Mapal recibió el desafío de diseñar las herramientas necesarias para el mecanizado del nuevo bloque motor en tan solo dos semanas
Innovación y eficiencia al servicio de Deutz España
Desde 1875, la fábrica de Deutz en Zafra ha sido sinónimo de excelencia en la fabricación de motores. Hoy en día, con alrededor de 500 empleados, produce componentes clave como bloques de motor, cilindros, bielas y engranajes para las líneas de montaje de Colonia y Ulm, así como para otros clientes. El nuevo motor diésel de 3,9 litros, diseñado principalmente para maquinaria agrícola y de construcción, es un símbolo de futuro para Deutz y ha confiado en la experiencia de Mapal —firma comercializada por Ayma— en la gestión de herramientas para asegurar el éxito.
Este motor, que comenzará su producción en serie el próximo año, tendrá una capacidad de 50,000 unidades anuales y se fabricará hasta al menos el año 2035. Con un rango de potencia de 55 a 160 kW, se posiciona como una solución eficiente que, además, podrá adaptarse a combustibles sostenibles como hidrógeno o gas. Según Alejandro Castilla De La Hoya, director de la planta en Zafra, “este motor refleja nuestro compromiso con la sostenibilidad y financia nuestras inversiones en movilidad verde”. Manuel Rodríguez López, director de Industrialización, añade: “Gracias su diseño versátil, estas unidades pueden convertirse en motores ecológicos a largo plazo mediante mínimas modificaciones”.
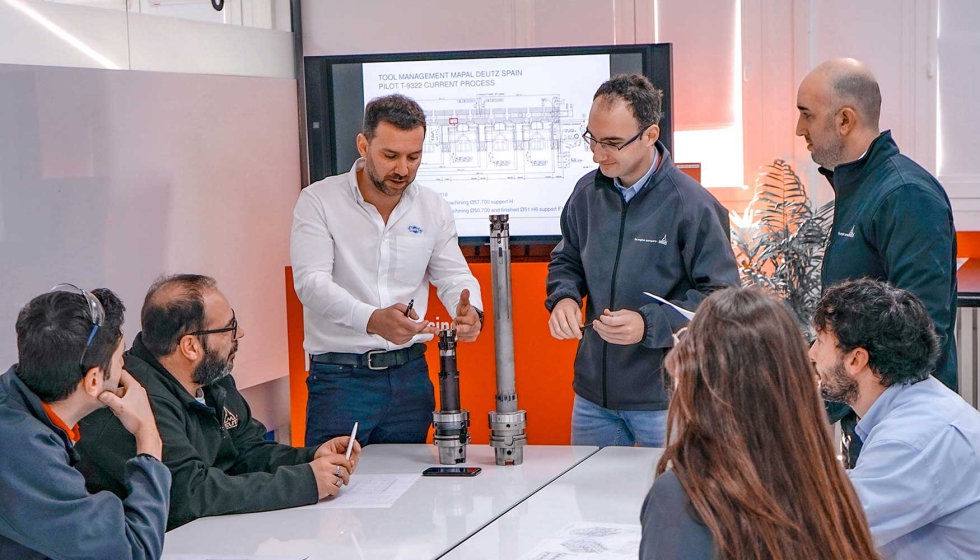
Retos superados en tiempo récord
La rapidez y precisión en el desarrollo de herramientas son esenciales en el sector. Mapal, proveedor estratégico de Deutz, recibió el desafío de diseñar las herramientas necesarias para el mecanizado del nuevo bloque motor en tan solo dos semanas tras la congelación del diseño.
Gracias a su experiencia previa con el motor de 3,6 litros, el equipo de expertos de Mapal logró cumplir el plazo con éxito. Esto fue posible gracias a la estrecha colaboración entre el equipo de Gestión de Herramientas y el Equipo de Expertos Tecnológicos (TET) en Aalen. En una primera fase, se recopilaron referencias de proyectos anteriores para definir un presupuesto y alcance preliminar. La oferta final incluyó casi 100 herramientas, muchas de ellas personalizadas para maximizar la eficiencia y reducir los tiempos de mecanizado.
