La respuesta a una mejora de la integridad superficial: el bruñido
Centrando atención en la industria aeronáutica, concretamente en la aviación comercial, actualmente uno de los negocios más globales, la empresa Airbus prevé grandes cambios para los próximos veinte años. La conectividad entre los aeropuertos, la cual se ha duplicado desde los años ochenta, seguirá creciendo gracias a las economías emergentes. En cuanto al modelo de negocio de las aerolíneas, éstas cada vez deberán ser más competitivas y diversificadas para sacarle beneficio al aumento del número de pasajeros y de conexiones internacionales. Están surgiendo ya aerolíneas de ‘ultrabajo coste’ y las de ‘punto a punto’ entrarán a competir pronto en las rutas largas, incluso en las trasatlánticas. Las aerolíneas de red también buscarán una mayor segmentación con un enfoque en la diferenciación de marca y en los ingresos auxiliares. Estas tendencias del mercado suponen tanto un reto como una enorme oportunidad para los fabricantes de aeronaves que se tendrán que esforzar por sacar el máximo partido a sus productos en términos de diseño, costes, fiabilidad y flexibilidad para satisfacer las nuevas necesidades de las compañías aéreas.
En cuanto al crecimiento del número de aviones, se prevé que para el año 2037 la flota actual se duplique. En concreto, la nueva flota contaría con alrededor de 37.400 aviones nuevos, por lo qué, sumando los aviones actuales en servicio, en 2037 se obtendría una flota de alrededor de 47.990 aviones. En cuanto al número de aviones a fabricar, un 30% serían aviones reemplazados de la flota actual y el 70% de sería el número de aviones que marcarían el número de aviones que suponen el crecimiento respecto al número de aviones que están hoy en día en servicio. Estos datos suponen un auténtico empujón para la industria aeronáutica puesto que, para alcanzar esta producción de aeronaves, sería necesaria la fabricación de aproximadamente 2.000 aviones por año. Por todo lo mencionado hasta ahora, los procesos de fabricación deberán evolucionar decididamente, con el objetivo de disminuir drásticamente los tiempos de producción en el sector [2].
Paralelamente, de cara a cumplir con los nuevos requisitos medioambientales, en la futura flota se busca disminuir las emisiones de CO2 al mismo tiempo que se aumenta la eficiencia de los motores, como es el caso del nuevo motor UltraFan de Rolls Royce, donde también se persigue un diámetro mayor del ventilador de la turbina para incrementar el empuje del conjunto turbopropulsor. No obstante, con esta nueva configuración la velocidad de la parte exterior de las palas será sensiblemente superior a la actual, generando nuevos problemas en cuanto a la resistencia y durabilidad de los álabes y demás componentes rotatorios haciendo que aumente la probabilidad de que surjan problemas de fatiga.
Por esta razón, para ciertas aplicaciones industriales como es el caso de los elementos y componentes de máquinas que trabajan recibiendo tensiones variables, será necesaria una mejora de las propiedades mecánicas para aumentar la vida útil de estos. Con el objetivo de dotar al componente de estas mejoras sin aumentar drásticamente los costes del proceso, en la mayoría de casos será suficiente con realizarle un tratamiento superficial. Estas mejoras con las que se dota a los materiales pueden ser obtenidas por medio de una gran variedad de técnicas. Sin embargo, si se requiere mejorar las propiedades físicas al tiempo que se cumple con las exigencias medioambientales, la técnica del bruñido parece ser la solución. Entre las posibilidades, el tradicional shot peening, laser peening, diferentes grados de granallado y el bruñido de baja plasticidad, de tipo hidrostático.
La tecnología del bruñido
El bruñido por deformación surgió con el objetivo de mejorar la rugosidad superficial de ejes rotativos y agujeros profundos. Sin embargo, otros procesos como el rectificado, el pulido y el lapeado consiguen mejores resultados en cuanto a rugosidad final. Por ello, con el avance de la tecnología, el bruñido acabó empleándose como tratamiento superficial, siendo de gran aplicación en ejes de ferrocarriles y en diferentes elementos de máquinas. De esta manera, se pudo observar que mediante esta técnica no sólo disminuía la rugosidad favorablemente, sino que, al mismo tiempo, la dureza de la capa superficial aumentaba y se generaban unas tensiones residuales de compresión, alargando así la vida a fatiga del componente. A partir de este hallazgo y con el paso del tiempo esta técnica ha ampliado su rango de aplicación, llegando hoy en día, entre otros, al campo de la aeronáutica, de la ingeniería de la energía y automoción, así como al de la medicina, dando paso a nuevas prótesis. Este tratamiento superficial es un proceso sencillo, de bajo coste y que consigue buenos resultados en cuanto a propiedades físicas y mecánicas. Este método, a pesar de llevar aproximadamente 30 años en el mundo de la industria como un proceso de acabado superficial, aún tiene como objetivo el ser implantado en la industria de la fabricación como un proceso habitual en el proceso de mecanizado. De este modo, se podrían remplazar procesos como el rectificado o incluso ciertos tratamientos térmicos, evitando así la gran contaminación que éstos producen [3].
