Este estudio plantea sustituir el Inconel 718 por Inox 321 en partes de piezas sin alta exigencia térmica y mecánica para abaratar coste y reducir peso
Análisis de viabilidad de soldadura láser disimilar entre Inconel 718 y acero inoxidable AISI 321
Para obtener una soldadura láser sin defectos, es necesario conocer la conductividad térmica de cada material, ya que el más conductor trasmitirá más calor a la pieza y el cordón crecerá más hacia ese material pudiendo dar lugar a defectos de soldadura como por ejemplo grietas intergranulares en la zona de fusión. La existencia de defectos de soldadura deteriora el rendimiento mecánico de las uniones soldadas. Se debe realizar un análisis metalúrgico exhaustivo para garantizar que la unión soldada no tenga defectos [1, 3].
En este estudio se ha analizado y validado la soldabilidad mediante la tecnología láser de los materiales Inconel 718 y acero inoxidable AISI 321. El Inconel 718 es una aleación base níquel resistente al calor que se utiliza en aplicaciones estructurales de prestaciones avanzadas. El acero inoxidable 321 es un material con gran resistencia a la corrosión intercristalina. La unión mediante soldadura láser de ambos materiales permitiría sustituir el Inconel 718 por el AISI 321 en ciertas zonas para reducir costes [1, 3, 4].
Uno de los puntos más problemáticos del proceso de soldadura láser es la obtención de unos parámetros que proporcionen una soldadura de calidad y repetitiva. El desarrollo de este proceso en materiales termorresistentes como los empleados en la turbina aeronáutica supondría un gran aporte científico-técnico debido a la poca divulgación experimental aportada en este campo, y también sería de ayuda en la reducción máxima de defectología asociada a la soldadura láser de materiales disimilares [5].
Con el desarrollo de este proceso, se espera reducir la cantidad de materiales utilizados y la cantidad de piezas defectuosas, reduciendo el impacto medioambiental y energético que supone su reciclado. Por otra parte, la posibilidad de fabricar piezas cada vez más eficientes, permitirá reducir la energía de su fabricación, con el consiguiente beneficio medioambiental.
Materiales y equipamiento empleado
Las uniones de soldadura se han realizado en las instalaciones del Centro de Fabricación Avanzada Aeronáutica (CFAA). El centro cuenta con una célula robotizada de soldadura láser, Trumpf Trulaser Cell 3000, que permite realizar cordones de soldadura de gran calidad con el mínimo daño térmico en pieza.
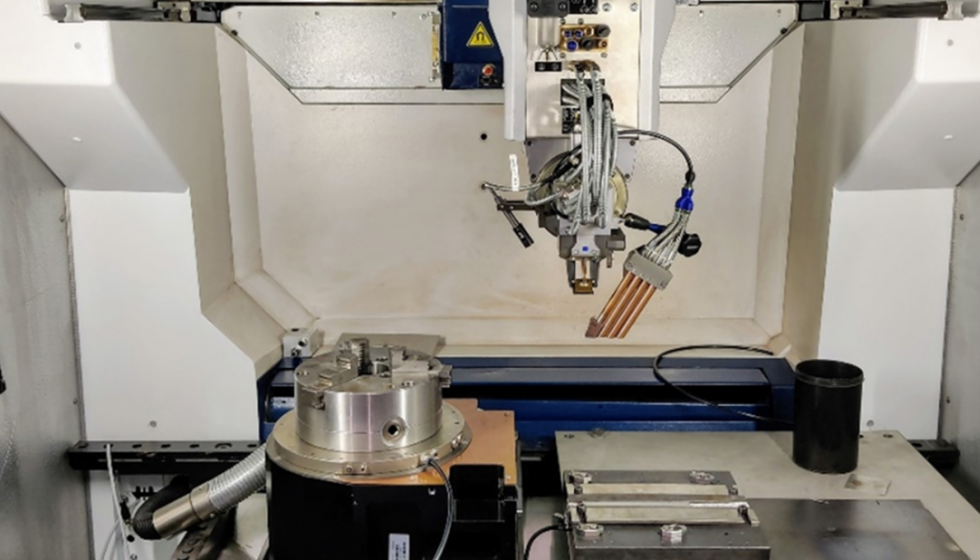
Como ya se ha comentado previamente, para el estudio se han empleado chapas de Inconel 718 y AISI 321 de 105x15 mm y espesor 1,3 mm. Las propiedades de cada material se pueden ver en las Tabla 1 y Tabla 2 respectivamente.
