El rectificado por generación continua permite trabajar espacios muy reducidos
Martin Witzsch, físico diplomado y periodista independiente para Kapp Niles, y Ralf Dremel, director técnico de producto en Kapp Niles
29/03/2022Cuando se trata del acabado duro de los dientes de los engranajes, el potencial relacionado con el proceso va de la mano de los altos costes de producción. La opción más económica es probablemente el rectificado por generación continua. Sin embargo, no todas las rectificadoras por generación continua son adecuadas para la producción de los componentes compactos. En este artículo se exponen las exigencias pertinentes y se muestran posibles soluciones.
No es necesario reinventar la fabricación de transmisiones para adaptarlas al sector de la movilidad eléctrica, pero sí hay que afrontar algunos nuevos retos. Entre ellos se encuentran, sobre todo, la alta densidad de potencia y el espacio de instalación compacto en el que debe alojarse todo el tren de potencia. Al mismo tiempo, las nuevas áreas de aplicación están abriendo nuevas oportunidades de venta: las e-bikes, por ejemplo, han ganado recientemente en popularidad. Aumentan considerablemente la autonomía y la capacidad de transporte en la vida cotidiana y durante el tiempo de ocio. En consecuencia, la demanda es alta.
Esto beneficia a los fabricantes y a sus proveedores, entre ellos los fabricantes de cajas de cambios. Sin embargo, ya sean dos o cuatro ruedas, la tecnología de accionamiento es sofisticada. La atención se centra en las capacidades de carga de los flancos requeridas y en el comportamiento acústico de los dientes de los engranajes debido a las condiciones límite impuestas por el motor de accionamiento eléctrico: un par elevado casi constante en la gama de velocidades de 0 a 18.000 rpm. Sin embargo, los nuevos retos no se limitan a las piezas mecanizadas, sino que también afectan directamente al proceso de fabricación: Debido al diseño compacto, en el diseño de la caja de cambios aparece un número cada vez mayor de componentes con contornos que interfieren. Las herramientas de gran tamaño con dimensiones estándar de la muela helicoidal alcanzan rápida y literalmente sus límites. Para no tener que recurrir a procesos más largos y, por tanto, más costosos, las herramientas también deben miniaturizarse.
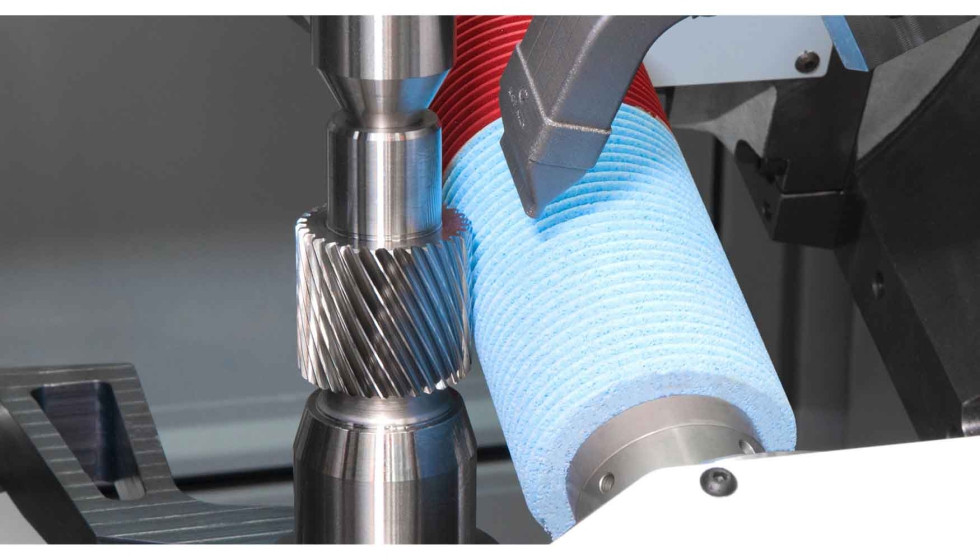
Identificar y superar los límites
Hasta ahora, el acabado duro de los engranajes con contornos de interferencia se ha realizado principalmente mediante el rectificado de perfiles discontinuos o el bruñido de engranajes. En comparación con el rectificado de generación continua, ambos procesos mencionados presentan diferentes desventajas en términos de productividad, eficiencia económica o consistencia de la calidad. El problema es que los tornillos sinfín de rectificado habituales, de 300 mm de diámetro, son demasiado grandes para tratar componentes con contornos interferentes. Al mismo tiempo, las herramientas más pequeñas requieren una mayor velocidad para alcanzar altas velocidades de corte.
Sin embargo, los conceptos de máquina implementados anteriormente no estaban diseñados para los elevados requisitos dinámicos relativos al accionamiento de la herramienta y la pieza. Los nuevos tipos de husillos de alta velocidad en combinación con un accionamiento directo dinámico del eje de la pieza ofrecen una solución. Esto permite aprovechar las ventajas del rectificado por generación continua, un proceso que se caracteriza por tiempos de mecanizado más cortos, costes de herramienta más bajos y un nivel de calidad muy alto. La eficacia económica del rectificado por generación continua en comparación directa con el rectificado de perfiles puede demostrarse mediante los dos componentes seleccionados ‘coche’ y ‘bicicleta’ (como se muestra en las figuras 1 y 2). Las tablas correspondientes (‘Coche’ y ‘Bicicleta’) proporcionan una visión general de los beneficios de tiempo y costes relacionados.
