Mecanización del sostenimiento de roca en minería subterránea
Francisco Javier Pérez Lira. Ingeniero de Minas. Departamento de Minería, Túneles y Sondeos INSERSA
29/09/2021En un contexto de minería subterránea, la efectividad del sostenimiento es importante por dos razones principales: la seguridad de las personas y los equipos involucrados en la operación y lograr la extracción más económica de mineral con la mínima dilución posible.
El tipo de sostenimiento requerido para una excavación va a depender de varios factores: los esfuerzos presentes en el macizo rocoso, la geometría de la excavación, el estrés presente en la roca, los daños originados por las voladuras, los procesos de deterioro y corrosión de los elementos de sostenimiento, etc.
Para mantener la capacidad de carga portante cerca de los límites de una excavación subterránea se pueden emplear dos técnicas diferentes de estabilización (Windsor and Thomson, 1992):
- Refuerzo de roca: El refuerzo de roca hace referencia a los elementos instalados en taladros perforados en la roca como, por ejemplo, bulones de adherencia o de fricción y cables cementados. Los elementos de refuerzo de roca proporcionan una estabilización eficaz, ya que ayudan a que el macizo rocoso se sostenga a sí mismo (Hoek and Brown, 1980).
- Sostenimiento de roca: se considera que el sostenimiento es exclusivamente de los elementos que se ubican en la superficie expuesta de la roca, por ejemplo, la malla de acero, correas, hormigón proyectado, cerchas. Los elementos de sostenimiento son externos a la roca y responden a un movimiento significativo del macizo rocoso que rodea a la excavación.
Como norma general, entendemos por sostenimiento de una excavación subterránea la combinación de los sistemas de refuerzo y soporte. Es una práctica normal diseñar el refuerzo para actuar junto con los elementos de soporte y así configurar un esquema adecuado de sostenimiento (Windsor and Thompson, 1992).
Por otro lado, cabe señalar la importancia de aplicar adecuadas prácticas de voladuras y el correcto saneo de la excavación previo al sostenimiento, que ayudará a reducir la cuantía de bloques sueltos que deban ser sostenidos, mejorando así el comportamiento autoportante del macizo rocoso.
