Reparación del Túnel de Monte Areo en la falla de Veriña, Asturias
1.- Introducción
El túnel entró en servicio en octubre de 1997 y a los pocos años de la puesta en funcionamiento se puso de manifiesto que la zona de la falla de Veriña no se encontraba estabilizada. En 2000, se realizaron unas columnas de ‘jet grouting’ en la solera de la zona donde el túnel atraviesa dicha falla, y con posterioridad se fueron realizando obras de refuerzo como el aumento del espesor del hormigón proyectado y reconstrucción de los drenajes del túnel. A pesar de las mismas, el terreno fue agotando el sostenimiento y, en la zona de contacto de la falla con las cuarcitas, se produjo el colapso parcial de la sección reforzada.
El Departamento de Transportes Internos de ArcelorMittal, usuario final del túnel, ha venido vigilando la evolución de esta sección conflictiva, de unos 60 m de longitud. En el año 2009, este departamento encargó una primera inspección del túnel a Geocontrol, que se repitió en el año 2015. Se obtuvo de esta manera una imagen clara de la evolución temporal de su estado. En concreto, la zona afectada por la falla de Veriña mostró su estado de conservación más crítico y con evidentes muestras de continuar deformándose a pesar del tiempo transcurrido desde su construcción.
ArcelorMittal y Geocontrol contaban con la experiencia del cercano túnel de Tabaza II, donde se detectó y se corrigió un fenómeno de fluencia durante la construcción. Apoyados en esta experiencia y con objeto de cuantificar las velocidades de deformación del terreno en la falla de Veriña, en mayo de 2015 se colocaron 7 secciones de convergencia que, medidas durante 6 meses, confirmaron la fluencia con velocidades de convergencia entre 0,024 mm/día y 0,087 mm/día. Como orden de magnitud, en el Túnel de Tabaza II, en 2009, se estaban midiendo en las zonas críticas velocidades de 7 mm/año (0,019 mm/día) cuando se decidió cerrar la sección con una contrabóveda, reduciéndose así las velocidades de convergencia a 2 mm/año (<0,01 mm/día).
Tras constatar la fluencia, ArcelorMittal encargó a Geocontrol la redacción del proyecto constructivo para la reparación del Túnel de Monte Areo en la falla que fue terminado de redactar en abril de 2016.
La programación del proyecto aprovechaba la oportunidad de una parada total en la factoría de 12 días en noviembre de 2016, y algunos días de parada nocturna antes y después. Las obras se licitaron en julio de 2016 con el fin de realizar los trabajos entre octubre y diciembre de 2016; resultando adjudicataria Acciona Infraestructuras S.A.
La solución de proyecto contemplaba la construcción de 15 m de contrabóveda y el refuerzo con hormigón proyectado y anclajes autoperforantes en una longitud de unos 60 m. Al inicio de las obras, tras demoler un carenado de chapa que se montó tras la construcción en la zona del paso de falla, se detectó un gran hueco tras las cerchas del sostenimiento en el hastial derecho, en el inicio de la zona de falla de Veriña. La solución técnica al mismo y los condicionantes diarios de explotación de la línea, sumados al ya de por sí ajustado plazo, han marcado la ejecución real en obra que se describe a continuación en este artículo.
2.- Modelo geológico de la falla de Veriña en su intersección con el Túnel de Monte Areo
Uno de los problemas con que hubo que tratar al hacer el proyecto constructivo, fue la escasa información ‘as built’ disponible. Apenas la estratigrafía, el RMR y los ratios de avance estaban disponibles para poder diseñar el refuerzo. Por otro lado, el túnel es vital para el funcionamiento de las factorías y la realización de reconocimientos geotécnicos que impliquen la parada era un asunto a evitar. Por ello, el modelo que se describe a continuación, corresponde mayormente a lo registrado durante las obras de reparación.
Desde el PK 11+846 hasta el PK 11+900, el túnel atraviesa terrenos muy tectonizados pertenecientes a la denominada falla de Veriña, donde argilitas muy fracturadas, y arcillas que presentan procesos de fluencia entran en contacto con cuarcitas.
El desarrollo de las obras ha permitido definir el modelo geológico de la falla de Veriña al paso del túnel. El resultado se muestra en las Figuras 2.a a la 2.c, tanto en croquis en tres dimensiones como en planta y alzado. Básicamente se han detectado dos fallas con contacto mecánico, observándose una mejora de las propiedades geomecánicas de las argilitas conforme avanza la progresiva del túnel.
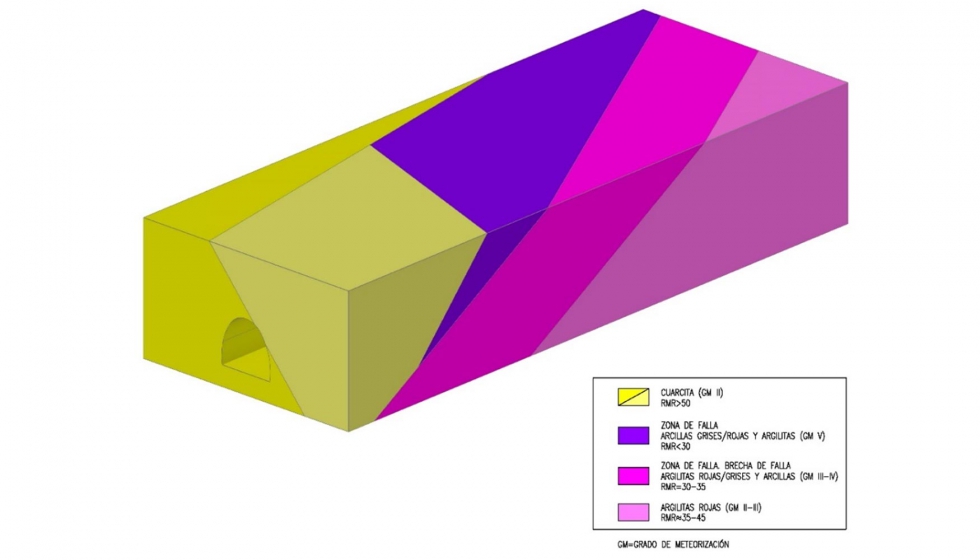
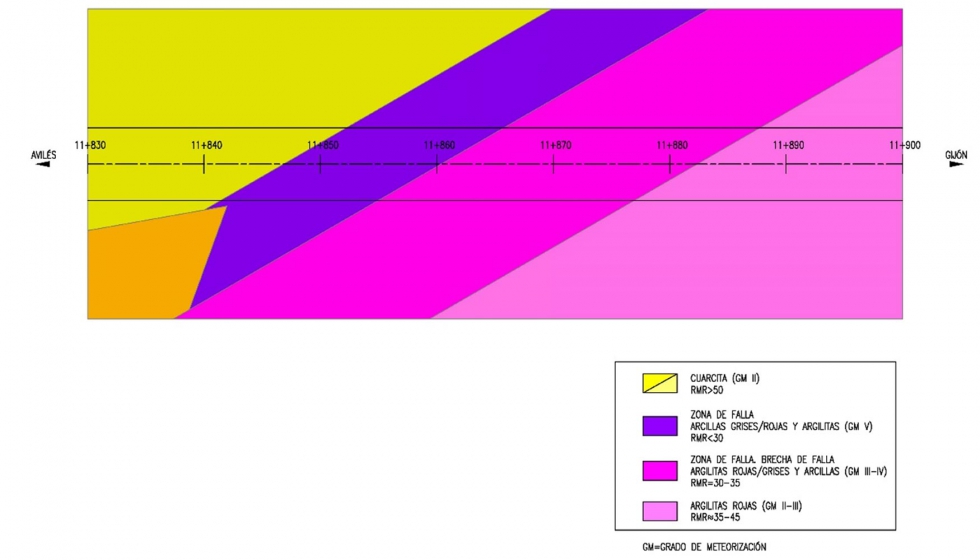
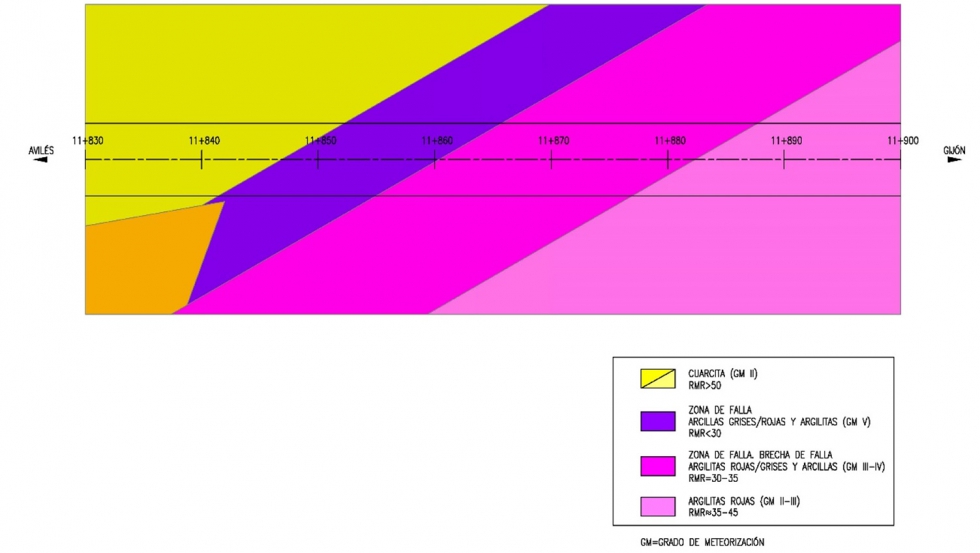
Conforme la progresiva del túnel se aleja de la zona de contacto entre ambos comportamientos geomecánicos tan contrastados, las argilitas van mejorando su condición geomecánica, reflejada en su aumento del RMR desde valores de 20-30 a valores del entorno de 35-45.
