Modelización térmica del centro de mecanizado Ibarmia THR16 con barras estructurales integradas
Brayan Medina Guibovich y Naiara Ortega, del Centro de Fabricación Avanzada Aeronáutica (UPV/EHU); y Juanjo Zulaika Muniain y Josu Larrañaga Leturia, de Tecnalia
15/03/2022Entre las distintas fuentes de errores nos podemos encontrar con errores estáticos, cuasi-estáticos y dinámicos, siendo los errores térmicos una fuente de error de origen cuasi-estático muy importantes y que afectan considerablemente al comportamiento de la máquina (en algunos casos los errores térmicos en máquina-herramienta han llegado a ser fuente del 70% de los errores totales). Es por ello, que la obtención de un modelo térmico en máquinas-herramienta que estime dichos errores térmicos que se generan durante el proceso puedan ser una solución de cara a una futura compensación de estos.
Errores térmicos en máquina-herramienta
Los errores térmicos que puede sufrir una máquina-herramienta, sobre todo de grandes dimensiones, son generados debido a las variaciones de temperatura que se dan a lo largo de la estructura por los focos de calor que aparecen cuando la máquina está en funcionamiento. Como consecuencia, aparecen dilataciones térmicas en los diferentes elementos de la máquina y se generan deformaciones. Además, estos errores también surgen por los cambios de la temperatura ambiente y los gradientes térmicos que se generan en la máquina. Se puede decir que los errores térmicos son de tipo cuasi-estático, ya que afectan a la máquina, pero de una manera lenta en el tiempo. Además, los errores no dependen sólo de las condiciones en el instante actual sino, que tienen memoria y también son influidas por las condiciones en instantes anteriores.
En una máquina-herramienta se pueden identificar principalmente seis fuentes de error:
- Calor generado en el proceso de corte.
- Pérdidas de energía de la propia máquina-herramienta.
- Intercambio de calor debido a sistemas hidráulicos y de refrigeración.
- Intercambio de calor que se da con el ambiente.
- El efecto térmico de las personas en el entorno de la máquina.
- La memoria térmica de la máquina por las condiciones anteriores.
Estas seis principales fuentes de error generan deformaciones termo-mecánicas que reducen la precisión de la máquina-herramienta. Es más, otro problema es la difícil repetitividad de un estado de la máquina, ya que las condiciones ambientales, junto con el tiempo de funcionamiento de la máquina son cambiantes. Por otro lado, cuanto más grande sea la máquina mayor suele ser el error térmico. La magnitud del error térmico en una máquina-herramienta de grandes dimensiones puede llegar a estar en torno a la décima de milímetro (0,1mm), que puede suponer la no validez de piezas con gran demanda de precisión.
Se pueden dividir las seis fuentes principales de error como fuentes internas y externas. Las fuentes internas son todas las fuentes que están conectadas con la estructura de la máquina-herramienta. Se pueden encontrar como fuentes internas los rodamientos, los actuadores lineales, los motores de par, el electro-husillo y otras unidades auxiliares. El calor que generan estos componentes suele deberse a las pérdidas de energía debido a efectos de fricción entre componentes y efectos eléctricos (por ejemplo, efecto Joule). Elementos auxiliares como el sistema de refrigeración pueden actuar como sumideros de calor que ayudan a evacuar el calor. La presencia de estos diferentes focos y sumideros de calor cambian la distribución de temperatura de la máquina.
Las fuentes externas de calor son las debidas a las condiciones del ambiente de la máquina. Los cambios de temperatura a lo largo del día, y también cambios a largo plazo como el efecto térmico de las estaciones (verano/invierno) son un claro ejemplo de estos. Otros efectos externos son la influencia de las máquinas cercanas y de las personas, si la máquina se encuentra en un recinto o está situada en el exterior, el efecto de la radiación solar si la máquina se encuentra al aire libre, etc. En la siguiente ilustración se puede ver la cadena de generación del error térmico en la punta de herramienta o TCP (Tool Center Point).