Thompson y Windsor (1992) realizaron una clasificación de los tipos, funciones, mecanismos básicos y comportamiento de los diferentes sistemas de sostenimiento y refuerzo de roca comerciales disponibles. Con el fin de explicar los mecanismos básicos de transferencia de carga entre el elemento de refuerzo y la masa rocosa, se diferencian tres categorías.
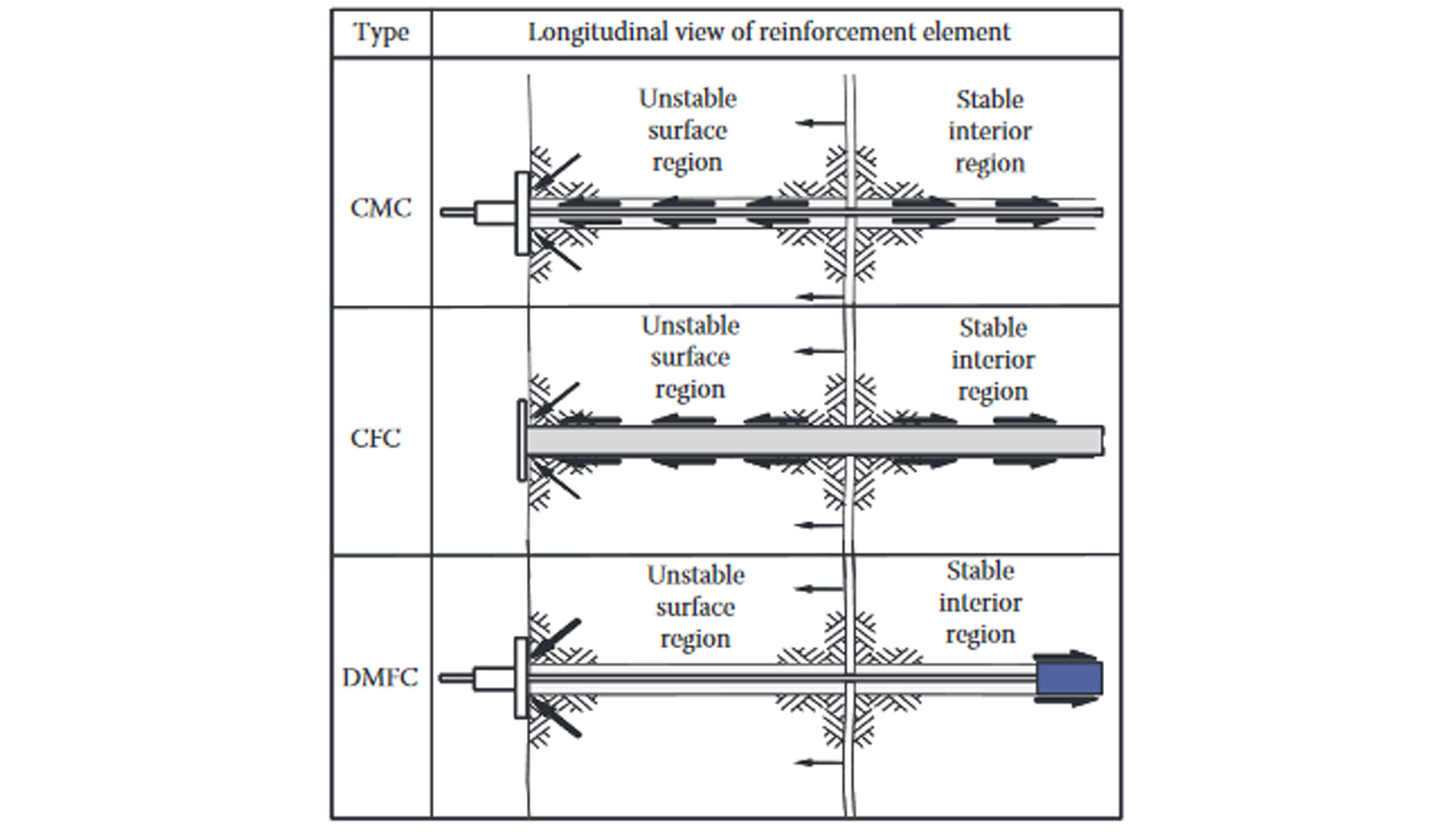
Las categorías se muestran en la figura 1. Se describen como acoplamiento mecánico continuo (CMC), acoplamiento por fricción continua (CFC) y acoplamiento mecánico y por fricción discreto (DMFC).
En la siguiente tabla se recogen algunos elementos de refuerzo típicos agrupado en cada una de las categorías:
Tipo | Descripción |
CMC | Barras de acero ancladas con inyección de lechada de cemento o resina o con cartuchos de cemento o resina. Cables inyectados con lechada de cemento o resina. |
CFC | Bulones de fricción (Split set, Swellex) |
DMFC | Anclajes mecánicos (CT y HGB Bolts) |
Los elementos de refuerzo englobados en la primera categoría (CMC), dependen de un agente fijador, normalmente cemento o resinas, que rellenan el espacio anular entre la barra de acero o el cable y el taladro realizado en la roca. La principal función del elemento fijador o de relleno es proveer un mecanismo de transferencia de carga entre la masa rocosa y el elemento de refuerzo, en este caso, la barra o el cable.
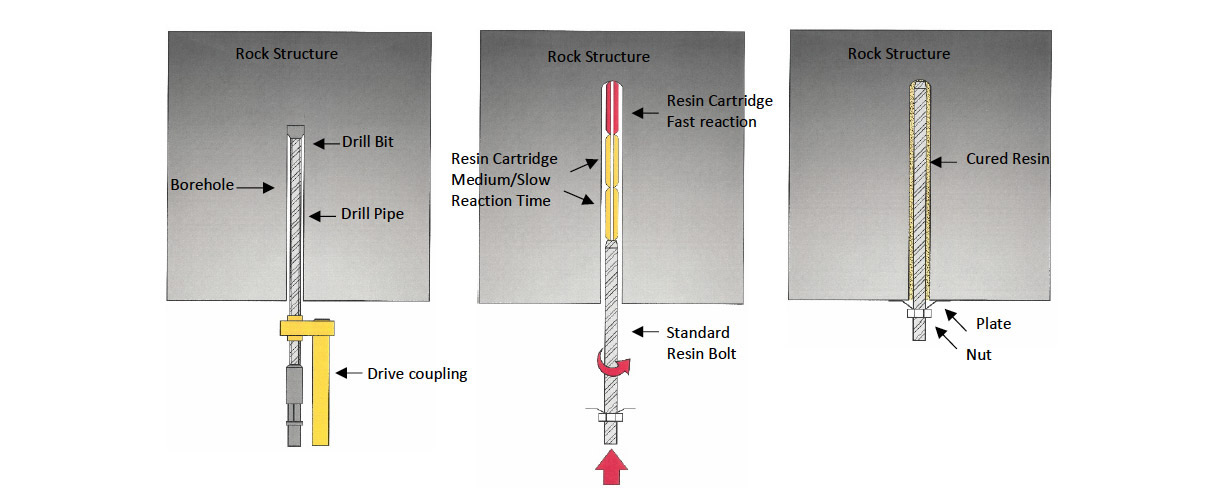
Por otro lado, los elementos de refuerzo englobados en la segunda categoría correspondiente al acoplamiento por fricción continua (CFC), son instalados en contacto directo con la roca. El mecanismo de transferencia de carga será en función de las fuerzas de rozamiento desarrolladas entre el elemento de refuerzo y la pared del taladro en el que se instala. La transferencia de carga vendrá limitada por el esfuerzo radial establecido durante la inserción del elemento de refuerzo en el taladro. Las fuerzas de unión estarán en función del diámetro del elemento de refuerzo, del diámetro del taladro y de cualquier irregularidad que aparezca en la pared de dicho taladro.
