Durante la fase de compactación, ¿trabajamos con las entradas abiertas o selladas?
No siempre es conveniente trabajar con entrada sellada o lo que es lo mismo aplicar un tiempo de compactación suficiente para que la entrada se congele y se cierre, determinado este tiempo bien a través de la evolución de los pesos de las piezas inyectadas o de la caída de presión en cavidad si disponemos de sensores de presión en cavidad. (Ver artículo publicado 'Compactación y mantenimiento, pack and hold, dos fases de la misma etapa')
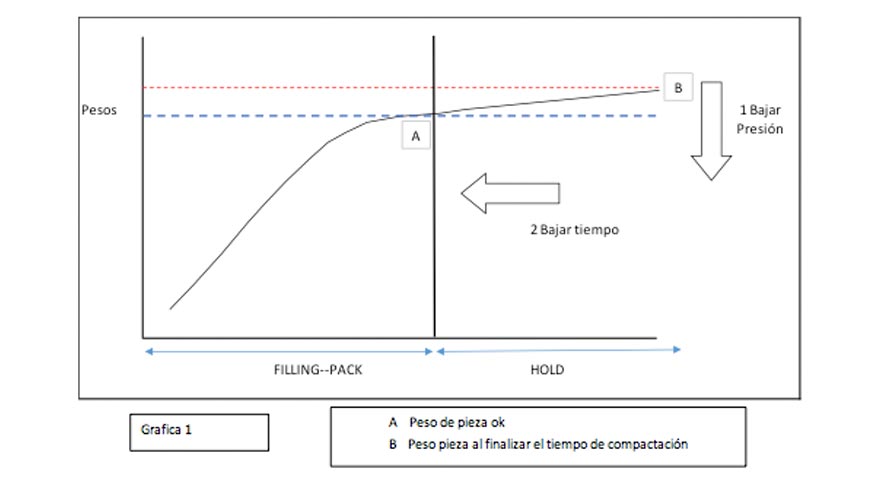
Esta decisión dependerá del tipo de pieza que vamos a inyectar.
Entrada sellada
Ventajas de la entrada sellada:
- Repetibilidad en las dimensiones y los pesos.
- Proceso más robusto y repetitivo.
- Inconvenientes de la entrada sellada.
- Posibles tensiones en las zonas cercanas a las entradas sobre todo cuando éstas son grandes o tenemos canales. calientes o boquillas de obturación.
Entrada abierta
Ventajas de la entrada abierta:
- Pocas tensiones en las zonas cercanas a las entradas.
- Inconvenientes de la entrada abierta.
- Dispersión en medidas y en pesos.
- Imprescindible alta precisión de la máquina en el punto de conmutación, proceso tiempo dependiente.
- Proceso 'tiempo dependiente'.
La recomendación es ensayar mecánicamente y con los procesos posteriores si los hubiera, soldadura, pintado, serigrafía, metalizado, cromado, etc. para determinar influencia de las presiones y el tiempo de compactación.
En resumen
Si bien la entrada cerrada o sellada nos aporta más repetibilidad de proceso y evita posibles reflujos o 'Flow back' del material, la decisión de trabajar con entrada cerrada o abierta la debemos tomar en función de la pieza que vamos a inyectar. Hay que tener en cuenta que la zona cercana a la entrada es siempre una zona con características físicas y de resistencia química diferentes al resto de la pieza.
Lo recomendado es ensayar piezas en test obtenidas con ambos métodos (entrada cerrada y abierta) y testar propiedades mecánicas, químicas, etc. y seleccionar el sistema que nos aporta piezas con mejores propiedades.
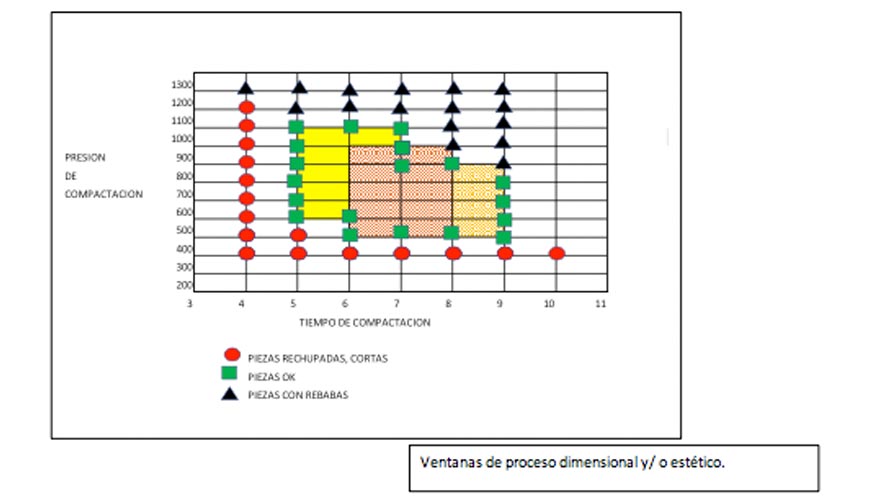
¿Y cuándo el peso no deja de aumentar?
En la mayoría de los casos, podremos seleccionar qué sistema nos interesa más, con entrada abierta o con entrada cerrada. No obstante, se pueden dar ocasiones donde el peso no se estabiliza, por ejemplo.
