Entrevista a Pere Badalló, coordinador científico-técnico de Leitat para el proyecto HAIRD
De entrada, ¿cómo nace este proyecto y cuál es su objetivo?
Este proyecto nace dentro del programa CleanSky2, de hecho, es una Join Technology Initiative, en la que la Comisión europea financia el 50% del proyecto de un privado, el ‘topic manager’, que en este caso era Fraunhofer ICT. Este centro está desarrollando un nuevo material, un poliuretano, con una resistencia estructural importante. Y su interés era encontrar un demostrador. Para ello abren un proyecto para realizar un asiento para aviones y que, además, sea apto para resolver algunos de los retos de esta industria: que sea ligero —por cada gramo de ahorro peso supone ahorro de emisiones de CO2 y de combustible—, pero que sea fácil de desmantelar, pero también de montar y desmontar, lo que implica la necesidad de reducir el número de piezas que lo componen. Y es que la vida útil de los asientos es menor que la de los aviones… por lo que debe facilitarse la reposición.
Las condiciones, usar su poliuretano, que el 90% del asiento fuera reciclable y reducir al máximo las piezas metálicas.
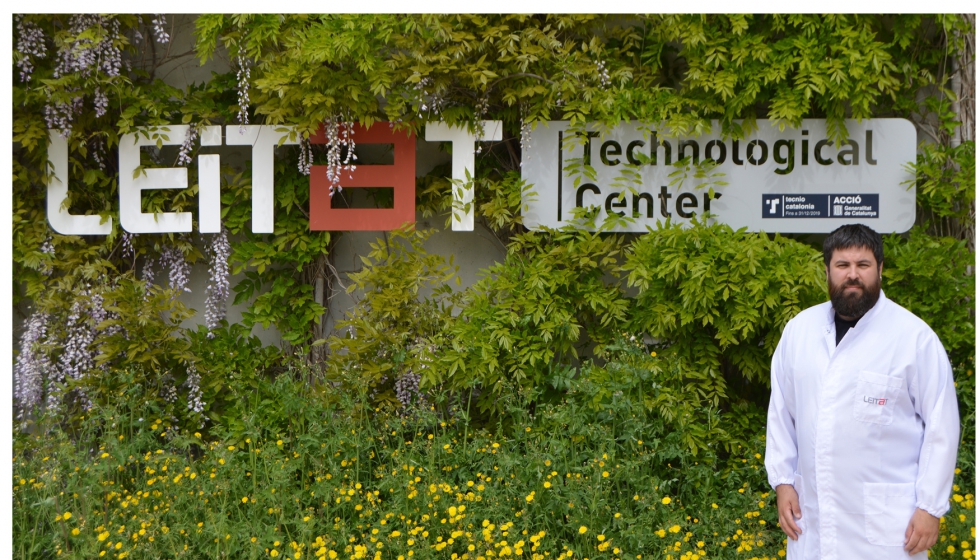
Pere Badalló, coordinador científico-técnico de Leitat para el proyecto HAIRD.
Creo que el tema de la reciclabilidad está superado…
Incluso hemos superado esta cifra: hasta el 95% del peso es reciclable. Todo el material usado está basado en el poliuretano: fibra de carbono con poliuretano (creado por Fraunhofer ICT), espumas con poliuretano, tejidos basados en poliuretano… y el objetivo sería lograr casi un monomaterial… aunque eso será imposible. Pero un 95% de reciclabilidad es un índice muy alto y eso es gracias a que el poliuretano es un termoplástico.
En cuanto al tema de las piezas metálicas… ¿reducir su presencia significa cambiarlas por piezas plásticas o bien rediseñarlas para reducir el porcentaje de metal usado?
Desde los dos puntos de vista. Sustituyéndolas por un diseño más innovador que redujera la cantidad de metal o bien por piezas realizadas por composites u otros materiales. Hay que tener en cuenta que en algunas piezas no se puede sustituir; desde los cinturones hasta los puntos de anclaje, las bisagras, tornillería… Hay cuestiones de seguridad y normativas que deben cumplirse.
