Conceptos que hacen mas fácil la vida en la planta de inyección
Pérdidas de Presión de Inyección en el sistema de llenado del molde
Durante el llenado del molde, el plástico en contacto con el molde empieza a enfriarse y se empieza a generar una piel fría debido a la refrigeración del molde. Esta piel va aumentando su espesor debido a este enfriamiento. Por otro lado, las capas límite del flujo en contacto con esta piel, en su avance durante el llenado, generan esfuerzos de cizalla que a su vez generan calor. Este pseudo equilibrio es el que permite el llenado, permite recorrer distancias considerables en función del espesor lo cual permite llenar cavidades complejas. No obstante, las necesidades de presión para hacer avanzar el frente de flujo a través de los canales de distribución, bebedero, entradas y cavidades cada vez son mayores generándose una inevitable perdida de presión.
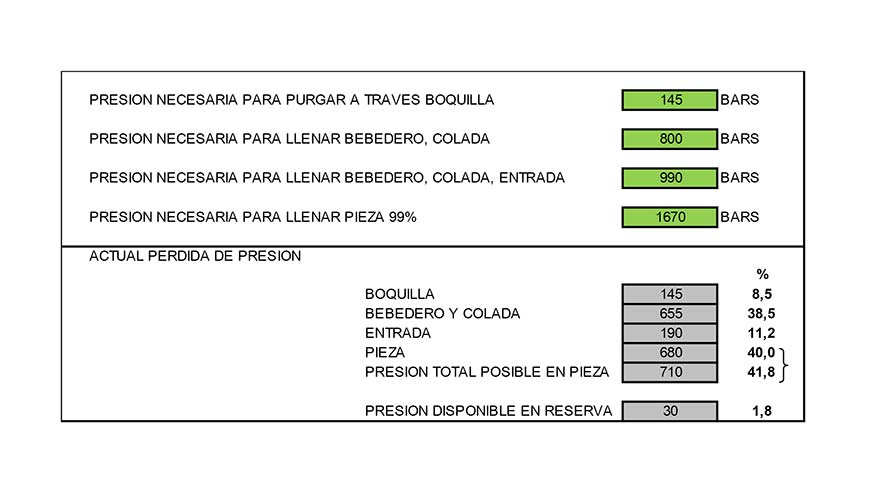
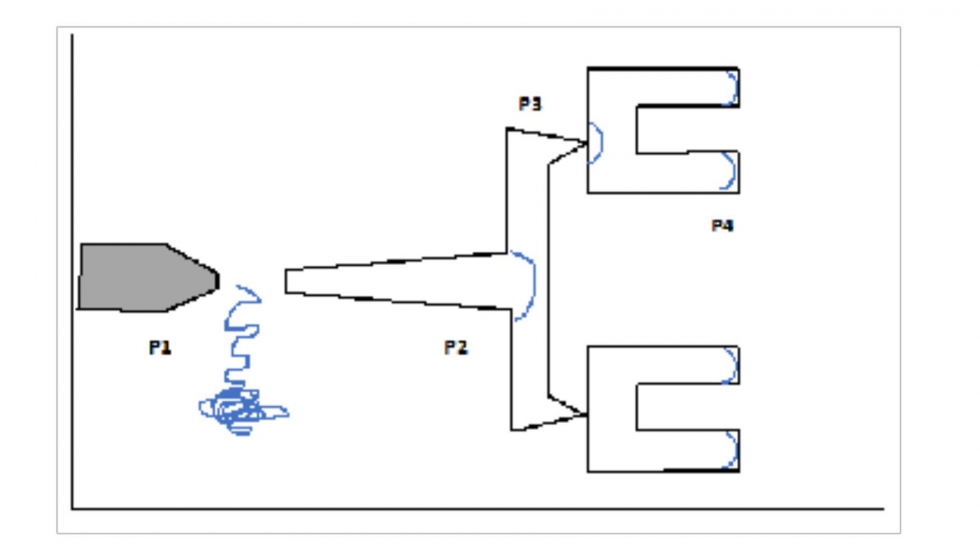
El proceso de inyección, desde el punto de vista de la presión de inyección es un proceso deficitario. Si miramos la presión que genera la bomba hidráulica en el caso de máquinas hidráulicas, la presión que se ejerce en el pistón de inyección y por ejemplo, la presión que recibe el bebedero, el canal de distribución, etc. hasta llegar a la cavidad, todo son pérdidas o caídas de presión generadas por las restricciones de paso del material y por su enfriamiento progresivo.
