La obra fue ejecutada para Interbiak, por UTE Urdinbide (Viuda de Sainz-Lurpelan Tunnelling-Excavaciones Cantabricas)
Proyecto de terminación de las obras del tramo Amorebieta – Muxika
Departamento Técnico Lurpelan Tunnelling S.A.
13/03/2020La finalidad de las obras del tramo Amorebieta – Muxika, en el que está incluido el túnel de Urdinbide, es la mejora de la actual carretera BI-635 desde Amorebieta hasta la bajada del alto de Autzagane, con una longitud total de la obra próxima a los 3.500 m, cuyo trazado general se ha mostrado en el apartado anterior.
El elemento más singular es el túnel de Urdinbide, formado por dos tubos de dos carriles de circulación cada uno y sentido del tráfico unidireccional con longitud final de 701 m, de los cuales el proyecto de terminación contempló la ejecución pendiente de 62 y 63 m de excavación de avance en Eje 1 y Eje 2 respectivamente y 160 y 164 m de destroza respectivamente mediante tratamientos especiales de inyecciones.
Inicialmente hay que indicar que el túnel presenta dos zonas claramente diferenciadas: un tramo cuya ejecución genera afecciones al acuífero existente que deben evitarse/minimizarse; y el resto del túnel, que no presenta tales afecciones y, por tanto, se ejecuta por procedimientos habituales de excavación del NATM (excavación y sostenimiento).
La zona de afección al acuífero se ha determinado mediante la observación y análisis de la geología existente, así como de los resultados de los sondeos horizontales realizados durante la ejecución. Esta zona se ubica entre los pk 2+859 y 3+019 en el eje 1, y entre los pk 2+840 y 3+004 en el eje 2.
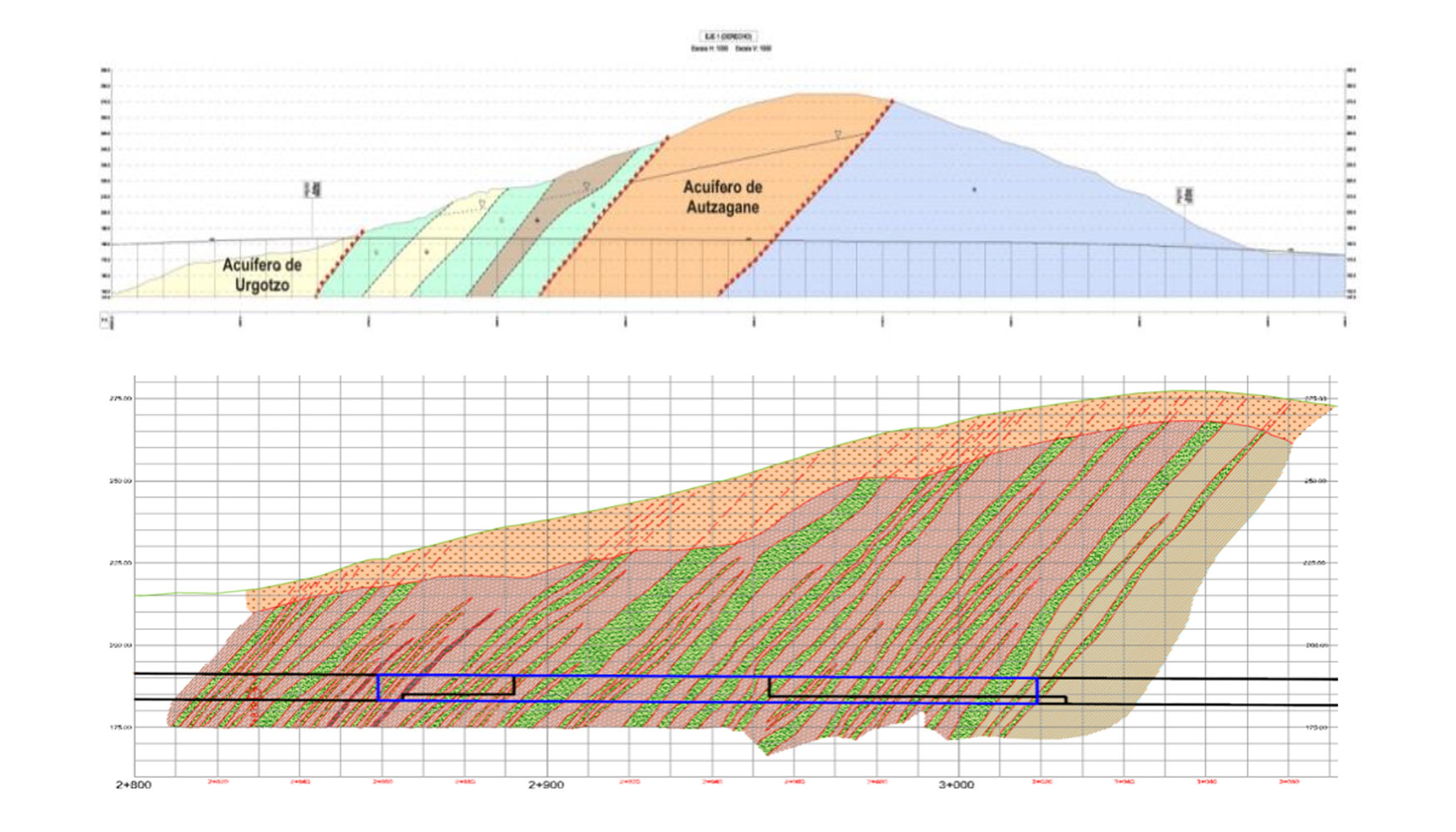
Geográficamente, las obras del tramo Amorebieta - Muxika, se sitúan en la zona norte de la Península, concretamente en el País Vasco, discurriendo por los términos municipales de Amorebieta - Etxano y Muxika, en la provincia de Vizcaya.
La aprobación ambiental del proyecto original vino condicionada a que la ejecución del túnel no afectase de forma sensible al acuífero que se iba a atravesar, así como a mantener el sistema de captaciones y aprovechamientos existentes y el propio caudal ecológico del arroyo Ategorri, proveniente de los manantiales que abastecen este acuífero.
Esta premisa se ha mantenido durante la ejecución de las obras como criterio básico de diseño del presente proyecto.
A partir de los datos recopilados durante el seguimiento hidrológico que se ha llevado a cabo desde el inicio de la obra, el cual ha incluido control de niveles piezométricos y control de aforos (aguas de infiltración del túnel y de los manantiales y arroyos), se ha realizado, por parte de Eptisa y para el presente proyecto, una actualización del modelo hidrogeológico, sobre el que se ha simulado el túnel terminado. En dicha simulación se ha considerado el coeficiente de permeabilidad alcanzado tras las labores de inyección del macizo rocoso, como se ha podido comprobar en la obra ejecutada hasta el momento.
A partir de este estudio, se han definido las soluciones de impermeabilización a llevar a cabo (inyecciones y tramo de túnel con revestimiento estanco) que permitan cumplir las condiciones establecidas.
En lo referente al túnel (la parte principal del proyecto) la excavación pendiente se encuentra prácticamente en su totalidad en la zona de afección al acuífero. Esta zona de afección al acuífero está limitada entre los pk’s 2+859 y 3+019 en el eje 1 (160 metros) y entre los pk’s 2+840 y 3+004 en el eje 2 (164 metros).
