Reparación de moldes mediante soldadura de aporte por láser
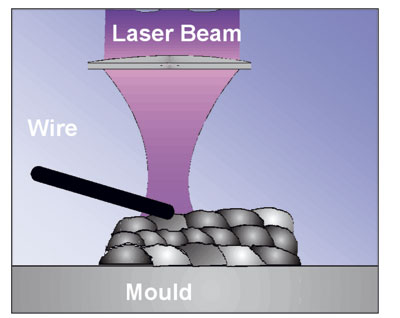
Hasta ahora, la soldadura por deposición ha sido realizada tradicionalmente y de forma mayoritaria con las técnicas: TIG ó micro-plasma. Otro método, la ligadura (soldeo por difusión) con resistencia utilizando polvo, es adecuado para reparaciones de moldes en aplicaciones donde se requiera una cohesión baja. Relativamente nuevo en el mercado es el proceso DMD (deposición directa de metal), que usa láseres de alta potencia (2 a 4 kW.) generados por YAG ó CO2. Ver la tabla adjunta, comparando algunos de estos procedimientos.
Las ventajas de la soldadura por deposición con láser en cuanto al material, sobre los métodos convencionales de arco eléctrico y microplasma, provienen de una mayor velocidad de calentamiento y enfriamiento, y volúmenes menores del baño de fusión. La zona afectada térmicamente en la pieza es mucho menor, y los riesgos de distorsiones, debilitamiento y formación de grietas se reducen considerablemente. Además, se pueden alcanzar mejores propiedades en las capas del cordón por medio de estructuras de grano fino ó empleando varilla de aportación de distintas aleaciones.
Desde el punto de vista de la producción, se pueden obtener estructuras notablemente más finas con técnicas asistidas por láser, ya que puede trabajarse con varillas de hasta 100 micras de diámetro. El haz láser puede ser focalizado muy bien, permitiendo a la pieza y al alambre recibir aporte térmico en una zona muy precisa y localizada.
Así, la energía incidente y consiguiente calentamiento de la pieza se pueden mantener muy bajos. Esto nos da una mínima distorsión y una zona afectada térmicamente muy reducida. Lo cual, junto con una operación muy precisa asistida por microscopio, supone que hay mucho menos trabajo de acabado (erosión, amolado, pulido) que con otros tipos de soldadura. Igualmente, podemos alcanzar altos grados de dureza dependiendo del material base: hasta 60 grados Rockwell HRC.
Concepto de la máquina
Una ventaja especial es la opción de carga. Sus 2 grandes puertas correderas proporcionan una apertura de 800 mm., y el raíl del láser puede ser retraído. Como resultado, podemos introducir piezas de grandes dimensiones con pesos de hasta 350 Kg. y volúmenes de hasta 125 ltr, desde el frontal con ayuda de una carretilla ó polipasto. Se pueden manejar una amplia gama de moldes e insertos. Las puertas correderas y los paneles de cubrimiento laterales se pueden extraer también para acomodar objetos incluso mayores. Cuando se utiliza así, la máquina es conforme a la protección láser clase IV; en tal caso, por supuesto deben observarse las normas de seguridad pertinentes.
El guiado de la pieza de trabajo tiene lugar en una mesa X-Y-Z. El objeto se posiciona con exactitud ayudándose de un microscopio estéreo y un ‘joystick’ (palanca articulada). Este mando da un control proporcional; el grado por el que se desplaza determina la velocidad de los ejes. Cuando movemos el joystick, el eje Z da una pasada. La posición correcta del área de soldadura se alcanza con máxima definición de imagen en el microscopio. Las series de parámetros de láser se ponen a la vista en el microscopio. Podemos recuperar hasta 50 registros de parámetros pre-programados, usando el joystick. Así, el operario puede comprobar y alternar los parámetros en cualquier momento sin tener que quitar la vista del microscopio o sacar las manos del cabinado. El operario mueve el joystick a través de unos conductos ergonómicos para los brazos.
Todas las funciones del dispositivo láser, tales como el pulso, control del obturador, control de la unidad de potencia, temperatura, focalización, circuito de seguridad, grabación de datos y rutinas de pruebas, se efectúan por un potente micro-procesador. Se incluye un teclado de membrana para introducir todos los datos. Los valores de voltajes para la batería de condensadores, frecuencia de pulso, ancho de pulso, energía del pulso, energía del pulso por cm2 (energía superficial relacionada con la soldadura), forma del pulso, mensajes de texto... y otros datos, pueden leerse en una pantalla.