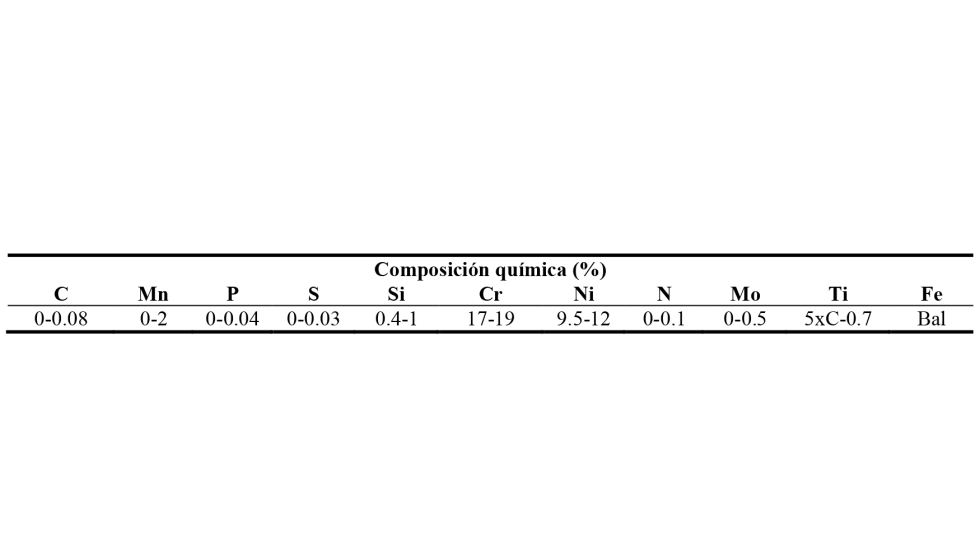
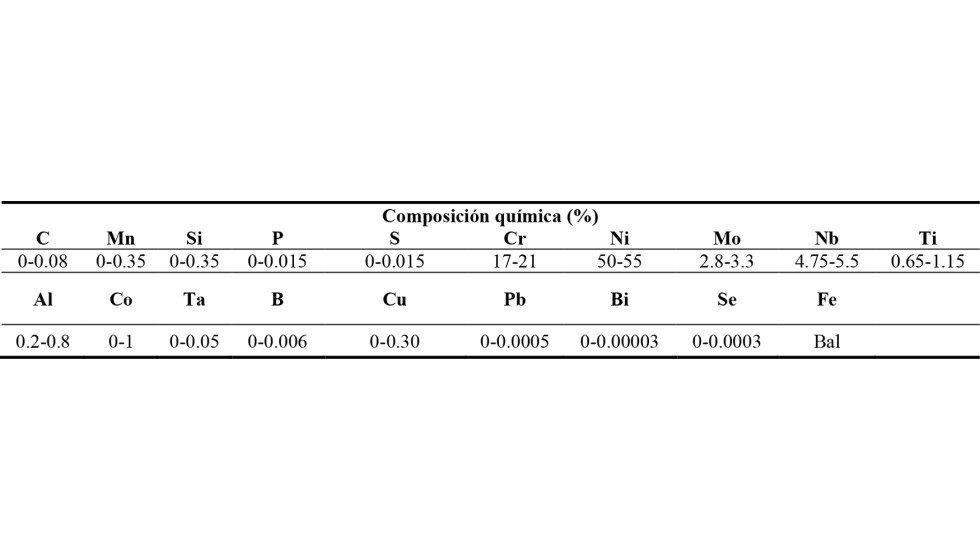
Las configuraciones de soldadura que se han empleado han sido soldadura a tope, y soldadura en solape colocando por una parte la chapa de Inconel 718 en la parte de arriba, y por otra parte la chapa de AISI 321 en la parte de arriba.
Los parámetros más influyentes en la soldadura láser son la potencia empleada, la velocidad de avance y la distancia focal. Para obtener los parámetros más adecuados para realizar las probetas se ha realizado una batería de ensayos sobre chapas planas de ambos materiales. Una vez obtenidos los parámetros óptimos, se han limpiado las chapas a soldar con acetona con el fin de eliminar posibles impurezas y restos de grasa que puedan generar defectos de soldadura. La Tabla 3 muestra los parámetros empleados en cada configuración soldada.
