Excavación de los túneles de Chimalpa (México)
A lo largo de sus más de 20 años de experiencia, Proacón se ha consolidado como una compañía altamente especializada en túneles. Cuenta con una amplia y diversa experiencia en la ejecución de túneles para Alta Velocidad ferroviaria, metro urbano, autovías y carreteras, obras hidráulicas, así como explotaciones mineras. Completa su cartera de especialidades con la ejecución de obras relacionadas con la mecánica de suelos y cimentaciones especiales.
Concretamente, en este artículo, Proacón explica la solución técnica empleada para los túneles de la carretera Toluca-Naucalpan, en México, un proyecto plagado de desafíos.
1. Antecedentes
Debido a requerimientos de trazo y a la compatibilidad que debe existir entre estructuras, particularmente túneles y puentes, la geometría de los túneles de la carretera Toluca-Naucalpan (2 en total) fueron planteados con una sección transversal de 4 carriles de uso bidireccional.
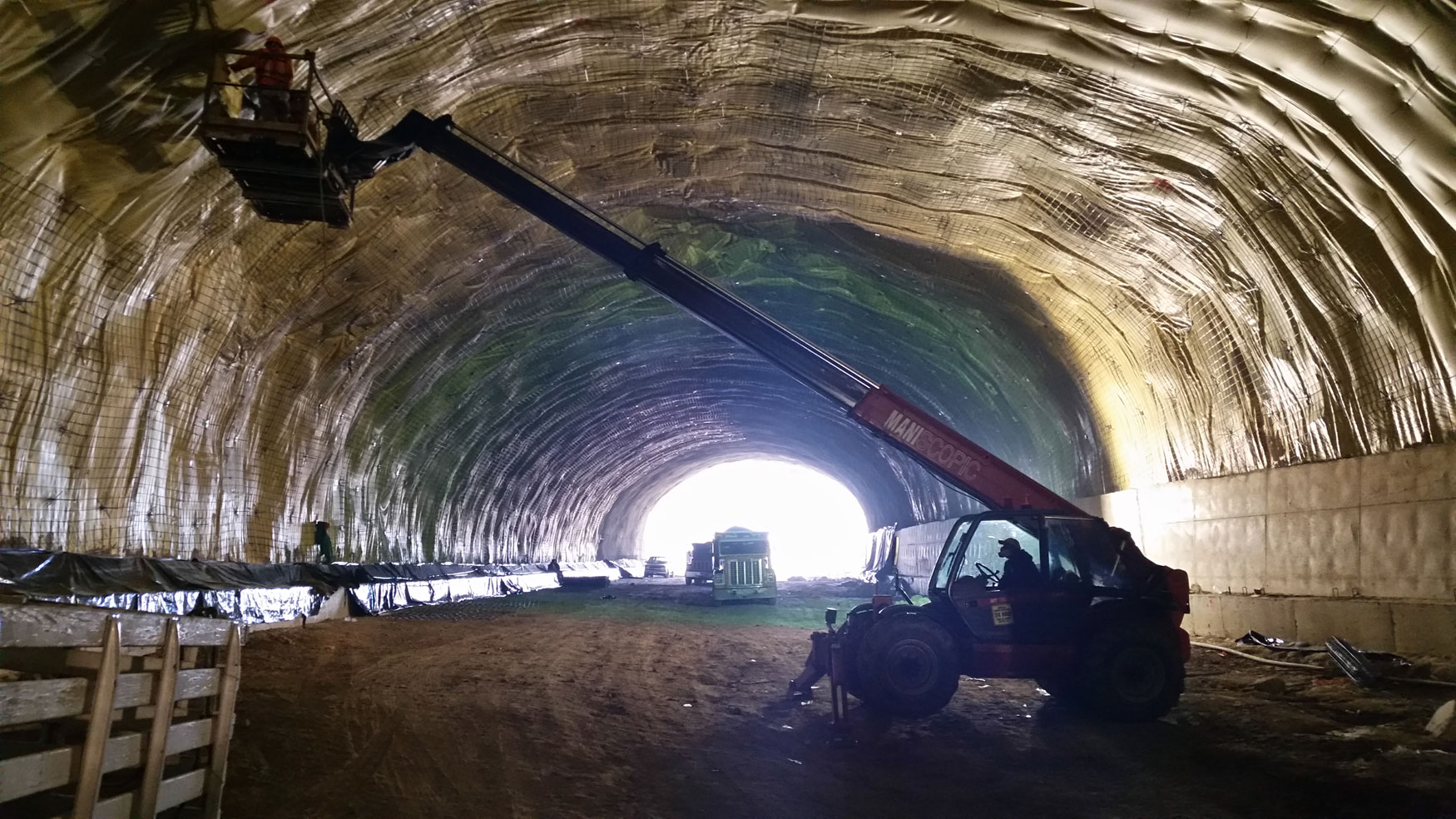
El grado de complejidad que implica, tanto en términos de diseño como constructivos, la concepción de un túnel de 4 carriles es por demás importante, y sobre todo cuando se trata con materiales de calidad geotécnica mala, ya que se requiere de técnicas más elaboradas que aquellas que convencionalmente se utilizan.
Por petición de la concesionaria y como parte del contrato de construcción entre ésta y la empresa Proacón, se solicitó a Consultec Ingenieros Asociados elaborar un nuevo diseño de los citados túneles. El objetivo es adaptar la sección y los procedimientos constructivos a nuevas tecnologías de excavación y sostenimiento a fin de hacer más eficientes y seguros los trabajos de construcción y concluir las obras en el tiempo acordado con la Administración. El nuevo diseño incluye: definición geométrica de la sección, diseño geotécnico estructural y diseño de procedimientos constructivos.
2. Geometría de la sección transversal
2.1. Optimización de la sección interior
En la Figura se muestran las secciones transversales en tangente y curva correspondientes al proyecto original. En la Figura 2 se muestran las modificaciones propuestas.
