Hacia una mayor comprensión del fenómeno de rotura de hilo en electroerosión
Borja Izquierdo, de la Universidad del País Vasco/ Euskal Herriko Unibertsitatea (UPV/EHU); Izaro Ayesta, del Centro de Fabricación Avanzada Aeronáutica, CFAA; y Jun Wang y José A. Sánchez, de la UPV/EHU y el CFAA
11/04/2023Las ventajas de la electroerosión por hilo respecto a otros procesos de fabricación son claras: una gran precisión y capacidad de procesar materiales independientemente de su dureza o baja maquinabilidad. Sin embargo, uno de sus mayores hándicaps es el tiempo de proceso, algo elevado en comparación con los métodos tradicionales de fabricación. En especial, las roturas del hilo penalizan de manera considerable el tiempo de erosión, ya que, aunque las máquinas están dotadas con sistemas de enhebrado automático, el tiempo entre la rotura, el enhebrado y la vuelta al corte, es un tiempo añadido al proceso que es mejor evitar.
En este campo, los primeros investigadores descubrieron que la rotura del hilo estaba relacionada de algún modo con las temperaturas excesivas. Hablaban de la carga térmica como una de las principales razones de la rotura de hilo [1] [2]. Sin embargo, parece que no es la única razón. La fuerza de tracción que se aplica para mantener la verticalidad del hilo y garantizar la precisión, puede ser otros de los actores que participan en la rotura, aunque alguno de los estudios que se ha realizado en el que se investiga el efecto Rehbinder (efecto que combina el daño del hilo y las cargas del proceso) muestra que este efecto no afecta de forma significativa a su rotura [3]. Otro trabajo [4] muestra que la disminución trasversal del hilo debido a la tensión mecánica aplicada puede ser una razón, pero no han profundizado más allá. Para seguir investigando la disminución de la sección transversal del hilo en el proceso de WEDM, los cráteres generados por las descargas cobran importancia y la construcción de modelos térmicos es un método esencial para conocerla [5]. En cuanto al fluido de corte, agua desionizada en la mayoría de casos, se inyecta en el canal de corte a alta presión mediante la boquilla superior e inferior para limpiar, que no se acumulen residuos y el corte sea más rápido y eficiente. Sin embargo, existe un estudio que habla que este fluido de corte también puede ser uno de los causantes de las roturas de hilo, haciendo que la acumulación de residuos se concentre en una altura determinada del hilo [6]. La inteligencia artificial no es ajena a este campo, ejemplo claro de esto es el trabajo de Abhilash y Chakradhar [7], se utilizó la red neuronal artificial para la predicción: con la entrada de energía de descarga, frecuencia de chispa, ratio de chispa abierta y ratio de cortocircuito, su sistema de predicción puede alcanzar una precisión del 90%.
Además de la comunidad científica, la comunidad industrial también ha realizado profundos estudios sobre la rotura del hilo dentro del marco de aumentar la eficiencia del proceso. Para ello se valen de modelos basados en los datos adquiridos de máquina, gracias a la analítica de datos avanzada y algoritmos IA. Uno de los fabricantes que más ha apostado por esto es GF Machining Solutions. Sus máquinas de hilo permiten integrar el sistema Spark Track [8], que permite detectar a tiempo real dónde se produce cada descarga a lo largo del hilo. Este sistema tiene ciertas limitaciones en materiales (acero, sobre todo) y alturas permitidas (hasta 100mm de altura), pero prometen un sistema Intelligent Spark Protection System (ISPS) con el que se evita la rotura del hilo en piezas de sección variables gracias a la monitorización constante de las descargas y al control adaptativo de los parámetros del proceso, lo que aumenta el rendimiento del proceso. Por último, también cabe destacar un par de artículos [9] [10] publicados en la revista EDM Today y una patente de uno de los fabricantes de hilo más prestigiosos a nivel europeo, Thermocompact. En estos artículos se repasan todas las posibles variables que toman parte en el proceso de rotura de hilo, concluyendo en que es un fenómeno complejo que combina el efecto térmico, la acumulación de las descargas, la tensión mecánica, además de la aparición de burbujas en la zona de rotura.
Esta revisión refuerza la necesidad de seguir trabajando en aumentar el conocimiento de las razones por las que el hilo rompe. Para ello, se ha realizado un análisis experimental del efecto térmico y de la acumulación de las descargas.