3.- Diseño de la solución constructiva, Pk 11+835 a 11+885
Para analizar la efectividad de las posibles alternativas de reparación, se empleó la modelización numérica, calibrando el comportamiento del terreno a partir de los pocos datos existentes en el ‘as built’ y las convergencias medidas en las inspecciones. La Figura 3.a muestra en planta la zona a reparar y las estaciones de convergencia empleadas para ajustar el comportamiento.
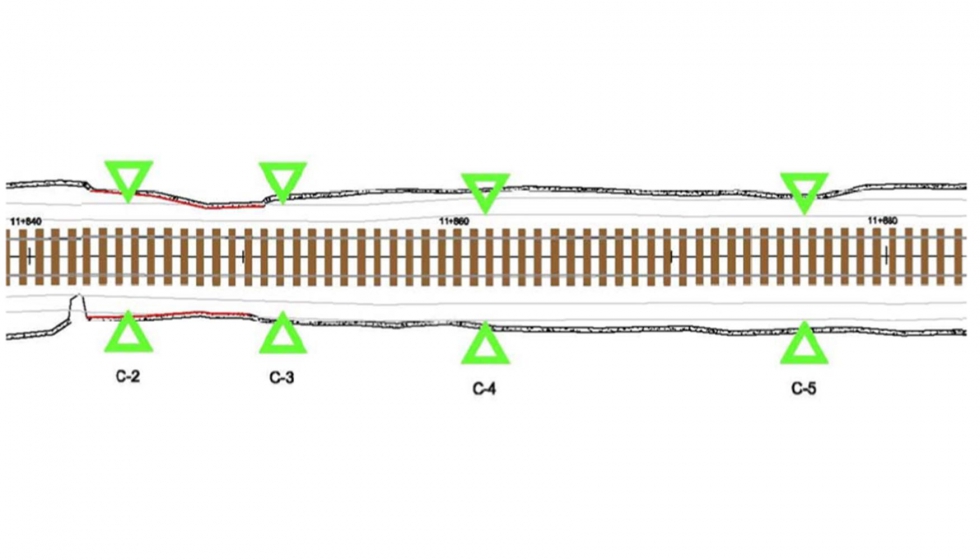
La Figura 3.b muestra la sección teórica empleada en la zona de la falla de Veriña durante la construcción del túnel.
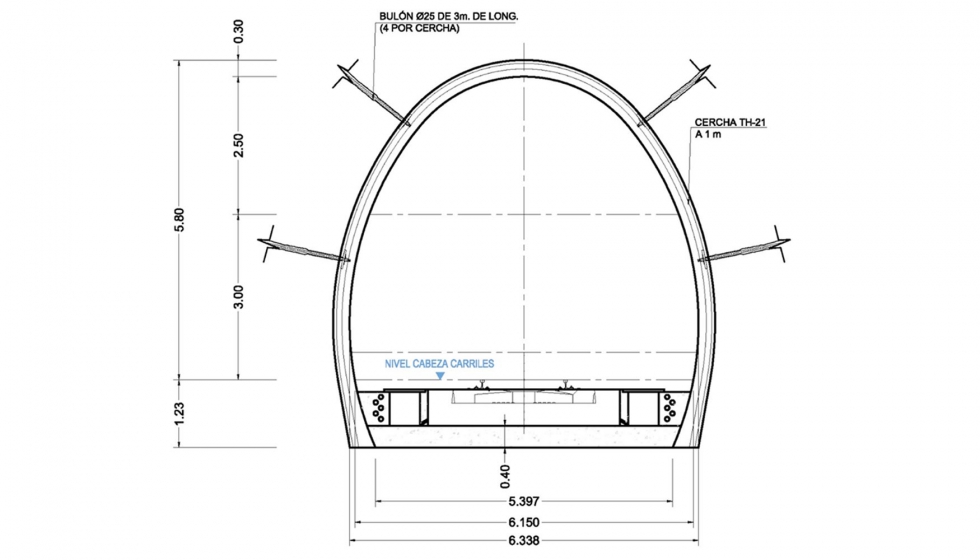
El modelo constitutivo del terreno de la falla considerado en los modelos numéricos considera el comportamiento tiempo-dependiente observado en el túnel y, además de las propiedades resistentes y elásticas habituales, precisa determinar los parámetros A y n del material en la ley potencial que define la velocidad de fluencia o ‘creep’.
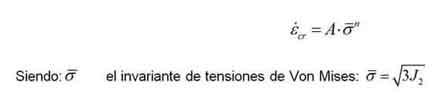
Para determinar sus valores, se ha hecho un ajuste de las propiedades del terreno más verosímiles con la ayuda de un proceso de análisis retrospectivo considerando finalmente los que se muestran en el Cuadro 3.I:
Módulo de Young (MPa) | Coeficiente Poisson | Cohesión (MPa) | Ángulo Fricción (º) | Resistencia a tracción (MPa) | K0 | Recubrimiento (m) | A | n |
270 | 0,3 | 0,19 | 25 | 0,02 | 1,0 | 120 | 2,7x10-29 | 3 |
El modelo ajustado de la falla permitió determinar la efectividad de los refuerzos y tramificar su aplicación a lo largo de la zona de actuación.
Esta efectividad, pudo expresarse en función del tiempo de vida útil, ya que el modelo de cálculo empleado explícitamente considera el tiempo en la formulación. Esto fue una ventaja a la hora de tomar decisiones sobre costo/beneficio de las distintas alternativas consideradas.
En el Cuadro 3.II se muestran las diferentes soluciones adoptadas.
Refuerzo | Descripción del refuerzo |
A | Hormigón proyectado (9 cm) |
B | Bulones autoperforantes de 9 m en hastiales (3 cada metro) |
C | Bulones autoperforantes de 9 m en hastiales (2 cada metro) |
D | Bulones de redondo de acero corrugado de 3 m en hastiales (4 cada metro) |
E | Contrabóveda |
En general, se han tenido que considerar de forma conjunta dos o tres de los refuerzos para llegar a obtener el comportamiento buscado, como se muestra en el Cuadro 3.III.
