Entrevista a David Pozo, director técnico de Factory & Process Automation, experto en Industria 4.0 de Siemens España
Industria 4.0, fábrica del futuro, ciberindustria… son conceptos basados en una manera de organizar los medios de producción. Se conoce también como la 4ª revolución industrial pero, exactamente, ¿qué cambios supone para una industria actual?
La IV revolución industrial supone la integración de las TIC en los procesos industriales y en las nuevas formas de fabricación de materiales. Esto da lugar a una serie de ventajas que sin duda marcan un antes y un después en la industria tal y como la conocemos hoy en día. Estas ventajas son la personalización de la producción en masa, procesos más rápidos y baratos, reducción del 'time-to-market' en hasta un 50%, productos más complejos, mayor volumen de información (nuevo motor de la economía) y además afectará a cómo y dónde se hacen las cosas. Por ejemplo, la localización de las fábricas cerca de los clientes permitirá responder más rápido y mejor a sus necesidades, lo que supondrá importantes ahorros. Además de una mayor eficiencia de energía y recursos, así como más flexibilidad para adaptar la producción a una demanda variable.
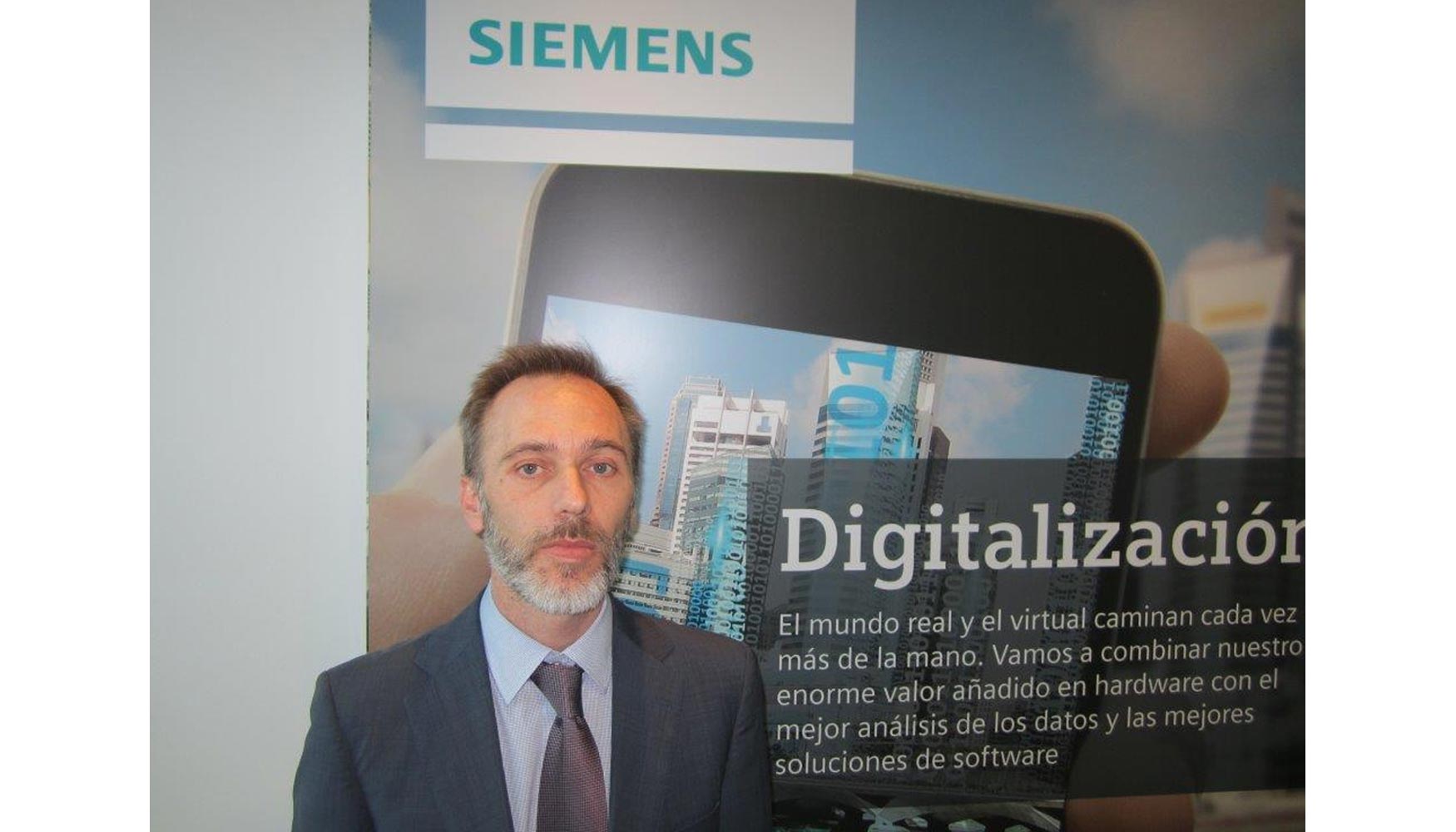
“Desde Siemens somos conscientes desde hace tiempo de que fenómenos como la incorporación de sensores y automatismos en la producción, Internet de las cosas o la gestión del Smart Data están revolucionando el mundo”, afirma David Pozo.
¿Qué significa la conectividad total en una planta de producción? Ya no sólo hablamos de automatización y lenguaje de máquinas…
Un claro ejemplo del futuro de la industria lo tenemos en la fábrica de Maserati en Turín. Se trata de una planta de producción conectada de forma digital a través de nuestra tecnología. El éxito de la planta de Maserati es un ejemplo perfecto de los beneficios que puede aportar la digitalización a los fabricantes de automóviles. Y es que en esta fábrica, la digitalización forma parte de todas las funciones que intervienen en el proceso de desarrollo y fabricación de un