Ranurado de NGVs por EDM: en la colaboración está el éxito
La creciente presión para reducir las emisiones de carbono está impulsando una inversión significativa en tecnologías más limpias y eficientes. Esto incluye la implementación de innovaciones tecnológicas como el diseño de turbinas más eficientes y el uso de materiales con mejores propiedades mecánicas.
Uno de los componentes clave de la turbina de un motor aeronáutico son los vanos de la turbina o NGV (Nozzle Guided Vanes). Los NGV forman el estator de la turbina. Se utilizan para redirigir el flujo de gas y conseguir el equilibrio termodinámico más eficiente entre velocidad y presión. De este modo se mejora la eficiencia de la turbina mediante una velocidad del gas adecuada en módulo y dirección para cada rotor. Aunque los NGVs podrían fundirse a la cera perdida como un anillo completo en motores de pequeño diámetro, normalmente se fabrican como anillos segmentados debido a las limitaciones de fundición. En este caso, es necesario ensamblar varios segmentos de NGV formando un anillo completo. Para ensamblarlos y reducir las fugas de gas, se fabrican ranuras de sellado en las caras laterales y se montan chapas metálicas en ellas. Estas ranuras se caracterizan por su elevada relación de aspecto, de 5:1 a más de 10:1, y su escasa anchura, de 0,5 a 2 mm. Incluso, los nuevos diseños de turbina necesitan de relaciones de aspecto mayores. Otro aspecto clave son los materiales, debido a las altas temperaturas de la turbina, se utilizan superaleaciones con base de níquel como MARM002, C1023 o Rene 77 para fabricar los NGVs, ya que estos materiales presentan muy buen comportamiento mecánico y de fluencia a altas temperaturas debido a sus propiedades físicas. Sin embargo, su maquinabilidad es inferior a la de otros metales utilizados en el entorno industrial.
![Figura 1. Imágenes de ejemplo de un segmento de NGV y detalle de las ranuras realizadas por electroerosión en dicho segmento [4]... Figura 1. Imágenes de ejemplo de un segmento de NGV y detalle de las ranuras realizadas por electroerosión en dicho segmento [4]...](https://img.interempresas.net/fotos/4713343.jpeg)
Con estas características de pieza y material, prácticamente el único método aplicable para fabricar estas ranuras es la electroerosión. Son conocidos los beneficios de este proceso, su independencia de la dureza del material y su alta precisión, hacen que sea una solución viable para realizar estas operaciones en los NGV. Es por ello, que es un proceso implantado en la industria de fabricación de motores aeronáuticos, gracias a las labores de investigación y mejora del proceso que se han llevado en los últimos años. En este contexto, ITP Aero, empresa líder global en motores y componentes aeronáuticos, ONA, empresa fabricante de máquinas de electroerosión y la Universidad del País Vasco, en el CFAA, llevan colaborando casi 15 años en proyectos de investigación orientados a la mejora del proceso de ranurado de NGV mediante electroerosión.
Este articulo pretende brindar una visión integral de las investigaciones llevadas a cabo en la fabricación de ranuras de NGV, abarcando desde la optimización de parámetros de proceso hasta el estudio de técnicas avanzadas de limpieza, el desarrollo de estrategias innovadoras de erosión y la implementación de métodos para recuperar y reafilar los electrodos directamente en la máquina de electroerosión.
Primer objetivo: ajustar los parámetros de proceso
La primera colaboración para la optimización de parámetros en ranuras de NGVs, comenzó hace más de 10 años [1]. En este trabajo se estudió la influencia de los principales parámetros de proceso que intervienen en la erosión con el objetivo de determinar el efecto de los parámetros relacionados con el proceso de descarga sobre el tiempo de mecanizado y el desgaste del electrodo.
