Satisfaciendo necesidades
Departamento técnico de A. Bianchini Ingeniero S.A. (Maccaferri Group)
19/09/2019El crecimiento de la población y las exigencias de las economías modernas son actores clave en la necesidad de inversión en infraestructuras. Cuando en la construcción de infraestructuras se ha tenido que hacer frente a la presencia de terreno blando o desfavorable, la aplicación de mejoras tradicionales tales como terraplenes pilotados o losas aligeradas han sido soluciones recurrentes. Sin embargo, la creciente importancia de considerar los rendimientos a largo plazo y los costes globales, ha conllevado que alternativas como los geosintéticos de refuerzo tengan cada vez más potencial.
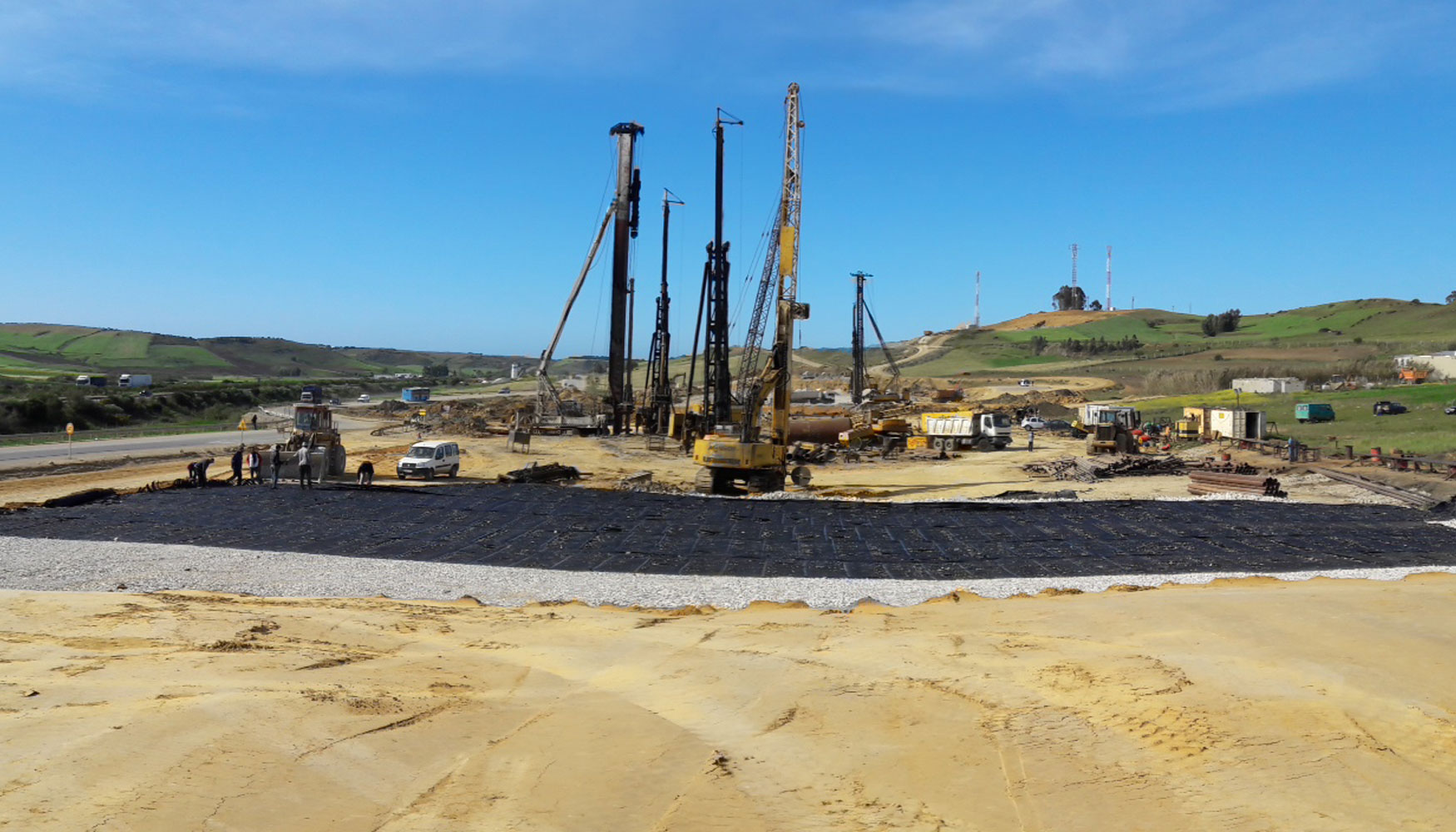
El uso de geosintéticos en la construcción no es nuevo, pero está adquiriendo progresivamente una mayor aceptación en la práctica. No obstante, debe hacerse una clara distinción entre la estabilización de suelos y el refuerzo de suelos anteriormente mencionado. La estabilización de suelos consiste en una estabilización superficial a corto o medio plazo de los materiales que conforman caminos de acceso o carreteras. Este refuerzo se hace mediante el uso de geotextiles, y muy a menudo, geomallas extruidas, con el objetivo de mejorar la capacidad de distribuir las cargas. Para el diseño de la estabilización de suelos se siguen prácticas que forman parte de un rango de procedimientos similares ampliamente aceptados y formulados por profesionales con experiencia en el sector.
En cambio, el refuerzo de suelos consiste en un refuerzo estructural del terreno a largo plazo, en el cual es necesario el rendimiento continuo de los geosintéticos que se emplean hasta el fin de la vida útil de la estructura. Los criterios de diseño siguen normas internacionalmente aceptadas, como la BS8006.
Los primeros productos geosintéticos y geomallas de la gama ‘Para’ se fabricaron en Yorkshire durante los años 70 y fueron desarrollados a partir de fibras ICI. Desde entonces, se han llevado a cabo mejoras continuas en la fabricación de las fibras y en los recubrimientos de protección. En el 2006, Maccaferri compró Linear Composites. Esto dio a ParaLink una plataforma mundial más amplia y actualmente sus productos son reconocidos como refuerzos geosintéticos de alta resistencia empleados en la construcción de terraplenes sobre terreno blando, pilotes y cavidades con exitosas aplicaciones a nivel mundial.