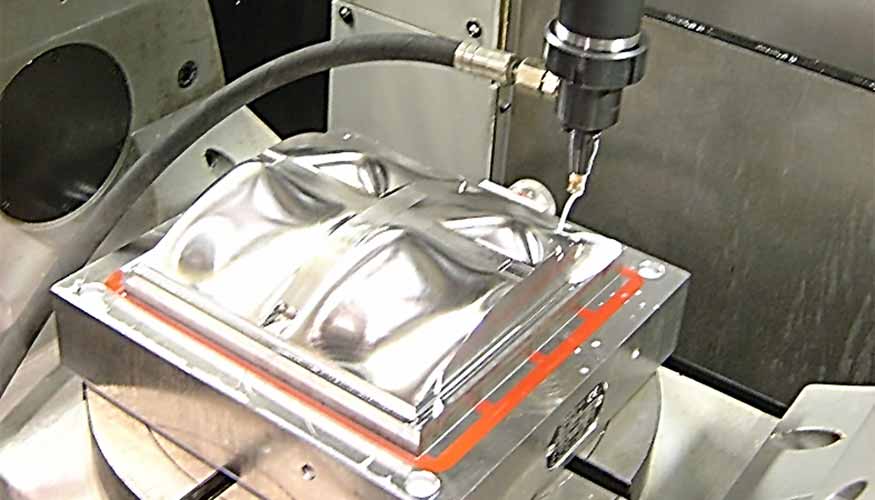
Ilustración 1. Bruñido de un molde realizado en 2017. Universidad del País Vasco.
El bruñido por deformación consiste en un proceso de deformación en frío y se realiza sobre la superficie previamente mecanizada de las piezas de trabajo, con el propósito principal de generar superficies lisas de alta calidad o superficies con una determinada estructura. Este proceso de deformación se basa en lo siguiente: cuando se crea un punto de contacto entre la herramienta de bruñido y la superficie de la pieza de trabajo, se forma una presión por tensión, ocasionando una deformación plástica que se da cuando se sobrepasa el límite de elástico en los materiales dúctiles. Los picos de rugosidad se presionan en sentido vertical contra la superficie, de manera que el flujo de material sobrante de los picos llena el valle de rugosidad desde abajo. De esta forma se consigue una capa superficial con mejores características tanto físicas como mecánicas respecto al material principal. El aplastamiento genera numerosos efectos beneficiosos en el componente tratado, como por ejemplo la mejora de la rugosidad y de la dureza superficial y la incorporación de tensiones residuales de compresión. De esta manera la vida a fatiga y la resistencia a la corrosión y al desgaste aumentan notablemente.
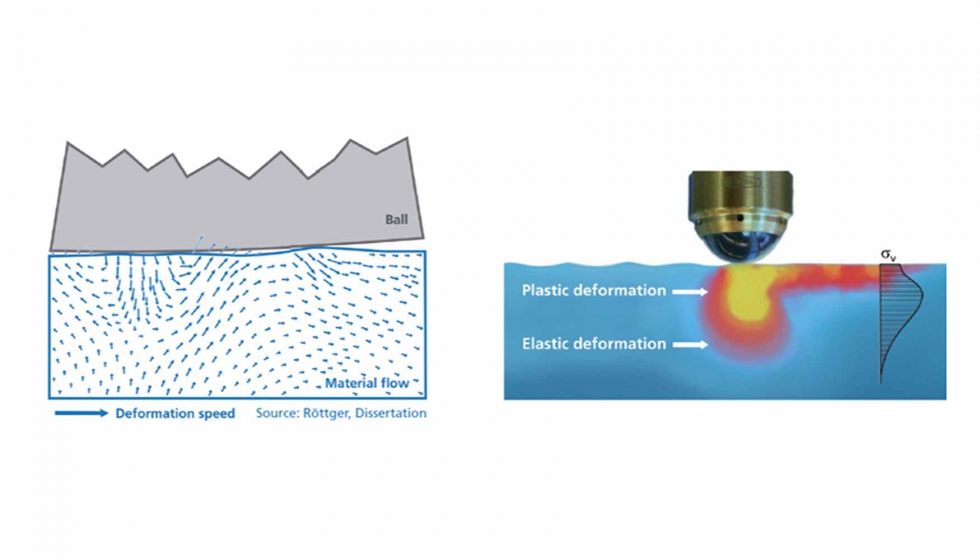
Este proceso se realiza mediante el deslizamiento y/o la rodadura de un elemento deformante, existiendo hoy en día una amplia variedad de herramientas para este uso. Y todo este abanico de herramientas y equipos de bruñido que las empresas pueden ofrecer se suele dividir en dos grandes grupos en función del mecanismo que emplean: mecánicas o hidrostáticas. En cuanto a la forma de la superficie, se debe seleccionar qué geometría de herramienta es más adecuada para la pieza o componente a tratar. Entre las diferentes opciones, las más utilizadas son los rodillos, los multi-rodillos y las bolas.