- Sección de entrada grande.
- Material muy fluido o materiales blandos, tipo TPE, TPV, TPU.
- Altos niveles de presión de compactación.
- Utilización de canales calientes.
- Utilización de boquillas de obturación en canales calientes.
Podemos observar que al realizar un estudio del tiempo de sellado de la entrada, el peso no deja de crecer. Cuando esto sucede, estamos haciendo entrar material en la cavidad cuando el polímero está empezando a enfriarse (recordemos que el polímero no avanza. Prácticamente está parado por lo que no hay aportación de calor por cizalla).
Esta situación provoca que la zona cercana a la entrada quede con un alto nivel de tensiones internas material desplazado en estado semi sólido) y con una gran orientación forzada.
Para evitar esta situación podemos plantearnos la siguiente metodología:
Podemos ir incrementando el tiempo de compactación y veremos que los pesos van aumentando siguiendo una proporcionalidad (igual que en la gráfica 1), con una tendencia similar. En el momento en el que obtenemos piezas correctas, bien por aspecto, por dimensiones, o ambas, fijamos éste como el peso ideal de la pieza, en el gráfico posición A. Si continuamos incrementando los tiempos de postpresión, en los casos antes comentados, los pesos irán aumentando. Esta vez con una proporcionalidad menor puesto que ya tenemos la cavidad presurizada.
En este cambio de tendencia del crecimiento de los pesos, hemos de presuponer que la cavidad está llena de material y que a partir de ahí el resto de material que estamos aportando con más tiempo de postpresión es material empaquetado en las zonas cercanas a la entrada y alcanzaremos el peso de pieza máximo, posición en el gráfico B.
1. En ese momento, bajamos el nivel de postpresión poco a poco hasta obtener inyectadas con el peso ideal A que tenemos registrado como peso objetivo con piezas buenas estética y /o dimensionalmente.
Una vez obtenido de nuevo el peso ideal a través de esta bajada de presión de compactación, 2 iremos reduciendo el tiempo de aplicación de la presión de compactación sucesivamente.
Habrá un momento en que el peso empezará a reducirse, esto quiere decir que hemos llegado al codo de la curva, pero esta vez reduciendo tiempos de compactación.
En este punto debemos añadir 2 o 3 segundos al tiempo de compactación programado para asegurar que estamos en la parte plana de la curva donde no se produce aumento de peso pero tampoco se produce reflujo o 'back Flow' del material.
Estaremos en este punto en el peso ideal A y con el tiempo de compactación en la fase de 'hold' para asegurar el sellado de la entrada de la cavidad sin que aumente el peso y por tanto, no crearemos tensiones residuales por la introducción de material semi sólido, en la cavidad.
¿Y con canales calientes o con boquillas de obturación?
Podemos realizar también un estudio de área de moldeo o ventana de proceso. Esta ventana de proceso puede ser dimensional o puede ser estética o ambas, dependiendo del tipo de pieza, sector, etc.
El procedimiento es por ejemplo:
1.- Fijamos el valor de la presión de compactación en 250 bares, con este valor realizamos una batería de inyectadas con diferentes tiempos de compactación, desde 4 segundos hasta por ejemplo 10 segundos. En este paso verificamos si las piezas obtenidas son correctas, tienen rebabas o presentan rechupes.
2.- Seguidamente fijamos de nuevo el valor de la presión de compactación en un valor superior al anterior, por ejemplo 400 bar y repetimos la batería de tiempo de compactación entre 4 y 10 segundos.
Repitiendo estos pasos hasta niveles de presión de compactación que producen piezas defectuosas en toda la gama de tiempos de postpresión. Podremos con esta información construir un diagrama de área de moldeo o ventana de proceso.
Seleccionando una combinación de presiones de compactación y de tiempos de compactación en la zona central de las ventanas de proceso generadas, estaremos en la zona más robusta del proceso. En este caso, el tiempo de postpresión seleccionado no sería el tiempo que nos aporta una estabilidad en los pesos sino un tiempo que nos aporta calidad estética y dimensional al margen de los pesos.
Si nuestro objetivo es parametrizar un proceso robusto y repetitivo, en la fase de pack and hold, debemos aplicar métodos que nos aseguren esta repetibilidad en esta fase tan critica del proceso, donde estamos definiendo características tales como dimensiones, peso, etc.
José Ramón Lerma es autor del Libro Manual Avanzado de Inyección de Termoplástico, que tiene como objetivo ser, por un lado, una herramienta para la formación y, por otro, un manual de ayuda para todo el personal de una empresa de inyección de plásticos. El libro, comercializado por Plásticos Universales / Interempresas (libros@interempresas.net), consta de detallados casos prácticos, amplia información de moldeo científico y un ‘pendrive’ con 20 hojas de cálculo y herramientas de SC Molding o Scientific Injection Molding, además de optimización y definición de proceso, lo que lo hacen único en el mercado. Página web sobre Scientific Injection Molding: www.asimm.es
Más información sobre los cursos Scientific Molding online impartidos en Inefco, en los que José Ramón Lerma es tutor https://www.ieaula.com/home/31-procesos-avanzados-de-inyeccion-de-termoplasticos.html