Fresado con bola para la fabricación de álabes aeronáuticos
En España, el sector aeroespacial juega un papel crucial en la economía nacional, siendo uno de los principales motores de innovación y desarrollo tecnológico. Empresas españolas como Airbus y Aernnova están a la vanguardia en la producción de componentes aeronáuticos, incluyendo los álabes aerodinámicos. La colaboración entre estas empresas y centros de investigación, como el Instituto Nacional de Técnica Aeroespacial (INTA) y diversas universidades, ha permitido avances significativos en técnicas de fabricación avanzadas. Estos esfuerzos están alineados con las políticas europeas de sostenibilidad y eficiencia energética, contribuyendo a la competitividad de España en el mercado global de la aviación.
![Figura 1 Crecimiento anual promedio de vuelos desde Europa 2019-2050 [2] Figura 1 Crecimiento anual promedio de vuelos desde Europa 2019-2050 [2]](https://img.interempresas.net/fotos/4713272.jpeg)
La fabricación de álabes aerodinámicos son componentes esenciales para el rendimiento y la eficiencia de los motores de los aviones, enfrentando desafíos significativos [3]. Entre los factores más importantes a tener en cuenta durante el mecanizado de álabes se encuentran las superficies libres complejas de los componentes, la necesidad de mantener tolerancias dimensionales estrictas y la calidad del acabado superficial. Otro factor a tener en cuenta es el material del que están hechas las piezas. Los materiales de los álabes presentan desafíos adicionales debido a su dureza y tendencia a generar altas temperaturas durante su mecanizado, en los ensayos realizados el material utilizado es una aleación de titanio, en concreto el Ti6Al4V. Es necesario una selección adecuada de herramientas de corte y parámetros de corte optimizados son cruciales para abordar estos desafíos.
Un aspecto crítico en el fresado de álabes es la inclinación de la herramienta de corte. La inclinación adecuada puede mejorar significativamente la calidad del mecanizado, especialmente en la creación de paredes delgadas, que son comunes en los álabes aerodinámicos [4]. La inclinación de la herramienta afecta a diversos factores del proceso de mecanizado, como son la estabilidad de la herramienta, la calidad del acabado superficial y la fuerza de corte que está relacionada con la potencia consumida de la máquina.
Una inclinación incorrecta puede producir una distribución desigual de las fuerzas de corte, lo que puede provocar vibraciones indeseadas y un mayor desgaste de la herramienta. Además, las paredes delgadas pueden ser particularmente susceptibles a deformaciones y defectos durante el mecanizado. La optimización del ángulo de inclinación es crucial para minimizar estos problemas y garantizar la integridad estructural de los componentes mecanizados.
En este artículo, se explora cómo la inclinación de la herramienta de corte influye en el fresado de álabes y en el mecanizado de paredes delgadas. Se analizan también las estrategias y técnicas que se han desarrollado para optimizar este parámetro, mejorando así la eficiencia y la precisión del proceso de fresado con bola. Este factor es fundamental para asegurar que los álabes cumplan con los estrictos estándares de precisión y durabilidad requeridos en la industria aeroespacial.
Para evaluar el efecto de la inclinación de la herramienta de corte en el mecanizado de álabes aerodinámicos, se prepararon varias muestras de la aleación de titanio Ti6Al4V. Las muestras eran piezas rectangulares de pared delgada, con dimensiones de 83 x 50 x 3,5 mm. Estas, se trataron térmicamente para eliminar tensiones residuales, asegurando así la estabilidad dimensional durante el proceso de mecanizado y se cortaron mediante corte por hilo, una tecnología que garantiza dimensiones consistentes entre las piezas. Posteriormente, se mecanizaron para obtener los resultados de mecanizados semejantes a los que se pueden obtener mediante el mecanizado de un álabe.
La batería de ensayos se llevó a cabo en un centro de mecanizado multitasking de 5 ejes Kondia HS1000, equipado con un electro husillo capaz de alcanzar las 24.000 rpm. Durante los ensayos, se registró la potencia eléctrica del husillo con el objetivo de, posteriormente, determinar el impacto ambiental del nuevo proceso de mecanizado para álabes de aviación. Una vez mecanizadas las probetas, estas fueron analizadas superficialmente con un microscopio de foco infinito Alicona® para verificar las rugosidades superficiales obtenidas y determinar su validez para ser aplicadas al mecanizado de álabes.