vehículo, desde la fase inicial de diseño hasta su comercialización, pasando por la simulación, las pruebas o la preparación de las líneas de producción. Por ejemplo, los componentes de los coches son desarrollados a través de la tecnología de Siemens NX, los procesos de producción se simulan utilizando la cartera de productos Tecnomatix, y Siemens TIA Portal se utiliza para la automatización flexible de la línea de producción. Los complejos procesos de producción están planificados, optimizados y controlados con el software Simatic IT MES. En este caso, la combinación virtual y real de Maserati permite reducir el tiempo de desarrollo de los vehículos en un 50%, flexibilizar la producción (modelos disponibles en 27 versiones, 13 colores y 205 configuraciones distintas) y, por supuesto, aumentar la eficiencia.
¿Qué ventajas a corto plazo puede advertir una empresa que apueste por la digitalización de procesos? ¿Puede ponernos algún ejemplo sobre, p.ej. el ahorro de costes que le supondría?
Las empresas que apuesten por la digitalización de sus procesos de fabricación pueden obtener diferentes beneficios. Entre ellos, cabe destacar un aumento de la productividad en un 20%, según hemos podido comprobar con datos de nuestros clientes. Además, la digitalización hace que las fábricas sean más eficientes. Por ejemplo, nuestra tecnología PLM puede reducir en algunos casos hasta un 80% el tiempo de instalación. Otro caso de eficiencia lo encontramos en la depuradora de Vigo, la estación depuradora de aguas residuales más grande de España y una de las mayores de Europa. Esta depuradora utiliza nuestra tecnología Simatic PCS7 que le permite maximizar la eficiencia en el consumo y ahorrar hasta un 40% los tiempos de desarrollo. Por otro lado, Siemens también dispone de un software integrado de ingeniería para diseñar plantas de producción en mucho menos tiempo y con un gran ahorro de costes. Se trata de Comos, que logra reducir el tiempo del proyecto un 12% y sus costes un 9% porque, entre otras razones, el 90% de la documentación que se emplea durante el proceso es ya digital.