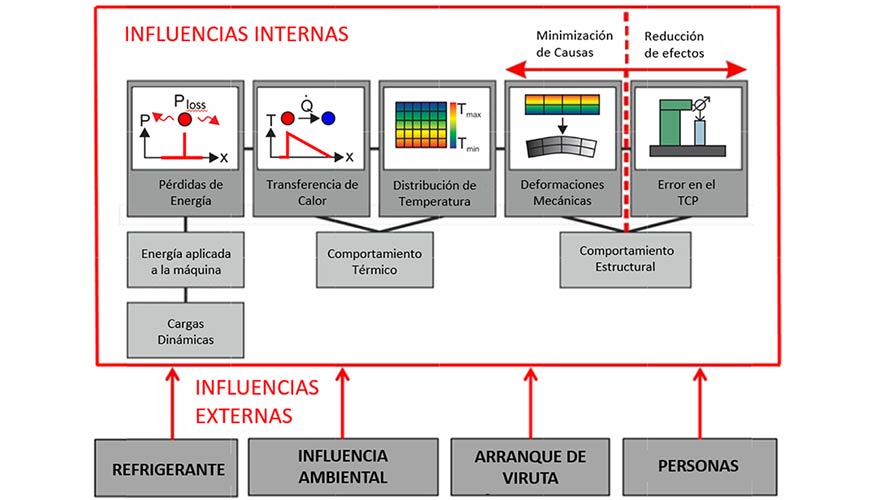
Otro punto importante además de las fuentes térmicas, son los mecanismos de transferencia de calor. Estos mecanismos determinan la transferencia de energía y distribución de temperatura que se da entre los distintos elementos de la máquina, y entre la máquina con el entorno. Se pueden dar tres formas de transferencia de calor: Conducción, convección y radiación.
- Conducción: la transferencia de calor por conducción se debe al intercambio de energía de la región de mayor temperatura a la de menor temperatura de un cuerpo o entre dos cuerpos por intercambio de la energía interna, la cual es combinación entre la energía cinética y potencial de sus partículas. En cuerpos sólidos metálicos se debe principalmente al intercambio de electrones libres. La conducción térmica está determinada por la ley de Fourier.
- Convección: la transferencia de calor por convección se debe al transporte de calor por medio del movimiento del fluido. En el caso de un fluido en contacto con un cuerpo sólido, la transferencia de calor se da debido al movimiento relativo del fluido y la superficie. El gradiente de temperatura depende de la rapidez a la que el fluido conduce el calor. Existen dos tipos de convección: La convección forzada y la convección natural. En la convección forzada la transferencia de calor se produce por el movimiento del fluido inducido por una fuente externa, mientras que en la convección natural el movimiento del fluido es generado por la diferencia de densidad del fluido debido a gradientes de temperatura.
- Radiación: cuando entre dos cuerpos de diferente temperatura hay una separación mediante vacío perfecto, no se puede dar transferencia de calor por conducción ni por convección. Sin embargo, se puede dar transferencia de calor por radiación térmica. Esta transferencia de energía se debe a la radiación electromagnética que es emitida por el movimiento térmico de las partículas de un cuerpo. El cuerpo emite energía radiante en forma de fotones por tener una temperatura mayor que el cero absoluto (0 K), y no requiere de un medio material para que se dé la transferencia de energía. La ecuación que determina el flujo de calor que emite un cuerpo real es la ecuación de Stefan-Boltzman.
Siguiendo con el esquema de la cadena que genera el error térmico, nos encontramos con la distribución de temperatura. La correcta gestión de los flujos de calor, permitirá una distribución de temperatura óptima que minimice los errores en el TCP. Estudios previos, dan importancia sobre todo a la transferencia de calor que se da por conducción y convección en máquina-herramienta mientras que la radiación térmica no influye significativamente. La geometría de la máquina también es determinante en la distribución de temperatura, siendo las estructuras simétricas las que consiguen una distribución más uniforme de la temperatura y que consiguen minimizar errores en el TCP. La correcta elección de los materiales de la máquina o combinación de materiales ayudan a una óptima distribución de temperaturas, por lo que la elección de materiales con mayor difusividad térmica consigue evacuar mejor el calor, o la elección de materiales con menor coeficiente dilatación térmica consiguen una menor deformación. También interesan materiales con conductividad térmica alta, ya que con ésta se consigue que los gradientes de temperatura sean menores.
La metodología que se ha llevado a cabo para la realización del modelo térmico de la Ibarmia ha tenido en cuenta todos los aspectos mencionados anteriormente, por lo que se ha aplicado la siguiente metodología de trabajo como se muestra en la figura 2. Primero se identifican los focos de calor de la propia máquina para posteriormente preparar los ensayos experimentales y realizar las correspondientes simulaciones FEM. Con los resultados obtenidos se realiza una comparativa y se realizan más ensayos y simulaciones que alimenten el modelo hasta su validación.