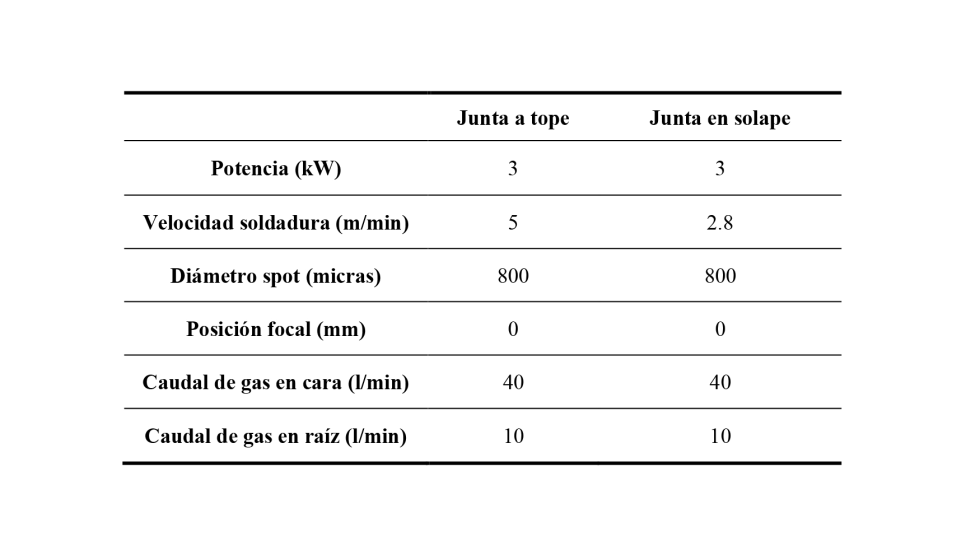
Una vez soldadas las muestras a tope y en solape, se han radiografiado para ver la calidad interna de la unión soldada, y después se han cortado y pulido para el análisis metalográfico. Una vez detectados los defectos internos, se han realizado ensayos de microdureza. Una de las probetas soldadas a tope se ha utilizado para cortar probetas de tracción para analizar la resistencia a tracción de la unión.
Resultados y discusión
Una vez realizados los tres ensayos, se ha procedido al análisis de las muestras. En primer lugar, se ha realizado una inspección visual para comprobar el aspecto de los cordones, y después se han realizado las radiografías. Las radiografías sirven para ver la integridad de la unión soldada y para ver de forma no destructiva si existen defectos internos, tales como poros, en el interior de la pieza soldada. En este caso, como se puede ver en la figura 2, figura 3 y figura 4, en ninguna de las tres radiografías se aprecian poros.