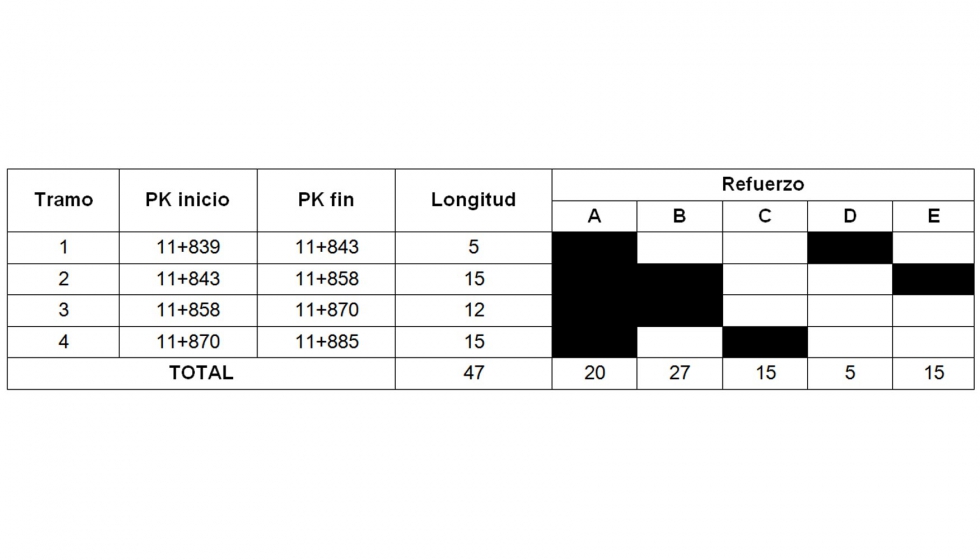
La efectividad de los sostenimientos alternativos se ha evaluado en función de las tensiones calculadas sobre el hormigón, o el acero de los pernos, en función del tiempo transcurrido desde la reparación. En las Figura 3.c y 3.d se muestran a modo de ejemplo las salidas gráficas de los momentos flectores sobre el refuerzo de hormigón proyectado y las fuerzas de tracción en los pernos del modelo de cálculo, en la previsión a 30 años, que fue el horizonte considerado por ArcelorMittal.
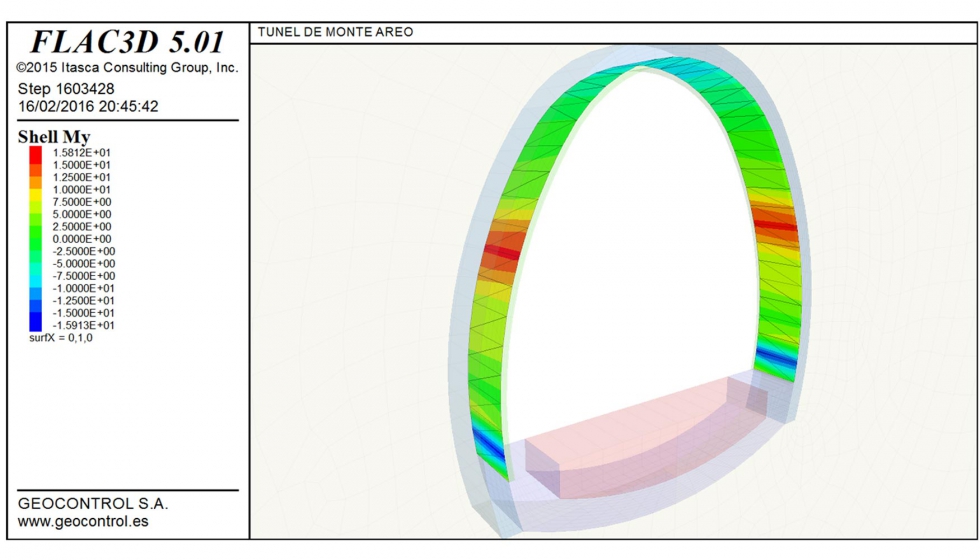
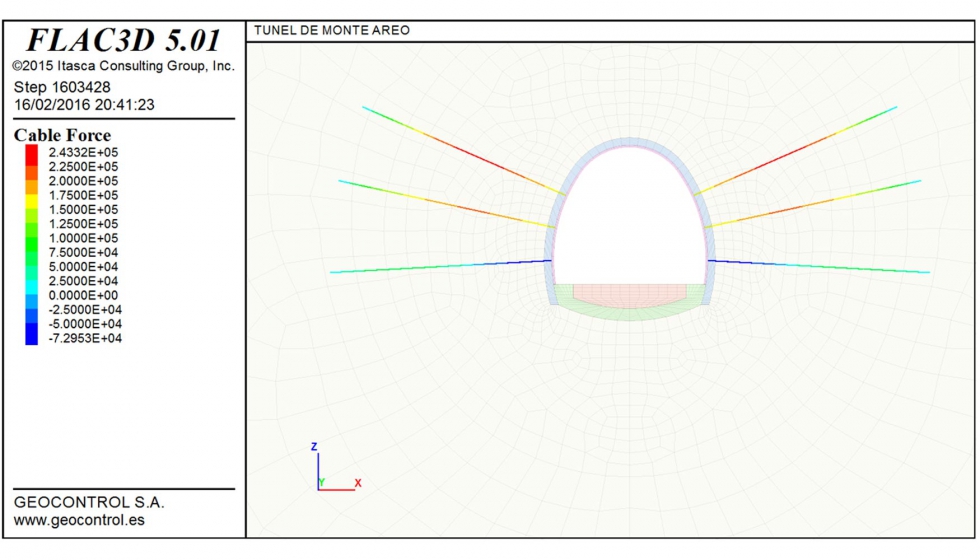
4.- Fase de ejecución de obra
El cronograma de las obras quedó encajado dentro de la disponibilidad de ArcelorMittal, en tres periodos seguidos: 39 días con paradas parciales nocturnas de 6-7 horas de trabajo efectivo, 12 días de parada total (24 h) y 13 días con paradas parciales nocturnas de 6 h de trabajo efectivo.
Además, se pudo contar con una parada de 16 horas el 31 de agosto de 2016 donde se debían recopilar datos faltantes que no había sido posible obtener durante la etapa de proyecto y realizarse varias tareas preparatorias para la parada: tendido de cable eléctrico de suministro y cuadro de obra, desmontaje de las chapas que ocultaban el sostenimiento justo en la zona de la falla (Fotografía 4.a), georreferenciación, medidas de seguridad e higiene, etc.
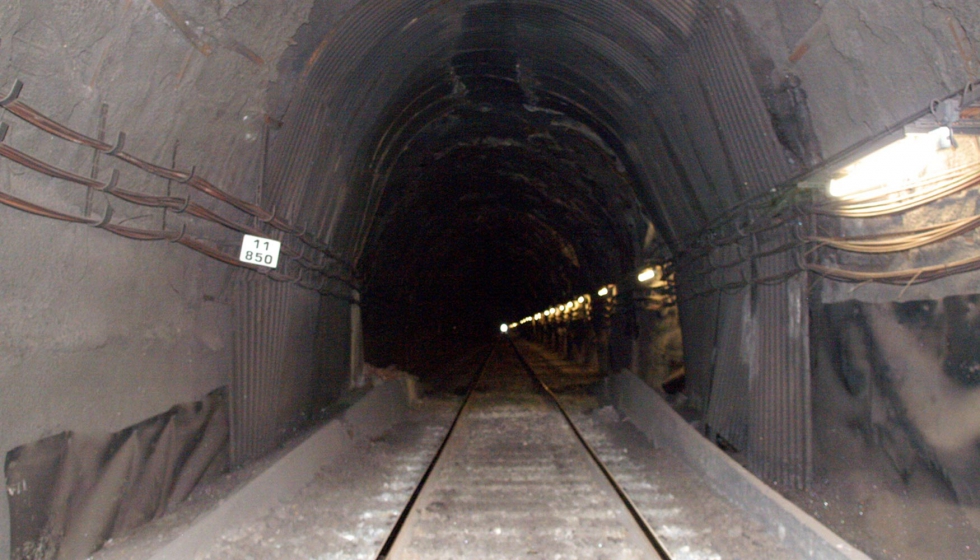
Tras el concurso de licitación en el que resultó adjudicataria Acciona Infraestructuras S.A., y el periodo de negociación del contrato, se iniciaron los trabajos previos en el exterior: documentación de planificación, seguridad y calidad, casetas de obras, aprovisionamiento y adecuación de los accesos. También se instaló un decantador para las aguas del túnel y evitar así verter sólidos al cauce existente del río Aboño, que transcurre por el lado de la boca de Gijón.
Igualmente, se realizaron los trabajos previos previstos en la parada del 31 de agosto y, finalmente, se iniciaron los trabajos propiamente dichos de reparación la noche del 6 de octubre de 2016.