En esta zona, la sección tipo a ejecutar (ST-V) contempla la ejecución de unas inyecciones sistemáticas, repetitivas y selectivas (tipo I.R.S.) en secciones separadas entre sí por 6 metros, cuyo objeto es conseguir una corona de terreno mejorado de un espesor mínimo de 3 metros alrededor del perímetros de la excavación y una impermeabilización que evite la infiltración de las aguas hacia el interior del túnel. Esta sección tipo también contempla la ejecución de contrabóveda y de otras condiciones de ejecución específicas.
Las inyecciones definidas son repetitivas y selectivas y se realizan mediante el sistema de reperforaciones sobre los mismos taladros con longitudes incrementadas en cada fase de perforación. Se diseñan de esta forma con objeto de uniformizar el procedimiento de ejecución utilizado en los últimos tramos ejecutados y que ha resultado más efectivo. Se trata de coronas de perforación e inyección troncocónicas ejecutadas en un mínimo de 4 etapas con inyecciones de cemento en las primeras etapas ('recintado') y de microcemento en las últimas ('impermeabilización y mejora').
La geometría de las inyecciones se realiza adaptándose a la orientación de las superficies de estratificación del macizo rocoso, de forma que la base de la superficie troncocónica sea siempre un plano virtual paralelo a dicha estratificación. Esta geometría es la que, en el tramo ejecutado, ha dado mejores resultados. Y esta geometría es la que obliga, a su vez, a realizar tratamientos en fase de avance y en fase de destroza.
El diseño completo de las inyecciones se ha realizado por parte de Pedro Sola (de la empresa IIT), ingeniero de dilatada y contrastada experiencia en este tipo de trabajos y que, además, ha participado como asesor durante los trabajos realizados en estos túneles.
Cabe indicar que el desarrollo y la adaptación a la obra para la ejecución de estas inyecciones inyecciones se han utilizado, como bases de partida, los resultados del estudio hidrogeológico indicado anteriormente, así como los resultados de los cálculos del túnel realizados por la empresa TYG, de contrastada experiencia en este tipo de trabajos. Para la realización de estos cálculos se han utilizado los datos de caracterización geomecánica del terreno obtenidos durante la excavación del túnel ya ejecutada.
Túnel de Urdinbide
El Túnel de Urdinbide se proyectó con sección circular de radio interior de 6,53 metros (en la zona fuera del acuífero) y de 6,48 metros en la zona de acuífero con ST-V, con una altura del centro de 1,286 metros sobre el eje con el firme a lo largo de todo el túnel; consiguiéndose, con esta geometría, un gálibo de, al menos, 5 metros sobre bordes de plataforma.
La boquilla norte del túnel proyectado queda dentro de la Reserva de la Biosfera de Urdaibai.
El túnel de Urdinbide es un túnel bitubo (un tubo por calzada) y dos carriles por calzada. La separación entre ambos tubos es de aproximadamente 21,50 m. Esta separación permanece prácticamente constante a lo largo de toda la longitud del túnel en mina.
La longitud total de los túneles es de algo menos de 700 m por tubo (695 y 693 m, respectivamente en el eje 1 y 2) con recubrimientos máximos en torno a 90 m, siendo la parte correspondiente al túnel en mina de 538 y 537 metros respectivamente para cada eje.
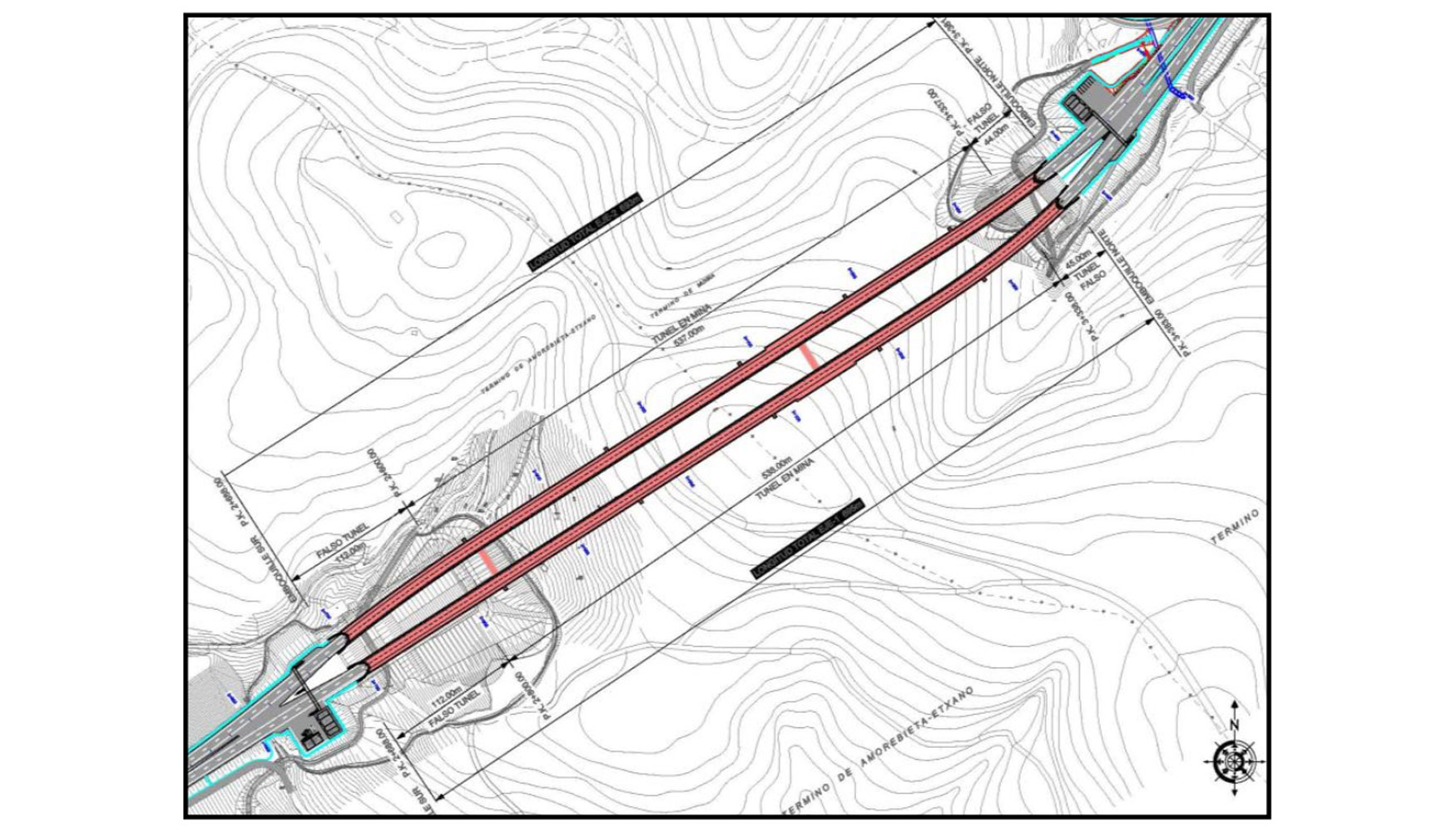
Geología
El trazado del túnel afecta a dos unidades estratigráficas que pertenecen a la Unidad Oiz, en el Sector Gernika, formado por materiales del Eoceno Inferior:
- L+Mg+Ca Lutitas, margas y calizas. Entre los Pk’s 3+012 y 2+994 hasta la boquilla norte del túnel (Pk 3+338), en los ejes 1 y 2 respectivamente y a cota de avance. Se trata de una serie fundamentalmente formada por margas masivas grises, lutitas hojosas algo micáceas grises, y calizas micríticas y masivas de color gris oscuro a negruzco con finas alternancias de bancos tabulares de 0.06 a 0.25 m de areniscas de grano fino o muy fino con un porcentaje muy variable de cemento carbonatado.
