El poder del filo
En los últimos años, los fabricantes de herramientas han encontrado en la propia micro-geometría del filo de corte otra clave para obtener la tan ansiada mejoría de rendimiento. Esta mejoría se da tanto en cuestiones de aumento de vida útil de herramienta, como en mejorías del acabado superficial de los componentes mecanizados. De esta forma se consigue aumentar la productividad de los procesos de corte por arranque de viruta.
El primer paso para estudiar la influencia del filo de corte durante el mecanizado es encontrar una forma para definir las diferentes formas posibles que puede tener. Buscando en la literatura, los investigadores proponen diferentes formas para definirlo. En la figura 1 se pueden ver algunos de los modelos propuestos por los investigadores.
A pesar de todos los modelos que hay, en la gran mayoría de los estudios realizados que se pueden encontrar en la literatura se usan tres opciones: el propuesto por Denkena et al. (2005) [1]; lo aproximan a un radio equivalente; o una mezcla de los dos anteriores, es decir, obtienen un radio equivalente e indican si tiende hacia la cara de desprendimiento (K>1) o tiende a la cara de incidencia (K<1). Muchos de los sistemas de medición de radios de filo, como el microscopio Alicona Infinite Focus G5, dan el radio aproximado además de los parámetros definidos en el estudio de Denkena et al. (2005) [1]. Por ello, este último es el sistema adoptado en este trabajo.
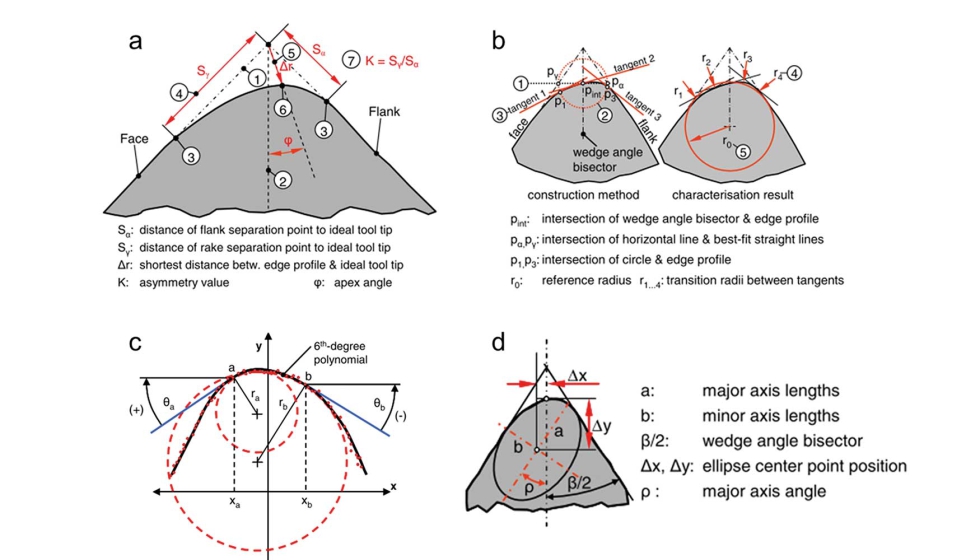
Una vez definido el filo, si se quiere modificar la geometría de los mismos es necesario tener una forma de hacerlo. En el mercado se pueden encontrar múltiples tecnologías para ello. Sin embargo, en la industria hay una preferencia por tres de ellos: la tecnología de Drag-Finishing, la de Abrasive Jet machining y el Brushing [5]. En el estudio realizado por Straka y Vopat (2022) se analizó la influencia de estos tres procesos de generación de radios de filo en la vida útil de la herramienta, obteniéndose como conclusión que el proceso que logra obtener mayor duración de vida de la herramienta con un radio de filo de 35 μm es el Drag-Finishing [5].
