Design of piece with compound materials
Enrique Díaz Escriche, Ph.D, responsible of composites of
The adhesion between the fibre and the matrix is a key appearance in the mechanical provision of a compound material. If there is not a good adhesion in the interfase fibre-matrix, each one of the materials will comport mecánicamente of individual form; like this, if we attend to the figure 1 in front of an effort of low intensity σ1 the fibre will deform ε1f and the matrix will do it in a greater quantity (ε1m). In these conditions, like the deformation of each one of the materials is different, produces a physical separation between the fibre and the matrix giving place to the fracture of the compound. This situation, logically is not desirable when it works with this type of material since it does not take advantage of the synergy in the combination of the different components. It would be possible moldear the piece with a material composed of these characteristics but the mechanical properties would not be the wished.
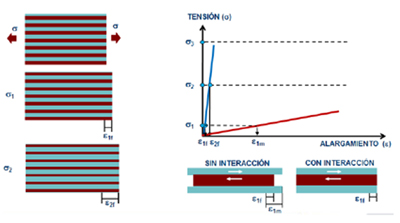
By the contrary, when it produces a good interaction in the interfase fibre-matrix, that is to say, exists good adhesion between the components, the fibre shapeless in an equivalent quantity to what indicates his diagram of traction (ε1f) and the matrix, when being entirely adhered to the fibre of reinforcement, will do it in the same extension (ε1f), in such a way that in these conditions, the matrix practically does not work from the mechanical point of view and is only the fibre the one who acts like resistant element. The compound material has acted of synergistic form between his constituents. This conditioning is basic to put a piece of material composed in operation.
The curve tension-deformation of the material composed in reality will situate between the ones of the reinforcement and the matrix, in function of the volumetric fraction of both components. Therefore, when a compound material is subjected to an excessive load in operation, the failure can produce well because they fail the constituents or because it fail his interfase. Of this way, a road to determine the resistance of a composite demands to know the state of tensions of (figure 2):
to) The fibres, that can fail to traction or to compressesion. Usually they do not present plastic behaviour, by what when reaching the elastic limit breaks the fibre, redistributing the loads between which still have not failed.
b) The matrix, that fails mainly by micro-fisuración that extends because of loads of traction, compressesion and cutting cutting shears.
c) The interfase fibre-matrix. Because of the difference of the sharp efforts between fibre and matrix, a phase displaces regarding the another. The results of this loss of adhesion have explained previously.
d) The interfase plate-plate. When distinct layers apilan to try counter the anisotropy of the material, the failure can produce in the zone of union between the distinct plates. If this sucede, can not distribute the loads between them.
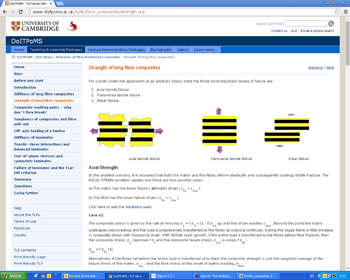
Going back to the case of a unisteeringal plate, in front of determinate load that increases successively and supposing a good adhesion between fibre and matrix, What fails first? The reinforcement (whose elastic module is upper by definition) or the matrix? Obviously this depends on the properties of said constituents and of the volumetric fraction of each one of them in the laminado. In concrete, will have to put attention to his elongation to break. It can give the case of matrices with upper elongation to break that some reinforcements. Like this, it is possible to find resins of type epoxi that they can deform until 6% before producing the extension of the microfisuraciones until observing the break of said phase, whereas so much the fibre of glass like the one of carbon do not are used to to allow more than 2% (especially these last).
When the elongation to break of the matrix is inferior to the of the reinforcement, when having a load such that produces said deformation, the matrix will crack and the load will have to be transferred entirely to the reinforcement. If, arrived to this point, the tension applied is still inferior to the product of the resistance to traction of the reinforcement by his volumetric fraction, the composite will follow bearing the load until it do not fulfil the previous condition, moment in which it will fail to traction (figure 2).
If, by the contrary, the elongation to break of the matrix is upper to the of the reinforcement, to measure that go failing the fibres, the load will transfer to the matrix, the one who presents of general form a resistance to inferior traction to the one of the reinforcement, by what also will fail of sudden form.
In the practice, is difficult to see the case of composites formed only by unisteeringal plates. Of frequent use are or the apilamientos multidireccionales or the presence of reinforcements in which the fibres orient of random form, although these last allow a level of empaquetamiento of fibres very reduced. In this type of compound materials. How predict the failure? On the one hand it is possible to attend to the classical theory of laminados, deliver the tension between all they and go deleting plates to measure that fail and redistributing again the tension between the remaining. However, the most used strategy is to trust criteria of failure polinomiales (type Tsai-Wu) in which from the properties of the compound material is possible to locate the zones of the susceptible piece of break in front of a determinate effort.
Arrived to this point, the reader can suppose that the physical laboratory – mechanic has to set up to characterise the properties of a good number of distinct laminados that compose the piece and like this can use computational tools based in finite elements where can analyse the zones of the piece in which the criterion of failure chosen predicts the split of the same. However, it is possible the reduction of the effort of characterisation with the employment of new tools that are able to predict the behaviour of the laminado (independently of the orientation of the fibres and his volumetric fraction) with a high level of precision from a very limited number of characterisations of the compound material.
In Aimplas have so much of the computational tools as of the necessary laboratories for the development of his concrete project with compound materials, optimising the design of the piece and his composition, of such form that was possible to substitute traditional materials by composites of reduced weight and cost.