La descarbonización, la sostenibilidad, la eficiencia energética y de recursos centran el debate de la industria metalúrgica
La transformación de la industria metalúrgica hacia la neutralidad climática fue el tema principal del Bright World of Metals, cuarteto ferial celebrado en Düsseldorf en junio de este año. Un evento en el que las empresas expositoras y las conferencias de expertos se centraron en las tecnologías y soluciones para la descarbonización, la sostenibilidad, la eficiencia energética y de los recursos en el sentido de la economía circular en todas las etapas de la cadena de valor añadido, siguiendo un enfoque de la cuna a la cuna.
Las estrategias de descarbonización de esta heterogénea industria son tan diversas como las materias primas y los procesos de cada fundición.
Sostenibilidad, eficiencia energética y de recursos son las tendencias de la industria de la fundición
Otro tema que forma parte de la agenda de sostenibilidad de las fundiciones y los proveedores de tecnología de fundición es el uso eficiente de los recursos y la energía. Especialmente el hidrógeno verde desempeña un papel importante como sustituto neutro para el clima del gas natural en los hornos de recalentamiento, aunque en mucha menor medida que en la industria siderúrgica, por ejemplo. La energía de transformación número uno para las fundiciones es la electricidad verde, como subrayó Max Schumacher, director general de BDG, en la Gifa.
Ejemplo DiHAG
Bajo el paraguas del grupo de fundiciones trabajan ocho fundiciones en los ámbitos de la fundición de hierro y acero. La empresa explota cinco hornos de inducción para fundiciones de hierro y un horno de arco eléctrico en la fundición de acero SHB de Leipzig. El director general Viktor Babushchak se centra en el suministro de energía propio para todo el grupo. Ya en 2016, el holding estableció su propia red en cooperación con Giga Energy GmbH. En la actualidad, alrededor de la mitad de la electricidad procede de energías renovables. El objetivo de Babushchak es generar su propio suministro de electricidad verde con un 80% de energía eólica y un 20% de energía solar. El principal problema, dice Babushchak, es la cantidad de burocracia que conlleva la obtención de permisos para las turbinas eólicas. Esta es la razón por la que el grupo de fundición apenas avanza actualmente hacia los objetivos de expansión que se había marcado.
El camino de la transformación hacia la descarbonización también conduce a la electricidad ecológica para la fundición Siempelkamp Giesserei. La digitalización desempeña un papel clave en este sentido. El año pasado, la fundición de Krefeld puso en marcha el primer proceso de fusión totalmente digitalizado junto con ABP Induction, fabricante de hornos de inducción, y la start-up digital Zorc Technology.
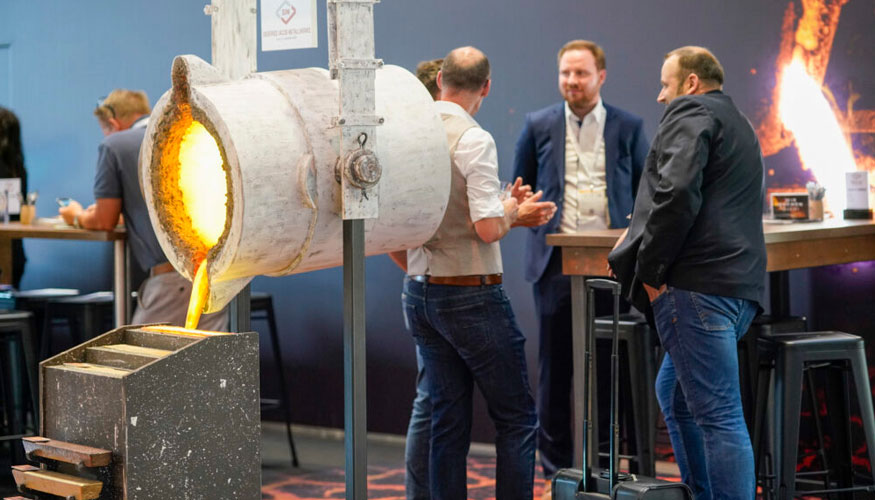
Los grandes fabricantes de hornos industriales, como ABP Induction y Otto Junker, elogian las instalaciones de fusión por inducción como sustituto de los hornos de cubilote y los hornos de gas.
