Nuevo artículo sobre conceptos que hacen más fácil la vida en la planta de inyección
POM, Polioximetileno. Foaming Test
El POM es el polímero de ingeniera semi cristalino con un mayor nivel de cristalinidad, (75%-85%), por ello son opacos con un color natural blanco debido a la cantidad de cristalitos contenido en su estructura. Su temperatura de fusión es del orden de 175 °C.
En 1920 se estudió la polimerización y estructura del POM, pero debido a su baja estabilidad térmica no fue comercializado. Fue más tarde en 1952 cuando fueron inicialmente introducidos por Dupont, en 1956 Dupont patentó los POM homopolímeros con su marca comercial Delrin.
El POM es muy utilizado mundialmente en aplicaciones de ingeniería con éxito, sin embargo en las plantas de inyección que lo transforman habitualmente, siempre cuentan historias o anécdotas con el POM tras una degradación severa, explosiones, boquillas arrancadas, material que llega hasta el techo tras una explosión, olores desagradables, etc. En todo esto hay algo de leyenda y también hay mucho de una deficiente utilización del material.
Estos materiales, cuando se degradan generan formaldehido, un gas con un olor peculiar y que si no tiene salida a la atmósfera provoca un consecuente incremento de la presión en la zona en que se produzca la degradación, husillo, canal caliente, etc.
Causas de degradación:
Estabilidad térmica
A pesar de la buena resistencia y estabilidad térmica de estos materiales en su paso por la máquina de inyección durante el proceso de transformación, un tiempo de permanencia prolongado a temperatura de moldeo (215 °C más de 30 minutos), posibles retenciones, etc., puede producir degradaciones.
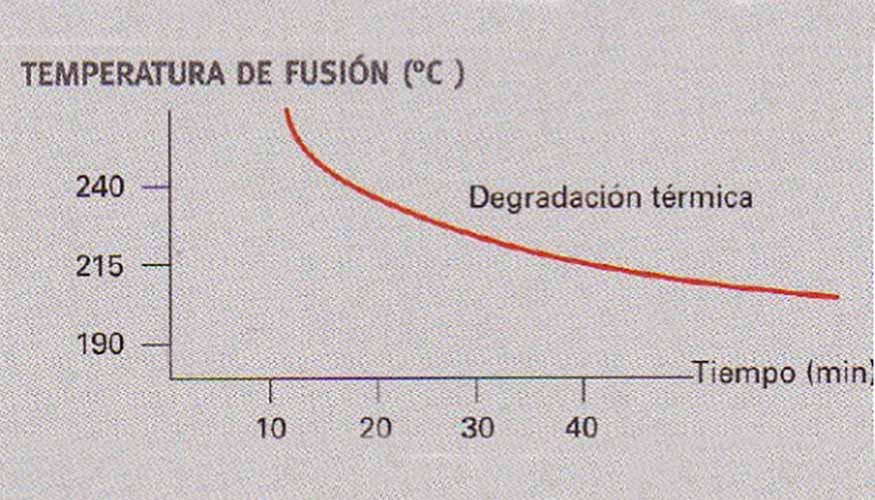
Estas degradaciones provocan una pérdida de peso molecular irreversible y una generación de gases (formaldehído principalmente).
Hay que tener muy en cuenta que no existan retenciones de material en la unidad de inyección o en el canal caliente. Estas retenciones adheridas al metal, cuando se degraden después de un tiempo generarán puntos de degradación, gases, betas marrones y por supuesto, la correspondiente pérdida de propiedades.
Incompatibilidad de pigmentos o aditivos
Cuando moldeamos POM con colorantes o masterbaches, la composición de pigmentos de la fórmula de color puede influir en la calidad del material fundido. Está demostrado que hay pigmentos y aditivos que provocan la degradación del POM en su estado fundido.
Por esta posible degradación motivada por los pigmentos o aditivos, debemos comprobar que el material que vamos a utilizar no se vea afectado por el coloreado.