Terreno blando
En lugar de extraer y reemplazar grandes volúmenes de terreno en la cimentación de un terraplén, o bien de proceder con aplicaciones de mejora del terreno a lo largo de una gran extensión, el ParaLink se utiliza a menudo para proporcionar una alternativa y una solución rentable para el apoyo de terraplenes sobre terreno blando.
Este tipo de soluciones se ha utilizado y especificado ampliamente en diversas regiones de Europa. Algunos de los trabajos recientes más relevantes son el Puerto de Belfast y la construcción de la pasarela del puente de Mersey. El Paralink también se ha utilizado para el proyecto de la Blue Water Island en Dubai.
Para el diseño de terraplenes sobre terreno blando con Paralink, se emplean los factores parciales que proporciona la BS8006. La resistencia de la geomalla se selecciona de modo que se verifique la estabilidad del terraplén por falla debida al corte, la rotura circular, el deslizamiento de la base y la estabilidad global.
Sobre pilotes
Paralink permite que las cargas verticales de un terraplén puedan transferirse más eficientemente a los pilotes y proporcionar confinamiento lateral. Comparando una solución en la que se emplee ParaLink con una aplicación convencional, esta última requeriría que las cabezas de los pilotes fuesen más grandes y el espaciamiento entre elementos menor.
Algunas aplicaciones recientes incluyen la nueva carretera de circunvalación Tinsley Link a Sheffield, la rampa de acceso al estadio Olympic de Lonres y un viaducto ferroviario elevado a Reading (Reino Unido). De entre los casos prácticos de más relevancia encontramos en este campo la nueva línea de alta velocidad de Kenitra a Tánger en Marruecos.
Cavidades
Las cavidades pueden ser consecuencia de la presencia de cavernas subterráneas generadas por procesos naturales tales como la erosión en áreas cársticas o la disolución de zonas yesíferas, o bien por la acción del ser humano en procesos como la minería subterránea.