La máquina de inyección para ejecutar el llenado con la velocidad del husillo programada necesitará de cierta presión. Esta nunca debe sobrepasar la presión máxima de inyección programada o disponible. En caso de sobrepasarla estaríamos ante un proceso limitado por presión, situación a evitar siempre por ser una situación de proceso sin control.
Si conocemos las pérdidas de presión en cada paso del proceso podemos valorar si son necesarias acciones para reducir la pérdida en algún paso o pasos concretos, de modo que disminuiremos la necesidad total de presión necesaria para llenar las cavidades, asegurándonos de que no alcanzamos nunca el límite máximo de la inyectora y de que disponemos de suficiente presión para disponer de un correcto Delta P. (Ver artículo dedicado al Delta P).
Para conocer las pérdidas de presión generadas por todo el sistema de alimentación de material desde la punta del husillo hasta la cavidad es necesario realizar el análisis de las pérdidas de presión. Para ello es interesante aprovechar la evolución del ensayo de llenado progresivo para determinar los momentos de paso del flujo a través de bebedero, canal principal, canales secundarios, entradas, cavidad y también en el momento de eyectar al aire.
Para ello iremos realizando el llenado progresivo conmutando en posiciones estratégicas como son, justo llenar el bebedero, justo llenar canal de distribución, justo pasar por la entrada con un leve llenado de la cavidad, llenado de la cavidad hasta el punto de conmutación escogido.
En el caso de canales calientes, el punto estratégico es justo atravesar el bloque caliente y entrar en cavidad un pequeña cantidad de material. En cada punto de conmutación o de llenado tomaremos el valor de presión de inyección necesaria real. Esto nos permitirá realizar el estudio de pérdidas de presión a lo largo del recorrido del material.
Con estos datos convenientemente tabulados se obtienen los porcentajes de pérdida de cada paso del sistema de distribución del material desde la punta del husillo hasta la cavidad. Este análisis nos permitirá tomar decisiones y priorizar las mismas de cara a reducir las pérdidas de presión en el sistema si fuera necesario.
Necesitamos conocer cuánta presión es necesaria para alcanzar determinadas posiciones del recorrido del llenado o recorrido del flujo. Estas son:
- Presión necesaria para inyectar a través de la boquilla de la unidad de inyección
- Presión necesaria para inyectar el bebedero
- Presión necesaria para recorrer el canal de distribución o colada hasta la entrada (sin pasar por la entrada). Aquí podemos tener canal principal, secundario, terciario, etc.
- Presión necesaria para pasar a través de la entrada.
En el caso de canales calientes:
- Presión necesaria para pasar a través del canal caliente
- Presión necesaria para llenar la cavidad.
Método de ensayo de las Pérdidas de Presión
Es por ello que dentro del Scientific Injection Molding está incluido el ensayo de Análisis de las Pérdidas de Presión a lo largo del recorrido del flujo.
Con este sencillo ensayo a pie de máquina, una vez establecida la velocidad de inyección que mantendrá el proceso más estable y robusto definida en el ensayo de la curva de viscosidad (ver artículo de la Curva de Viscosidad Relativa), procederemos a conocer las presiones en cada etapa que nos interese controlar.
Así pues podemos ver todas las etapas (incluyendo canales calientes) y procederemos a analizar dónde están las principales pérdidas y valorar si los valores obtenidos son aceptables o requieren de algún tipo de acción de mejora sobre el molde.