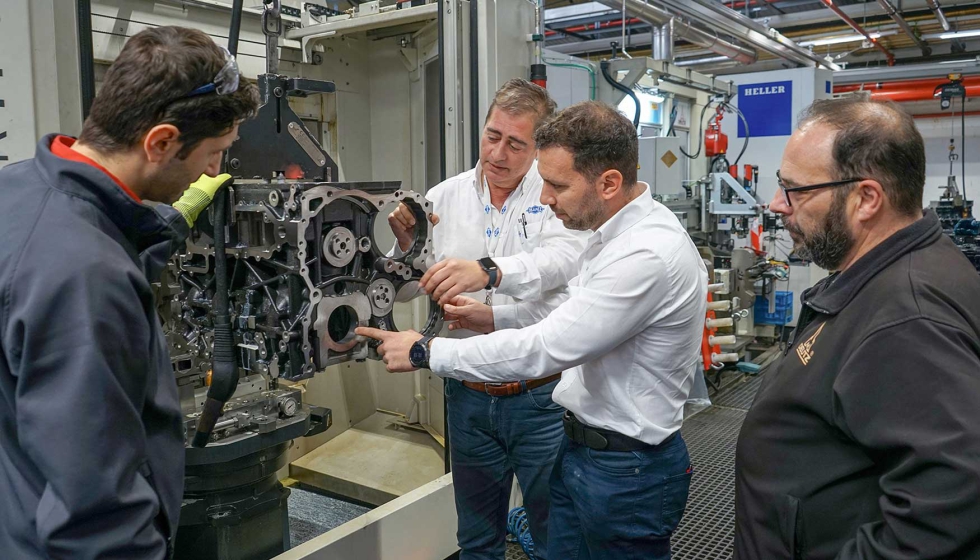
Optimización continua y colaboración estrecha
Mapal no solo suministró herramientas de corte y adaptadores para la producción inicial, sino que implementó un modelo de gestión que optimiza costos a lo largo del contrato. Este enfoque, basado en mejoras continuas y acuerdos flexibles, adopta un modelo de facturación basado en costos por pieza terminada en lugar de por herramienta.
La gestión de herramientas en Zafra incluye aproximadamente 1,300 unidades distintas, con soporte de sistemas digitales como el software c-Com, que automatiza procesos y analiza datos clave. Esta integración garantiza que las herramientas adecuadas estén siempre disponibles, justo a tiempo para la línea de montaje.
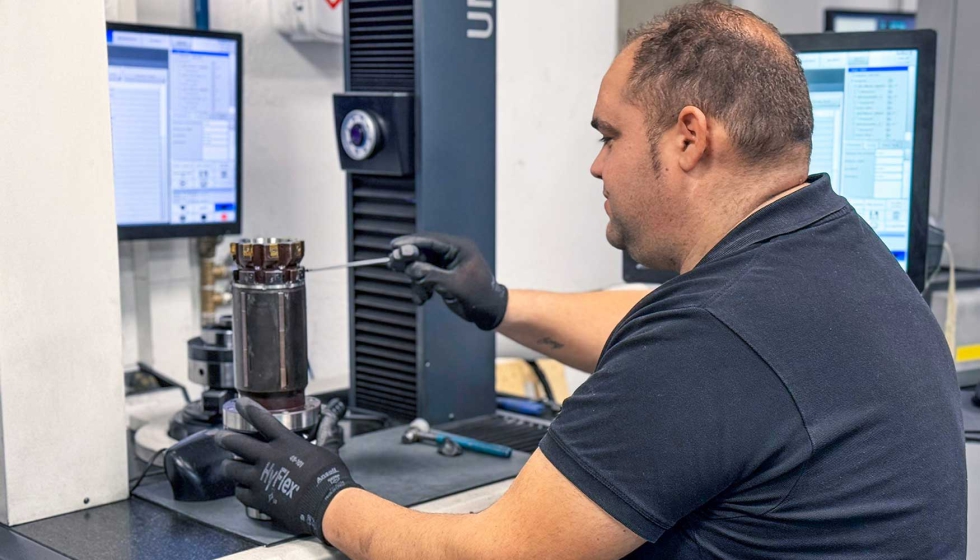
Manuel Rodríguez López resalta la importancia de esta colaboración: “Mapal no solo reduce costos, sino que garantiza el ajuste preciso de las herramientas, lo que es clave para mantener la calidad y eficiencia de nuestra producción”. David Castaño, responsable en obra de Mapal, es un ejemplo de esta sinergia: “Su conocimiento técnico y disponibilidad directa nos permite abordar desafíos en tiempo real y con resultados sobresalientes”.
