Cómo una empresa del sector siderúrgico y minero logró ahorrar 6000€/hora gracias al mantenimiento predictivo
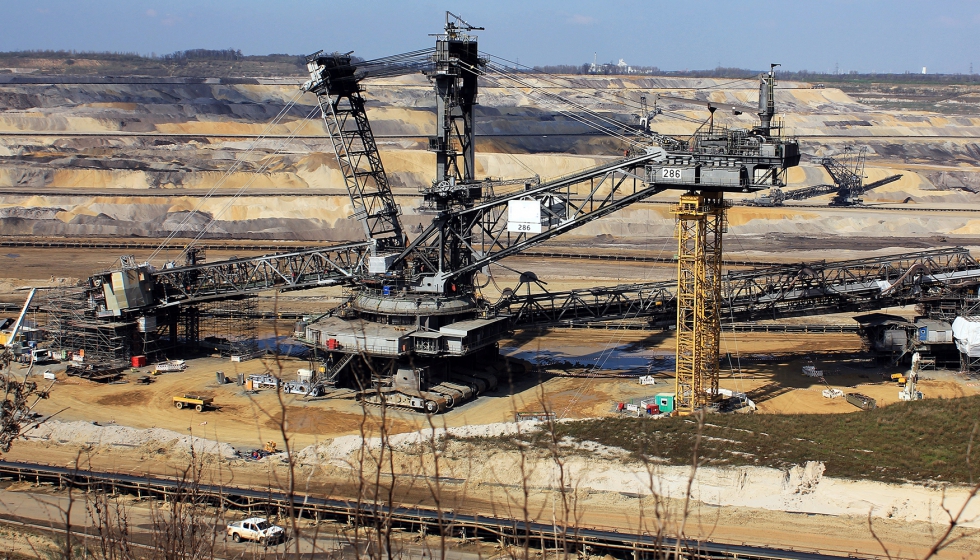
Tiempo atrás, y gracias a la visión del equipo de mantenimiento y dirección, se decidió invertir en soluciones de mantenimiento predictivo con la intención de poder avanzarse a paradas no planificadas de sus líneas más críticas, sin duda una decisión muy acertada, como se verá más adelante.
Aplicación
En este caso en concreto hablamos de un motor trifásico de jaula de ardilla asíncrono de 450 kW a 3.000 rpm que acciona un compresor de martillo mediante un acople rígido. Una de las aplicaciones a monitorizar debido a su criticidad en el proceso.
Este compresor fue objeto de observación y sensorización debido a anteriores reparaciones y paradas de producción en el pasado. Objetivo: identificar las causas de forma anticipada, sin afectación a la producción.
Situación
Al tiempo de la implementación de la solución de predictivo en el compresor se detectó un incremento de las vibraciones en la aplicación monitorizada y más concretamente en el motor eléctrico indicando síntomas ascendentes de desalineación y posibles holguras entre el motor y el compresor.
Mediante el análisis de tendencias se pudo observar claramente el inicio de esa anomalía y como con el paso del tiempo se incrementaba la vibración resultante.
Sin duda, localizar la avería de forma temprana permitió realizar un buen diagnóstico y planificar su reparación en horas no productivas. Así se evitó una clarísima parada en la producción de forma no planificada, que por el tipo de avería/reparación hubiese supuesto un tiempo de paro de al menos 5 horas a un precio de 6.000€/hora de producción con un total de 30.000€ por dicha avería.
Diagnóstico/solución
Mediante el análisis espectral se pudo precisar que muy probablemente el problema podría estar en el lado del motor del acople y no del compresor, diagnóstico que también permitió un ahorro de tiempo importante en la detección exacta de la causa.
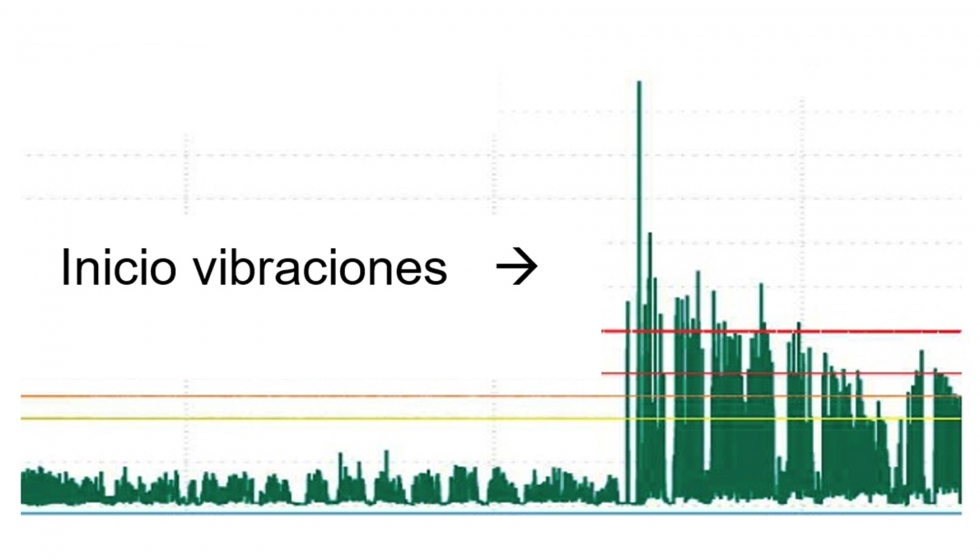
Finalmente, un aflojamiento prematuro de los tornillos de fijación del disco de acoplamiento fue la causa de la vibración ascendente detectada por lo sensores. Se procedió a su correcto apriete y adecuación, volviendo las vibraciones a su situación normal.