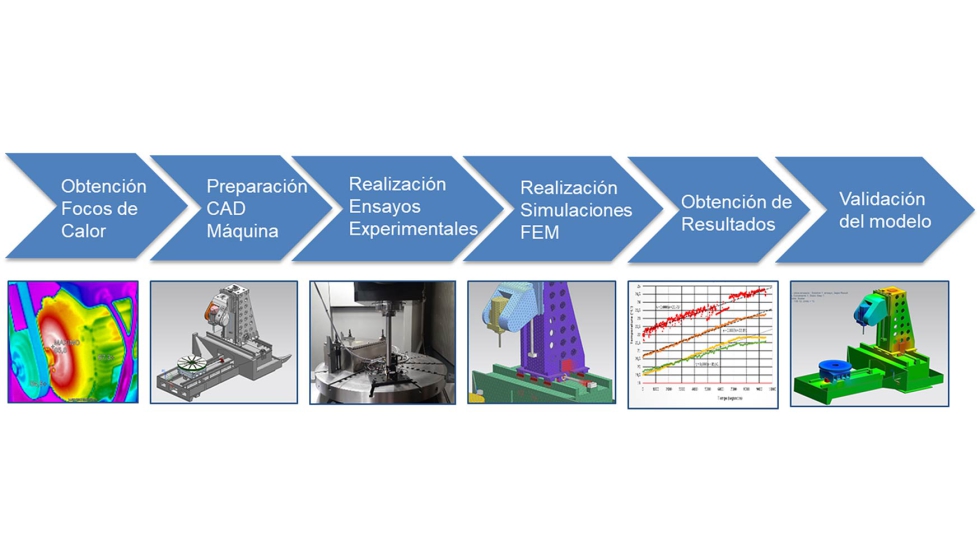
Identificación de los focos de calor
Las fuentes de error térmico principalmente se pueden clasificar en seis grupos distintos. A continuación, se describe cada una de ellas y donde se han identificado en el centro de mecanizado de 5 ejes Ibarmia THR-16 Multiprocess.
1. Calor generado en el proceso de corte
El foco de calor que se genera durante el proceso de corte suele ser muy importante y depende de distintos aspectos como el material de la herramienta de corte, el material de la pieza a mecanizar, la velocidad de giro del electro-husillo, la velocidad de avance durante el proceso de corte, etc. De experiencias previas, se ha podido estimar el calor que se desprende durante el mecanizado de una pieza con una velocidad de avance determinada, en la punta de herramienta y en la superficie de la mesa de trabajo debido al calor del proceso. En el presente trabajo no se han realizado ensayos experimentales con proceso de mecanizado, por lo que estos valores no se han tenido en cuenta para el modelo térmico. Para futuros ensayos en los que se mecanicen piezas, se pueden añadir estos parámetros al modelo.
2. Pérdidas de energía de la propia máquina-herramienta
Las pérdidas de energía se deben principalmente al rozamiento que se dan entre los distintos componentes mecánicos que transfieren el movimiento de los accionamientos y a las pérdidas eléctricas y magnéticas que se dan en los propios accionamientos. En cuanto al primer aspecto, los componentes donde se genera calor debido al rozamiento son los siguientes: en los rodamientos de los soportes de los husillos a bolas, los rodamientos de la tuerca del husillo (calentamiento que va directamente ligado a la precarga de la tuerca del husillo), los rodamientos que soportan al electro-husillo y los rodamientos donde se alojan los motores de torque (tanto de la mesa rotatoria como del cabezal tilting). De experiencias previas, se ha estimado el calor que desprenden los rodamientos de los ejes lineales cuando estos se mueven con una velocidad de avance de 15 m/min. Como no se tiene experiencia previa del ensayo de rotación en el eje A (giro del cabezal tilting), se estimará dicha evacuación de los rodamientos en función de los datos obtenidos del propio ensayo. Cómo en los ensayos experimentales se van a realizar ensayos de movimiento de los ejes X, Y y Z por separado y movimiento en los 3 ejes se podrá comparar si hay una correlación directa entre la velocidad de avance de los ejes lineales y el calor que generan. También se dispone de datos sobre el calor que desprende el husillo a bolas, los rodamientos, las guías lineales y los patines de dichas guías cuando la máquina se mueve a un avance de 15 m/min. Por otro lado, tanto en el servo-reductor del eje Y como en el contacto entre las correas con las poleas de los ejes X y Z se da una fricción que genera calor. El calor que desprende el reductor es muy importante ya que en su interior los engranajes helicoidales tienen una alta pérdida de potencia en forma de calor. Los valores del calor desprendidos tanto por los servo-reductor como las correas y los motores lineales con las poleas se estimarán a partir de los ensayos experimentales. El calor generado por el movimiento del electrohusillo es muy importante, sin embargo, como no se han realizado ensayos moviendo dicho accionamiento, no se han tenido en cuenta para este modelo.
3. Intercambio de calor debido a sistemas de refrigeración
Otro aspecto a tener en cuenta es el intercambio de calor que se genera por la refrigeración de ciertos componentes del centro de mecanizado que se pueden ver afectados por las altas temperaturas de calentamiento. En el caso concreto de la Ibarmia THR-16 Multiprocess se dispone de un sistema de refrigeración para el cabezal del electro-husillo y para la mesa rotatoria. En el caso del electro-husillo se refrigera con agua que circula con un caudal de 24 l/min a 14 °C. Para el caso de la mesa rotatoria, son dos los flujos de corriente que recorren dicho componente. La mesa tiene una refrigeración de aceite con un caudal 5 l/min para los rodamientos donde se aloja el motor de Torque y otro flujo de corriente de agua con un caudal de 15 l/min que se encarga de refrigerar el motor. La refrigeración se activa superado un umbral de temperatura por lo que no tiene por qué activarse en todos los ensayos.
