Norcort Engineering is consolidated as a supplier for the aeronautics sector thanks to its two Chiron Mill 2000 machines
March 17, 2009
Around the world are increasingly more production companies wishing to access the growing aviation market. In addition to constructive solutions, technical materials and production, absolute quality, flexibility and meeting deadlines, aircraft manufacturers expect their undertakings costs per piece as economic potential.
This also see him as Steve Fogg, director of production of the English manufacturer of aeronautical parts Norcot Engineering Ltd.: "of course, the ability to solve problems is the most important thing in our business." However, customers are now oriented worldwide to make their purchases of parts and components. On our planet there are many productive sites clearly more economical and more favoured. The people who live there also wants its piece of the pie of well-being. Globalized competition leads to a drop in prices. "If we want to continue living on our business, we not only have to convince our clients from the professional and organizational point of view, but that we also need to develop and use better concepts of production".

According to the technical director David Broomfield "countries who do not have own technologies that are key in creating value with the technique of machining stop being independent and lose their strength of innovation." "Companies like Norcot are extremely important to us and have many possibilities of achieving demanding orders for the aircraft industry."
In this sense, the English company produces about 600 different pieces for a dozen of companies on demand in own facilities with zinc coating, graffiti and more and more, also mounted.
They are especially proud of the three structural components for two small aircraft engines Eclipse 500, which include a plate base and two pieces of fuselage in 3D must be manufactured in two inverted versions. They share these pieces with a weight of up to 80 kg as blank, is its high percentage of machining up to 95%. In addition to roughing is a large number of machining tolerances very close on all sides as, for example, smoothing, drilling, threading, beveled, rounded and deburring. To all this is added the bad habit of the aluminium parts that its reliable fixation is all the more difficult the more work has progressed. Furthermore, should provide just-in-time between 40 and 60 units per month within the time limits. Automation does not enter into consideration. The rapid changes of preparation are converted into an obligation.
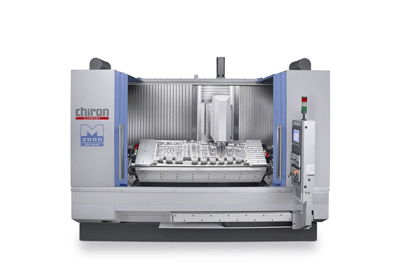
Steve Fogg: "together with our Bedford plant 40 CNC machining centers we have in use, but they had failed us term and not targets of costs and technical requirements." However, the important thing for us is the client and their parts. To be able to deliver an offer, we have developed a production process and we were looking for a suitable partner for solutions. "After many conversations with different suppliers of machines, we have favored the offer from Chiron UK Broomfield David."
The basis of the offer were two machines Chiron Mill 2000 high speed plus of Chiron in Tuttlingen, each equipped with a swivel head installable (+/-100 °, spindle of 20,000, 75 Nm), rotating table (400 mm x 2,000 mm)a store chain for 24 tools HSK-63, robust stainless steel roofs, as well as control Fanuc 18i MB5 as CNC. As particularity, Chiron surrendered two precision 5-axis machining centers with a table reduced by 100 mm at a height of 700 mm.
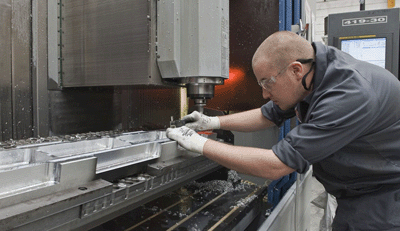
David Broomfield: "we have successively completed machines to turn them into a turnkey solution and installed it in January and may of 2007." "Commissioning the conducted in parallel to the process and instruimos at the same time operators". Among the custom adaptations of the client was, for example, the equipment with a zero-point clamping system, as well as different devices of subject specific parts. There was also an accommodation with vacuum for the determination of the Board of the aircraft, as well as several hotels that have been milling in Mill 2000 3D for the subject without deformation of structural components for the cabin with their way of snow shoe. For the measurement of the pieces a transducer of measuring Renishaw OMP has been integrated in the CNC control software. This transducer has a post protected within the loader tools and can be inserted automatically in the spindle as a tool, if necessary. In addition, machines were equipped with a supply of coolant 30 bar with a reserve of 900 liters in each case, as well as devices of suction of the workspace and filter installations. Steve Fogg expresses his satisfaction: "Currently use the Mill for up to 15 shifts per week." In addition to the structural components of large formats for the Eclipse, we also mechanized clearly smaller parts with 5 axes. The large working table is simply ideal for multiple pylons. We manage unattended machining times of up to 3 hours. "And the preparation not really takes a long time."