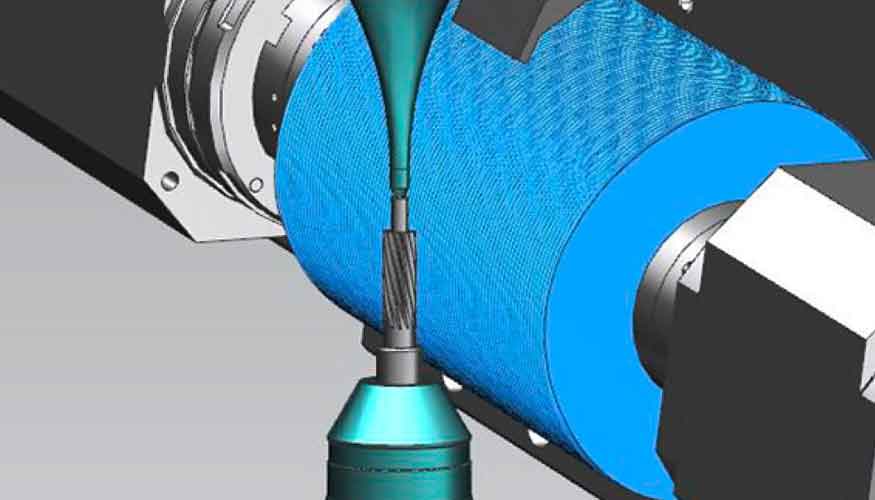
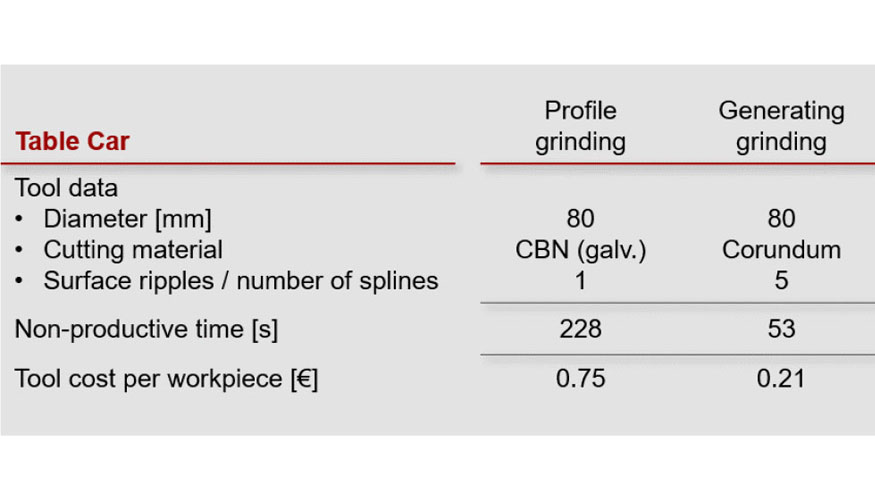
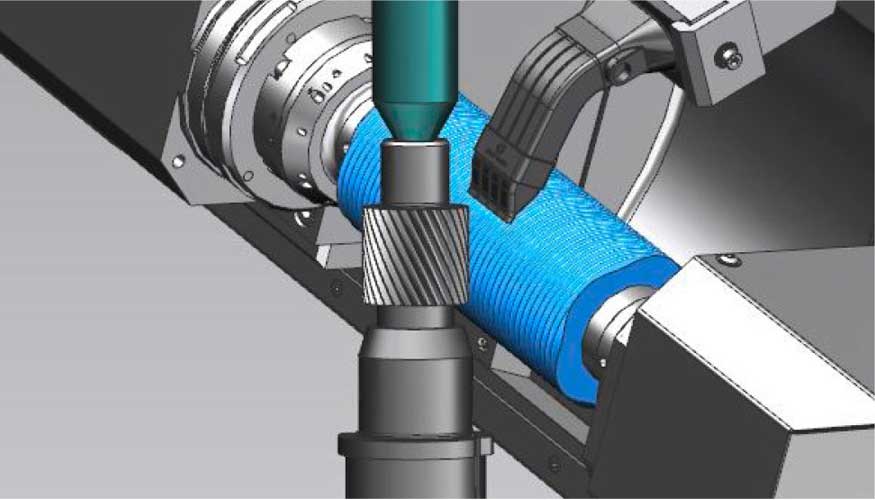
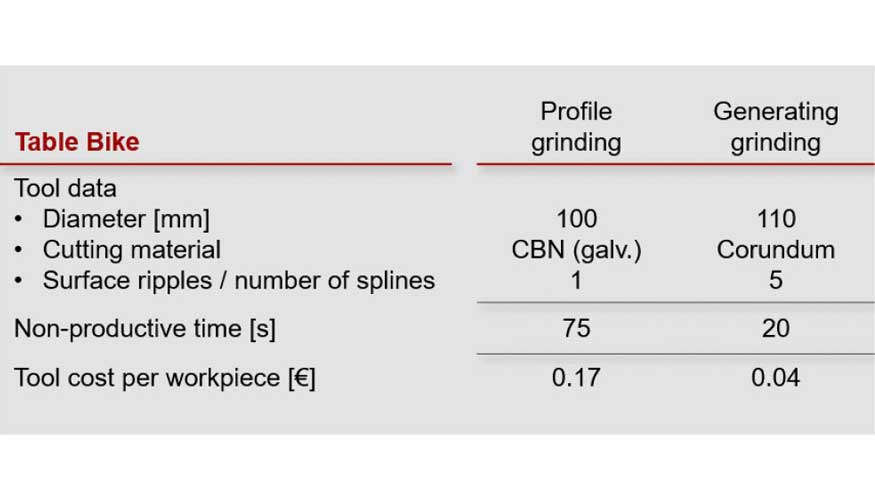
Las máquinas adecuadas para cubrir las necesidades
El fabricante de máquinas-herramienta Kapp Niles., con sede en Coburg, Alemania, y especializado en soluciones de sistema para el rectificado de engranajes, ofrece dos tipos de máquinas para satisfacer las necesidades de los clientes. Ambas series están equipadas con accionamientos de alto rendimiento para las herramientas (25.000 rpm) y las piezas (5.000 rpm).
