Tecnología aditiva en troqueles: la siguiente generación de reparaciones de alto valor añadido
Iker Villarón Osorno, Magdalena Cortina Burón, Jon Iñaki Arrizubieta Arrate, Iñigo Hernando Arriandiaga, Jose Exequiel Ruiz Salas y Marta Ostolaza Gaztelupe, de la Escuela de Ingeniería de Bilbao, Dpto. de Ingeniería mecánica; y Natalia Colinas Armijo, de Ideko S. Coop
11/04/2019La estampación es una técnica de fabricación empleada en diversos sectores orientados a productos diferentes entre sí y que se basa en la fabricación de piezas de chapa metálica, siendo el ejemplo más común la automoción. A pesar de que la problemática es diferente para cada sector, se puede afirmar que en todos los casos se busca mejorar la eficiencia de los procesos, incrementar las productividades y reducir los costos de fabricación. Esta demanda ha generado un desarrollo de las técnicas de estampación, así como de los procesos de fabricación de lo útiles que se emplean en el proceso. Si bien es cierto que la manera de realizar la estampación es la misma, existen diferencias que hacen que la vida del troquel sea mayor o menor. La estampación en caliente de piezas aleadas para la fabricación de componentes de automoción críticos tiene un impacto en el desgaste del troquel totalmente diferente que los generados por los procesos de estampación en frío.
El desgaste es un fenómeno que ocurre en todas las herramientas debido a su uso y ocurrirá antes o después según las exigencias del proceso de fabricación. Algunas herramientas pueden ser sustituidas por otras nuevas, sin embargo, dado que los troqueles son herramientas de muy alto valor añadido y su sustitución conllevaría una inversión muy importante, su reparación constituye un campo que suscita un gran interés, dado que es una alternativa eficiente y rentable.
Sin duda, uno de los procesos de estampación donde el troquel sufre de manera notable es el proceso de estampación en caliente. En este proceso, el troquel, el cual está refrigerado internamente, recibe una chapa a alta temperatura (900 950˚C), la cual se estampa y enfría simultáneamente en la propia matriz del troquel, de manera que se da la transformación martensítica del material. Como resultado de esta operación, se consiguen fabricar componentes de ultra-alta resistencia, alcanzando valores de hasta 1500 MPa.
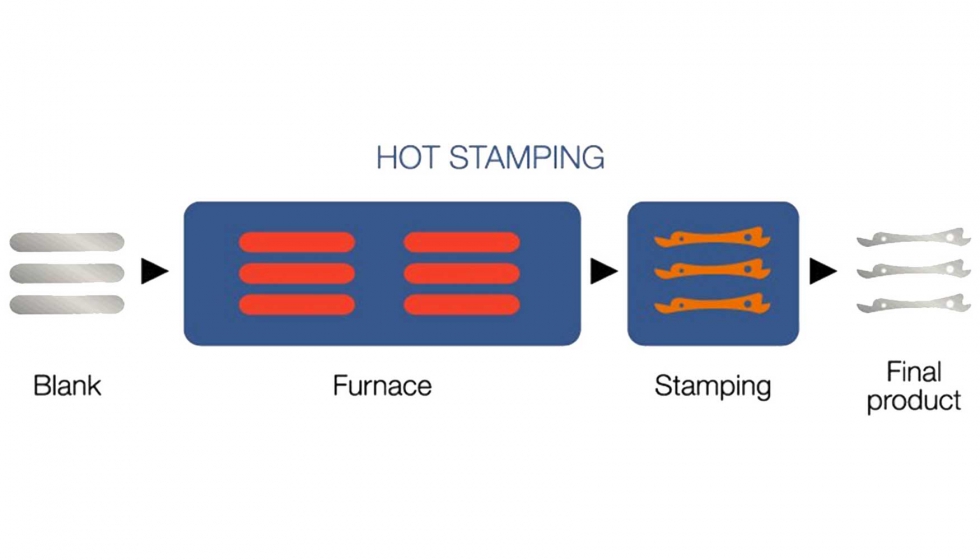
Debido a las altas temperaturas implicadas en el proceso, junto con el rozamiento que existe entre chapa y troquel, éste último puede verse sometido a elevado desgaste en función de las condiciones de proceso y la geometría. Además, a todo esto, hay que añadirle los ciclos térmicos que el troquel soporta, pues se calienta y enfría cada vez que fabrica una pieza.