![Figura 2. Esquema de la geometría de electrodos utilizada y puntos de medición de las ranuras [1] Figura 2. Esquema de la geometría de electrodos utilizada y puntos de medición de las ranuras [1]](https://img.interempresas.net/fotos/4713344.jpeg)
El material en los que se hicieron los ensayos fue la aleación base níquel C1023, en ranuras en ángulo, de 0,8 mm y profundidad de 6,5 mm. Para cada ensayo (tandas de 5 ranuras) se midió el desgaste del electrodo, el tiempo de erosión y las dimensiones de las ranuras. Los ensayos se realizaron en una ONA CS300 y con grafito POCO EDM3. Se realizó un DOE variando los siguientes procesos de descarga:
- La corriente (I): valor medio de la corriente de la descarga. Se probaron 3 niveles de descarga 24A, 32A y 48A.
- El tiempo de impulso (tp): tiempo de duración de la descarga en microsegundos. Se probaron valores entre 40 y 100 microsegundos. El valor de tiempo de pausa para cada ensayo fue el doble del valor del tiempo de pulso.
- El servo (S): parámetro responsable de mantener constante la distancia entre el electrodo y la pieza durante el proceso. Se utilizaron valores de entre 40V y 60V.
Los resultados se analizaron con la metodología ANOVA. En lo referente al desgaste de electrodo, los resultados mostraron que el valor de desgaste aumenta al disminuir el tiempo de impulso para las 3 corrientes de intensidad (24A, 32A y 48A). Es decir, para una intensidad de descarga fija, una mayor cantidad de descargas aumenta el desgaste del electrodo. Por lo que, el mayor desgaste de electrodo se encuentra con valores bajos de tiempo de impulso y la intensidad más alta. Por el contrario, para el valor más alto de tiempo de pulso, se observó el efecto contrario (Figura 3). Esto se debe a que la combinación de una intensidad de corriente alta y un tiempo de pulso alto hacen que el electrodo sufra durante menos tiempo, disminuyendo el desgaste del electrodo. Finalmente, la influencia del servo en el desgaste del electrodo fue inexistente.
![Figura 3. Comparación del desgaste del electrodo entre las tres corrientes de intensidad [1] Figura 3. Comparación del desgaste del electrodo entre las tres corrientes de intensidad [1]](https://img.interempresas.net/fotos/4713345.jpeg)
Por otro lado, el servo tiene efecto en el tiempo de erosión (Figura 4). Cuanto menor es éste, menor es el tiempo de proceso. Esto se debe a que cuando el valor del servo es mayor, la separación entre pieza y electrodo también es mayor, resultando en un mayor número de descargas que no eliminan material. Además, para el tiempo de impulso, se observaron dos tendencias. En corrientes de intensidad bajas (24A y 32A), a medida que disminuye también lo hace el tiempo de erosión. Sin embargo, para la corriente media de 48A, a medida que aumenta el tiempo de impulso, disminuye el tiempo de erosión.
![Figura 4. Tiempo medio de erosión de las ranuras en función del tiempo de impulso y del servo para tres intensidades de corriente [1]... Figura 4. Tiempo medio de erosión de las ranuras en función del tiempo de impulso y del servo para tres intensidades de corriente [1]...](https://img.interempresas.net/fotos/4713346.jpeg)
En general, los resultados revelaron que la corriente de descarga, así como el tiempo de pulso, son los parámetros de proceso más influyentes. Siendo los valores óptimos, para menor desgaste de electrodo y menor tiempo de erosión, una intensidad de corriente alta, un tiempo de impulso alto y servo bajo. A partir de este estudio se adquirió conocimiento sobre el proceso, permitiendo así continuar con investigaciones para optimizar la electroerosión de ranuras.
Segundo objetivo: evacuación total de los residuos
El efecto de la limpieza en el proceso de erosión se ha estudiado en profundidad durante décadas [2], pero hoy en día sigue siendo uno de los parámetros más difíciles de aplicar correctamente. Existen varios métodos para aplicarlo: limpieza interna, limpieza externa, succión o movimientos de electrodo. Sin embargo, conseguir una evacuación completa de los residuos es una tarea difícil porque el espacio entre el electrodo y la pieza es muy estrecho y el flujo de limpieza no puede acceder a la zona fácilmente.