4. Intercambio de calor que se da con el amiente
El efecto del ambiente externo de la máquina es otro aspecto muy importante a considerar para el modelo térmico. Para simular la temperatura en el medio ambiente se aplicarán los datos de temperatura captados en los ensayos experimentales con los termopares de temperatura ambiental. Los mecanismos de transferencia de calor que se dan con el ambiente son principalmente de convección con el aire exterior, por lo que se han aplicado distintos coeficientes de convección con el aire distintos en función si el componente es estático, móvil o se trata del husillo a bolas.
5. Efecto térmico de las personas en el entorno de la máquina
Para evitar este efecto durante los ensayos experimentales, se evita el acceder a la máquina durante el ensayo y mantener la puerta de la cubierta de la máquina completamente cerrada. El número de personas que estén durante los ensayos será mínimo (2 personas) para despreciar este efecto. De todas maneras, cualquier cambio en la temperatura ambiental que se pueda generar debido a la presencia de las personas y su calor corporal se ha tenido en cuenta debido a que los termopares de temperatura ambiental captan las condiciones ambientales de la temperatura ambiente con el efecto de las personas (y de máquinas aledañas) incluido.
Ensayos experimentales
El procedimiento de montaje y la preparación de los ensayos ha tenido como referencia la Norma UNE-ISO 230-3:2007, que aporta una guía de actuación para la determinación de ensayos térmicos en máquina-herramienta. También se ha seguido la metodología seguida en ensayos previos que ha realizado Tecnalia para el proyecto Smartemps y la bibliografía existente de ensayos del mismo tipo.
Se ha empleado la siguiente configuración para los ensayos térmicos en centros de mecanizado con husillo vertical:
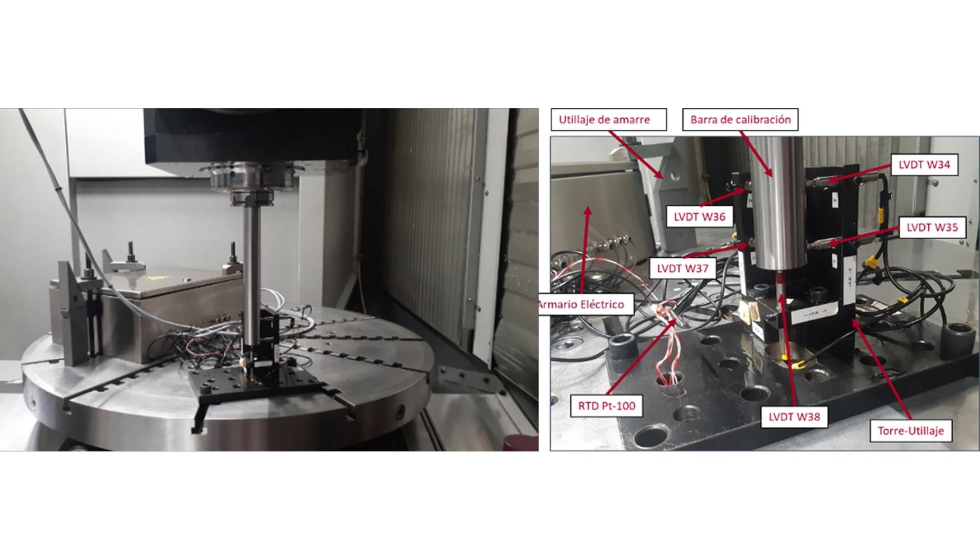
Los ensayos se realizan de la siguiente manera, en el centro de mecanizado se han dispuesto de una torre de transductores de posición (LVTDS’s 34, 35, 36, 37 y 38) que recogen valores de las desviaciones que sufre el mandril de ensayo tras el calentamiento de la máquina. Se han realizado 5 ensayos en los que se mueve la máquina durante un tiempo determinado para calentarla y posteriormente se mantiene parada (etapa de enfriamiento) durante otro tiempo. Durante estos ensayos, aparte de medir las desviaciones que sufre en punta de herramienta también se va a monitorizar en todo momento con termopares las temperaturas en distintos puntos de la máquina, y, por otro lado, las deformaciones termo-mecánicas que sufre la máquina en zonas locales mediante barras IDS (barras sensorizadas estructuralmente integradas). Todos estos valores son captados a través del PLC que se encuentra embebido en el centro de mecanizado, también a través de un sistema de adquisición de datos de National Instruments y el software Labview.