Las ventajas de aumentar el radio de filo son múltiples. Sin embargo, hay que tener cuidado a la hora de decidir hasta qué radio aumentarlo debido a que, a partir de cierto punto, esas ventajas desaparecen y se puede empeorar el proceso de corte tal y como Schiffler et al (2020) demostraron en su investigación [6]. Además, un mayor radio de filo mejora la generación de calor debido a la mayor deformación plástica y a la fricción, pero mayor radio equivale a una mayor profundidad del efecto ploughing y, con ello, puede obtenerse un peor acabado superficial por el acumulamiento de material si ese radio es muy grande [7].
Caso práctico: fresado de bola de acero endurecido AISI D2
Diseño de los ensayos
Para los ensayos se han usado fresas del fabricante Elfer S.C. a las que se les ha modificado la geometría de los radios de filo y se ha hecho una comparativa con una herramienta de referencia sin tratar. Las fresas de bola eran de diámetro 10 mm (D), con una radio de bola de 5 mm (R), una longitud de corte de 24 mm (Lc) y una longitud total de 80 mm (L). El ángulo de hélice de era de 25° y tenían cuatro filos.
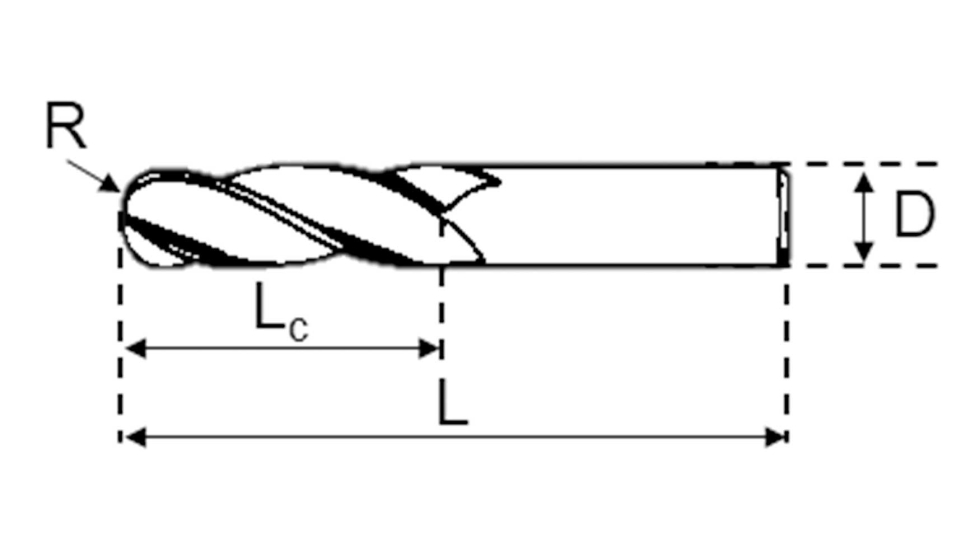
Los radios de filo objetivo son 5, 10 y 15 µm y han sido generados mediante el proceso de Drag-Finishing. Por consiguiente, se han ensayado cuatro fresas distintas: tres tratadas y una tal y como viene de fábrica. Después de los tratamientos del filo, la empresa Metal Estalki S.L ha recubierto las cuatro herramientas c mediante la técnica de PVD. El recubrimiento escogido ha sido Trinaco-Red con un espesor de 1,5 μm. Este recubrimiento se caracteriza por su gran resistencia a la abrasión, su gran dureza y su bajo coeficiente de fricción, algo muy conveniente para el mecanizado de un material de extrema dureza como el AISI D2 templado. Una vez realizados los tratamientos del filo y los distintos recubrimientos, las fresas se han analizado en el microscopio Alicona Infinite Focus G5. En la tabla 1 se detallan las mediciones de los radios de filo de cada herramienta.