Gracias al conocimiento adquirido en el primer estudio, el equipo de la UPV/EHU llevó a cabo una investigación [3] para analizar diversos métodos de evacuación de residuos en el mecanizado por electroerosión de ranuras. En los ensayos realizados en ranuras, se detectó que hasta cierta profundidad la erosión se mantenía estable pero superada esa profundidad, la inestabilidad hacía que la tasa de arranque decayese (Figura 5). La razón de esta inestabilidad se achaca a que llega una profundidad en la que los residuos generados no salen fácilmente y generan cortos que inestabilizan el proceso, influyendo esto en la tasa de arranque.
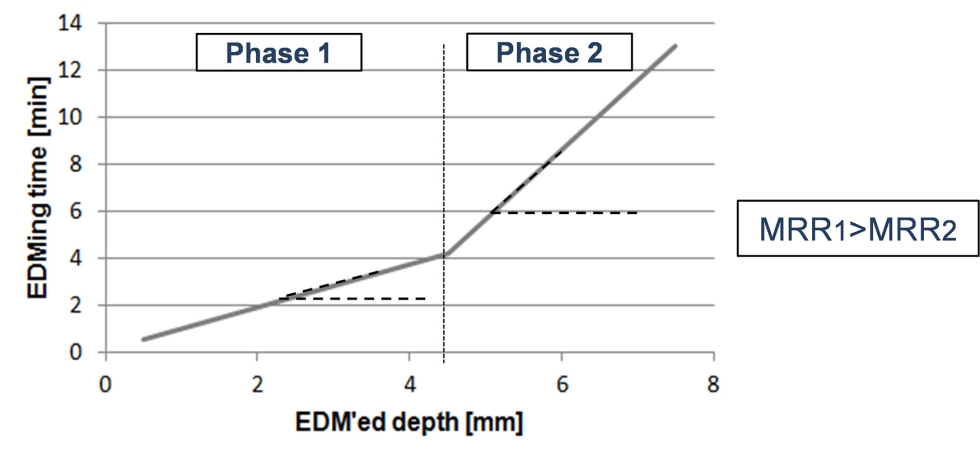
Utilizando una cámara de alta velocidad, y un montaje donde la zona de erosión estaba cubierta por material trasparente, se probaron y grabaron diferentes estrategias de limpieza con el fin de analizar los movimientos de los residuos generados durante la erosión y elegir la técnica más adecuada.
![Figura 6. (a) Esquema del sistema de grabación de alta velocidad y (b) montaje realizado [3] Figura 6. (a) Esquema del sistema de grabación de alta velocidad y (b) montaje realizado [3]](https://img.interempresas.net/fotos/4713348.jpeg)
Para ello, se realizaron con dos electrodos diferentes (recto e inclinado, ambos de 0.8 mm de espesor) unos ensayos sin limpieza, con limpieza intermitente (aplicada mediante una boquilla) y con limpieza en continuo. Además, se programó el movimiento de salida del electrodo a diferentes alturas: hasta la mitad de la ranura, hasta la entrada de la ranura y hasta un punto fuera de la ranura.
Las grabaciones mostraron el movimiento de los residuos en las diferentes condiciones (Figura 5). En general, en el caso de las ranuras rectas la evacuación es más difícil que en las ranuras inclinadas. Esto se debe a que, en el caso de las ranuras inclinadas, la fuerza de gravedad ayuda a evacuar las partículas de la cavidad.
![Figura 7. Ejemplo de secuencias de las grabaciones realizadas para ranuras (a) rectas e (b) inclinadas [3] Figura 7. Ejemplo de secuencias de las grabaciones realizadas para ranuras (a) rectas e (b) inclinadas [3]](https://img.interempresas.net/fotos/4713349.jpeg)
En conclusión, los resultados revelaron que la mejor limpieza de ranura se obtiene con un flujo de aceite aplicado de forma continua y un movimiento de electrodo hasta un punto por encima del límite de la ranura. De este modo, el flujo de aceite entra en la cavidad para una limpieza más profunda. En ranuras inclinadas, la aplicación de este método obtiene una limpieza total de la cavidad. Sin embargo, para ranuras rectas, aunque la mayoría de las partículas salían de la cavidad, no se conseguía la evacuación total con los métodos propuestos.