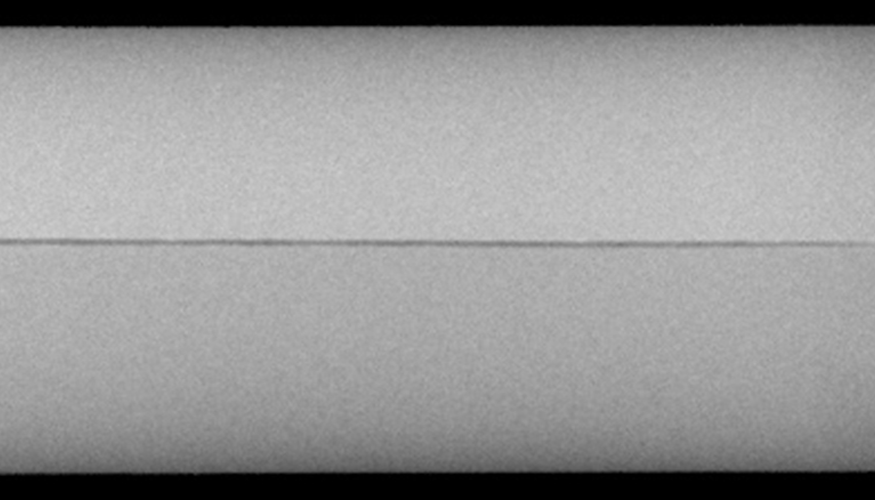
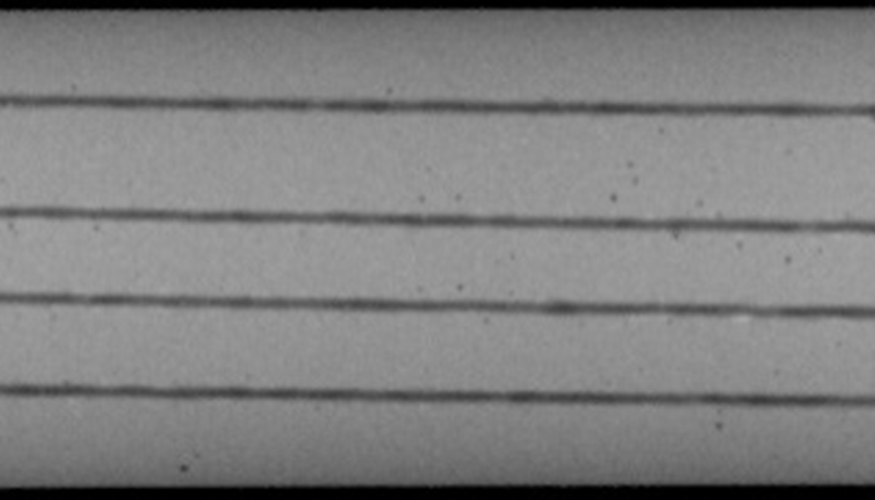
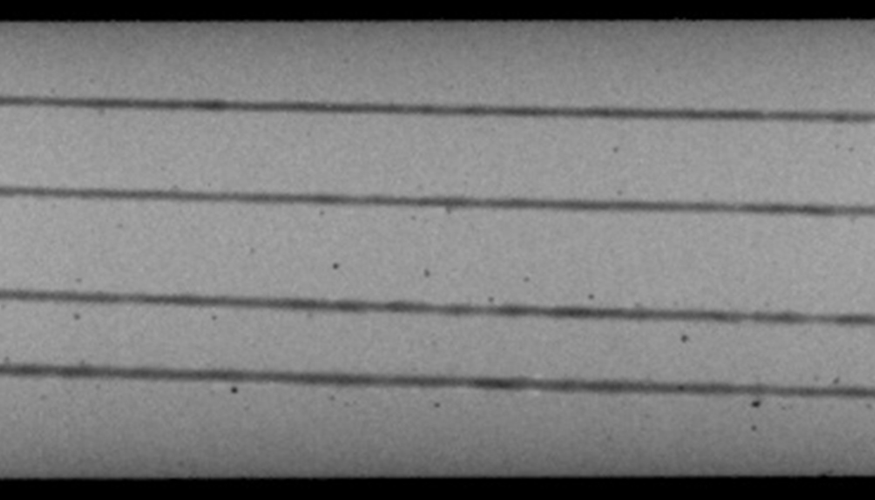
Una vez finalizados los ensayos no destructivos, se ha procedido a realizar los ensayos destructivos, tales como el análisis metalográfico, microdurezas y ensayos de tracción. Los resultados del análisis macrográfico tanto en las uniones soldadas en solape como a tope, muestran un cordón uniforme.
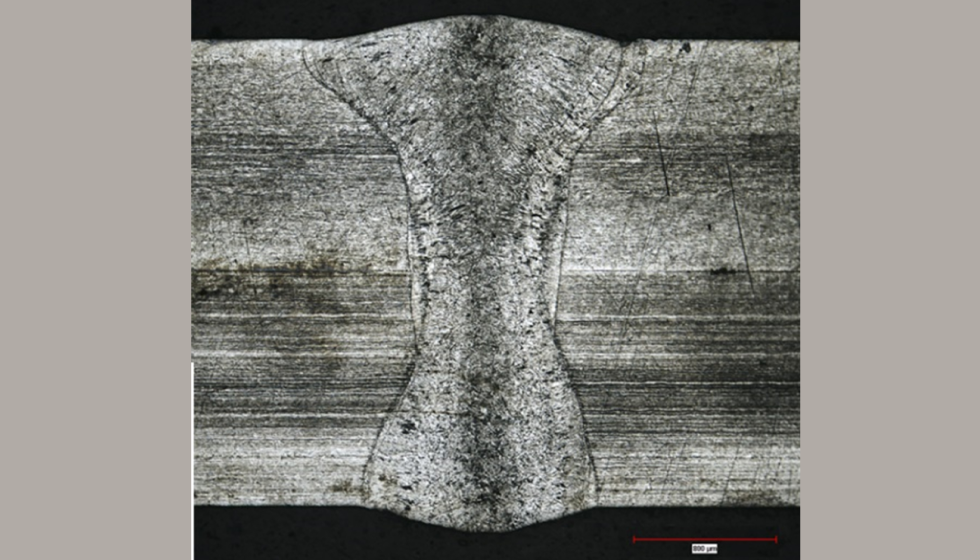
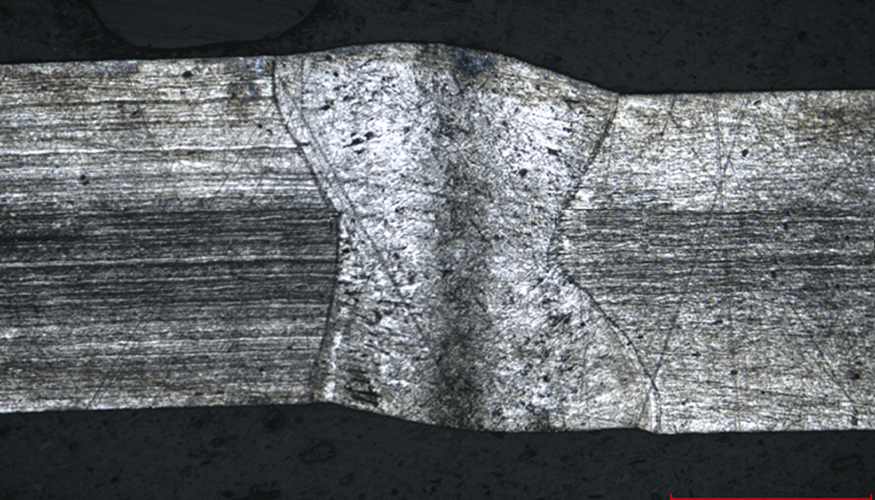
Las figuras 5 y 6 muestran las macrografías de las uniones realizadas en solape con la chapa AISI 321 colocada en la parte de arriba y a tope respectivamente. El cordón tiene forma de reloj de arena en ambos casos, con penetración completa y buena fusión con ambos materiales base.