- Ar+L Areniscas, lutitas y microconglomerados. Areniscas de Algorta. Aparecen entre la boquilla sur del túnel (2+800) hasta los Pk’s 3+012 y 2+994 de los ejes 1 y 2 respectivamente y a cota de avance. Consiste en una sucesión de bancos de magnitud decimétrica a métrica de areniscas con cemento calcáreo de grano medio a grueso, con un porcentaje muy variable de matriz arcillo-limosa que se presenta con estructura masiva o finamente laminada. Estos bancos están separados entre sí por intercalaciones más finas formadas por limolitas y lutitas calcáreas.
Inyecciones sistemáticas de impermeabilización y mejora
La excavación del túnel en el tramo de afección al acuífero requiere de la realización de unas inyecciones previas sobre el terreno, cuyos objetivos son:
- Conseguir una corona de terreno 'mejorado' de un espesor mínimo de 3 metros en todo el perímetro de la excavación.
- Reducir la permeabilidad del terreno hasta unos valores con los que la infiltración de agua al túnel no supere el caudal máximo que se puede detraer sin afectar de forma sensible al acuífero.
El primero de los objetivos es un requisito que viene determinado por la estabilidad del túnel durante la ejecución. Los cálculos estructurales realizados han determinado la necesidad de disponer de una corona de espesor mínimo 3 metros en todo el perímetro, en la que el grado de mejora conseguido sea un aumento del valor del GSI en 20 puntos.
El segundo objetivo viene determinado por el estudio hidrológico realizado, que establece el caudal máximo a detraer para evitar afecciones sensibles al acuífero de Autzagane y a su sistema de captaciones y manantiales. A partir de este caudal máximo y de las permeabilidades conseguidas con los tratamientos de inyección realizados durante las obras, se ha establecido también la tramificación del túnel con revestimiento estanco y drenado, con la cual se cumple dicho requisito.
Las inyecciones se realizan desde el interior del túnel y consisten en recintos troncocónicos exteriores al perímetro de las excavación realizados mediante el sistema I.R.S. (inyecciones repetitivas y selectivas). Adicionalmente se complementan con tratamientos del frente.
La geometría de los tratamientos se ha determinado de forma que el plano definido por los puntos finales de todas las perforaciones de cada sección de tratamiento, conformando un plano virtual paralelo a la superficie de estratificación y estableciendo como longitud máxima de perforación (taladro más largo), 32 metros, por operativa de la maquinaria (jumbo).
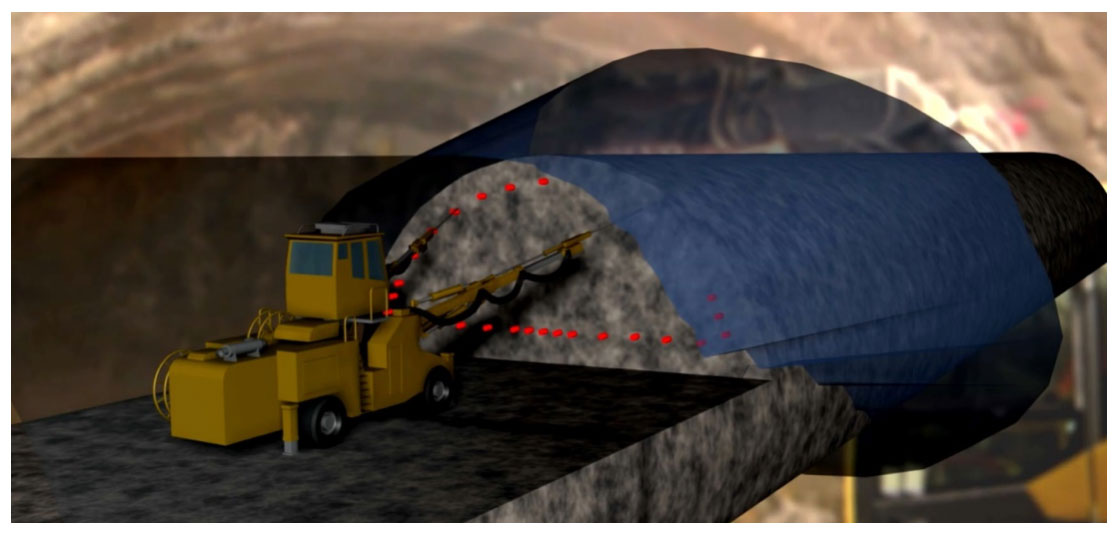
Con estas premisas y estableciendo un contorno exterior a la excavación de 4,5 metros, que asegure, teniendo en cuenta las posibles desviaciones, la corona mínima de 3 metros, se obtiene que la longitud máxima de excavación entre dos secciones de tratamiento es de 6 metros en avance y de 8 metros en destroza. De esta forma se asegura el solape de 6 metros que se ha considerado.
También se ha determinado la necesidad de realizar las inyecciones en 2 fases, avance y destroza, ya que con los requisitos anteriormente citados, es geométricamente imposible conseguir una corona de tres metros de terreno mejorado bajo la línea de excavación de la contrabóveda con un solo tratamiento desde el avance.
El tratamiento se realiza mediante la inyección de mezclas de diversa tipología y dosificación a través de las perforaciones previas cuya disposición conforma coronas troncocónicas de una geometría determinada, ya descrita anteriormente.
Las coronas de tratamientos se realizan en varias etapas, que tienen diferentes contornos exteriores y mezclas a utilizar. Cada etapa consta de 30 taladros en fase de avance y 19 taladros en fase de destroza.