Tercer objetivo: cambio de estrategia
En la última década se han desarrollado diferentes estrategias con el objetivo de mejorar las condiciones de limpieza y poder garantizar la estabilidad del mecanizado en profundidad. Una estrategia ampliamente utilizada en la industria para conseguir la rugosidad superficial requerida es el movimiento planetario del electrodo. Se consigue programando una secuencia de movimientos predeterminados por el sistema de control CNC que están condicionados por la subdimensión del electrodo y el valor de rugosidad superficial requerido.
Con el fin de mejorar la eficiencia del proceso de mecanizado de ranuras por electroerosión, en esta colaboración [4] se propuso el uso del movimiento planetario del electrodo como estrategia para acelerar la evacuación de los residuos.
La figura 8 muestra un esquema de la estrategia propuesta. El movimiento planetario del electrodo se realizó orbitando dos ejes que no están incluidos en el servo-control, en este caso los ejes X e Y, y la profundidad de mecanizado se determinó mediante el eje servo-controlado, en este caso el eje Z. Para aplicar la estrategia de movimiento planetario, se debía definir el valor del radio de órbita, que determina los movimientos del eje XY. El estudio experimental analizó la efectividad de la estrategia y el efecto del radio de órbita.
![Figura 8. Esquema de la estrategia de movimiento planetario propuesta [4] Figura 8. Esquema de la estrategia de movimiento planetario propuesta [4]](https://img.interempresas.net/fotos/4713350.jpeg)
El material utilizado para realizar los ensayos fue la aleación base níquel C1023, en ranuras en ángulo de espesor 0.8 mm. Para analizar el efecto del movimiento planetario, se realizaron dos estrategias diferentes. Para los ensayos se utilizó grafito ELLOR +50 y se realizaron en una máquina ONA QX7, dotada de generador digital de última tecnología. Dado que el objetivo era comparar las estrategias de mecanizado propuestas, las condiciones de mecanizado por electroerosión no se modificaron durante el estudio, y se seleccionaron a partir de trabajos de investigación anteriores [1]. Los resultados se discutieron en términos de tiempo de proceso, tasa de eliminación de material (MRR) y desgaste volumétrico del electrodo (V%), que se calcula dividiendo el volumen de desgaste del electrodo entre el volumen de material eliminado.
En primer lugar, se analizó el efecto del valor del radio de órbita. Se estudiaron cinco radios (R) diferentes, desde 0, que corresponde con la condición estándar, hasta 0,1 mm. En este caso, el movimiento planetario del electrodo de la herramienta se aplicó desde el inicio del mecanizado.
Como era de esperar, en estos ensayos se observó que el uso del movimiento planetario reduce el tiempo de erosión y aumenta la MRR. Esto se atribuye a que el movimiento planetario produce dos efectos. Por un lado, cuando se aplica el movimiento planetario el electrodo se mueve en los ejes XYZ. Esto implica un movimiento del dieléctrico diferente y, por tanto, diferentes movimientos de los residuos, lo que puede mejorar las condiciones de limpieza. Por otro lado, la separación entre el electrodo y la pieza aumenta con el valor del radio programado, facilitando la evacuación de las partículas. Así, la combinación de ambos efectos, el movimiento del dieléctrico y la ampliación de la separación, mejoraban la estabilidad del proceso, lo que resultaba en la mejora de la eficacia del mecanizado.