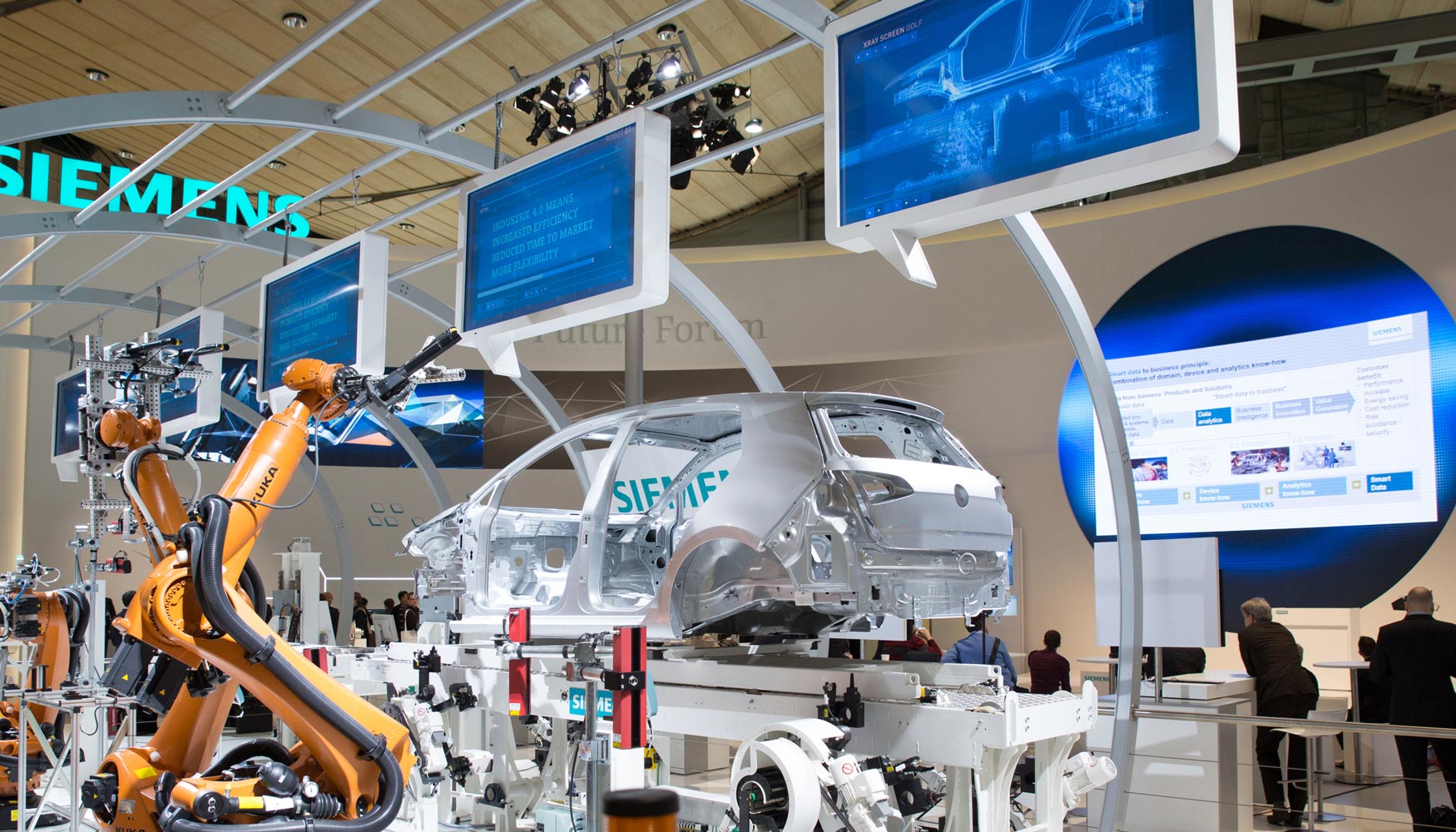
El sector de la automoción es uno de los que más ha apostado por la digitalización en planta. Foto: Siemens AG.
Estamos hablado de la automatización (cuasi) total… ¿Qué limitaciones tiene?