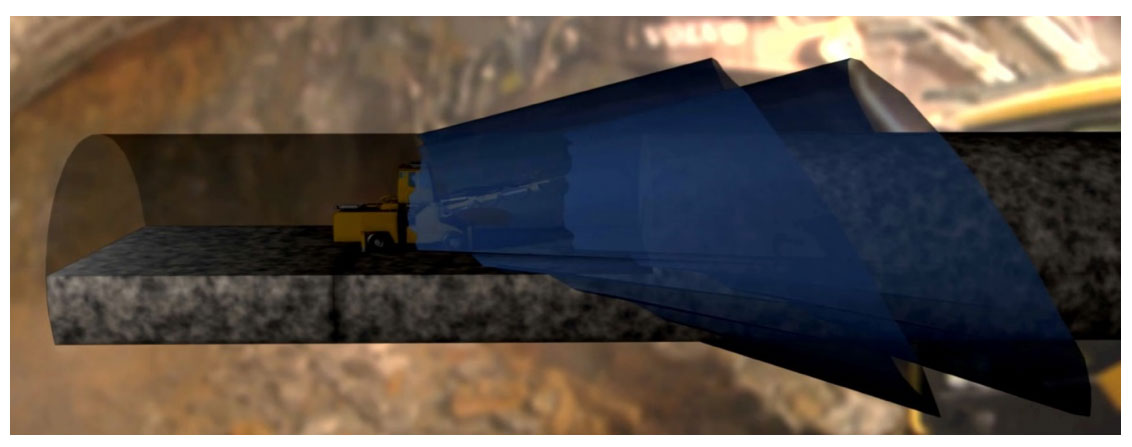
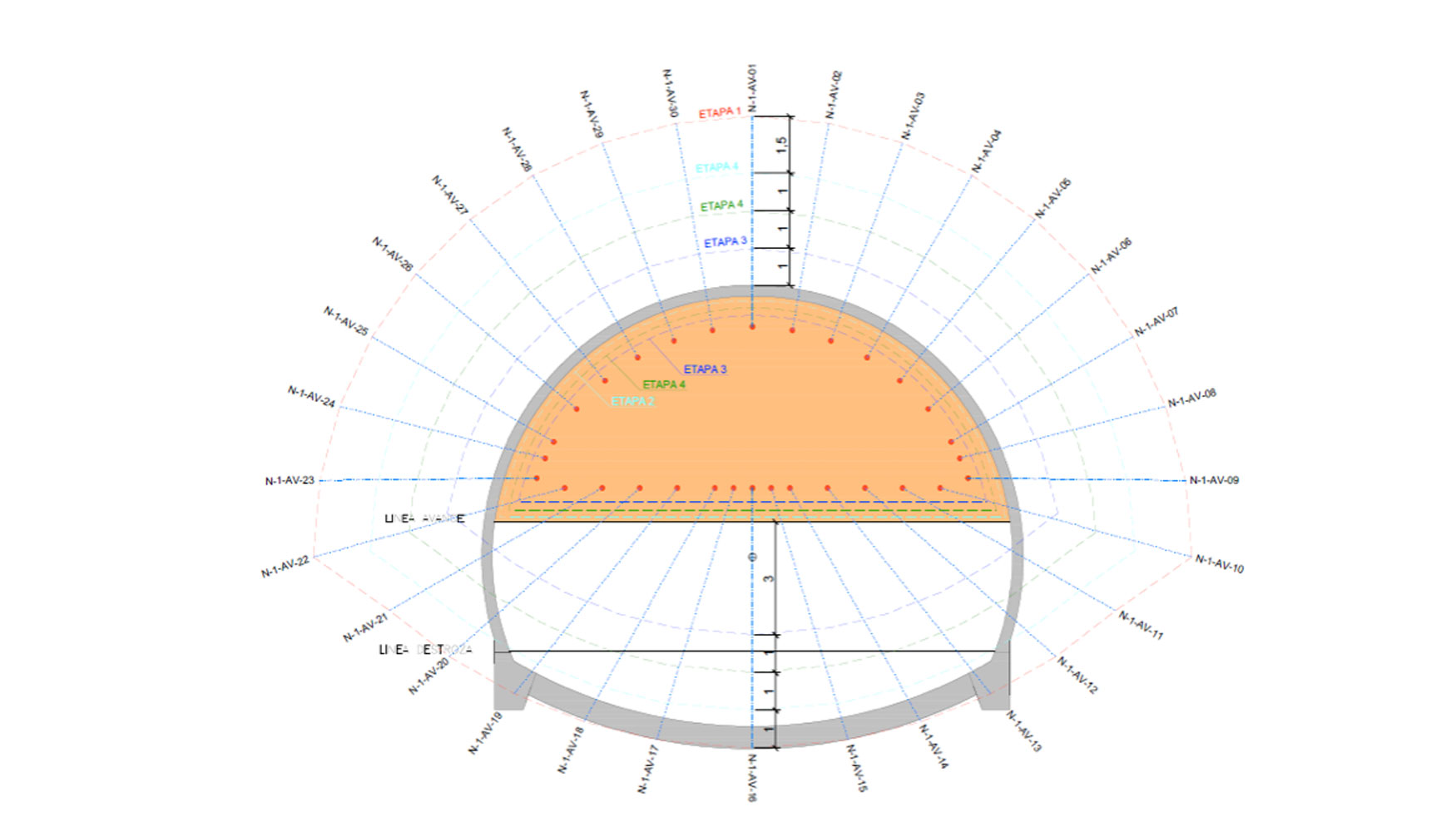
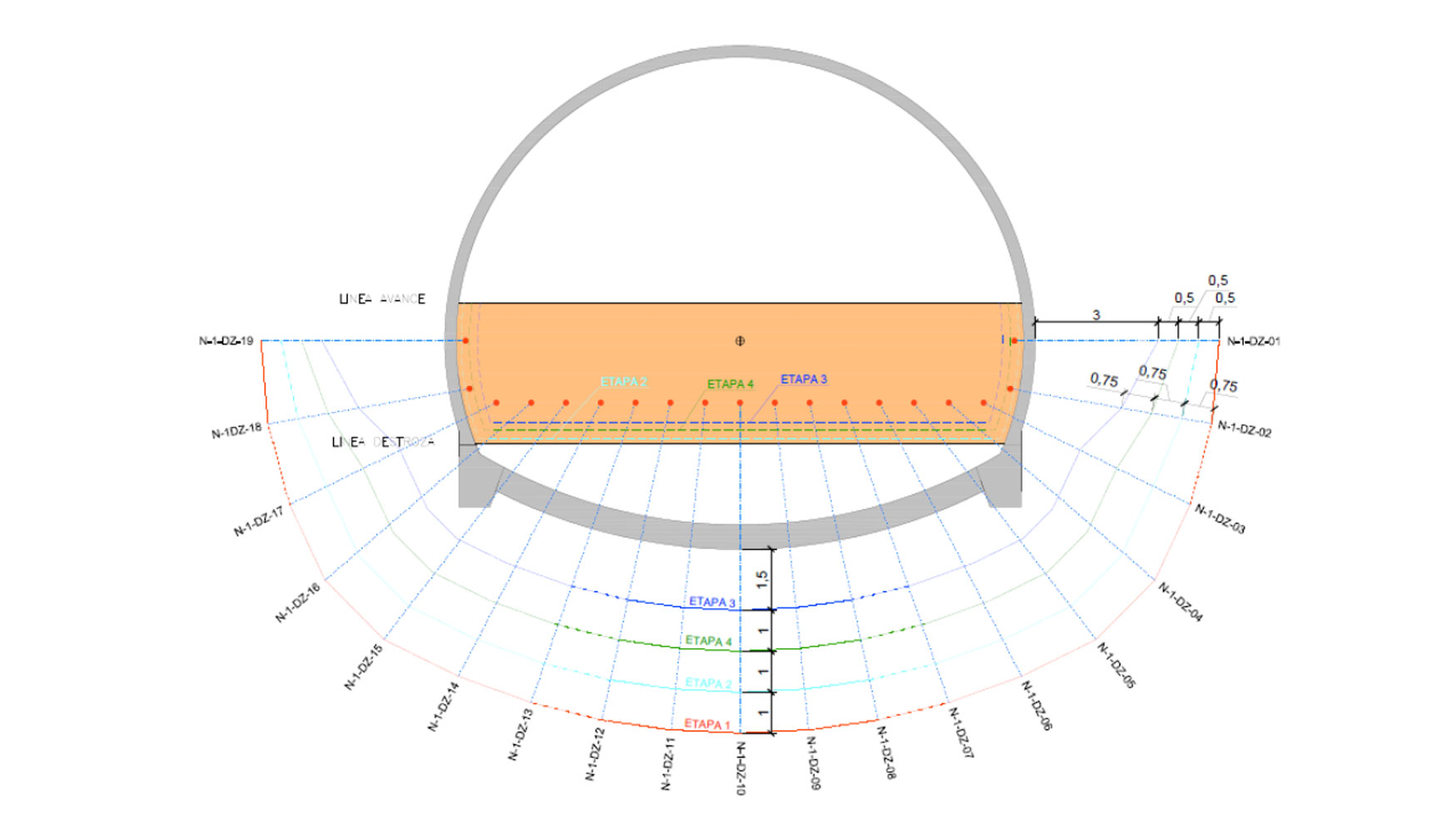
Las dos primeras etapas tienen la misión principal de 'recintado'. Se trata de conseguir un recinto de terreno pretratado que reduzca los caudales de infiltración y permita, en las siguientes etapas, realizar el tratamiento de impermeabilización y mejora del terreno.