Cuando existe esta afectación de los pigmentos o aditivos con el material base, se produce una reacción química que genera de nuevo gases o burbujas.
¿Cómo comprobar que nuestro proceso no está degradando al POM en la planta de inyección?
Foaming Test
Este sencillo test nos va a ayudar a detectar cuándo sucede la degradación del POM, situación a evitar siempre. Los pasos a seguir para la correcta realización de este test son los siguientes: Trabajar con el proceso definido durante al menos 30 minutos para que el material permanezca en el sistema de unidad de inyección –canal caliente si lo hay–, durante este tiempo de proceso habitual y esté sometido a la temperatura y presión de inyección, velocidad periférica del husillo, contrapresión, etc.
1 Parar el proceso de inyección y dejar esperar un tiempo de reacción
Esperar en función de la temperatura utilizada y de si el material está siendo coloreado con colorantes o masterbaches.
- Tiempos de espera: 20 minutos en los casos
- Temperatura de masa 200 °C grados
- Transformación de color natural
- Tiempo de espera: 5 minutos en los casos
- Temperatura de masa 215 grados
- Transformación de material coloreado.
2 Efectuar una purga del material de la unidad de inyección
Purgar si es posible en un recipiente para purgas. Cuando el material purgado se haya solidificado se puede hacer dos comprobaciones:
- Cortar la purga y observar los cráteres internos. Siempre habrá burbujas o cráteres internos pero la superficie interna de los cráteres será diferente si estos los ha provocado la contracción y cristalización del material o si por el contrario los ha provocado la generación de gases por degradación Si los cráteres son por cristalización estos tendrán una superficie interior mate. Si son provocados por los gases provenientes de una degradación, su superficie interna será brillante.
- Sumergir la purga en agua. Observar el comportamiento de la purga al sumergirla en agua. Si la purga está formada por material correctamente fundido, esta masa fundida no tiene burbujas de gas en su interior mientras que una masa fundida con degradaciones sí tiene burbujas de gas en su interior. Por tanto. la densidad de la masa fundida con burbujas de gas será menor y esta purga flotará en el agua mientras que la masa fundida correctamente será más densa y se hundirá en el agua.
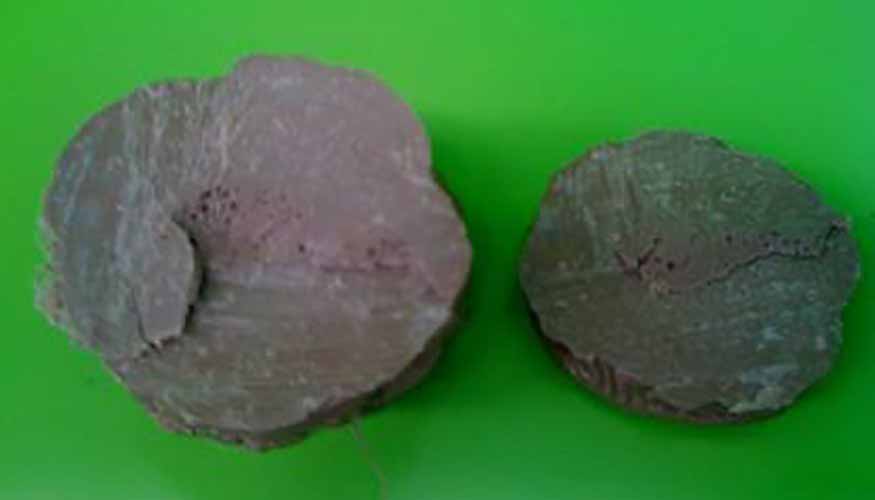
Test OK.