Los ensayos experimentales son los siguientes:
- Ensayo 1 (movimiento Eje Y) → Avance: 15 m/min
- Ensayo 2 (movimiento Eje X) → Avance: 15 m/min
- Ensayo 3 (movimiento Eje Y) → Avance: 15 m/min
- Ensayo 4 (movimiento Eje A) → Avance: 5 m/min
- Ensayo 5 (movimiento 3 Ejes) → Avance: 15 m/min
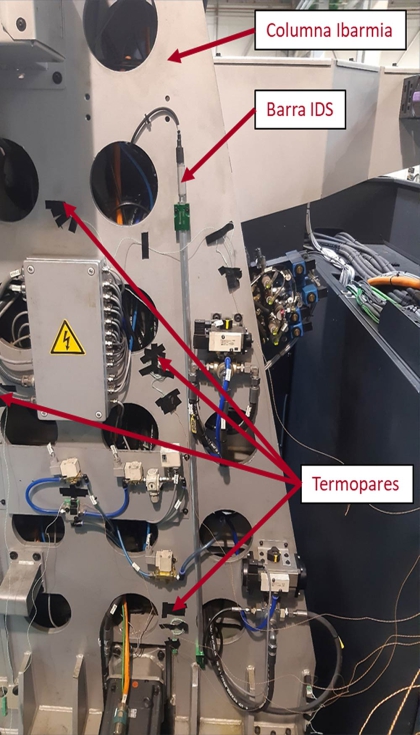
Validación del modelo termo-mecánico
Se ha empleado el software Simcenter 3D de la empresa Siemens para realizar los correspondientes análisis. Para el análisis del modelo térmico de la máquina-herramienta se debe tener en cuenta las hipótesis de partida que se han planteado previamente en el apartado de identificación de los focos de calor. Conocidos los valores de coeficientes de convección y el valor preliminar de las fuentes de calor, se procede a plantear el modelo y las simulaciones que se van a llevar a cabo.
Para correlacionar los valores de temperatura, deformaciones y desviaciones que experimenta la máquina-herramienta son necesarias dos tipos de análisis: análisis estático-estructurales y análisis térmicos. Con los análisis térmicos se pueden obtener valores del campo de temperaturas que experimenta uno o varios componentes tras experimentar un intercambio de calor debido a las fuentes de calor y otras condiciones de contorno que presenta la máquina. Con el análisis estructural se puede obtener información de las desviaciones y deformaciones que experimenta la máquina en situación estática o cuasi-estática cuando se le aplican unas determinadas cargas. En nuestro caso, las cargas aplicadas que reciben estos análisis como input van a ser los campos de temperatura que salgan como solución del análisis térmico previo. Por lo tanto, se puede decir que estos análisis termo-estructurales van a ser simulaciones acopladas. El solver que se encarga de ofrecer la solución a todos estos tipos de análisis va a ser NX Nastran.
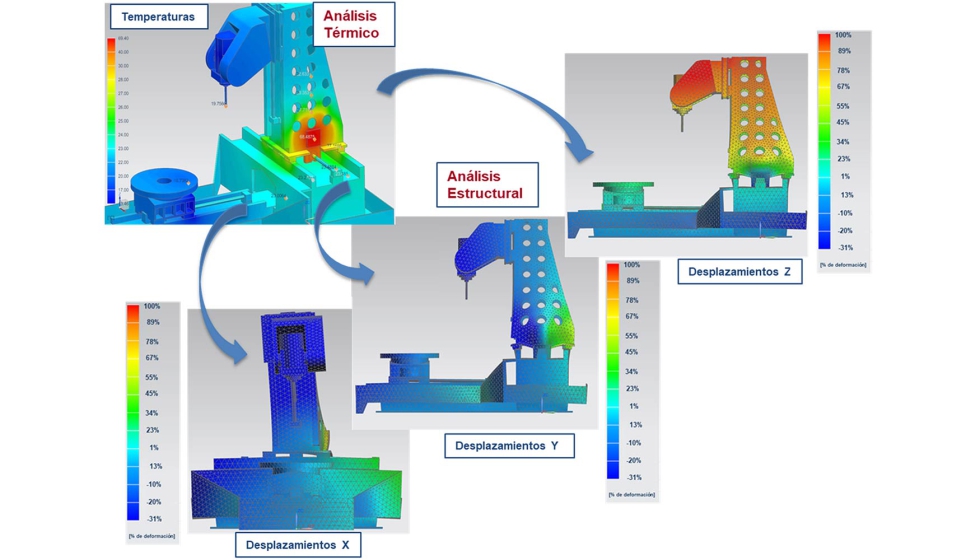
Para poder realizar los análisis, primero se debe simplificar la máquina, por lo que se pretende realizar una idealización de los archivos CAD de los componentes del centro de mecanizado, ya que el analizar el modelo como está de partida resultaría en un coste operativo muy alto. Posteriormente, se procede al mallado de los diferentes componentes, y se empleará principalmente elementos tridimensionales, siendo los elementos hexaédricos (CHEXA) los que obtienen unos resultados bastante precisos. Se debe evitar mallar elementos con relación de aspecto mayores de 10, ya que aumentaría la imprecisión de los resultados. Sin embargo, en zonas más específicas donde la relación de aspecto era muy superior a 10 o donde se quiere analizar con mayor detalle, se ha refinado la malla con elementos de menor tamaño. Posteriormente al mallado, se aplica a los componentes las propiedades del material y la aplicación de las condiciones de contorno. Para el caso del análisis térmico se deben aplicar cargas térmicas llamadas ‘heat flux’ que simulan el flujo de calor que se genera en determinadas zonas de la máquina y ‘fixed temperature’ que simulan las zonas donde pasa la refrigeración, además de introducir los valores de temperaturas iniciales de cada componente.