Apenas se aprecia la zona afectada térmicamente puesto que el calor que aporta la soldadura laser es muy concentrado, y por su alta velocidad la pieza se ve poco afectada térmicamente. Los ángulos que se crean entre el material base y el cordón de soldadura no son prominentes, por lo que se puede concluir que la soldadura es adecuada. En la figura 5 se aprecia como el cordón tiende a crecer algo más hacia el acero inoxidable 321, debido a su mayor conductividad térmica.
Se han realizado varios estudios de microdureza en las probetas para analizar el efecto del aporte de calor en las propiedades mecánicas de las chapas base y la zona soldada. La gráfica 1 muestra los resultados de los ensayos de microdureza en la probeta soldada en solape con la chapa de Inconel 718 en la parte de arriba. Los resultados muestran que el material base Inconel 718 presenta la dureza más alta, siendo ésta de 178HV. La dureza a lo largo del material base Inconel 718 disminuye progresivamente al acercarse a la zona afectada térmicamente (ZAT) hasta llegar a 157HV, aumentando en la zona soldada hasta 164HV. En el caso del material base acero inoxidable 321, el material base también presenta el valor de dureza más elevado, siendo éste de 176HV. La disminución de la dureza al acercarse a la ZAT no es tan pronunciada como en el caso del Inconel 718, llegando a 161HV. La dureza aumenta de nuevo en el cordón soldado hasta llegar a 168HV, pero sin llegar a los valores del material base.
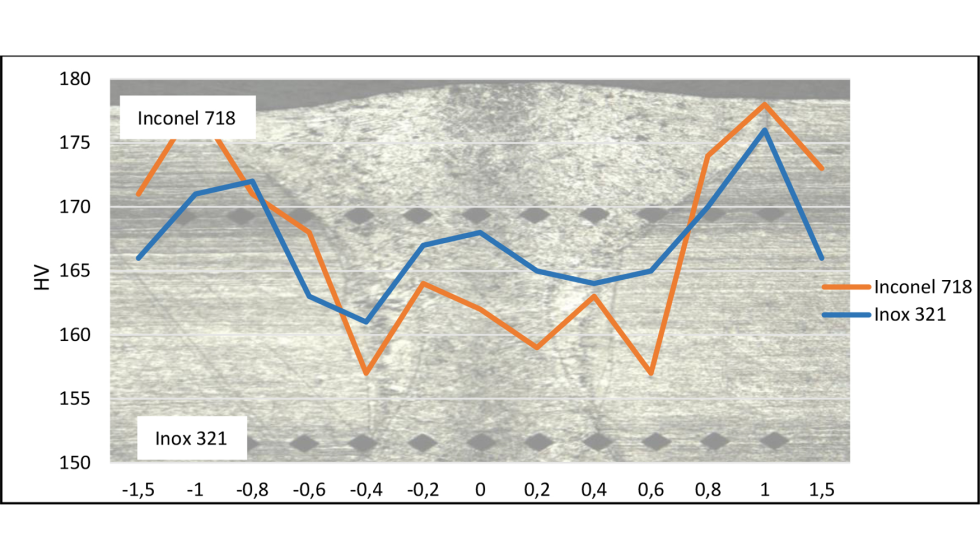
La gráfica 2 muestra los resultados de microdureza de la probeta soldada en solape con la chapa de acero inoxidable 321 en la parte de arriba. Los resultados son muy similares tanto en los materiales base como en la zona soldada. Aunque los valores de dureza del Inconel 718 en el material base son más bajos que en el caso anterior.