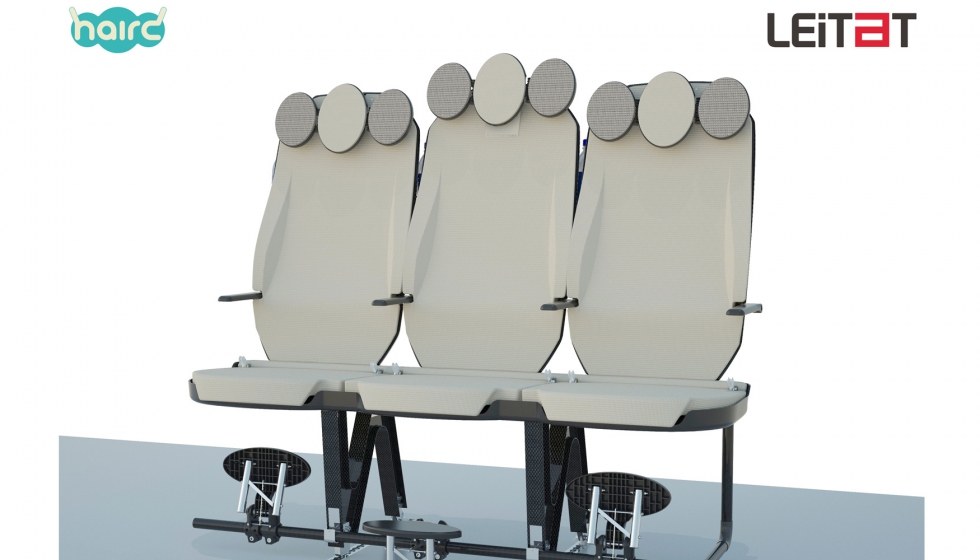
El diseño quería ser rompedor; Leitat hizo 5 propuestas de más conservadoras a más disruptivas, y el ‘topic manager’ eligió este.
Es un asiento de diseño amigable, saludable, eficiente en cuanto a costes, reciclable y de bajo peso… ¿cómo logran todo ello?
Quizá la principal innovación está en la propia producción: está fabricado con composites, pero con unas técnicas de producción automatizadas, o parcialmente automatizadas, algo poco común cuando se trabaja con estos materiales pero que supone una importante reducción de costes. Por ello decimos que es ‘cost effective’, de bajo coste, pero con un resultado de gama alta. Así hemos desarrollado dos categorías, la Economy Class y la Economy Class +, al que hemos incorporado dos elementos como son el reposapiés y el reposacabezas.
Pero además de ‘cost effective’… es también ‘healthy’, saludable, y aquí entra el trabajo del diseñador. Este asiento pretende combatir una de las principales problemáticas para los que viajan en avión durante horas: la trombosis de vena profunda (DVT por sus siglas en inglés, Deep vein thrombosis). Está pensado, a partir de estudios antropomórficos y dimensionamiento del cuerpo humano, para que sea confortable para el 95% de la media de usuarios de aviones. También introducimos un pequeño margen de movimiento, de 5º de inclinación, del asiento, de modo que, según la posición del usuario, esté más cómodo y que la espalda esté en posición correcta y, según se quiera estirar más o menos las piernas, este margen de basculación evita chocar contra el asiento de delante. Y teniendo en cuenta que el espacio entre asientos los marca cada compañía, dentro de unos márgenes, el objetivo podemos decir que es que, en la situación más desfavorable, garantizar el máximo confort. Todo gracias a un arduo trabajo del diseñador y de todo el equipo, que ha trabajado con espumas de diferentes densidades, ha estudiado la distribución de peso del cuerpo humano…
De hecho, es un diseño pensado para que pueda evolucionar fácilmente y adaptarse a las necesidades de producción reales. Ahora esperaremos a saber si pasamos a la segunda fase, que supone la fabricación real y las pruebas de impacto, de 16G de impacto frontal (16 veces la fuerza de la gravedad) y 14G inclinado, que hemos calculado, pero hay que ponerlos a prueba.