Concretamente, los resultados óptimos en cuanto a tiempo de erosión y MRR se obtuvieron con un radio de 0.05mm, a partir de este radio no se mejoraba el tiempo de erosión. En comparación con los resultados obtenidos sin movimiento planetario, el tiempo de erosión disminuyó un 18% y la MRR aumentó un 52%. Sin embargo, el desgaste volumétrico del electrodo fue menor con un radio más grande de órbita, el de 0,1 mm.
En segundo lugar, se realizaron experimentos adicionales para estudiar la posibilidad de combinar ambas estrategias, la estándar sin movimiento planetario y la de movimiento planetario a partir de una determinada profundidad de mecanizado. De esta manera, se propuso una estrategia en la que de 0 a 3,5 mm de profundidad no se aplica movimiento orbital, ya que hasta esta profundidad el proceso es estable (tal como se muestra en la figura 5), y de esta profundidad en adelante se erosionó con movimiento orbital. Además, se compararon dos valores diferentes de radio, radio de 0,035 y de 0,05 mm. Los resultados mostraron que en comparación con la estrategia anterior se consiguió una ligera mejora en tiempo de erosión y MRR con el radio de 0.035mm, pero no con el de 0,05 mm.
En general, los resultados demostraban que el movimiento planetario del electrodo durante el proceso de mecanizado es una solución industrial prometedora para mejorar la productividad. Además, se concluyó que la segunda estrategia resulta mejor cuando el radio de la órbita no es superior a 0,05 mm.
Cuarto objetivo: recuperación de electrodos durante el proceso
Una vez desgastados los electrodos, una técnica para ahorrar tiempo de mecanizado, es el reafilado de electrodos. Este proceso consiste en utilizar la propia máquina de electroerosión, donde se realizan las ranuras, para recuperar la forma del electrodo. Se realiza erosionando la zona desgastada del electrodo contra una placa denominada sufridera. Teniendo esta idea de base, se exploró la posibilidad de obtener mejores tiempos de proceso aplicando un reafilado de electrodos capaz de recuperar completamente su cara frontal [5] mediante una interpolación lineal.
Inicialmente se probaron dos trayectorias de mecanizado diferentes para comparar la influencia del área de descarga entre el electrodo y la placa. Una de ellas implicaba interpolar el electrodo con la dimensión más larga paralelamente a la placa, obteniendo un área de descarga pequeña (Figura 9 condición 1), erosionada a través de una traslación larga del electrodo. La otra interpolaba perpendicularmente a la placa para obtener la configuración contraria, una gran área de descarga erosionada a través de una pequeña traslación del electrodo (Figura 9 condición 2). La estrategia paralela fue más rápida y produjo menos desgaste lineal en la placa, como era de esperar. Este trabajo se centraba en esta estrategia, sólo aplicable a electrodos rectos.
![Figura 9. Condiciones de trabajo de las pruebas. Durante las pruebas se utilizó la condición 2 [5] Figura 9. Condiciones de trabajo de las pruebas. Durante las pruebas se utilizó la condición 2 [5]](https://img.interempresas.net/fotos/4713351.jpeg)
Utilizando grafito ultrafino ELLOR +50 como material del electrodo y el acero dulce y cobre tungsteno como materiales de sufridera, se estudió la influencia de diferentes parámetros de proceso en los materiales de las placas. Los ensayos se realizaron en la máquina ONA QX7 del CFAA. Los parámetros de trabajo iniciales se basaron en las recomendaciones del fabricante de la máquina herramienta (ONA) y se ajustaron el tiempo de impulso y el ciclo de trabajo para conseguir un proceso estable que permitiera un mecanizado estable con el valor de ciclo de trabajo más alto. Cuando se encontró este valor de ciclo de trabajo, se varió la intensidad de descarga para observar su efecto en los parámetros de prueba. Finalmente, se hicieron cambios similares con el valor del servo.