Para ello, en las dos etapas iniciales se inyectan lechadas de cemento con acelerante; mezclas densas y de fraguado rápido que permitan realizar el 'recintado'. Por el contrario, en las siguientes etapas se inyectan lechadas de microcemento de 12µ; mezclas más fluidas y de mayor penetrabilidad e inyectadas a presiones más altas para que penetren de forma eficaz en las juntas o espacios intergranulares consiguiendo la reducción de permeabilidad y la mejora de las características del terreno buscadas.
El proyecto contempla la ejecución de un mínimo de 4 etapas por sección de tratamiento y un máximo de 5 etapas.
Para conseguir el tratamiento I.R.S., los taladros de cada etapa se perforan, a su vez, por fases de longitudes múltiplos de 6 m (6, 12, 18, 24, …). Es decir, inicialmente se perforan una longitud de 6 metros y se inyectan. Una vez la mezcla ha fraguado, se reperforan hasta 12 metros y se inyectan, y así sucesivamente hasta la longitud final definida para cada taladro. Este sistema de ejecución permite inyectar de forma selectiva por tramos y ha sido utilizado con resultados satisfactorios en los tramos de túnel ya inyectados. Cabe indicar que el sistema diseñado mantiene el diseño conceptual del proyecto original de inyecciones IRS, sustituyendo el uso del tubo manguito por un procedimiento con perforaciones y reperforaciones consecutivas de longitud creciente, que permiten ir tratando diferentes tramos de terreno por fases. Este procedimiento ha resultado efectivo durante las obras ejecutadas.
En la primera etapa (y con menos probabilidad en la segunda) es cuando los taladros pueden interceptar capas sin tratamiento previo y generarse vías de agua hacia el interior del túnel con arrastres de arenas. En esta primera etapa (y en la segunda si fuese necesario) se ha previsto la instalación previa de boquillas tipo 'preventer', que permiten detener las entradas de agua con grandes caudales e inyectar con seguridad. Estas actuaciones preventivas son especialmente importantes, ya que si durante la ejecución se producen salidas de importantes caudales de aguas con arrastres sólidos, generan un empeoramiento del terreno que hace más difícil conseguir las mejoras del tratamiento. En situaciones con caudales reducidos y sin arrastres se han previsto obturadores simples con accionamiento mecánico o neumático (tipo bimbar), según el caso.
La tipología de mezclas a utilizar y sus dosificaciones se establecen en función de los caudales aforados en la perforación y de la presencia o no de arrastres de sólidos.
Cabe indicar que, adicionalmente a las coronas anteriormente descritas, se realiza un tratamiento del frente para cerrar frontalmente el recinto. Consta de 17 taladros de 12 metros de longitud repartidos uniformemente por la sección.
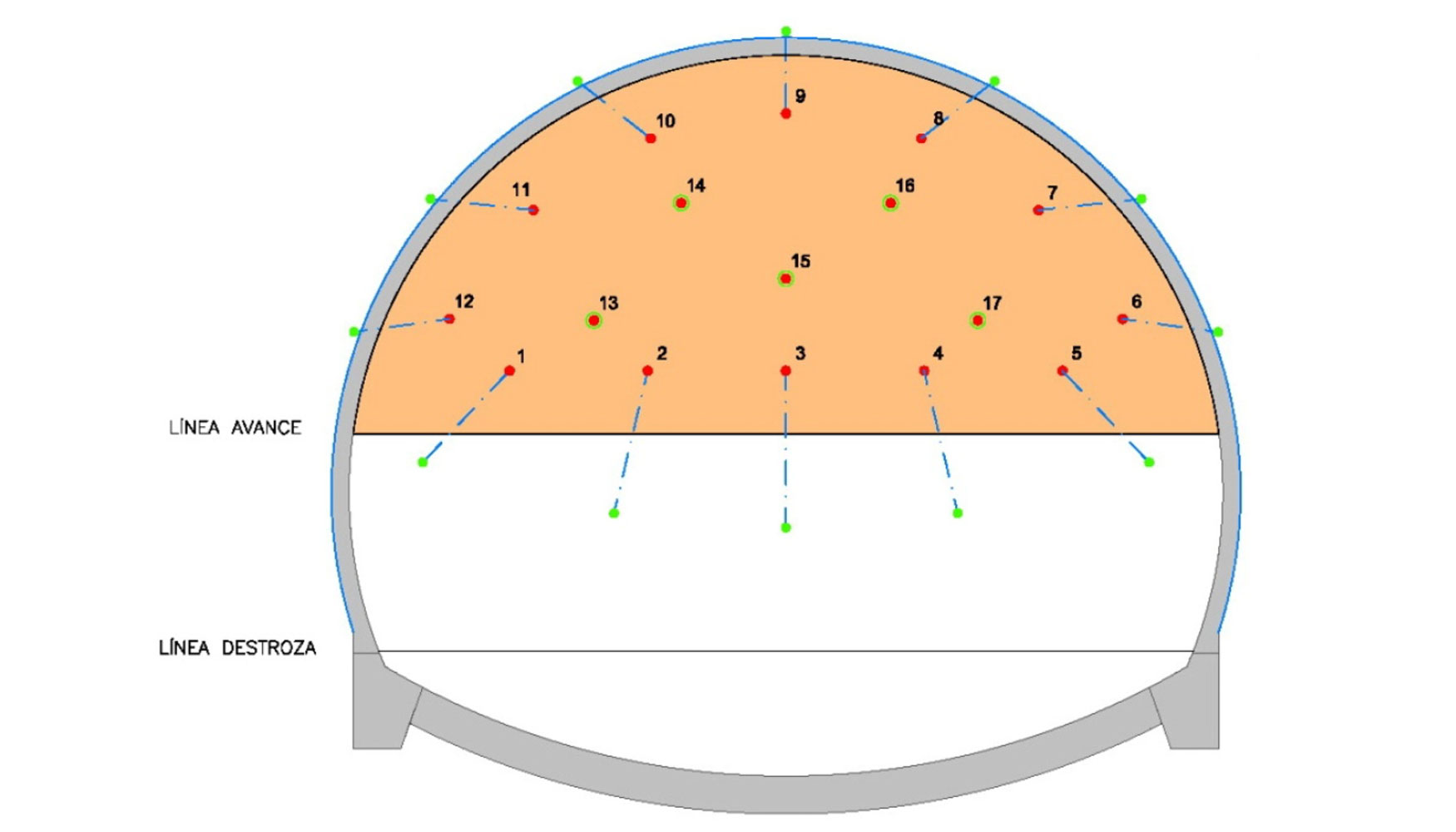
Finalización del tratamiento
El proyecto contempla criterios de control objetivos que permitan evaluar el grado de mejora e impermeabilización conseguido. Como ya se ha mencionado, son dos los objetivos de los tratamientos; por un lado la mejora de las características del terreno en una corona de mínimo 3 metros alrededor del perímetro de la excavación, y por otro, conseguir reducir la permeabilidad para que los caudales infiltrados no superen los admisibles.