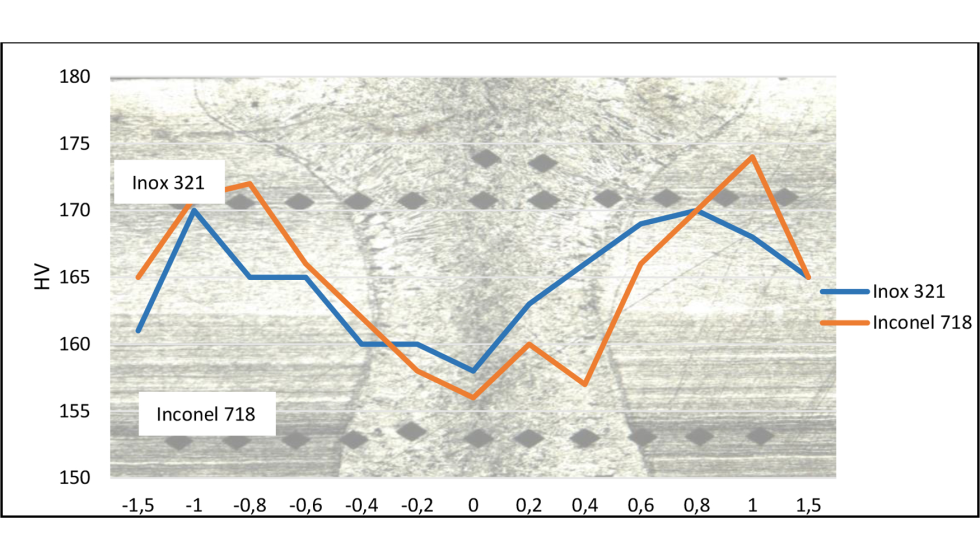
La gráfica 3 muestra los resultados de dureza de la muestra soldada a tope. En este caso también se repite el mismo patrón que en los casos anteriores. Los valores de dureza más elevados se encuentran en el material base, tanto en la chapa de Inconel 718 como en la de acero inoxidable 321 con valores máximos de 170HV en ambos casos. La dureza disminuye al acercarse a la ZAT hasta 154HV en el lado del Inconel 718 y hasta 152HV en la chapa de acero inoxidable 321, y vuelve a aumentarse en la zona central del cordón de soldadura hasta llegar a 165HV.
Se puede concluir que el rayo láser ha sido capaz de provocar la fusión de todos los elementos metálicos y formar una mezcla uniforme.
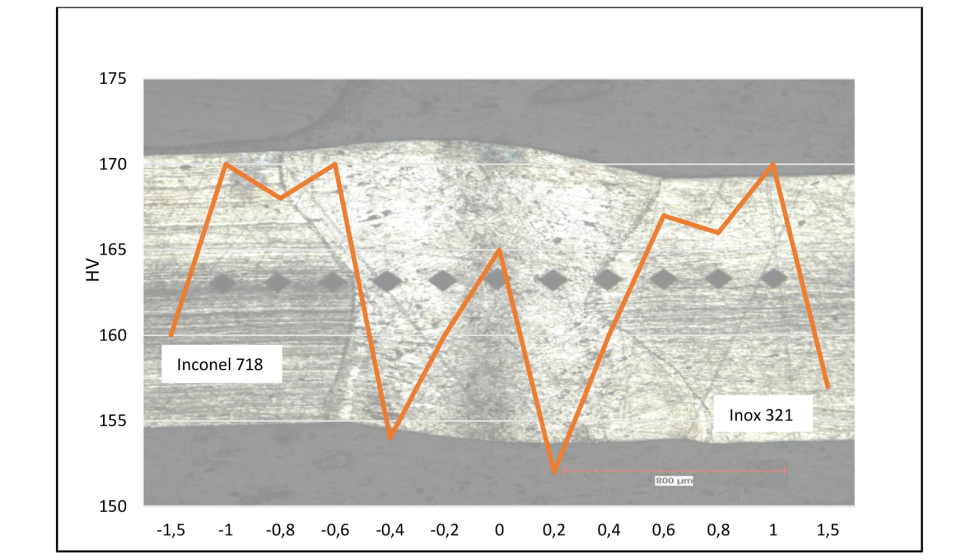
Los resultados de las pruebas de tracción muestran que la fractura de las probetas se ha producido en el metal base, lejos de la zona de fusión de las soldaduras en los dos ensayos. Esto significa que la resistencia de la unión es superior a la del metal base.
La figura 7 muestra la geometría de la probeta de tracción, y la figura 8 muestra la preparación de las muestras en la máquina MTS-Insight 100.
