Una innovadora fresa madre con plaquitas de metal duro de perfil completo gana puntos en eficiencia
27 de junio de 2011
Las mayores velocidades en todas las áreas, con vidas de la herramienta más prolongadas y menores niveles de ruido, son la causa de que cada vez existan más exigencias en la precisión de ruedas de engranajes. La competición internacional y las presiones resultantes sobre los costes añaden más razones a la necesidad de mantener una búsqueda constante de nuevas posibilidades de ahorro y una producción más optimizada. Por supuesto, esto es el trasfondo de por qué se desarrollan nuevos procesos, e incluso de que métodos antiguos y probados se evalúen para actualizarlos con las últimas novedades técnicas.
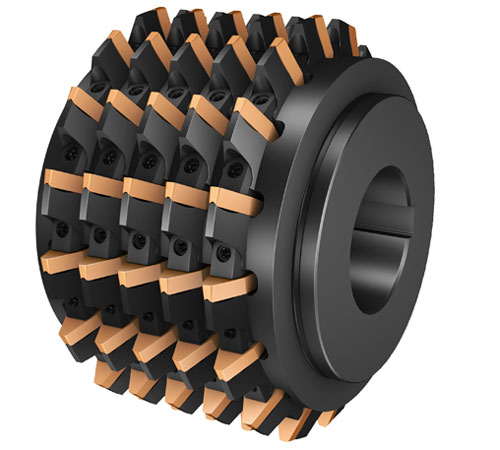
Uno de los procesos más rentables y precisos en cuanto a la fabricación de dientes de engranajes es la talla con fresas madre. En este proceso, como en el caso de los engranajes de tornillo sin fin, la pieza de trabajo y la herramienta están engranadas continuamente en la máquina fresa madre para engranajes. Al hacerlo, la fresa madre corta los dientes y los espacios para los dientes en la pieza de trabajo con la forma necesaria para el emparejamiento de las ruedas de engranaje en la caja de cambios acabada. Los errores mas frecuentes que se daban en el proceso clásico (desviaciones de perfil y errores de paso) no pueden ocurrir aquí porque la creación de dientes en el proceso de la fresa madre se produce al generar cortes envolventes durante la continua generación de dos cuerpos entre sí.
Una ventaja adicional del proceso de talla con fresa madre es que, además de ruedas de engranajes, se pueden crear piezas de trabajo con otros perfiles, por ejemplo ejes acanalados o ruedas de trinquete, siempre que tengan espacios de la misma forma y paso.
La herramienta
La fresa madre para engranajes tiene la forma de una herramienta cilíndrica individual o múltiple con filos de corte distribuidos alrededor de la circunferencia en combinación con desahogos de virutas. Los materiales de corte utilizados hasta la fecha han sido principalmente aceros de alta aleación de alta velocidad (high speed steels, HSS). Además de fresas de metal duro integral de HSS de fabricación metalúrgica, también se utilizan en el mecanizado herramientas con barras o raíles de metal duro. De hecho, las herramientas de HSS clásicas aún tienen una cuota de mercado de más del 50%. La razón de ello se basa en el hecho de que ni las fresas de metal duro integral ni las herramientas preparadas con filos de corte de metal duro son capaces de cumplir con todos los requisitos. Esto incluye sobre todo una gran pérdida de vida útil después de un rectificado, o fracturas de filos individuales que hacen necesaria la sustitución de la fresa completa. Para poder rectificar las herramientas es a menudo necesario eliminar el recubrimiento y esto priva al filo de corte de metal duro del recubrimiento de cobalto. Esto lleva a una reducción en la vida útil de la herramienta debido a la fragilidad del filo de corte, lo que resulta en una vida de la herramienta menos predecible.
Cuando se trabaja con módulos mayores, durante los últimos años han sido cada vez más populares las herramientas con plaquitas intercambiables de metal duro de montaje tangencial. Esta solución proporciona claras ventajas: El carburo cementado (metal duro) también puede utilizarse como material para la herramienta de corte de fresas madre para engranajes con grandes diámetros; además, los cuerpos de las fresas tienen una vida de la herramienta larga y pueden prepararse con diferentes calidades que han sido adaptadas al material de la pieza de trabajo y la geometría del diente respectivos. Por tanto, un mismo cuerpo de fresa se puede utilizar para diferentes tareas, lo que reduce el número de herramientas necesarias y con ello los requisitos de inventario. Este concepto también hace posible conseguir no sólo la precisión requerida de perfil, sino también reducir de forma significativa los tiempos de fabricación, y reducir de manera considerable los costes de reacondicionamiento implicados en el rectificado y recubrimiento de las herramientas.
Nuevas estrategias y colaboradores para el mecanizado más eficiente de engranajes
Sandvik Coromant es una empresa relativamente nueva en el campo de herramientas de corte para los engranajes que hay la actualidad. Como líder mundial con una oferta completa de herramientas, el objetivo natural era desarrollar no sólo conceptos de herramienta que fueran convincentes para el corte de engranajes, sino también asociarse de forma estrecha con socios reconocidos en términos de fabricantes de máquinas y clientes. Dos productos en la actualidad han realizado una entrada con éxito en el mundo de la fabricación de herramientas de corte para engranajes: la fresa de disco CoroMill 170 en la gama de módulos entre 12 y 22 y fresas madre grandes para engranajes con plaquitas intercambiables de montaje tangencial. Ambas herramientas han mejorado considerablemente el rendimiento.