Para el análisis estructural, no existirán cargas aplicadas de fuerzas o momentos en la máquina. Se deben introducir como condiciones de contorno los valores de temperaturas iniciales de cada componente y se cargará el nuevo campo de temperaturas obtenido del análisis térmico previo. Por otro lado, se fija la base del centro de mecanizado con un ‘fixed constraint’ que simule el empotramiento de la máquina con la cimentación y se especifica el contacto entre los componentes mediante ‘face gluing’. Con el análisis estructural se pretenden poder ver como se deforma la máquina y los desplazamientos en las tres direcciones que se dan debido a esas deformaciones.
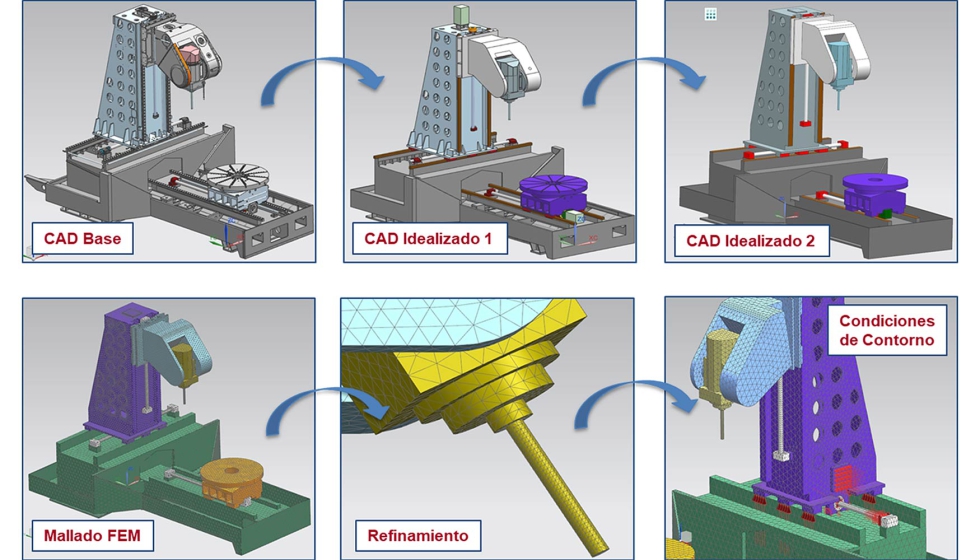
Resultados y discusión
Los resultados obtenidos en los ensayos experimentales han sido las variaciones de temperatura en distintos puntos de la máquina, las deformaciones locales y la desviación en punta de herramienta. En todos los ensayos se puede apreciar la variación de la relación entre estos desplazamientos relativos con la variación de la temperatura. Al aumentar la temperatura, la máquina se dilata y se deforma, lo que conlleva a un desplazamiento relativo positivo de las barras IDS. Se puede también apreciar que debido a la deriva térmica que posee la máquina, los picos máximos de temperatura se dan tiempo después del fin del ciclo de calentamiento de los ensayos. Dicho tiempo de offset se da en mayor o menor medida si el punto donde se mide la temperatura se encuentra más cerca o más lejos de los principales focos térmicos. Una vez se llega al pico máximo de desplazamiento positivo en las barras, se aprecia el efecto inverso debido al ciclo de enfriamiento (la máquina está parada). Las deformaciones locales captadas por las barras IDS pasan a estabilizarse hasta el punto en el que el efecto del enfriamiento devuelva a las barras a su posición original. Las barras que más se deforman son las que están más próximas a los focos de calor y la deformación que se da durante el calentamiento presenta una tendencia lineal en el que la pendiente varía en función de la proximidad a dichos focos de calor.