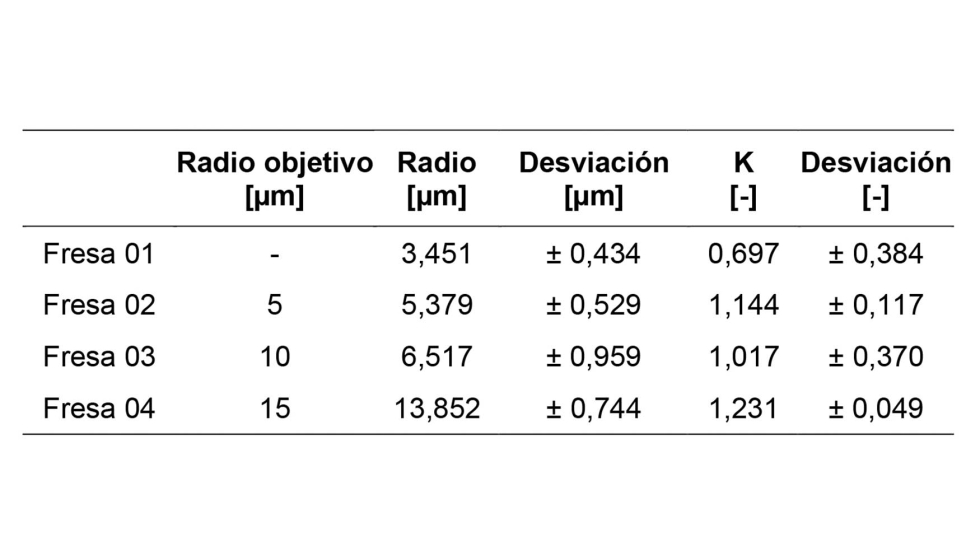
El factor K, denominado factor de forma, determina hacia qué lado, incidencia o desprendimiento, tiende el semieje mayor de la elipse. Si es mayor que uno, tiende a la cara de desprendimiento mientras que, si es menor que uno, tiende a la cara de incidencia.
Los ensayos se han realizado en un bloque de 200 mm de largo (L) y 100 mm de alto (H) con un espesor de 200 mm (W) de AISI D2. Entre fresa y fresa se ha realizado una limpieza de la superficie mecanizada para que no haya diferencias entre una y otra. Además, se ha decidido dejar 40 mm de voladizo en la herramienta en todos los ensayos. Las características del material y su composición química se pueden ver en la tabla 2.
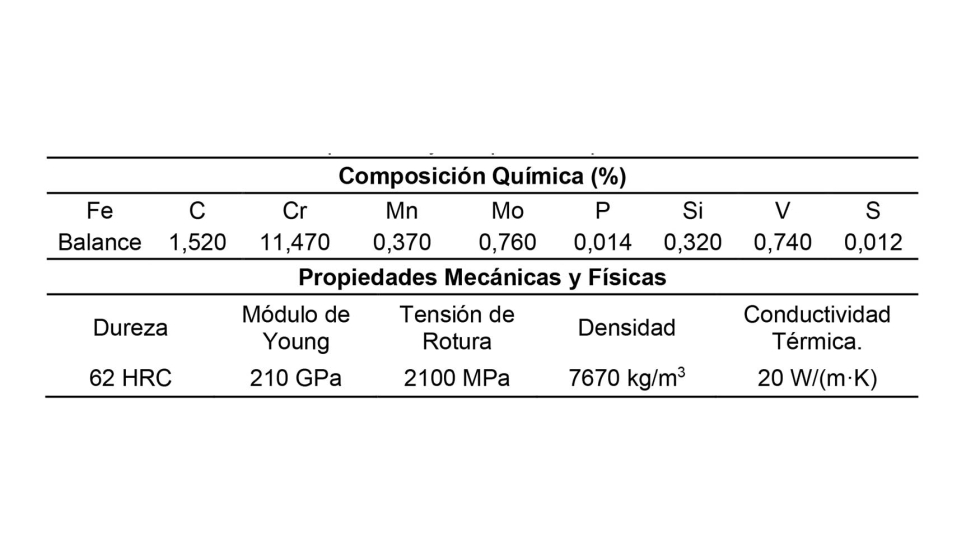
Para la realización de los ensayos se ha utilizado una fresadora-torno Ibarmia THR Multiprocess 16. En la figura 2 se puede ver el montaje experimental utilizado durante la realización de los ensayos. La estrategia seguida durante los ensayos ha sido en Zig y se paraba para realizar mediciones de desgaste y de rugosidad cada 25 metros de mecanizado.