La herramienta de bruñido se trata de una bola sujeta mediante un cabezal garantizando el giro de la bola en cualquier dirección mediante un fluido, que en este caso es taladrina. La presión ejercida por esta puede ser generada mediante diferentes tipos de mecanismos: de forma mecánica con un muelle, de forma hidrostática alcanzando mayores presiones de trabajo o incluso de forma neumática. El bruñido hidrostático con bola se diferencia del resto de mecanismos existentes por permitir procesar una gama más amplia de geometrías y por ejercer una mayor presión sobre la superficie, provocando un efecto positivo en cuanto a las propiedades mecánicas de la pieza tratada. La pieza central de la herramienta de bruñido es un elemento de laminado que consta de un complemento esférico y un sistema de arrastre. El complemente esférico contiene una esfera de metal duro, acero rápido o cerámica, que hace contacto con la superficie de la pieza de trabajo.
No obstante, al igual que todo proceso mecánico, el bruñido también presenta ciertas limitaciones. La principal limitación es la geométrica, ya que el ángulo entre la normal a la superficie bruñida y el eje de la herramienta debe estar comprendido entre ±28° para la mayoría de las herramientas de bola, ya que este puede variar dependiendo de su fabricante. Sin embargo, a pesar de estas limitaciones, es un proceso que cuenta con grandes beneficios técnicos, económicos y medioambientales.
En cuanto a los beneficios técnicos, como se ha mencionado anteriormente, es un proceso que trae mejoras tanto físicas, disminuyendo la rugosidad generando superficies de alta calidad, tanto mecánicas, que como ya se ha mencionado, aumentan la vida a fatiga y la resistencia al desgaste y a la corrosión, todo esto sin generar elevadas temperaturas durante su aplicación. Además, gracias a la naturaleza del proceso, la herramienta no tiende a sufrir desgastes excesivos. Por otro lado, el bruñido genera un potencial ahorro de costes al sustituir tecnologías caras como, entre otras, el rectificado o el esmerilado. La reducción de coste se basa principalmente en el tiempo de mecanizado, que es esencialmente menor que el de las tecnologías alternativas. Asimismo, el bruñido tiene la ventaja de poder aplicarse en la misma máquina donde se ha realizado el mecanizado previo, evitando de esta manera el traslado de pieza de una máquina a otra y el error que el traslado de pieza puede suponer. Por último, este proceso es ecológicamente mucho más limpio que el resto de técnicas de acabado, ya que no genera desperdicios al no existir arranque de viruta.
El bruñido, la solución para la mejora de la integridad superficial de los materiales
Desde hace 15 años existe una actividad muy viva respecto al bruñido en el grupo de la Universidad del País Vasco (UPV/EHU), habiéndose realizado y publicado trabajos en las principales revistas relacionadas con la fabricación mecánica, así [5,6]:
1- Bruñido de moldes y matrices, tras el proceso de fresado.
2- Bruñido de ejes de acero.
3- Bruñido en 5 ejes de cabezas de prótesis y otros elementos de forma compleja.
4- Bruñido de uniones aleadas por “friction stir welding”, de familia de aluminio Al-Li.
5- Bruñido de Inconel 718, tras operaciones de fresado.