Las condiciones de corte utilizadas se establecieron acorde a los valores dados por el fabricante en el catálogo. Estas condiciones incluyeron una velocidad de corte de 240 m/min, un avance por diente de 0,05 mm/z, una profundidad de corte de 1 mm y un desplazamiento constante de la fresa perpendicular a la superficie de 0,50 mm. Las orientaciones de herramienta estudiadas fueron de 30°, 45°, 60° y 75° con respecto al eje de la herramienta tal y como se observa en la figura 2.
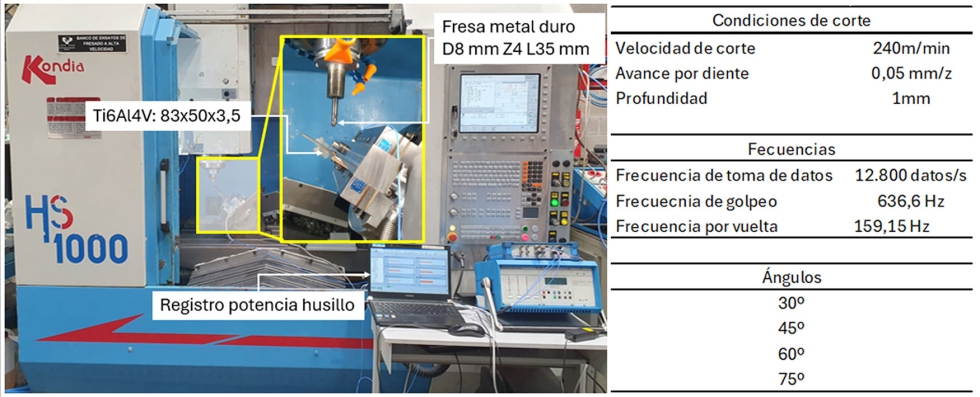
En el proceso de fresado de álabes aerodinámicos, es crucial comprender cómo las variaciones en la inclinación de la herramienta de corte pueden afectar el régimen de corte, pasando de ser una técnica de corte en concordancia a oposición. Este fenómeno ocurre cuando, al mantener constantes todas las condiciones de corte, solo se ajusta la inclinación de la herramienta. Tal como se observa en la figura 3, la fresa puede cambiar su punto de contacto, pasando de cortar con la parte izquierda a cortar con la parte derecha y el centro de la bola. Este fenómeno se produce específicamente cuando se mecaniza desde el extremo de la pieza, con el material por debajo de la herramienta. Esta es la forma común de mecanizar los álabes, ya que permite mantener la rigidez del mismo durante el proceso.
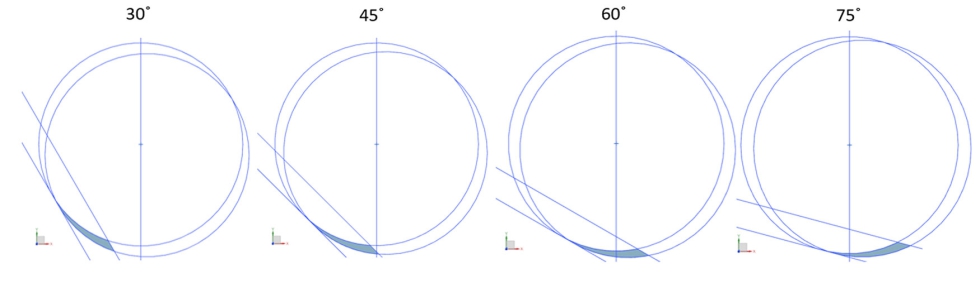
Tal como se ha explicado, al mantener constantes todos los parámetros de corte excepto el ángulo de inclinación de la herramienta, se obtuvieron las piezas mostradas en la figura 4. Durante el mecanizado de las piezas con ángulos de 30° y 45°, se produjeron vibraciones significativas, especialmente en las áreas con mayor voladizo. Estas zonas, debido a su naturaleza como paredes delgadas empotradas en un extremo, estas son particularmente propensas a las vibraciones porque la falta de soporte adicional reduce su rigidez estructural, permitiendo una mayor deformación de la pieza durante le mecanizado, a medida que la herramienta se acerca al punto de amarre la vibración y la deformación de la pieza disminuye.
Las vibraciones no solo afectan la precisión del mecanizado, sino que también pueden provocar un acabado superficial deficiente y desgaste prematuro de la herramienta. En contraste, las piezas mecanizadas con ángulos de 60° y 75° no experimentaron vibraciones, logrando un buen acabado superficial y un corte estable a lo largo de toda la pieza, que es el resultado deseado en el proceso de mecanizado.