El criterio de fin de ensayo ha sido llegar a mecanizar 150 metros o superar un desgaste medio de flanco de todos los filos de 0,300 milímetros de acuerdo con la norma ISO 8688-2. Para medir el desgaste se ha utilizado un microscopio PCE-200 para sacar fotos de los filos. Para las mediciones de rugosidad se tomaron negativos de la superficie con resinas para posteriormente analizarlas en el microscopio confocal Leica DCM3D.
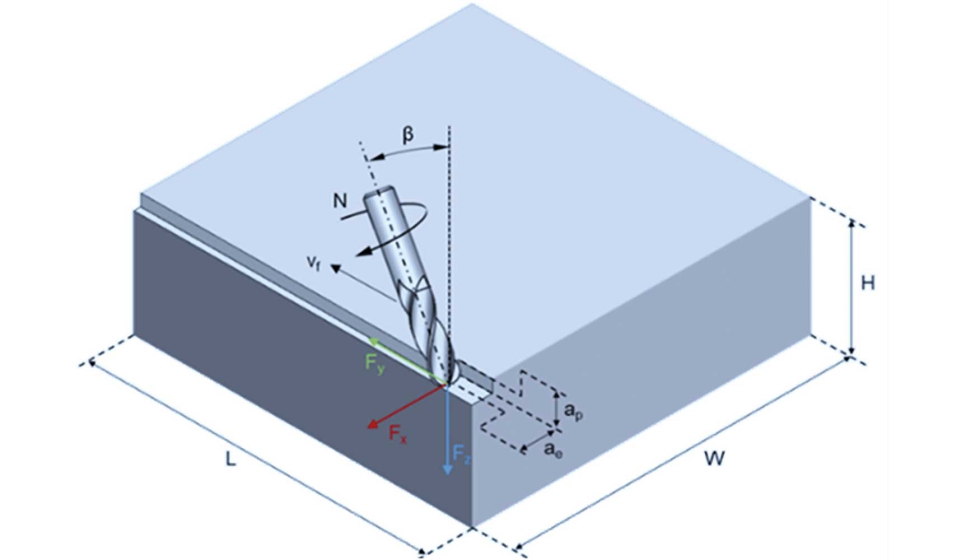
Las condiciones de corte utilizadas durante los ensayos son las típicas para operaciones de acabado de fresa de bola para aceros endurecidos y vienen dadas en la siguiente tabla.
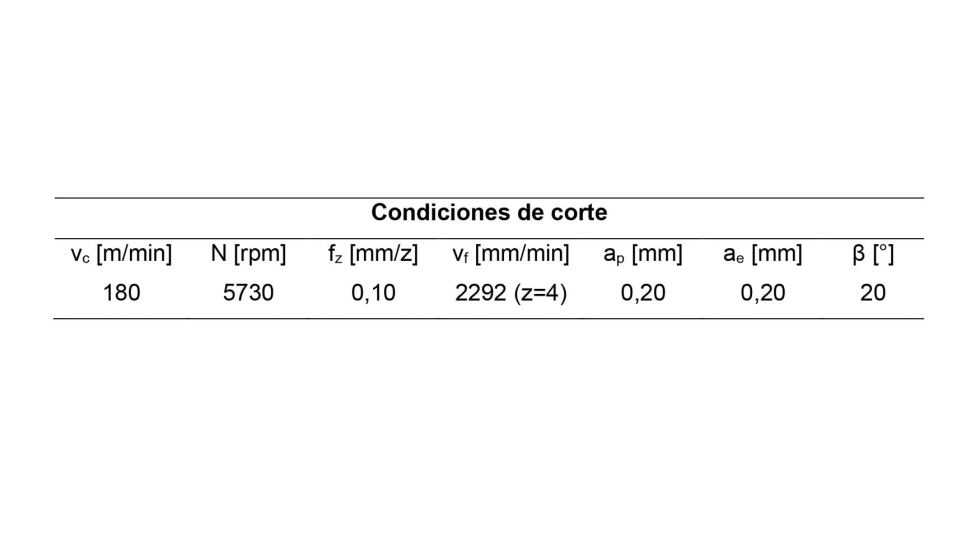
Tabla 3. Condiciones de corte.
