Cemento compactado con rodillo
Las presas de gravedad, de cemento armado, ya no están de moda. El cemento RCC es más que un nuevo material, es un nuevo método de construcción, en el que todo son ventajas: menor consumo de cemento, mayor resistencia, menor tiempo para terminar, para coronar la presa, menor costo. El concepto compactar el cemento a base de un rodillo vibratorio es fácil de comprender. La ejecución ya no es tan fácil. Los mismos equipos de compactación del cemento asfáltico los usamos para el RCC, con una carga estática de 30 kg, como mínimo. Terminada la compactación comienza el fraguado o hidratación del cemento.
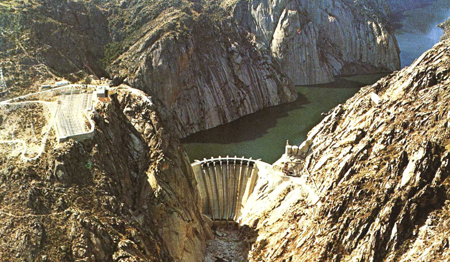
El Simposio de Zaragoza trataba de presas en general. Hay muchos tipos, y no me refiero a si son altas (generar energía eléctrica) o bajas, para riego. Unas son de gravedad, una pared recta con sus dos vertientes inclinadas, que soportan el empuje del agua embalsada. El peso de la presa es suficiente para contener la presión hidráulica.
Luego las hay de arco, y arco de doble curvatura, en el plano vertical y en el horizontal (presa de bóveda). La forma de la presa es la encargada de resistir el empuje del agua. La presión se transfiere en forma muy concentrada hacia los extremos derecho e izquierdo de la pared. Laderas que deben ser de roca muy dura y resistente. Requieren menor cantidad de hormigón. Ya los romanos hicieron una presa de arco en Glanum, Francia.
El ladrillo, sillería y manpostería, materiales sueltos, son para las presas de poca elevación, que hay que impermeabilizar. En España tenemos el accidente de la Presa de Tous, construida con materiales sueltos. El 20 de octubre de 1982 se derrumbó, debido a varios fallos, en una crecida del rio Júcar. Aguas abajo destruyó parte de la población de Alcira. En 1994 se construyó la nueva presa, más alta, de hormigón, que genera energía eléctrica. En España el 67% de las presas son de gravedad, hechas con hormigón, con o sin armaduras de acero. Son las presas de antes.
Cemento hidráulico y el RCC
Recordemos qué es una mezcla de clinker: áridos, cenizas volantes y grava, y al reaccionar con agua (una fuerte reacción exotérmica) se solidifica con el curado, fraguado. Aumenta su consistencia y en 27 días formará una masa pétrea. Existe el periodo de prefraguado, que oscila entre 2 y 4 horas. La hidratación del cemento es indispensable para mejorar la resistencia a la compresión. El curado húmedo continuo, mojar el cemento, desde el momento en que es colocado hasta que ha adquirido la calidad deseada. Es posible la inmersión del cemento en agua, el rociado y las cubiertas húmedas, arpillera húmeda, membranas de curado, o encofrado provisional, papel Kraft impermeable. La evaporación excesiva de agua en el hormigón recién colocado puede retardar apreciablemente el proceso de hidratación a edad temprana. La pérdida de agua también provoca la retracción del hormigón, generando tensiones, fisuras, en la superficie expuesta.
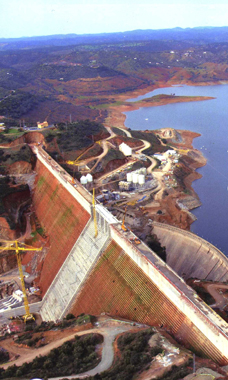
Evitar el riego periódico con agua. La hidratación progresa lentamente cuando la temperatura es baja, por debajo de los 10°C. Los compuestos de curado pueden impedir la adherencia entre el hormigón fresco y el endurecido, un incidente importante al construir la presa con RCC. El proceso de curado debe prolongarse hasta que el cemento haya alcanzado, como, mínimo, el 70% de su resistencia de proyecto, normalmente durante unos 7 días. Pero hacen falta más si el RCC es de endurecimiento lento. El curado acelerado es posible: Es el cemento de albañilería. Para construir una presa no nos sirve, hace falta el cemento de alta resistencia.
En la fábrica de cementos se calcina la piedra, el carbonato cálcico, se forma CaO, cal viva, y ésta reacciona a su vez con silicatos, para formar silicato cálcico. En el mismo horno, a 1.400 °C, se forma aluminato tricálcico y ferroaluminato tetracálcico. A esos productos llamamos clinker. La energía necesaria para obtener un gramo de clinker es de 1.700 julios/gramo. El cemento comporta una gran demanda de energía. Al clinker se le añade un 2% de yeso y la mezcla es molida.
En propiedades mecánicas el RCC equivale al cemento hidráulico, pero contiene menos agua y mayor densidad, debido al agregado fino y grueso. Suponen el 75-85% del total. El RCC contiene 12-15% de cemento y 4-6% de agua, menos agua que el C.hidráulico. El RCC después de compactado se cura y puede lograr una alta resistencia antes que el cemento hidráulico, si hacemos uso de ciertos ingredientes, por ejemplo: aumentar el cemento, la densidad, hasta 356-593 kg/m3, o disminuir el porcentaje de agua hasta 0,20-0,45%.