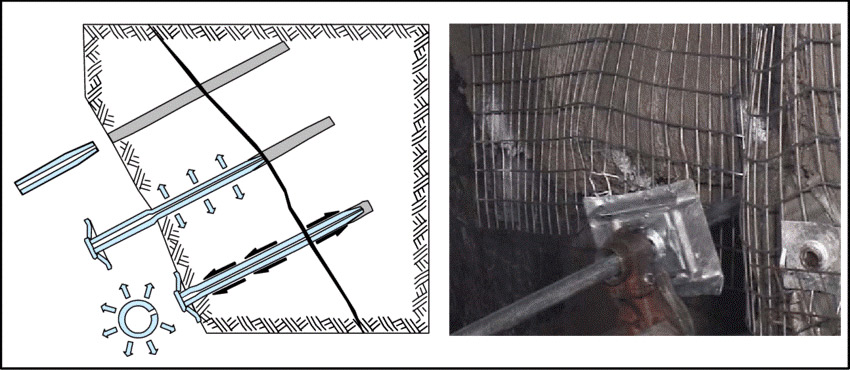
Por último, los elementos de refuerzo englobados en la categoría DMFC (Discrete Mechanical and Friction Coupled) transfieren la carga a dos puntos, el de anclaje, ubicado dentro del taladro y a la placa de reparto. La distancia existente entre los dos elementos, cabezal de anclaje y placa, se encuentra desacoplada de la roca, por tanto, la transferencia de carga está limitada a la longitud del cabezal de anclaje.
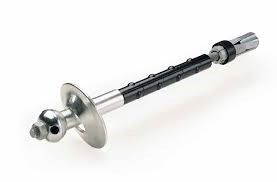
Como un elemento principal del sostenimiento de roca, cabe destacar la malla de alambre de acero. Elemento esencial del sostenimiento requerido para mantener la capacidad de carga de la masa rocosa cerca de los límites de la excavación subterránea (Villaescusa, 1999b). Mientras que los bulones se emplean para controlar la estabilidad de la excavación en general, la malla tiene el objeto de retener fragmentos de roca u hormigón proyectado sueltos que no se pudieron sostener con el patrón de bulonado utilizado.
El deterioro de la roca entre el patrón de bulones puede deberse a diversos factores. Entre otros podemos mencionar a los daños originados por las voladuras, el número y la orientación de las juntas, la meteorización, etc. El sostenimiento con malla nos produce una contrapresión en los huecos existentes entre los bulones colocados.
Existen diferentes configuraciones de malla de alambre de acero empleada en el sostenimiento de excavaciones subterráneas. Los tipos más comunes son la malla electrosoldada, que consiste en un conjunto de alambres rectos dispuestos en una rejilla cuadrada o rectangular soldados entre sí. Por otro lado, tenemos la malla de alambres tejidos y doblados regularmente formando una serie de eslabones de cadena que se entrelazan e interconectan mecánicamente.
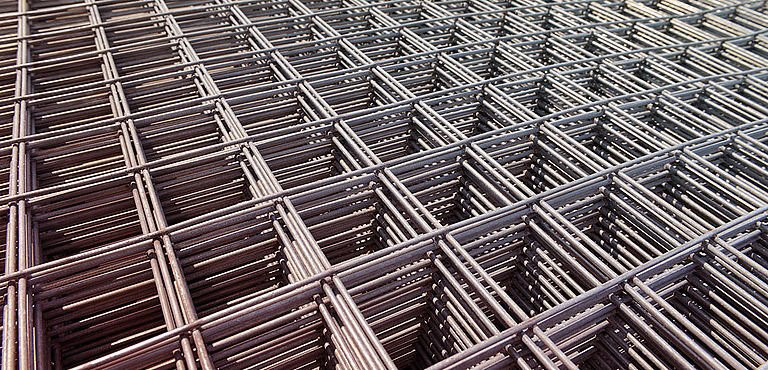
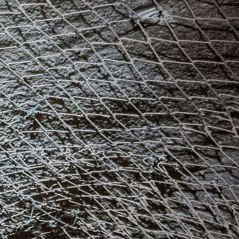
La malla electrosoldada puede tener diferentes diámetros de alambre y diferente espaciamiento entre ellos y se suministra en varios tamaños. La configuración más común es la de alambre de 5,6 mm de diámetro formando una cuadrícula de 100 x 100 mm. Las mallas suelen ser de 2,4 m de anchura por longitudes que varían ente 3,6 hasta los 6 m. Longitudes más largas dificultan la manipulación y la colocación.
