitiip y coordinador del proyecto, declaró que “la máquina está lista para el mercado, ha sido probada en un entorno de fabricación real y las empresas han validado los demostradores del proyecto en condiciones reales. Ahora podemos entregar piezas o instalar células Kraken de acuerdo con las demandas del cliente“.
Los socios del proyecto presentaron los resultados del proyecto a la audiencia y expresaron su objetivo de revolucionar la fabricación de piezas grandes, metálicas, en resina e híbridas. Gracias a la calidad y el tamaño de las piezas finales así junto con la eficiencia del proceso y la velocidad de producción, Kraken es un sistema de fabricación todo en uno único en el mundo.
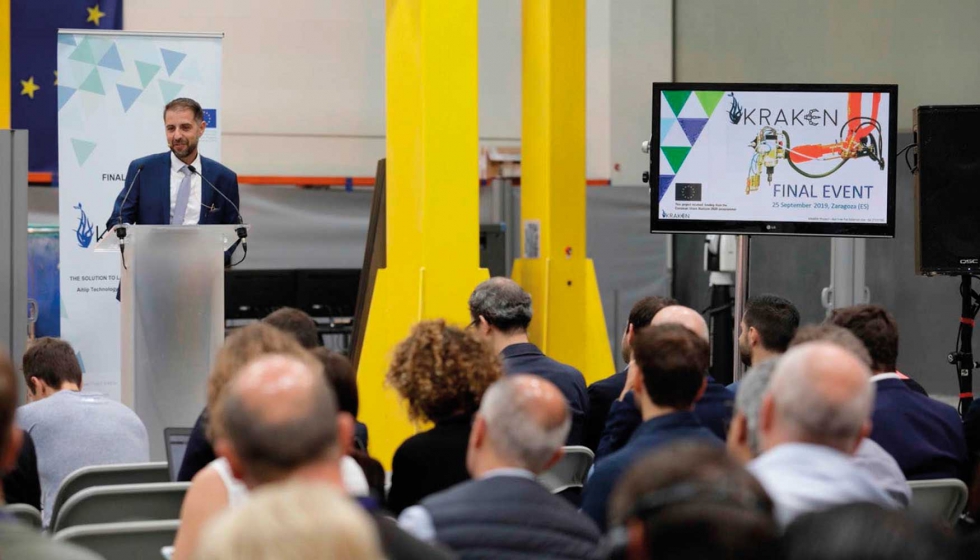
Además de calibración, alineaciones y corrección en tiempo real, la inspección de calidad de las piezas semiacabadas o finales es un paso muy importante y una ventaja adicional del sistema de metrología incorporado. En este sentido, Markus Steiner (Hexagon Manufacturing Intelligence) declaró: “Gracias al Leica Absolute Tracker integrado, las piezas fabricadas por la máquina Kraken pueden digitalizarse en 3D y compararse con el diseño CAD para verificar la calidad de fabricación en todo el volumen de la máquina, incluso completamente automatizado si es necesario”.
“Garantizar la precisión en grandes espacios de trabajo (100 m²) es un desafío que Kraken ha resuelto integrando tecnologías de seguimiento láser en tiempo real dentro del control de circuito cerrado del sistema robótico. Gracias a este método, la precisión de la herramienta puede garantizarse hasta 0,1 mm”, en palabras de Francesco Crivelli, CSEM SA, responsable del diseño de los algoritmos de control y la implementación del software.
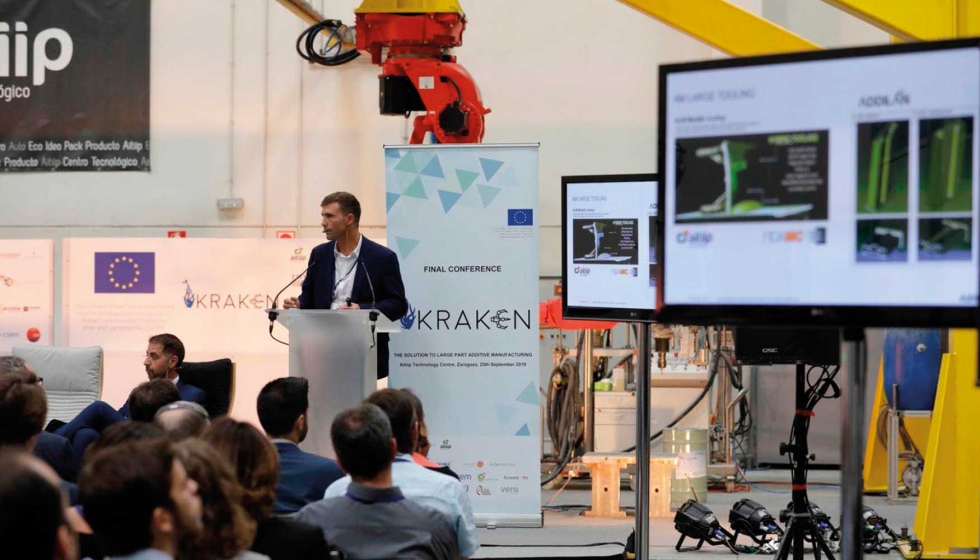
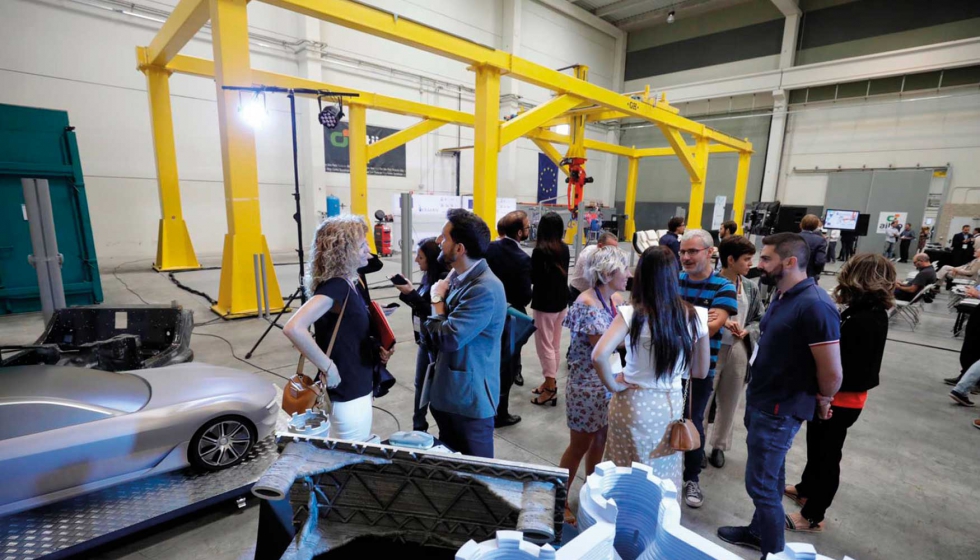
Método de fabricación
