Entrevista a Aníbal Reñones, investigador de Cartif
Con un presupuesto de 9,8 millones de euros, han comenzado los trabajos del proyecto europeo Reemain sobre la fabricación del futuro, una iniciativa liderada por Cartif que agrupa a 16 socios de 6 países. Durante los próximos cuatro años se trabajará en tres demostradores situados en España, Turquía e Italia; tres empresas de muy diferentes ámbitos pero con un objetivo común: alcanzar la eficiencia energética. Aníbal Reñones, jefe de proyecto en Cartif, detalla cuáles son los objetivos de la iniciativa y cuáles las oportunidades que ofrecerán los resultados. La ‘Factoría del Futuro’ es aquella que no sólo ofrecerá procesos productivos más eficientes sino que también persigue alcanzar la eficiencia energética, la fábrica inteligente, en definitiva, la excelencia.
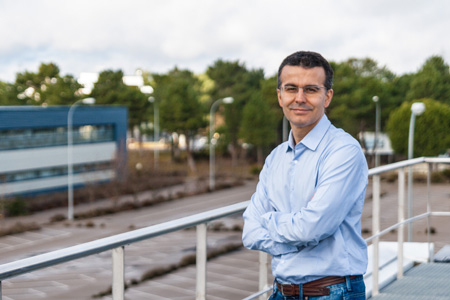
¿En qué consiste exactamente el proyecto?
Se trata de un proyecto de I+D de ámbito europeo que se engloba dentro de la denominada ‘Factoría del futuro’ impulsada por la Comisión Europea y por la asociación de fabricantes europeos, Efra. Está centrado en hacer las fábricas más eficientes desde el punto de vista de utilizar los recursos energéticos y materiales de una forma más adecuada.
¿Cuál es su principal objetivo?
Diseñar la factoría del futuro en base a criterios de eficiencia energética y gestión sostenible de los residuos generados durante los procesos de fabricación. Para conseguirlo, se utilizarán modelos de simulación predictiva para la producción que se usarán para establecer nuevas y eficaces herramientas de gestión energética. Estas herramientas proporcionarán información sobre los flujos de energía, la huella de carbono y su relación con la producción y la programación y el abastecimiento de la planta.
¿Qué empresas hay implicadas en el proyecto?
En realidad, los resultados tecnológicos obtenidos se probarán y validarán en una planta de demostración del centro tecnológico alemán Fraunhofer IWU, para posteriormente implementarlas en tres fábricas de distintos sectores. En principio, los resultados pueden ser extrapolables a prácticamente cualquier factoría, pero nos hemos centrado en tres tipologías de fábrica más o menos diferentes pero complementarias: Gullón, fabricante de galletas español; Bossa, empresa textil turca; y SCM, una fundición situada en Italia.
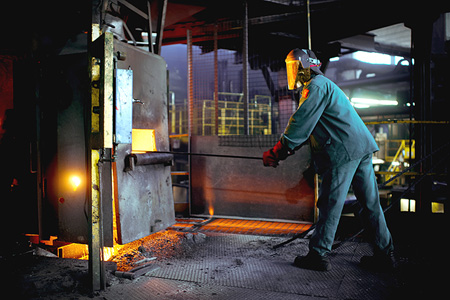
¿Qué conseguirán estas empresas?
Se pretende lograr una producción cercana a los cero residuos (zero carbon manufacturing) dentro de los estándares de eficiencia energética 2.0. Todo ello integrando la generación, conversión, distribución, control, uso, almacenamiento y reutilización de los recursos energéticos necesarios para la fabricación.
¿Estas soluciones también están enfocadas a empresas pequeñas?
Dado que se está tratando de hacer un uso más eficiente de la energía y recursos, cualquier empresa que tenga una elevada carga de uso energético y que pretenda ser energéticamente eficiente, puede adoptarlas. Obviamente, a la hora de plantearse una inversión, una pyme no tiene las mismas posibilidades financieras que las grandes empresas, por ejemplo, que pueden planear a más largo plazo. En realidad, depende mucho de la tipología de pyme, si ésta tiene una visión a más largo plazo, pues se lo puede plantear, y en vez de esperar amortizar a un año, quizá lo haga en dos o tres.
¿Hay una demanda real por parte de las empresas de nuestro país por obtener herramientas que mejoren la eficiencia energética?
Sí, la optimización energética está siempre entre los objetivos de cualquier gestor de una fábrica. Dependiendo del tipo de fábrica, hay que pensar que en muchas ocasiones está asignada las principales facturas que tienen que pagar. Lo que les cuesta la energía eléctrica, el gas consumido y todos los recursos, al final se ve repercutido en el precio final del producto. Se puede conseguir ofrecer productos a un precio más competitivo siendo energéticamente eficientes. Además, los precios de la energía suben cada vez más y la competencia en el mercado es cada vez más alta.
Lideran el proyecto, pero trabajan en común con varias empresas. ¿En qué aspectos se centran ustedes desde Cartif?
Nosotros somos los coordinadores del proyecto pero también tenemos nuestras actividades de i+D y demostrativas. Fundamentalmente, nos centramos en el análisis de la eficiencia energética de la factoría de Gullón, y también tenemos que dar apoyo de forma transversal en otros ámbitos, por ejemplo, el análisis de las otras fábricas.
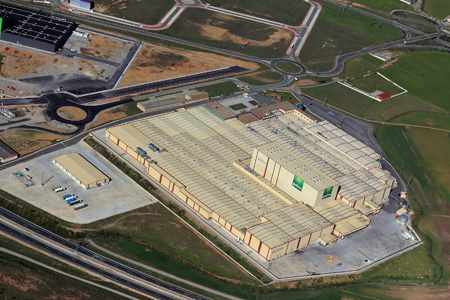
Un vez concluido el proyecto, ¿cómo se materializarán los resultados? ¿Será un software, por ejemplo?