En principio, para el mercado español, compuesto por pequeñas y medianas empresas en su mayoría, una de las limitaciones más importantes son los problemas de acceso a la financiación para invertir en tecnología. Tenemos que cambiar este modelo y facilitar su acceso. En este sentido, Siemens Financial Services acompaña a las empresas en los procesos de financiación para que puedan acometer sus proyectos más fácilmente.
Centrándonos en Siemens, ¿qué papel juega en este proceso, en el impulso de Internet de las Cosas (IoT)?
Desde Siemens somos conscientes desde hace tiempo de que fenómenos como la incorporación de sensores y automatismos en la producción, Internet de las cosas o la gestión del Smart Data están revolucionando el mundo. Por ello, Siemens acompaña a la industria en esta revolución como la primera compañía europea con Fábrica Digital como una división de negocio. De hecho, hemos invertido 4.000 M€ en la compra de compañías de software y contamos con más de 17.000 ingenieros de software. El mundo gira hacia lo digital y quien se muestre ajeno a este fenómeno perderá el tren.
¿Qué soluciones están actualmente ya disponibles para implementar?
Actualmente, Siemens dispone de soluciones innovadoras para la puesta en marcha de la Industria 4.0. Con nuestra Digital Enterprise Software Suite, los clientes ya pueden invertir en soluciones de futuro, para la aplicación progresiva de los conceptos de la Industria 4.0 en sus fábricas. Nuestra propuesta se compone de cuatro elementos básicos: Digital Enterprise Software Suite, que ayuda a digitalizar toda la cadena de valor en la industria; Redes de comunicación Industriales, como Profinet, que consta de componentes para la comunicación inalámbrica industrial, switches Ethernet, productos Rugged.Com, Simatic Net, Sinema Server, etc.; Seguridad en la automatización, donde ofrecemos productos y servicios que garanticen la seguridad industrial; Y servicios industriales específicos del negocio, con una amplia gama de propuestas derivadas de las nuevas posibilidades que ofrece la digitalización en la industria.
Siemens ha puesto en marcha su modelo digital en la planta de producción de los controladores Simatic. ¿Puede considerarse un ejemplo de Industria 4.0? ¿Puede explicarnos qué características la definen?
La fábrica de Siemens en Amberg ha conseguido establecerse como un referente dentro del mundo industrial ya que es, a día de hoy, una de las plantas más eficientes de Europa. En sus instalaciones se producen diariamente más de 1.000 versiones de autómatas de la gama Simatic que son comercializados en todo el mundo. Entre sus muchas características, la fábrica de Amberg dispone de un porcentaje de calidad casi perfecto: logra producir Simatic con un ratio de calidad del 99,9988%; produce un Simatic cada segundo; realiza envíos en 24 horas; gracias a la calidad de su cadena de producción la fábrica es capaz de cubrir las demandas de sus más de 60.000 clientes de un día para otro; Con los propios sistemas Simatic instalados en la planta se ha conseguido que el 75% de la producción se realice de manera autónoma. Y cuenta con la digitalización de la producción: los productos se comunican con las máquinas y todos los procesos están optimizados mediante control IT. Gracias a la combinación del trabajo real con el uso de las TIC, se ha conseguido aumentar ocho veces la producción.
¿Qué nivel de innovación y desarrollo de tecnologías para IoT están presentes en Europa? Las principales empresas desarrolladoras están en EE UU….