En estas áreas, el ParaLink puede emplearse en la base de los terraplenes para prevenir el colapso repentino del terraplén hacia el vacío, así como para limitar las deformaciones excesivas que podrían aparecer en la superficie durante la vida útil de la estructura. La geomalla debe estar en funcionamiento durante los 120 años de vida útil de la infraestructura que está soportando. El diseño y análisis aplicando la BS8006 indican que la deformación óptima de la geomalla se encuentra normalmente en el intervalo del 3 y el 6%, y que un refuerzo con una deformación última a corto plazo comprendida entre el 8 y el 14% es la que mejor se adapta a esta aplicación. La fabricación de una geomalla muy rígida, con una deformación última - inferior al 8% - es técnicamente posible, pero desafortunadamente no es compatible a nivel de deformaciones con el terreno al que está reforzando, y resulta en una menor contribución por parte del terreno y en la necesidad de una geomalla de más resistencia para ofrecer el mismo soporte.
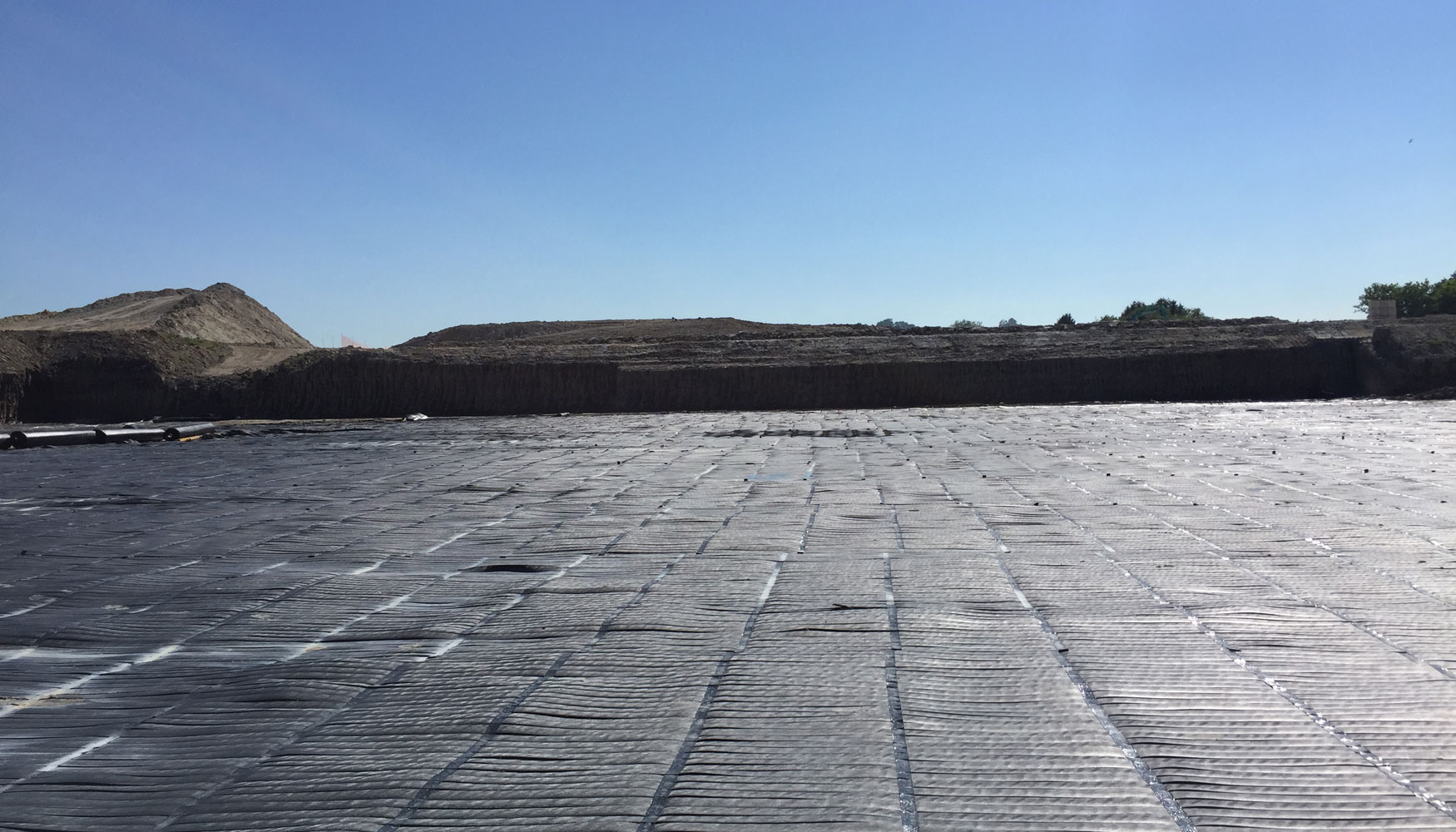
El diámetro máximo de cavidad que puede abarcarse depende de la resistencia última a la tracción a corto plazo, así como de la deformación máxima permitida en la geomalla para controlar las deformaciones en superficie. Una ratio óptima entre ‘la altura del terraplén y el diámetro de la cavidad’ es generalmente cercana a la unidad. Para estos tipos de aplicaciones siempre se recomienda ampararse en materiales que hayan sido rigurosamente ensayados y certificados por autoridades nacionales independientes.
En regiones propensas a los terremotos, el ParaLink se utiliza como medida correctiva del fenómeno de licuación del terreno. En estas zonas, las normas de diseño locales se han desarrollado para proporcionar medidas atenuantes por la mitigación del desastre, como por ejemplo poder garantizar la obtención de vías de transporte de emergencia.