Marco Rische, del fabricante de hornos de inducción ABP Induction Systems, y Wolfgang Baumgart, de Zorc Technology, hablaron en el Foro Gifa sobre cómo cambiar el procedimiento de fundición de hornos de cubilote que utilizan combustibles fósiles a hornos de frecuencia media casi neutros en carbono.
Rische, de ABP, no ve futuro para el horno de cubilote. El experto en hornos tampoco ve la tecnología del hidrógeno como una solución para las fundiciones. “El hidrógeno no tiene futuro en la tecnología de hornos”, afirma Rische. El hidrógeno como tecnología de fusión y calentamiento no tiene sentido ni desde el punto de vista económico ni desde el ecológico. No tiene mucho sentido utilizar electricidad renovable para producir hidrógeno verde, lo que ocasiona pérdidas de conversión, y luego quemar dicho hidrógeno, lo que ocasiona más pérdidas, afirma Rische. Es mucho más eficiente utilizar la electricidad verde directamente para la inducción para fundir y calentar.
Según ABP, el cuarteto de ferias Gifa, Metec, Thermprocess y Newcast fue todo un éxito. “Los temas generales de la descarbonización y la digitalización son el núcleo de la feria de este año”, dice Till Schreiter, CEO de ABP. “Como parte de nuestra promesa ‘Su socio en el camino hacia la emisión cero’, estos temas, aparte de la desglobalización y el cambio demográfico, eran exactamente las cuestiones centrales para las que los visitantes de la feria buscaban soluciones”, afirma Schreiter. Tras los años de pandemia y el consiguiente cambio hacia el trabajo digital, se hizo patente el deseo de reuniones personales. “La proporción de visitantes cualificados y con autoridad para tomar decisiones fue aún mayor que en años anteriores, por lo que no es de extrañar que esta vez incluso se firmaran acuerdos imprevistos en la feria”, informa Schreiter con orgullo. Y añade: “Después de la feria es antes de la feria y ya estamos deseando dar la bienvenida de nuevo a nuestros amigos y socios comerciales en el Bright World of Metals 2027 en Düsseldorf”.
Especialmente para los fabricantes de hornos, la sostenibilidad y el uso eficiente de la energía son cuestiones importantes; la gestión de los procesos industriales para minimizar su impacto medioambiental es el estado del arte. Al igual que ABP, el especialista en hornos Junker presentó soluciones novedosas para plantas de fusión por inducción y de termoprocesamiento. Gracias a la tecnología digital de las instalaciones y a un funcionamiento correcto, es posible reducir la cantidad de energía que consume un horno. Esto incluye también la recuperación de calor y el uso de electricidad procedente de sistemas fotovoltaicos adicionales. Por ejemplo, Otto Junker presentó a los visitantes de ecoMetals Trails los nuevos sistemas “power-to-heat”, que amortiguan el excedente de electricidad en forma de calor que posteriormente está disponible como calor de proceso. El calor se almacena a temperaturas de hasta 1.100 °C.
En el stand de Otto Junker, los visitantes pudieron experimentar cómo puede utilizarse la moderna tecnología de sistemas para controlar un horno en funcionamiento en realidad virtual (RV). Con unas gafas de RV se pudo entrar y manejar una nave de fundición totalmente funcional que incluía un horno de inducción. Este desarrollo no está pensado para el entretenimiento, sino que aborda un problema muy serio: la falta de trabajadores cualificados. Las fundiciones deben formar cada vez más a trabajadores no cualificados para que ocupen el lugar de los trabajadores cualificados, como informa Georg Born, jefe del Servicio de Ventas de Otto Junker. Antes de que esto ocurra en el horno real, la formación en RV permite practicar los pasos más importantes de forma segura.