En el gráfico se puede observar en el tiempo toda la anomalía: desde que se produce hasta su reparación y cómo se vuelve a la situación normal esperada y deseada.
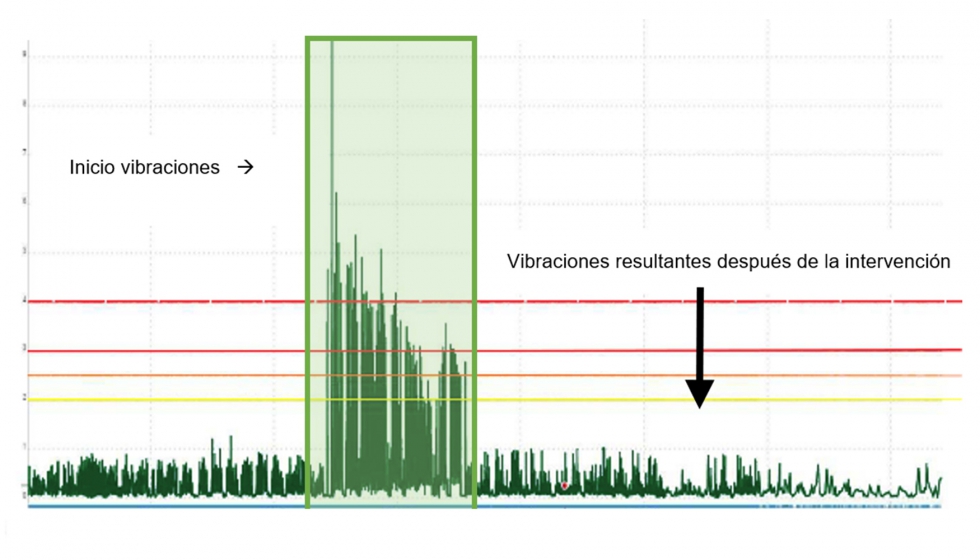
Conclusión
¿Qué hubiese pasado sin una solución de mantenimiento predictivo instalada en esa aplicación? Muy probablemente, y tomando como dato las gráficas mostradas, los tornillos se hubiesen ido aflojando cada vez más y por lo tanto la holgura se hubiese incrementado hasta probablemente afectar a la parte más débil de la aplicación, que pueden ser varias y ninguna buena, ya que su repercusión no sólo está en la parada no planificada de la producción, sino que depende del elemento mecánico o eléctrico afectado se podría dar el caso de que no se tuviese duplicado o en stock de algún proveedor.
Sin duda, la inversión en predictivo liderada por el equipo de mantenimiento y apoyada por la dirección de la empresa demostró las bondades del sistema y evidenció que la anticipación es una forma de ahorro directo en problemas y dinero.
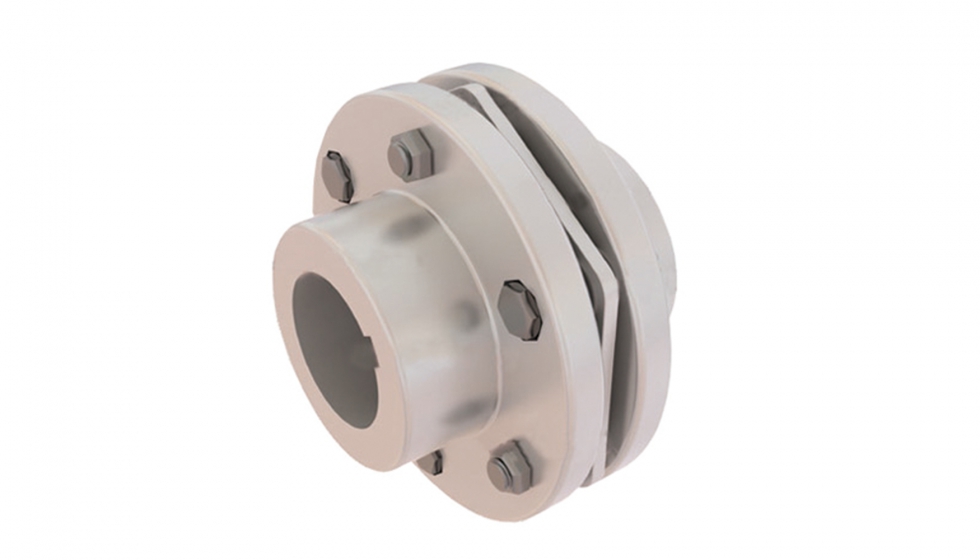
KfeW Systems es una empresa tecnológica con producción propia que desarrolla soluciones de mantenimiento predictivo y que puede controlar una línea cinemática, tanto en la parte eléctrica como mecánica.