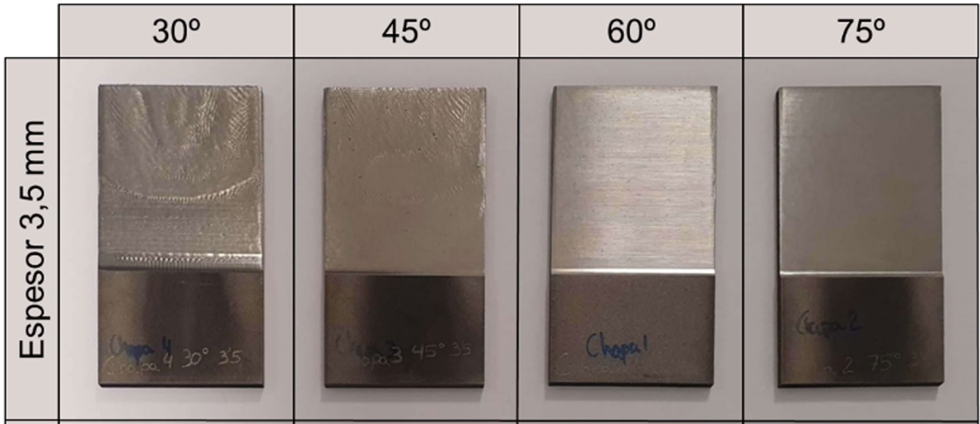
En cuanto a los resultados obtenidos, como se ha indicado anteriormente, en esta batería de ensayos se registró la energía consumida por el husillo con el fin de determinar las condiciones óptimas para poder ser aplicada en el mecanizado de un álabe y obtener unas piezas semi acabadas y dentro de tolerancias. En relación con el consumo eléctrico del husillo, en la figura 5 se muestran los consumos medios con cada uno de los ángulos de herramienta analizados.
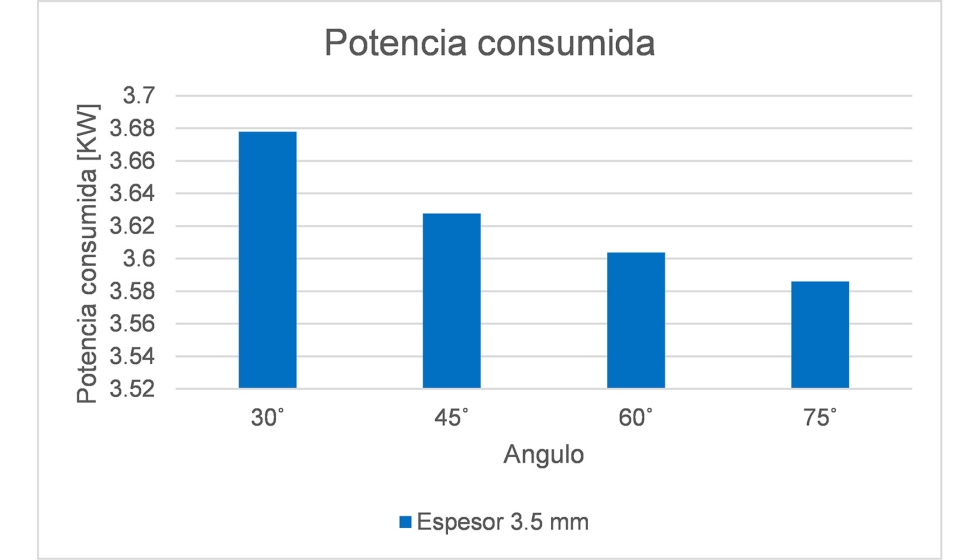
La potencia media máxima recogida ha sido en el caso de la pieza con ángulo de 30°, mientras que la potencia media mínima recogida se ha producido en la pieza de mecanizada con el ángulo de inclinación de herramienta de 75°. La diferencia de potencia entre ambas situaciones difiere en 95 W lo cual implica la existencia de un 3% de mejora al utilizar un ángulo respecto al otro en lo que respecta a potencia consumida.
Este fenómeno se debe a que, en los casos de 30° y 45°, la herramienta mecaniza en concordancia en lugar de en oposición, ya que la fresa de acabado utilizada es una fresa de bola, y este efecto es intrínseco a este tipo de mecanizado con el material por debajo de la herramienta tal y como se ha explicado. Este, es un fenómeno a tener en cuenta ya que la diferencia de técnica afecta tanto a las fuerzas de mecanizado como al acabado superficial y dimensional de las piezas.