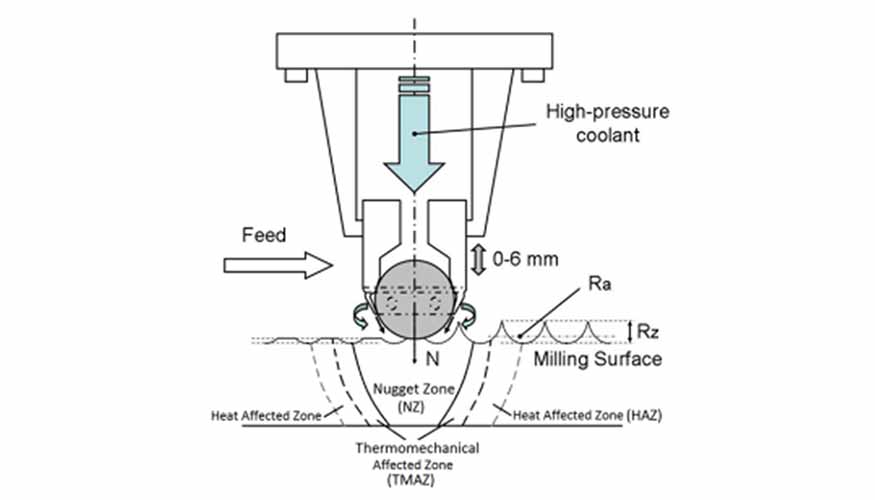
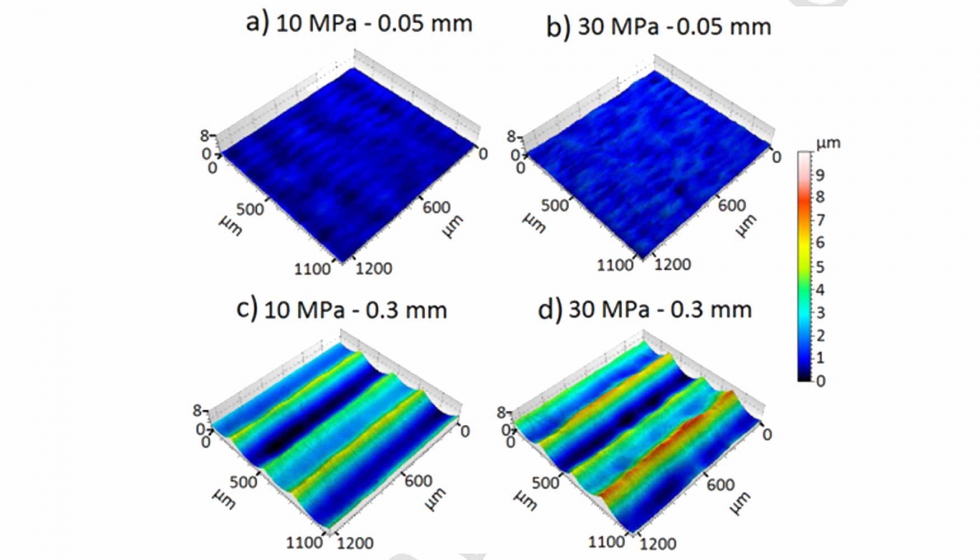
Sin embargo, en el último trabajo titulado ‘Procesos de superacabado: análisis multimaterial de la aplicación de bruñido por bola en componentes metálicos’ aquí presentado se ha ido un paso más allá y se ha analizado el comportamiento de las diferentes clases tras la aplicación del proceso de bruñido con bola.
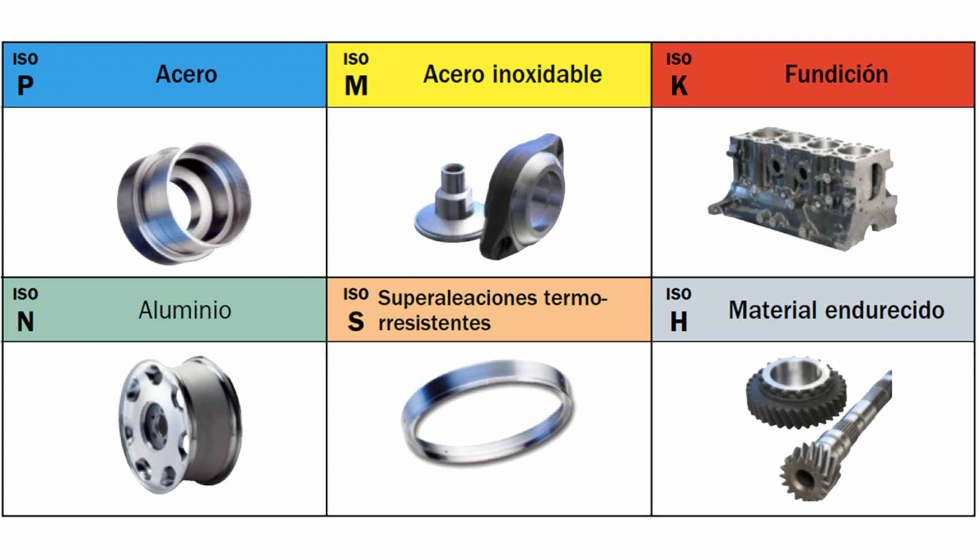
Para la realización del trabajo se ha seleccionado un material representativo de cada grupo según la norma ISO 513:2004. Esta norma tiene como fin regular la ‘Clasificación y aplicación de materiales de corte duro para la eliminación de metales con filos de corte definidos – designación de los principales grupos y grupos de aplicación’. De esta manera, la norma ISO divide los grupos de materiales estándar en 6 tipos. Cada tipo cuenta con propiedades únicas de acuerdo a la maquinabilidad y las preparaciones que plantean distintas exigencias sobre la herramienta, designando así cada grupo con una letra, como se puede ver en la imagen adjunta.