La fuente del haz láser empleada, es un generador de Nd:YAG con una potencia media máxima de 100 W. El tiempo de pulso para soldadura de reposición está entre 2 y 10 milisegundos, dependiendo del material. Con potencias de pulso de hasta 50 Jul, se pueden conseguir densidades máximas de pulso de varias decenas de MW/cm2. Esto es más que suficiente para trabajos rápidos, incluso con varillas gruesas. La máquina incorpora un sistema de refrigeración aire/agua integral, y un filtro de aire para evacuar los humos de soldadura.
Destacamos las siguientes características en cuanto a flexibilidad de la tecnología de soldadura manual por reposición, y su alto grado de fiabilidad de proceso. Un sistema óptico patentado, que puede ser direccionado girando en ambos ejes, permite la soldadura en caras verticales y hendiduras (Fig.2). La calidad de soldadura, optimizada y dentro de mínimos tolerancias de error, se garantiza por un resonador láser especial. Su longitud focal permite un margen amplio de tolerancia a las fluctuaciones verticales en la superficie del componente, en relación con el punto de soldadura. Se asegura un volumen constante de aplicación de varilla de aportación por un modo de software específico. Durante el procesado manual de la pieza a trabajar, este modo permite la relación entre solapes de los pulsos de soldadura, manteniéndola constante por el acoplamiento de la frecuencia de pulsos a la velocidad de alimentación.
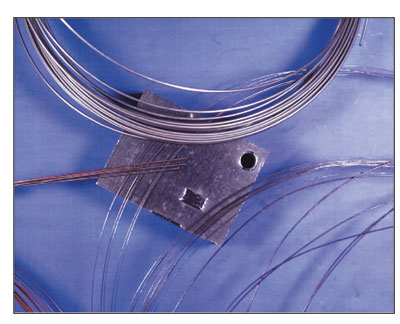
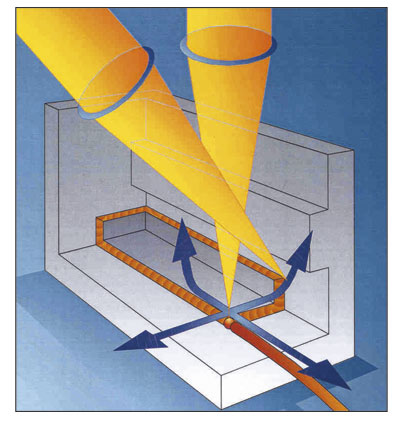
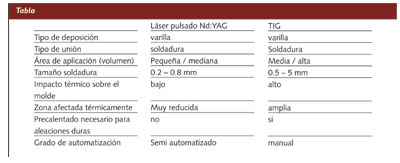
Ejemplo de aplicación
Como ejemplo, la compañía Schweiger de Baviera (Alemania) ha estado produciendo y reparando moldes de inyección para las industrias de automoción y eléctricas, durante más de 25 años. Para ello tenían un impresionante parque de máquinas de erosión, fresadoras y mucho más. Desde los comienzos del 2000, cuentan con una máquina de soldadura de deposición por láser en operación.
El cliente ha utilizado la máquina para soldar y reparar incluso moldes de gran tamaño. El equipo les permite realizar trabajos con rapidez y precisión en sus propias instalaciones, informando que el mecanizado posterior es muy bajo debido a la precisión de la soldadura.
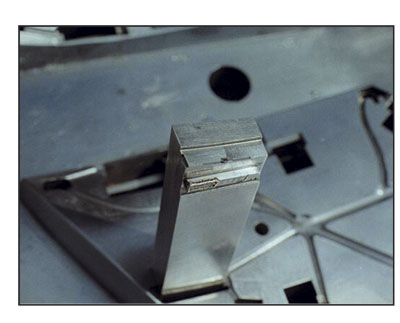
Resumen
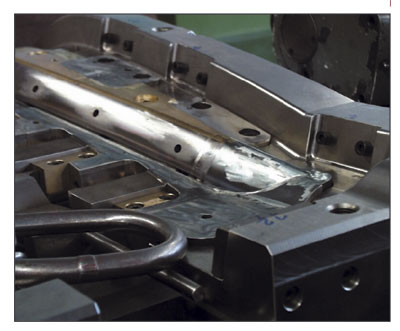