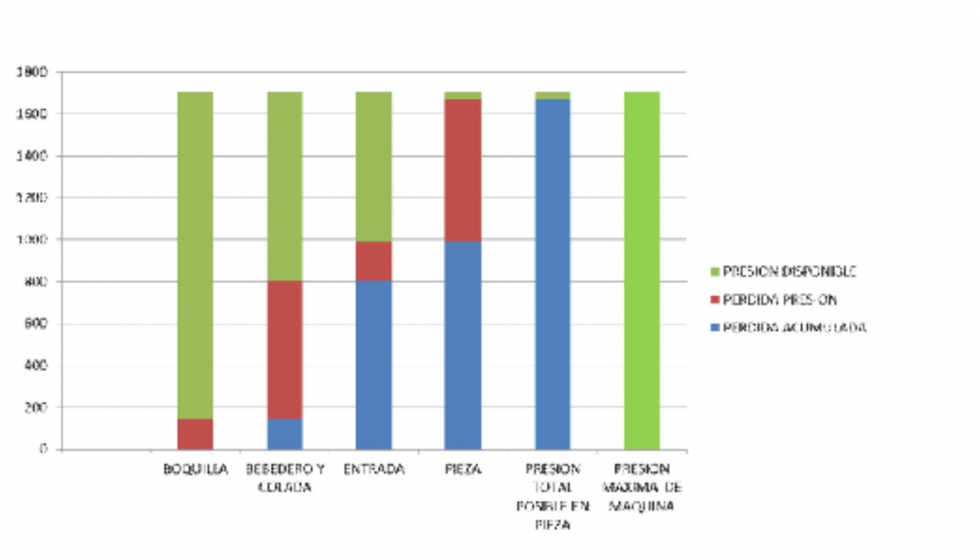
Gráfica obtenida en el ensayo de Pérdidas de Presión, donde podemos ver las distintas presiones en cada etapa controlada. De esta manera podemos determinar en qué etapa realizar acciones de mejora que ayuden a reducir la presión de inyección necesaria. Esto es imprescindible cuando la presión necesaria para llenar la cavidad, o lo que es lo mismo la presión en la última etapa del recorrido del flujo, se sitúa en valores cercanos a la Presión de Inyección Límite de la inyectora.
En resumen
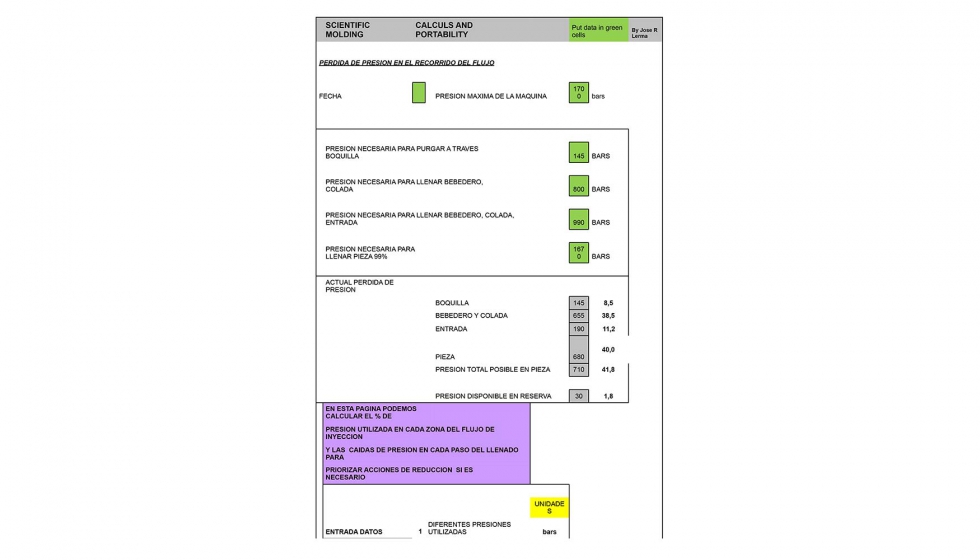
Hoja de cálculo prevista para la entrada de datos del Estudio de Pérdidas de Presión a lo largo del recorrido del flujo para su posterior análisis.
Podremos ver y analizar cuáles son los mayores consumidores de presión y si alguno de ellos es excesivo podemos modificar espesores o diseño para reducirlo.