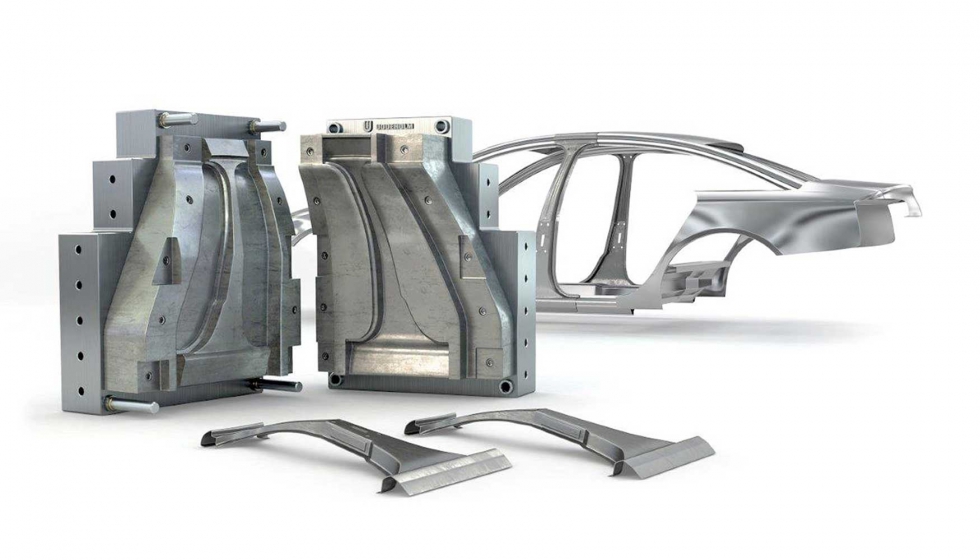
Así, el proceso de aporte por láser, también conocido como Laser Material Deposition o LMD, es una alternativa que permite reparar los troqueles desgastados para volver a poner en funcionamiento estos útiles
1. La tecnología LMD (Laser Metal Deposition)
La fabricación aditiva se ha convertido en una de las tecnologías emergentes más importantes. Su principio de fabricación está suponiendo una revolución en el diseño de producto y las nuevas características que este ofrece. De entre todas las técnicas de fabricación aditiva, nos centraremos en la tecnología LMD (Laser Metal Deposition).
La tecnología LMD emplea un láser como fuente de calor para generar un baño fundido sobre el material que hace de base, o sustrato, mientras se inyecta material de forma simultánea [1]. Este material puede presentarse en forma de polvo o hilo y, para ambos casos, es necesario emplear un cabezal o boquilla que dirija el material de forma apropiada al baño fundido generado por el láser. El aporte de material se da en forma de cordón, y la generación de recubrimientos o capas se consigue mediante el solape de cordones. Por último, superponiendo capas se pueden generar estructuras en 3D.
![Figura. 3. Esquema del proceso LMD [2] Figura. 3. Esquema del proceso LMD [2]](https://img.interempresas.net/fotos/1934862.jpeg)
Este proceso se caracteriza por su capacidad de generación de piezas con propiedades semejantes a las del substrato base, al cual se encuentra unido metalúrgicamente, con gran flexibilidad en cuanto a generación de geometrías y aplicable a una amplia variedad de materiales [3]. Los campos de aplicación de esta tipología de aporte por láser se centran principalmente en la fabricación y reparación de componentes de alto valor añadido, enfocados a sectores industriales como el aeronáutico, aeroespacial, automoción o petrolero. No obstante, la principal limitación del aporte por láser reside en el acabado de los componentes fabricados mediante esta técnica. Por consiguiente, las piezas fabricadas por LMD son normalmente sometidas a operaciones de mecanizado, solventándose así dicha limitación [4].