Análisis del desgaste
En la figura 3 se presenta el desgaste medio de flanco de las herramientas proporcionadas por diferentes fabricantes. El desgaste se ha medido en todos los filos de cada herramienta y en la figura se presenta la media entre los filos junto con la desviación de los mismos.
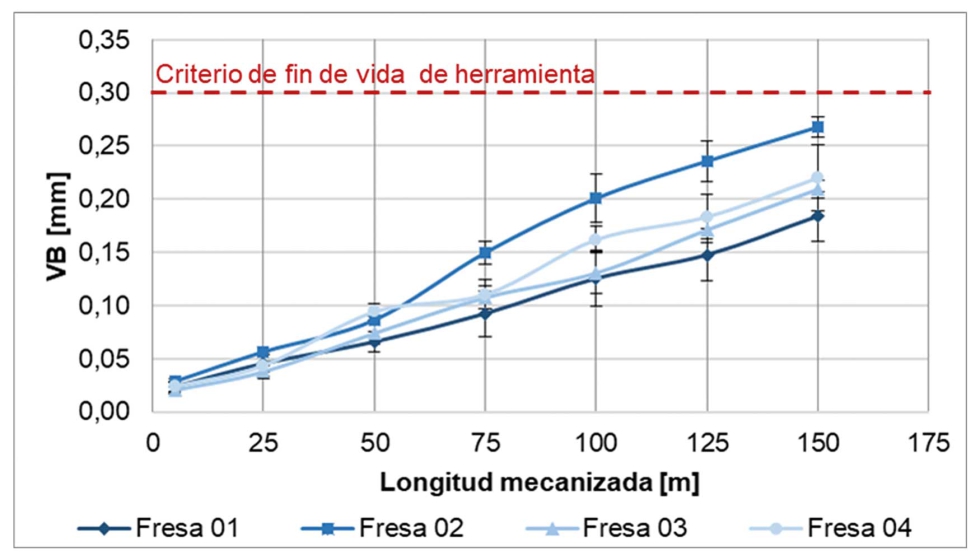
Figura 4. Evolución del desgaste de las herramientas con distintos radios de filo.
Como se puede apreciar, ninguna de las fresas alcanzó el final de la vida útil de 0,3 mm propuesta por la ISO 8688-2. La fresa 01, la usada a modo de referencia, es la que menor desgaste ha tenido a lo largo de toda su vida útil. Sin embargo, las fresas con radios de filo de 10 y 15 μm (fresas 03 y 04 respectivamente) tuvieron un comportamiento similar tanto en valores del desgate como en la tendencia del mismo. En el caso de la herramienta de 5 μm, sufrió una pequeña fractura en uno de los filos a mitad de ensayo que hizo que el desgaste se acelerara.
Análisis del acabado superficial
Para evaluar la rugosidad, se ha medido los parámetros de Ra y Rz utilizando para ello un filtro gaussiano con una longitud de corte de 0,25 mm y una longitud de muestreo de 4 mm de acuerdo con la norma ISO 4288: 1996. Se han tomado cinco muestras en cada pasada.
En la figura 4 se observa la evolución de la rugosidad media (Ra) a lo largo del mecanizado para las tres fresas, mientras que en la figura 5 se puede ver el parámetro de rugosidad Rz. En ambas figuras se presentan las medias de las cinco mediciones junto con sus desviaciones.