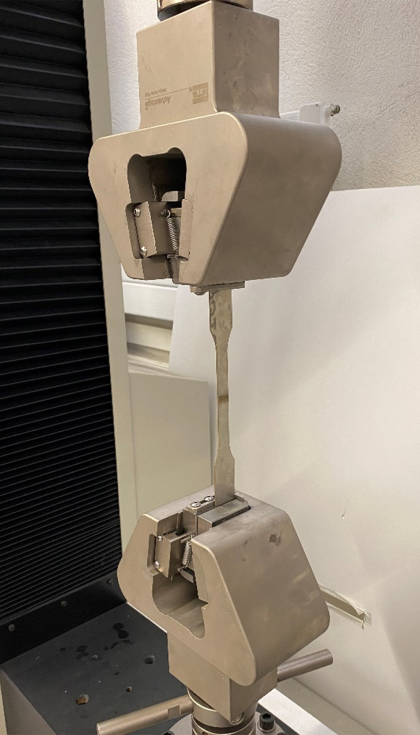
En la figura 9 se muestran las probetas tras la rotura por el ensayo de tracción. En ambos casos, se aprecia que la rotura se ha dado en el material base de acero inoxidable 321.
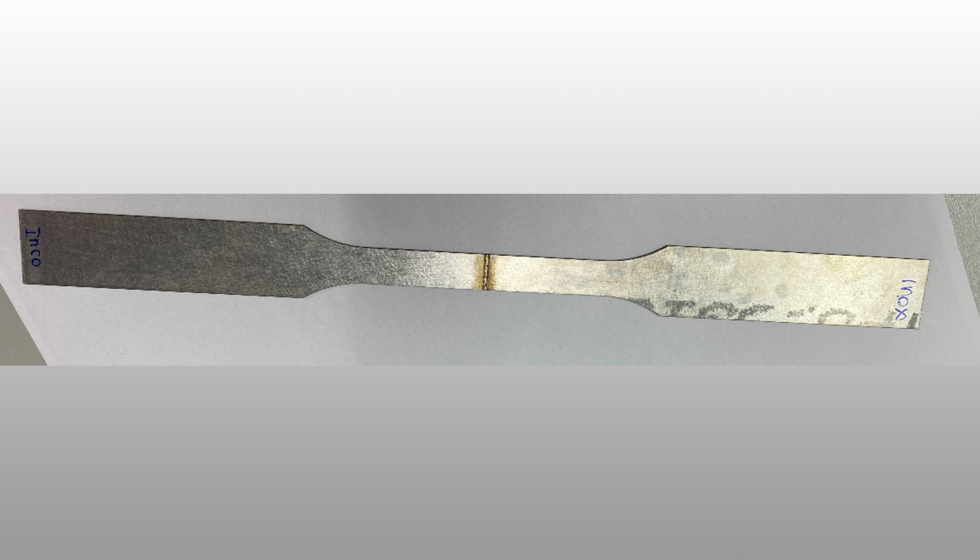
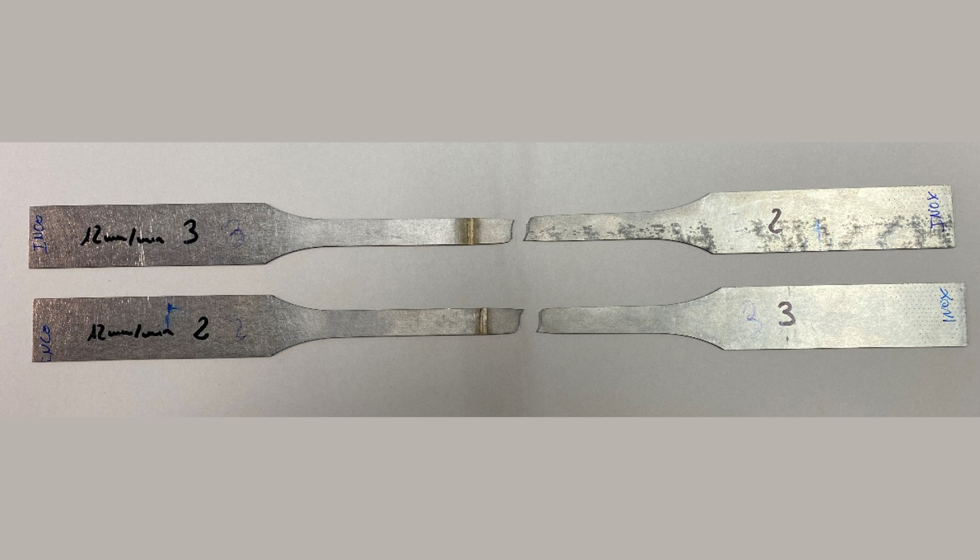
Las gráfica 4 y 5 se muestran las curvas de tensión-deformación obtenidas a temperatura ambiente. Durante los ensayos de tracción transversal, todas las probetas han fallado en el metal base menos resistente, en este caso el acero inoxidable 321.