Comparativamente entre ensayos se puede ver como se dan mayores deformaciones en una barra cuando el foco se sitúa cerca de esta. Por ejemplo, en las barras del cabezal las deformaciones son mucho mayores en los ensayos en los que se mueve el eje Z o los tres ejes debido a que el servomotor situado encima de la columna y acciona dicho eje se encuentra próximos a estos.
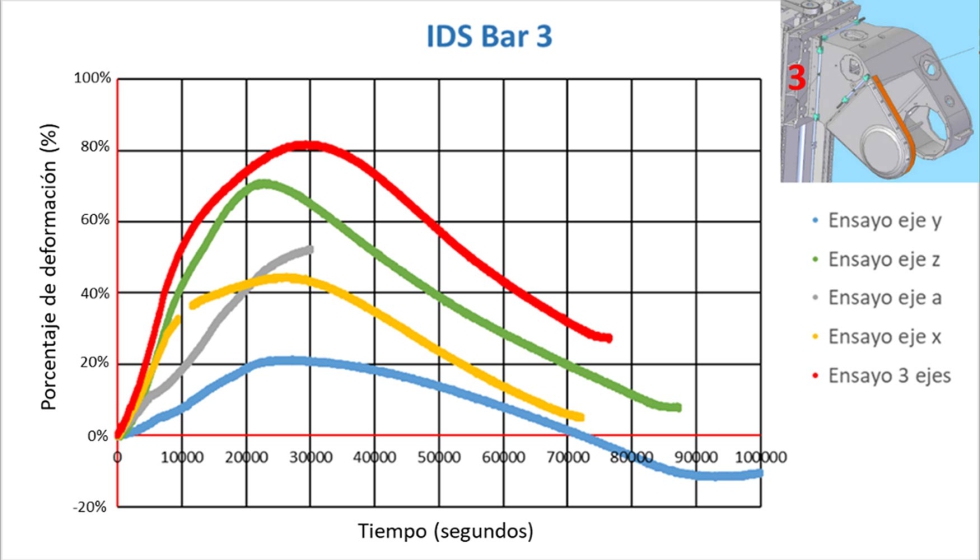
De manera parecida se da en los termopares, donde se puede ver como la tendencia de calentamiento es aproximadamente lineal, en las distintas zonas captadas por los termopares, teniendo una mayor pendiente las captadas por el termopar más cercano al servomotor (el que se encuentra más abajo en la columna). Se puede notar que ese termopar presenta unos picos de caída momentáneos, que se corresponde cuando la máquina se detiene para tomar la posición del TCP en la torre de transductores de posición. Esto nos lleva a la conclusión de la mayor sensibilidad en la temperatura que se dan cerca de los focos de calor, ya que en los otros termopares esos picos no se dan y la temperatura aumenta de manera más constante y fluida.
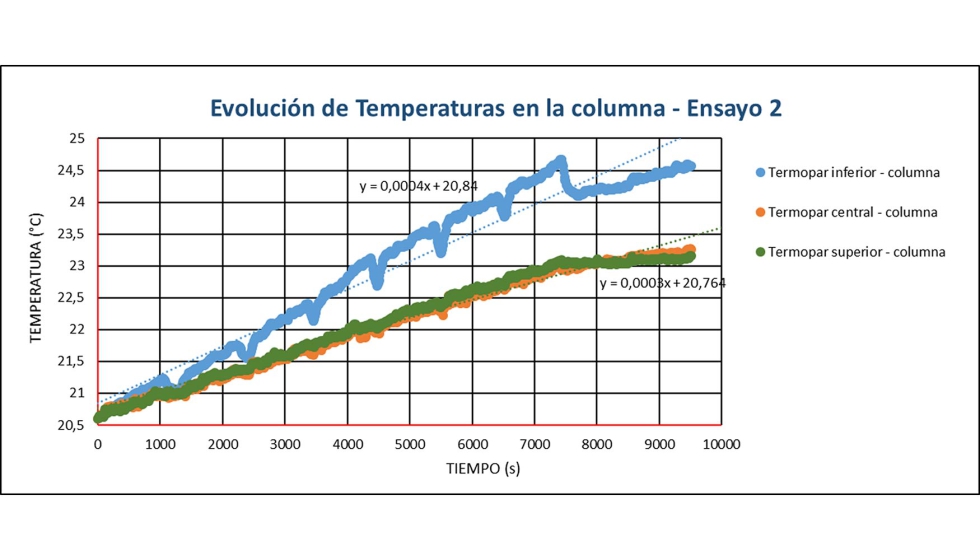
En cuanto a los resultados de las simulaciones por el modelo de elementos finitos, se ha conseguido un campo de temperaturas muy cercano a los ensayos experimentales con las condiciones de contorno aplicadas. Sin embargo, en el campo de desplazamientos en el análisis estructural la diferencia aumenta un poco, aunque sigue la misma tendencia de deformaciones que en los ensayos experimentales. En los casos en el que los valores entre ambos ensayos no se acercan lo suficiente se puede deber a las imprecisiones al idealizar el modelo o en la simplificación de las condiciones de contorno aplicadas. De cara a futuras líneas de investigación se puede buscar y optimizar el modelo añadiendo nuevas variables que no se han tenido en cuenta en este estudio para poder obtener unos resultados aceptables de manera simple. En la siguiente tabla comparativa se puede ver las desviaciones en porcentaje de las barras IDS normalizadas, siendo el 100% la barra que más se ha deformado en el ensayo o en el modelo FEM y el resto de valores estando en proporción:
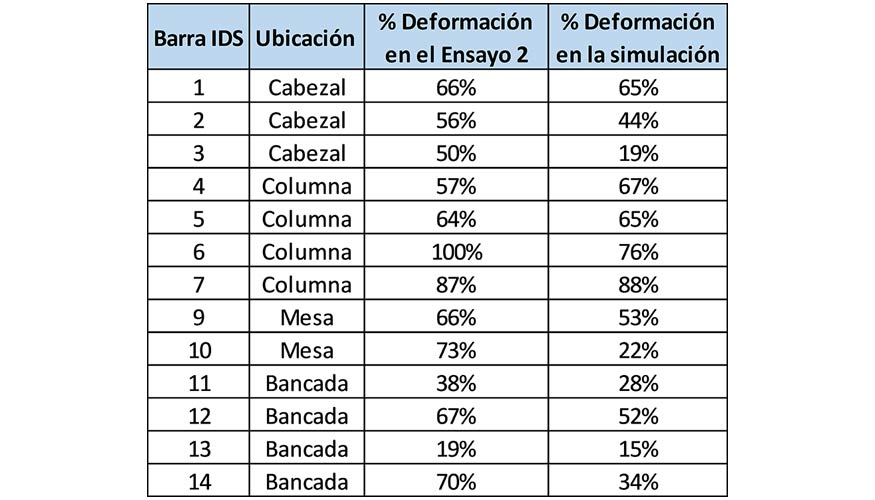
Finalmente, se puede observar una clara reducción en las desviaciones que sufre la punta de la herramienta si se aplica una compensación en las desviaciones que sufre esta en los ensayos experimentales con los calculados en la simulación FEM. Esta reducción del error térmico sería del 72,2% en el eje X, del 14,7% en el eje Y del 90,9% en el eje Z.