Para el primer objetivo (mejora del terreno), el proyecto contempla un control basado en las presiones de inyección alcanzadas en la última etapa. Se considera que conseguir presiones de cierre elevadas supone disponer de un terreno de mejores características. Para considerar que la mejora exigida (incremento de 20 puntos de GSI) se ha conseguido, las presiones de cierre de las inyecciones de los taladros de la última etapa deberán cumplir las siguientes condiciones:
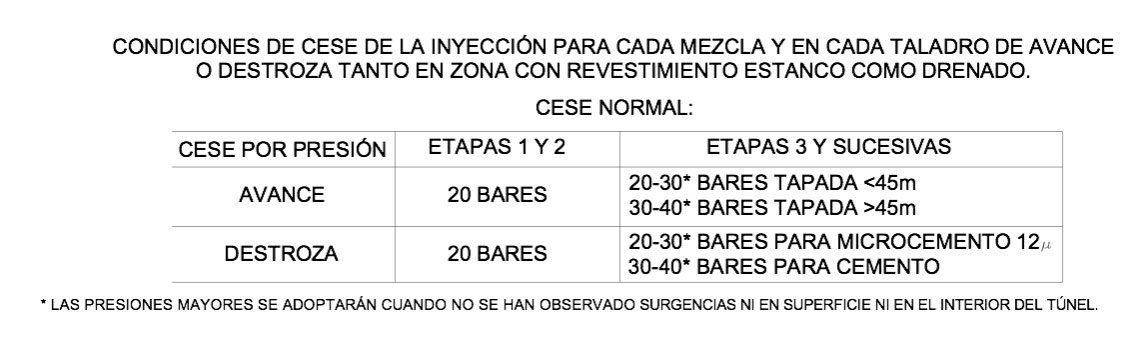
En cuanto a la reducción de permeabilidad, el proyecto contempla la realización de 8 taladros de control repartidos por el perímetro y frente de la excavación de una longitud igual a la excavación a realizar más un mínimo de 6 metros de solape (mínimo de 12 metros). Una vez realizados, se aforan para medir los caudales que deben cumplir unos máximos en función de las características del tramo a considerar, con revestimiento estanco o drenado.
Tramo con revestimiento estanco:
- Caudal medio de los taladros de control = 10 litros/minuto
- Ningún taladro con caudal mayor a 30 litros/minuto
Tramo con revestimiento drenado:
- Suma de los caudales de los taladros de control = 1,5 litros/minuto
Ejecución de los trabajos
Los trabajos de inyección ejecutados por Lurpelan en esta obra fueron:
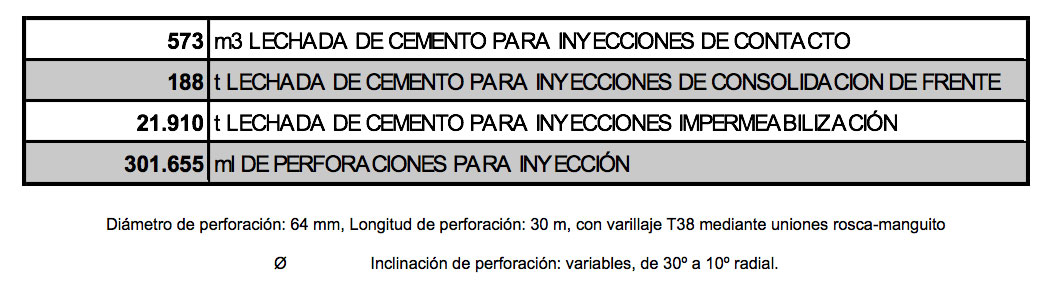
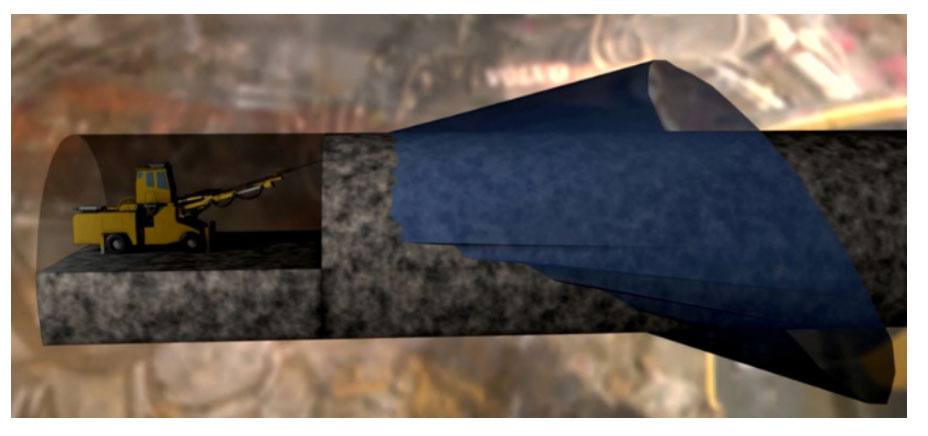
Esta geometría se ejecutó tanto en los tratamientos en fase de avance como en fase de destroza de túnel y fueron ejecutados mediante jumbo Sandvik DT1130 semiautomático, con navegación y recogida de parámetros de perforación que permitió el control de los trabajos durante toda la ejecución de la obra.
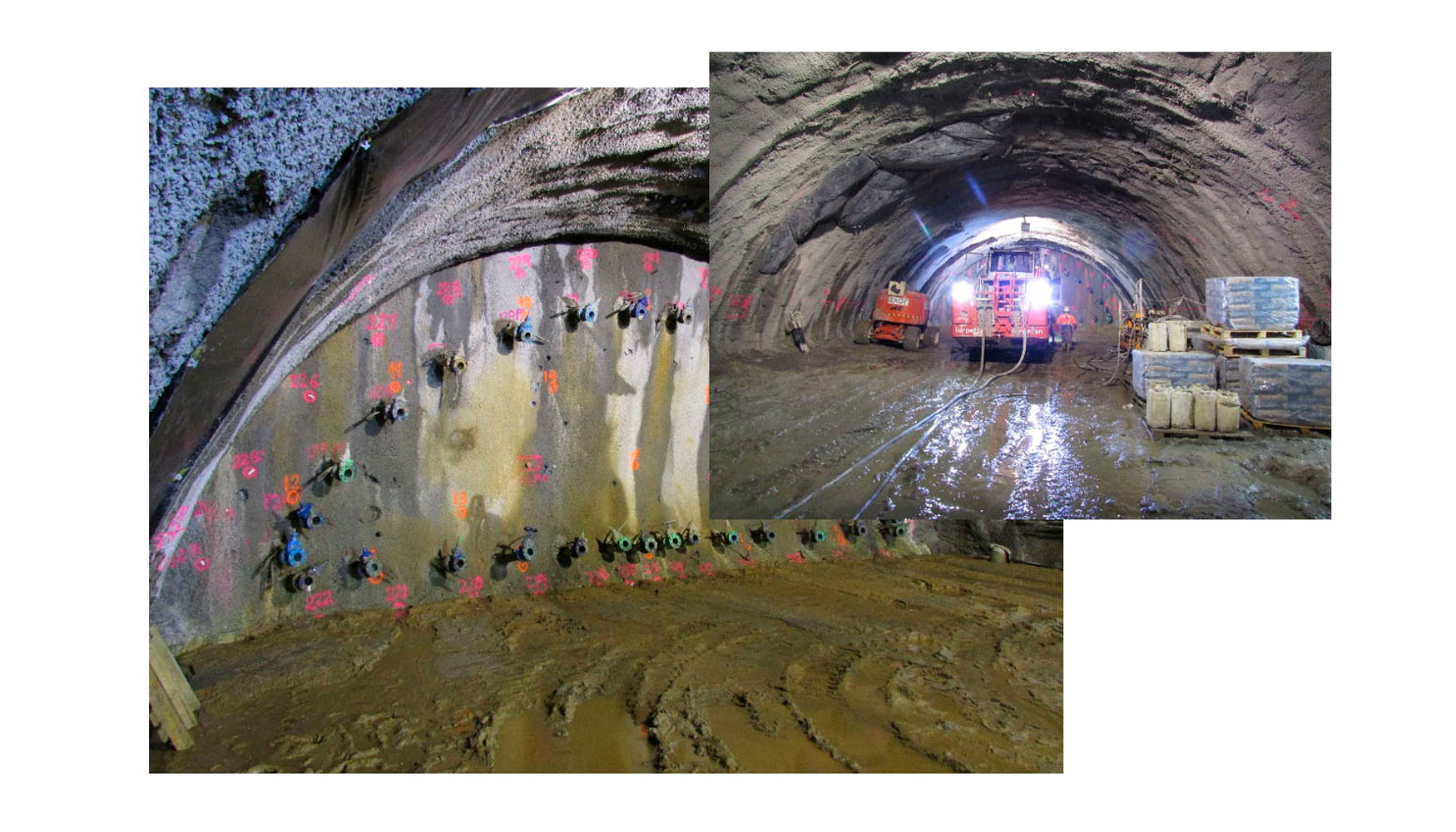
Lurpelan monitorizó las inyecciones mediante el uso de centrales de inyección con dos cuerpos de bomba PH5, una central de engrase y una central hidráulica con grupo motobomba de 5,5 kW, para inyección de lechada de 120 a 1.400 l/h por bomba a presión máxima de 85 bar.