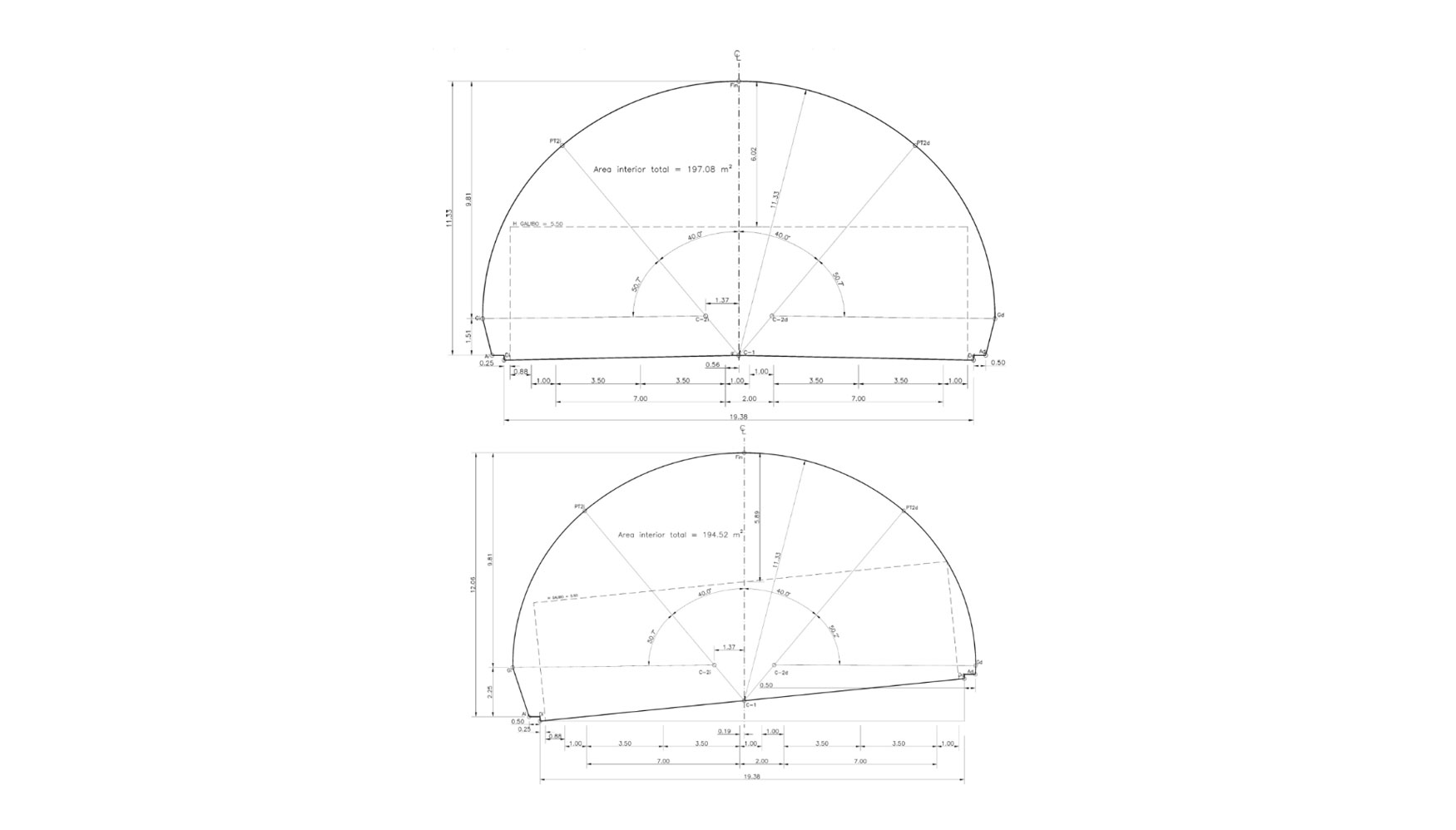
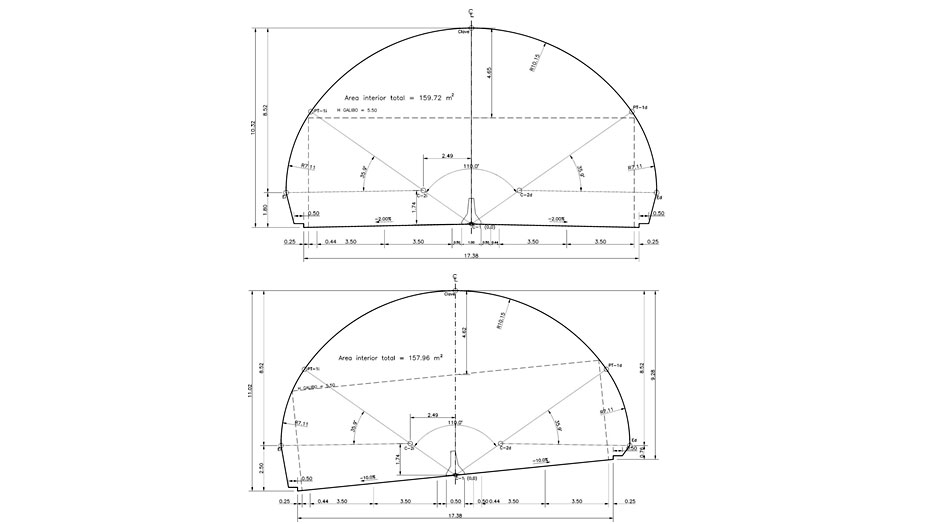
Al optimizar las dimensiones de la sección interior se consiguieron las siguientes reducciones:
-
Reducción del área total interior en tangente = 197. 08 m2 / 159.72 m2 • 1 • 100 = 23.3 %
-
Reducción del área total interior en curva: 194. 52 m2 / 157.96 m2 • 1 • 100 = 23.1 %
La longitud total para los dos túneles es de 730 m, lo que significa que con la nueva geometría se alcanza un ahorro aproximado de 27,000 m3 en sección interior. Adicionalmente, la nueva propuesta reduce la distancia vertical máxima entre línea de gálibo y clave del túnel de 6.02 a 4.65 (1.37 m).
El cambio en la sección interior no tiene ninguna repercusión en términos de estabilidad estructural y flujo de aire respecto a la original. En cambio, sí representa un ahorro considerable en la fase de operación ya que disminuye de manera importante la iluminación requerida.
2.2. Sección de excavación
En el caso de los proyectos originales no resulta fácil definir a ciencia cierta la sección de excavación exacta, ya que no existen planos geométricos en los que se especifiquen las dimensiones. Tampoco se localizó el volumen estimado de excavación en el catálogo de conceptos y cantidades de obra. Pero siguiendo las especificaciones de sostenimiento de concreto lanzado y de espesores de revestimiento definitivo que aparecen en los planos, se determinó un volumen total de excavación para los dos túneles de 169,944 m3. Con las modificaciones a la geometría propuestas por Consultec y a partir de las secciones geométricas de excavación definidas para las distintas condiciones geotécnicas previstas, el volumen total de excavación resulta de 122,540 m3. Por lo tanto, el ahorro total de excavación estimado es de 47,404 m3.
3. Procedimientos constructivos y sostenimientos
3.1. Esquema de proyecto
El procedimiento constructivo del proyecto original implica la excavación del túnel en 7 etapas con un sostenimiento de concreto lanzado y anclas. La Figura 3 muestra esquemáticamente este procedimiento.