Las cenizas volantes, porosas, el residuo formado al quemar lignito (carbón mineral), componente del cemento hidráulico, también se incorporan al RCC, e igualmente las escorias de altos hornos. Del volcán de Puzuolli, Vesubio (Italia), se obtenían cenizas en la antigüedad para añadir a la cal, el cemento. Las puzolanas, materiales aluminio-silíceos, sintéticos, añadidos históricamente al cemento, se incorporan al RCC. Su composición es la mezcla de 3 óxidos, de silicio, aluminio y hierro. Del volcán de Puzuolli salían lavas ígneas, que al enfriarse rápidamente se convertían en vidrio amorfo, polvo, poroso, es decir, la puzolana. El clinker en el RCC sigue siendo el normal, 70% de puzolana (aglutinante mínimo) y 30% de cal.
El RCC va ganando con la edad en resistencia, tanto mecánica como química, superando al portland. Los agregados son gravas de hasta 8 cm de diámetro. El porcentaje ideal de agua es 6%, pero puede llegar hasta 10%. Los aditivos pueden hacer a la pasta más fluida. La compactación son golpes de martillo (4,5 kg), que se deja caer desde 50 cm de altura sobre la pasta.
El método RCC
Se remonta a 1960 cuando Taiwán construyó la presa de Shihmen, luego vino la presa de Tarbela, Pakistán, y confirma que es el mejor método de construcción: el cemento compactado con rodillo vibratorio, con menor contenido de agua, precisamente para permitir la compactación. El contenido de cemento es del mismo orden que el de los cementos vibrados para pavimentación, entre 280 y 330 kg/m3. En la presa se superponen las diversas capas, con uniones bien cuidadas. El método permite mayor rapidez, construir 2-2,5 m de altura de presa por semana, acortando el plazo de ejecución y utilizando a gran escala dumpers, bulldozers, rodillos. La mayor parte de estas presas son rectas, son de gravedad. Las de arco no permiten tanta rapidez.
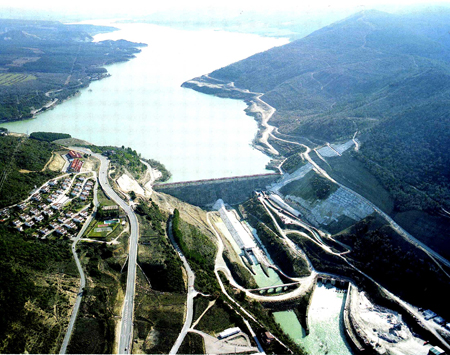
A partir de la década de los 70 la presa RCC ha seguido 3 conceptos: mezcla pobre, mezcla de contenido medio y contenido alto de pasta.
Por mezcla pobre entendemos 70-100kg/m3 (presa de Wilow Creek, EE.UU). En 1996, Brasil construyó la presa de Jordao, con 85kg/m3 de conglomerante. La ventaja es un menor desarrollo de calor durante el proceso de hidratación.
Como presa de contenido medio citemos Les Olivettes, Francia. 130kg/m3 de un cemento especial.
Como presas de alto contenido de pasta, con dosificaciones de conglomerante entre 150 y 270 kg/m3, con una alta proporción de cenizas volantes, podemos destacar las de Upper Stillwater, EE UU (1987) y Rialb, España, (2000), con 200 kg/m3. Desde 1995 las presas españolas pertenecen a este tercer grupo. Alto calor de hidratación, alta densidad, pero impermeable, lo cual indica que podemos prescindir de obra adiciona, para impermeabilizar las paredes de la presa. Con el método RCC la presa no es más fácil de construir pero es algo más económica.
El espesor de cada capa en la pared de la presa es de 50-100 cm, que se compactan de una sola vez. Las nuevas presas de alto contenido de pasta son las más frecuentes, el 47% de las nuevas presas, y todas generan energía eléctrica. Por supuesto, las paredes son muy impermeables al agua. La sección transversal de la presa puede reducirse, incluso en las zonas de actividad sísmica. La solidez está garantizada, con un cemento de bajo contenido de cal, y a un costo inferior al de una presa construida con el método convencional. El fraguado es más lento, menos generación de calor en la reacción con el agua, calor de hidratación más reducido. Se traduce en un plazo mayor para compactar el material.
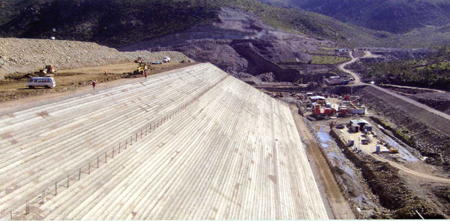
Las presas españolas RCC usan mucho las cenizas volantes (con un contenido de cal bajo, 35%) porque España produce al año unas 7 millones de Tm de cenizas volantes. Las escorias granuladas de alto horno se usan menos. La resistencia a la compresión es de 210-400 kg/cm2 de la probeta. La retracción del cemento es nula. El porcentaje de agua oscila entre 4-6%. La resistencia del cemento RCC completamente consolidado es inversamente proporcional al porcentaje agua/cemento. A nivel mundial las mayores presas RCC son la de Longtan, China, 216,5 m de altura y la de High Diamer Basha, Pakistán, 272 m de altura.
American Concrete Institute. Roller compacted Mass Concrete. Act 207.5R-99.
Choi, Y. RCC mix Design – Soil approach. Journal of materials in civil engineering. Enero 2001.
Dunstan, M. Recent developments in RCC Dams. Hydropower & Dams 1999.
Hansen, K. Roller compacted concrete dams. McGraw Hill, New York 1991.
Rodríguez, F. The use of roller compacted concrete. Brasil, Sao Paulo 1998.
Santana, J. A geotechnical methodology for roller compacted concrete Design. Universidad Nova de Lisboa, 2007.