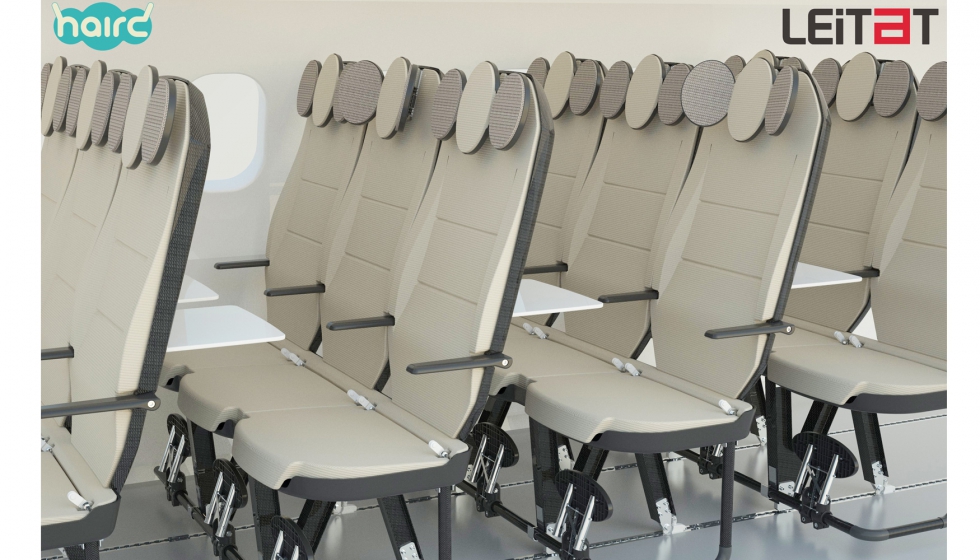
¿Puede explicar un poco sobre el tema de producción innovador que ha comentado?
En general, cuando se trabaja con composites, es una manufactura muy manual. Y es lo que intentamos superar. En Leitat usamos la tecnología de prepreg compression moulding, que consiste en poner el prepreg en un molde de compresión calentado y empieza a curar; el WCM (wet compression moulding) en el que sobre la fibra de carbono se añade el poliuretano en forma líquida y todo se introduce dentro de un molde para darle la geometría final al tejido, que es completamente plano; y el SMC (sheet moulding compound), que se basa en una manta precurada, donde la matriz de fibra larga y la resina ya están mezcladas, que se introduce en un molde y al calentarse, se licua y adquiere la forma deseada. La ventaja del SMC son la posibilidad de obtener geometrías complejas. Y es una técnica fácil de automatizar; basta con tener un operario que corte la manta precurada y la introduzca en el molde… e incluso esto se puede robotizar. ¿El problema? Que estructuralmente no da un resultado tan bueno como las anteriores porque la fibra no es continua. ¿La solución propuesta por nosotros? El comoulding, comoldeo. Realizar dos técnicas en una en distintos pasos: para las geometrías simples de las partes estructurales en las que se requiere resistencia estructural alta en zonas críticas, utilizamos la tecnología del wet compression moulding o en prepreg; Una vez obtenida esta pieza, se introduce en un molde preparado para SMC y hacemos lo que llamamos comoldeo: el resto de la pieza se fabrica como si fuera por inyección con geometrías complejas. Al final tenemos un proceso de unión de dos piezas realizadas con un mismo material, pero con una parte realizada con fibra continua y otra con fibra larga o corta discontinua. Así, aseguramos la rigidez estructural en las zonas críticas, pero no perdemos ‘tiempo’ en aquellas donde no es necesario. Se unen ambas piezas y tenemos el asiento final, solamente juntando las dos partes manufacturadas mediante dos técnicas. Esta es la innovación, usar técnicas cuyo resultado serían perfiles planos pero que, al combinarlas, generamos volúmenes. Y que además estructuralmente consistentes, que se puedan anclar unos con otros, pegar, que sean practicables y que además cumplan con las normativas del sector aeronáutico.