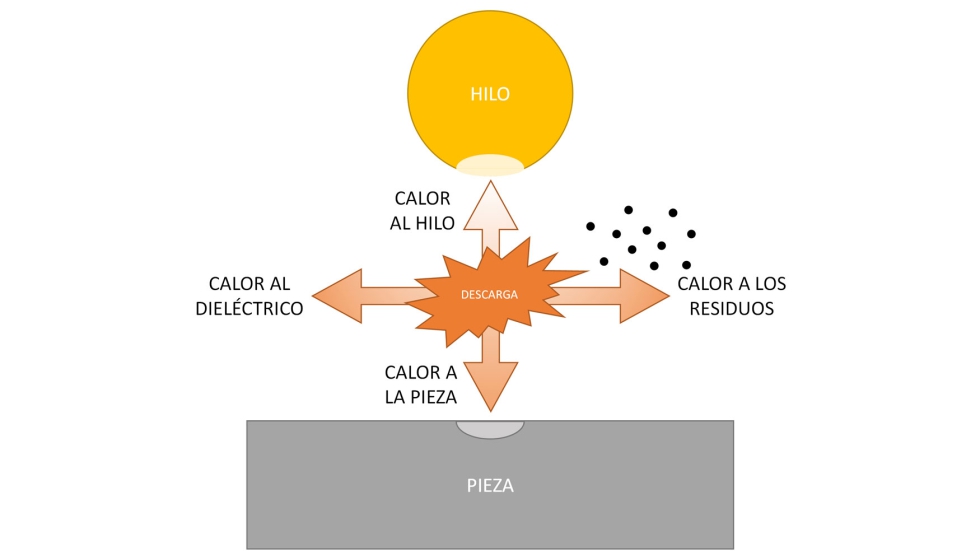
Análisis del efecto térmico del proceso
La conceptualización del proceso de arranque de material en WEDM se centra principalmente en el fenómeno térmico. El hilo y la pieza se sumergen en un medio dieléctrico (agua desionizada en la mayoría de las máquinas). El generador digital de la máquina controla cada descarga en términos de tensión, corriente y duración, con un periodo de descarga de pocos microsegundos. La descarga se produce allí donde se reduce la conductividad dieléctrica local, posiblemente debido a la presencia de una mayor concentración de residuos, o debido a una separación más corta en ese momento y lugar. Así, el calor generado se transfiere a la pieza, al hilo, a los residuos y al dieléctrico, como se muestra en la figura 1. Para entender mejor la rotura, hay que comprobar cuanto de ese porcentaje de calor se transfiere al hilo, ya que esa parte contribuirá a debilitarlo.
Por ese motivo, se han realizado una serie de experimentos en la maquina ONA AV35 del CFAA. La finalidad de los experimentos ha sido medir el tamaño de cráter del hilo para después contrastar este valor con la de un modelo térmico desarrollado. Los ensayos se han realizado con hilo de latón (Cu63%/Zn37%, UTS 960 N/mm2) de 0,25 mm de diámetro como herramienta y un tocho de 50 mm de Acero Sverker21 (acero de gran dureza y alta resistencia al desgaste) como pieza. Se han utilizado parámetros de tablas tecnológicas de máquina para realizar los ensayos. Se han realizado 3 ensayos en las mismas condiciones.
Una vez realizados los cortes, se ha recogido el hilo para analizar su desgaste. La idea consiste en medir en la sección trasversal del hilo el área de material de hilo arrancado (Aarranque) y multiplicar esta área por la longitud del hilo para obtener el volumen total de material de hilo arrancado durante las pruebas. Además, se han recogido el número total de descargas que ha habido durante la prueba mediante el control de la maquina (Ndes). Si se divide el volumen total de material de hilo arrancado entre el número de descargas totales, se obtiene el volumen medio de cada cráter (vcráter). Además, en el proceso de electroerosión, parte del material que se funde, se vuelve a resolidificar en la propia superficie, tanto de la pieza como del hilo. Se genera una capa de material refundido que se conoce como ‘capa blanca’. Esta área de material refundido también se puede medir en la sección transversal del hilo (Acapablanca).