La malla tejida, al igual que la anterior, se presenta en diferentes diámetros de alambre. Los más comunes son de 3 y 4 mm. Este tipo de mallas se suministran en rollos de varias dimensiones que pueden variar entre 15 y 20 m de longitud y un ancho de 2,3 m.
La malla tejida es más ligera que la malla electrosoldada, ofrece una resistencia superior, garantiza menor solape entre paños y los tiempos de instalación suelen ser menores.
En el pasado, los paños de malla electrosoldada se colocaban de forma manual con ayuda de plataformas elevadoras y empleando los jumbos de perforación. Para evitar trabajar en zonas sin sostenimiento, y no exponer a los trabajadores al riesgo de caída de roca, previamente era necesario gunitar toda la sección de galería excavada y seguido, instalar los bulones con el patrón diseñado. Tras esta operación, con ayuda de una plataforma elevadora y al menos, tres operadores, se colocaba el sostenimiento con malla. En el caso de emplear bulones de fricción, desprovistos de tuerca de apriete para la placa de anclaje, era necesario aplicar un nuevo patrón de bulonado para fijar la malla al contorno de excavación. Cuando los bulones disponen de tuerca, era posible aflojarla, colocar la malla y volver a fijar la tuerca. En la mayoría de los casos, por tiempo de ejecución y por calidad de la misma, lo más común era volver a colocar un nuevo patrón de bulonado, incurriendo en un incremento de costes de sostenimiento por empleo de exceso de materiales.
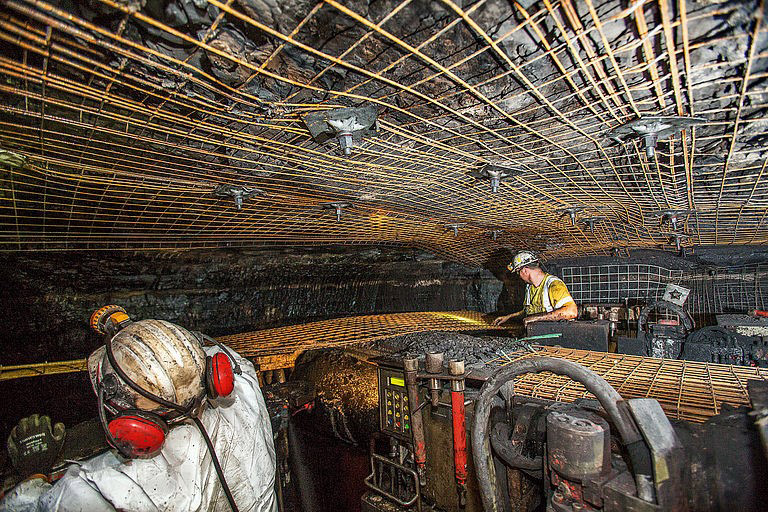
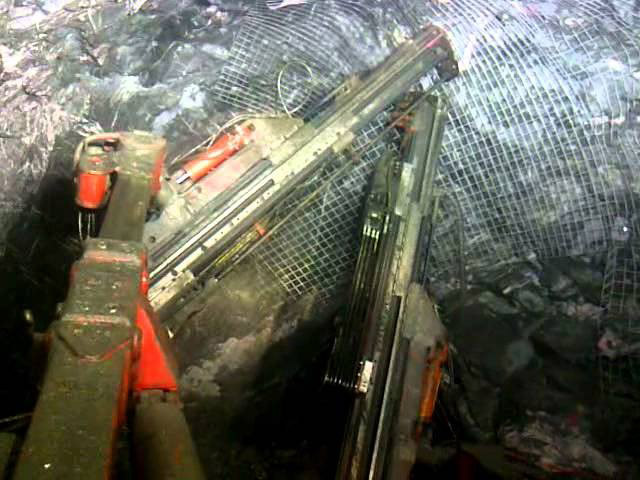
El sostenimiento de la excavación supone un elevado coste adicional y aumenta el tiempo de los ciclos de avance de excavación de galerías, por lo que automatizar este proceso con el fin de mejorar en aspectos como la seguridad, la calidad de instalación y la eficiencia, es un factor de gran importancia en el que INSERSA viene trabajando en los últimos años.
INSERSA es una compañía que se constituyó en 1988 con una actividad inicial en sondeos y perforaciones mineras y en un ámbito de actuación localista. Hoy en día, está segmentada además en otras áreas productivas, como son la minería, túneles y construcción con un ámbito de trabajo internacional.
La sociedad ejecuta todo tipo de trabajos tanto en minería de interior como de exterior, desde el desarrollo de infraestructuras hasta la extracción y transporte del mineral, disponiendo de medios y personal propios para ello. Actualmente INSERSA cuenta con uno de los parques de maquinaria para túneles y minería más amplio del país.