El proceso de engranajes uP para la producción completa de engranajes en bisel con engranajes en espiral en únicamente dos disposiciones de sujeción en centros de mecanizado de 5 ejes fue un paso adicional con éxito para convertirse en un proveedor de servicio completo para la producción de cajas de cambio. Sandvik Coromant ha desarrollado esta tecnología junto con Voith Turbo y Gebr. Heller Maschinenfabrik GmbH.
Como una consecuencia lógica de los éxitos anteriores, Sandvik Coromant está en la actualidad trabajando en el próximo paso: la fabricación de fresas madre para engranajes con plaquitas intercambiables de perfil completo.
Al contrario que las plaquitas intercambiables de montaje tangencial, donde generalmente no más de dos filos de corte hacen contacto, una fresa para engranajes con plaquitas intercambiables de perfil completo también crea virutas de tres flancos. Esto significa que el filo de corte circunferencial debe ser accesible en tres lados para la evacuación de material. El resultado son exigencias específicas en la interconexión entre la plaquita intercambiable y el cuerpo de la fresa o, si se utiliza, la cuña o el cartucho y la plaquita intercambiable: Además, la posición y la sujeción de la plaquita intercambiable deben tener lugar con la mayor precisión posible para poder ser capaces de cumplir con las estrechas tolerancias de la norma DIN 3968.
Se ha desarrollado un nuevo tipo de asiento de plaquita para garantizar también un posicionamiento y una sujeción de la plaquita intercambiable precisos en la rutina de desbaste. Debido a estas plaquitas, en función del tamaño del módulo y del uso que se le vaya a dar, puede tener uno o dos filos; no se trata en general de una cuestión acerca de plaquitas de filos de corte múltiples: Aunque los filos de corte están situados en tres lados de la circunferencia, si se observa con detalle se verá que son plaquitas intercambiables de filo sencillo o doble que naturalmente también se pueden llamar “plaquitas intercambiables”.
Para la producción de fresas madre para engranajes con plaquitas intercambiables, Sandvik Coromant se basa en la experiencia y conocimientos y también en socios reconocidos: Junto con Höfler Maschinenbau GmbH, un conocido fabricante de máquinas especializadas para la talla con fresa madre y el rectificado de engranajes, también se habló con Carl Zeiss GmbH para que se uniera al equipo como experto en metrología industrial para la medida precisa de herramientas y engranajes acabados.
La cooperación también incluyó el trabajo con algunos conocidos fabricantes de cajas de cambios y con universidades de renombre, por ejemplo el Lunds Institute of Technology (Suecia) y el grupo de trabajo de engranajes WZL (laboratorio para máquinas-herramienta, RWTH Aachen).
Resultados iniciales
Las pruebas de campo iniciales con las nuevas fresas madre han sido completadas y analizadas. Se demostró que una fresa madre para engranajes preparada con plaquitas intercambiables de metal duro no cumple de forma natural los requisitos de precisión que una fresa madre hecha de una pieza de HSS o metal duro integral es capaz de conseguir. Sin embargo, se puede garantizar el cumplimiento con la calidad B de acuerdo con la norma DIN 3968, lo que significa que se pueden fabricar ruedas de engranaje de calidades de 9 a 11 de acuerdo con la norma DIN 3962. Si se necesita alcanzar una calidad de pieza de trabajo mayor, se requiere un proceso adicional con una fresa madre de una pieza o una operación de rectificado. La calidad de la talla con fresa madre no solo se determina por la calidad de la fresa madre para engranajes. Otros factores que influyen son una disposición de sujeción de la pieza de trabajo segura, precisión de la máquina fresa madre para engranajes y la concentricidad y desviación de la fresa madre junto con la pieza de trabajo. En general, los resultados de la prueba de campo han demostrado, bajo tres criterios importantes, unas verdaderas ventajas de las nuevas fresas madre: reducción de los tiempos de mecanizado y de los costes de talla con fresa madre por componente y aumento de la vida útil de la herramienta. Un estudio detallado de los resultados revela los verdaderos niveles de mejora.
Tiempos de mecanizado reducidos
El principal tiempo de proceso durante la talla de engranajes con fresas madre se determina, entre otras cosas, por la velocidad de corte y el avance axial de la pieza de trabajo. El emparejamiento del tipo de acero y el material de la herramienta de corte, así como la estabilidad y el rendimiento de las máquinas-herramienta utilizadas, son factores críticos a la hora de determinar la velocidad de corte más efectiva en cuanto al coste. Pruebas realizadas bajo condiciones reales de producción mostraron que la velocidad de corte, mientras se retenía la velocidad de avance de cada rotación de la fresa, se puede más que doblar en la mayoría de los casos. De este modo, en un caso concreto el tiempo de mecanizado de 200 minutos se redujo a 90 minutos por cada rueda del engranaje.