En concreto, se ha buscado seleccionar los metales de cada grupo más empleados en la industria:
• ISO P, Acero - AISI 1045
• ISO M, Acero Inoxidable - AISI 304L
• ISO K, Fundición - AISI 100-70-03
• ISO N, Aluminio - AL 5083
• ISO S, Superaleaciones termorresistentes - INCONEL®718
• ISO H, Material endurecido - AISI P20
Mediante la elección de estos materiales, se desea obtener unos valores o unas tendencias significativas que sirvan como base para extrapolar el efecto del bruñido hidrostático con bola en el resto de materiales, siempre y cuando estén definidas las condiciones de trabajo del material.
Para realizar el bruñido en los metales seleccionados, se practicó un fresado en todos ellos. Posteriormente, se bruñeron dos zonas a diferentes presiones, una zona a 100 bar y la otra a 300 bar. En cuanto a los parámetros de bruñido se emplearon los siguientes: avance radial del bruñidor de 0,1 mm y una velocidad de avance de 2000 mm/min. Tras la operación de bruñido se realizaron medidas de dureza superficial, rugosidad y tensiones residuales.
Una vez terminados todos los ensayos, se obtuvieron los resultados y las gráficas que se muestran a continuación. Para empezar con el análisis de datos, la aplicación del proceso de bruñido en los diferentes materiales ofrece en todos ellos un aumento en la dureza superficial, como se puede observar en la gráfica. Además, reparando en el efecto de las presiones de aplicación en el material, se observa que un incremento de presión en la herramienta de bruñido supone siempre un aumento en la dureza superficial. Esto se debe a la física del bruñido, ya que el proceso presiona los picos del material contra la superficie rellenando con el flujo sobrante de los picos los valles, creando una capa más compacta en la superficie, la cual supone un refuerzo para el componente y evita que las condiciones de trabajo agresivas acorten la vida útil de la pieza de trabajo.
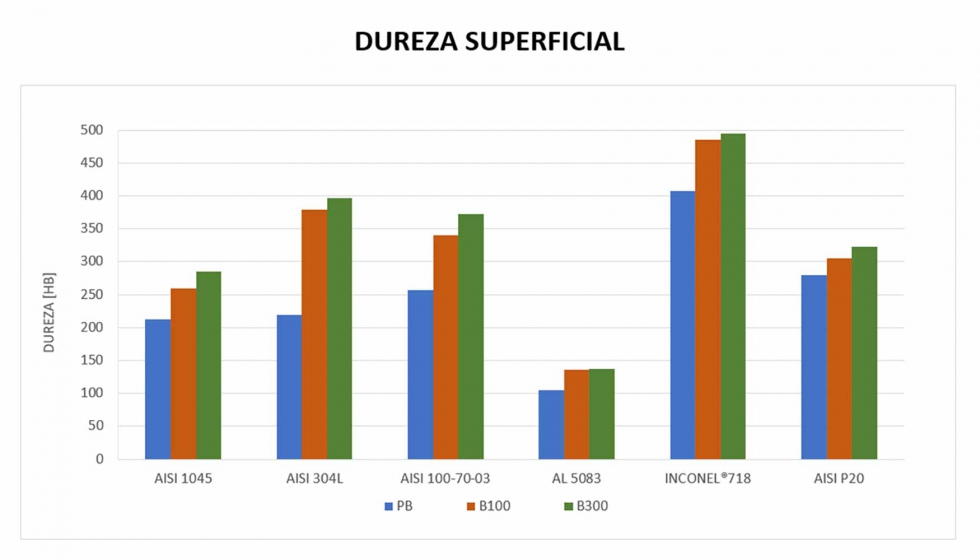
Reparando más profundamente en los datos de dureza previos y posteriores al proceso de bruñido obtenidos, se observa que para la mayor parte de los materiales la presión más favorable a aplicar es la de 300 bar. Sin embargo, en el caso del AL 5083 e Inconel 718 un aumento de presión de 200 bar no supone una gran mejora, generando un aumento la dureza superficial en los dos casos de entre un 1 y 2%. Por esta razón, respecto a la aplicación del bruñido en estos dos materiales, en cuanto a dureza se refiere, un bruñido a 100 bar sería más que suficiente para obtener resultados notables. Por otro lado, no puede quedar sin analizar el impacto del proceso de deformación en el acero inoxidable AISI 304L, ya que las mejoras obtenidas saltan a la vista en la gráfica. Para ser exactos, una aplicación a 100 bar de presión supone un incremento de la dureza superficial de un 73% respecto al material base, el cual logra un aumento del 81% con la aplicación del proceso a 300 bar.