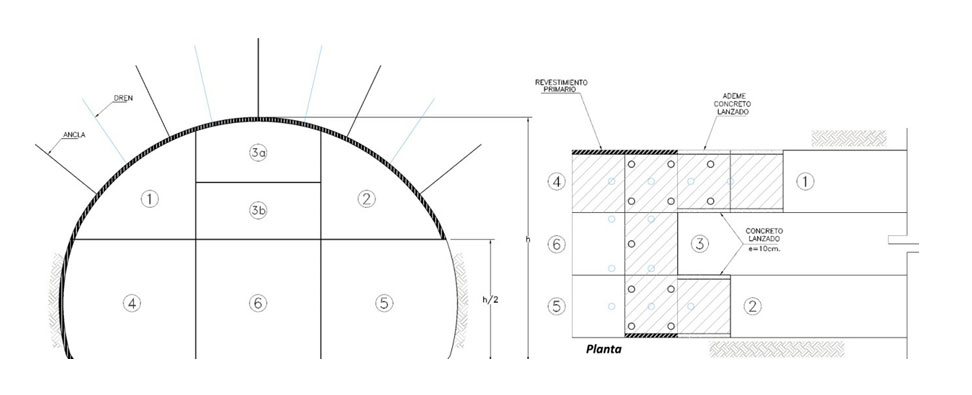
A grandes rasgos, este procedimiento consiste en excavar pequeñas secciones de avance en el orden que se indica en la figura, con desfases de 4 metros entre frentes tal y como se aprecia en la planta. Después de cada avance se indica colocar 10 cm de concreto lanzado y las anclas correspondientes (longitud = 12 m). También se especifica la aplicación del concreto lanzado en las paredes del pilar central (bloques 3a y 3b en la Figura 3).
3.2. Adecuaciones propuestas
A raíz de las reuniones efectuadas entre la empresa concesionaria y la constructora Proacón, esta última propuso una serie de cambios en los procedimientos de excavación y sostenimiento encaminados a reducir los tiempos de construcción a fin de cumplir con los plazos de obra planeados. Por su parte, la empresa Consultec brindó el apoyo técnico necesario a Proacón para definir dichos procedimientos constructivos de tal manera que se consigan los rendimientos necesarios preservando el nivel de seguridad de las excavaciones.
Después de revisar los proyectos ejecutivos de los dos túneles, se determinó que las adecuaciones necesarias más importantes en los procedimientos constructivos son las siguientes:
- Cambiar el esquema de excavación de uno multifase con avances largos (4m) a uno de media sección superior completa y banqueo con avances cortos y sostenimiento cercano al frente. Este esquema permite el trabajo de maquinaria más potente que la que se tendría que introducir en las pequeñas secciones de avance; permite hacer más eficientes los ciclos de carga-voladura-rezaga-sostenimiento ya que los equipos no deben estar entrando y saliendo continuamente de las pequeñas galerías; permite, en los tramos de roca de mala calidad, llevar un sistema de soporte (marcos metálicos), muy cerca del frente, proporcionando mayor seguridad a la excavación; permite introducir robots lanzadores de concreto de grandes dimensiones que hacen mucho más eficiente la implementación del sostenimiento, así como potentes jumbos de perforación que introducen los anclajes en tiempos mucho más reducidos; en general, avanzar más rápidamente y terminar la excavación de toda la media sección superior antes de proceder al banqueo, el cual se puede realizar con mayor seguridad ya que se tiene un conocimiento previo del terreno.
- Tramificar los procedimientos constructivos de acuerdo con la calidad geotécnica del macizo rocoso: el proyecto original contempla un sólo esquema de avance-sostenimiento independiente de la calidad de los materiales por excavar (salvo en el caso de los anclajes que podrían no ser siempre necesarios); sin embargo, después de revisar los resultados de la campaña de exploración y los modelos geológicos, se pudo determinar que la mayor parte de las excavaciones se realizarán en roca de calidad media a buena; estas características del macizo hacen poco justificable un procedimiento de avance tan complejo como el planteado en proyecto y se puede garantizar la estabilidad de la excavación con avances en secciones mucho más grandes.