En consecuencia, el LMD puede emplearse como una tecnología moderna de mantenimiento y reparación de defectos en componentes de alto valor añadido, como por ejemplo grietas o desgaste, con una baja distorsión y afección térmica del material base. Esto permite tener un bajo impacto metalúrgico en la microestructura del material, la cual determina sus propiedades. En lo que a la industria de moldes y matrices se refiere, el LMD es una técnica ya consolidada para la reparación y modificación de moldes de inyección de plástico, aunque también está comenzando a establecerse como método de reparación y modificación de troqueles de estampación de metal. De este modo, el LMD permite la reparación de áreas críticas que hayan podido sufrir un desgaste a lo largo de su vida útil. Asimismo, es también una tecnología viable para la corrección de geometrías de pieza debido a modificaciones de última hora en el diseño.
El proceso LMD puede realizarse en diferentes máquinas que se ajusten a las necesidades del tipo de pieza a fabricar o reparación a realizar. De entre todas, las más comunes son las máquinas cartesianas o los robots como puede apreciarse en la figura 3. Las configuraciones que emplean una máquina cartesiana, actualmente pueden ser de dos tipos: en una de ellas, la máquina se dedica de forma exclusiva al proceso de aporte de material, mientras que en la otra puedan integrar procesos de arranque de material junto con procesos de aporte de material. Las empresas líderes en el mercado de ambas vertientes son DMG MORI, Yamazaki Mazak Corporation, Trumpf entre otras.
La otra opción, habitual en la aplicación de aporte láser en troqueles, es emplear un robot serie con una boquilla de aporte instalada en su último eje. De esta manera, se consigue abordar el problema que supondría introducir un troquel de grandes dimensiones en una máquina cartesiana para la ejecución de la reparación en cuestión.
![Figura. 4. Ejemplo de máquina cartesiana (dcha.) cortesía del CFAA [5], y ejemplo de robot serie con un cabezal de aporte (izda.) cortesía de TWI [6]... Figura. 4. Ejemplo de máquina cartesiana (dcha.) cortesía del CFAA [5], y ejemplo de robot serie con un cabezal de aporte (izda.) cortesía de TWI [6]...](https://img.interempresas.net/fotos/1934864.jpeg)
2. La importancia de la transferencia de calor en el proceso de estampación en caliente
En las operaciones en las que el troquel trabaja en caliente, la evacuación de calor es fundamental para poder prolongar la vida del mismo. Sin embargo, es imposible conseguir una superficie en la que el contacto sea del 100%. Como consecuencia, se encuentra huecos en los que no existe contacto.
Este hecho, conlleva a que la transferencia de calor sufra variaciones, haciendo que este pierda su uniformidad. Como el proceso se lleva a cabo con el contacto de chapas con troqueles, el coeficiente que predomina es el de conducción, pero al no estar en pleno contacto la chapa y el troquel, se establece un nuevo coeficiente que incluye estas irregularidades en la superficie denominado IHTC (del inglés interfacial heat transfer coefficient).
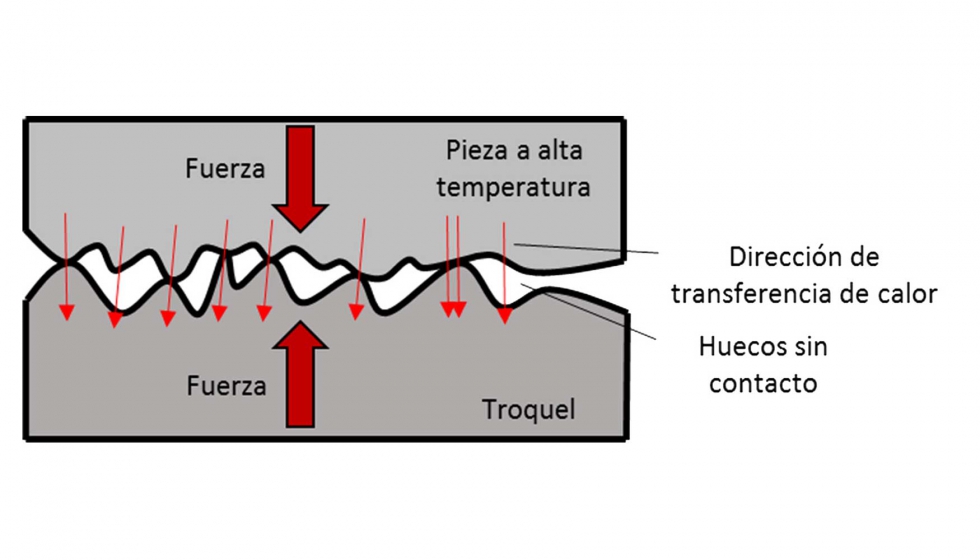
Este coeficiente ha sido y sigue siendo objeto de estudio ya que juega un papel crucial en el enfriamiento de la chapa y, por tanto, en la creación de la microestructura adecuada de la misma. En el IHTC influyen los siguientes factores [7].