Por otro lado, cuando el objetivo de la aplicación del bruñido hidrostático con bola en el componente no se limita en aumentar la dureza, sino que también debe cumplir ciertos requisitos de acabado, resulta necesario una disminución de la rugosidad respecto al mecanizado previo. De esta manera, en los siguientes párrafos se analizará el impacto del bruñido y del aumento de presión en el acabado final de los materiales seleccionados, y para ello se reparará en los parámetros de máxima rugosidad Rz y rugosidad media de la superficie Ra, ya que son los parámetros más significativos en un análisis de rugosidad.
Si se repara en la imagen adjunta de rugosidad, se puede examinar cómo la aplicación del bruñido disminuye notablemente la rugosidad del mecanizado previo, ya que tanto Ra como Rz presentan disminuciones de entre un 60-97% respecto al material base. Por otro lado, si se observan los resultados de rugosidad tras un incremento de presión en la herramienta de bruñido, se concluye que este incremento no supone una mejoría en cuanto al acabado final de la pieza en todos los materiales seleccionados, por ello, en muchos de ellos un valor de presión de 100 bar resulta más que suficiente. En concreto, el INCONEL®718 y el AISI 304L, siendo los dos materiales austeníticos, han sido los únicos metales que han mejorado su acabado con una presión de 300 bar. Además, al igual que en los resultados obtenidos de la dureza superficial, los mejores resultados de rugosidad los ha obtenido la pieza de acero inoxidable, la cual ha disminuido, con una aplicación de 300 bar, su rugosidad media en un 97% respecto a la rugosidad del material sin la aplicación de proceso alguno.
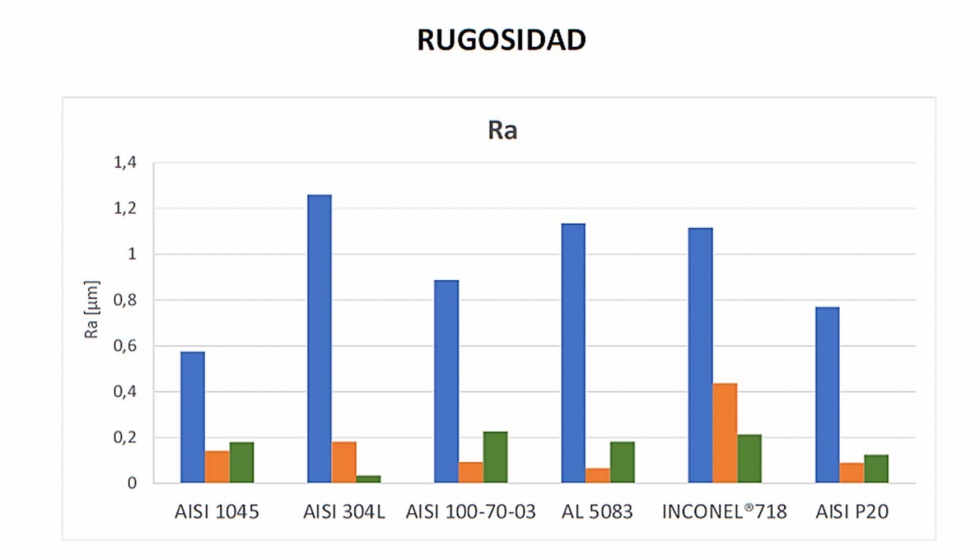
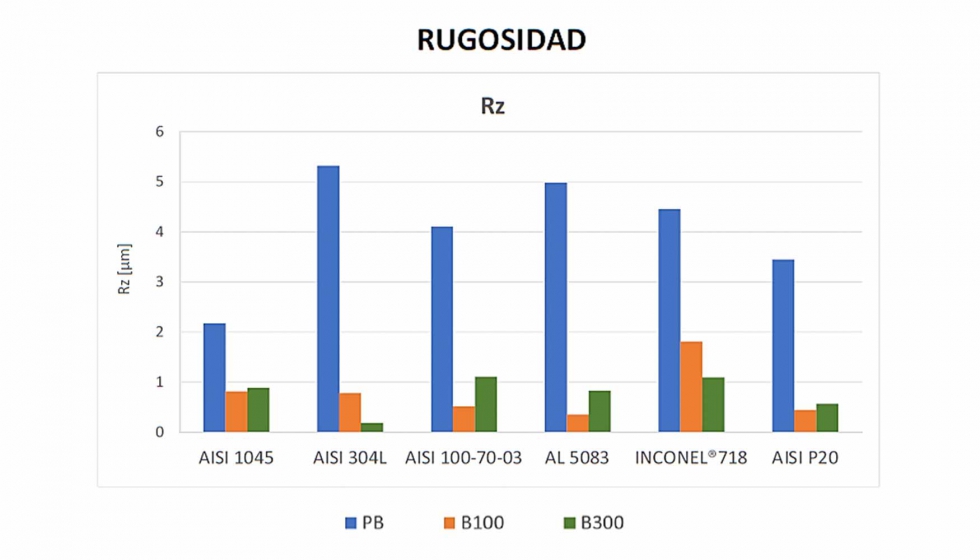
Por último, se realiza el análisis de los datos que se han obtenido de las tensiones residuales en la superficie y en la capa más próxima a la superficie, los cuales han sido obtenidos mediante el proceso hole drilling. En cuanto a este concepto, se denominan tensiones residuales o internas al estado tensional presente en el interior del material cuando éste no se encuentra sometido a cargas externas u otras fuentes de tensiones, como por ejemplo los gradientes térmicos. Este estado tensional interno tiene su origen en los tratamientos mecánicos y térmicos, y en ocasiones puede ser generado debido a las cargas aplicadas en servicio. Además, dicho estado tensional puede provocar