- Cambiar el esquema de soporte-sostenimiento en los tramos de roca extremadamente mala a muy mala: se propone implementar el sistema de enfilaje frontal pesado y marcos metálicos en los emportalamientos y tramos de roca muy mala, mientras que en los tramos de roca mala, se propone el empleo de marcos metálicos (pesados o ligeros), con o sin anclajes, dependiendo del nivel de fracturamiento del macizo.
- Cambiar el esquema de sostenimiento en tramos de roca regular a buena, colocando 15 a 20 cm de concreto lanzado reforzado con fibras y anclajes (autoperforantes o tipo Swellex MN-24): este esquema permite mejorar mucho la eficiencia en la implementación de los sostenimientos.
En las Figuras 4 a 8 se muestran los esquemas de las diferentes secciones de excavación y sostenimiento propuestas.
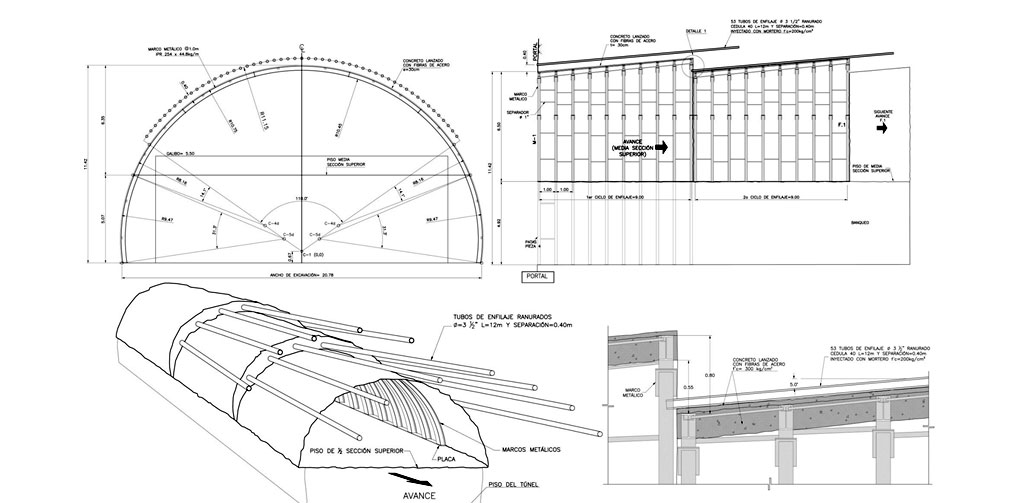
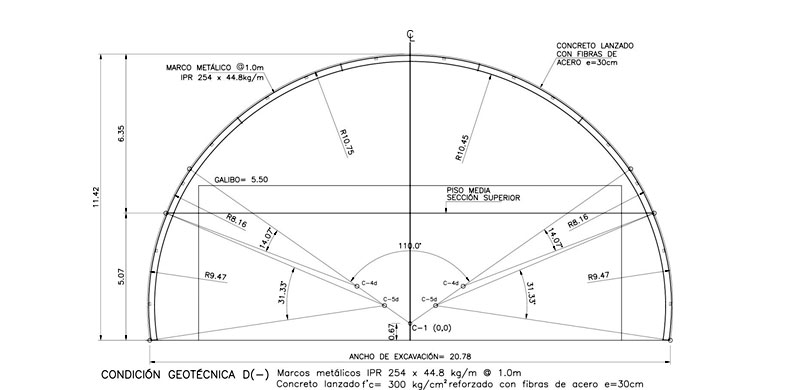
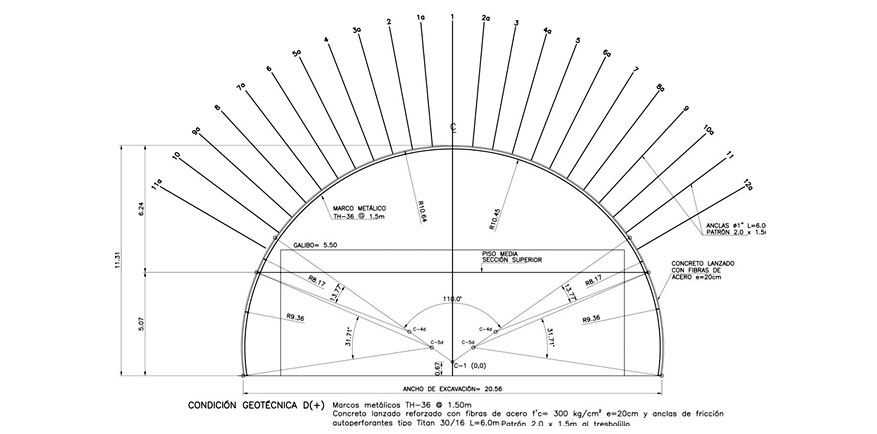
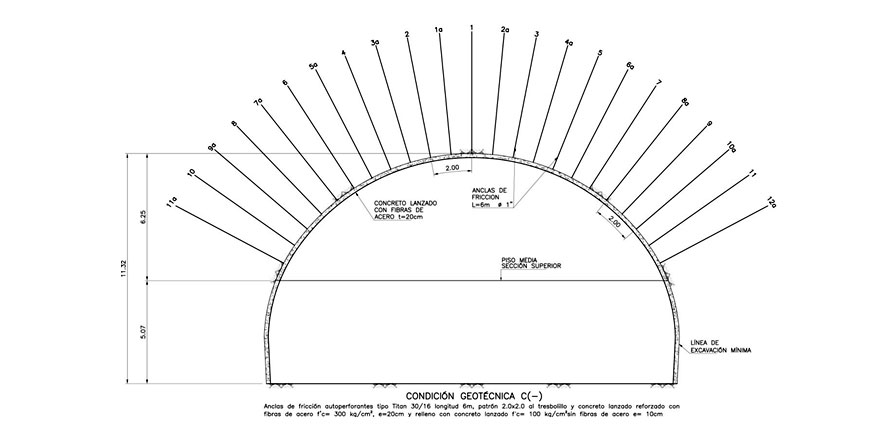
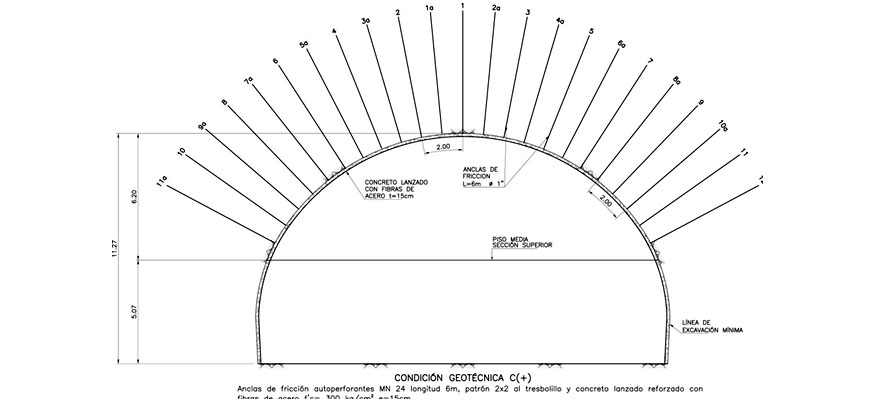
4. Construcción
A continuación se detallan las particularidades acontecidas en la excavación y sostenimiento de los túneles, Chimalpa I, el cual ocupa los pk 30+620 al 31+150 y Chimalpa II, del pk 31+700 al 31+925 de la Autopista Toluca-Naucalpan en el Estado de México – México, obra ejecutada por Proacón México SA de CV.
Dimensiones
Ambos túneles, Chimalpa I de 530 ml de longitud y Chimalpa II de 225 ml de longitud, son túneles carreteros de 4 carriles y dimensiones de excavación de 20,49 metros de ancho por 11,32 metros de alto para completar una sección de 196 m2. Esto los convierte en los túneles de mayor sección excavados en Latinoamérica.
Sostenimientos
Se realizó un cambio al proyecto original por parte de la empresa Consultec adaptando el método de excavación y sostenimiento al nuevo método austriaco y sobre ese proyecto se inició la excavación del túnel.
El proyecto preveía sostenimiento ST-E para los emboquilles con enfilaje pesado de 53 micropilotes de 88,9 mm de diámetro y 12 metros de longitud cada uno, dejando 3 metros de traslape, con cerchas de 44.8 kg/m colocadas a cada metro y 30 cm de hormigón proyectado de 300 kg/cm2 añadiendo 30 kg/m3 de fibra metálica.
Sostenimiento ST-D de transición después del emboquille de cerchas TH-36 a cada 1,5 metros y 20 cm de hormigón proyectado.
Sostenimiento ST-C con anclas autoperforantes Titan 30/16 de 6 m y patrón 2x2 m y 15 cm de hormigón proyectado en interior túnel, pues se esperaba una calidad de roca con RMRs por encima de 40 puntos.
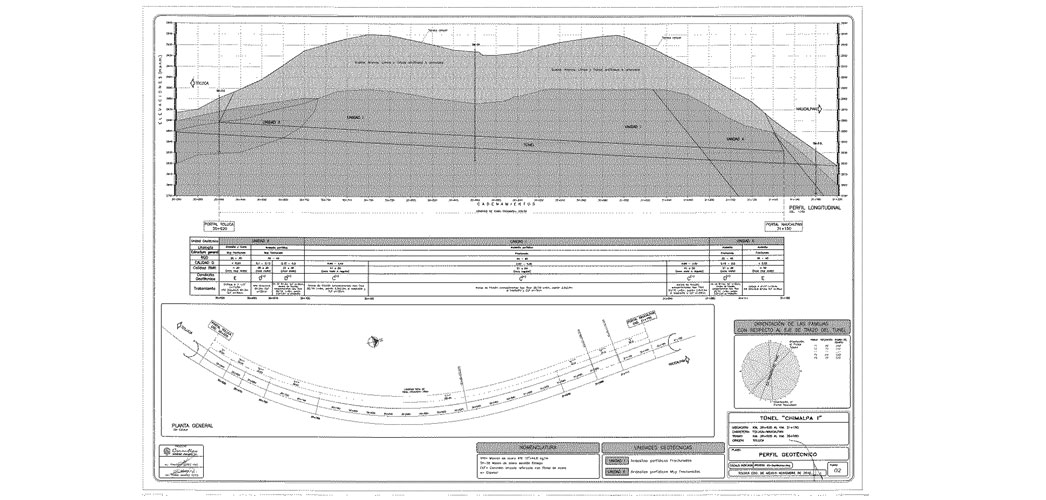
5. Excavación del túnel Chimalpa I
Mencionaremos únicamente la excavación del túnel Chimalpa I donde acontecieron varias particularidades, ya que el túnel Chimalpa II se excavó sin ningún cambio en la geología esperada y, por tanto, sin incidencias reseñables.