4.1. Corroboración del mal estado del sostenimiento en la zona de falla y reajuste del programa de trabajos
Durante las inspecciones que se pudieron hacer previas al proyecto, ya se había constatado la baja resistencia (apenas 20 MPa) del hormigón proyectado por vía seca del túnel. También se habían mapeado las grietas, la oxidación de elementos metálicos expuestos, la falta de grapas de las cerchas THN-21 y otros daños puntuales por agua y calor.
En la fase de proyecto, la zona de falla estaba cubierta, como se ve en la fotografía 4.a, por una chapa metálica ondulada colocada desde el inicio de la fase de operación para que no se produjese el goteo de agua al paso de los vagones torpedos de arrabio, lo cual produce estallidos violentos, por reacción con el material fundido que transportan.
Sin embargo, una vez retiradas las chapas al inicio de las obras, se detectó que el estado del sostenimiento era mucho más precario que lo supuesto y se encontraba hasta 1,5 m separado del terreno (Fotografía 4.1.a).
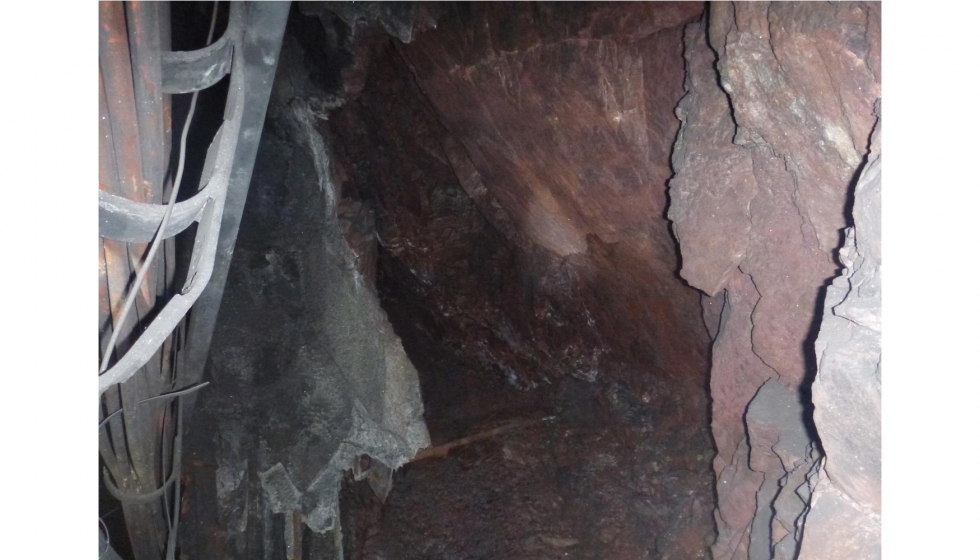
Analizada esta situación entre el contratista, la dirección de obra y la propiedad, se decidió que no era posible el refuerzo en esta zona, de unos 7 metros, como se había previsto, esto es: proyectando sobre el sostenimiento existente hormigón. Tampoco los pernos autoperforantes podían ser efectivos en esas condiciones y se decidió que esta parte del túnel requería la sustitución de las cerchas THN-21 originales y la recuperación de la sección original. Se optó por el empleo de perfiles THN-29 más resistentes que los existentes.
Esto que en condiciones normales no plantea mayor dificultad, se convertía, por lo ajustado del plazo y las implicaciones para la producción de ArcelorMittal de no dar servicio a la vía en el momento necesario, en un reto por el incremento de obra y por los plazos de aprovisionamiento.
El hecho de sustituir cerchas y excavar, además, requiere un plazo de trabajo continuado mayor que las 6-7 horas disponibles durante los días de trabajo nocturno. Esto suponía que se debería reducir el tiempo disponible de la parada de 12 días para hacer esta tarea. Este asunto iba en detrimento de la construcción de contrabóveda que ya de por sí tenía un plazo muy ajustado para la construcción y su fraguado necesario ya que el peso que los vagones torpedo transmiten a la vía es de más de 40 tn por eje.
Ello obligó al contratista a planificar una serie de tareas, aprovisionamientos y obras auxiliares, como la ejecución de plataformas de encarrilamiento en ambas entradas del túnel lo que permitió disminuir los ciclos de trabajo de la maquinaria con diploris de movimiento de tierras de 50 a 30 minutos.
La Asistencia técnica de la Dirección de Obra autorizó además la sustitución del mallazo electrosoldado por fibras metálicas en el hormigón proyectado, con lo que se conseguía un ahorro de plazo y personal, que podía dedicarse a otras tareas y se restudió la secuencia de bataches de construcción de la contrabóveda prevista en proyecto.
Finalmente, ArcelorMittal reorganizó el tráfico ferroviario para poder contar con 56 horas de parada adicional entre el 25 y 27 de septiembre, durante la que se realizaron parte de las tareas de sustitución de cerchas.
4.2. Tratamientos de refuerzo en bóveda y hastiales
Estos tratamientos han comprendido la ejecución de pernos autoperforantes, el saneo de la gunita antigua, la proyección del hormigón proyectado nuevo y las labores de demolición del sostenimiento antiguo y reposición del mismo en su totalidad (cerchas y hormigón proyectado). A continuación, se sintetizan los detalles más reseñables de cada una de ellas.
Bulonado de los hastiales, mediante jumbo Atlas Copco Rocket Boomer 282:
- Bulones autoperforantes de 9 m de longitud, tipo MINOVA R32S de Rtracción > 260 kN. Para la inyección de los autoperforantes se utilizó lechada a/c 0.5, CEM I 52.5R con súper fluidificante de propiedades tixotrópicas, MasterRoc FLC100, al 6%.
- Bulones corrugados de acero corrugado Ø25 de 3 m de longitud, de Rtracción > 250 kN. La inyección se realizó mediante cartuchos de resina MINOVA tipo ST-90/1.
Los rendimientos diarios y los medios conseguidos se indican en la Figura 4.2.a.
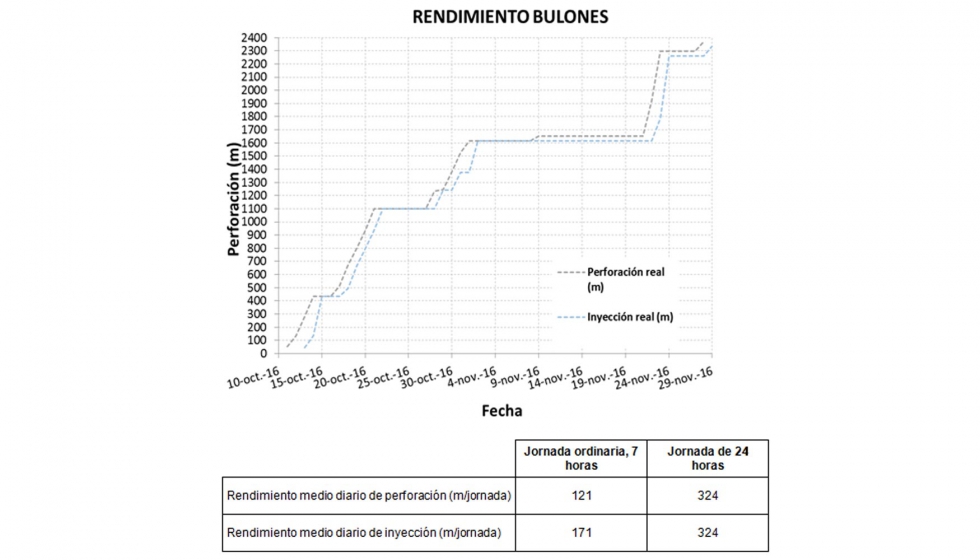
Saneo, limpieza del gunitado existente y proyección de 9 cm de hormigón proyectado con fibras metálicas:
- Saneo mediante retroexcavadora mini de 8 tn sobre orugas, con martillo rompedor acoplado.
- Limpieza con equipo de agua a presión con un rendimiento de 15 m/jornada (en jornada ordinaria de 7 horas).