Hay diferentes tipos de productos que se están barajando desde el primer momento. Tenemos en mente diferentes soluciones del tipo software para que las fábricas puedan analizar de una forma más global su factoría y puedan decidir mejor cuáles son los puntos de eficiencia. También trabajamos para generar soluciones específicas que serán proporcionadas por integrantes específicos del consorcio como, por ejemplo, el almacenamiento eléctrico mediante baterías o sistemas de concentración solar para poder dotar de energía térmica a los procesos productivos.
¿En qué aspectos puede mejorar la fábrica su eficiencia energética? ¿En qué puntos se centran?
Fundamentalmente, queremos analizar cuáles son aquellas demandas energéticas que tiene la factoría, ver cómo se puede optimizar esa energía, por ejemplo, viendo dónde se desprenden residuos energéticos. Una de las cosas que se investigan son los flujos energéticos que se están, por así decirlo, desaprovechando y cómo se pueden llegar a reintegrar otra vez dentro del proceso para ser utilizados en otro punto.
También es importante conocer cuál es la forma más eficiente de integrar energías renovables dentro de la propia factoría. No se trata sólo de instalar la placa fotovoltaica y vender energías de forma más económica sino de integrar energías, por ejemplo, de concentración solar térmica. Se basa en la recuperación de energía, en la integración de energías renovables y, en algún caso, dado que estamos analizando los procesos productivos, si es susceptible de realizar algún cambio en la forma del proceso productivo que permita a la empresa fabricar lo mismo pero consumiendo menos energía.
Otro de los aspectos es el de los residuos, ¿realmente es posible una producción de cero residuos?
Depende mucho del tipo de factoría. Yo creo que, en general, las empresas tienen hoy en día una mayor preocupación por lo que pueden hacer dentro del ámbito de residuos. Nosotros básicamente estamos entrando en este proyecto, más que en los residuos materiales, en los residuos energéticos. No nos estamos centrando en si una industria es más o menos contaminante, pero la idea sobre todo es llegar a que todo lo que se pueda aprovechar dentro de la factoría para uso y beneficio propio de la fábrica se pueda utilizar. Puede haber algún tipo de residuo que normalmente no se puede aprovechar dentro de la propia factoría y que se suele poner en manos de algún tipo de gestor de residuos o de otra empresa. En todo caso, eso recae fuera del espacio de este proyecto, que está centrado en el ámbito de la factoría. Pero llegar a cero es complicado, implica la participación de más agentes de la cadena de valor, no sólo de la propia factoría.
Para implementar todas las herramientas que proponen será necesaria una inversión que, con el tiempo, se recuperará…
Claro, además hay que tener en cuenta que, dado que este proyecto es de tipo de demostrativo, se quiere fomentar estas pruebas piloto. Por ello, se ha obtenido financiación por parte de la Comisión Europea. Se tendrán en cuenta esos cálculos de rentabilidad para poder por un lado, seleccionar aquellas soluciones que sean rentables, pero que también tengan un grado de innovación lo más alto posible ya que es un proyecto de I+D.
Trabajarán con tres empresas muy diferentes entre sí...
En sí mismos, los productos que desarrollan son totalmente diferentes pero nosotros estamos tratando de encontrar aquellos procesos más comunes en las fases iniciales de análisis y llegar a soluciones que puedan ser fácilmente trasplantables.
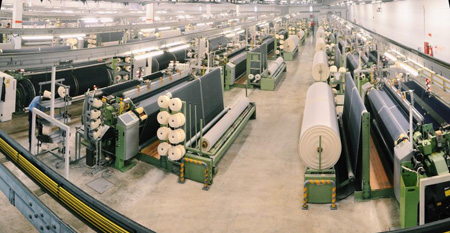
Grosso modo, ¿cuánto esperan que ahorre cada una de estas empresas una vez aplicadas las soluciones?
Es un proceso de evaluación que llevará varios años y aún no disponemos de cifras. Potencialmente, se pueden llegar a desarrollar muchísimos matices, pero luego al final lo que se puede llegar a demostrar dentro del proyecto como algo innovador no va ser todo lo que nosotros quisiéramos. Me explico: es muy típico el ahorro con iluminación de bajo consumo, pero eso es algo que no se hará porque no es un aspecto innovador a demostrar.
¿Y los aspectos innovadores que sí tratarán?
Ya tenemos temas identificados preliminarmente, como comentaba, el almacenamiento eléctrico de baterías o la concentración solar térmica para integrar en los procesos industriales. Son aspectos que precisamente y dado que hemos conseguido esta propuesta, se han apreciado en la valoración inicial como innovadores.
Háblenos de la iniciativa ‘Factorías del futuro’.
Es una iniciativa en la que colaboramos desde hace cuatro años, fecha en la que se inició. La línea de financiación de ‘Factoría del futuro’ es especialmente interesante. Comenzó en 2009 y la Unión Europea ha decidido ampliarla hasta 2020 con una importante financiación de proyectos porque entiende que la fabricación es uno de los pilares de la industria y para la creación de empleo.
¿Queda mucho por innovar todavía?
Sí, en el tema de factorías del futuro hay muchísimos campos, no sólo en la parte de eficiencia energética sino de optimización de procesos, de productos, factorías más inteligentes... El campo es elevado, de hecho hay una hoja de ruta para los próximos siete años donde se han definido aquellos retos más importantes a abordar en los proyectos existentes.