Con el fin de avanzar en la mecanización de la operación de refuerzo y sostenimiento de roca en minería subterránea, INSERSA adquiere en el año 2016, el primero de los equipos de bulonado, concretamente, el modelo Sandvik DS411, equipo de perforación de refuerzo de roca diseñado para instalar los tipos de bulones más comunes en combinación con malla de acero.
La bulonadora está equipada para instalar bulones de fricción tipo SPLIT SET y bulones de adherencia de resina encartuchada. Incorpora un brazo manipulador de malla electrosoldada para la colocación mecanizada de la misma. Además, dicho brazo está adaptado para montar el implemento de instalación de malla tejida en rollo. El proceso de empernado y colocación de malla es totalmente mecanizado y las tareas de control están a cargo de un solo operador.
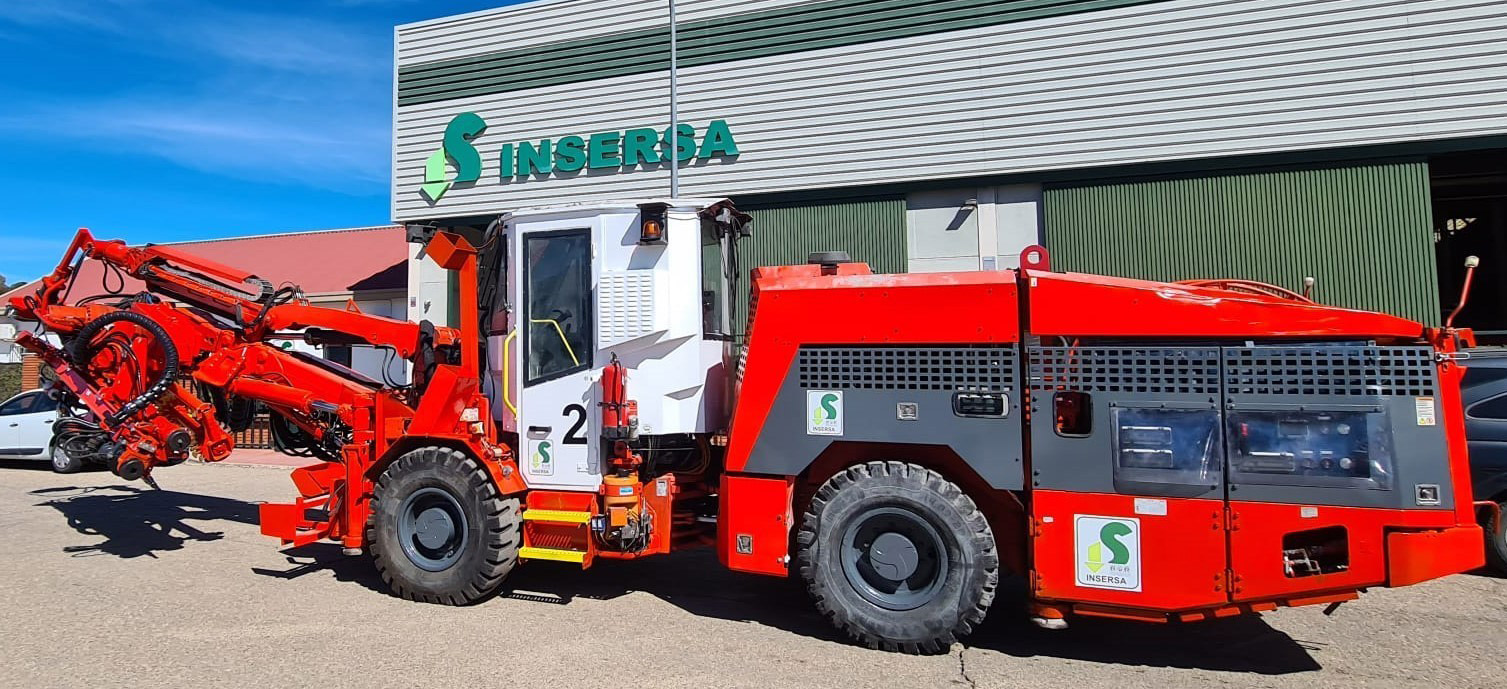
El equipo está articulado en el centro para permitir una mejor maniobrabilidad y tiene unas dimensiones de 12.040 x 3.960 x 2.940 mm. La altura de trabajo máxima es de 8,4 m montando el brazo de bulonado denominado BH30. Para el desplazamiento, emplea un motor diésel de 110 kW y una vez emplazado en el lugar de trabajo, la operación de perforación y colocación de bulones y malla se realiza a través de accionamiento eléctrico con una potencia instalada de 70 kW, pudiendo operar con tensiones de alimentación de 390 y 690 V.