El control del caudal y el volumen inyectado se realiza a través de caudalímetros Siemens y el valor de la presión se mide a través de los transmisores de presión Sensotec.
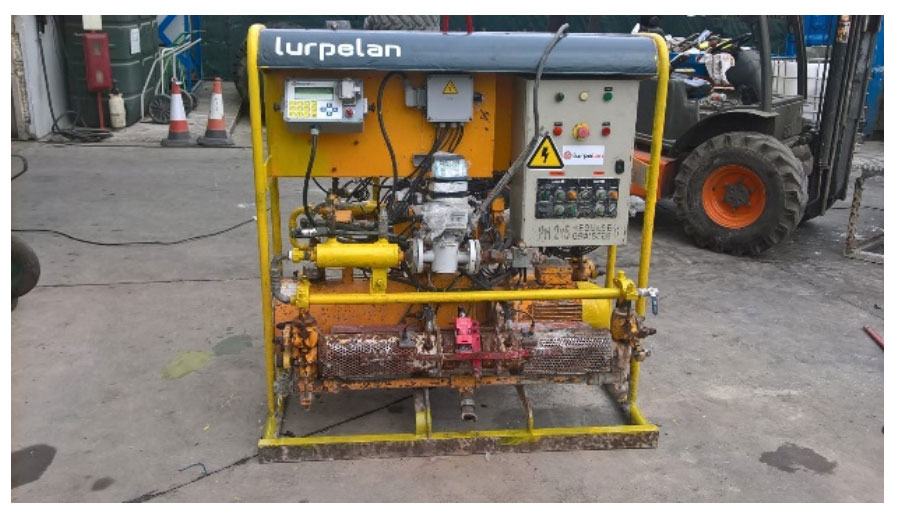
Caudalímetros Siemens: Sitrans F M MAG 5100 W, MAG 5000/6000
En estos caudalímetros, el principio de medición de caudal se basa en la ley de Faraday de la inducción electromagnética. Las bobinas están montadas diametralmente en el tubo a medir generando un campo electromagnético pulsado. El líquido que fluye a través de este campo electromagnético induce un voltaje.
Los transmisores evalúan las señales de los sensores electromagnéticos asociados, luego las convierten en señales estándar apropiadas (p. ej. 4 a 20 mA) y realizan también la función de una unidad de alimentación que proporciona una corriente constante a las bobinas.
El transmisor consta de una serie de bloques de función que convierte el voltaje del sensor en lectura de caudal.
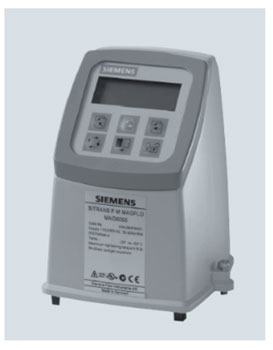
Transmisor de presión relativa Sensotec: 26.000 G-6002-R-1-5-100-200-1-000
Para la medida de presión con transmisores de presión, o sensores de presión se requiere un sensor que mide el valor de presión o la variación de la misma y lo convierte en una señal eléctrica. La señal eléctrica indica el valor de presión recibida.
El modelo que empleamos en cada línea de inyección es de 60 bar a 20 mA y 32 VDC.
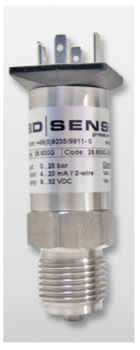
La maquinaria utilizada para la ejecución del túnel de Urdinbide fue la siguiente:
- Manipulador telescópico JCB 535-125
- Jumbo Atlas Copco Boomer 282
- Jumbos Sandvik DT1130
- Robot Gunitador Sika PM-500
- Palas cargadoras sobre ruedas
- Miniretro JCB 8060
- Lagartos Volvo A25 y A30
- Retroexcavadoras Volvo 300ECR y 290
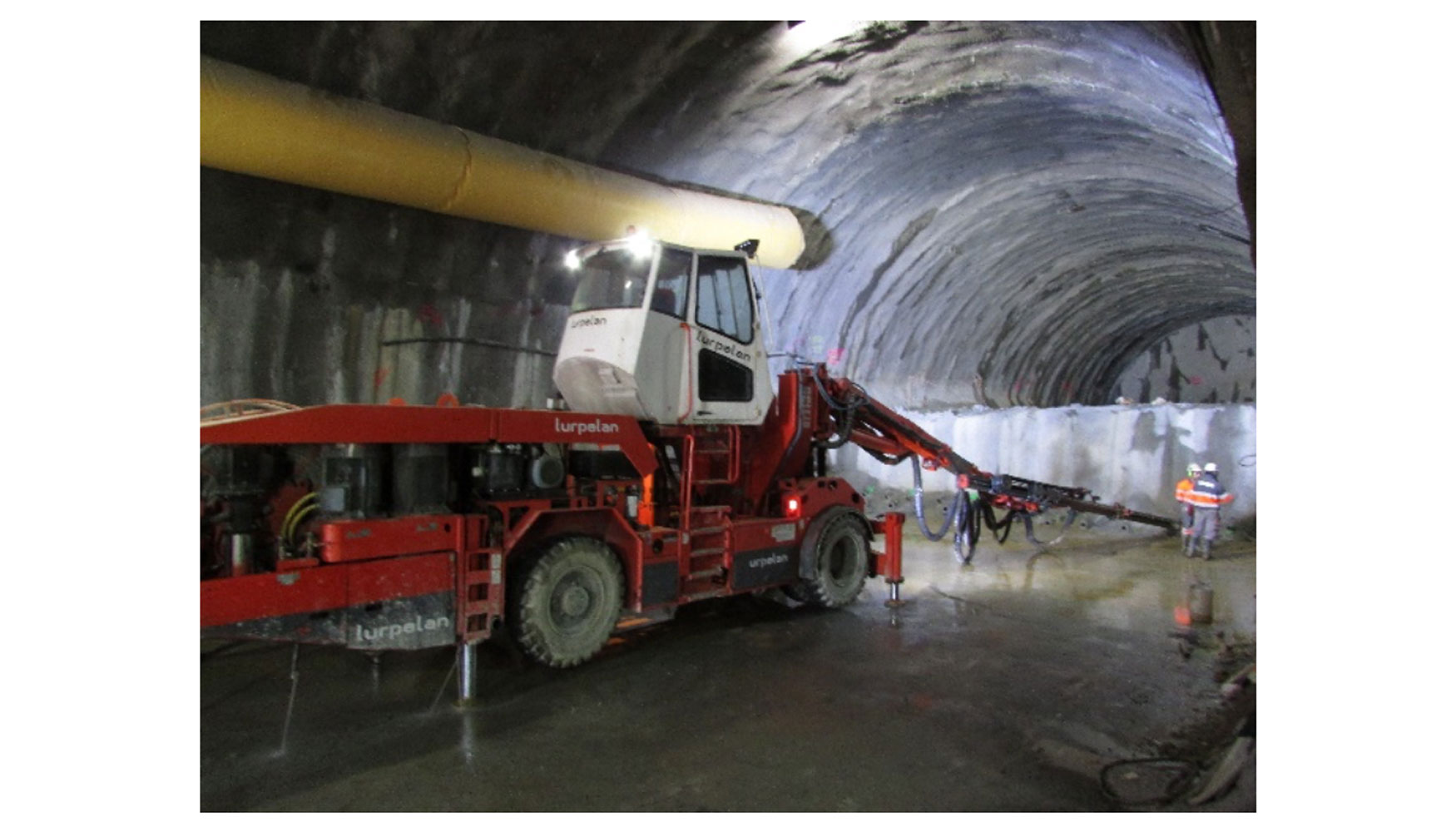
Ilustración 9. Trabajos de perforación con el Jumbo DT11.