Inductotherm es un especialista mundial en fusión y calentamiento por inducción. Con el sistema Solar Unipac 5.0, la empresa presentó en el cuarteto de ferias de este año una tecnología de fusión para fundiciones impulsada por energía verde. Se supone que la integración de energía solar, hidroeléctrica, eólica y otras tecnologías de energías renovables garantizará que la nueva tecnología de fundición ecológica ocupe un lugar destacado en la reducción de emisiones de carbono. El sistema combina células de energía solar, turbinas eólicas, sistemas de almacenamiento en baterías, una fuente integrada de electricidad de inducción y un moderno horno de inducción. Combinado con fuentes de energía renovables, este paquete, presentado en el marco de la iniciativa ecoMetals, ofrece una solución de fusión completa que no depende de la red eléctrica y permite a las empresas aplicar la sostenibilidad sin comprometer la eficiencia.
¿La electrificación como solución ideal?
No todas las fundiciones consideran la electrificación como la solución ideal. Al fin y al cabo, el gas sigue desempeñando un papel en la industria, por ejemplo, en los hornos de tratamiento térmico. Promeos, especialista en tecnología de quemadores de gas sin llama a lo largo de toda la cadena de procesos y, según su propia cuenta, líder en tecnología de sistemas de quemadores de gas premezclados, presentó en la Gifa su gama de sistemas de calefacción desarrollados individualmente con tecnología de quemadores de gas sin llama. Una contribución rentable y energéticamente eficiente al aumento de la productividad, protegiendo al mismo tiempo el medio ambiente, afirma el proveedor. “Preparado para hidrógeno” a petición, opcionalmente también disponible como solución eléctrica.
La fundición de hierro Eisengießerei Fritz Winter demostró que una fundición, incluso para el procedimiento de fusión, no necesita confiar en la electrificación como única solución para la descarbonización. Otro producto destacado en el stand de la Gifa fue un nuevo disco de freno de bajas emisiones conforme a las normas Euro-7, que fue galardonado con el premio NEWCAST en la categoría de construcción ligera. Otras innovaciones fueron las soluciones ligeras para automoción fabricadas mediante fundición de hierro de paredes finas, de peso neutro en comparación con el aluminio, entre ellas una novedosa carcasa de motor para vehículos eléctricos desarrollada en colaboración con un fabricante de vehículos (OEM).
Los fundidores de hierro de Stadtallendorf, en Hesse, siguen con su horno de cubilote alimentado con coque. “No debemos renunciar en ningún caso a la ventaja del horno de cubilote”, afirma Markus Semmler, jefe de Materiales de Explotación y Protección del Medio Ambiente. Sólo un horno de cubilote alimentado con coque puede convertir el 100% de la chatarra en 100% de arrabio de alta calidad. Un horno de inducción no puede convertir el 100% de la chatarra, como sí puede hacerlo el horno de cubilote, afirma Semmler. La cuestión de la descarbonización no es sólo una cuestión económica, sino sobre todo una cuestión de disponibilidad de materias primas. En el curso de la descarbonización de la industria siderúrgica, con la reducción directa mediante hidrógeno y con la vía eléctrica, dejará de existir el mercado de materias primas para las fundiciones de hierro con procesos de fusión electrificados, así lo teme el experto. Semmler: “Los productores de acero utilizan las mismas materias primas que necesitaríamos para la electrificación. Aunque estuviéramos dispuestos a pagar por ellas, tenemos que preocuparnos de que ni siquiera consigamos las materias primas. Estamos viendo el balance completo. Y ahí es donde vemos grandes problemas en el suministro de materias primas, si optáramos por la electrificación al 100%”.
La chimenea del horno de cubilote de Fritz Winter ya no es un mal necesario, sino el primer paso hacia una economía circular según el principio CCU. La fundición de Stadtallendorf quiere separar el CO2, transformarlo y utilizarlo como materia prima sin afectar al medio ambiente. Hasta 2030, Fritz Winter quiere instalar un sistema de tratamiento de aire y recuperación de calor en la chimenea de humos, antes de iniciar la aplicación técnica a gran escala de la separación del dióxido de carbono. El CO2 separado se introducirá en el aprovechamiento del carbono a través de cooperaciones locales.