El túnel Chimalpa I consta de dos portales, nombrados Portal Toluca y Portal Naucalpan. A finales de agosto de 2013 dio comienzo la ejecución del enfilaje de entrada correspondiente al sostenimiento ST-E de emboquille arriba mencionado por el portal Toluca.
Se inició la excavación de la sección avance con los sostenimientos de proyecto, se excavaron 30 ml colocando sostenimiento ST-E, a continuación se colocó sostenimiento ST-D de transición y se entró en sostenimiento ST-C con anclas autoperforantes después de los primeros 80 ml (metros lineales) iniciales de excavación.
Se esperaba roca andesita porfídica fracturada en los siguientes 360 ml. Se avanzaba con voladuras de toda la sección de avance completa y 4 ml de longitud, pero ya en el pk 30+740 cuando se llevaban 120 metros excavados se apreciaron varias familias de estratificación en distintas direcciones y la fracturación de la andesita era muy intensa. Por esta razón, se hizo necesario cambiar los parámetros de voladura y hacer voladuras a 2 m por debajo de la línea de excavación en todo el contorno. El resto de excavación de sección de avance que no se extraía con voladura se realizó con martillo hidráulico para evitar sobreexcavaciones, lo cual ralentizó considerablemente la producción.
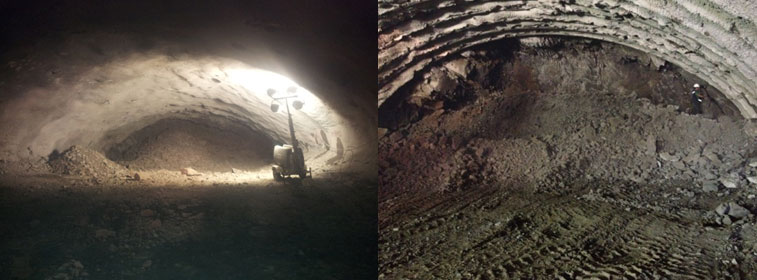
Llegando ya con la excavación al pk 30+760, con solo 140 ml excavados, la Andesita se presentó tan descompuesta que originó un caído a la altura del hombro izquierdo de la excavación de aproximadamente 6x4x5 m3. Ello dio lugar a cambiar el sostenimiento de anclas por cerchas y, una vez protegida la zona, se continuó excavando con enfilaje pesado para proteger la excavación, pues en esta zona el RMR era menor a 20 puntos. Se avanzaba únicamente con martillo hidráulico en pases de 1 ml y el contorno de excavación no se mantenía.
Aún se encontró una zona más complicada a la altura del pk 30+785 donde ya el terreno era un suelo de arenas no compactas que hizo necesario sellar el frente para evitar desmoronamientos. La presencia de estas arenas, aunado a la gran sección del túnel, imposibilitó la excavación. Por ello fue necesario realizar inyección de consolidación del terreno.
Se realizaron varios barrenos tanto para inyección como para sondeo del frente y se inyectó lechada de relación agua-cemento A/C=0,6. Inicialmente se inyectó sin presión para relleno de huecos existentes y, una vez rellenos los huecos, se inyectó lechada con obturador a presión de 5 bar para consolidación del terreno. Este proceso duró 10 días, tras los cuales, se pudo reanudar la excavación.
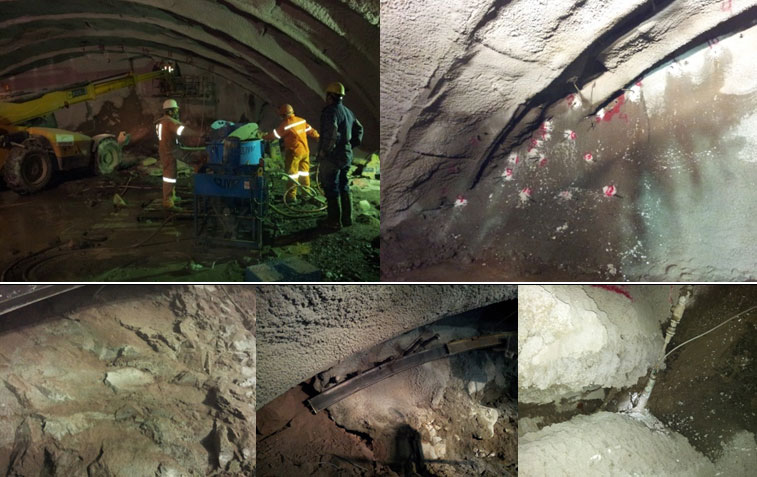
Debido a la sección de 100 m2 a excavar y la mala calidad del terreno, en muchas ocasiones se tenían tres tipos de materiales totalmente distintos en el frente de excavación. Se continuó con sostenimiento de cerchas a 1 m y excavación bajo enfilaje pesado hasta el pk 30+812. En este punto kilométrico se apreció mejoría en el terreno y se cambió a sostenimiento tipo C con anclas autoperforantes de 6 metros de longitud en malla 2x2 m, aunque la fracturación que presentaba la roca no permitía realizar voladura de sección de avance completa y el contorno debía excavarse con martillo hidráulico.
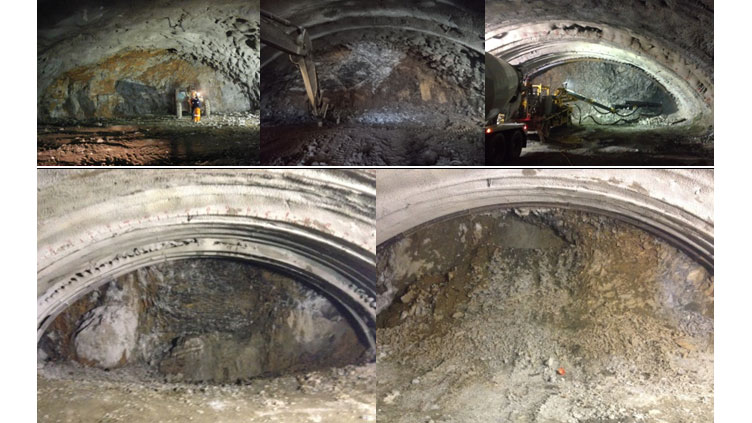
En el pk 30+884 nuevamente se encuentra terreno tipo suelo, de mala calidad, en el cual el contorno de excavación no se mantiene al excavar y, de nuevo, se hace necesaria la excavación bajo enfilaje. Se excavó bajo enfilaje hasta el km 30+971 y desde ahí se continuó ya sin enfilaje pero igualmente con cerchas a cada metro hasta conectar con el sostenimiento ST-E de emboquille por el portal Naucalpan.