Cada vez más las empresas europeas apuestan por la innovación y el desarrollo de nuevas tecnologías. Pero es cierto que en el caso de España se invirtió el pasado año un 1,24% del PIB en actividades de I+D+i, (según estudio de EAE Business School), lo que supone un 3% menos que en el año anterior y una caída acumulada del 11% desde 2008. Además, España es el cuarto país de la Unión Europea con menor exportación en tecnología punta, según los datos del Eurostat recogidos por el Instituto e Estudios Económicos (IEE). Una tendencia que hay que cambiar porque el futuro en Europa lo va a marcar precisamente IoT. De hecho, estudios recientes apuntan a que el valor potencial del Internet de las Cosas llegará a un billón de euros en Europa en 2025. Es más, se trata de una apuesta de futuro que tendrá una compensación económica. Según un estudio de A.T. Kearney, cada euro dedicado a soluciones para Internet de las Cosas (IoT, por sus siglas en inglés) podría generar hasta doce euros en ganancias de productividad, poder adquisitivo y ahorro de tiempo. También asegura que el mercado de soluciones para IoT llegará a 80.000 millones en Europa en 2025.
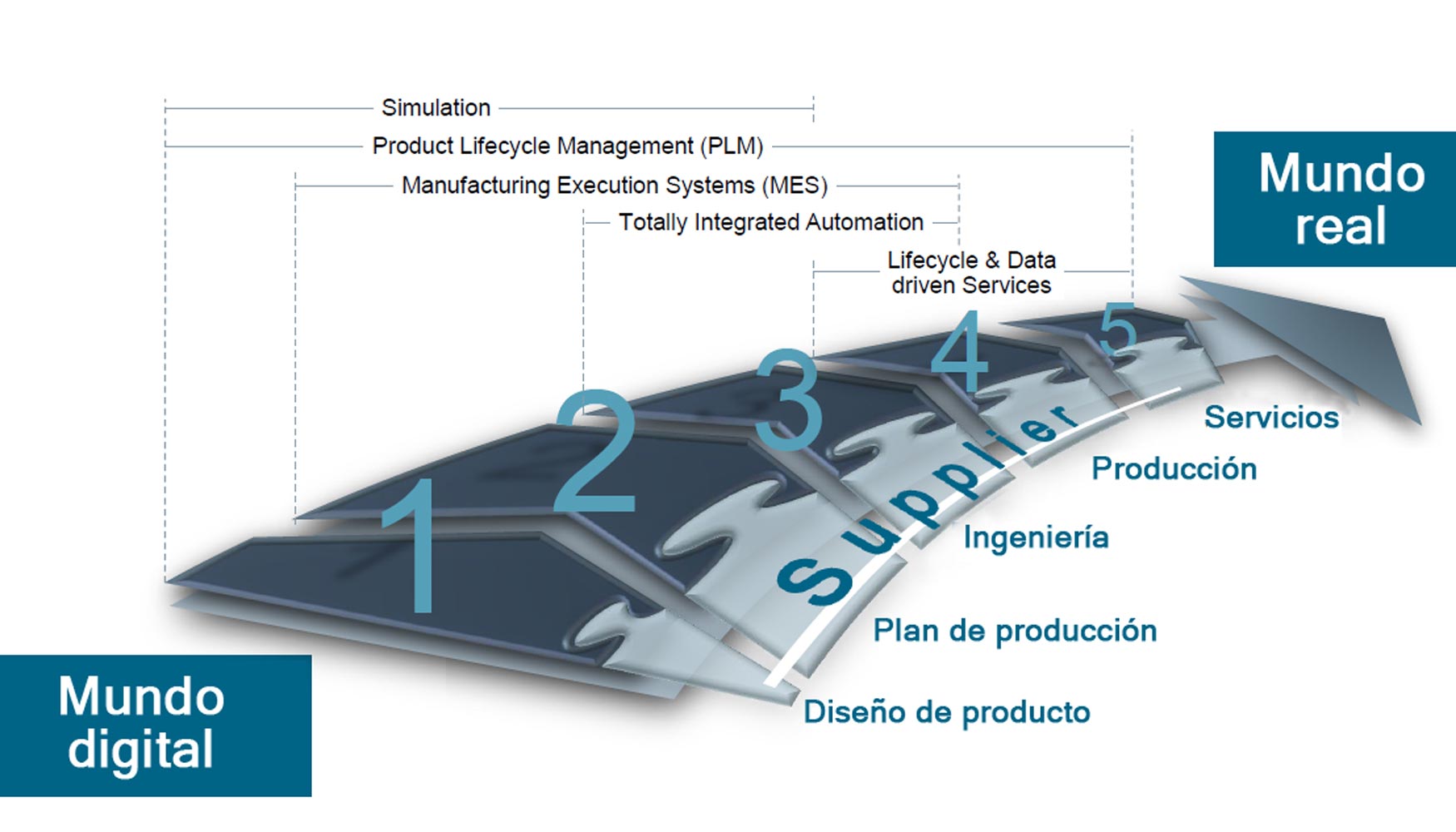
Cadena de valor en la que, desde el diseño de producto al servicio, están digitalizados e integrados. Foto: Siemens AG.