Conclusiones
La ejecución del Túnel Urdinbide ha supuesto una hito excepcional para las obras de la BI-635. Se requerían y se obtuvieron elevados ritmos de producción. Se tuvo que flexibilizar el método constructivo debido a la aparición de infiltraciones de agua mayores de lo esperado, y se hizo imprescindible el empleo de inyecciones. Lurpelan ha sabido responder ágilmente a los altos requerimientos exigidos por los técnicos responsables de Interbiak y en estrecha colaboración con el equipo humano de Interbiak, se ha podido completar este túnel de forma satisfactoria y con una calidad óptima.
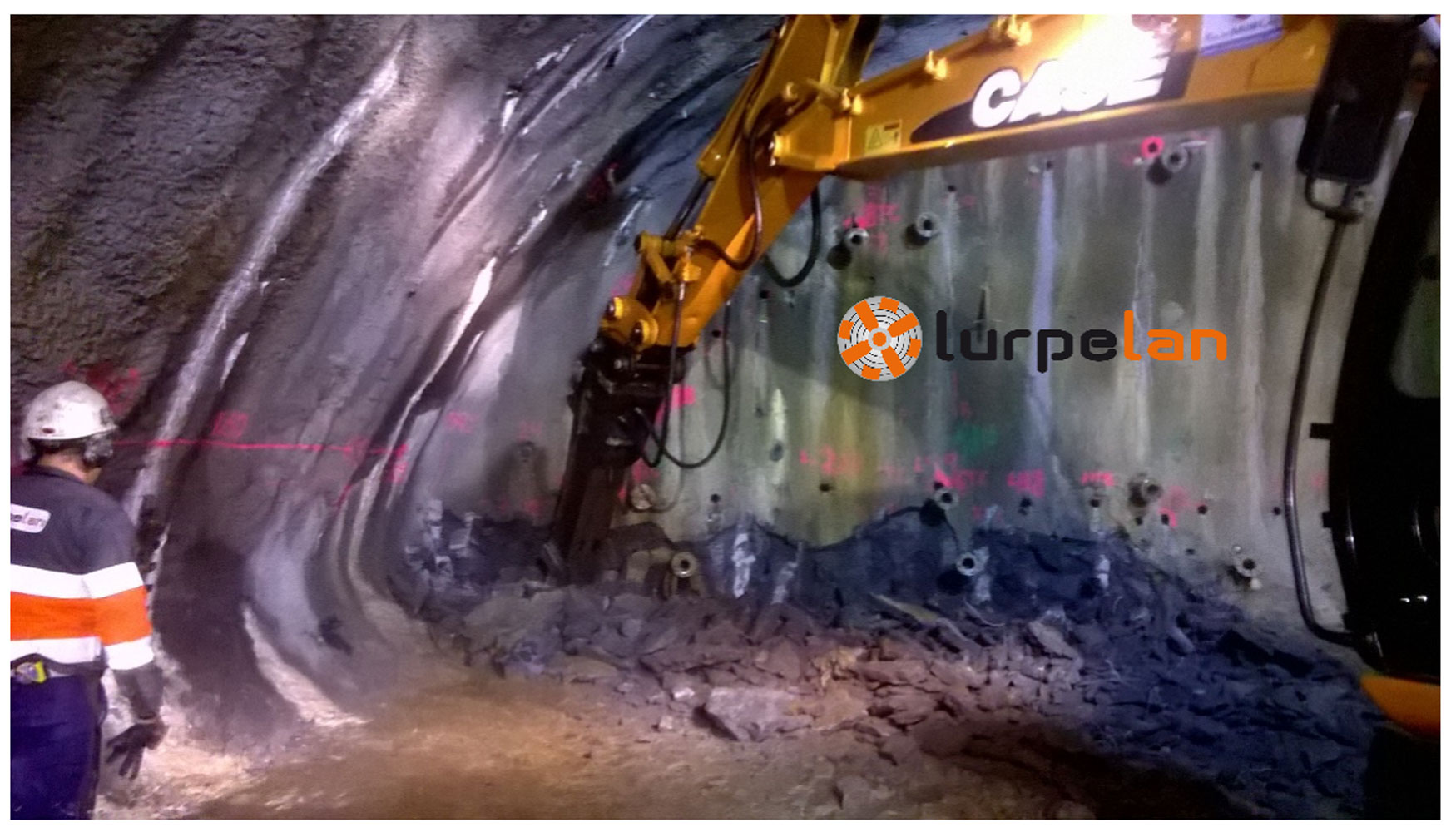
Ilustración 10. Trabajos de excavación posteriores a impermeabilización de túnel.
En la fotografía podemos observar el control y la supervisión de trabajos por parte de los capataces del equipo de Lurpelan, muestra del buen trabajo realizado. Este tipo de infraestructuras requieren un esfuerzo reseñable durante toda su ejecución, pero ésta en particular, por sus especiales condicionantes. Fue maquinaria técnica de tipo minero adaptada por fabricación a las condiciones duras de trabajo de las obras subterráneas.
Con este artículo queremos agradecer a Manuel Arlandi y Alberto Bernardo, asesores de la obra subterránea, a Miguel Gil y Eduardo Casado como director de Obra de Interbiak y adjunto respectivamente, y a Andoni Alkorta como responsable geotécnico de Interbiak, todas las aportaciones realizadas para la ejecución de la obra.