El túnel Chimalpa I se caló en noviembre de 2014 y en diciembre de 2014 se terminó la excavación de destroza. La excavación del túnel Chimalpa II comenzó en junio de 2014, transcurrió sin incidencias y se caló también en noviembre de 2014. Mes y medio después se terminó la excavación de destroza de este túnel. Actualmente ambos se encuentran en fase de revestimiento.
6. Impermeabilización y revestimiento
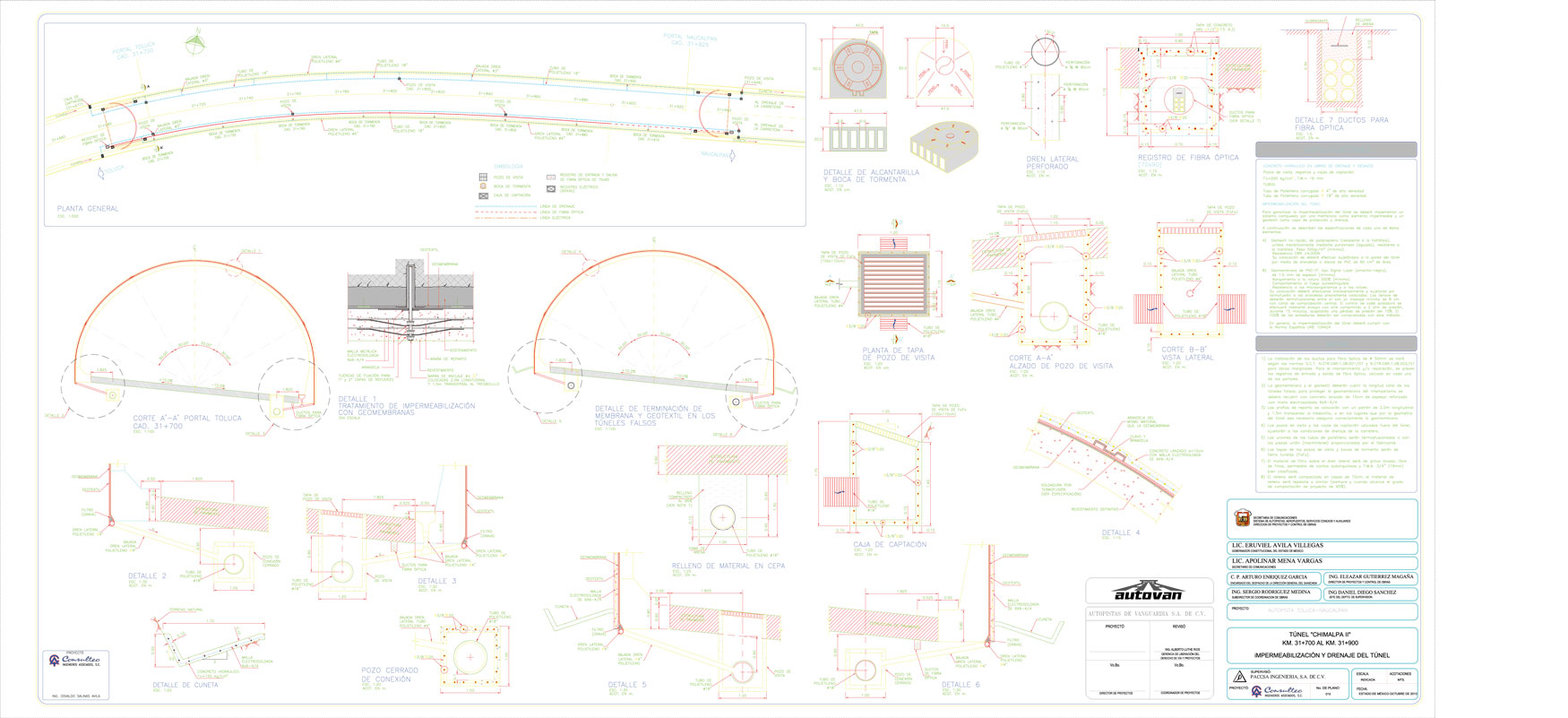
La impermeabilización de Chimalpa I y Chimalpa II, como viene siendo habitual en los túneles modernos, consta de una lámina de geotextil y una geomembrana de PVC colocadas sobre el sostenimiento primario que reconducen los abscesos de agua hacia el drenaje.
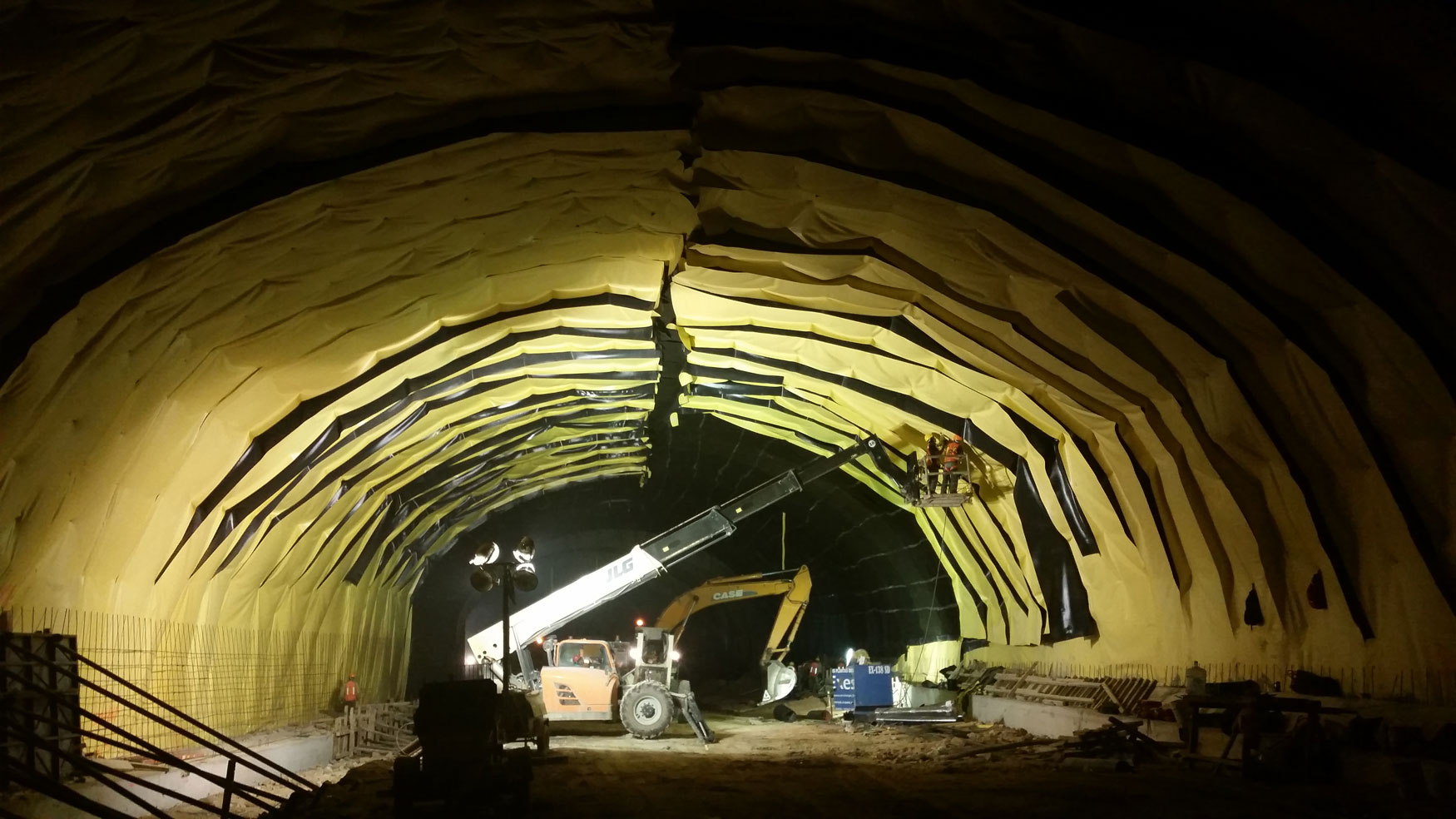
El revestimiento consta de dos capas de malla electrosoldada calibre 4 que se sujetan por medio de ‘arañas’ embebido en 30 cm de hormigón de 350 kg/cm2. Se presenta la particularidad de que, en este caso, el hormigón es proyectado y no con carro de encofrado y bombeable.