Monta dos brazos, uno de ellos incorpora la perforadora de roca RD314 de 14 kW de potencia, la cual permite, para la longitud de bulones preestablecida, perforar diámetros entre 33 y 43 mm. Este brazo, aparte del martillo de perforación, monta el cabezal de bulonado y un carrusel para el alojamiento de 8 bulones, limitado por la dimensión de la placa de anclaje de 150 x 150 mm. La longitud de los bulones que puede colocar oscila entre los 1.500 mm y los 3.000 mm.
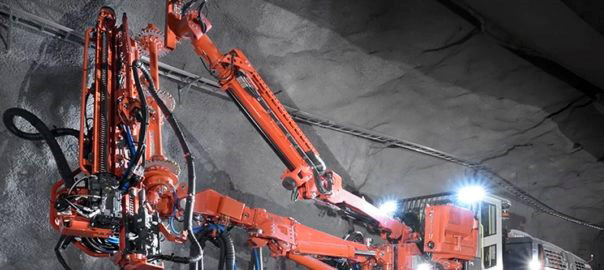
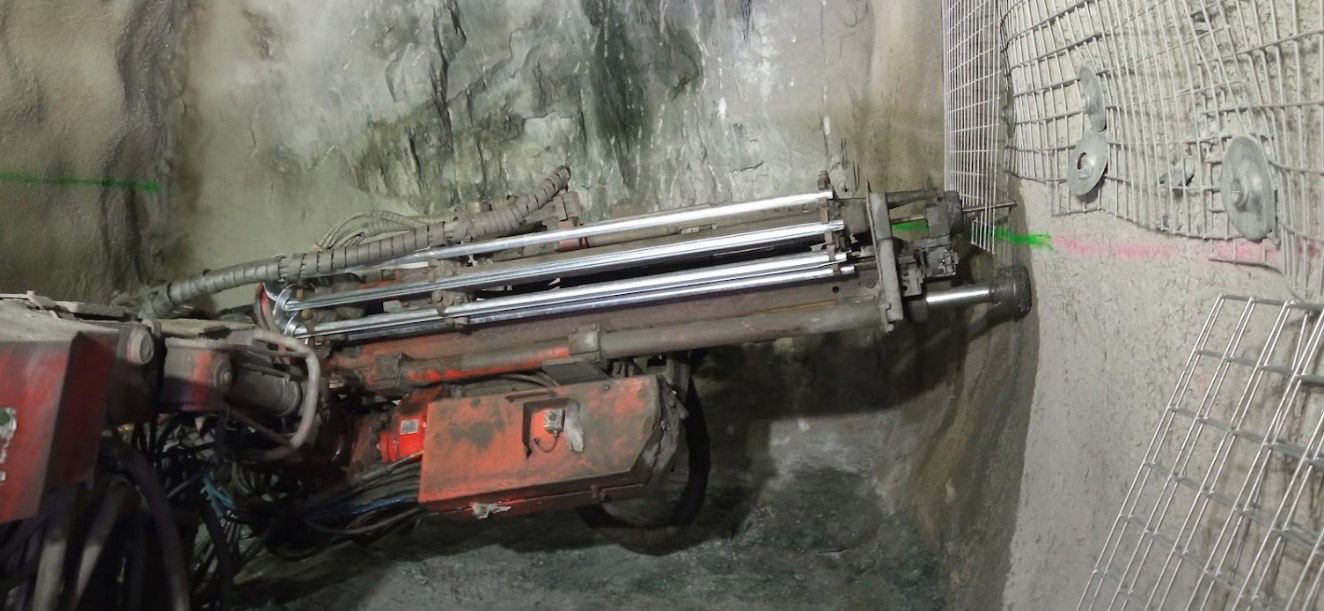
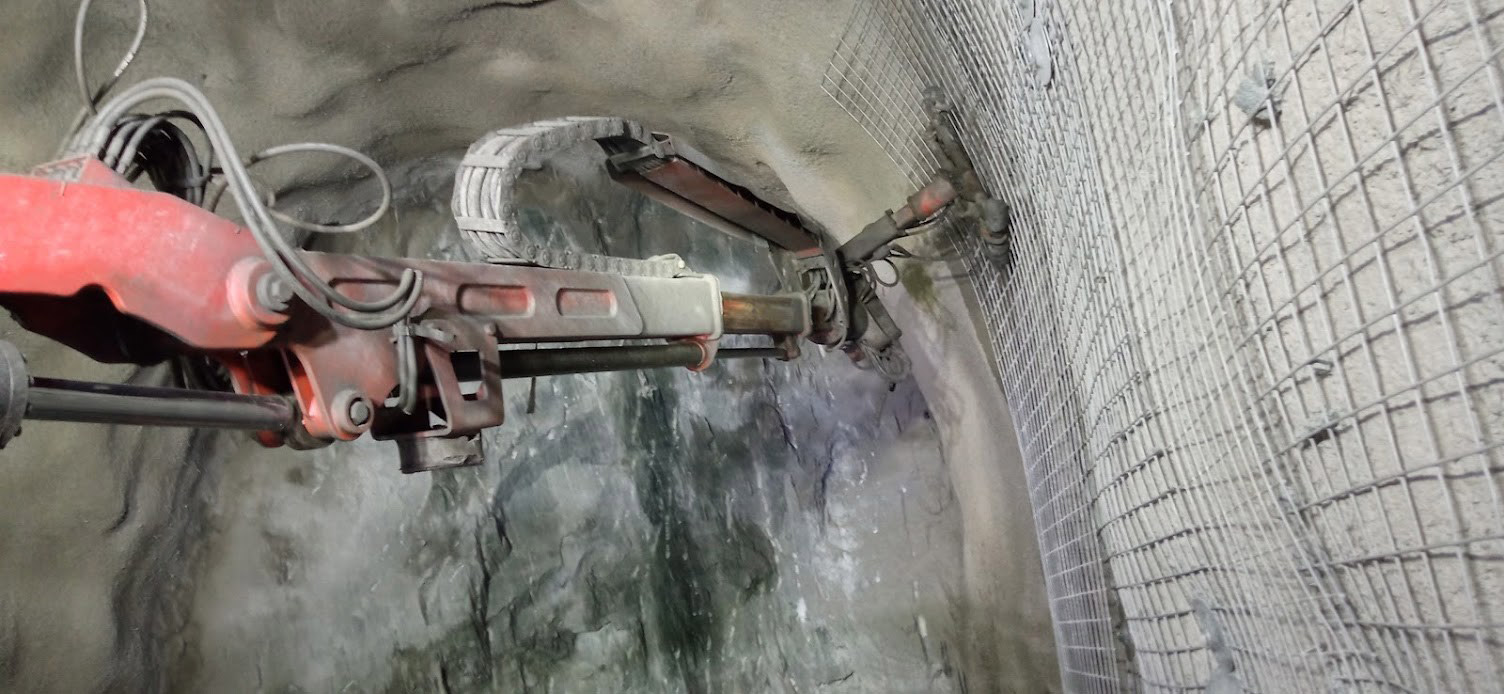
El operador de la bulonadora trabaja desde en el interior de la cabina FOPS/ROPS de la máquina. En ningún momento está expuesto a roca sin sostener, por lo que las condiciones de seguridad con el empleo de estos equipos mejoran significativamente comparado con la operación de colocación manual de bulones y malla. Entre otros factores, no es necesario proyectar hormigón en la sección previo al refuerzo de roca con bulones, reduciendo los tiempos del ciclo de excavación y los costes de sostenimiento.

Desde la adquisición del primer equipo en el año 2016, INSERSA ha apostado por la colocación mecanizada del refuerzo de roca y sostenimiento mediante el empleo de bulonadoras. En la actualidad contamos con 14 equipos, todos ellos operando en las minas de la Faja Pirítica Ibérica.
La ventaja del empleo de bulonadoras en las operaciones de refuerzo de roca y sostenimiento son:
- Mejora en las condiciones de seguridad durante la operación. El operador trabaja desde la cabina FOPS/ROCS, por lo que no tiene que estar expuesto a zonas de roca sin sostener.
- La cabina dispone de aire acondicionado, por lo que es posible trabajos en zonas donde la temperatura es elevada.
- Se pueden aligerar los estándares de sostenimiento, ya que no es necesario aplicar una primera capa de hormigón proyectado previo a la instalación de los bulones y la malla.
- Se consigue una mejor calidad de colocación.
- Los costes operativos disminuyen al aumentar los rendimientos y al disminuir los medios empleados.