Máquinas de fundición: aumento de la eficiencia energética y la productividad
Como proveedor de tecnología de fundición a presión, la agenda de Oskar Frech incluye nuevos desarrollos para el ahorro de energía, la recuperación de calor y la economía circular. Las máquinas de fundición a presión de cámara caliente y fría presentadas en la Gifa se optimizaron aún más. Por ejemplo, se mejoró el sistema hidráulico no solo para garantizar la máxima dinámica y rendimiento, sino también para posibilitar un mayor ahorro de energía. En una nueva presentación se presentó una planta de reciclado de llantas de aluminio, que funciona de forma especialmente eficiente gracias a la recuperación de calor.
Oskar Frech también participa en el fabricante austriaco de hornos industriales Meltec. La empresa es un proveedor líder de innovadoras unidades de dosificación de aluminio al vacío (AVD). Las AVD pueden instalarse en cualquier horno de fusión o de mantenimiento. Permiten la extracción segura y la dosificación precisa de la masa fundida de aluminio en la cámara de llenado de la máquina de fundición a presión de cámara fría. Uno de los puntos fuertes de los sistemas es la toma de masa fundida sin óxido por debajo del nivel del baño, la transferencia de la masa fundida sin admisión de aire a un recipiente cerrado de cerámica con sólo una baja caída de temperatura y una alta precisión de dosificación conseguida mediante la medición integrada y precisa de la cantidad de masa fundida desgasificada. Como novedad, Meltec presentó al público el ACD controlado por robot para 150 kg de aluminio líquido.
Thomas Franco, director general y CTO de Oskar Frech, está convencido de que este desarrollo supondrá una mejora significativa de la productividad y la calidad no sólo para las máquinas de fundición a presión y giga fundición utilizadas por Tesla.
El grupo internacional Norican estuvo muy presente en la Gifa con sus filiales Italpresse Gauss, StrikoWestofen, Simpson, Wheelabrator y DISA. Los temas centrales fueron el uso eficiente de la energía y los recursos en todas las áreas de una fundición, así como un uso rentable de los materiales de fundición que también disminuya el impacto sobre el medio ambiente.
Italpresse Gauss, por ejemplo, se centró en la eficiencia energética de las máquinas de fundición a presión. El fabricante italiano de maquinaria presentó Eco-Fit Mode, un sistema de control para bombas hidráulicas que reduce el consumo de energía hasta un 50% e incluso hasta un 60% con Eco-Fit Mode Plus.
La atención se centró en un pedido de BMW que se ha completado con éxito. El fabricante de vehículos de Múnich está utilizando la TF5700+ de Italpresse Gauss, una máquina de fundición a presión de gran tamaño. Gracias a ella, la empresa automovilística ha podido fundir en una sola pieza de aluminio de sólo 6 kg de peso una carcasa de batería de nueva construcción apta para colisiones, que originalmente constaba de 16 piezas diferentes. Esto convierte a BMW en la primera empresa europea de fundición a presión en fabricar grandes componentes estructurales de una sola pieza con una máquina de fundición a presión que cuenta con más de 5.000 toneladas de fuerza de cierre.