Una vez obtenidos el tiempo de proceso y el desgaste de la placa para las diferentes condiciones, se llegó a las siguientes conclusiones:
- Tiempo de proceso: ambos materiales mostraban un punto óptimo de intensidad de descarga a partir del cual cualquier variación en ella provocaba un aumento del tiempo, aunque la placa de acero mostraba una menor influencia de este parámetro que la placa de cobre-tungsteno. Del mismo modo, la variación del ciclo de trabajo, mostraba unos valores muy estables en el caso de placa de acero. Este efecto puede atribuirse a la mayor maquinabilidad del acero, que permite la estabilidad a través de grandes cambios en los valores de ciclo de trabajo. Finalmente, la variabilidad del servo mostraba una influencia mínima en el tiempo de proceso.
- Desgaste de placa: las variaciones del valor de intensidad de la descarga mostraban efectos similares en el desgaste a los del tiempo de proceso. Esto sugiere la existencia de una banda estrecha de valores de intensidad en la que se encuentran los valores más bajos de tiempo y de desgaste de la placa. En el caso del servo, había muy poca variación, aunque parece que valores más bajos de servo obtenían menor desgaste. El parámetro menos influyente fue el ciclo de trabajo.
De este estudio se concluyó que el parámetro más influyente es el valor de la intensidad de la descarga, tanto en el tiempo de proceso como en el desgaste de las placas. Además, el ciclo de trabajo es poco influyente en el tiempo de proceso cuando se trabaja con la combinación grafito-acero y mucho mayor cuando se trabaja con la placa Cu-W.
La colaboración continua
En este artículo, nos propusimos reunir y presentar los estudios realizados en colaboración entre tres pilares clave: el fabricante de piezas (ITP Aero), el fabricante de máquinas (ONA EDM) y el centro de investigación (UPV/EHU, CFAA). Queremos mostrar cómo la colaboración entre estos tres mundos es esencial si se quiere obtener un conocimiento integral del proceso de cara a su mejora. Se ha analizado cuáles son los parámetros de proceso que más afectan a su productividad, se ha estudiado la importancia de una buena limpieza y se han probado diferentes estrategias para mejorarla y, además, se han desarrollado una metodología para evitar el mecanizado de electrodo y recuperar su forma en la propia máquina. Sin embargo, los estudios realizados en colaboración que se han tratado en este artículo no han contemplado el uso de los datos de proceso para la mejora y optimización de éste. La revisión realizada sobre los estudios más recientes de otros grupos de investigación muestra que puede ser un aspecto clave a la hora de tener un control de lo que está sucediendo. En un proceso establecido, la búsqueda de un patrón de normalidad puede ayudar a detectar problemas durante la fabricación, desechando la pieza antes de los controles de calidad pertinentes y evitando así el tiempo del propio control.
Además, los datos pueden ayudar a conocer mejor el proceso, el tipo de descargas que se generan durante la erosión y el efecto que tiene cada tipo puede ser muy valioso para mejorar la adaptación de la maquina a situaciones no deseadas de una manera más eficaz y específica para el tipo de operación. El proceso de electroerosión conlleva una frecuencia de descargas muy alta, por lo que es necesario captar señales a alta frecuencia si se quiere actuar sobre el proceso, a niveles del microsegundo. En otros niveles de actuación, para tener métricas globales de lo que está sucediendo en las maquinas durante su operación, es suficiente con captar datos a niveles de segundo. Es por ello por lo que se está apostando por la adquisición de datos a distintos niveles de frecuencia y actualmente se está trabajando en proyectos de colaboración para trabajar en esta línea.
Y es que, a lo largo de todos estos años, hemos aprendido que la colaboración es fundamental para adquirir el conocimiento necesario que se refleja en mejoras significativas en nuestros procesos de producción. Desde el principio, hemos comprendido que trabajar juntos nos permite avanzar más rápido y de manera más eficiente. Esta filosofía ha sido el motor que nos impulsa a unir fuerzas, compartir experiencias y conocimientos, y alcanzar metas que de otro modo serían inalcanzables. A través de la colaboración continua entre el fabricante de piezas, el fabricante de máquinas y el centro de investigación, hemos logrado no solo avanzar en la comprensión de nuestros procesos, sino también en la implementación de soluciones innovadoras que nos llevan hacia un futuro más prometedor en el ámbito de la producción industrial. Como dice el famoso proverbio africano, ‘si quieres ir rápido, camina solo, pero si quieres llegar lejos, ve acompañado’.