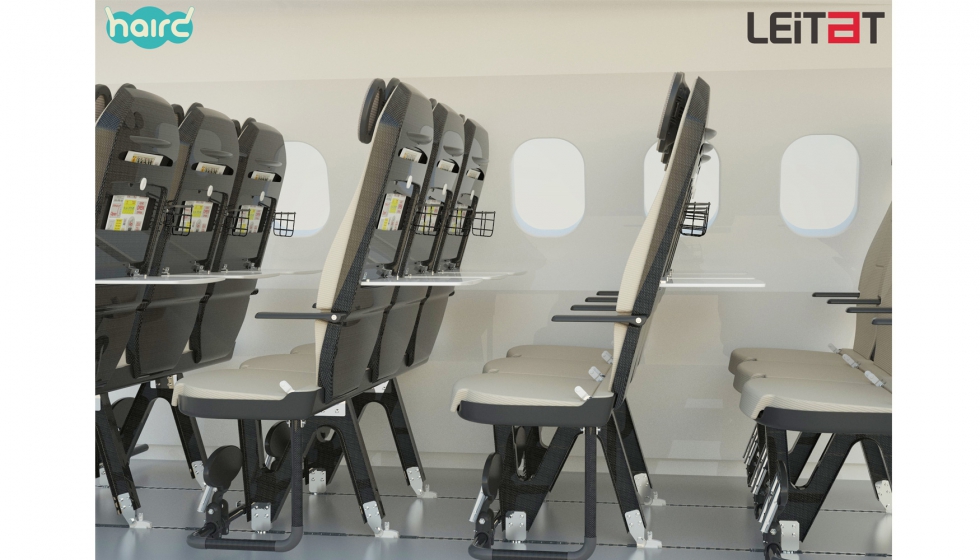
Que no son pocas… en el asiento también hay que tener en cuenta las características de la tela, la espuma…
Son especificaciones que ya deben cumplir el tejido propiamente. En nuestro caso, hemos ‘utilizado’ el tejido de un proveedor que sabemos que ha pasado todas las normativas al respecto. De hecho son los que se ven en los renders.
En cuanto al tema de toxicidad y fuego, es necesario hacer las pruebas componente por componente, para comprobar su resistencia, pero también que no interaccionen los componentes entre ellos. Es una prueba que todavía no hemos realizado, aunque prevemos que no será un problema puesto que son materiales basados en el mismo poliuretano, no hay mezclas de producto. Hemos utilizado sólo espumas de mercado destinadas a la industria aeronáutica.
En resumen, hemos desarrollado un producto único, con ciertos componentes que sabemos que en el futuro serán materiales que estarán en la cresta del estado del arte, pero teniendo claro que, si se quisiera ahora, con algunas modificaciones, se podría lanzar al mercado.
Es decir, es ‘fabricable’
Sí, con ciertos cambios, y con el tiempo necesario de adaptación y pruebas, el producto está diseñado con un concepto funcional. Pero hoy, si lo fabricáramos tal como está diseñado, funcionaría; la mesa se abre, el reposapiés no es mera decoración, el reposacabezas se adapta a la altura del viajero y se abre y cierra para poder apoyar la cabeza… y está todo basado en materiales y componentes de proveedores que sabemos que están disponibles para fabricar. De hecho, está pensado para incorporar a un Airbus A320.