¿Están las factorías de los países industrializados preparadas para alcanzar un mundo en el que instalaciones, almacenes y máquinas puedan intercambiar información, actuar por cuenta propia y vigilarse mutuamente?
Estamos iniciando el camino, sobre todo en lo que se refiere a ciberseguridad. De hecho, los ataques a plantas industriales son ya una realidad que se verá incrementada en el futuro si no aumentamos la protección. Para poder proteger una planta de producción así como los sistemas de automatización, la ciberseguridad se convierte en esencial. La expansión del Internet de las Cosas hace que, cada vez más, los equipos industriales estén conectados. Debido a ello, cualquier cadena de producción puede sufrir el espionaje de datos confidenciales, el sabotaje de la propia producción en planta, sus tiempos de parada, la manipulación de los datos o del propio software de aplicación o el uso no autorizado de funciones del sistema.
De hecho, uno de los requisitos será pasar del mundo físico al virtual. Pero la seguridad, o la desconfianza en ella, es uno de los principales motivos para que muchas empresas se muestren reticentes…
Claro. Por eso, desde Siemens hemos creado una serie de productos que responden a la creciente necesidad de disponer de sistemas de protección industrial. De este modo, ayudamos a combatir los ciberataques y a proteger las instalaciones críticas de un modo eficiente y seguro, tanto en acceso remoto a instalaciones como en protección genérica. La compañía dispone de cortafuegos industriales, que son dispositivos que permiten restringir o permitir el tráfico de información en función de quien quiera acceder o los protocolos que se vayan a utilizar. Sistemas de automatización con funciones de seguridad integradas que incorporan funciones de seguridad a los sistemas de control estándar, entre otros. Y routers industriales, que ofrecen una conectividad segura para diferentes tipos de comunicación. De esta forma, se pueden establecer comunicaciones seguras mediante redes privadas virtuales.
En su opinión, ¿en qué sectores industriales se implantará con mayor facilidad? ¿Y en cuáles costará más? ¿Y por qué?
Aunque son numerosos los sectores que pueden ser víctimas de un ciberataque, algunos como el financiero, el energético, el transporte, las telecomunicaciones o el suministro de agua son más vulnerables de sufrir sus consecuencias. Los efectos de estas amenazas son importantes, ya que pueden abarcar desde el riesgo de muerte y heridas graves, hasta un desastre medioambiental, perdidas financieras o de propiedad intelectual, eliminación o disminución de la calidad de la producción o daño a la imagen corporativa.
Para finalizar, siendo realistas, ¿Cómo se puede impulsar el cambio allí donde, a duras penas, están todavía en la industria 2.0?
Es necesario que tanto empresas como instituciones públicas sean conscientes de la necesidad de una industria fuerte para tener un país competitivo que genere riqueza. Para subirse al tren de la Empresa Digital es necesario realizar una fuerte inversión en tecnología, porque sin la mejor tecnología ningún país o comunidad podrá afrontar los nuevos desafíos globales a los que nos enfrentaremos en el futuro. Afortunadamente esa inversión puede ser gradual y es nuestra labor analizar y entender primero el funcionamiento de una empresa para proponerle a continuación las medidas que mayores beneficios le pueden reportar. Si queremos crear una España distinta, innovadora y competitiva con un modelo productivo sólido es clave apostar por la tecnología y, en especial, por la digitalización.