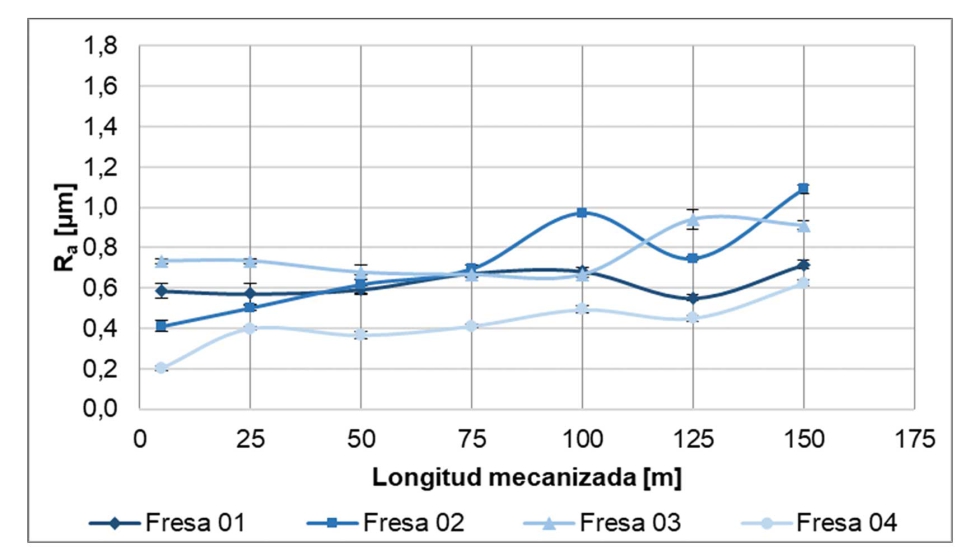
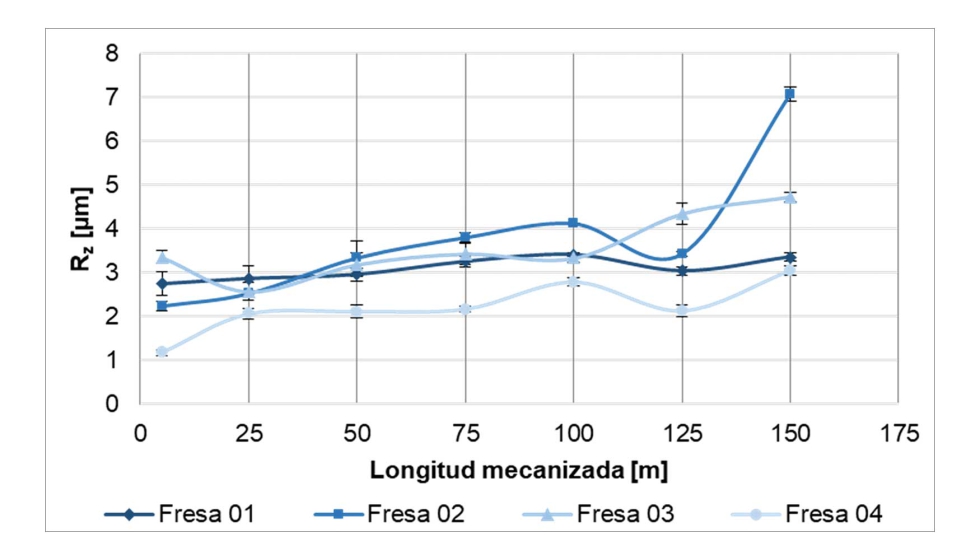
A diferencia de lo ocurrido en los desgastes, el comportamiento de las rugosidades es muy similar con todas las fresas ensayadas, pues apenas varían a lo largo de la vida útil de la herramienta. La fresa 03 (radio 5 µm) es la única que empeora mucho la rugosidad justo cuando llega al final de su vida útil. Es cierto que en el algunas de las otras fresas dejan mayores rugosidades en alguna pasada, pero después vuelve a su tendencia anterior. Esto se debe a pequeñas roturas que han ido apareciendo en los filos. Cabe resaltar que la que menor rugosidad presenta, tanto para el parámetro Ra como para el Rz, es la fresa de radio 15 µm (Fresa 04) dejando el acabado superficial de la pieza por debajo de las 0,5 µm y 2,5 µm respectivamente (salvo en la pasada final). Esto es debido a dos factores: al menor desgaste que presentó la fresa frente al resto de las fresas tratadas y a su mayor radio de filo. Si se tiene en cuenta únicamente la primera pasada para evitar el efecto del desgaste sobre las fresas, la mejor rugosidad es la que proporciona las fresas de radio 15 µm, seguida por la que dejan las fresas de radio 5 µm y por la de referencia. Finalmente, la que peor rugosidad deja es la de radio 10 µm.