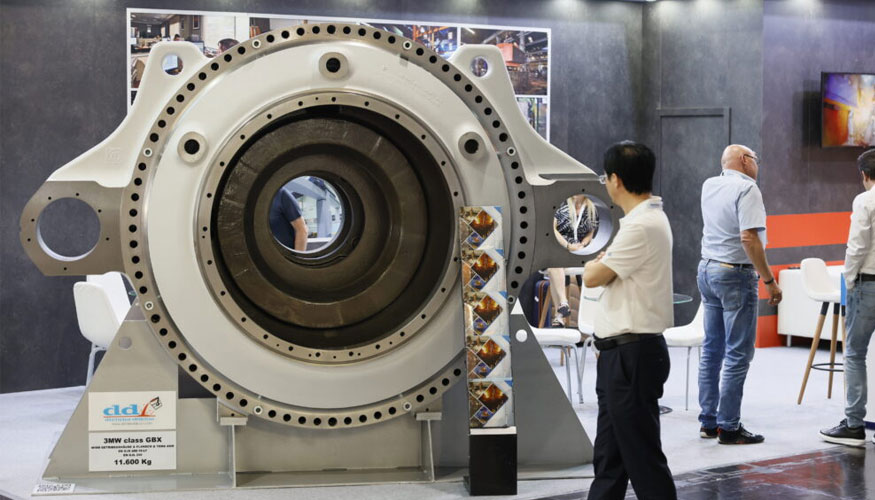
Las impresoras 3D de arena, camino del éxito
En la anterior Gifa, los procedimientos de fabricación aditiva seguían siendo un tema de nicho. Este año, hubo una tendencia notable hacia la impresión 3D indirecta utilizando arena. Las impresoras 3D de proveedores líderes como ExOne y Voxeljet son cada vez más capaces, y los núcleos impresos en arena están creciendo en complejidad. La fabricación aditiva indirecta en arena ofrece a las fundiciones posibilidades de diseño totalmente nuevas. A menudo, las geometrías complejas sólo pueden realizarse mediante la impresión 3D en arena. Se fabrican como machos y moldes y, a continuación, se moldean como modelos de machos acabados.
En la edición de este año, Voxeljet y su socio Loramendi presentaron un hito en la producción aditiva en serie. Para la fábrica de BMW en Landshut, el fabricante de impresoras y Loramendi desarrollaron e implementaron conjuntamente una tecnología y un sistema para la producción automática e inorgánica a gran escala de machos de arena para la fundición de metales ligeros. La línea de producción con impresoras 3D VX1300-X integradas y soluciones de desempaquetado y microondas totalmente automatizadas de Loramendi para el endurecimiento de los machos ofrece una solución a medida, eficiente e innovadora para los motores de alto rendimiento de BMW. Como fabricante líder de máquinas para la producción de machos y moldes, Loramendi junto con el fabricante de herramientas Aurrenak ha formado una alianza de tecnología de fundición y fabricación de herramientas dentro de la corporación mexicana Mondragón.
Laempe, fabricante de disparadoras de machos, también ha descubierto los puntos fuertes de la fabricación aditiva. En la Gifa, la empresa presentó por primera vez una línea de impresión en arena 3D totalmente automatizada para la fabricación de motores para BMW. El fabricante de automóviles y motores aprovecha la libertad de diseño que ofrece el proceso aditivo indirecto para la fundición de metales ligeros.
Sin embargo, a Laempe no le preocupa la canibalización del negocio principal, como afirma Thomas Baumann, empleado de ventas. Con velocidades de disparo de aproximadamente 25 segundos, las disparadoras de machos siguen siendo componentes indispensables de toda producción en serie.
No hay fundición sin química de fundición
Los grandes proveedores de productos químicos para fundición ASK Chemicals, Foseco y Hüttenes Albertus (HA) también se centraron en nuevos productos y tecnologías de aplicación para mejorar la calidad de la fundición, reducir el impacto sobre el medio ambiente y aumentar la productividad.
ASK Chemicals se centró en soluciones para aumentar la eficiencia, reducir los costes de proceso y minimizar el impacto sobre el medio ambiente mediante la utilización de materias primas menos nocivas. Esto incluye el desarrollo de productos que, por ejemplo, permitan prescindir de materias primas caras como las arenas especiales, o reducir el uso de otros materiales de consumo. Además, el proceso de fundición puede beneficiarse del uso de productos químicos y materias primas de alto rendimiento, ya que, por ejemplo, se reducen los trabajos de acabado y algunas fases de trabajo pueden omitirse por completo. De este modo, la última generación de aglutinantes para cajas frías, Ecocure Blue Pro, mejora las propiedades de la pieza fundida al tiempo que reduce el consumo de aglutinantes y aminas.