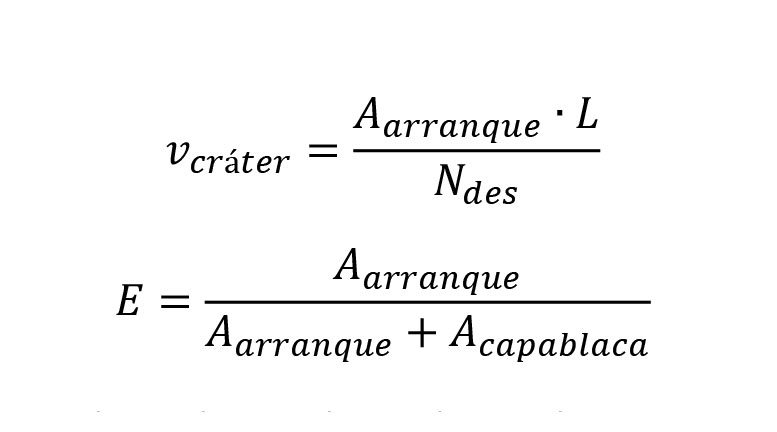
La tabla de la figura 2 muestra los valores obtenidos en los experimentos. En esa misma figura, se muestra la sección trasversal del hilo obtenida en el microscopio electrónico de barrido (Hitachi S-3400 N), donde se puede apreciar que la descarga se produce aproximadamente en un 68% de perímetro del hilo. Cabe destacar que en el análisis de composición de capa blanca han aparecido elementos de la propia pieza, además de material del hilo. Por último, se ha calculado la eficiencia de fusión E como 44.98% relacionando el área de material de hilo eliminada y la suma de ésta con el área de material refundido.
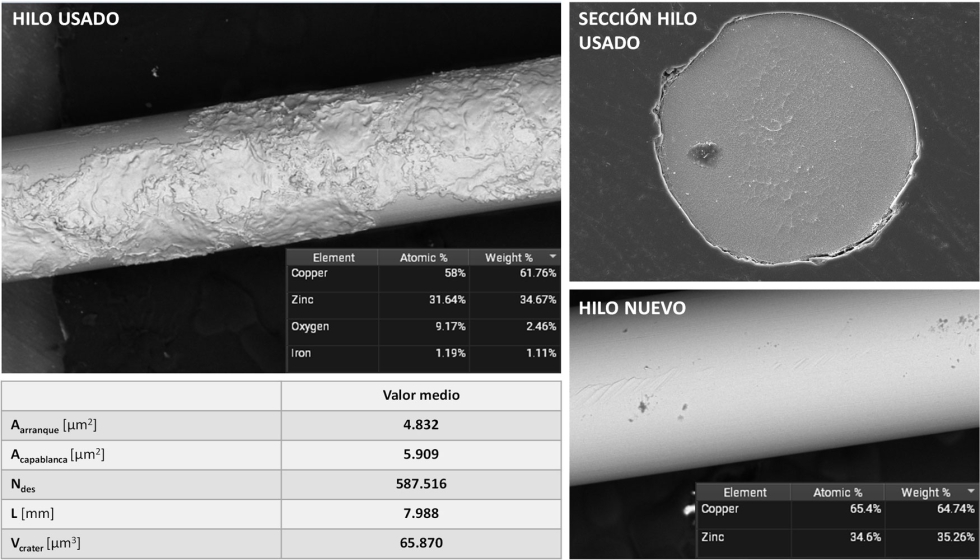
Una vez que se ha obtenido el valor del volumen del cráter del hilo, los resultados experimentales pueden compararse con el modelo térmico desarrollado anteriormente [11], de modo que es posible obtener un valor de la relación de partición de calor que llega al hilo. Dependiendo del volumen de cráter experimental, se obtiene la fracción de calor que pasa el hilo (fc) mediante el grafico de la figura 3. Este grafico se ha obtenido con el modelo experimental desarrollado. El valor de porcentaje de calor que se transfiere al hilo es de 46,74%. Tras esto, se ha realizado una simulación de verificación entre el volumen de cráter de los experimentos y el obtenido mediante la simulación numérica (vteórico) y el error es del 0,53%, calculado mediante la ecuación de la figura 3. Este error muestra que el valor obtenido para el porcentaje de calor que pasa al hilo es admisible.