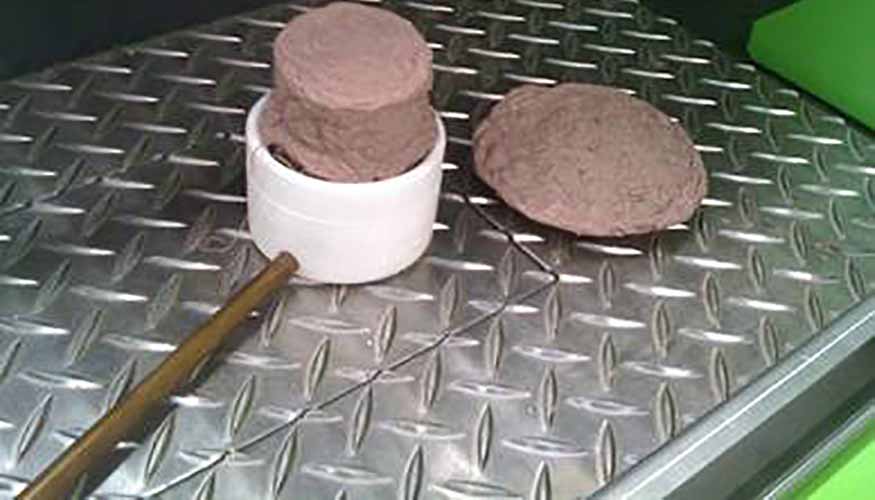
Foaming Test.
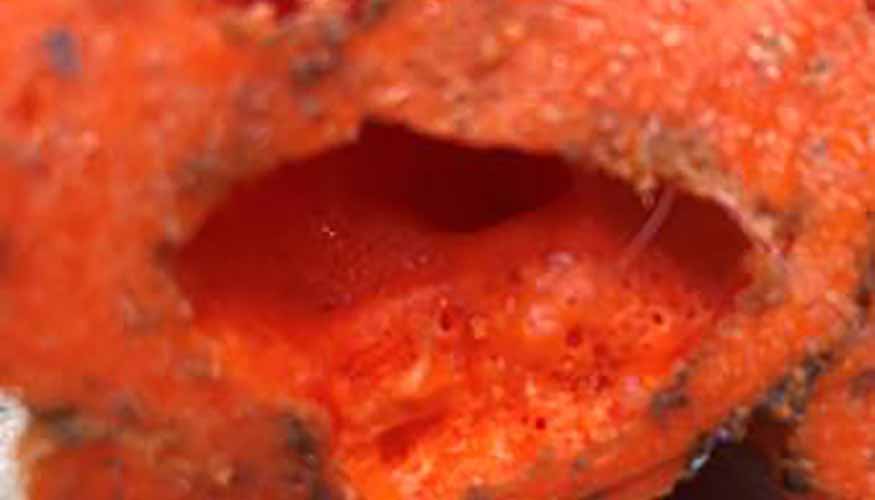
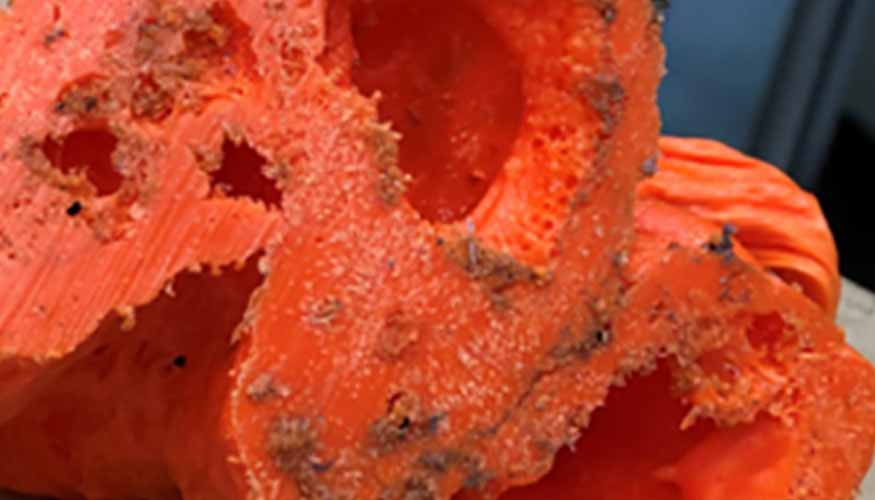
Test KO