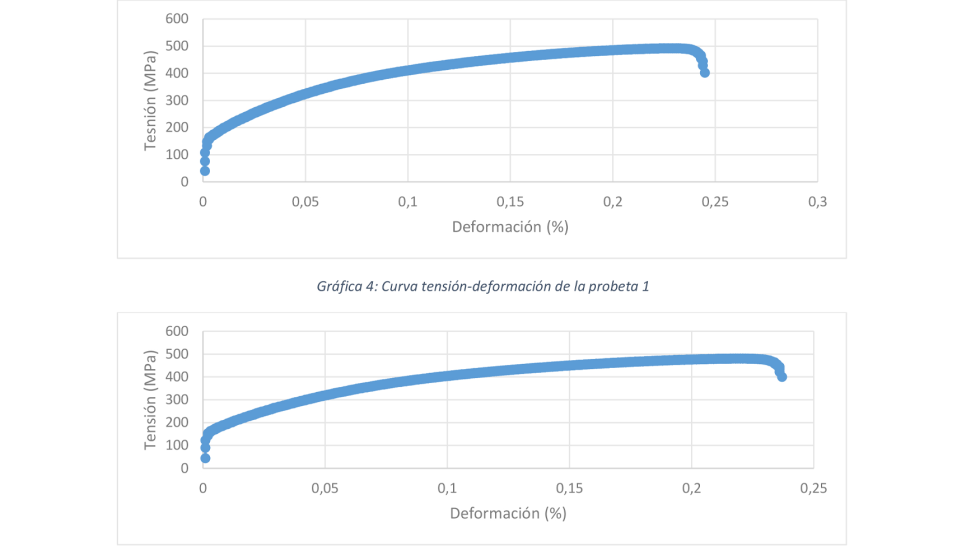
Conclusiones
Los resultados obtenidos en los ensayos realizados demuestran la viabilidad de unir mediante la soldadura láser los materiales Inconel 718 y acero inoxidable 321. Las radiografías muestran una buena integridad en los materiales fundidos, y los ensayos metalográficos demuestran que la unión soldada es homogénea y está libre de defectos. El orden de solape entre los dos materiales no afecta en los resultados de microdureza obtenidos. Los ensayos de tracción demuestran que la resistencia a tracción de la unión es superior a la del acero inoxidable 321.
Con este estudio, se pretende abaratar y reducir el peso en componentes que actualmente se fabrican íntegramente con Inconel 718, pudiendo sustituir este material por el acero inoxidable 321 en zonas que no tengan tanta exigencia térmica y mecánica.
Referencias
[1] Aghayar, Y., Naghashzadeh, A. R., & Atapour, M. (2021). An assessment of microstructure and mechanical properties of inconel 601/ 304 stainless steel dissimilar weld. Vacuum, 184(November 2020), 109970. https://doi.org/10.1016/j.vacuum.2020.109970
[2] Anup Kumar Maurya, Chandan Pandey, Rahul Chhibber, Dissimilar welding of duplex stainless steel with Ni alloys: A review, International Journal of Pressure Vessels and Piping, Volume 192, 2021, 104439, ISSN 0308-0161, https://doi.org/10.1016/j.ijpvp.2021.104439.
[3] Devendranath Ramkumar K., Dev Sidharth, Phani Prabhakar K.V., Rajendran R., Giri Mugundan K., Narayanan S., Microstructure and properties of inconel 718 and AISI 416 laser welded joints, Journal of Materials Processing Technology, Volume 266, 2019, Pages 52-62, ISSN 0924-0136, https://doi.org/10.1016/j.jmatprotec.2018.10.039.
[4] T. Ramkumar, M. Selvakumar, P. Narayanasamy, A. Ayisha Begam, P. Mathavan, A. Arun Raj, Studies on the structural property, mechanical relationships and corrosion behaviour of Inconel 718 and SS 316L dissimilar joints by TIG welding without using activated flux, Journal of Manufacturing Processes, Volume 30, 2017, Pages 290-298, ISSN 1526-6125, https://doi.org/10.1016/j.jmapro.2017.09.028.
[5] Gaurav Dak, Chandan Pandey, A critical review on dissimilar welds joint between martensitic and austenitic steel for power plant application, Journal of Manufacturing Processes, Volume 58, 2020, Pages 377-406, ISSN 1526-6125, https://doi.org/10.1016/j.jmapro.2020.08.019.