De esta manera se consigue un método de caracterización de los errores de origen térmicos para dicho centro de mecanizado. La metodología empleada puede servir como base para la caracterización térmica de otros tipos de máquinas-herramientas de grandes dimensiones. Las simulaciones FEM permiten identificar los componentes térmicos más críticos y a la vez validar los ensayos experimentales llevados a cabo. La implementación de barras IDS se presenta como una solución óptima para estimar los errores térmicos que se den en la máquina. Con estas barras se puede monitorizar en todo momento las deformaciones locales que sufre el centro de mecanizado durante su tiempo de trabajo y así poder compensar las desviaciones de origen térmico del TCP. No obstante, de cara a una implementación industrial de este tipo de monitorización en esta tipología de máquinas, el coste que implica integrar 14 barras IDS sería inasumible por parte del fabricante de la máquina-herramienta, ya que dispararía el precio final de la propia máquina. Los ensayos realizados y el modelo FEM permiten poder escoger que barras IDS son más significativas y que puedan permitir reducir en mayor medida las desviaciones de origen térmico. De esta manera se implementaría un menor número de barras y se reduciría el coste.
Líneas futuras de investigación
Se ha identificado las siguientes líneas que permitan continuar la investigación en la reducción de errores de origen térmico en máquinas-herramientas:
- Desarrollo de nuevos ensayos y simulaciones que permitan optimizar el modelo térmico y caracterizar la máquina en otras condiciones de trabajo a parte de las estudiadas en el presente documento. El estudio del movimiento de la mesa rotatoria, del electro-husillo o el movimiento de dos ejes simultáneamente son posibles vías.
- El estudio de las deformaciones de origen térmico teniendo en cuenta el efecto de la taladrina.
- El estudio de las deformaciones de origen térmico durante diferentes procesos de mecanizado.
- Estudio de la reducción de errores de origen térmico mediante la implantación de tablas de compensación dinámicas en el controlador numérico.
- Aplicación de la metodología realizada en este documento a otros tipos de máquinas-herramientas (centros de torneado, de rectificado, máquinas de electroerosión, etc.).