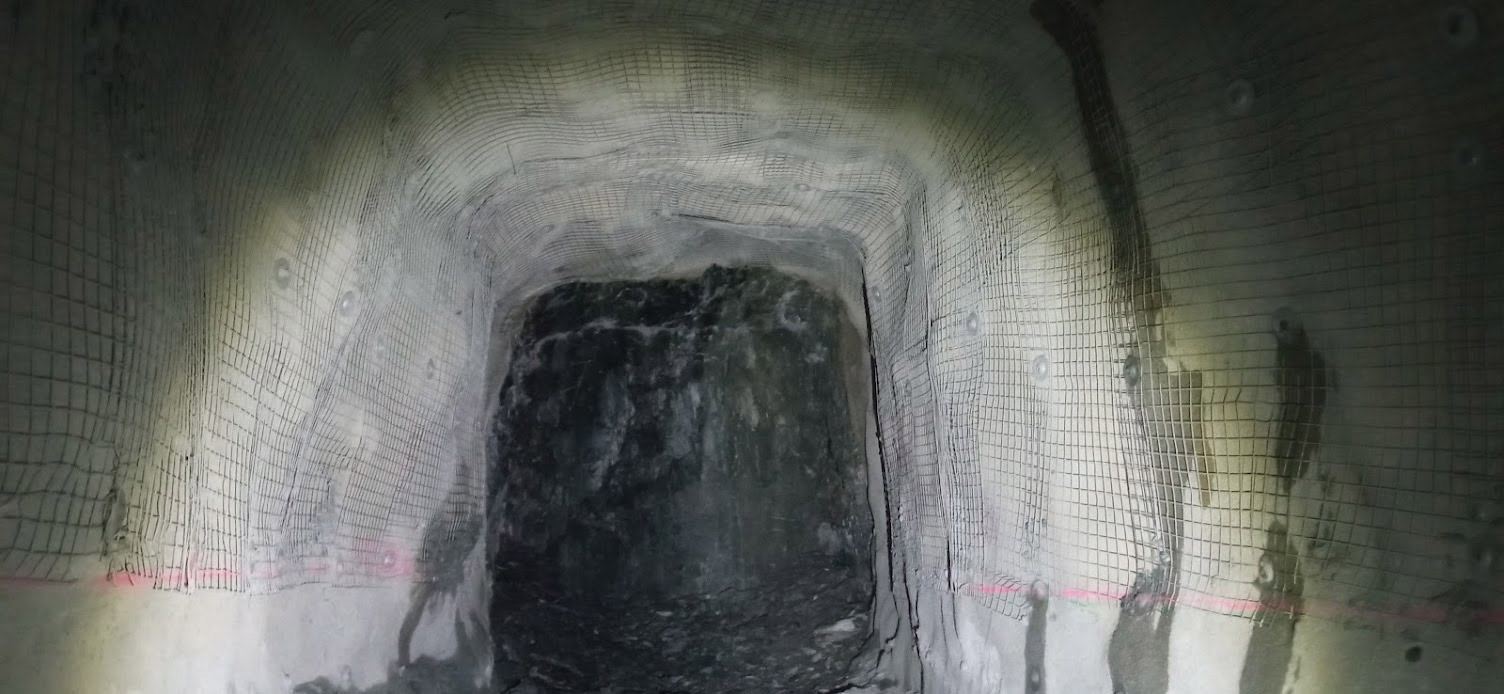
El proceso de puesta en funcionamiento de estos equipos en INSERSA desde la adquisición del primer equipo hasta el día de hoy, se ha basado en dos aspectos fundamentales:
- La formación de los operadores en la utilización del equipo.
- La especialización en el mantenimiento de los mismos.
Gracias a la formación y a la especialización de los operadores/as, actualmente se obtienen rendimientos de colocación muy elevados, resumidos en la siguiente tabla:
Id. del equipo | Disponibilidad Mecánica (%) |
Utilización (%) |
Rdto. Bulones (ud/h) * |
Rdto. Malla electrosoldada (m2/h) * |
Bulonadora | 72,64 | 60,16 | 43,62 | 9,24 |
Hay que tener en cuenta a la hora de interpretar estos datos, que en minería subterránea no suelen existir tajos continuos donde colocar bulones y malla, excepto que sean galerías que necesiten, en un tramo concreto, un refuerzo del sostenimiento o una rehabilitación del mismo. La longitud de tramo de galería a sostener está limitada por la longitud de pase o longitud de galería excavada, normalmente entre 3 y 5 m. Por tanto, los rendimientos globales se ven mermados por el tiempo que el equipo emplea para los desplazamientos entre los diferentes frentes de trabajo.
Las elevadas tasas de disponibilidad mecánica se consiguen gracias a un equipo altamente cualificado para el mantenimiento. INSERSA cuenta con más de 4.000 m2 de instalaciones destinadas al mantenimiento especializado de equipos mineros, tanto de minería subterránea como de cielo abierto, situadas en la localidad de Minas de Riotinto, en la provincia de Huelva, en el corazón de la Faja Pirítica Ibérica. Además, en cada uno de sus centros de trabajo asociados a la mina subterránea, cuenta con instalaciones de mantenimiento y personal altamente cualificado, formado por una plantilla de más de 150 especialistas en mecánica, hidráulica, electricidad y electrónica junto con un equipo de técnicos encargados de la gestión.
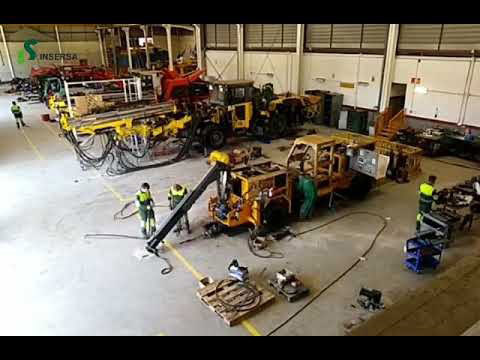
El desarrollo y crecimiento de INSERSA ha sido posible, entre otros, gracias a factores como la formación y especialización de su personal, a la mecanización y automatización de los procesos y a la maquinaria especializada.