- Topografía de las superficies en contacto: Como se ha mencionado anteriormente, es imposible garantizar una superficie 100% lisa y continua, por tanto, la transmisión de calor se dará únicamente entre los puntos que estén en contacto. Del mismo modo, otros factores como la presión pueden alterar el área de contacto con lo que el IHTC varía a lo largo del tiempo.
- Presión de contacto: Este factor afecta en gran medida al IHTC ya que, al haber una mayor presión, ocurre una deformación que hace que el área total real de contacto aumente, aumentando la tasa de transferencia de calor y reduciendo así el tiempo necesario de la pieza para reducir su temperatura. Este factor se ha vuelto realmente atractivo desde que la capacidad de controlar la fuerza de la prensa es una realidad en el entorno industrial.
- Propiedades termo-físicas de los materiales: El campo térmico del troquel vendrá determinado por las propiedades termo-físicas del material (densidad, calor especifico, conductividad térmica…). Por lo tanto, el material empleado para fabricar el troquel tiene un impacto directo en el IHTC, de manera que, a mayor difusividad térmica, mayor será el valor del IHTC. No es de extrañar, por tanto, que se haya comenzado a comercializar aceros de alta conductividad térmica y alta resistencia al desgaste para tratar de maximizar dicho coeficiente en lo que a la parte de ciencia de materiales se refiere.
- Recubrimiento de los materiales: Si se estampa una chapa en caliente y se enfría, se genera una capa de óxido que dificulta la transmisión de calor. De este modo, se genera una superficie que además de la reducción del coeficiente de transmisión de calor ya mencionado, aumenta también el coeficiente de rozamiento entre el troquel y la chapa. Para evitar esta oxidación, se recubren las chapas con aceite o con una aleación de Al-Si aunque, ha sido demostrado que este recubrimiento disminuye drásticamente el valor del IHTC. [8]
Gracias a las investigaciones realizadas en torno al IHTC queda patente el papel que desempeña la transmisión de calor en el proceso de estampación en caliente. A su vez, son varias las variables que influyen en el valor que toma este coeficiente teniendo un impacto directo en el producto final. El estudio y control de estas variables conllevará a piezas con propiedades mecánicas mejoradas.
3. Capacidades y retos de la tecnología LMD en troqueles
Como se ha mencionado anteriormente, la tecnología aditiva ofrece grandes ventajas en la reparación de geometrías de troqueles. De entre todas las posibilidades, el proceso LMD destaca por la flexibilidad que ofrece la inyección de polvo para poder ser ejecutada en cualquier entorno.
Si bien es cierto que la fabricación aditiva ofrece muchas posibilidades a la hora de crear geometrías complejas, no es una tecnología exenta de retos ya que aun habiendo demostrado ser una gran opción a la hora de realizar reparaciones, aún quedan campos en los que se requiere más investigación.
3.1. Capacidades del proceso LMD en troqueles
La aplicación más intuitiva de la fabricación aditiva, en este caso el proceso LMD, son las reparaciones de troqueles. El desgaste en los troqueles se caracteriza en gran medida por las grietas que sufren el punzón y la matriz. En el proceso de estampación en caliente a las fuerzas que ya existen en el proceso hay que sumar los ciclos térmicos que sufre la herramienta que actúan como catalizadores de la creación y propagación de grietas.
Anteriormente, la reparación de dichas grietas se realizaba mediante recargues manuales de material mediante la soldadura. Este método suponía una inversión mucho menor que la compra de un nuevo troquel y es por ello que optaba por esta opción.