A la práctica, a menudo es imposible adoptar métodos de mejora del terreno convencionales para abordar este fenómeno ya que el coste es muy significativo. Sin embargo, se ha desarrollado una simple medida atenuante para la licuefacción del terreno que puede implementarse con un coste limitado y que consiste en la colocación de una geomalla ParaLink intercalada entre 2 capas de gravas. Si bien muchas de las aplicaciones mencionadas podrían haberse resuelto utilizando métodos tradicionales, la utilización de refuerzos geosintéticos ofrece grandes beneficios en términos de coste, tiempo y sostenibilidad.
Software MacBars
El software de Maccaferri MacBars es una herramienta popular para el diseño de refuerzo basal que sigue los criterios de la BS8006:1-2016. El usuario puede determinar la carga del refuerzo utilizando la fórmula de Maston o el método de Hewlett i Randolph.
El programa también calcula las longitudes de anclaje que se requieren para el refuerzo y estima la carga vertical en los pilotes. Las características del material y los factores parciales para la gama de refuerzos ParaLink se extraen del nuevo certificado BBA 03/4065.
Con una vida útil de 120 años, el ParaLink tiene los factores parciales más bajos de entre los refuerzos presentes en el mercado. Esto se debe a su revestimiento altamente resistente que protege las fibras del polímero que proporcionan el refuerzo.
El hecho que el material presente factores parciales bajos en los daños por instalación, resistencia química y fluencia implica que, en la determinación de la resistencia a largo plazo (LTDS), en la cual interviene la resistencia última del refuerzo, (UTS), se obtienen valores superiores con respeto a otros productos con la misma UTS. Por ejemplo, un ParaLink de grado 1.500 (UTS=1508 kN/m) colocado sobre grava a 20°C de temperatura de diseño tiene una LTDS de 999,59 kN/m. Un geosintético con una UTS similar de 1.500 kN/m, pero con factores parciales menos favorables podría alcanzar únicamente una LTDS de 777,11 kN/m. Esta diferencia del 22% en la resistencia de diseño a largo plazo obliga al diseñador a tener que seleccionar un producto con una UTS superior y un coste adicional para alcanzar la LTDS satisfactoria para la estructura.
Finalmente debe tenerse cuidado en asegurar que el producto seleccionado podrá adaptarse a las condiciones medioambientales que cabe esperar durante su uso, por ejemplo, algunos tipos de polímeros tiene rendimientos distintos en condiciones de humedad.