- Proyección de hormigón con robot Putzmeister PM-500, alimentado mediante autohormigonera de 5 m3 articulada con diploris:
- Se proyectó hormigón HMP-35/P-RF/F/12-TF/IIa por vía húmeda con refuerzo de fibras metálicas tipo FIBRE 55/35 con una dosificación de 25 kg/m3 y fibra de polipropileno monofilamento para protección frente al fuego tipo SIKAFIBER M-12 con una dosificación de 2 kg/m3. El rendimiento alcanzado, fuera de la zona de estaje, fue de 18 m3/jornada (en jornada ordinaria de 7 horas).
Estajado del sostenimiento existente y reposición del sostenimiento del túnel del PK 11+843 al 11+849:
Esta labor se realizó en jornadas de 24 h. Pese a lo impermeable de los materiales excavados, en el contacto entre las cuarcitas y las argilitas se detectó abundante surgencia de agua, lo que dotaba a las arcillas de una rápida inestabilidad a corto plazo. Se colocaron cerchas THN-29 y se proyectó hormigón HMP-35/P-RF/F/12-TF/IIa por vía húmeda. El hormigón se reforzó, con fibras metálicas tipo FIBRE 55/35 con una dosificación de 25 kg/m3 y fibra de polipropileno monofilamento para protección frente al fuego tipo SIKAFIBER M-12 con una dosificación de 2 kg/m3. En total se colocaron 7 cerchas nuevas en sustitución de 7 cerchas antiguas demolidas, a las que hay que añadir 2 cerchas previas del PK 11+841 al 11+842, como pórtico de reacción necesario para la colocación del nuevo sostenimiento. Las cerchas se colocaron mediante plataforma Normet HIMEC 9910 B REX. El avance de dichos trabajos fue mediante pases de 1 m. Se detallan a continuación algunos de los rendimientos alcanzados:
- El ciclo de trabajo (demolición, excavación, desescombro, montaje y colocación de cercha y proyección de hormigón), obtuvo rendimiento medio de un 1 m/10 h.
- Se sirvieron para estas labores 140 m3 de hormigón. El rendimiento de proyección de hormigón en el estaje fue de 28 m3/jornada (jornada de 24 h).
En las Fotografías 4.2.b, 4.2.c, 4.2.d y 4.2.e se muestra la demolición del sostenimiento agotado, la colocación de las cerchas y el resultado final de dicha actividad.
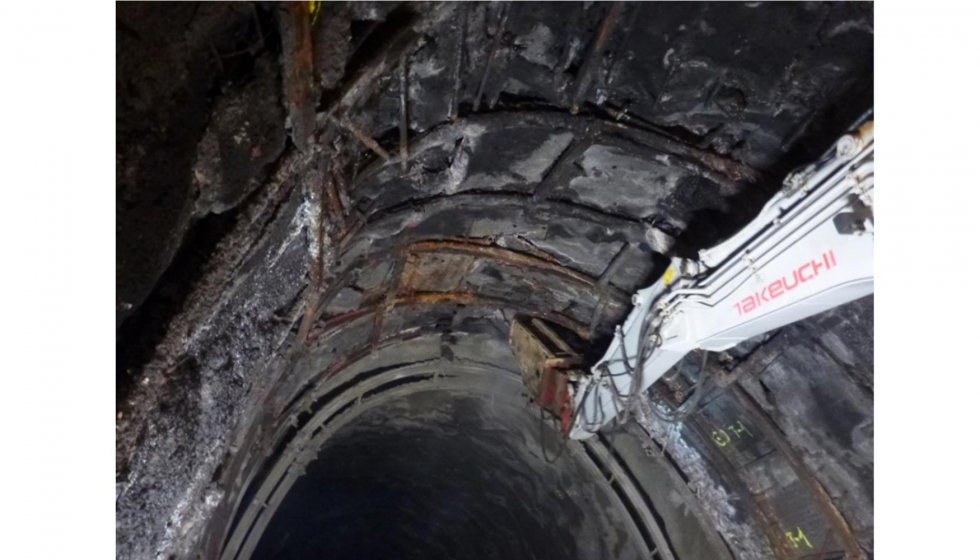
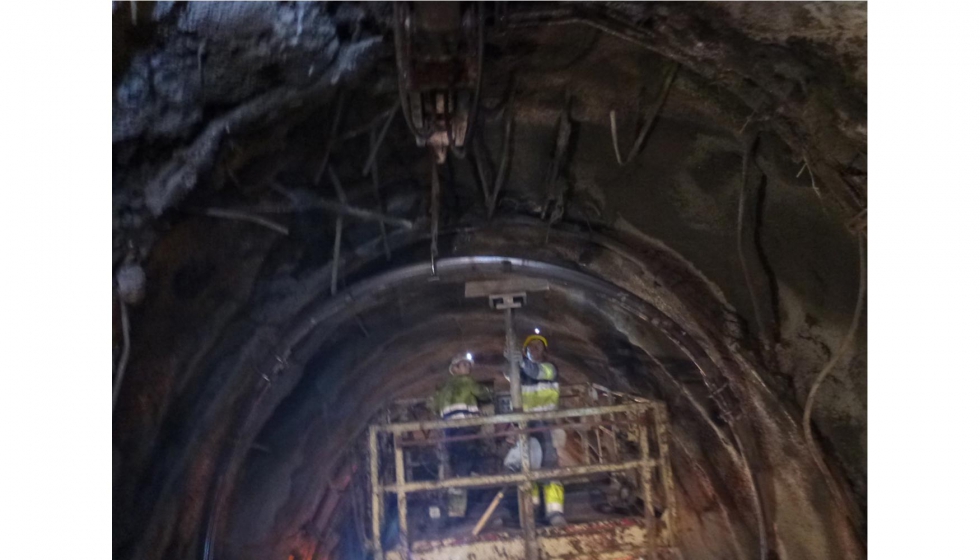
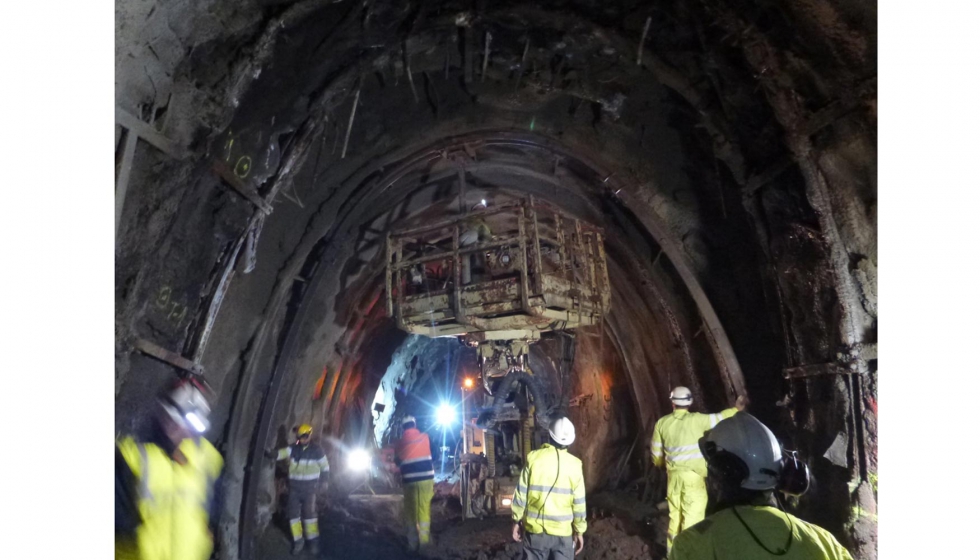
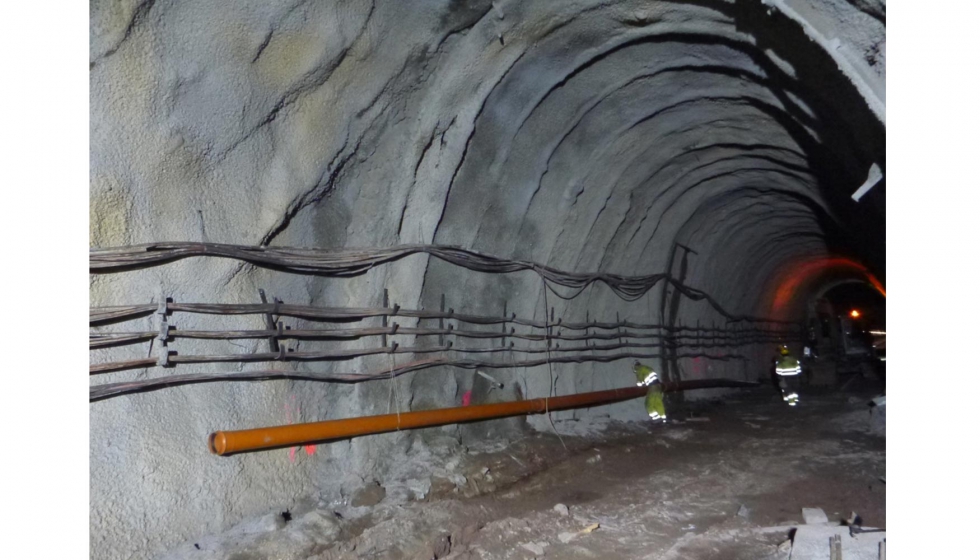
4.3 Contrabóveda de refuerzo de hormigón armado pk 11+843 a 11+858
Una vez colocadas las cerchas nuevas y desviada la red de drenaje del túnel, se ejecutó la contrabóveda en un único batache de 15 m de longitud.