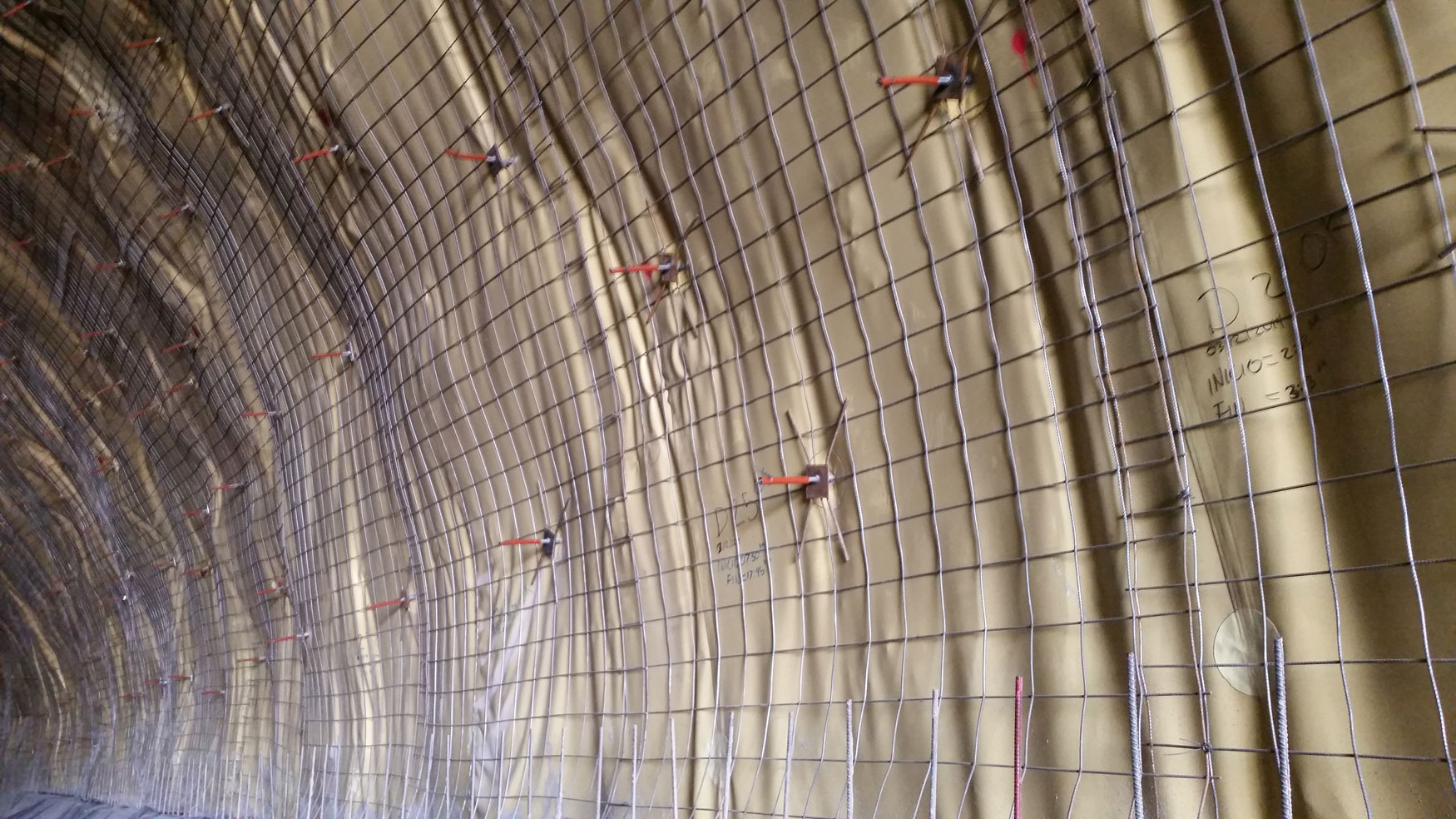
Para ejecutar este proyecto, al tiempo que se coloca la impermeabilización, geotextil y PVC, se anclan varillas al terreno, del cual sobresalen 30 cm y se sellan con parche de PVC para evitar filtraciones. A continuación se coloca la malla electrosoldada con ayuda de arañas (una araña por varilla). La malla electrosoldada comprime la impermeabilización contra el hormigón del sostenimiento primario. Es muy importante que esta primera capa de malla se comprima lo máximo posible contra las paredes del túnel para no generar bolsas de aire que puedan producir defectos en la estructura y que, además, genera rechazo en el lanzado de hormigón de revestimiento.
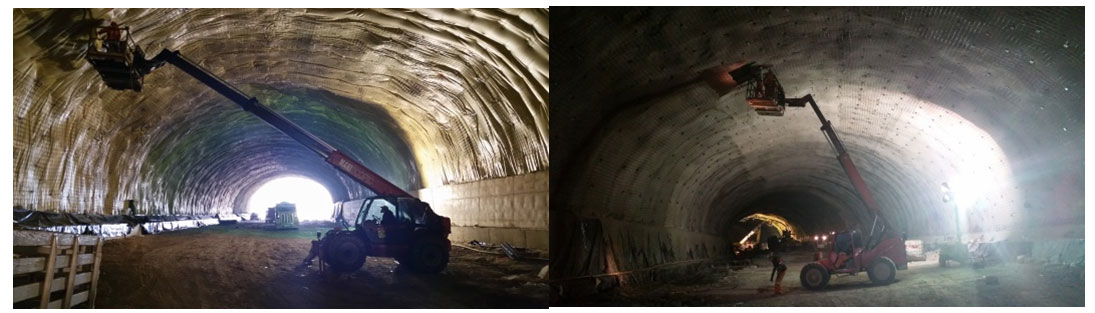
Se realizó una prueba inicial en 30 metros lineales colocando una malla de anclas de 2x2 m y se obtuvo rechazo de hormigón proyectado mayor al esperado debido a las bolsas de aire entre hormigón de sostenimiento primario y PVC de las que hablamos. Se apreció que las bolsas se generaban en la zona entre-anclas, por tanto, se aumentó la densidad de anclas a una malla 1x1 m y se obtuvieron muy buenos resultados de rechazo del hormigón proyectado, menor al 20%.