cambios dimensionales y distorsiones en las piezas, además de otros problemas relacionados con el crecimiento de grietas cuando se trata de tensiones de tracción cercanas a la superficie. Por ello, el estado tensional interno del componente es de gran importancia y suele ser uno de los factores clave en los estudios de integridad, el cual tiene una gran influencia sobre el comportamiento a fatiga del componente. De esta forma, se produce una mayor resistencia a la fatiga si la superficie presenta tensiones residuales de compresión [3].
En cuanto a la designación de las tensiones residuales, por convenio, se consideran con signo positivo las tensiones residuales a tracción y con signo negativo las tensiones residuales a compresión.
Por otra parte, haciendo referencia a las medidas obtenidas de las tensiones residuales por medio del proceso hole drilling, se han obtenido las gráficas que aparecen a continuación, donde por cada gráfica de los materiales seleccionados se puede observar cuatro curvas, donde se diferencian las diferentes presiones de aplicación de bruñido y las curvas de tensión x e y. Mediante la curva definida como tensión-y se observa el efecto que ejerce el proceso en la dirección en la que ha sido programado el proceso de bruñido. En relación a la otra curva adquirida, es decir, la curva tensión-x, se observan las tensiones residuales que el proceso provoca en la dirección de avance del fresado.
Reparando en las gráficas, donde se obtienen las tensiones residuales que ofrece el proceso de deformación en el material en una profundidad de 1 mm desde la superficie, se puede apreciar que no en todos los materiales realizar el proceso a altos valores de presión en la herramienta de bruñido ofrece al material unas curvas que se mantengan en la zona de compresión, no solo en la superficie si no también en la capa mas inmediata a la superficie. Esto se puede examinar en el aluminio, por ejemplo, donde realizar el proceso a 100 bar las tensiones se mantienen en la zona de compresión y, sin embargo, al realizarlo a 300 bar de presión estas tensiones se han transformado en curvas de tracción a 0,6 mm de la superficie. Asimismo, de estas graficas se deduce que la aplicación del bruñido a 300 bar solo favorece, en cuanto a tensiones a compresión, al acero, a la fundición y al material endurecido seleccionado. El los materiales restantes, una aplicación a 100 bar sería suficiente para conseguir resultados notables.