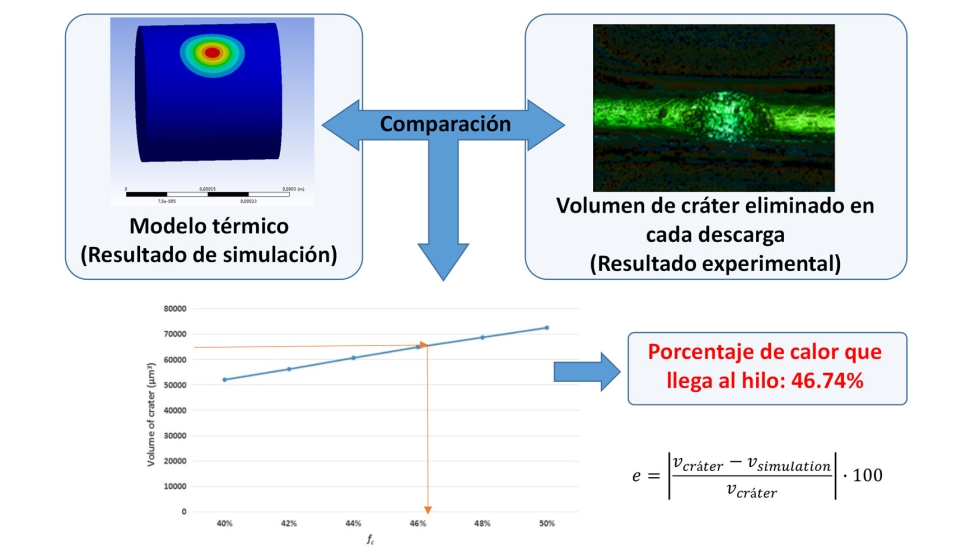
Además, también se ha observado el hilo roto en al microscopio electrónico de barrido. El modo de fallo es claramente el de un fallo dúctil y puede observarse claramente la forma de copa y cono típica de los materiales dúctiles. La región de fractura rápida se produce a 45° respecto al plano de la carga de tracción, ángulo en el que aparece el mayor esfuerzo cortante. Este tipo de fallo dúctil está causado posiblemente por una disminución del área de la sección transversal del hilo.
Acumulación de descargas
Tal como se ha mencionado en la introducción, la acumulación de descargas es un aspecto que se ha estudiado en varios trabajos en los que se ha analizado la rotura de hilo y por ese motivo, merece la pena profundizar en ese fenómeno. La acumulación local de descargas se atribuye a la imposibilidad de eliminar eficazmente los restos generados por una o varias descargas anteriores. El origen de esto puede estar relacionado con causas como un tiempo de pausa demasiado corto, que dificulta la eliminación de los residuos y el enfriamiento del hilo. Así, la conductividad local en una región cercana a las descargas anteriores se vuelve entonces mayor y aumenta la probabilidad de que se produzca una nueva descarga en esa región. La hipótesis es que, si la acumulación de descargas en una región es suficientemente alta, la carga térmica local sobre el hilo aumenta de tal manera que se reduce la sección de carga activa del hilo. Si esta reducción es suficientemente alta, la sección del hilo no puede soportar la fuerza axial y, en consecuencia, se produce el fallo dúctil. Para verificar esta hipótesis, es necesario encontrar la posición de varias descargas justo antes de la rotura del hilo.
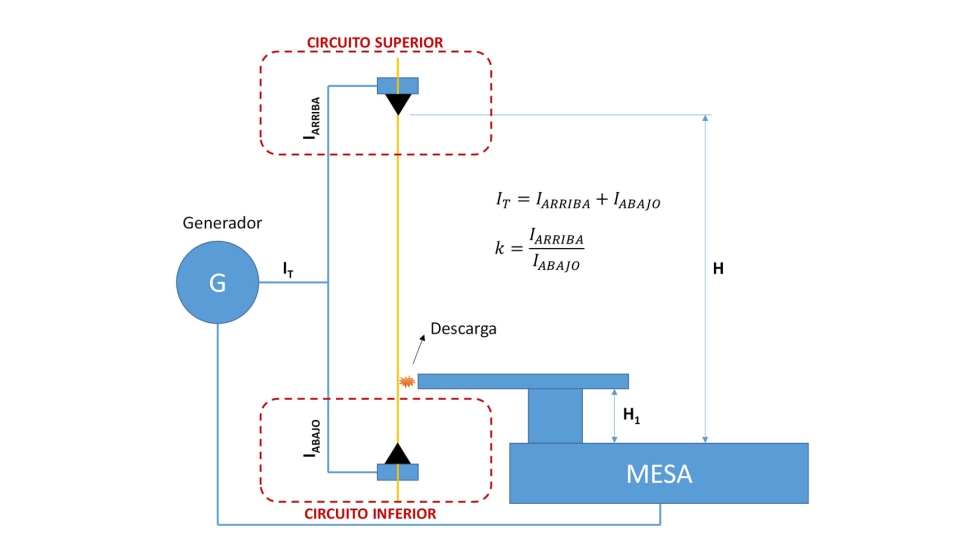
La detección de la localización de la descarga en la longitud del hilo es un principio que se conoce desde hace más de 30 años [12] pero su aplicación industrial sigue estando en estudio por diversas razones, entre las que destaca la necesidad de un sistema de adquisición de muy alta frecuencia y que la detección del espesor depende de varias variables. Entre otras cosas, depende del material de la pieza de trabajo, el tamaño y el tipo de hilo, y la precisión de la detección depende de la estabilidad del impulso del generador y de la impedancia del circuito de la descarga. Sin embargo, el principio en sí, es simple. En las máquinas de hilo, la corriente eléctrica que aporta el