A causa del hueco existente tras el sostenimiento antiguo del hastial derecho al inicio de la zona de falla, la contrabóveda se ha ejecutado del PK 11+842 al 11+850 al amparo del sostenimiento nuevo ejecutado (cerchas THN-29, bulones autoperforantes y hormigón proyectado) y desde el PK 11+850 al 11+857 al amparo del sostenimiento antiguo. A continuación, se reseñan las características principales de la construcción de la contrabóveda.
Excavación:
- La contrabóveda se excavó mediante medios mecánicos convencionales (retroexcavadora de orugas Takeuchi de 100 CV y 14 tn, provista de cazo y martillo). Los terrenos excavados fueron arcillas y argilitas meteorizadas en grado V. El rendimiento medio fue de 10,5 m3/h lo que permitió realizar la totalidad de los 128 m3 excavados en 12 horas (Fotografía 4.3.a).
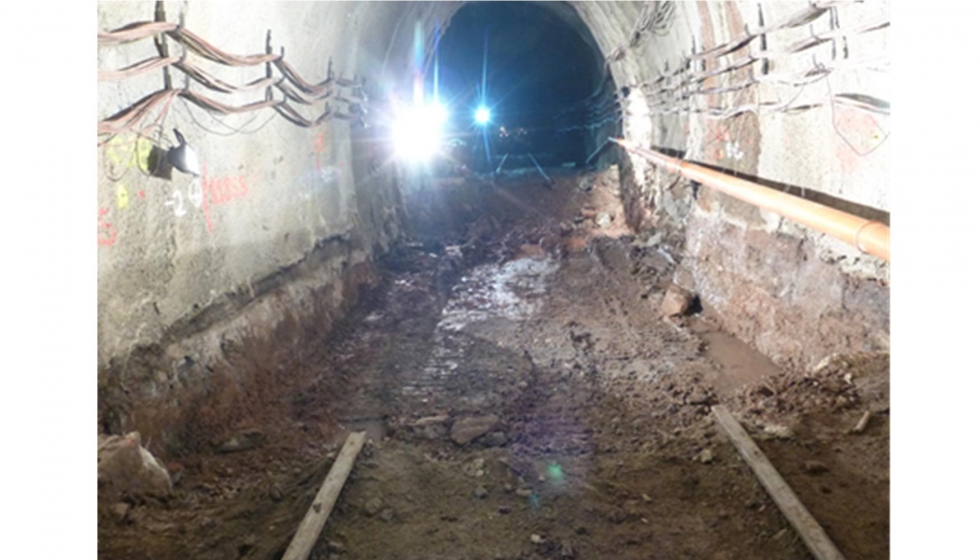
- A causa de la existencia de agua en el terreno se colocó una cama de balasto y bombas de achique de 7-12 CV. En la Fotografía 4.3.b se muestra la colocación de la cama de balasto.
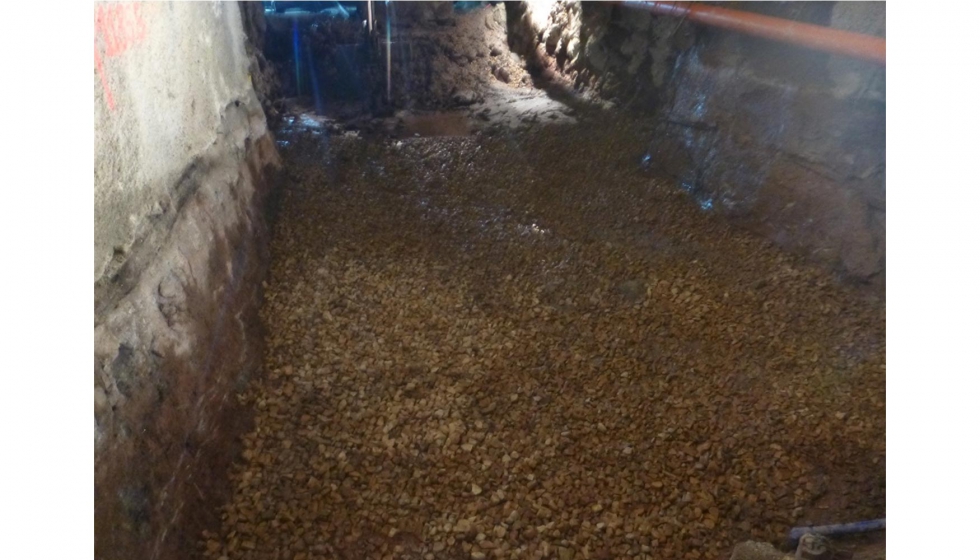
Ferrallado:
- Las armaduras pasivas previstas en proyecto para la solera de la contrabóveda, se sustituyeron por mallazo 150x150 Ø12 lo que permitió un montaje más rápido de las mismas.
- En la Fotografía 4.3.c se muestra el ferrallado de los tacones de la contrabóveda.
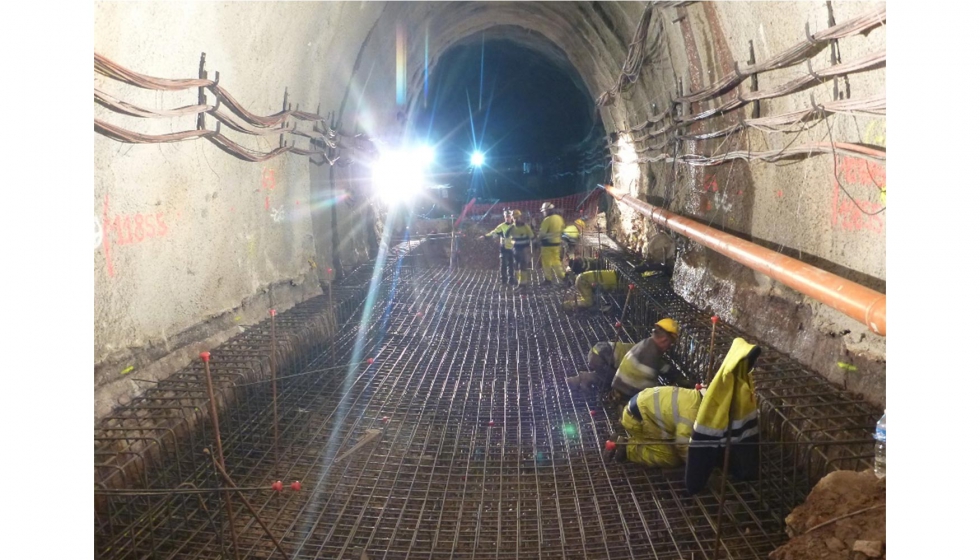
Hormigonado:
- Se usó el robot de Putzmeister PM500 como bomba para el vertido del hormigón. El rendimiento alcanzado fue de 7 m3/h.
- En la Fotografía 4.3.d y 4.3.e se muestra el hormigonado de la contrabóveda y de la capa de forma.