Conclusiones
A continuación, se presentan las principales conclusiones obtenidas durante la realización de este estudio del análisis de la influencia del radio de filo en el fresado de acero AISI D2 templado con fresas de bola del fabricante Elfer S.C. y recubiertas por Metal Estalki S.L.:
- La fresa de referencia (Fresa 01) es la que menor desgaste presentó a lo largo de todo el ensayo. Esto está en línea con lo concluido por Schiffler et al. (2020) [6]. Analizando por radios de filo, la fresa de radio 5 µm (Fresa 02) fue la que peor desgaste tuvo debido a una rotura de uno de sus filos. La fresa de radio 10 µm (Fresa 03) fue la que mejor comportamiento frente al desgaste tuvo de las fresas tratadas. La fresa de radio 15 µm (Fresa 04) tuvo una tendencia similar a la de 10 µm, presentando valores muy similares de desgaste.
- En el acabado superficial de la primera pasada, las mejores rugosidades obtenidas fueron las generadas por la fresa de radio 15 µm, seguida por las de 5 µm y la de referencia y, por último, la de radio 10 µm. Se puede observar que diferentes radios de filo mejoran diferentes propiedades del corte tal y como concluyen Liu et al. (2021) en su estudio [7].
Referencias
[1] B. Denkena, J. C. Becker, and L. de León-García, ‘Study of the influence of the cutting edge microgeometry on the cutting forces ande wear behavior in turning operations’, in 8th CIRP Int.Workshop on Modeling of Machining Operations, May 2005, pp. 503–507.
[2] F. Tikal and S. Holsten, ‘Bedeutung der Kantenverrundung bei Zerspanungswerkzeugen’, In-house trade fair 2008 of OTEC Präzisionsfinish GmbH, 2008.
[3] C. J. Corte´s Rodri´guez, Cutting edge preparation of precision cutting tools by applying micro-abrasive jet machining and brushing..
[4] C.-F. Wyen, W. Knapp, and K. Wegener, ‘A new method for the characterisation of rounded cutting edges’, doi: 10.1007/s00170-011-3555-4.
[5] R. Straka and T. Vopat, ‘Cutting edge preparation methods comparison in terms of tool life’, 33rd DAAAM Int. Symp. Intell. Manuf. Autom., pp. 188–0192, 2022, doi: 10.2507/33rd.daaam.proceedings.026.
[6] M. Schiffler, T. Maul, F. Welzel, H. Frank, T. Cselle, and A. Lümkemann, ‘Machining Technology and PVD Coatings for Milling Thin Structural Parts of Inconel 718’, SSRN Electron. J., Nov. 2020, doi: 10.2139/SSRN.3724144.
[7] Y. Liu, A. Hrechuk, M. Agmell, A. Ahadi, J. E. Stahl, and J. Zhou, ‘FE analysis on the association between tool edge radius and thermal-mechanical load in machining Inconel 718’, Procedia CIRP, vol. 102, pp. 91–96, 2021, doi: 10.1016/J.PROCIR.2021.09.016.