generador se divide en dos corrientes parciales: un circuito que pasa por el cabezal superior y otro que pasa por el cabezal inferior. En ambos cabezales existen dos piezas por las que fluye la corriente al hilo. Como se muestra en la figura 4 cuando se produce la descarga se puede ver el hilo dividido en dos partes (parte superior y parte inferior). Mientras tanto, se forman dos circuitos cerrados (circuito superior y circuito inferior) que incluyen respectivamente partes relativas al hilo. Si se obtiene la relación entre la intensidad superior y la inferior, se puede obtener la localización de la descarga.
Para verificar la viabilidad de este método, se ha montado un banco de ensayo en la máquina ONA AV35 del CFAA. Para ello, se han colocado dos sondas tipo ‘Rogowky’ que miden la intensidad eléctrica que pasa a través de los dos circuitos. Estas sondas se han conectado a un osciloscopio digital que permite ver las descargas eléctricas en tiempo real. Para analizar la localización de las descargas en el momento en el que el hilo rompe, se ha planteado un experimento en dos fases. En la primera fase se ha construido una curva de calibración. Se ha colocado una chapa de pequeño espesor (2 mm) en distintas alturas. Como se muestra en la figura 4, la distancia entre dos boquillas (H) se ha mantenido constante y se han elegido 7 alturas de colocación de la pieza de trabajo de chapa (H1). Para cada altura, se han medido un numero de descargas y para cada descarga, se ha calculado la relación k entre la intensidad de arriba y la de abajo (ver figura 4). Una vez realizado esto, se calcula una ecuación de ajuste. Esta ecuación sigue una tendencia casi lineal, con un error aproximado de 2 mm.
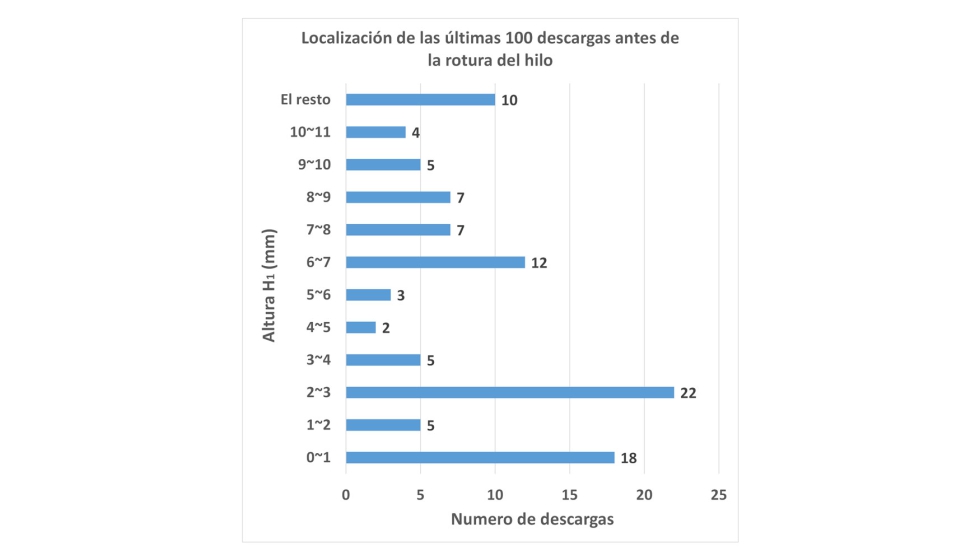
En la segunda fase, se ha realizado otro experimento con un espesor de pieza de 50 mm y, para facilitar la obtención de la rotura del hilo, se ha bajado el tiempo de pausa. Durante el corte se han medido la intensidad de arriba y la de debajo de todas las descargas. Cuando el hilo se ha roto, se han elegido las ultimas 100 descargas para saber en qué altura caen y comprobar si existe una acumulación de descargas en algún punto. Se calcula la relación k para cada una de las 50 descargas y se aplica la ecuación de ajuste. En la figura 5, se muestra que la mayor parte de las descargas caen en torno a los 3 mm. Esto muestra que existen una acumulación de descargas en una longitud de hilo concreta antes de la rotura del hilo.