El sistema de fabricación aditiva deposita material metálico utilizando WAAM a una velocidad de 1,5 l / h. La máquina Kraken también incluye un sistema de extrusión de resina bimaterial que puede alcanzar tasas de deposición de 120 kg / h. El proceso de metalización puede alcanzar tasas de hasta 6 kg/h.Además, las capacidades sustractivas de la máquina permiten operaciones de corte, lijado, pulido... alcanzando 2 mm de corte a 10 m/minuto.Todas estas operaciones son controladas por un láser tracker, que monitorea y controla la posición de la cabeza 1.000 veces por segundo, corrigiendo su posición automáticamente. El sistema también incorpora dos tipos de cámaras y sistemas de visión artificial para controlar los flujos de deposición y para la verificación posterior de la pieza, mediante escaneo tridimensional.
Los primeros demostradores finalizados se enseñaron por primera vez
La posibilidad de construir grandes piezas de metal y resina mediante la impresión 3D de alta calidad ha despertado el interés de una gran parte de la industria. Estos demostradores tenían como objetivo validar la funcionalidad del sistema y se presentaron por primera vez en las instalaciones del Centro Tecnológico Aittip en Zaragoza (España). Se han fabricado paneles híbridos para el revestimiento de túneles de carretera de 3 x 1,2 m para Acciona, uno de los socios del consorcio. Gracias a la combinación de resina y metal, las conexiones eléctricas pueden hacerse mucho más fáciles ahora.Con respecto al sector automóvil, se ha producido una maqueta de uno de los últimos modelos de automóviles de Pininfarina para validar su diseño. La pieza construida tiene un tamaño de 2,2 x 1 x 0,6 m y un peso de 250 kg. Estas son algunas de las aplicaciones reales que ya se han probado, aunque los sectores que pueden beneficiarse de este sistema son mucho más amplios, ya que ofrece alternativas de bajo coste, alta calidad, rápidas y eficientes para el sector de los utillajes y moldes y para la fabricación de grandes piezas.
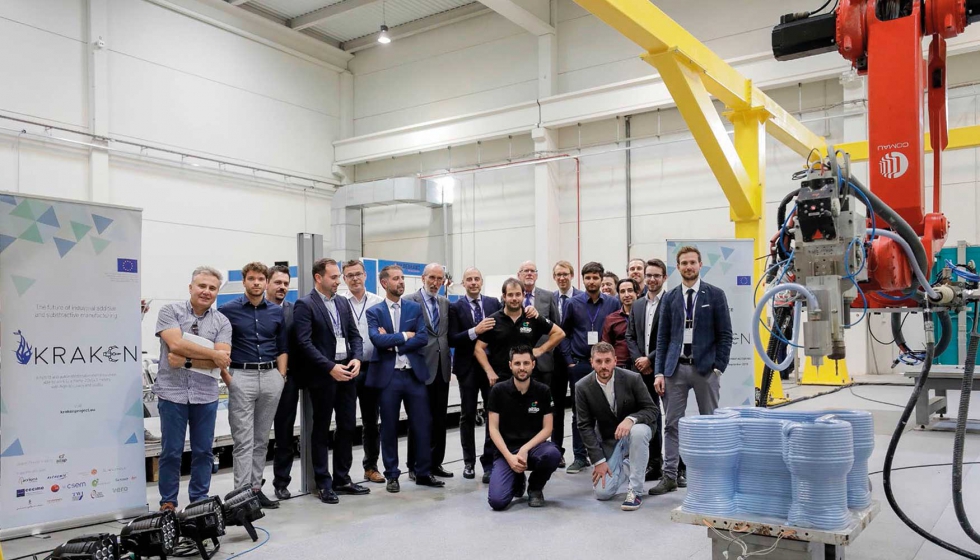