La KNG 350 flex HS tiene un diseño convencional con un accionamiento de la pieza. La máquina está disponible en dos versiones: para miniaturas y lotes pequeños con carga manual. Para volúmenes mayores, está disponible una versión automatizada con un cargador de anillos integrado. Con esta máquina se pueden procesar piezas de hasta 350 mm de diámetro. La máquina se caracteriza por sus cortos tiempos de preparación, que se consiguen gracias al uso de componentes inteligentes y a una ergonomía única.
Sin embargo, para la producción a gran escala, merece la pena tener en cuenta los tiempos no productivos de la máquina preestablecidos por el diseño. La serie KX TWIN, con dos accionamientos de piezas y un proceso de carga y descarga que se realiza en paralelo a la operación de rectificado propiamente dicha, ofrece un potencial adicional para la reducción de los tiempos no productivos. El centrifugado en línea de los componentes directamente en la máquina permite cumplir con el enfoque de ‘Fábrica Limpia’ en todos los conceptos de automatización conocidos.
Requisitos adicionales relacionados con la producción
Además del mecanizado de componentes compactos con contornos interferentes, se plantean los siguientes retos adicionales cuando se trata de la producción de cajas de engranajes electrónicas:
- El comportamiento acústico de la caja de cambios y, por tanto, especialmente de los dientes de los engranajes, ha ido ganando importancia.
- Dado que la capacidad de carga de los dientes de los engranajes se perfecciona continuamente, la topología del flanco del diente es cada vez más importante. Durante el proceso de rectificado generador, se produce un enclavamiento natural en los flancos de los dientes mecanizados. Con el innovador software de rectificado KN, este fenómeno no solo puede simularse de antemano, sino que también puede eliminarse por completo o manipularse con precisión.
- Otra cuestión es la rugosidad de la superficie. Con una herramienta estándar, se pueden alcanzar de forma fiable valores de una profundidad de rugosidad media Rz = 2,5 - 3 μm con un rectificado de generación continua. Para requisitos más elevados, Kapp Niles ofrece herramientas combinadas que tienen dos zonas diferentes: una con grano estándar y otra diseñada para el esmerilado fino o el pulido, en función de los requisitos de la superficie. Esto permite alcanzar valores de rugosidad de Rz <1 μm. La relación de contacto significativamente mayor de los flancos de los dientes aumenta la capacidad de carga máxima del engranaje. Otra ventaja de este proceso es que puede integrarse en cadenas de procesos automatizados con ‘flujo de una pieza’, lo que no ha sido posible con el acabado vibratorio utilizado hasta ahora.
Conclusión
Para la producción de cajas de cambios electrónicas que ofrezcan algo más que el nivel técnico de las cajas de cambios utilizadas en los motores de combustión convencionales se necesitan amplios conocimientos y soluciones de última generación. Esto supone un reto, pero también crea grandes oportunidades para los fabricantes que dominan el despliegue de los últimos métodos de producción. El rectificado de generación continua con herramientas pequeñas es uno de los pilares. En la actualidad, Kapp Niles ofrece una amplia gama de soluciones que van más allá de la fabricación convencional con máquinas herramienta. La supervisión del proceso, el seguimiento de las piezas y la garantía de calidad en línea se están convirtiendo cada vez más en una parte integral de los sistemas de fabricación modernos. Esto significa que incluso los fabricantes de lugares con salarios elevados pueden imponerse en la competencia internacional. Especialmente en tiempos en los que la industria se ha vuelto dolorosamente consciente de la vulnerabilidad de la fabricación globalizada, esto supone una enorme oportunidad para contrarrestar las presiones de los costes.