Y los demás, ¿qué hacen?
Una revisión de la bibliografía nos muestra que otros grupos de investigación han seguido líneas similares de investigación en la temática de la fabricación de ranuras mediante electroerosión. En lo referente al estudio y optimización de los parámetros de corte, destacan trabajos como los de Aas [6], en el que estudiaron el efecto de diferentes parámetros de electroerosión en las ranuras cerradas en el material aeronáutico con níquel base IN100mod, modificando intensidad y el tiempo de pulso. Ulhmann y su equipo también realizaron numerosos trabajos en este campo. Destaca la labor que hicieron analizando el proceso de ranurado en la superaleación de base níquel MAR-M247, modificando los parámetros para mejorar los tiempos de erosión [7]. En este trabajo lograron un ahorro del 50% respecto a los tiempos de proceso que se obtenían en el proceso industrial. Más adelante, Klocke [8] también realizó un estudio en dos aleaciones gamma de titanio-aluminio, GE 48-2-2 y 45XD, del desgaste del electrodo y de las cantidades de material eliminado, modificando los parámetros de erosión en la fabricación de ranuras por electroerosión. En esta misma línea, este mismo autor, realizó en un trabajo posterior [9] un estudio en otra aleación gamma TiAl, TNM-B1, para la erosión de ranuras con un grafito estándar SGL R8650. Lo más significativo de este estudio es el control de proceso desarrollado basado en el umbral de la tensión. Apoyándose en estudios anteriores, determinó que una de las señales eléctricas de proceso más importantes es la tensión y de forma más especifica el umbral de la tensión de descarga. Cuando el umbral que se fija es demasiado alto, se interrumpen demasiadas descargas buenas. En cambio, si este se fija demasiado bajo, se producen demasiadas descargas con una tensión de descarga baja. Por consiguiente, se puede estimar un valor óptimo de la tensión de descarga o del umbral para cada aplicación.
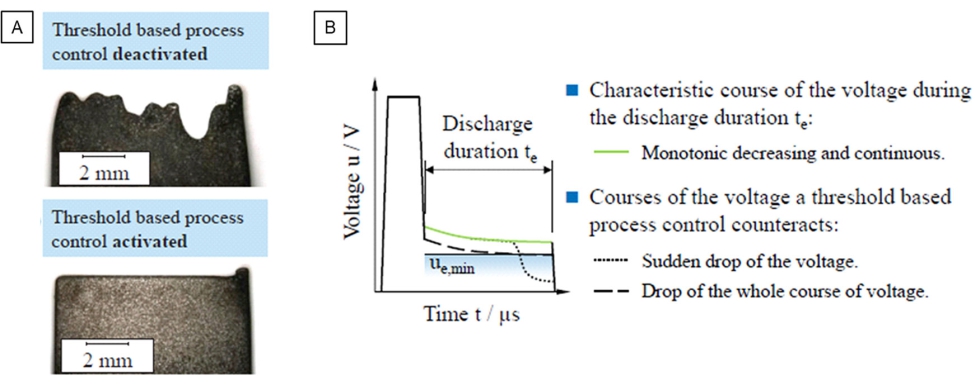
En lo referente al reafilado de electrodos, los trabajos bibliográficos sobre esta tecnología son escasos y todos son del mismo equipo de investigación, relacionado en otros trabajos con MTU dentro del programa CLAIRE (Clean Air Engine from MTU Aero Engines). Este equipo publicó dos trabajos en los que se trata la problemática de reafilado de electrodos para realizar ranuras en NGV en la aleación base níquel MAR-M247 [10] [11]. Ambos artículos son muy parecidos, se utilizaron electrodos de grafito de dos tipos, siendo ambos grafitos ultrafinos. En cuanto al material de las sufrideras se eligieron 3 materiales distintos para las pruebas: grafito, latón y metal duro.