Soluciones innovadoras en el mecanizado de precisión
Un ejemplo reciente de esta colaboración fue la optimización del mecanizado para los agujeros del cigüeñal y árbol de levas, lograda mediante el escariador HPR400 de MAPAL. Este nuevo concepto de mecanizado ha triplicado la vida útil de la herramienta, alcanzando 1,000 piezas sin necesidad de rearme, con una calidad de acabado excepcional.
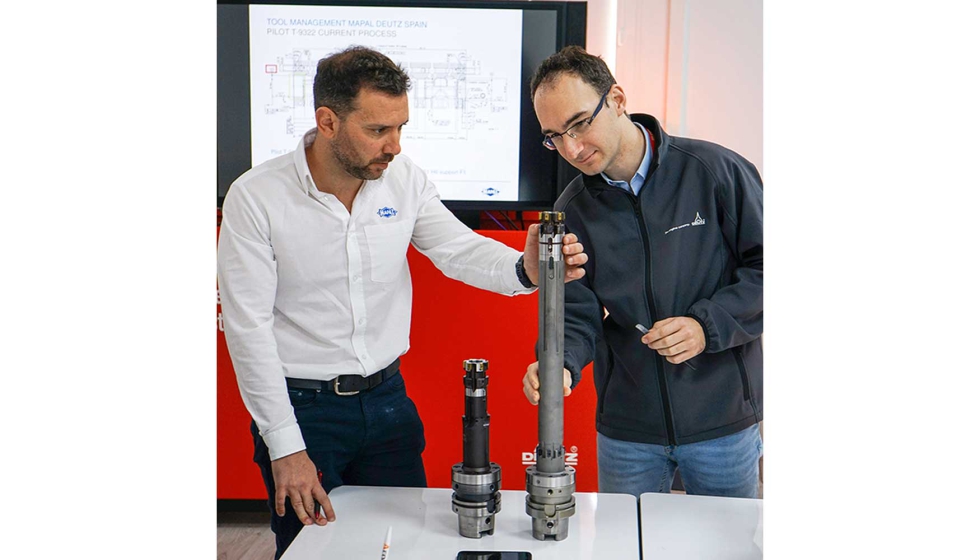
Con este proyecto, y a través de su compromiso conjunto, Mapal y Deutz demuestran que la innovación, la experiencia y la cooperación son fundamentales para superar los desafíos de la industria y alcanzar la excelencia en fabricación.
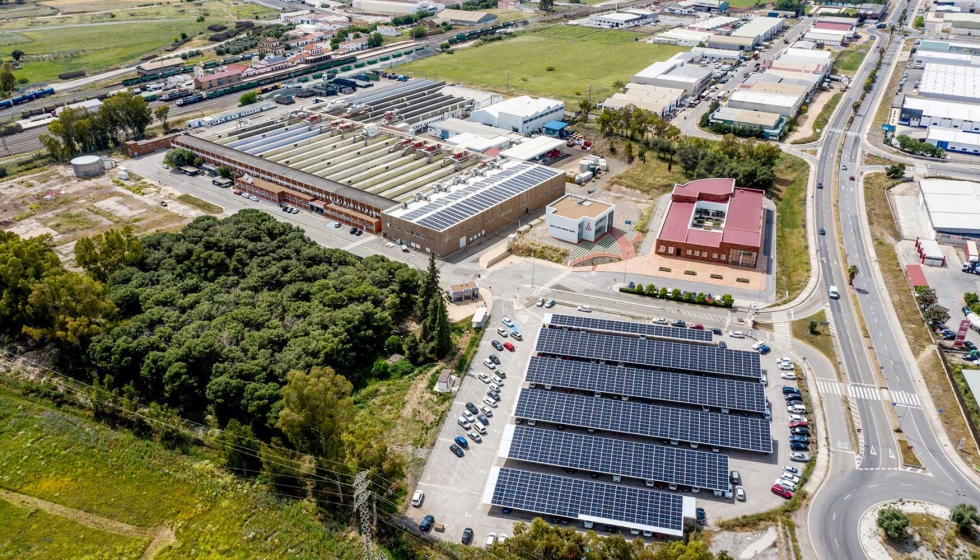