El fresado en concordancia, también conocido como fresado a favor, ofrece varias ventajas significativas. Una de las principales es la calidad superior del acabado superficial, ya que la herramienta de corte rota en la misma dirección que el avance de la pieza, lo que reduce la formación de rebabas y mejora la suavidad de la superficie. Sin embargo, una desventaja notable es que el fresado en concordancia puede inducir vibraciones, especialmente en piezas con gran voladizo. Estas vibraciones se deben al mayor compromiso del filo de corte, lo que puede causar inestabilidad y afectar la precisión del mecanizado, como se observa en los ángulos de 30° y 45°.
Por otro lado, el fresado en oposición, conocido también como fresado en contra, tiene sus propias ventajas y desventajas. Una ventaja clave es la mayor estabilidad y control sobre el proceso de mecanizado, por lo que se minimiza el riesgo de vibraciones y mejora la precisión en piezas tal y como se observa en las piezas de 60° y 75°.
A continuación, se analiza el acabado superficial de las piezas mecanizadas con el fin de obtener cual ha sido el efecto de la inclinación la herramienta en las mismas. En la figura 6, se muestran los resultados obtenidos con el microscopio Alicona. En dicha figura se observa como en las superficies mecanizadas con un ángulo de herramienta de 30° y 45°, respectivamente se generan marcas en forma de onda producidas por un corte inestable el cual genera vibraciones, la diferencia de la superficie es mayor a 200 micrómetros. Sin embargo, al mecanizar con los ángulos de 60° y 75°, este efecto desaparece obteniendo una calidad superficial homogénea a lo largo de toda la pieza.
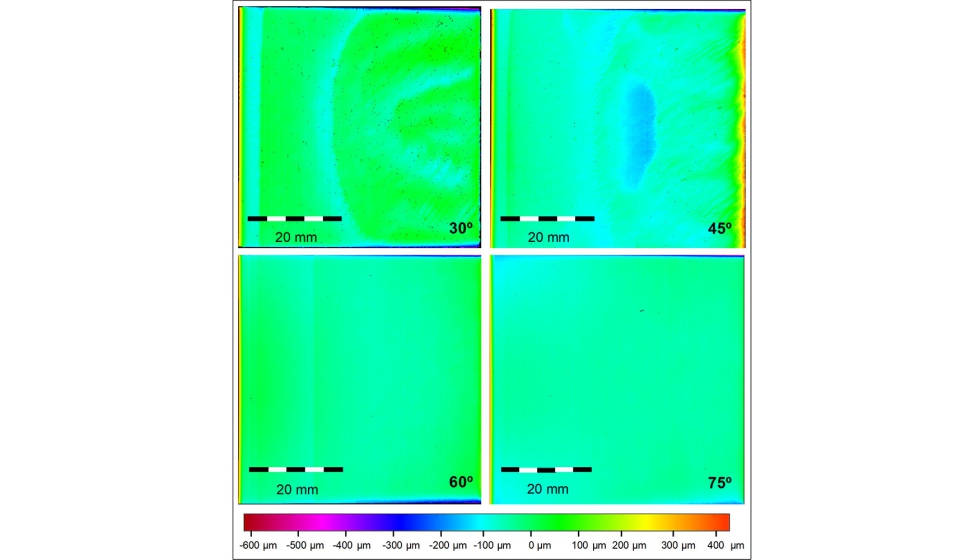
La figura anterior es del área mecanizada completa de 50 x 50 milímetros, lo cual no es la distancia óptima para evaluar la rugosidad real. Según las normas ISO 4287 e ISO 4288, la longitud de evaluación debe ser adecuada para captar la rugosidad superficial. En este caso, mediante el mismo microscopio Alicona también se obtienen las mediciones reales de la rugosidad superficial del área adecuada. La metodología utilizada es la aplicación un filtro de paso alto para eliminar la forma de la pieza y, posteriormente, un valor de longitud de corte (Lc) de 800 µm, adecuado para procesos de mecanizado y torneado con valores de rugosidad que oscilan entre 1-2 µm. La norma establece que el área mínima requerida para aplicar este valor de longitud de corte es de 4 mm y máximo de 12 mm, por lo que se midieron áreas cuadradas de 10 x 10 mm para obtener la rugosidad tal y como se observa en la figura 7.