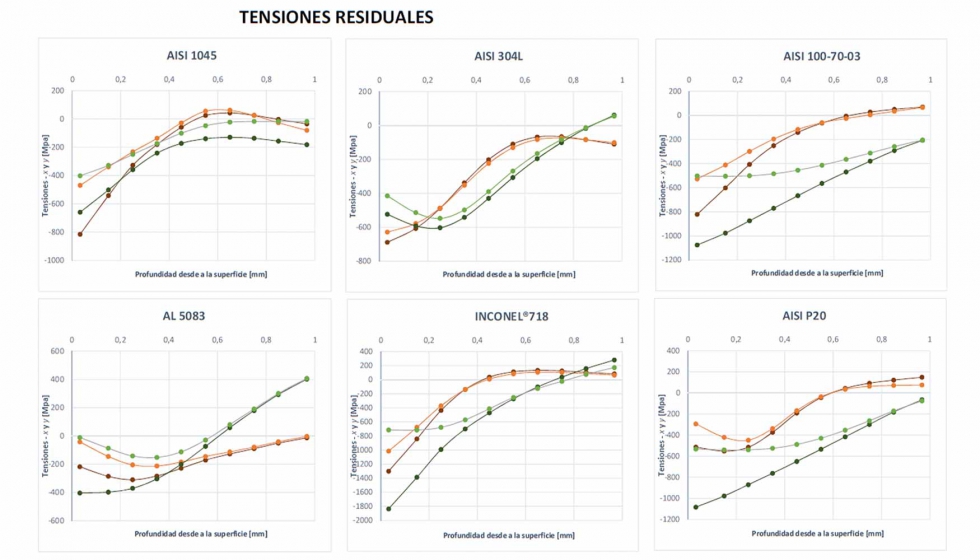
Conclusiones
Tras haber analizado todos los datos recopilados de las medidas obtenidas en los materiales seleccionados sometidos a este proceso de deformación, se puede afirmar que el bruñido ofrece grandes mejoras en cuanto a propiedades físicas y mecánicas en estos.
Por otro lado, cabe mencionar que para cada tipo de material se deberán encontrar los parámetros óptimos del proceso para lograr en cada material una gran mejora en cuanto a propiedades. Es decir, a pesar de que la fundición AISI 100-70-03 una aplicación a 300 bar implique un incremento de dureza superficial y unos buenos resultados en incorporación de tensiones residuales de compresión en la superficie de material, no ofrecerá al componente un acabado final ideal, puesto que como se ha mencionado anteriormente este material logra una mayor disminución de rugosidad si el proceso se realiza a 100 bar. Por ello, a la hora de efectuar la aplicación del bruñido hidrostático con bola en el componente metálico seleccionado, se deberá analizar cuál será su uso o en qué condiciones estará trabajando, y una vez realizado este estudio se escogerá la presión a la que se realizará el tratamiento superficial.
En cambio, si se realiza una comparación con las mejoras que ha ofrecido el proceso en los diferentes metales, se puede apreciar una mejora remarcable en el acero inoxidable austenítico AISI 304L, obteniendo un aumento de dureza del 81% y una disminución de rugosidad media del 97% respecto al material sin tratamiento alguno.
En resumen, el bruñido es un tratamiento superficial que con la obtención de unos parámetros óptimos de proceso para cada material ofrecería al mismo unas características excelentes tanto físicas como mecánicas. De esta manera, se podría evitar el uso de materiales con propiedades superiores, pero de un coste muy elevado, al poder obtener propiedades beneficiosas en materiales fáciles de adquirir una vez aplicado en el componente la técnica del bruñido hidrostático con bola.
Referencias
[1] AFM, ‘El sector de máquinas-herramienta creció un 5,4% para cerrar un buen 2018’, 2018. [En línea]. Disponible en: https://www.afm.es/es/noticias/el-sector-de-maquinas-herramienta-crecio-un-5-4-para-cerrar-un-buen-2018.
[2] ‘Global Market Forecast 2018-2037 - Market – Airbus’. [En línea]. https://www.airbus.com/aircraft/market/global-market-forecast.html.
[3] D. A. R. Ezquerro, ‘Mejora funcional se superficies en componentes mecánicos mediante bruñido hidrostático con bola’, p. 282.
[4] Ecoroll, ‘Tool Techology for Mechanical Metal surface Improvement’. [En línea]. https://www.ecoroll.de/fileadmin/blaetterkataloge/index.html?catalog=2018_01_E.
[5] LN López de Lacalle, A Rodriguez, A Lamikiz, A Celaya, R Alberdi, Five-Axis Machining and Burnishing of Complex Parts for the Improvement of Surface Roughness, Materials and Manufacturing Processes 26(8):997-1003.
[6] J.Sánchez Egea, A.Rodríguez, D.Celentano, A.Calleja, L.N.López de Lacalle, Joining metrics enhancement when combining FSW and ball-burnishing in a 2050 aluminium alloy, Surface and Coatings Technology, Volume 367, 15 June 2019, Pages 327-335.