Conclusiones y trabajo futuro
Este trabajo muestra los avances que se han realizado para entender mejor la razón por la que el hilo rompe. Cabe destacar, que una gran parte del calor que se genera en el proceso se transmite al hilo (un 46,74%), lo que debilita su sección útil y es uno de los factores que afecta en la propia rotura. Además, los resultados de los ensayos realizados para localizar dónde caen las descargas antes de que rompa el hilo, muestra que existe una acumulación de descargas en una zona, otro de los factores importantes para la rotura. Sin embargo, hay que mencionar que este aspecto necesita de mayor estudio para localizar las descargas con una mayor precisión, ya que el sistema de localización desarrollado, tiene un error que puede afectar en la detección online de la rotura.
Referencias
[1] Dekeyser W, Snoeys R, Jennes M (1985). A thermal model to investigate the wire rupture phenomenon for improving performance in EDM wire cutting. J Manuf Syst 4:179–190. https://doi.org/10.1016/0278-6125(85)90024-X
[2] Saha S, Pachon M, Ghoshal A, Schulz MJ (2004) Finite element modeling and op-timization to prevent wire breakage in electro-discharge machining. J Mater Process Technol 31:451–463. https://doi.org/10.1016/j.mechrescom.2003.09.006
[3] Fedorov AA, Blesman AI, Postnikov DV, Polonyankin DA, Russkhik GS, Linovsky AV (2018) Investigation of the impact of Rehbinder efect, electrical erosion and wire tension on wire breakages during WEDM. J Mater Process Technol 256:131– 144. https://doi.org/10.1016/j.jmatprotec.2018.02.002
[4] Bredgauer IO, Polonyankin DA, Fedorov AA, Blesman AI, Linovsky AV, Postnikov DV (2021) Investigating wire breakage during EDM with fractographic analysis. J Phys Conf Ser 1791:012005. https://doi.org/10.1088/1742-6596/1791/1/012005
[5] Klocke F, Mohammadnejada M, Zeisa M, Klink A (2018) Investigation on the variability of existing models for simulation of local temperature feld during a single discharge for electrical discharge machining (EDM). Procedia CIRP 68:260–265
[6] Okada A, Konishi T, Okamoto Y, Kurihara H (2015) Wire breakage and defection caused by nozzle jet fushing in wire EDM. CIRP Ann 64:233–236.
[7] Abhilash P, Chakradhar D (2022) Wire EDM failure prediction and process control based on sensor fusion and pulse train analysis. Int J Adv Manuf Technol 118:1453–1467.
[8] https://www.gfms.com/en-gb/machines/edm/wire-cutting/intelligent-spark-protection-system.html
[9] Ouvrard B, Do K, Lafleur L, Dutrieux J, Ly M, Sanchez G (2019) Wire Breaks during EDM rough cuts with Non-sealed Flushing Conditions. EDM Today, Winter 2019 Issue: 60-64
[10] Do K, Ly M, Ouvrard B, Lafleur L, Sanchez G (2019) Wire Creaks during EDM rough cuts Part 2. EDM Today Fall 2019: 36-38
[11] Wang J, Sánchez JA, Izquierdo B, Ayesta I (2023) Effect of discharge accumulation on wire breakage in WEDM process. Int J Adv Manuf Technol 125: 1343–1353 (2023). https://doi.org/10.1007/s00170-022-10786-z
[12] Boccadoro M, D’Amario R, Baumeler M (2020) Towards a better controlled EDM: industrial applications of a discharge location sensor in an industrial wire electrical discharge machine. Procedia CIRP 95:600–604. https://doi.org/10.1016/j.procir.2020.02.266