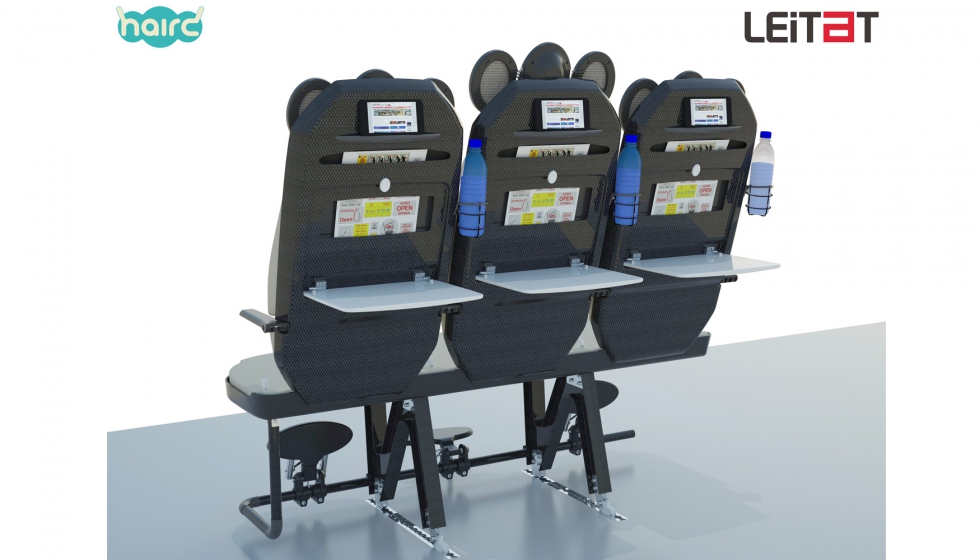
A pesar de estar en una fase intermedia, si hoy una empresa se planteara la fabricación tal y como está diseñado, el asiento es funcional: la mesa se abre, el reposapiés no es mera decoración, el reposacabezas se adapta a la altura del viajero y se abre y cierra para poder apoyar la cabeza, etc.
Comentaba que era la primera fase… ¿qué supone la siguiente?
En caso que consigamos la adjudicación de la segunda fase, ésta comporta la fabricación de los moldes, las pruebas de resistencia a 16 y 14G que comentaba antes, caracterizar los materiales más innovadores y aplicarlos de manera real; ahora los hemos caracterizado previendo las propiedades, pero sin ser reales. Es decir, se manufacturará varios asientos completos para las diversas pruebas y se fabricarán los moldes para que en el instituto Fraunhofer fabrique en sus instalaciones con estos materiales. Para la caracterización de los materiales hemos alcanzado un acuerdo con la Universidad de Girona y para la fabricación de los moldes, interviene una empresa austríaca.
¿Cómo valoran de participar en un proyecto CleanSky?
La posibilidad de compartir conocimientos. En realidad, un fabricante de aviones puede innovar en un asiento nuevo; y, de hecho, las normas que ponen se basan en su experiencia, los plazos de entrega son realistas. Pero los programas CleanSky permiten distribuir proyectos que podrían realizarse internamente en grandes empresas y, para éstas, supone que Europa financie el 50% del coste. Además, también supone aire fresco en el diseño, captar nuevas ideas.
Y para Leitat, ganamos experiencia y conocimiento. Ahora podemos decir que tenemos la capacidad de producir asientos de aviones. Con resultados que lo demuestran.
This project has received funding from the Clean Sky 2 Joint Undertaking under the European Union’s Horizon 2020 research and innovation programme under grant agreement No 738076. This publication reflects only the author’s views and the European Union is not liable for any use that may be made of the information contained therein.
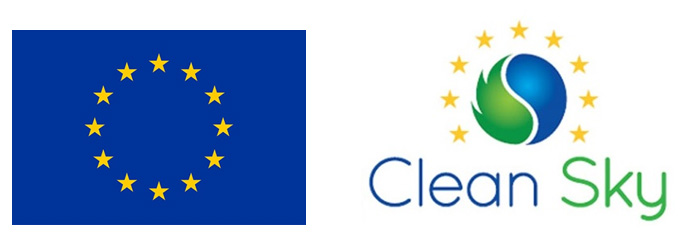