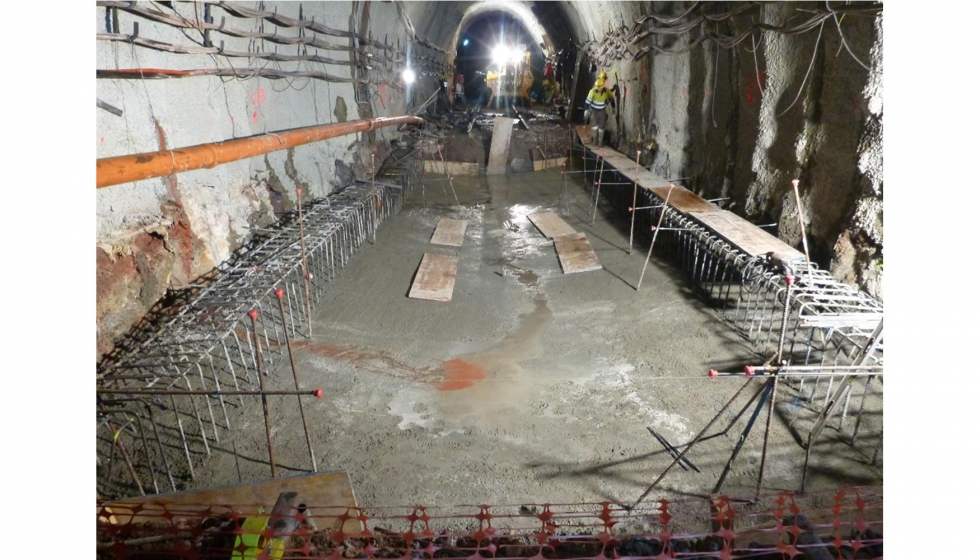
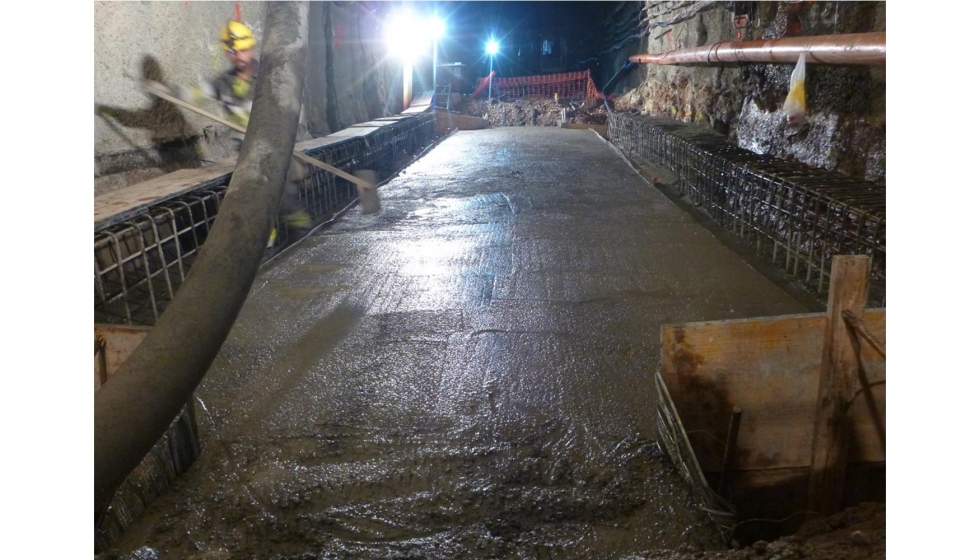
- Los encofrados la contrabóveda se ejecutaron con nervometal y madera. En la Fotografía 4.3.f y 4.3.g se muestran dichas labores.
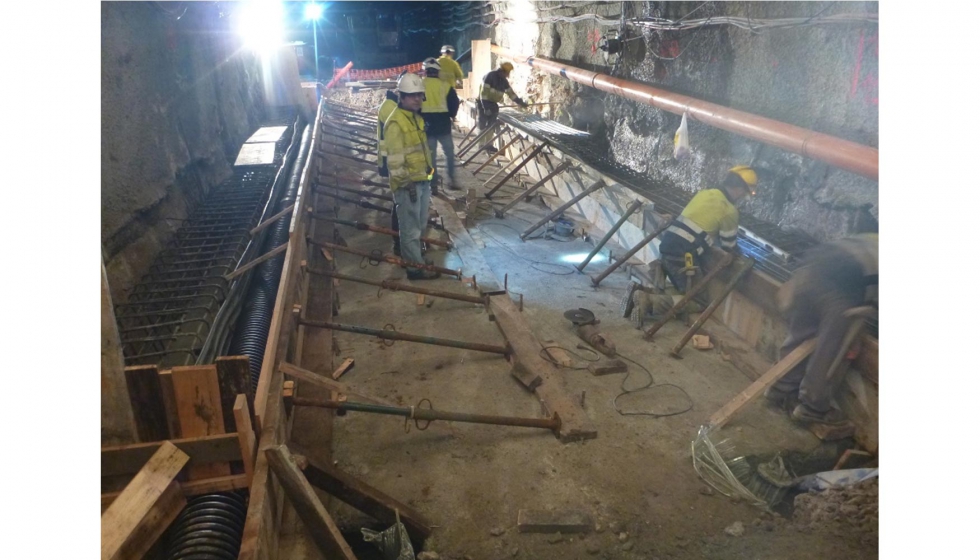
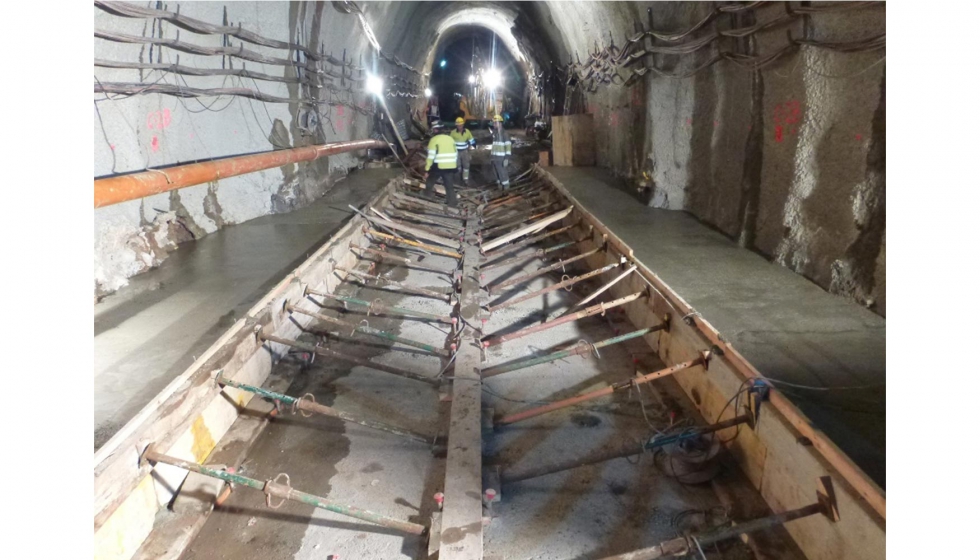
4.4. Drenes profundos en la zona de falla y zanja drenante en la boca de veriña del túnel
Se diseñó un sistema de drenaje profundo en los puntos detectados con mayor surgencia de agua al excavar el terreno en ambos hastiales del PK 11+843 al 11+858. Se ejecutaron mediante jumbo Atlas Copco Rocket Boomer 282. Los rendimientos en la perforación fueron de 13,5 m/h.
Se trata de perforaciones de entre 5 y 10 m de longitud y 72 mm de diámetro entubadas con tubería de PVC de 50 mm de diámetro y 3 mm de espesor, ranuradas, achaflanadas en cabeza y conectadas en su boca, mediante codos, con bajantes de tubería de P.E. corrugado flexible a canaleta de drenaje superficial. En total se han realizado 5 unidades en el hastial izquierdo y 4 unidades en el hastial derecho.
En la Fotografía 4.4.a se muestra la colocación de la tubería de drenaje en el interior de la perforación mediante plataforma elevadora. En las Fotografías 4.4.b y 4.4.c se muestra su conexión a la red de drenaje superficial del túnel mediante tuberías que desaguan en las canaletas y que finalmente conducen el agua a las arquetas.