No obstante, al ejecutar dichas reparaciones se dependía en gran medida de la pericia y experiencia del operario que reparase la superficie afectada. Del mismo modo, los métodos tradicionales de soldadura introducen grandes cantidades de calor de manera poco focalizada dejando una zona afectada térmicamente relativamente grande pudiendo afectar a las propiedades de la herramienta.
Ante los puntos previamente expuestos, el aporte láser ofrece como respuesta una automatización del proceso, pudiendo así elevar la precisión con la que se realiza la reparación y evitando incertidumbres inherentes al factor humano. En apartados anteriores se ha presentado el láser como una fuente de calor capaz de concentrar en áreas muy pequeñas grandes cantidades de calor. Gracias a esta propiedad, la zona afectada por el calor se reduce notablemente, manteniendo así las propiedades del troquel.
En el apartado 3 se menciona la importancia que tiene la transmisión de calor en el proceso de estampación en caliente. La evacuación de calor y la velocidad con la que ese calor se evacua tienen un impacto directo en el producto final. Tradicionalmente, esta refrigeración se ha realizado mediante conductos rectos lo más cerca posible del foco de calor.
El conformal cooling consiste en generar conductos adaptados a la geometría en la que se encuentra el foco de calor. El objetivo es aumentar la tasa de evacuación de calor, optimizando la posición de los conductos, fabricándolos más cerca del foco de calor. Desde la UPV/EHU se han estudiado casos representativos de la reparación y fabricación de geometrías en 5 ejes de troqueles [7].
![Figura. 6. Aspecto final del troquel en 3D [7] Figura. 6. Aspecto final del troquel en 3D [7]](https://img.interempresas.net/fotos/1934866.jpeg)
Al ser el LMD una tecnología capaz de operar tanto en 3 como en 5 ejes, es posible la reparación de geometrías complejas en troqueles, habilitando así el alcance a prácticamente cualquier superficie: Habiéndose caracterizado y optimizado los parámetros de aporte, es posible lograr todo tipo de geometrías.
Otra de las capacidades que aún se encuentra en desarrollo es la capacidad de embeber sensores en la matriz en el punzón. Estos sensores ayudarían a la monitorización y control de parámetros del proceso de estampación en caliente como la temperatura de la matriz. Sin embargo, esta aplicación aún se encuentra en desarrollo ya que es necesario encontrar la manera de poder introducir sensores en el troquel sin dañarlos por el calor o por el material a la hora de solidificar.
3.2. Retos del proceso LMD en troqueles
Uno de los retos que existen hoy en día en torno a la implementación de la fabricación aditiva en los troqueles reside en la etapa de diseño. Para poder hacer uso de las ventajas que aportan las tecnologías de fabricación aditiva es necesario un cambio en el paradigma de diseño.
Es una realidad que la fabricación aditiva presenta una serie de limitaciones que, aún hoy en día, no se tiene en cuenta a la hora de realizar el diseño del troquel. Para superar dicho reto, se deberá ser capaz de diseñar troqueles de estampación en caliente teniendo en cuenta las restricciones del proceso de aporte por láser, alcanzando un compromiso entre un diseño ideal y una pieza de fabricación viable.
Para las condiciones de estampado más exigentes, se emplea la serie H de AISI. Estos aceros de herramientas son específicos para trabajos en caliente y es por ello, que la gran mayoría de troqueles destinados a estos procesos de estampación en caliente están fabricados en este material. Sin embargo, estos aceros contienen un alto porcentaje de componentes de aleación, lo cual les resta ductilidad a cambio de una elevada dureza y resistencia al desgaste.
Debido a esta falta de ductilidad, tenacidad de estos aceros disminuye, haciéndolos susceptibles de sufrir grietas después del proceso de solidificación, debido a las tensiones residuales inherentes al proceso LMD. Es por ello, que la serie AISI H es objeto de estudio por los grupos de investigación a lo largo del mundo. El objetivo es encontrar una solución que permita el aporte de este material con garantías, libre de poros o grietas que afecten a las propiedades mecánicas o a las características frente al desgaste que éstos aceros ofrecen.