Los filos de corte de metal duro pueden soportar una carga de viruta mucho mayor que los filos de corte de HSS. Esto significa que se pueden conseguir unos valores de avance por cada diente significativamente mayores. Es más, una reducción en el número de filos de corte efectivos es más que compensada si se aplica este método.
Cuando se determina la velocidad de avance, la carga de viruta, el grosor teórico máximo de viruta que se crea al cortar las virutas de las cabezas de los dientes, debería registrarse siempre y utilizarse para calcular la velocidad de avance. Si todos los factores decisivos que influyen en el rendimiento de las máquinas-herramienta y el material de la pieza de trabajo lo permiten, con la nueva herramienta es posible mecanizar cargas de viruta de hasta 0,35 mm y velocidades de corte de hasta 350 m/min en función del módulo en cuestión.
Mayor vida de la herramienta / longitud de la herramienta
En estudios de rendimiento de fresas madre para engranajes, en lugar de la habitualvida de la herramienta especificada en minutos, la fresa madre se evalúa en términos de longitud de corte de la herramienta. Esta longitud corresponde a la suma de las longitudes de los dientes de todas las piezas de trabajo que se pueden mecanizar entre dos afilados, o entre cambios de las plaquitas intercambiables de la herramienta.
En condiciones óptimas, es decir, con el mejor recubrimiento y la mejor preparación del filo de corte de las placas de metal duro de la fresa madre, en pruebas de campo se consiguieron longitudes de herramienta por cambio de fresa hasta tres veces mayores que con herramientas de HSS recubiertas. La mayor velocidad de avance por diente también contribuyó a esto. Una velocidad de avance que es demasiado baja tiene el efecto de causar desgaste, con lo que se reduce la vida de la herramienta y se provoca una excesiva generación de calor en la pieza de trabajo. Para que las plaquitas intercambiables de metal duro se puedan utilizar sin vacilar también para el mecanizado sin refrigerante sin pérdida de vida de la herramienta, la velocidad de avance debe seleccionarse siempre de modo que la mayor parte del calor se evacue con la viruta.
Una vida de la herramienta mayor también significa un aumento del tiempo de producción, ya que cuando la vida de la herramienta, por ejemplo, se triplica, ya no se necesita el 66% del tiempo de configuración y ahora ese tiempo se puede utilizar para mecanizar.
Lo que pocas veces se tiene en cuenta son las pérdidas debidas a la configuración que de forma ocasional se da durante la producción en serie: el rectificado de fresas romas lleva a tener diferentes diámetros de fresas, lo que siempre requiere un reajuste de la configuración de la máquina. De nuevo aquí el riesgo se reduce en un 66% con la nueva herramienta. También se produce una reducción del tiempo que generalmente se requiere para reacondicionar las fresas madre de HSS romas, que deben enviarse fuera para su rectificado y recubrimiento. Esto se asocia con un largo periodo de tiempo, desde el cambio de herramienta hasta la entrega de la herramienta ya acabada y reacondicionada. Por supuesto, con las nuevas herramientas de Sandvik Coromant todavía se recomienda que el cambio se produzca para optimizar la vida de la herramienta y mejorar la eficiencia en cuanto al coste. Además, las plaquitas intercambiables que solo muestran desgaste en un filo tras el uso se pueden cambiar de izquierda a derecha.
Reducción del coste de talla con fresas madre por componente
El principal objetivo de desarrollos adicionales en las herramientas es la reducción de los costes de producción, directos e indirectos. Al mismo tiempo, la calidad de las piezas de trabajo que se van a mecanizar debe mantenerse o incluso aumentarse aún más. Además, es necesario garantizar la fiabilidad de la producción.
La nueva fresa madre de perfil pleno de Sandvik Coromant cumple totalmente los requisitos relacionados con la herramienta, incluso la primera vez que se usa: los costes proporcionales de la herramienta también se podrían reducir de forma considerable con un gasto mínimo en inversión, inventario, manipulación y costes de reacondicionamiento. Además de esto, se consiguió un compromiso de capital menor a través de un número de fresas madre en circulación significativamente menor. Una ventaja adicional: la producción diaria podría mejorarse de forma significativa a través de un aumento en la velocidad de corte, con lo que se reduce también el tiempo real de corte (se superó un ahorro del 50% varias veces). El tiempo ganado al utilizar la máquina reduciendo el tiempo de corte y el tiempo de configuración se puede utilizar para aumentar aún más la producción. En algunos casos ya no era necesario utilizar aceites y refrigerantes, lo que aumenta la vida útil de la herramienta y también reduce las emisiones en forma de aceite nebulizado o vapor. Los costes de utilizar lubricante o aceites no se deberían subestimar porque, dependiendo de cada caso de aplicación, a menudo llegan al 15% de los costes totales de producción.
En resumen
Con las nuevas fresas madre, el cliente dispone de las herramientas que se pueden utilizar para una producción económica y fiable, que reducen los costes de inversión, son más fáciles de manipular y que pueden hacer que la operación sea independiente de cualquier reacondicionamiento externo de la herramienta.