Al lanzar hormigón proyectado sobre PVC, no se consigue adherencia. El hormigón se adhiere gracias a la malla electrosoldada, por este motivo, también es importante comprimir la malla contra el terreno. Es necesario que la primera capa de hormigón lanzada sobre el PVC sea lo más fina posible, de 1 ó 2 cm únicamente. Una vez fraguada la primera capa se lanzará una segunda, también de 1 a 2 cm de espesor. Ya una vez fraguada esta segunda capa se va completando el espesor de revestimiento con capas entre 5 y 10 cm.
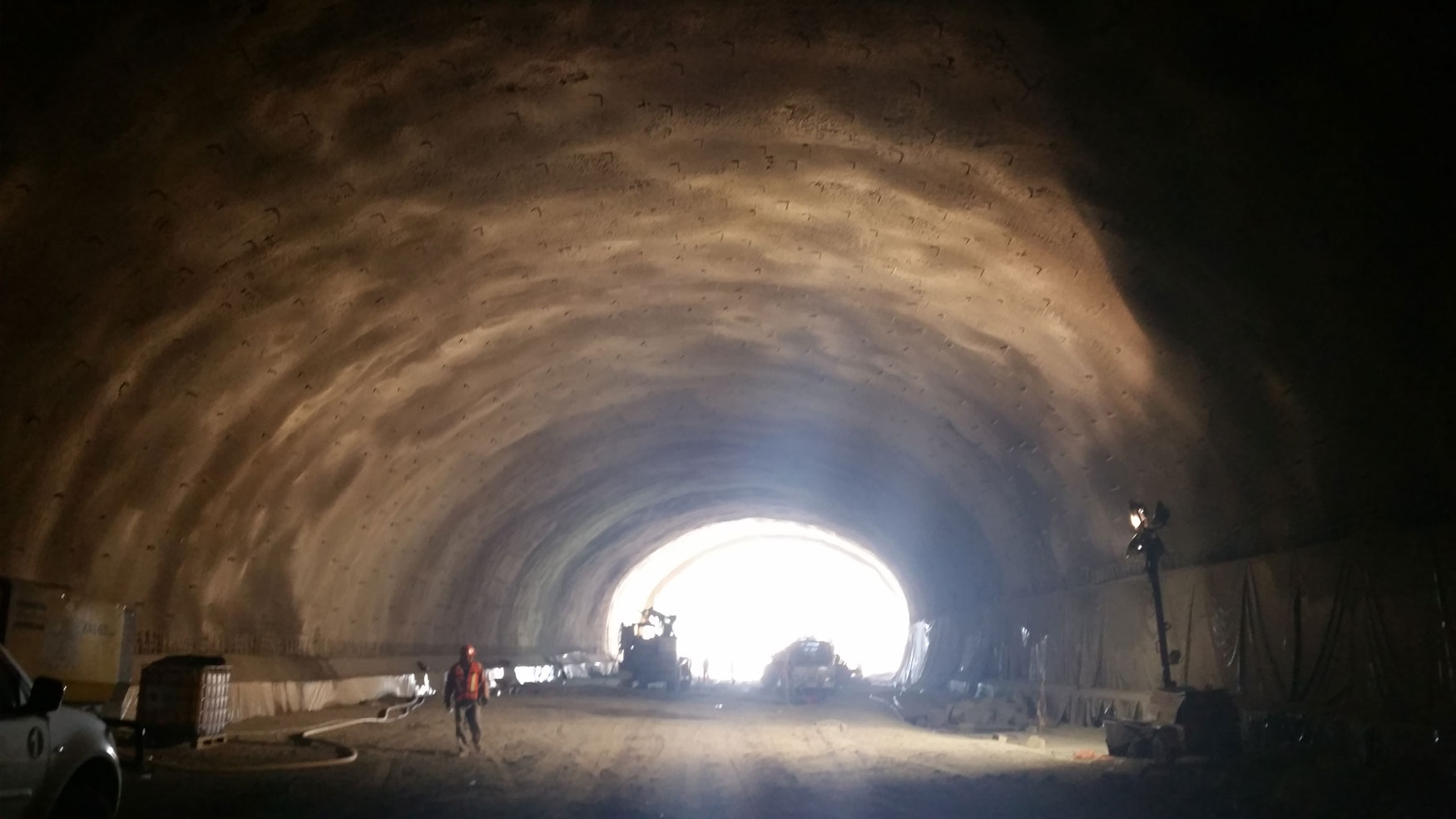
Debido a la no adherencia hormigón-PVC, hemos comentado la importancia de que las dos primeras capas de hormigón lanzado sean de muy poco espesor, por tanto, es recomendable lanzar sobre una gran superficie para poder extender el hormigón sin dar espesor.
En este proyecto en concreto, una vez lanzada la primera capa de revestimiento de 15 cm de espesor de hormigón proyectado 350 kg/cm2, se coloca una segunda malla electrosoldada y se vuelven a proyectar otros 15 cm de hormigón. Ya en este segundo lanzado no se presenta el problema de adherencia antes mencionado y puede realizarse de forma habitual sin problemas.
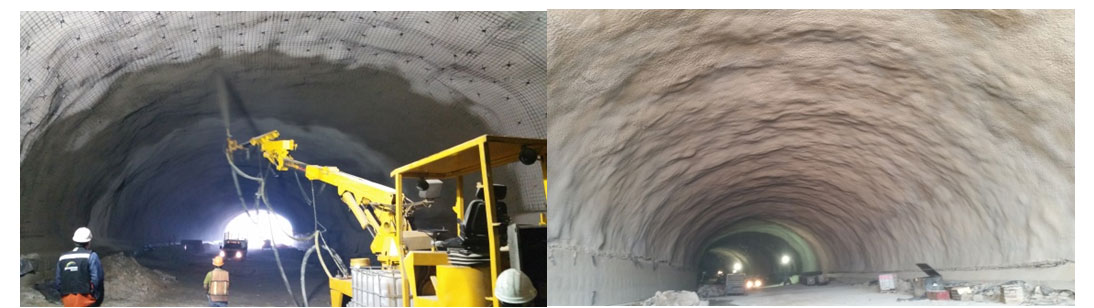
La ventaja de este procedimiento es un importante ahorro, al no ser necesario el uso de carro de encofrado. Las propiedades estructurales del revestimiento, las mismas que con hormigón bombeado.