Del mismo modo, las piezas que se obtienen mediante LMD presentan un acabado superficial pobre, y que requiere de un mecanizado posterior. Es sabido que el acabado de los troqueles presenta una rugosidad superficial exigente. Por esta razón, obtener piezas near-net-shape es solamente posible en términos estructurales y no en acabados superficiales.
4. Conclusiones
La investigación del contacto en troqueles está permitiendo obtener piezas de mayor calidad y de propiedades mecánicas más conocidas y controladas. Gracias a la definición y estudio del IHTC (interface heat transfer coefficient) se está consiguiendo un mayor control y conocimiento tanto del proceso como del producto. Por tanto, este coeficiente se presenta como una de las claves más importantes para la obtención de productos de alto valor añadido.
La fabricación aditiva ofrece una serie de ventajas que anteriormente no podían alcanzarse debido a restricciones geométricas. El ejemplo del conformal cooling ilustra la capacidad del aporte láser de generar geometrías complejas donde las tecnologías de arranque de viruta no podían operar. Así mismo, ha demostrado ser una tecnología consolidada en el campo de la reparación de troqueles; sustituyendo los métodos tradicionales empleados para efectuar dichas reparaciones.
El aporte de aceros de herramientas es un proceso que requiere una optimización minuciosa de parámetros para lograr aportes de material con garantías, es decir, libres de poros o grietas que puedan comprometer las propiedades que tiene que tener dicho aporte. El aporte de dicho material es, por tanto, objeto de estudio por los grupos de investigación.
Para poder conseguir una implementación total del proceso de aporte láser en la fabricación y reparación de troqueles, es necesario diseñar éstos teniendo en cuenta las limitaciones del proceso de aporte láser para poder hacer uso de las ventajas que la fabricación aditiva brinda.
Las piezas obtenidas mediante la tecnología LMD, aunque pueden ser clasificadas como piezas near-net-shape o piezas cuya forma es muy cercana a la final, presentan un acabado superficial que dista mucho del requerido por los troqueles. Esto implica que las tecnologías de arranque de viruta seguirán jugando un papel importante a futuro, haciéndonos recordar que ambas tecnologías, aditiva y sustractiva, son complementarias, no suplementarias.
Referencias
[1] Arrizubieta, J.I.; Ruiz J.E.; Cortina, M.; Ukar, E.; Lamikiz, A. Evaluación de la sobreacumulación de material en los cambios de dirección durante el proceso de aporte por láser mediante un modelo integral. Revista Iberoamericana de Ingeniería Mecánica 2018, 22 (2), 3-12.
[2] Arrizubieta J.I., Ruiz J.E., Martínez S. Ukar E., Lamikiz A. «Intelligent nozzle design for the Laser Metal deposition process in the industry 4.0» Procedia Manufacturing vol 13, pp 1237-1244, 2017.
[3] Ruiz, J.E.; Gonzalez, H.; Cortina, M.; Arrizubieta, J.I.; Lamikiz, A. Desarrollo de estrategia y sensorización en proceso de LMD para reparación de geometrías tipo blisk. Revista Iberoamericana de Ingeniería Mecánica 2018, 22 (2), 13-18.
[4] Cortina, M.; Arrizubieta, J.I.; Ruiz J.E.; Ukar, E.; Lamikiz, A. Análisis de la influencia del uso de fluido de corte en procesos híbridos de mecanizado y aporte por láser. Revista Iberoamericana de Ingeniería Mecánica 2018, 22 (2), 33-39.
[5] Centro de Fabricación Avanzada Aeronautica (CFAA)
[6] The Welding Institute (TWI)
[7] Cortina M., Arrizubieta J.I., Calleja A., Ukar E., Alberdi A. «Case Study to Illustrate the Potential of Conformal Cooling Channels for Hot Stamping Dies Manufactured Using Hybrid Process of Laser Metal Deposition (LMD) and Milling» Metals 2018, 8, 102.
[8] Y. Chang, X. Tang, K. Zhao, P. Hu, Y. Wu, «Investigation of the factors influencing the interfacial heat transfer coefficient in hot stamping» Journal of Materials Processing Technology, vol. 228, pp. 25-33, 2016.e