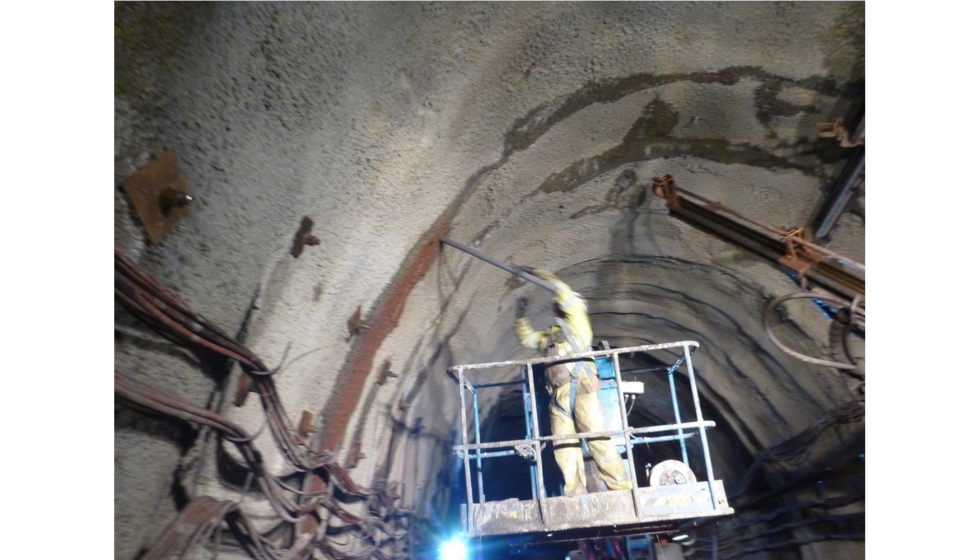
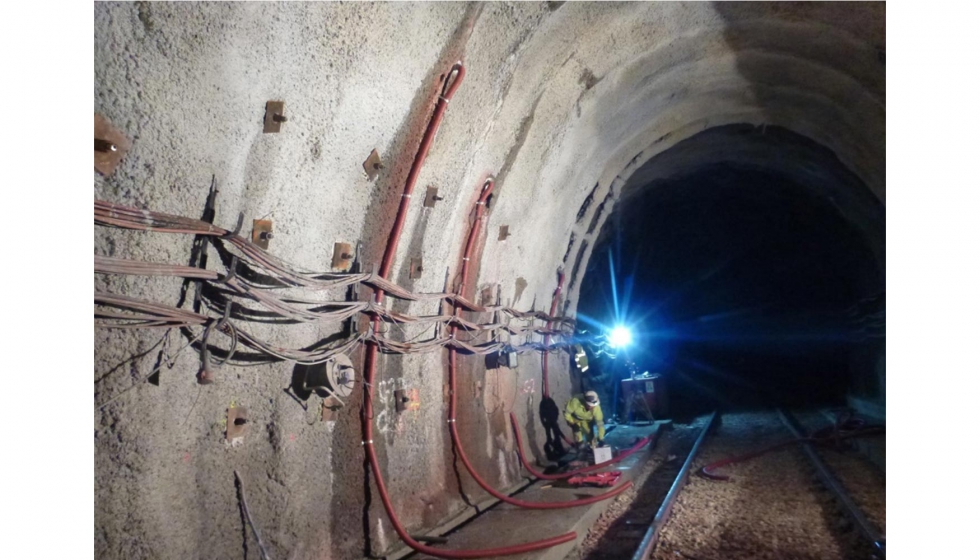
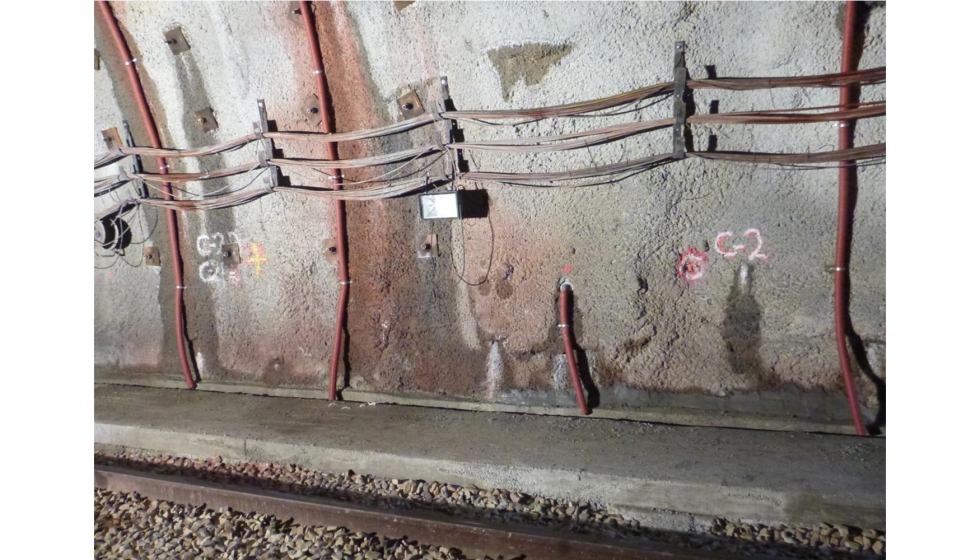
Cabe destacar el buen funcionamiento de los drenes ejecutados desde su perforación.
Por otro lado, concluidos los trabajos en la zona de falla y en vista del encharcamiento que se producía en la boca de Gijón del túnel en presencia de fuertes lluvias, se procedió a la ejecución de una zanja drenante que evacuara el agua de esta zona hacia el exterior. La zanja se compone de tubería de PVC 100, ranurada, envuelta en geotextil y colocada en el fondo de una excavación de altura 0,40-0,60 m, rellenada con balasto.
4.5. Instalaciones
Los trabajos se completaron con la ubicación definitiva de las arquetas de drenaje, condicionada por las canalizaciones existentes rotas, la ejecución de zanjas drenantes, la disposición de tuberías en las grietas del sostenimiento antiguo (para encauzar el agua del terreno a las nuevas arquetas), la revisión de los circuitos eléctricos de todo el túnel y la instalación de luminarias NEOS 2 32 LEDS óptica 5139 en la zona de la falla de Veriña.
5.- Conclusiones y lecciones aprendidas
Entre las conclusiones y lecciones aprendidas, cabe destacar:
- El estudio y la planificación cuidadosa en la fase de proyecto es necesaria en una obra subterránea de reparación. La capacidad de poder reaccionar a imprevistos durante la ejecución es función directa del tiempo dedicado en proyecto al estudio y la planificación.
- En espacios limitados, debe cuidarse la selección de maquinaria en función de su movilidad, optando siempre por la de mayor capacidad y flexibilidad posible. A la hora de considerar rendimientos, se debe disponer de todas las facilidades para aumentarlos, como maquinaria con diploris y plataformas de encarrilamiento.
- La aparición de imprevistos en este tipo de obras es de una probabilidad de ocurrencia muy elevada y, para afrontarlos con éxito se requiere la colaboración de todas las partes involucradas y la preparación técnica de los participantes.
- Los fenómenos de fluencia pueden ser resueltos, en casos moderados, con refuerzos de pernos largos, normalmente autoperforantes e inyectados con cemento, y hormigón proyectado. Medidas que pueden hacerse en actuaciones nocturnas o cortes parciales.
- Los casos más fuertes de fluencia requieren la construcción de contrabóveda que supone el corte total de la infraestructura.
- En algunas obras de refuerzo de este tipo se ha renunciado a los pernos por los efectos que el agua de perforación puede tener en el terreno. En nuestra experiencia, habiendo observado incrementos de convergencia de 1 ó 2 mm durante la perforación e incluso inyección, el efecto negativo está muy limitado en el tiempo y el comportamiento final es más satisfactorio que el solo empleo de hormigón proyectado.
- El empleo de súper fluidificante de propiedades tixotrópicas, en nuestro caso, MasterRoc FLC100, empleado siguiendo las indicaciones del fabricante, es imprescindible en la inyección de terrenos y sostenimientos fracturados para asegurar la permanencia de la lechada en su lugar. De hecho, no ha fallado ninguno de los pernos ensayados a pesar de la baja calidad del terreno.
- Ante la presencia de agua en el terreno, las medidas de drenaje y canalización pueden ser de eficacia similar a la de los refuerzos estructurales.