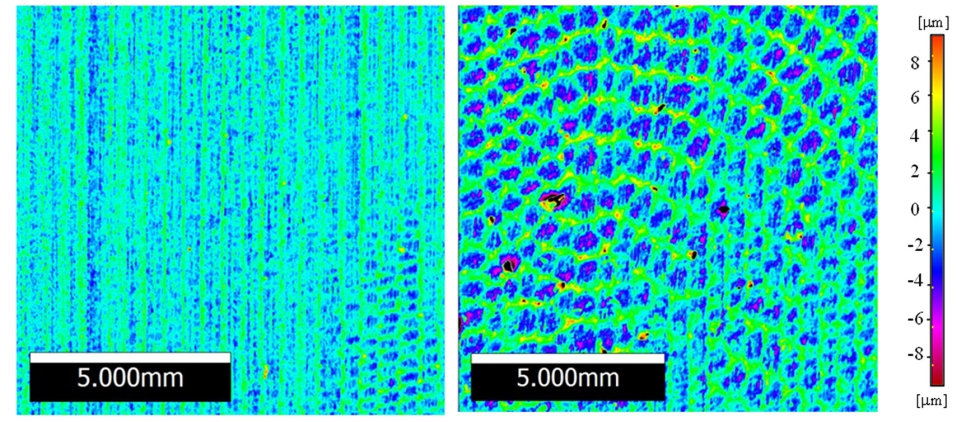
Como se puede observar en la figura 7, en el área con vibraciones el valor de la rugosidad es mayor a 2 µm, haciendo que estas piezas no sean admisibles. Las mediciones de rugosidad obtenidas son siempre mayores en dirección perpendicular al avance de la herramienta. Por lo tanto, los ángulos de 30° y 45° quedan fuera de rango debido a la inaceptable calidad superficial obtenida ya que durante el mecanizado de estas se produce vibraciones y en la superficie generada se observa cada uno de los cortes de los dientes de la fresa generando valles y picos de gran magnitud y un mal acabado superficial.
Conclusiones
Se han evaluado las implicaciones de la inclinación de la herramienta de corte en el fresado de álabes aerodinámicos, enfocándose en los ángulos de 30°, 45°, 60° y 75° con respecto a la vertical de la herramienta. Las pruebas se llevaron a cabo utilizando la aleación de titanio Ti6Al4V, un material común en la fabricación de álabes debido a su alta resistencia y capacidad para soportar temperaturas extremas.
Los resultados indican que los ángulos de inclinación de 60° y 75° ofrecen un rendimiento superior en términos de estabilidad y acabado superficial. Las piezas mecanizadas con estos ángulos no experimentaron vibraciones significativas, lo que se traduce en un corte más estable y un mejor acabado superficial. Este comportamiento es deseable ya que minimiza el desgaste de la herramienta y mejora la precisión dimensional del componente.
Por otro lado, los ángulos de 30° y 45° mostraron una mayor propensión a las vibraciones, especialmente en las áreas con mayor voladizo. Estas vibraciones afectan negativamente la calidad del acabado superficial y pueden acelerar el desgaste de la herramienta. Las mediciones de rugosidad obtenidas en estos ángulos revelan que las superficies presentan marcas en forma de onda, generadas por un corte inestable, lo que hace que estas piezas no sean adecuadas para aplicaciones que requieren alta precisión.
Por todo ello se puede concluir que la inclinación de la herramienta de corte es un factor crítico en el fresado de álabes aerodinámicos. La optimización de este parámetro es esencial para mejorar la eficiencia del proceso y garantizar que los álabes cumplan con los estrictos estándares de precisión y durabilidad requeridos en la industria aeroespacial.
Referencias
[1] ‘IATA forecast predicts 8.2 billion air travellers in 2037 | Times Aerospace’. Accessed: May 21, 2024. [Online]. Available: https://www.timesaerospace.aero/news/air-transport/iata-forecast-predicts-82-billion-air-travellers-in-2037
[2] ‘EUROCONTROL Aviation Outlook 2050 Main Report’, 2022.
[3] B. Yan, Y. Hao, L. Zhu, and C. Liu, ‘Towards high milling accuracy of turbine blades: A review’, Mechanical Systems and Signal Processing, vol. 170. Academic Press, May 01, 2022. doi: 10.1016/j.ymssp.2021.108727.
[4] I. Del Sol, A. Rivero, L. N. L. de Lacalle, and A. J. Gamez, ‘Thin-wall machining of light alloys: A review of models and industrial approaches’, Materials, vol. 12, no. 12, Jun. 2019, doi: 10.3390/ma12122012.