Dentro del aspecto de la sostenibilidad, la empresa química de fundición Foseco presentó una amplia gama de productos para todos los procesos habituales de fundición. Esto incluye material de alimentación para sistemas automatizados de moldeo con arena verde de ciclo rápido. Con un nuevo aglutinante orgánico fabricado a partir de materias primas sostenibles, se liberan menos componentes orgánicos volátiles (COV) y menos CO2 durante la fundición. La ecología y la sostenibilidad también han servido de guía para el desarrollo de nuevos revestimientos de fundición a base de agua. Los nuevos recubrimientos prescinden de los biocidas que liberan formaldehído y ayudan a las fundiciones a cumplir las nuevas directrices de la UE. Otro foco de atención de la química de fundición es el desarrollo de materiales inorgánicos, por ejemplo, en Hüttenes Albertus (HA). En muchas fundiciones de aluminio, sobre todo en el sector de la automoción, se ha establecido con éxito el uso de machos fabricados inorgánicamente. Esto es válido tanto para piezas de fundición para motores de combustión como para vehículos híbridos y puramente eléctricos. En el ámbito de la fundición de hierro, HA ya se ha hecho un nombre en el pasado y, junto con el fabricante de frenos Brembo, ha conseguido que los materiales inorgánicos estén listos para la producción en serie. En la Gifa, presentó también materiales aglutinantes y revestimientos de fundición para grandes piezas de hierro colado. La química inorgánica, como se pudo comprobar en la feria, está ganando terreno definitivamente, también en el sector de la fundición.
La tendencia hacia la impresión en arena 3D de machos, moldes y modelos también supone un reto para la química de la fundición. La impresión 3D es importante para los proveedores en varios aspectos. En la Gifa, Foseco presentó una nueva tecnología patentada para la filtración de piezas de fundición de hierro y acero. Los filtros (Stelex Optiflow3D) se realizan mediante fabricación aditiva, lo que ofrece una gran libertad en cuanto a la geometría y el diseño poroso de la estructura. Por primera vez, es posible diseñar filtros individuales para piezas de fundición concretas, optimizados en términos de eficacia de filtración, capacidad de metal y volumen de paso.
Con el aumento de las capacidades de las impresoras 3D, los núcleos que se fabrican mediante procesos de fundición en arena también están ganando en tamaño y complejidad. Sin los avances en la química de la fundición, esto sería imposible. Este tipo de geometrías complejas a menudo sólo pueden realizarse mediante impresión en arena en 3D. Se fabrican como núcleo y molde y después se funden como un paquete de núcleo acabado. Sin embargo, los mayores pesos de fundición resultantes también aumentan las exigencias de precisión y el mínimo trabajo de acabado de las piezas de fundición producidas de este modo.
Especialmente para los procesos de impresión en 3D, Foseco ha desarrollado un nuevo tipo de revestimiento. Mediante la combinación de materiales de relleno altamente ignífugos que no contienen circonio, fue posible aumentar significativamente la estabilidad térmica del revestimiento. Esto permite a los clientes trabajar con las capas de revestimiento más finas posibles y, al mismo tiempo, evitar la metalización y la formación de vetas. Ya no es necesario el tratamiento previo ni el uso de costosos revestimientos especializados, afirma Foseco. El revestimiento también tiene un efecto positivo en la rugosidad superficial de las superficies individuales de las piezas de fundición fabricadas con machos y moldes impresos en 3D.
El competidor Hüttenes Albertus también se centra en la impresión en arena. Entre los sistemas de aglomerante que la empresa ha desarrollado para la impresión 3D se encuentra, por ejemplo, una arena de moldeo especialmente desarrollada para la fabricación aditiva.
Newcast en el punto de mira de los compradores
Newcast es el escaparate internacional número uno de la industria de la fundición. Esto no solo lo saben las empresas expositoras, sino también los visitantes, por lo que este año se ha vuelto a aumentar la superficie de exposición con respecto a 2019. La importancia de la feria para la industria de la fundición se refleja claramente en la estructura de visitantes. Un total del 71% de los visitantes eran compradores. El 31% procedía de los departamentos de compras de importantes industrias usuarias como la automovilística y la aeroespacial.
El cuarteto de ferias regresará a Düsseldorf del 21 a 25 de junio de 2027