Por último, es interesante destacar los trabajos realizados en el ámbito de los datos. Lo más destacado lo realizaron Caggiano y su equipo, trabajando en la monitorización de proceso de ranurado en NGVs [12]. El objetivo de este trabajo de investigación fue desarrollar un procedimiento avanzado de monitorización del proceso de electroerosión basado en la identificación de correlaciones entre los parámetros del proceso de electroerosión por penetración y las condiciones inadecuadas del proceso que podrían incrementar el tiempo de mecanizado y causar una calidad de pieza inaceptable. El objetivo final fue emplear el procedimiento avanzado de monitorización de sensores para supervisar el proceso de electroerosión desde la perspectiva de control de los defectos. Este mismo grupo, en un trabajo posterior [13] aplicó una técnica de clustering a las señales obtenidas en los ensayos. Compararon los resultados obtenidos con el método anterior de detección de anomalías, teniendo resultados, mejores que el método anterior.
Referencias
[1] Ayesta I, Izquierdo B, Sánchez JA, Ramos JM, Plaza S, Pombo I, Ortega N, Bravo H, Fradejas R, Zamakona I. Influence of EDM Parameters on Slot Machining in C1023 Aeronautical Alloy. Procedia CIRP 2013; 6:129-134.
[2] Masuzawa T, Tsukamota J, Fujino M. Drilling of deep microholes by EDM. CIRP Annals-Manufacturing Technology 1989; 38:195-198.
[3] Ayesta I, Flaño O, Izquierdo B, Sánchez JA, Plaza S. Experimental Study on Debris Evacuation during Slot EDMing. Procedia CIRP 2016; 42:6-11.
[4] Flaño O, Bravo H, Ayesta I, Ramos JM, Zamakona I. Enhancement of EDM performance in high-aspect ratio slots for turbomachinery by planetary motion of the electrode. Procedia CIRP 2020; 95:516-521.
[5] Bravo H, Ayesta I, Sánchez JA, Zamakona I, Izquierdo B, Flaño O, del Campo J. Study of Interpolation Strategies to Dress Electrodes by Means of EDM. Procedia CIRP 2018; 68:393-398.
[6] Aas KL. Performance of two graphite electrode qualities in EDM of seal slots in a jet engine turbine vane. Journal of Materials Processing Technology 2004; 149:152-156.
[7] Uhlmann E, Domingos DC. Development and Optimization of the Die-Sinking EDM-Technology for Machining the Nickel-Based Alloy MAR-M247 for Turbine Components. Procedia CIRP 2013; 6:180-185.
[8] Klocke F, Holsten M, Hensgen L, Klink A. Experimental Investigations on Sinking-EDM of Seal Slots in Gamma-TiAl. Procedia CIRP 2014; 24:92-96.
[9] Klocke F, Holsten M, Welling D, Klink A, Perez R. Influence of Threshold Based Process Control on Sinking EDM of a High Aspect Ratio Geometry in a Gamma Titanium Aluminide. Procedia CIRP 2015; 35:73-78.
[10] Uhlmann E, Domingos DC. Automated dressing of graphite electrodes for electrical discharge machining (EDM) of seal slots in turbine components. Procedia Manufacturing 2016; 6:45-52.
[11] Uhlmann E, Domingos DC. Dressing of graphite electrodes for EDM of seal slots in nickel-base alloy MAR-M247. Procedia CIRP 2016; 42:328-333.
[12] Caggiano A, Napolitano F, Teti R, Bonini S, Maradia U. Advanced die sinking EDM process monitoring based on anomaly detection for online identification of improper process conditions. Procedia CIRP 2020; 88:381-386.
[13] Caggiano A, Napolitano F, Teti R. Hierarchical cluster analysis for pattern recognition of process conditions in die sinking EDM process monitoring. Procedia CIRP 2021; 99:514-519.